Gas Metal Arc Welding: Introduction
Gas Metal Arc Welding (GMAW) (Figure 1), commonly referred to by its slang name “MIG” (metal inert gas welding) uses a continuously fed bare wire electrode through a nozzle that delivers a proper flow of shielding gas to protect the molten and hot metal as it cools. Because the wire is fed automatically by a wire feed system, GMAW is one of the arc welding processes considered to be semi-automatic. The wire feeder pushes the electrode through the welding torch where it makes electrical contact with the contact tube, which delivers the electrical power from the power supply and through the cable to the electrode. The process requires much less welding skill than Shielded Metal Arc Welding (SMAW) or Gas Tungsten Arc Welding (GTAW) [LINK TO SECTION] and produces higher deposition rates.
The basic equipment components are the welding gun and cable assembly, electrode feed unit, power supply, and source of shielding gas. This set up includes a water-cooling system for the welding gun which is typically necessary when welding with high duty cycles and high current.
GMAW became commercially available in the late 1940s offering a significant improvement in deposition rates and making welding more efficient. Deposition rates are much higher than for SMAW and GTAW, and the process is readily adaptable to robotic applications. Because of the fast welding speeds and ability to adapt to automation, it is widely used by automotive and heavy equipment manufacturers, as well as a wide variety of construction and structural welding, pipe and pressure vessel welding, and cladding applications. It is extremely flexible and can be used to weld virtually all metals. Relative to SMAW, GMAW equipment is a bit more expensive due to the additional wire feed mechanism, more complex torch, and the need for shielding gas, but overall it is still relatively inexpensive.
GMAW is “self-regulating”, which refers to the ability of the machine to maintain a constant arc length at all times. This is usually achieved using a constant-voltage power supply, although some modern machines are now capable of achieving self-regulation in other ways. This self-regulation feature results in a process that is ideal for mechanized and robotic applications.
Figure 2 provides important GMAW terminology. Of particular importance is electrode extension. As shown, electrode extension refers to the length of filler wire between the arc and the end of the contact tip. The reason for the importance of electrode extension is that the longer the electrode extension, the greater the amount of resistive (known as I2R) heating that will occur in the wire. Resistive heating occurs because the steel wire is not a good conductor of electricity. This effect can become significant at high currents and/or long extensions, and can result in more of the energy from the power supply being consumed in the heating and melting of the wire, and less in generating arc heating. As a result, significant resistive heating can result in a wider weld profile with less penetration or depth of fusion. The stand-off distance is also an important consideration. Distances that are excessive will adversely affect the ability of the shielding gas to protect the weld. Distances that are too close may result in excessive spatter build-up on the nozzle and contact tip. Various gases are being used for shielding the in GMAW process. The most common ones include argon (Ar), helium (He), and carbon dioxide (CO2) and combinations of these. Figure 3 illustrates the effect of the shielding gas on the weld profile.
AWS A5.18 is the carbon steel filler metal specification for SMAW, and includes both filler metal for both GMAW and GTAW. A typical electrode is shown on Figure 4. The “E” refers to electrode and the “R” refers to rod which means the filler metal can be used either as a GMAW electrode which carries the current, or as a separate filler metal in the form of a rod that could be used for the GTAW process. The “S” distinguishes this filler metal as solid (vs. the “T” designation which refers to a tubular GCAW electrode or “C” for composite electrode), the number, letter, or number/letter combination which follows the S refers to a variety of information about the filler metal such as composition, recommended shielding gas, and/or polarity.
