Fundamentals and Principles of Adhesive Joining
Adhesive bonding is a joining process for metals and non-metals that uses and adhesive or glue, typically in the form of a liquid or a paste. It offers the major advantage of being able to join a wide array of materials, but is limited by joint strength and applicable service conditions. Many of the fundamentals are similar to brazing and soldering, in particular the need for wetting and capillary action, and overlapping joint designs that rely on joint area for strength. Adhesives are categorized as thermosetting or thermoplastic. Thermosetting adhesives require a chemical reaction to cure and cannot be remelted once cured. They are the most common adhesives for structural applications. Thermoplastic adhesives soften when heated and harden when cooled, a process that can be continually repeated. They are generally not used for structural applications because of their poor mechanical properties (in particular, creep) and decomposition that can occur at relatively low temperatures.
Surface preparation is usually a very important and time-consuming step prior to applying the adhesive, and typically includes cleaning and deoxidizing procedures. Further steps may be taken such as the application of a coating. Adhesives may be applied a variety of ways, including caulking and spray guns, dipping, rollers, and brushes. Curing may be accelerated by heating or some other energy source. In addition to joining, adhesives may be used for many other reasons including sealing, electrical insulation, and sound suppression. Some of the larger users of adhesive bonding include the automotive, appliance, and electrical/electronics industry sectors.
Adhesive Joining Procedures
The bond strength of an adhesive is constant, and in design applications, is proportional to the area covered by the adhesive. The adhesive joint strength will be unchanged and analysis of the joint should be comprehensive. In general, the use of AHSS with high-strength structural adhesives will result in higher bond strength than for mild steel if the same sheet thickness is applied (Figure 1). Reduction of sheet thickness will decrease the strength because more peel load will occur. The true mechanical load in the component part must be considered. If higher joint strengths are needed, the overlapped area may be enlarged. Adhesives with even higher strength are under development.
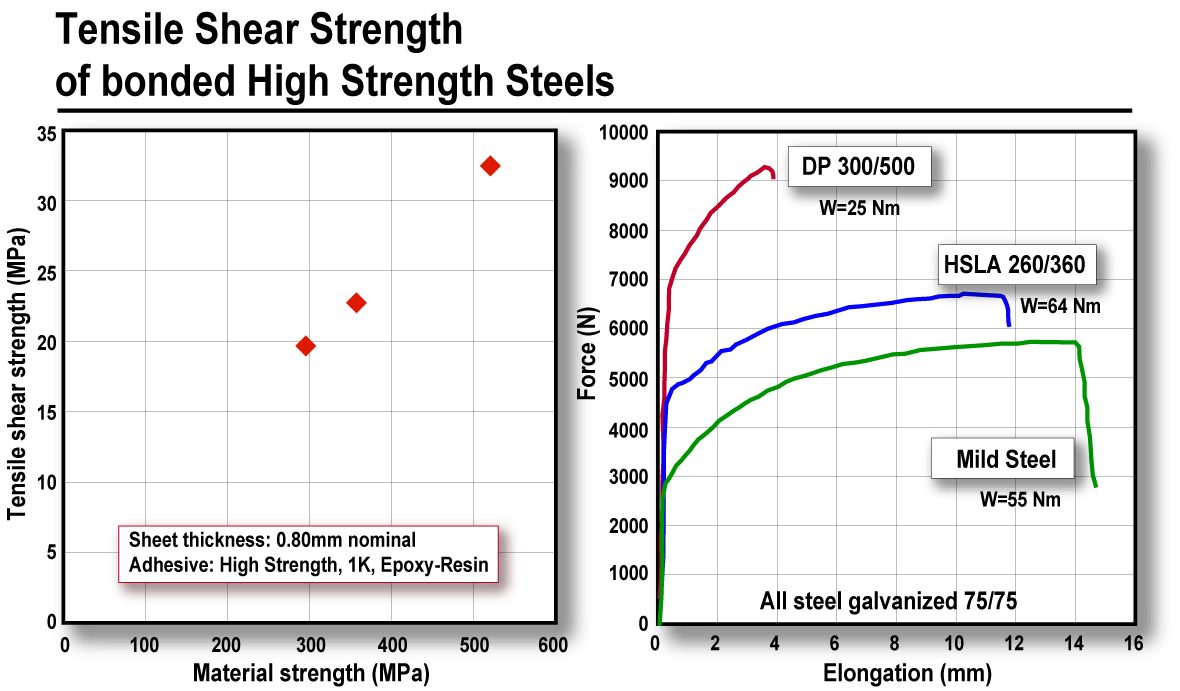
Figure 1: Effect of material strength on bond strength (W is the integral of the force/elongation curve.B-2).
Joining of AHSS with adhesive bonding is a good method to improve stiffness and fatigue strength in comparison to other joining methods (spot welding, mechanical joining, arc welding, and laser welding). Due to the larger bonding area with adhesive bonding, the local stresses can be reduced and therefore the fatigue strength is increased. These improvements in stiffness and fatigue strength are important factors to consider at the design stage, especially in those cases when AHSS is used to decrease the weight of a component.