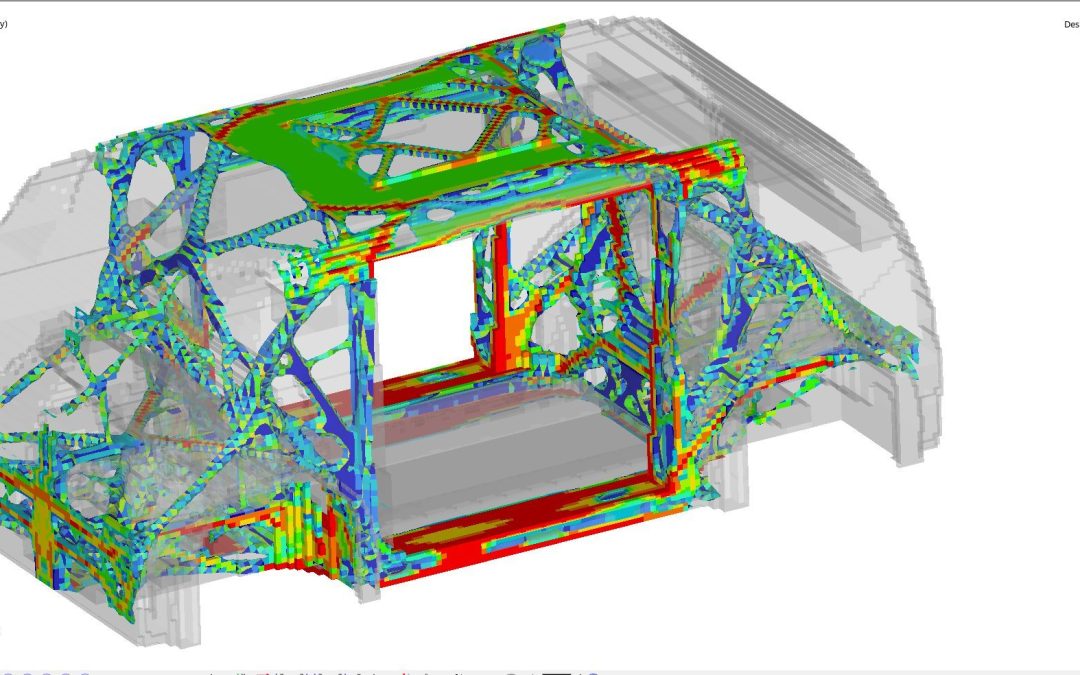
More Reveals of the Steel E-Motive Autonomous Vehicle Demonstration
WorldAutoSteel has a 30-year legacy of steel demonstration all the way back to the Ultra-Light Steel Auto Body (ULSAB), whose engineering report is still being downloaded from our worldautosteel.org site today. The one you may remember best is the FutureSteelVehicle (FSV), results of which we launched in 2011. FSV demonstrated steel innovation for not only Battery Electric vehicles (BEV) but also Fuel Cell vehicles (FCV). Steel E-Motive is the sixth of our global steel industry programs.
So Why Mobility as a Service?
The Automotive sector is undergoing the most rapid change in 40 years. This transformation shifts our thinking – from the movement of vehicles to the efficient movement of people and goods. Over the past eight years, we have conducted extensive research into global trends such as urbanization, transport emissions reduction, as well as the waning interest in vehicle ownership among the young and old. This is especially prevalent in megacities characterized by pollution, congestion, limited parking and enormous ownership costs. Our research concluded that mobility as a service (MaaS) will grow exponentially in high population areas and would place a significant challenge on vehicle design and manufacturing. Therefore, we needed to make sure we as an industry were active and visible in providing STEEL solutions in this new market place.
Steel E-Motive will demonstrate the benefits of steel, linking the properties of the material to the required architectures and attributes for MaaS vehicles.
This program will demonstrate the benefits of steel, linking the properties of the material to the required architectures and attributes for MaaS vehicles. It connects us with original equipment manufacturers (OEMs) and future mobility providers (FMPs), reinforcing steel’s advantages in strength, durability, sustainability and affordability.
