1stGen AHSS, AHSS, Steel Grades
Ferrite-Bainite (FB) steels are hot rolled steels typically found in applications requiring improved edge stretch capability, balancing strength and formability. The microstructure of FB steels contains the phases ferrite and bainite. High elongation is associated with ferrite, and bainite is associated with good edge stretchability. A fine grain size with a minimized hardness differences between the phases further enhance hole expansion performance. These microstructural characteristics also leads to improved fatigue strength relative to the tensile strength.
FB steels have a fine microstructure of ferrite and bainite. Strengthening comes from by both grain refinement and second phase hardening with bainite. Relatively low hardness differences within a fine microstructure promotes good Stretch Flangable (SF) and high hole expansion (HHE) performance, both measures of local formability. Figure 1 shows a schematic Ferrite-Bainite steel microstructure, with a micrograph of FB 400Y540T shown in Figure 2.

Figure 1: Schematic Ferrite-Bainite steel microstructure.

Figure 2: Micrograph of Ferrite-Bainite steel, HR400Y540T-FB.H-21
The primary advantage of FB steels over HSLA and DP steels is the improved stretchability of sheared edges as measured by the hole expansion test. Compared to HSLA steels with the same level of strength, FB steels also have a higher strain hardening exponent (n-value) and increased total elongation. Figure 3 compares FB 450/600 with HSLA 350/450 steel. Engineering and true stress-strain curves for FB steel grades are shown in Figure 4.

Figure 3: A comparison of stress strain curves for mild steel, HSLA 350/450, and FB 450/600.
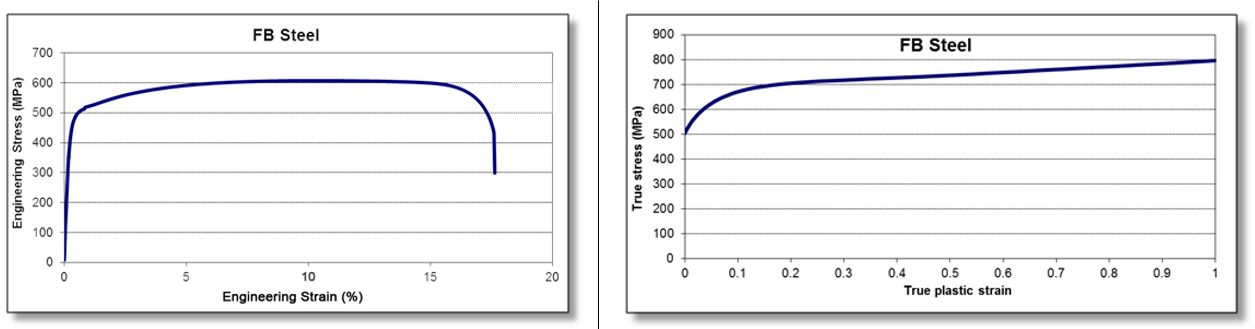
Figure 4: Engineering stress-strain (left graphic) and true stress-strain (right graphic) curve for FB 450/600.T-10
Examples of typical automotive applications benefitting from these high strength highly formable grades include automotive chassis and suspension parts such as upper and lower control arms, longitudinal beams, seat cross members, rear twist beams, engine sub-frames and wheels.
Some of the specifications describing uncoated hot rolled 1st Generation ferrite-bainite (FB) steel are included below, with the grades typically listed in order of increasing minimum tensile strength and ductility. Different specifications may exist which describe uncoated or coated versions of these grades. Many automakers have proprietary specifications which encompass their requirements.
- EN 10338, with the terms HDT450F and HDT580F D-18
- VDA239-100, with the terms HR300Y450T-FB, HR440Y580T-FB, and HR600Y780T-FB V-3
- JFS A2001, with the terms JSC440A and JSC590AJ-23
Forming Modes
Stretching is the sheet metal forming process where the punch which creates the part shape forces the sheet metal to thin since lock beads prevent metal flow inward from the flange area. In contrast with drawing, significant metal thinning occurs in stretching, especially in the biaxial tension mode. The biaxial increase in surface area reduces the metal thickness, maintaining the constancy of volume. The thinning soon reaches the onset of the local neck and failure as defined by the appropriate forming limit curve. The steel property that improves stretching is the strain hardening exponent, or n-value.
