1stGen AHSS, AHSS, Press Hardened Steels, Steel Grades
Introduction
Press hardening steels are typically carbon-manganese-boron alloyed steels. They are also commonly known as:
- Press Hardening Steels (PHS)
- Hot Press Forming Steels (HPF), a term more common in Asia
- Boron Steel: although the name may also refer to other steels, in automotive industry boron steel is typically used for PHS
- Hot Formed Steel (HF), a term more common in Europe.
The most common PHS grade is PHS1500. In Europe, this grade is commonly referred to as 22MnB5 or 1.5528. As received, it has ferritic-pearlitic microstructure and a yield strength between 300-600 MPa depending on the cold working. The tensile strength of as received steel can be expected to be between 450 and 750 MPa. Total elongation must be over a minimum of 12% (A80), but depending on coating type and thickness may well exceed 18% (A80), see Figure 1*. Thus, the grade can be cold formed to relatively complex geometries using certain methods and coatings. When hardened, it has a minimum yield strength of 950 MPa and tensile strength typically around 1300-1650 MPa, Figure 1.B-14 Some companies describe them with their yield and tensile strength levels, such as PHS950Y1500T. It is also common in Europe to see this steel as PHS950Y1300T, and thus aiming for a minimum tensile strength of 1300 MPa after quenching.
The PHS1500 name may also be used for the Zn-coated 20MnB8 or air hardenable 22MnSiB9-5 grades. The former is known as “direct forming with pre-cooling steel” and could be abbreviated as CR1500T-PS, PHS1500PS, PHSPS950Y1300T or similar. The latter grade is known as “multi-step hot forming steel” and could be abbreviated as, CR1500T-MS, PHS1500MS, PHSMS950Y1300T or similar.V-9

Figure 1: Stress-Strain Curves of PHS1500 before and after quenching* (re-created after Citations U-9, O-8, B-18).
In the last decade, several steel makers introduced grades with higher carbon levels, leading to a tensile strength between 1800 MPa and 2000 MPa. Hydrogen induced cracking (HIC) and weldability limit applications of PHS1800, PHS1900 and PHS2000, with studies underway to develop practices which minimize or eliminate these limitations.
Lastly, there are higher energy absorbing, lower strength grades, which have improved ductility and bendability. These fall into two main groups: Press Quenched Steels (PQS) with approximate tensile strength levels of 450 MPa and 550 MPa (noted as PQS450 and PQS550 in Figure 2) and higher ductility PHS grades with approximate tensile strength levels of 1000 and 1200 MPa (shown as PHS1000 and PHS1200 in Figure 2).
Apart from these grades, other grades are suitable for press hardening. Several research groups and steel makers have offered special stainless-steel grades and recently developed Medium-Mn steels for hot stamping purposes. Also, one steel maker in Europe has developed a sandwich material by cladding PHS1500 with thin PQS450 layers on both sides.

Figure 2: Stress-strain curves of several PQS and PHS grades used in automotive industry, after hot stamping for full hardening* (re-created after Citations B-18, L-28, Z-7, Y-12, W-28, F-19, G-30).
PHS Grades with Tensile Strength Approximately 1500 MPa
Hot stamping as we know it today was developed in 1970s in Sweden. The most used steel since then has been 22MnB5 with slight modifications. 22MnB5 means, approximately 0.22 wt-% C, approximately (5/4) = 1.25% wt-% Mn, and B alloying.
The automotive use of this steel started in 1984 with door beams. Until 2001, the automotive use of hot stamped components was limited to door and bumper beams, made from uncoated 22MnB5, in the fully hardened condition. By the end of the 1990s, Type 1 aluminized coating was developed to address scale formation. Since then, 22MnB5 + AlSi coating has been used extensively.B-14
Although some steel makers claim 22MnB5 as a standard material, it is not listed in any international or regional (i.e., European, Asian, or American) standard. Only a similar 20MnB5 is listed in EN 10083-3.T-26, E-3 The acceptable range of chemical composition for 22MnB5 is given in Table 1.S-64, V-9

Table 1: Chemical composition limits for 22MnB5 (listed in wt.%).S-64, V-9
VDA239-500, a draft material recommendation from Verband Der Automotbilindustrie E.V. (VDA), is an attempt to further standardize hot stamping materials. The document has not been published as of early 2021. According to this draft standard, 22MnB5 may be delivered coated or uncoated, hot or cold rolled. Depending on these parameters, as-delivered mechanical properties may differ significantly. Steels for the indirect process, for example, has to have a higher elongation to ensure cold formability.V-9 Figure 1 shows generic stress-strain curves, which may vary significantly depending on the coating and selected press hardening process.
For 22MnB5 to reach its high strength after quenching, it must be austenitized first. During heating, ferrite begins to transform to austenite at “lower transformation temperature” known as Ac1. The temperature at which the ferrite-to-austenite transformation is complete is called “upper transformation temperature,” abbreviated as Ac3. Both Ac1 and Ac3 are dependent on the heating rate and the exact chemical composition of the alloy in question. The upper transformation temperature for 22MnB5 is approximately 835-890 °C.D-21, H-30Austenite transforms to other microstructures as the steel is cooled. The microstructures produced from this transformation depends on the cooling rate, as seen in the continuous-cooling-transformation (CCT) curve in Figure 3. Achieving the “fully hardened” condition in PHS grades requires an almost fully martensitic microstructure. Avoiding transformation to other phases requires cooling rates exceeding a minimum threshold, called the “critical cooling rate,” which for 22MnB5 is 27 °C/s. For energy absorbing applications, there are also tailored parts with “soft zones”. In these soft zones, areas of interest will be intentionally made with other microstructures to ensure higher energy absorption.B-14

Figure 3: Continuous Cooling Transformation (CCT) curve for 22MnB5 (Published in Citation B-19, re-created after Citations M-25, V-10).
Once the parts are hot stamped and quenched over the critical cooling rate, they typically have a yield strength of 950-1200 MPa and an ultimate tensile strength between 1300 and 1700 MPa. Their hardness level is typically between 470 and 510 HV, depending on the testing methods.B-14
Once automotive parts are stamped, they are then joined to the car body in body shop. The fully assembled body known as the Body-in-White (BIW) with doors and closures, is then moved to the paint shop. Once the car is coated and painted, the BIW passes through a furnace to cure the paint. The time and temperature for this operation is called the paint bake cycle. Although the temperature and duration may be different from plant to plant, it is typically close to 170 °C for 20 minutes. Most automotive body components made from cold or hot formed steels and some aluminum grades may experience an increase in their yield strength after paint baking.
In Figure 4, press hardened 22MnB5 is shown in the red curve. In this particular example, the proof strength was found to be approximately 1180 MPa. After processing through the standard 170 °C – 20 minutes bake hardening cycle, the proof strength increases to 1280 MPa (shown in the black curve).B-18 Most studies show a bake hardening increase of 100 MPa or more with press hardened 22MnB5 in industrial conditions.B-18, J-17, C-17

Figure 4: Bake hardening effect on press hardened 22MnB5. BH0 is shown since there is no cold deformation pre-strain. (re-created after Citation B-18).
There are two modified versions of the 22MnB5 recently offered by several steel makers: 20MnB8 and 22MnSiB9-5. Both grades have higher Mn and Si compared to 22MnB5, as shown in Table 2.