An autonomous BEV structure aligns perfectly with steel’s best attributes, however most new concepts trial alternative materials. The global steel industry is investing significantly in product and fabrication development to continually prepare for the next challenge. High Strength and Advanced High-Strength Steel (AHSS) portfolios have grown from the 11 highlighted in the ULSAB program, to more than 60 grades available for use in designing and optimizing Steel E-Motive’s autonomous BEV architecture. Third Generation AHSS (3rd Gen AHSS) will have a prominent role in Steel E-Motive’s body-in-white, taking strength levels ever higher while improving manufacturability. And our industry continues to evolve Press Hardened Steels (PHS) with strength levels upwards of 2000 MPa.
Finally, efficient fabrication processes such as roll stamping, press hardening, and hydroforming use less steel and therefore contribute lower vehicle production emissions. These are the details being highlighted in Steel E-Motive, where we hope to demonstrate that only Steel can make it Real.
Steel E-Motive: A game changing, world first?
Many OEM’s and mobility service providers follow the typical vehicle development process where they adapt an existing vehicle structure to the new vehicle requirements. We don’t have that in Steel E-Motive We believe Steel E-Motive is one of the world’s firsts.
- The first for a Level 5 autonomous vehicle that is compliant with global high-speed crash requirements.
- The first autonomous vehicle to be a conventional high-volume stamped steel body construction, creating an affordable platform for the mobility service provider.
- First to offer a competitive, robust, and sustainable MaaS solution.
For engineers, being first is very exciting but a little nerve wracking – there are no benchmarks out there. There is less to “hang on to.” We’re on our own. Target setting is more challenging; we are the benchmark. Time will tell if we make it to the automotive hall of fame.
We are producing concepts for two BEVs based on a single modular platform. SEM1 (Figure 1) is a front-wheel drive short wheelbase urban version for inter-city travel for four passengers. It has a compact design and vehicle footprint, comparable in footprint to a European B/C segment size. SEM2 (Figure 2) is an all-wheel drive, long wheelbase extra urban version designed to carry up to six passengers. It has an adaptable interior volume that can result in additional luggage capacity compared to SEM1.
Body in White Steel Usage
Steel E-Motive benefits from a broad portfolio of steel grades and fabrication process, as identified by our member steel experts. The design is nearly finalized, and material selections are being evaluated against various performance targets with the representative structure shown in Figure 3 with high PHS usage at this stage in the design (as of May 2022). This is mainly driven by the safety requirements. Steel E-Motive BIW steel and steel technologies include:
- Right steel grade in the right place
- Significant proportion of >1500MPa grades, primarily for occupant and battery intrusion zones
- Mixture of stamped, roll formed, roll stamped, press hardened steel and hydroformed parts
- Spotweld, laser weld and structural adhesive
At the Core of the Steel E-Motive Concept Is an Innovative Battery Design
Figure 4 shows Steel E-Motive’s battery frame design’s construction:
- Battery modules and cooling plates are mounted to an AHSS carrier frame (off-line).
- The carrier frame is mounted to the body structure (in general assembly).
- The BIW floor acts as the top cover and provides sealing.
- The AHSS bottom cover plate provides impact protection.
This design provides significant cost and weight savings, as well as improved NVH. This extremely efficient package does not compromise safety and enables a flat floor with a lower step-in height.
Figure 4: Steel E-Motive Battery package assembly. (© WorldAutoSteel 2022)
Competitive Body Stiffness with an Open B-Pillarless Body Structure
With clean sheet design, and generally less package constraints in a Level 5 vehicle, our design teams have had more freedom to engineer and optimize the crash and stiffness structural loadpaths. We used topology, optimization, and Virtual Reality tools to determine the most efficient structural loadpaths (Figure 5). The results informed the joint designs and enabled optimization of the joining and structural adhesives. These steps and the advantage of steel’s high modulus resulted in impressive performance.