Stretchability, or the ability for a sheet metal to be stretched with no metal flowing from the flange or binder, often is assessed by the hemispherical dome test. Here, a hemispherical punch (usually with a 100 mm diameter) deforms a fully clamped blank. This ensures pure biaxial stretch without metal flowing from the blank into the deformation zone (Figure 1).
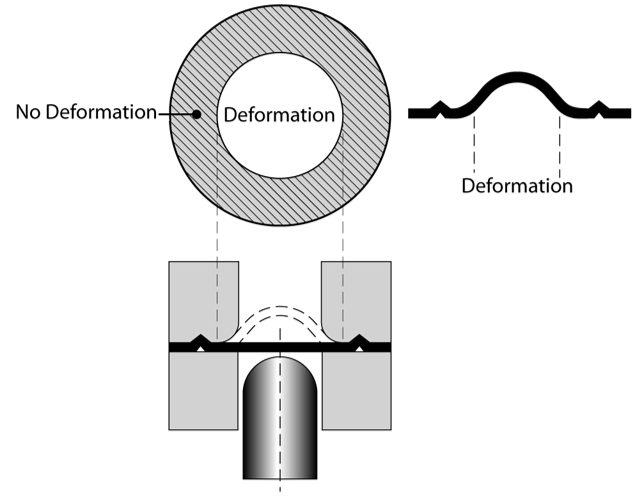
Figure 1: Stretch forming generated by a hemispherical punch stretching a locked circular blank.
Comparing the ratio of maximum dome height to punch diameter (H/d) is one way to view the results. Figure 2 illustrates a typical test output. Note the maximum dome height (H/d) at failure decreased as the yield strength increased and the n-value decreased.

Figure 2: Dome stretch tests of 1mm thick steel using a 100 mm hemispherical punch and a clamped blank.C-9
Additional stretch tests are possible with the hemispherical dome tester other than the dome height at failure shown in Figure 2. The limiting dome height (LDH) test stretches a rectangular steel strip which is locked in the longitudinal direction (Figure 3). Typically, a conventional rust preventive oil coats the blanks. Strips of different width are tested, with a circular lock bead preventing metal flow from the binder in the regions where the blank dimensions are large enough. The