Table 2: Chemical compositions of PHS grades with 1500 MPa tensile strength (all listed in wt.%).V-9
Both of these relatively recent grades are designed for Zn-based coatings and are designed for different process routes. For these reasons, many existing hot stamping lines would require some modifications to accommodate these grades.
20MnB8 has been designed for a “direct process with pre-cooling”. The main idea is to solidify the Zn coating before forming, eliminating the possibility that liquid zine fills in the micro-cracks on the formed base metal surface, which in turn eliminates the risk of Liquid Metal Embrittlement (LME). The chemistry is modified such that the phase transformations occur later than 22MnB5. The critical cooling rate of 20MnB8 is approximately 10 °C/s. This allows the part to be transferred from the pre-cooling stage to the forming die. As press hardened, the material has approximately 1000-1050 MPa yield strength and 1500 MPa tensile strength. Once bake hardened (170 °C, 20 minutes), yield strength may exceed 1100 MPa.K-22 This steel may be referred to as PHS950Y1300T-PS (Press Hardening Steel with minimum 950 MPa yield, minimum 1300 MPa tensile strength, for Pre-cooled Stamping).
22MnSiB9-5 has been developed for a transfer press process, named as “multi-step”. As quenched, the material has similar mechanical properties with 22MnB5 (Figure 5). As of 2020, there is at least one automotive part mass produced with this technology and is applied to a compact car in Germany.G-27 Although the critical cooling rate is listed as 5 °C/s, even at a cooling rate of 1 °C/s, hardness over 450HV can be achieved, as shown in Figure 6.H-27 This allows the material to be “air-hardenable” and thus, can handle a transfer press operation (hence the name multi-step) in a servo press. This material is also available with Zn coating.B-15 This steel may be referred to as PHS950Y1300T-MS (Press Hardening Steel with minimum 950 MPa yield, minimum 1300 MPa tensile strength, for Multi-Step process).

Figure 5: Engineering stress-strain curves of 1500 MPa level grades (re-created after Citations B-18, G-29, K-22)

Figure 6: Critical cooling rates of 1500 MPa level press hardening steels (re-created after Citations K-22, H-31, H-27)
Grades with Higher Ductility
Press hardened parts are extremely strong, but cannot absorb much energy. Thus, they are mostly used where intrusion resistance is required. However, newer materials for hot stamping have been developed which have higher elongation (ductility) compared to the most common 22MnB5. These materials can be used in parts where energy absorption is required. These higher energy absorbing, lower strength grades fall into two groups, as shown in Figure 7. Those at the lower strength level are commonly referred to as “Press Quenched Steels” (PQS). The products having higher strength in Figure 7 are press hardening steels since they contain boron and do increase in strength from the quenching operation. The properties listed are after the hot stamping process.
- 450–600 MPa tensile strength level and >15% total elongation, listed as PQS450 and PQS550.
- 1000–1300 MPa tensile strength level and >5% total elongation, listed as PHS1000 and PHS1200.

Figure 7: Stress-strain curves of several PQS and PHS grades used in automotive industry, after hot stamping for full hardening* (re-created after Citations B-18, Y-12).
Currently none of these grades are standardized. Most steel producers have their own nomination and standard, as summarized in Table 3. There is a working document by German Association of Automotive Industry (Verband der Automobilindustrie, VDA), which only specifies one of the PQS grades. In the draft standard, VDA239-500, PQS450 is listed as CR500T-LA (Cold Rolled, 500 MPa Tensile strength, Low Alloyed). Similarly, PQS550 is listed as CR600T-LA.V-9 Some OEMs may prefer to name these grades with respect to their yield and tensile strength together, as listed in Table 3.
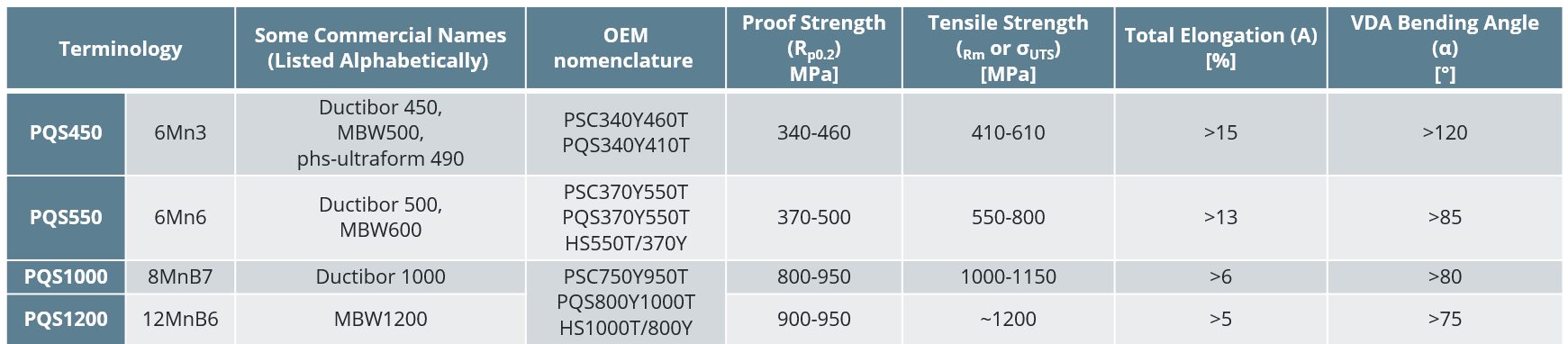
Table 3: Summary of Higher Ductility grades. The terminology descriptions are not standardized. Higher Ductility grade names are based on their properties and terminology is derived from a possible chemistry or OEM description. The properties listed here encompass those presented in multiple sources and may or may not be associated with any one specific commercial grade.Y-12, T-28, G-32
PQS grades have been under development at least since 2002. In the earliest studies, PQS 1200 was planned.R-11 Between 2007 and 2009, three new cars were introduced in Europe, having improved “energy absorbing” capacity in their hot stamped components. VW Tiguan (2007-2016) and Audi A5 Sportback (2009-2016) had soft zones in their B-pillars (Figure 8B and C). Intentionally reducing the cooling rate in these soft zone areas produces microstructures having higher elongations. In the Audi A4 (2008-2016) a total of three laser welded tailored blanks were hot stamped. The soft areas of the A4 B-pillars were made of HX340LAD+AS (HSLA steel, with AlSi coating, as delivered, min yield strength = 340 MPa, tensile strength = 410-510 MPa) as shown in Figure 8A. After the hot stamping process, HX340LAD likely had a tensile strength between 490 and 560 MPaS-65, H-32, B-20, D-22, putting it in the range of PQS450 (see Table 3). Note that there were not the only cars to have tailored hot stamped components during that time.
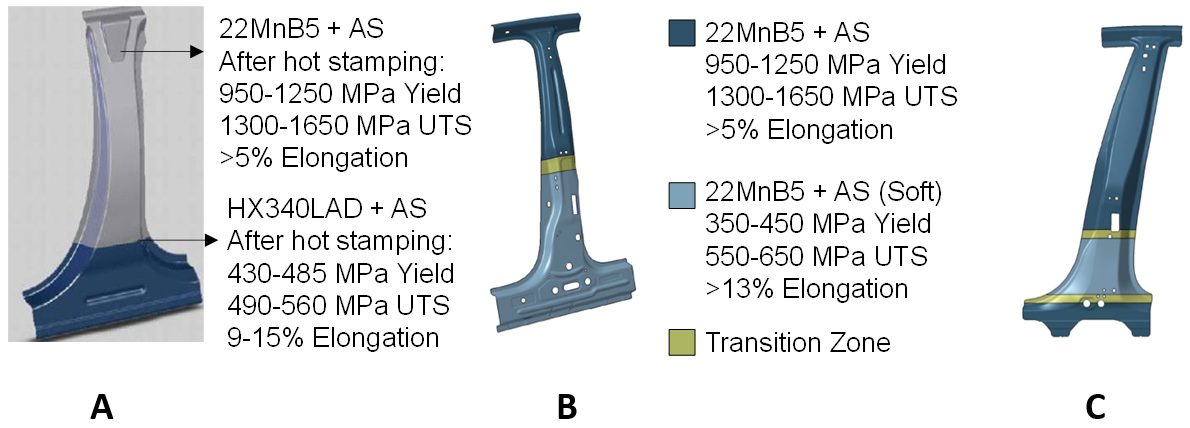
Figure 8: Earliest energy absorbing hot stamped B-pillars: (A) Audi A4 (2008-2016) had a laser welded tailored blank with HSLA material; (B) VW Tiguan (2007-2015) and (C) Audi A5 Sportback (2009-2016) had soft zones in their B-pillars (re-created after Citations H-32, B-20, D-22).
A 2012 studyK-25 showed that a laser welded tailored B-Pillar with 340 MPa yield strength HSLA and 22MnB5 had the best energy absorbing capacity in drop tower tests, compared to a tailored (part with a ductile soft-zone) or a monolithic part, Figure 9. As HSLA is not designed for hot stamping, most HSLA grades may have very high scatter in the final properties after hot stamping depending on the local cooling rate. Although the overall part may be cooled at an average 40 to 60 °C/s, at local spots the cooling rate may be over 80 °C/s. PQS grades are developed to have stable mechanical properties after a conventional hot stamping process, in which high local cooling rates may be possible.M-26, G-31, T-27