In summary, the GMAW process offers the following advantages and limitations:
- Advantages:
- Higher deposition rates than SMAW and GTAW
- Better production efficiency vs. SMAW and GTAW since the electrode or filler wire does need to be continuously replaced
- Since no flux is used there is minimal post-weld cleaning required and no possibility for a slag inclusion
- Requires less welder skill than manual processes
- Easily automated
- Can weld most commercial alloys
- Deep penetration with spray transfer mode
- Depending on the metal transfer mode, all position welding is possible
- Limitations:
- Equipment is more expensive and less portable than SMAW equipment
- Torch is heavy and bulky so joint access might be a problem
- Various metal transfer modes add complexity and limitations
- Susceptible to drafty conditions
GMAW Procedures and Properties
Despite the increase alloying content used for Q&P 980, there is no increased welding defect type or rate compared with mild steel Gas Metal Arc Welding (GMAW) welds. Figure 5 is the microhardness profile of 1.6-mm Q&P 980’s GMAW weld joint. Both welded seam and HAZ are all less than 500 HV, and there is no obvious softened zone in HAZ.B-4
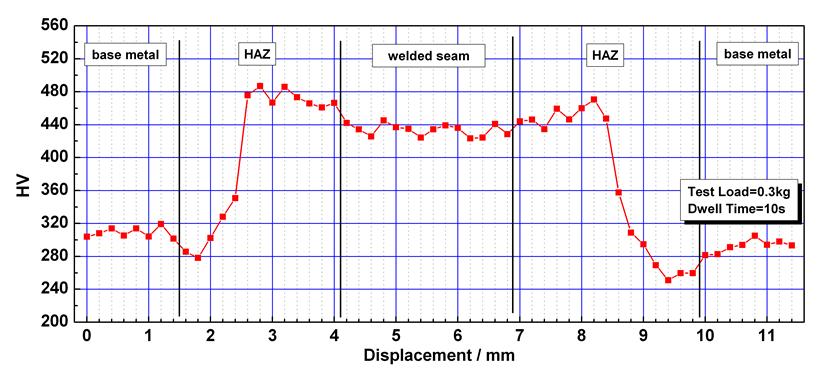
Figure 5: Microhardness profile of 1.6-mm DP 980’s GMAW weld joint. B-4
GMAW was used on three steels studied under a range of conditions. The left represents the FZ location and the middle is the HAZ. The figures show various degrees of HAZ hardening and softening depending on material grade and other conditions. The highest hardness occurs in the near HAZ, while the softest point is in the far HAZ. DP 980 [LINK TO THE MATERIAL IN METALLURGY] shows the greatest degree of HAZ hardening and softening. The nominally high CR condition is a combination of low heat input and heat sink. The plots show that CR tends to have the largest effect on the DP steels, with the TRIP steel being somewhat less affected. Pre-strain