The approach for achieving body stiffness was as follows. Results are shown in Figure 6 following.
- Topology load path optimization
- Appropriate section size, profiles, part integration and flange / joint design
- Strut towers integrated with key body members, such as A-pillars, vertical dash brace
- Contribution from structural battery frame and battery cover closing, roof structure trusses
- Rigidly connected front and rear subframes
- Optimized joining and use of structural adhesives
- Capitalizing on the Inherent high modulus of steel
Figure 6: SEM Torsional Rigidity animation. (© WorldAutoSteel 2022)
Static torsional stiffness 38,000Nm/deg
Global trimmed BIW modes >28Hz
Local attachment static stiffness ten times bushing stiffness
Front Crash Structure Engineered to Balance the Requirements of 56kph USNCAP FFB, IIHS ODB, IIHS SORB and EuroNCAP MPDB Load cases
One of the most challenging aspects of the Steel E-Motive program has been achieving the front crash performance that minimizes occupant injury. The challenge has been compounded by the overall compact size of the vehicle and the short front overhang dimensions, meaning less space to manage and balance the required crush energy with intrusion resistance.
For the IIHS 25% Small Overlap test, we worked from the outset to achieve a barrier “glance off.” The goal is to deflect the vehicle off the barrier by the time the barrier reaches the hinge pillar. This results in a reduced amount of vehicle kinetic energy converted to crush energy. The vehicle continues after the impact with some onward velocity and kinetic energy. This strategy results in reduced intrusion to the passenger compartment and a much lower vehicle pulse (below 20g), which translates into lower occupant injury. We are very excited by this outcome, as in our benchmarking we have not seen many (if any) vehicles of this size managing to achieve a glance off for this test. Figures 7 and the bullets following provide a look at the results.