Figure 9: Energy absorbing capacity of B-pillars increase significantly with soft zones or laser welded tailored blank with ductile material (re-created after Citation K-25).
PQS grades have been in use at latest since 2014. One of the earliest cars to announce using PQS450 was VolvoXC90. There are six components (three right + three left), tailor welded blanks with PQS450, as shown Figure 10.L-29 Since then, many carmakers started to use PQS450 or PQS550 in their car bodies. These include:
- Fiat 500X: Patchwork supported, laser welded tailored rear side member with PQS450 in crush zonesD-23,
- Fiat Tipo (Hatchback and Station Wagon versions): similar rear side member with PQS450B-14,
- Renault Scenic 3: laser welded tailored B-pillar with PQS550 in the lower sectionF-19,
- Chrysler Pacifica: five-piece front door ring with PQS550 in the lower section of the B-Pillar areaT-29, and
- Chrysler Ram: six-piece front door ring with PQS550 in the lower section of the B-Pillar area.R-3
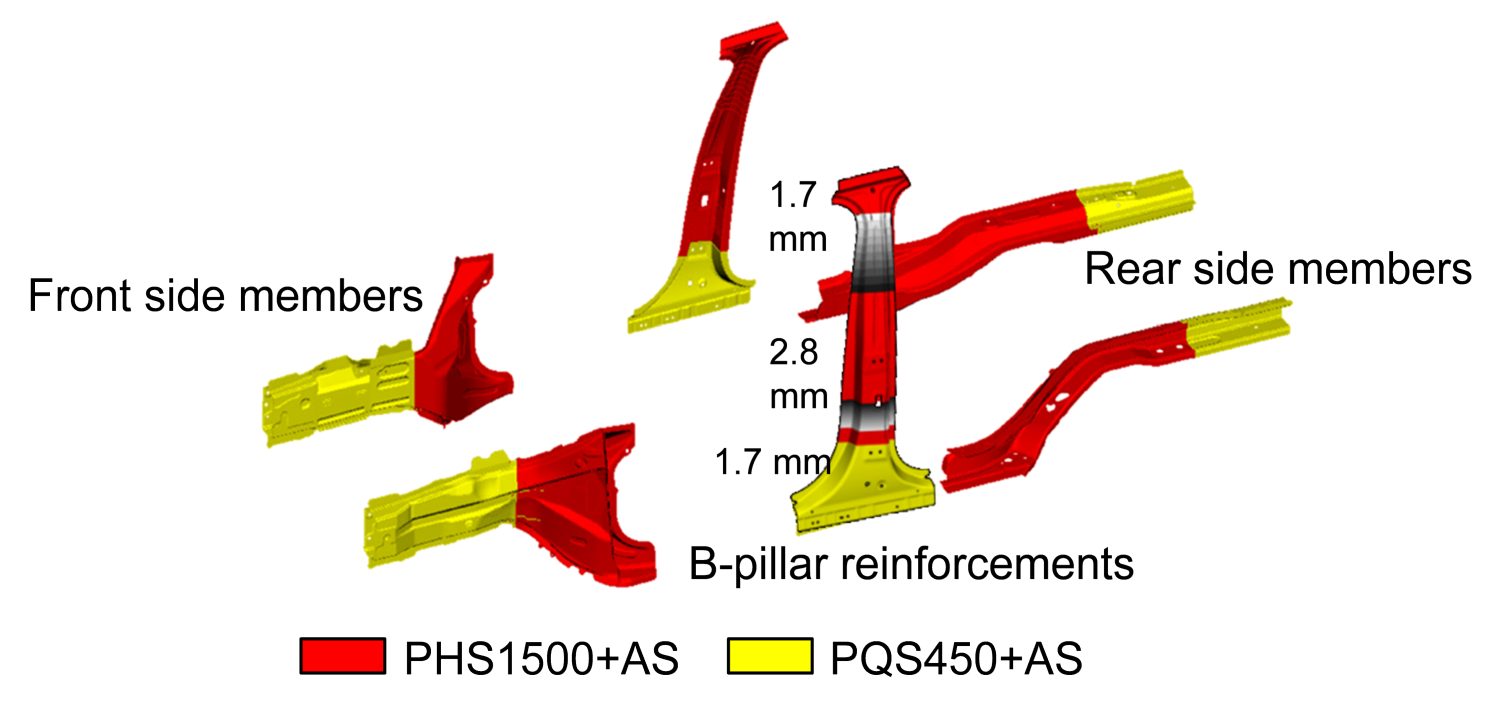
Figure 10: Use of laser welded tailored PQS-PHS grades in 2nd generation Volvo XC90 (re-created after Citation L-29).
Several car makers use PQS grades to facilitate joining of components. The B-Pillar of the Jaguar I-PACE electric SUV is made of PQS450, with a PHS1500 patch that is spot welded before hot stamping, creating the patchwork blank shown in Figure 11A.B-21 Early PQS applications involved a laser welded tailored blank with PHS 1500. Since 2014, Mercedes hot stamped PQS550 blanks not combined with PHS1500. Figure 11B shows such components on the Mercedes C-Class.K-26