output of this test is the maximum dome height at failure. Figure 3 shows the achievable hemispherical dome height is substantially higher for the TRIP steel compared to the HSLA steel grade of equivalent tensile strength.
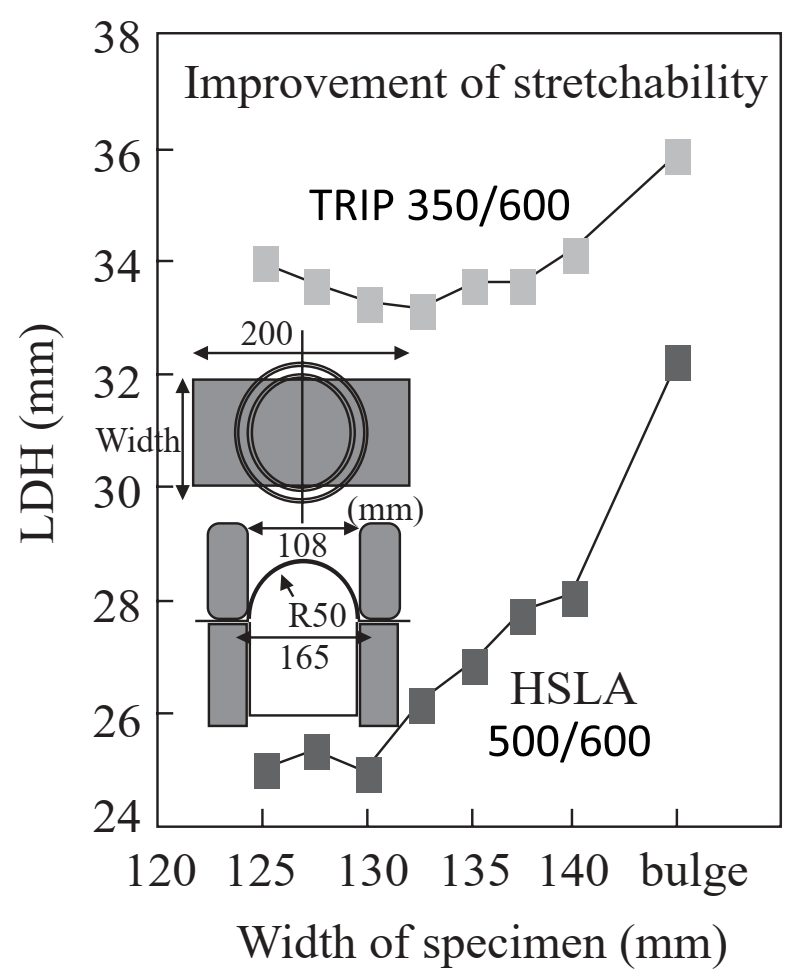
Figure 3: Limiting Dome Height is greater for TRIP than HSLA at the same tensile strength.T-2
The same tooling, steels, and lubricant from Figure 3 generated the thinning strains in Figure 4. Instead of forming to failure, the 50 mm radius hemispherical punch stretched the dome height to only 25 mm for both steels. The high n-value of TRIP steels minimizes strain gradients and reduces localizes thinning, helping to delay necking and form more complex geometries.
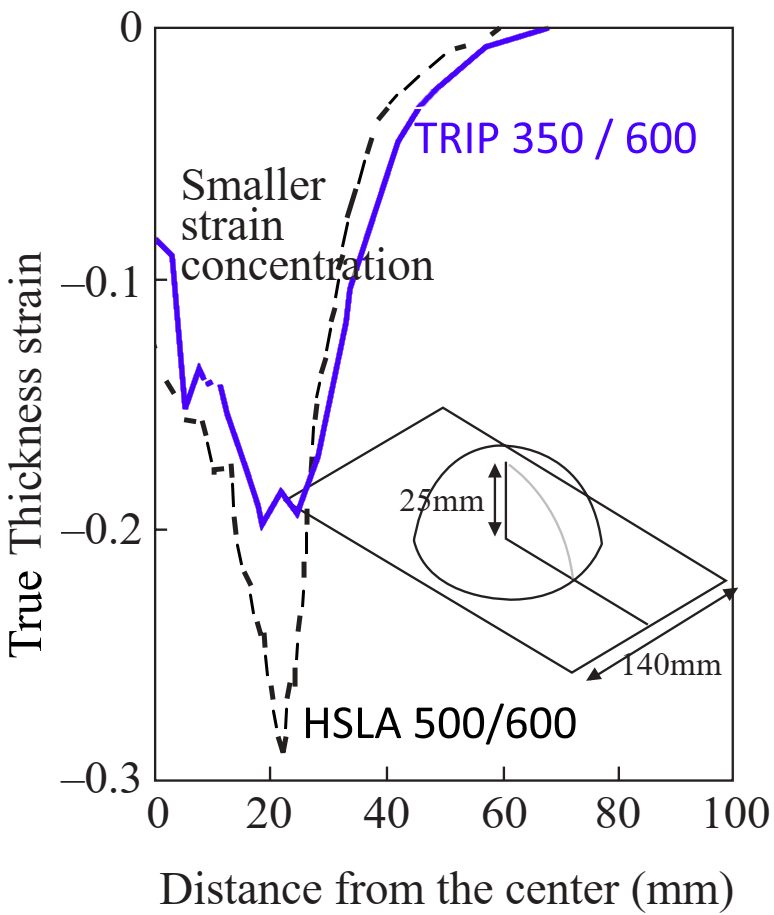
Figure 4: TRIP steel experiences less thinning than HSLA steel of the same tensile strength when formed to a constant dome height.T-2
The Limiting Dome Height test results for EDDS (vacuum-degassed interstitial-free) steel and three Advanced High Strength Steel grades are in Figure 5. Instead of plotting the various dome heights (as in Figure 3) to find the minimum value, Figure 5 simply shows the minimum value for each steel. TWIP (Twinning Induced Plasticity) steel has unique properties for stretchability and total elongation. Stretchability exceeds even that of EDDS IF steel.