Figure 7: IIHS 25% Small Overlap test. (© WorldAutoSteel 2022)
- IIHS “good” rating achieved (based on predicted intrusions).
- Our strategy for IIHS Small Overlap test was to achieve a “glance off” the barrier, which is a significant challenge given the vehicle’s short front overhang.
- Front suspension engineered to detach on impact. This is important for achieving glance off.
- Glance off results in some continued onward vehicle velocity after the impact.
- This results in reduced crush energy, lower vehicle pulse and intrusions = enhanced occupant protection
Figure 8 points out features of the front crash structure. Most of the crush energy in FFB and ODB is absorbed by conventional longitudinal mid-rails, which are made of cold stamped, tailor welded blank Dual Phase steels. The plan view angle of the longitudinals has been optimized to provide load reaction early in the SORB event while remaining largely inside of the SORB barrier.
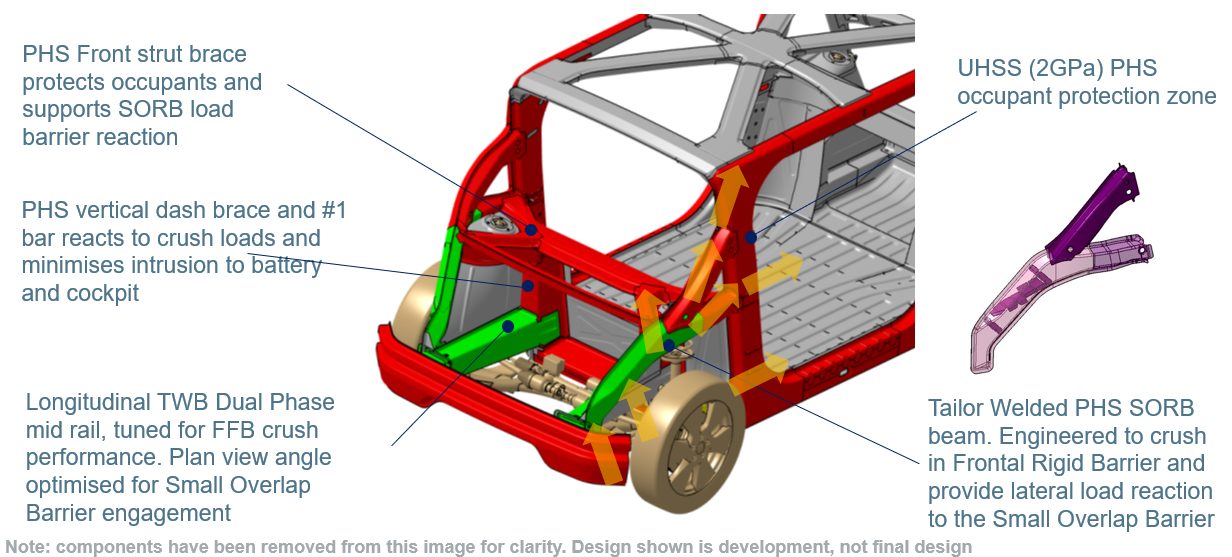
Figure 8: Front crash structure engineered to balance the requirements of 56kph USNCAP FFB, IIHS ODB, IIHS SORB and EuroNCAP MPDB load cases. (© WorldAutoSteel 2022)
Following in Figures 9 and 10 are animations of the FFB results:
Figure 9: USNCAP 56kph Rigid Barrier – Top View. (© WorldAutoSteel 2022) |
Figure 10: USNCAP 56kph Rigid Barrier – Side View. (© WorldAutoSteel 2022) |
MaaS vehicles will need to accommodate quick ingress and egress as well as provide comfort and safety for the occupants. Consequently, we have flipped the front occupant around to a rear facing configuration and provided a B-Pillarless wide door aperture to enable comfortable and quick access for passengers. This changes the approach required for occupant protection in a front crash. Effectively we are dealing with a high-speed rear impact situation for the occupant. Current rear impact tests cover lower speed rear end shunts. Figure 11 notes the key points and challenges that Steel E-Motive is designed to meet.