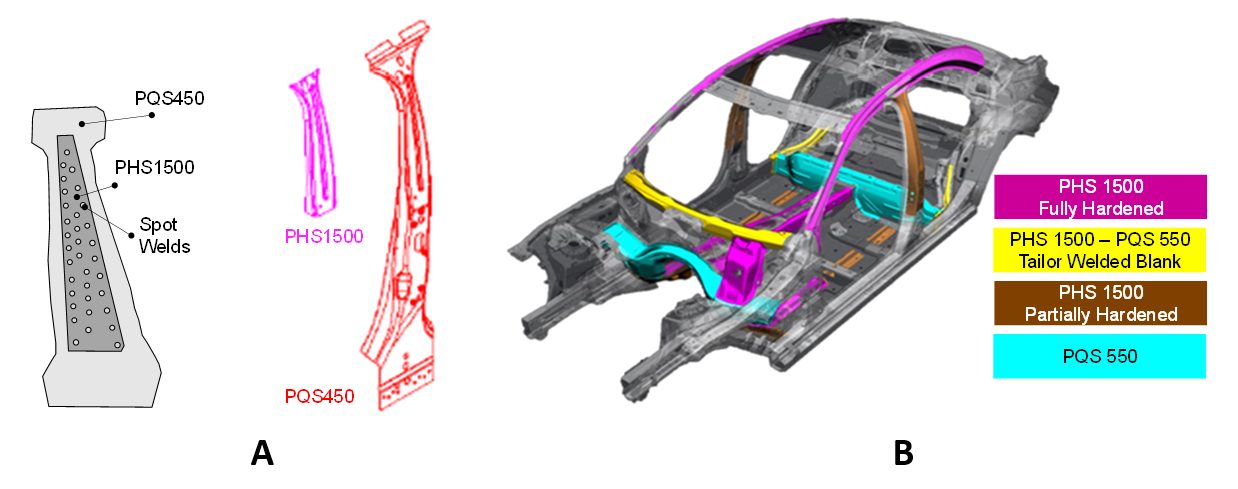
Figure 11: Recent PQS applications: (a) 2018 Jaguar I-PACE uses a patchwork B-pillar with PQS450 master blank and PHS1500 patchB-21, (b) 2014 Mercedes C-Class has a number of PQS550 components that are not laser welded to PHS1500.K-26
PHS Grades over 1500 MPa
The most commonly used press hardening steels have 1500 MPa tensile strength, but are not the only optionsR-11, with 4 levels between 1700 and 2000 MPa tensile strength available or in development as shown in Figure 12. Hydrogen induced cracking (HIC) and weldability problems limit widespread use in automotive applications, with studies underway to develop practices which minimize or eliminate these limitations.
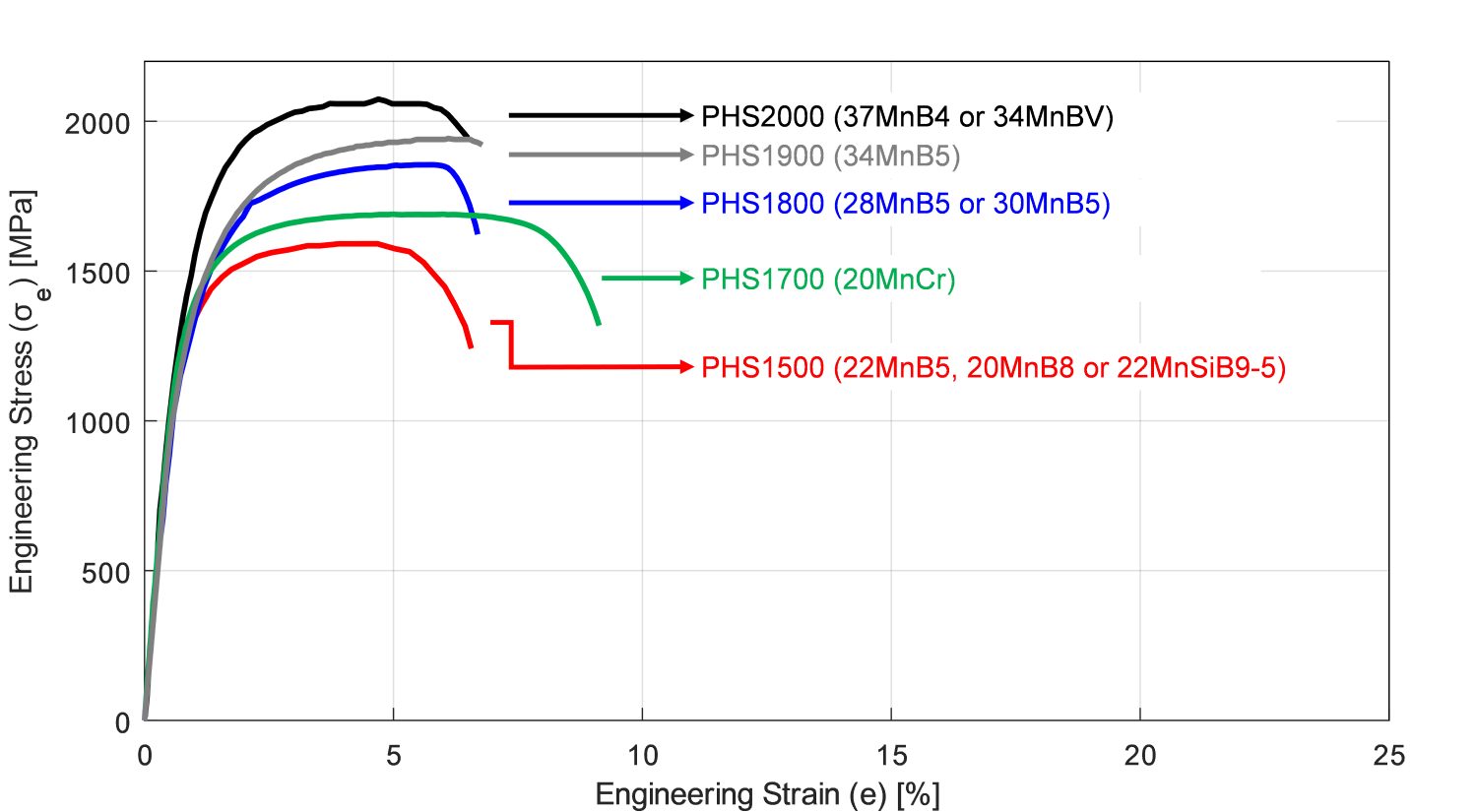
Figure 12: PHS grades over 1500 MPa tensile strength, compared with the common PHS1500 (re-created after Citations B-18, W-28, Z-7, L-30, L-28, B-14).
Mazda Motor Corporation was the first vehicle manufacturer to use higher strength boron steels, with the 2011 CX-5 using 1,800MPa tensile strength reinforcements in front and rear bumpers, Figure 13. According to Mazda, the new material saved 4.8 kg per vehicle. The chemistry of the steel is Nb modified 30MnB5.H-33, M-28 Figure 14 shows the comparison of bumper beams with PHS1500 and PHS1800. With the higher strength material, it was possible to save 12.5% weight with equal performance.H-33