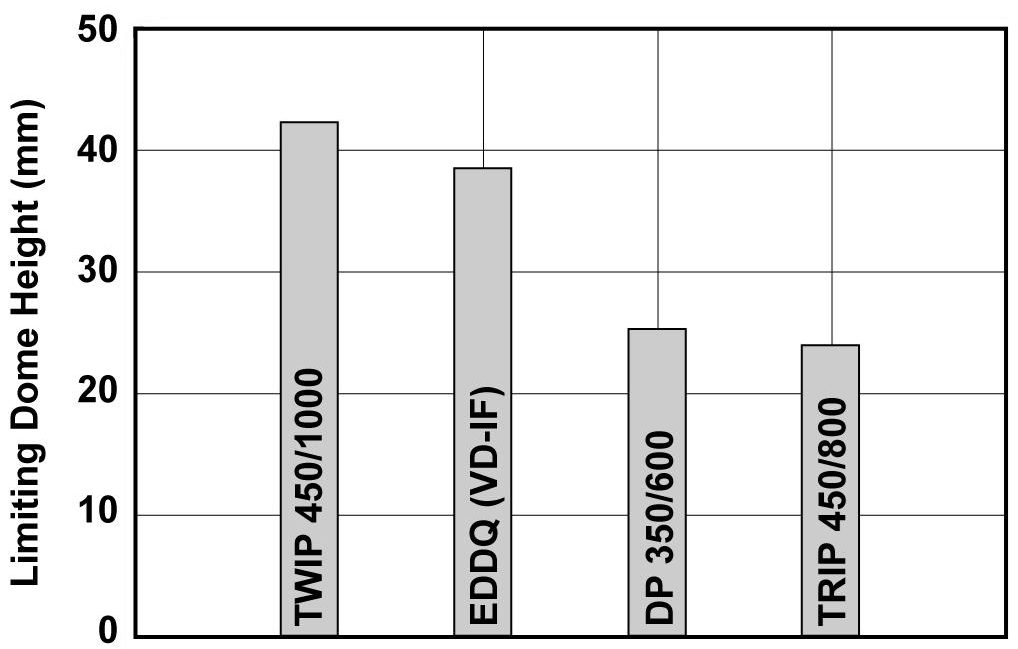
Figure 5: Limiting Dome Height values reflect relative stretchability of three AHSS compared with a low strength IF steel.P-2
Forming Modes
Stamping and die designers are interested in the forming capabilities of the steels they specify. Complex stampings are created from several different basic forming modes, which are sensitive to different mechanical properties. For this reason, steel formability, especially for AHSS grades, cannot be characterized by a single number, but instead must be done for each basic forming mode.
Forming modes and key points include:
Stretching
- Stretching is the sheet metal forming process where the punch which creates the part shape forces the sheet metal to thin since lock beads prevent metal flow inward from the flange area.
- The steel property that improves stretching is the strain hardening exponent, or n-value.
- Dome testing characterizes stretchability.
- Higher n-values flatten strain gradients, reduce localized thinning that leads to early failure, and allows the forming of more complex parts.
Bending
- Tensile testing cannot be used to determine bendability, since these are different failure modes. Different bend tests characterize bendability.
- The failure strain in the bend is related to the total elongation of conventional steel, but are limited by other issues in AHSS grades.
- For equal strengths, most AHSS grades have higher total elongations than conventional HSLA steels. However, several AHSS grades have limited local formability based on their microstructure, and may be at risk for cracking during edge expansion. AHSS grades with multiphase microstructures such as DP and TRIP experience shear fracture that severely reduces the bendability before failure occurs.
Drawing
- Drawing is the sheet metal forming process where the punch that creates the part shape forces the sheet metal to pull in from the flange area.
- The steel property that improves cup drawing or radial drawing is the normal anisotropy or rm value.
- The Limiting Draw Ratio (LDR) characterizes cup drawability.
- Higher r-value increases the LDR, but the absolute value of the LDR also depends on the lubrication, blank holder load, die radius and other system inputs.