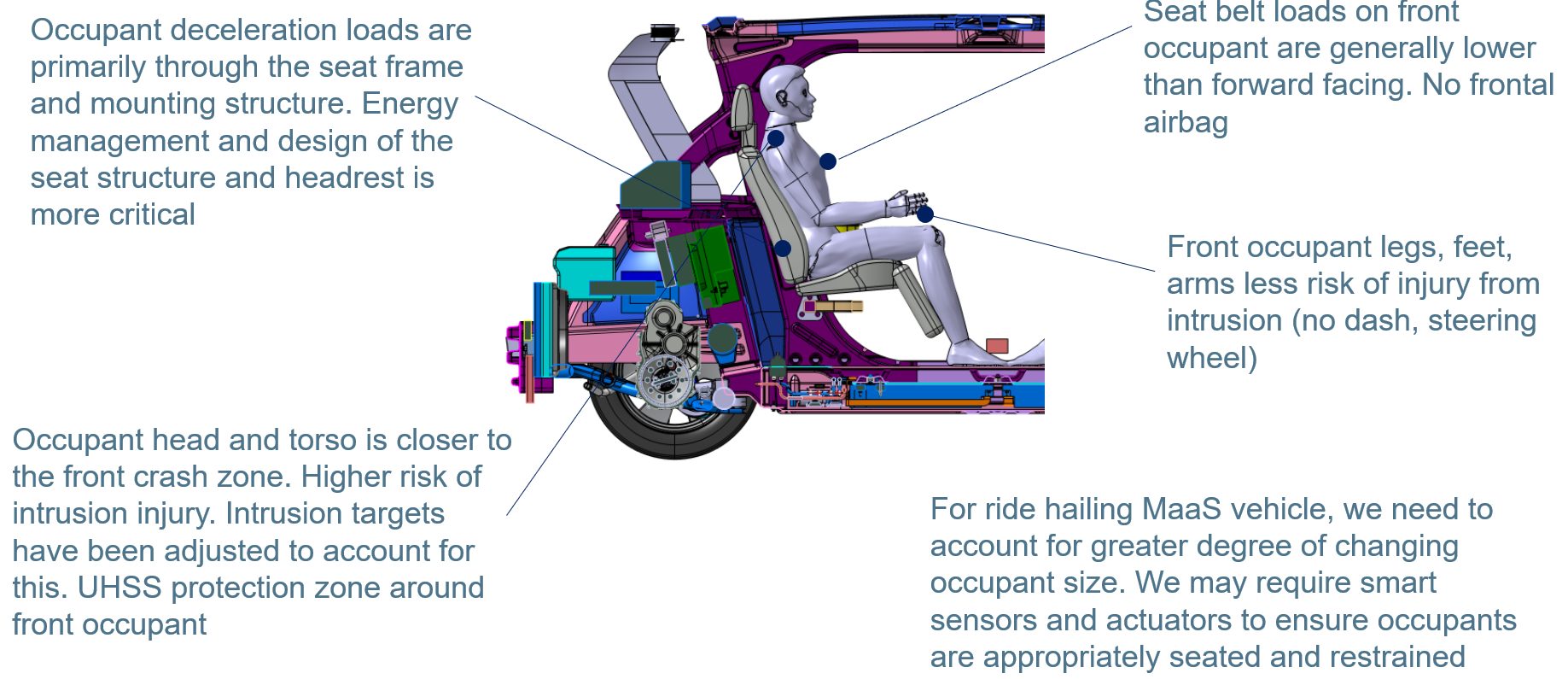
Figure 11: Different approach and considerations are required for the protection of rear facing front occupants. We are effectively addressing a high-speed rear impact event. (© WorldAutoSteel 2022)
Side Crash Structure Consists of Absorption and Intrusion Prevention Zones, Compensating for Large Body Aperture
The side structure includes roll-stamped martensitic door waist rail beams and a one-piece Tailor Welded Blank, Press Hardened Steel door ring outer. A- and C-pillars in line with occupants provide good side impact protection. (You can learn more about the door design in our May blog).
In the section AA schematic in Figure 12 the TRIP690 hydroformed tube interlocking door B-pillar is shown (wrapped over the rocker and cantrail). The load travels through the side impact crush “hex” beam, which is a two-piece roll formed DP590 component.
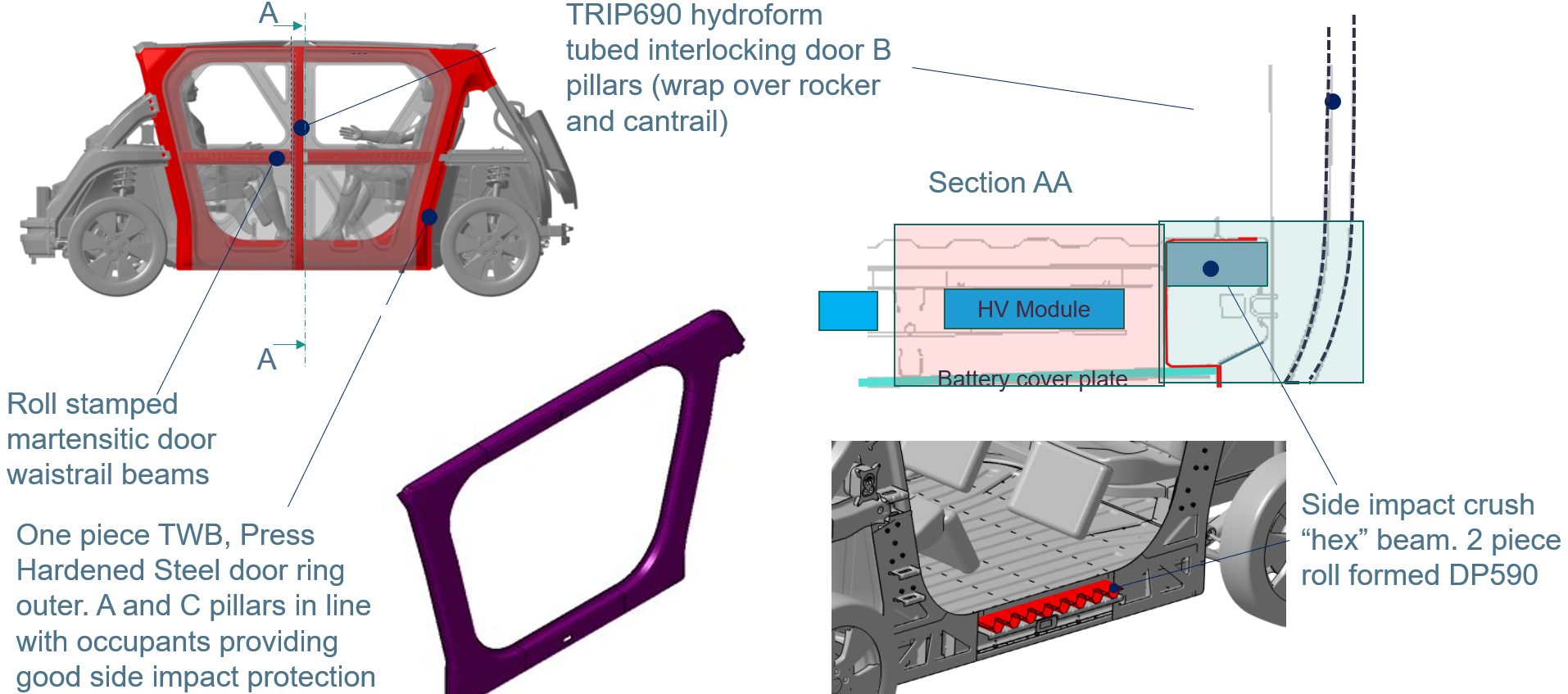
Figure 12: Side crash structure consists of absorption and intrusion prevention zones, compensating for large body aperture. (© WorldAutoSteel 2022)
Steel E-Motive Design Demonstrates Good Side Crashworthiness and Good Levels of Occupant and Battery Protection
In addition to occupant protection tests, additional side impact load cases have been simulated to ensure optimal battery protection. The design maintains a less than 30 mm clearance to the battery.
In reviewing the design according to IIHS standards and based on the predicted intrusions, we are confident this vehicle would achieve an IIHS “good” rating. See Figures 13 and 14 following:
Figure 13: USNCAP 32kph side pole (battery protection). (© WorldAutoSteel 2022)
In addition to occupant protection test, additional side pole load cases to ensure battery protection