Figure 13: Bumper beam reinforcements of Mazda CX-5 (SOP 2011) are the first automotive applications of higher strength boron steels.M-28

Figure 14: Performance comparison of bumper beams with PHS1500 and PHS1800.H-33
PHS 1800 is used in the 2022 Genesis Electrified G80 (G80EV) and the new G90, both from Hyundai Motor. A specialized method lowering the heating furnace temperature by more than 50℃ limits the penetration of hydrogen into the blanks, minimizing the risk of hydrogen embrittlement. L-64.
MBW 1900 is the commercial name for a press hardening steel with 1900 MPa tensile strength. An MBW 1900 B-pillar with correct properties can save 22% weight compared to DP 600 and yet may cost 9% less than the original Dual-Phase design.H-34 Ford had also demonstrated that by using MBW 1900 instead of PHS 1500, a further 15% weight could be saved.L-30 Since 2019, VW’s electric vehicle ID.3 has two seat crossbeams made of MBW 1900 steel, as seen in Figure 15.L-31 The components are part of MEB platform (Modularer E-Antriebs-Baukasten – modular electric-drive toolkit) and may be used in other VW Group EVs.
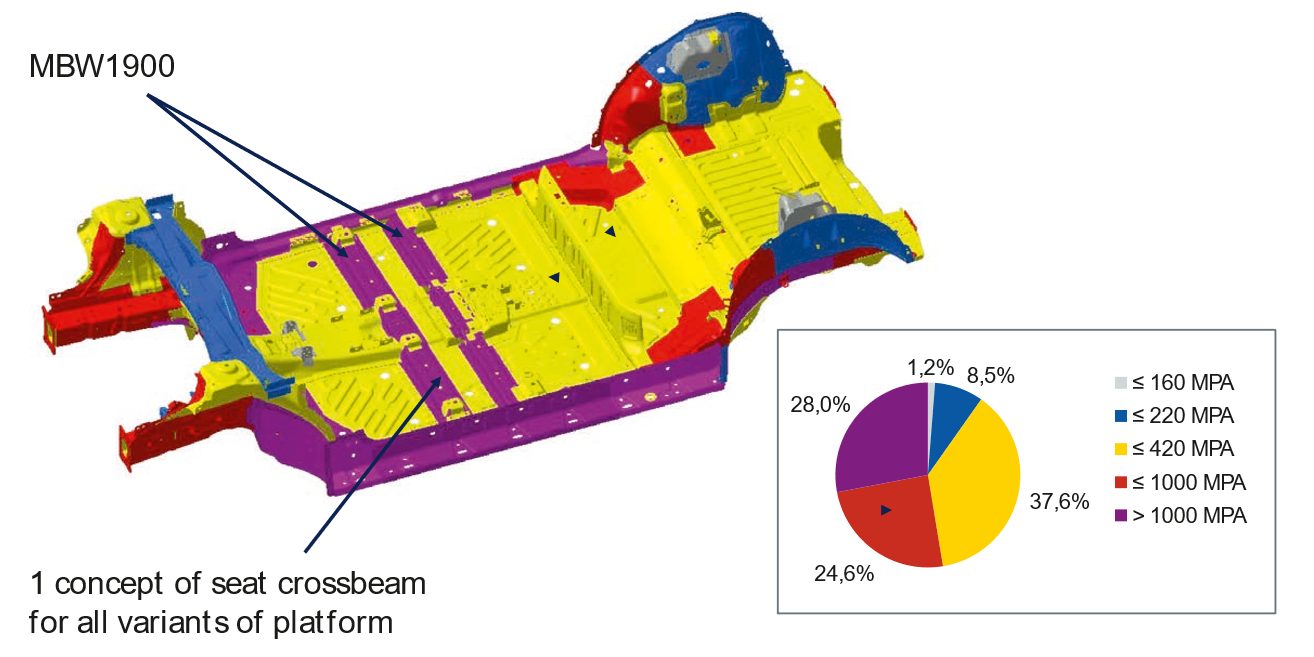
Figure 15: Underbody of VW ID3 (part of MEB platform).L-31
USIBOR 2000 is the commercial name given to a steel grade similar to 37MnB4 with an AlSi coating. Final properties are expected only after paint baking cycle, and the parts made with this grade may be brittle before paint bake.B-32 In June 2020, Chinese Great Wall Motors started using USIBOR 2000 in the Haval H6 SUV.V-12
HPF 2000, another commercial name, is used in a number of component-based examples, and also in the Renault EOLAB concept car.L-28, R-12 An 1800 MPa grade is under development.P-22 Docol PHS 1800, a commercial grade approximating 30MnB5, has been in production, with Docol PHS 2000 in development.S-66 PHS-Ultraform 2000, a commercial name for a Zn (GI) coated blank, is suited for the indirect process.V-11
General Motors China, together with several still mills across the country, have developed two new PHS grades: PHS 1700 (20MnCr) and PHS2000 (34MnBV). 20MnCr uses Cr alloying to improve hardenability and oxidation resistance. This grade can be hot formed without a coating. The furnace has to be conditioned with N2 gas. The final part has high corrosion resistance, approximately 9% total elongation (see Figure 12) and high bendability (see Table 4). 34MnBV on the other hand, has a thin AlSi coating (20g/m2 on each side). Compared with the typical thickness of AlSi coatings, thinner coatings are preferred for bendability (see Table 5).W-28 More information about these oxidation resistant PHS grades, as well as a 1200 MPa version intended for applications benefiting from enhanced crash energy absorption, can be found in Citation L-60.
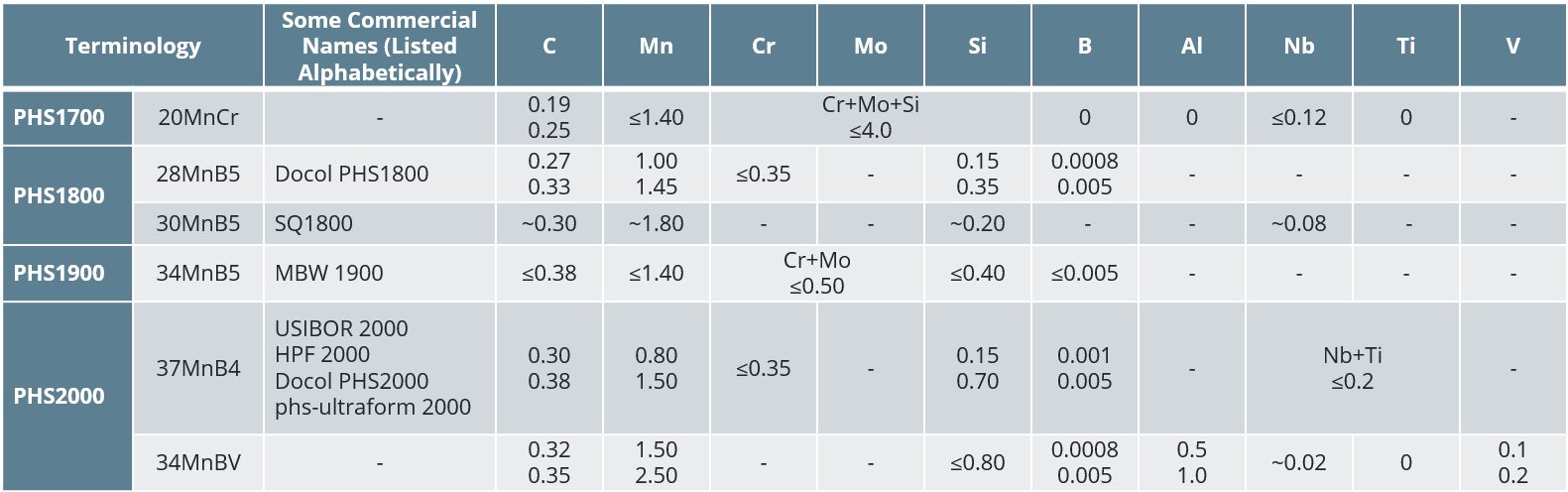
Table 4: Chemical compositions of higher strength PHS grades. “0” means it is known that there is no alloying element, while “-” means there is no information. “~” is used for typical values; otherwise, minimum or maximum are given. The terminology descriptions are not standardized. PQS names are based on their properties and grade names are derived from a possible chemistry or OEM description. The properties listed here encompass those presented in multiple sources and may or may not be associated with any one specific commercial grade.W-28, B-32, H-33, G-33, L-28, S-67, S-66, Y-12, B-33
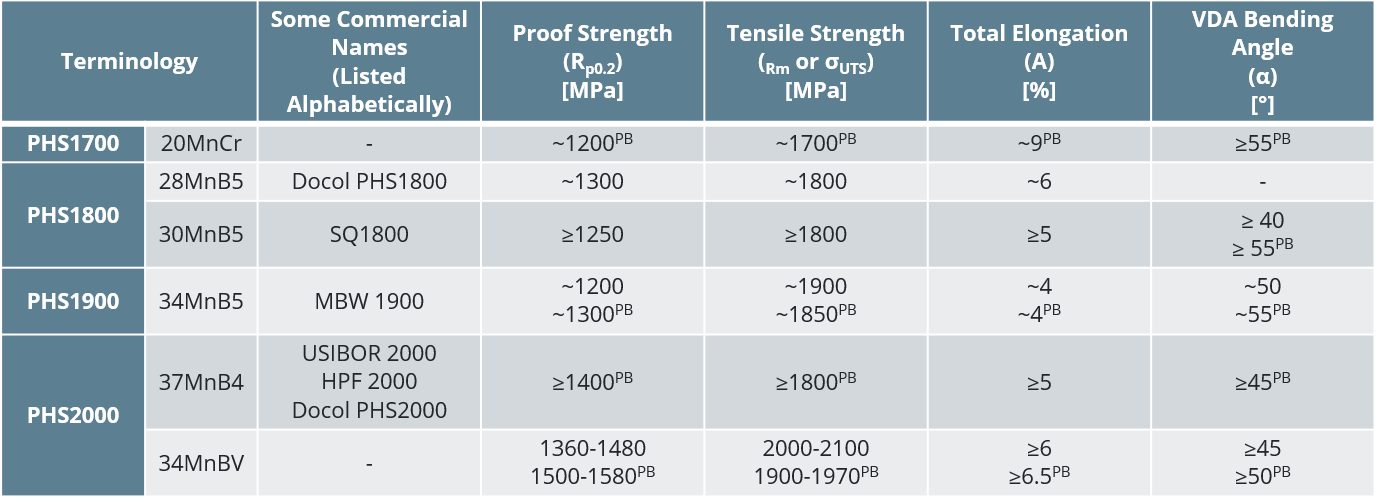
Table 5: Mechanical properties of higher strength PHS grades. “~” is used for typical values; otherwise, minimum or maximum are given. Superscript PB means after paint bake cycle. The terminology descriptions are not standardized. PQS names are based on their properties and grade names are derived from a possible chemistry or OEM description. The properties listed here encompass those presented in multiple sources and may or may not be associated with any one specific commercial grade.W-28, B-32, H-33, G-33, L-28, S-67, S-66, Y-12
Other Steels for Press Hardening Process
In recent years, many new steel grades are under evaluation for use with the press hardening process. Few, if any, have reached mass production, and are instead in the research and development phase. These grades include:
- Stainless steels
- Medium-Mn steels
- Composite steels
Stainless Steels
Studies of press hardening of stainless steels primarily focus on martensitic grades (i.e., AISI SS400 series).M-36, H-42, B-40, M-37, F-30 As seen in Figure 16, martensitic stainless steels may have higher formability at elevated temperatures, compared to PHS1500 (22MnB5). Other advantages of stainless steels are:
- better corrosion resistanceM-37,
- potentially higher heating rates (i.e., induction heating) F-30,
- possibility of air hardening – allowing the multi-step process — as seen in Figure 17a H-42,
- high cold formability – allowing indirect process – as seen in Figure 17b.M-37
Disadvantages include (a) higher material cost, and (b) higher furnace temperature (up to around 1050-1150 °C).M-37, F-30 As of 2020, there are two commercially available stainless steel grades specifically developed for press hardening process.