has the largest effect on the TRIP Base Metal (BM) , increasing the BM hardness by about 25%. The hardness of the softest location of the TRIP 780 HAZ is also increased by pre-strain, although degree of softening (about 20%) is not significantly changed. Pre-straining increased the DP 780 BM hardness by only about 10%. Pre-straining did not affect the peak HAZ hardness for either material. Post-baking did not appear to have a significant influence on the HAZ hardness profiles of the DP 780 material or the TRIP 780 material, regardless of pre-strain condition (Figures 6 through 8).
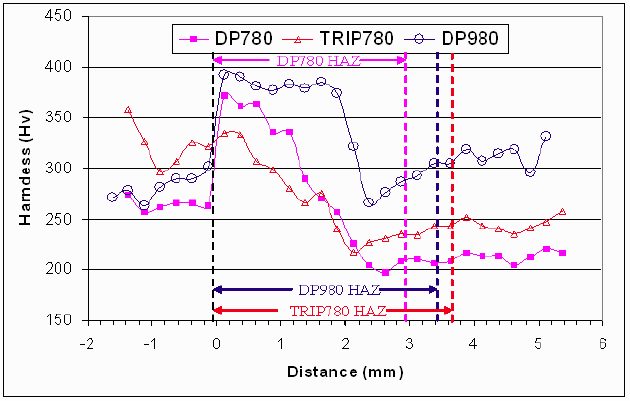
Figure 6: Hardness profiles of DP 780, TRIP 780, and DP 980 lap welds produced with the nominally high CR, no pre-strain or post-baking.P-7
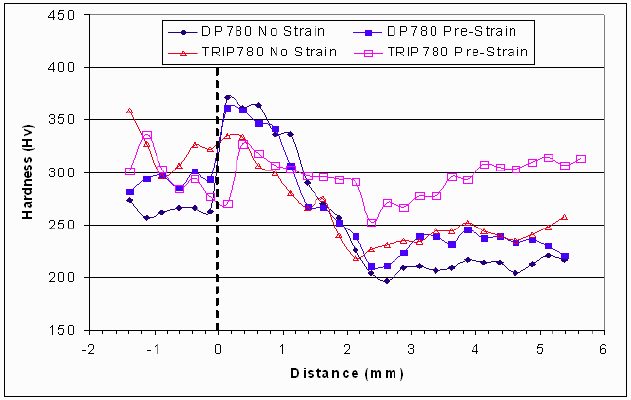
Figure 7: Hardness profiles of DP 780 and TRIP 780 welds
produced both with and without pre-strain for the high CR condition.E-1
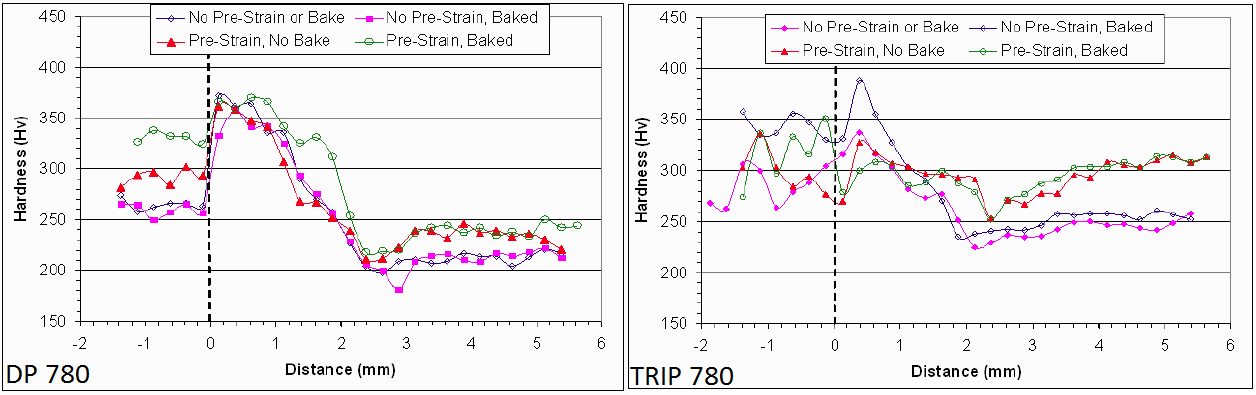
Figure 8: Hardness profiles of DP 780 and TRIP 780 welds produced both
with and without post-baking for both pre-strained sheet and not pre-strained
sheet for the nominally high CR condition.E-1
TRIP 780 lap joint static tensile results for different filler metal and CR conditions are shown in Figure 9. The results are expressed in terms of joint efficiency and the strain at peak load. The data indicates joint efficiencies ranged from about 50% to about 98%. Strains at peak load ranged from less than 3% to nearly 8%. Fracture occurred either in the far HAZ or at the weld fusion boundary. Filler metal strength had no discernable effect on the tensile properties. Figure 9 shows static tensile test results of the TRIP 780 butt joints. All the welds failed in the softened region of the far HAZ with joint efficiencies in excess of 89%. On average, welds made using higher CR experienced higher strains during loading than those made using lower CR. As was the case with the lap welds, filler metal strength did not appear to influence the static tensile properties. The abbreviations of high and low “CR” indicate high and low CR used for each weld.