>30mm clearance to battery maintained
Figure 14: IIHS 60kph side barrier II (occupant protection). (© WorldAutoSteel 2022)
IIHS “good” rating (based on predicted intrusions).
Total Cost of Ownership: Vehicle and Body Is Designed for Conventional Fabrication and Assembly Processes
The Steel E-Motive body has been designed with low cost in mind to provide the foundation for a lower total cost of ownership for fleet owners. The steel body design is optimized to maximize material utilization and minimize scrap rate. Steel E-Motive is suitable for >250,000 units/year production and is compatible with existing global automotive manufacturing facilities using conventional press and fabrication tools. We are also using Life Cycle Assessment as an integral part of the engineering process to ensure that Steel E-Motive is responsible for the lowest possible emissions throughout its entire life cycle. We will report on environmental performance and sustainability as a part of our final results.
Steel E-Motive Key Outcomes
The Steel E-Motive program is delivering an exciting futuristic vehicle, optimized from the ground up for autonomous MaaS application. We are addressing key challenges through careful design, application of simulation tools and efficient use of the latest Advanced High-Strength Steels and fabrication processes. Steel’s inherent characteristics of low production emissions, lightweighting capabilities for mass efficiency, infinite recyclability and product durability underscores its suitability as an integral part of stakeholder strategies to offer sustainable mobility solutions, today and in the future.
Be sure to follow us on our journey as we enter our final months of design, engineering and reporting by subscribing at the Steel E-Motive website. We welcome your questions about this program using the Comment box below.
Images are not for use without permission. Contact steel@worldautosteel.org.