Figure 16: Tensile strength and total elongation variation with temperature of (a) PHS1500 = 22MnB5M-38 and (b) martensitic stainless steel.M-36

Figure 17: (a) Critical cooling rate comparison of 22MnB5 and AISI SS410 (re-created after Citation H-42), (b) Room temperature forming limit curve comparison of DP600 and modified AISI SS410 (re-created after Citation M-37).
Final mechanical properties of stainless steels after press hardening process are typically superior to 22MnB5, in terms of elongation and energy absorbing capacity. Figure 18 illustrates engineering stress-strain curves of the commercially available grades (1.6065 and 1.4064), and compares them with the 22MnB5 and a duplex stainless steel (Austenite + Martensite after press hardening). These grades may also have bake hardening effect, abbreviated as BH0, as there will be no cold deformation.B-40, M-37, F-30

Figure 18: Engineering Stress-Strain curves of press hardened stainless steels, compared with 22MnB5 (re-created after Citations B-40, M-37, F-30, B-41).

Table 6: Summary of mechanical properties of press hardenable stainless steel grades. Typical values are indicated with “~”. (Table generated from Citations B-40, M-37, F-30.)
Medium-Mn Steels
Medium-Mn steels typically contain 3 to 12 weight-% manganese alloying.D-27, H-30, S-80, R-16, K-35 Although these steels were originally designed for cold stamping applications, there are numerous studies related to using them in the press hardening process as well.H-30 Several advantages of medium-Mn steels in press hardening are:
- Austenitization temperature may be significantly lower than compared to 22MnB5, as indicated in Figure 19.H-30, S-80 Thus, using medium-Mn steels may save energy in heating process.M-39 Lower heating temperature may also help reducing the liquid-metal embrittlement risk of Zn-coated blanks. It also may reduce oxidation and decarburization of uncoated blanks.S-80
- Martensitic transformation can occur at low cooling rates. Simpler dies could be used with less or no cooling channels. In some grades, air hardening may be possible. Thus, multi-step process could be employed.S-80, B-14
- Some retained austenite may be present at the final part, which can enhance the elongation, through the TRIP effect. This, in turn, improves toughness significantly.S-80, B-14

Figure 19: Effect of Mn content on equilibrium transformation temperatures (re-created after Citations H-30, B-14)
The change in transformation temperatures with Mn-alloying was calculated using ThermoCalc software.H-30 As seen in Figure 19, as Mn alloying is increased, austenitization temperatures are lowered.H-30 For typical 22MnB5 stamping containing 1.1 to 1.5 % Mn, furnace temperature is typically set at 930 °C in mass production. The multi-step material 22MnSiB9-5 has slightly higher Mn levels (2.0 to 2.4 %), so the furnace temperature could be reduced to 890 °C. As also indicated in Table 7, the furnace temperature could be further lowered in hot forming of medium-Mn steels.
A study in the EU showed that if the maximum furnace temperature is 930 °C, which is common for 22MnB5, natural gas consumption will be around 32 m3/hr. In the study, two new medium-Mn steels were developed, one with 3 wt.% Mn and the other with 5 wt% Mn. These grades had lower austenitization temperature, and the maximum furnace set temperature could be reduced to 808 °C and 785 °C, respectively. Experimental data shows that at 808 °C natural gas consumption was reduced to 19 m3/hr, and at 785 °C to 17 m3/hr.M-39 In Figure 20, experimental data is plotted with a curve fit. Based on this model, it was estimated that by using 22MnSiB9-5, furnace gas consumption may be reduced by 15%.

Figure 20: Effect of maximum furnace set temperature (at the highest temperature furnace zone) on natural gas consumption (raw data from Citation M-39)
Lower heating temperature of medium-Mn steels may also help reducing the liquid-metal embrittlement risk of Zn-coated blanks. It also may reduce oxidation and decarburization of uncoated blanks.S-80
Medium-Mn steels may have high yield-point elongation (YPE), with reports of more than 5% after hot stamping. Mechanical properties may be sensitive to small changes in temperature profile. As seen in Figure 21, all studies with medium-Mn steel have a unique stress-strain curve after press hardening. This can be explained by:
- differences in the chemistry,
- thermomechanical history of the sheet prior to hot stamping,
- heating rate, heating temperature and soaking time, and
- cooling rate.S-80

Figure 21: Engineering Stress-Strain curves of several press hardened medium-Mn steels, compared with 22MnB5. See Table 7 for an explanation of each tested material (re-created after Citations S-80,L-37, W-30, L-38).

Table 7: Summary of mechanical properties of press hardenable Medium-Mn grades shown in Figure 18. Typical values are indicated with “~”. Toughness is calculated as the area under the engineering stress-strain curve. Items 4 and 5 also were annealed at different temperatures and therefore have different thermomechanical history. Note that these grades are not commercially available.L-38, W-30, L-37, S-80
Composite Steels
TriBond ® is the name given to a family of steel composites.T-32 Here, three slabs (one core material (60 to 80% of the thickness) and two cladding layers) are surface prepared, stacked on top of each other, and welded around the edges. The stack is hot rolled to thickness. Cold rolling could also be applied. Initially, TriBond ® was designed for wear-resistant cladding and ductile core materials.
The original design was optimized for hot stamping.B-14 The core material, where bending strains are lower than the outer layers, is made from generic 22MnB5 (PHS1500). Outer layers are made with PQS450. The stack is cold rolled, annealed and AlSi coated.Z-9 Two grades are developed, differing by the thickness distribution between the layers, as shown in Figure 22.R-14

Figure 22: Sample microsections of the conventional hot stamping grade PHS1500+AS, the high strength composite Tribond® 1400 and the high energy absorbing composite Tribond® 1200. The Tribond® 1200 microsection is experimental and is taken from Citation R-14. The other two images are renditions created by the author for explanation purposes. (re-created after Citations R-14, R-15)
Total elongation of the composite steel is not improved, compared to PHS1500, as shown in Figure 23. The main advantage of the composite steels is their higher bendability, as seen in Table 8. Crashboxes, front and rear rails, seat crossmembers and similar components experience axial crush loading in the event of a crash. In axial crush, Tribond® 1200 saved 15% weight compared to DP780 (CR440Y780T-DP). The bending loading mode effects B-pillars, bumper beams, rocker (sill) reinforcements, side impact door beams, and similar components during a crash. In this bending mode, Tribond® 1400 saved 8 to 10% weight compared to regular PHS1500. Lightweighting cost with Tribond® 1400 was calculated as €1.50/kgsaved.G-37, P-26

Figure 23: Engineering Stress-Strain curves of core layer, outer layer and the composite steel (re-created after Citation P-26).