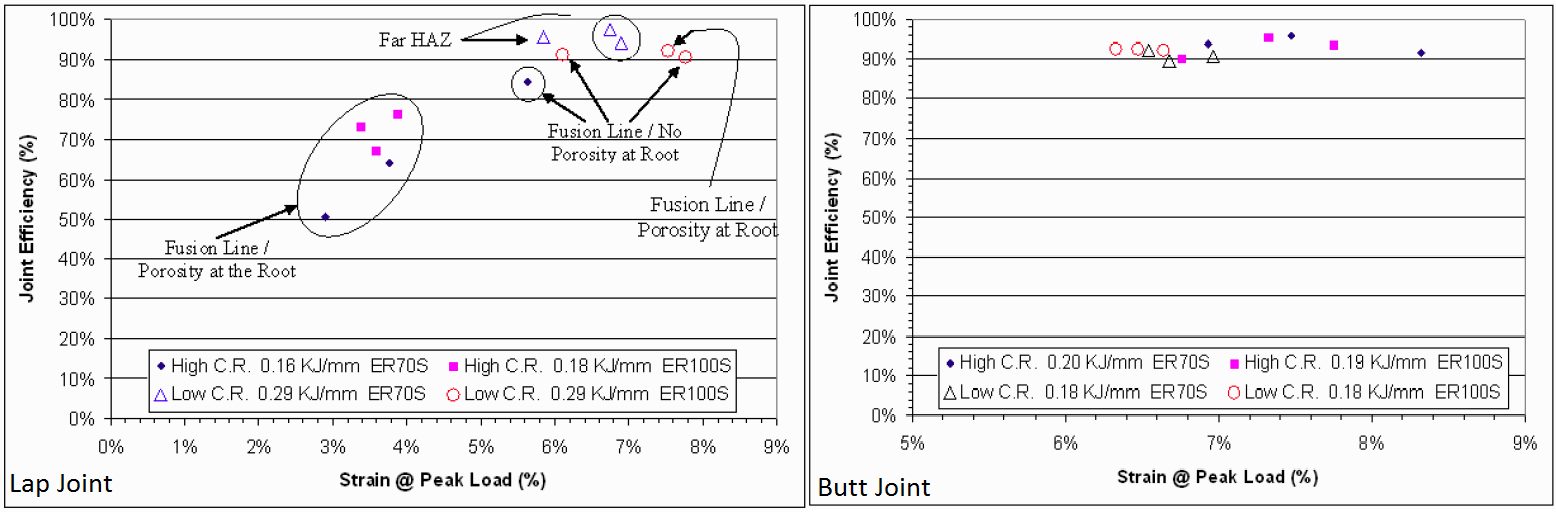
Figure 9: Static tensile test results of TRIP 780 lap and butt joints.E-1
The static tensile test results of the DP 780 butt welds are shown in Figure 10. All welds failed in the softened region of the far HAZ. As shown, the high CR welds had joint efficiencies in excess of 90%. The high CR welds also appear to have slightly greater strains at peak load.
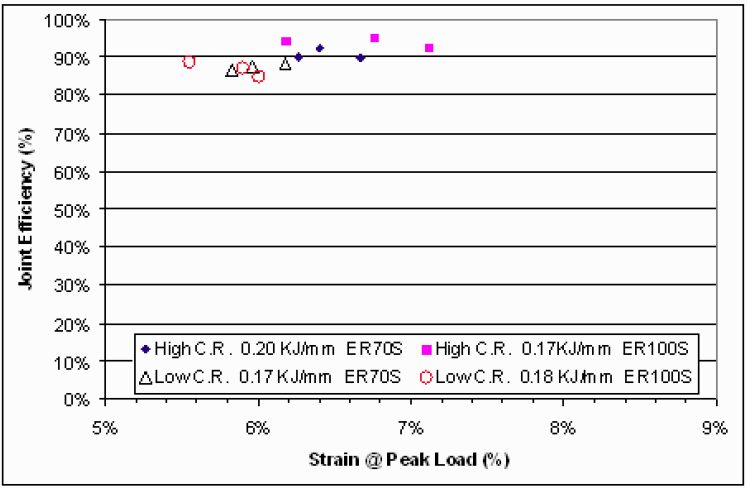
Figure 10: Static tensile test results of DP 780 butt joints.E-1
Figure 11 (left) shows the TRIP 780 lap joint dynamic tensile results for different filler metal and CR conditions. UTS ranged from 372 to 867 MPa (54 to 126 ksi) and strain at peak load ranged from less than 1% to over 5%. The high CR lap joints had lower strengths and strains at peak load. These welds failed along the fusion line presumably due to porosity present at the root. All the low CR lap welds produced with the ER70S-6 wire failed in far HAZ of the bottom sheet. Of the low CR lap joints produced with the ER100S-G wire, two dynamic tensile specimens failed in the softened region of the far HAZ, and one failed along the fusion line of the top sheet without the presence of porosity at the weld root. Analysis of Figure 11 (left) indicates that filler metal strength did not have a distinguishable effect on the dynamic tensile test results. Figure 11 (right) shows the dynamic tensile test results of the TRIP 780 butt joints. All failed in the softened region of the far HAZ. The UTS of the butt joints ranged from 840 to 896 MPa (122 to 130 ksi), and strain at peak load was generally between 3 and 4%. The figure indicates that neither filler metal strength nor CR condition had a distinguishable effect on the dynamic tensile test results of the butt joints.
