It has been a long-standing challenge to extend the usage of the very high-strength steels in hydrogen-rich environments, given that these steels are prone to Hydrogen Cracking, due to their increased mechanical strength. Hydrogen embrittlement (HE) is known to be a premature fracture caused by a small amount of hydrogen atoms concentrated at highly stressed regions inside susceptible high tensile strength materials. (See examples in Figure 1.)
The factors controlling the occurrence of HE, susceptible microstructure, stress, and the presence of hydrogen, are well known and have been sufficiently quantified to develop procedures that minimize its occurrence mostly in arc welding thicker gauge steels. When advanced high strength steel (AHSS) with tensile strength over 980 MPa are applied in automotive applications, there is a small risk that hydrogen embrittlement fracture (sometime called delayed fracture) may occur after welding, while a vehicle is in use. Although there have been no reports that automotive parts made of AHSS have fractured due to hydrogen embrittlement, a risk assessment of delayed fracture for AHSS is considered necessary to ensure the safety of the automotive body and encourage wider use of Advanced High-Strength Steel (AHSS) sheets.
Another common embrittlement phenomenon involves the zinc coating discussed previously. Resistance spot welding is dependent on the interfacial contact resistance between the electrodes and the material. During welding, a metal with a lower melting point, such as zinc can penetrate in a liquid state into the grain boundaries of the material. By the end of the welding process, liquid metal embrittlement (LME) can become a problem due to the ductility of the grain boundary being reduced by the impeding tensile stress. (Example can be seen in Figure 2.) Also, brittle intermetallic compounds, such as Cu5Zn8, are created by the reaction with the Cu electrode and the material at the high temperature, which promotes LME or surface cracking.
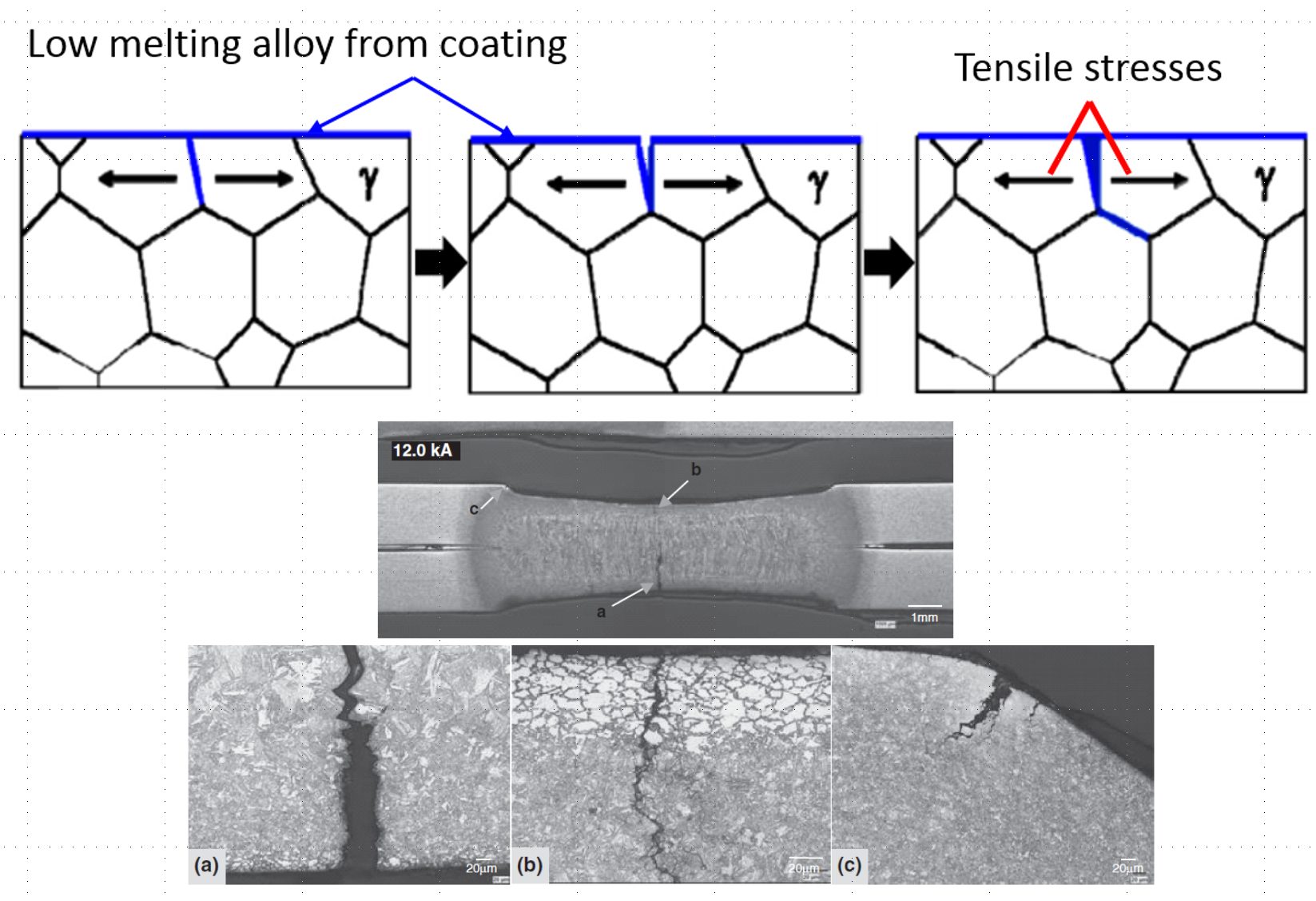
Figure 2: Description of (top image) and actual example (bottom) of the LME phenomenon in zinc coated AHSS.
There are many research papers investigating and analyzing Liquid Metal Embrittlement in mild steel and AHSS. LME is not unique to automotive AHSS steels or RSW, but is discovered in other ferrous materials, heat treatment and other welding processes. In spot welding AHSS, the complex microstructure and the greater spring back behavior of AHSS eventually lead to weld discontinuities such as LME.
A detailed multi-year, multi-organization study investigated the root causes of LME and how to test for, control, and prevent LME. The full report can be downloaded here, and is summarized in an AHSS Insights Blog.
The Joining Team of the Auto/Steel Partnership (A/SP) also recognizes the concerns surrounding LME, and conducted several rounds of testing, summarized here.
A/SP developed two separate procedures to test for Liquid Metal Embrittlement:
- testing with a Gleeble® unit to dynamically simulate spot welding conditions and assess LME susceptibility of steel coupons as a function of temperature and strain rate. Version 1.0 of the Gleeble-based procedure can be accessed from this link. https://www.a-sp.org/wp-content/uploads/2023/06/ASP-LP2.1-OSU-Gleeble-Based-Test-Proc.pdf
- a quicker, lower cost test procedure that better replicated spot weld conditions, called the Rapid LME Test. This test applies a series of spot welds with increasing amperage followed by cross sectioning and metallurgical evaluation to assess the location and severity of LME cracks by location. Version 1.0 of the Rapid-LME test procedure can be accessed from this link: https://www.a-sp.org/wp-content/uploads/2023/08/ASP-LP3.1-Rapid-LME-Test-Proc-0623.pdf.
In summary, LME cracking may occur when a combination of tensile stress, liquid metal and susceptible microstructure exist. Studies are being performed to evaluate whether LME is mitigated by today’s automotive RSW processes, where the volume of welds significantly exceeds engineering requirements, or whether the occurrence of LME actually affects in-use properties at all.