Table 8: Summary of composite steels and comparison with conventional PHS and PQS grades. Typical values are indicated with “~”. (Table re-created after Citation B-14).
* Graphs in this article are for information purposes only. Production materials may have different curves. Consult the Certified Mill Test Report and/or characterize your current material with an appropriate test (such as a tensile, bending, hole expansion, or crash test) test to get the material data pertaining to your current stock.
For more information on Press Hardened Steels, see these pages:
Back To Top
Forming, Press Hardened Steels
PHS and PQS Overview
A Brief Overview of Press Hardening
Press hardening (also commonly known as hot stamping or hot press forming) combines forming and heat treatment technology to create high strength complex shapes. Elevated temperature allows for production of complex shapes. This can be achieved by 10 different processes. To summarize:
- Forming from the “as delivered” ferritic-pearlitic microstructure (i.e., at ❶ in Figure 1). The formed part is later heated in a special furnace and quenched in a cooled press die. This process is commonly known as “Indirect Hot Stamping”, “Form Hardening” or “Post Form Heat Treatment”.
- Forming after heating a blank to over 880 °C to create an austenitic microstructure (i.e., at ❷ in Figure 1). The process is known as “Direct Hot Stamping”, “Press Hardening” or “Hot Press Forming”.
Selection of the process type usually depends on the coating and part complexity.
In press hardening, the required press forces are relatively low – compared to the final part strength – and springback is significantly reduced, if not eliminated. The parts get their final properties during the quenching cycle. In Press Hardening, OEMs require the final mechanical properties within the formed part to be guaranteed by the part supplier. In contrast, in cold stamping, the mechanical properties of the incoming sheet steel must be guaranteed by the steel supplier.
If the cooling rate is faster than the critical cooling rate of the steel, the final microstructure will be almost fully martensitic producing what is called the “Full Hard” (FH) condition. Depending on a part design, “soft zones” may be required. In this case, the heat treatment is controlled such that the soft zones have other phases such as bainite and in some cases ferrite and pearlite. The process of tailoring the microstructure distribution is called as “tailored tempering” or “tailored properties”. Parts with tailored properties may be described as a “multi-strength part” or a “tailored-part”.
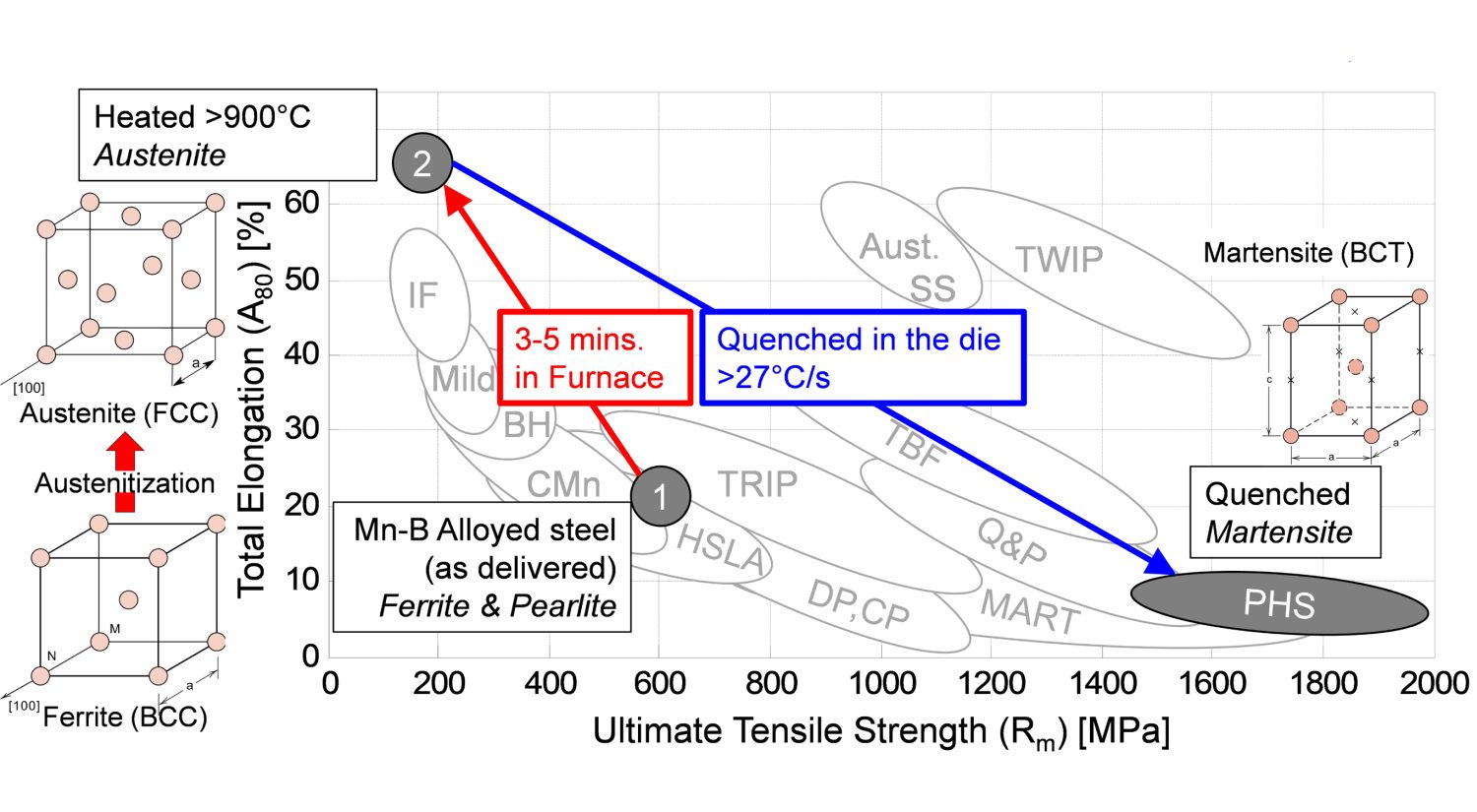
Figure 1: A short summary of press hardening process (re-created after B-14).
Press hardening steels use carbon and manganese, with boron for additional hardenability. They have been used in the automotive industry since 1980s, however their use has increased significantly in the last two decades. There are mainly three groups of PHS grades:
- PHS1500 (see PHS Grades with TS approximately 1500 on link page): refers to the first and most commonly used PHS grade 22MnB5 or the recently developed grades like 20MnB8 used in the “pre-cooled direct process” or the air-hardening 22MnSiB9-5 used in the “multi-step process.” These grades have approximately 1,500 MPa (typical range: 1300-1650 MPa) tensile strength after quenching.
- Higher elongation grades – with some also known as Press Quenched Steels (PQS): PQS450, PQS550, PHS1000, and PHS1200 (see the section on Grades With Higher Ductility on the linked page): these grades have high elongation and/or bending angle after quenching. Tensile strength should range from 450 MPa to 1,300 MPa after the hot stamping process.
- Higher strength grades: PHS1800 and PHS2000 (see PHS Grades with TS over 1500 on link page): these grades have tensile strength of 1,800 MPa to 2,000 MPa after quenching.
- Emerging grades (see Other grades for press hardening process on link page for this and the stainless link following), such as Medium-Mn steels, and even some types of stainless steels are suitable for the hot stamping process.
Other PHS Pages in these Guidelines:
Press Hardened Steels – Metallurgy
PHS Production Methods
PHS Simulation
PHS Tailored Products
PHS Automotive Applications and Usage
Tailored Products
topofpage
Types of Tailored Products
Key materials characteristics for formed parts include strength, thickness, and corrosion protection. Tailored products provide opportunities to place these attributes where they are most needed for part function, and remove weight that does not contribute to part performance.