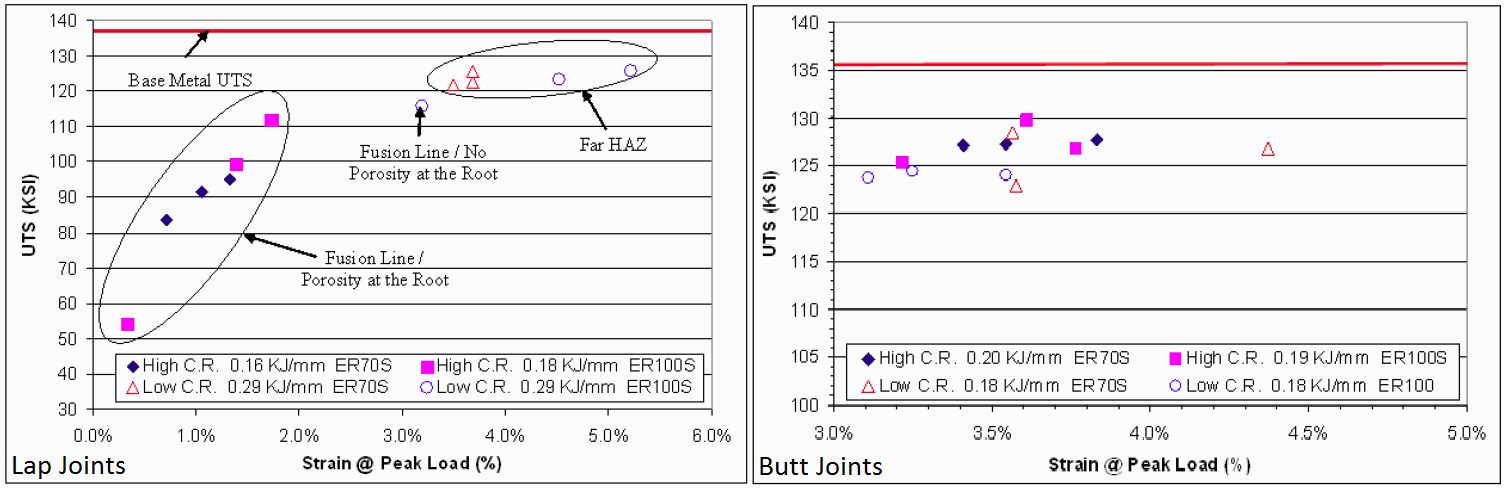
Figure 11: Dynamic tensile test results of TRIP 780 lap joints and butt joints.E-1
The dynamic tensile test results of the DP 780 butt joints are shown in Figure 12. All failed in the softened region of the far HAZ. UTS ranged from 841 to 910 MPa (122 to 132 ksi), and strain at peak load ranged from 2.25% to less than 4.0%. It should be noted that similar UTS were obtained for the DP 780 and TRIP 780 butt joints. On average, TRIP 780 butt joints had slightly higher strain at peak load. Neither filler metal strength nor CR condition appears to have a distinguishable effect on the dynamic tensile properties.
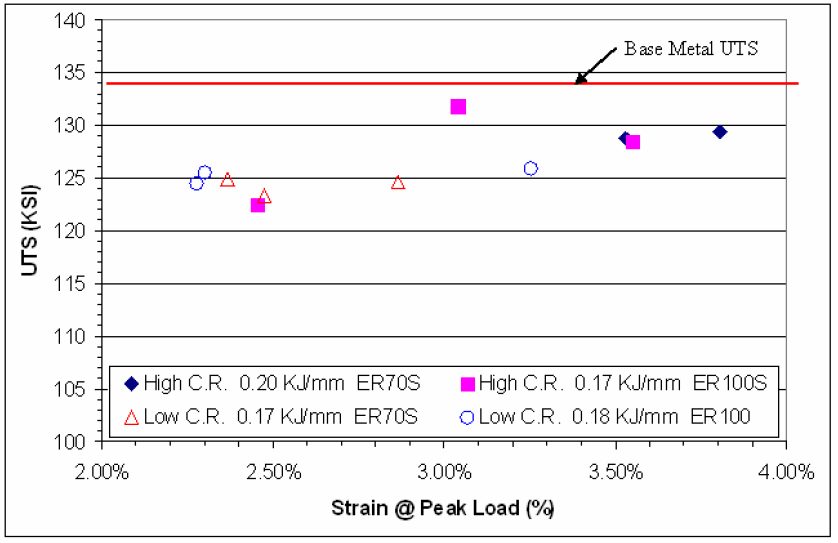
Figure 12: Dynamic tensile test results of DP 780 butt joints.E-1