Welded Tailored Blanks (Tailor Welded Blanks)
Welded tailored blanks are a type of tailored product, as are patchwork blanks, tailor welded coils, tailor rolled coils, tailor rolled tubes and tailor welded tubes.
Laser welding is the most common approach to creating these products, but other options like resistance mash seam welding are possible. Mash seam welding requires that the blanks overlap, which adds mass. The heat affected zone (HAZ) for mash seam welds is considerably larger than that of laser welds. Compared with laser welding, the temperature reached when resistance mash seam welding is lower. This may improve formability due to reduced martensite formation, but the larger HAZ and thicker joint may negate this benefit. Non-linear welds are more challenging to produce with the mash seam approach. Welded Tailored Blanks refers to blanks made via either laser welding or mash seam welding. The following discussion centers on blanks and coils joined by lasers.
Butt-welding two or more flat sheets into a single blank creates a laser welded tailored blank (LWTB), also known as a tailor welded blank or laser welded blank (LWB). Steel grades and thickness may be (and usually are) different in the component sheets. Corrosion protection strategies may be different on each component of the welded blank. “Sub blanks” is another name for these component sheets.
Figure 1 shows a laser welded door ring with multiple grades and thicknesses. This technology allows for a reduction in panel thickness in non-critical areas, thus contributing to an overall mass reduction of the part. The lower strength product in the bottom section of the B-Pillar helps dissipate the crash energy in the event of a side impact, playing a key role in crash energy management.
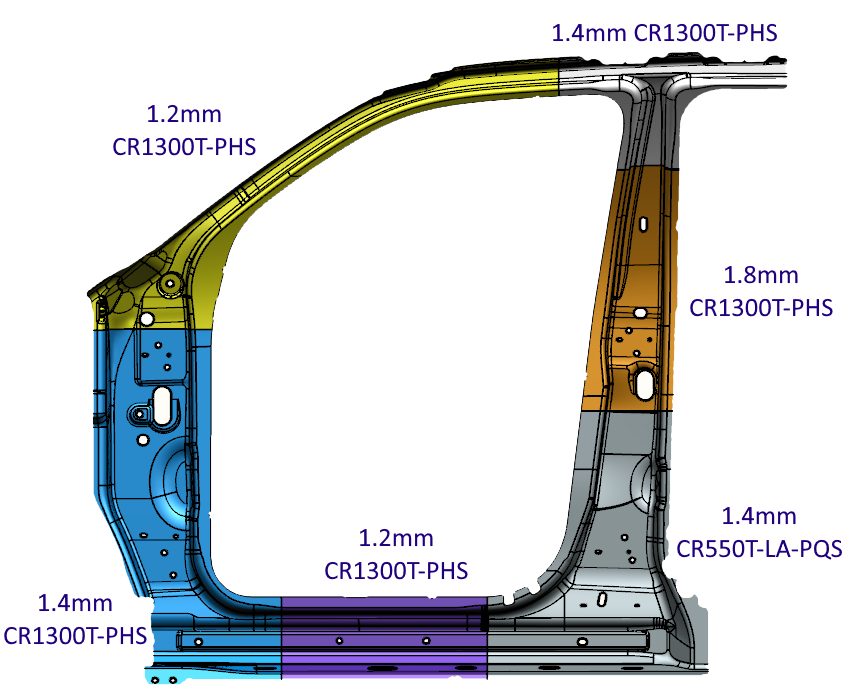
Figure 1: Six-piece Laser Welded Tailored Blank with multiple grades and thickness.R-3
Patchwork Blank
An alternate approach to a laser welded tailored blank involves the creation of what is known as a patchwork blank, consisting of two or more blanks potentially having different thickness or grades. The unique characteristic is that the blanks are placed one on top of the other and (typically) spot welded together while still flat. The patched blank requires only one stamping operation, eliminating the need to join them after forming the components separately. This approach is satisfactory for both cold stamping and hot stamping. The correct number of spot-welds is important in terms of cost and safety. Furthermore, if the components shift relative to one another during the forming operation, the spot welds may shear. There is excellent fit between both parts after forming, allowing for easy application of additional spot welds if needed. Part size, the number and location of reinforcements, and available infrastructure are among the key considerations in deciding between a laser welded or patch blank approach. For example, patchwork blanks may be preferred if the reinforced area is relatively small with complex contours or located within the boundaries of the main blank.
Tailor Welded Coils
Rather than building blanks from individual components, a similar approach is to join entire coils together, edge to edge. These tailor welded coils (Figure 2) are used in coil-fed processes such as blanking, progressive die stamping, transfer press stamping, and roll forming operations. The basic process takes separate coils, prepares their edges for contiguous joining, and laser welds these together into one master coil. The new strip is either directly blanked or re-coiled for future blanking or use as feedstock for a continuous coil-fed stamping or roll forming line (Figure 3). Variations in strength, thickness, and coating occur across the width.
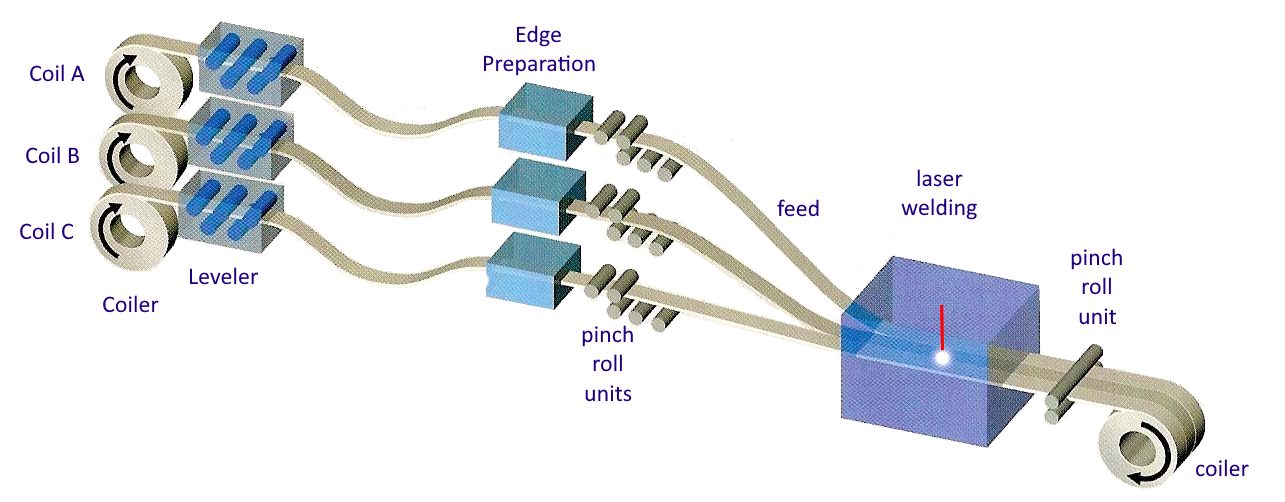
Figure 2: Production Process of Tailor Welded Coils.S-28
![Figure 3: General usage of Tailor Welded Coils [S-28]](https://ahssinsights.org/wp-content/uploads/2020/07/tailor-welded-cole-common-use.jpg)
Figure 3: General usage of Tailor Welded Coils.S-28
Tailor Rolled Coils
Whereas tailor welded coils can vary in properties across the coil width, tailor rolled coils have variable thickness down the length of the coil. Production facilities for tailor rolled coils vary the gap between the rolls used for thickness reduction, allowing for different strip thicknesses in the direction of rolling (Figure 4). Accurate measuring and feedback control technology guarantees the strip thickness tolerances. A significant advantage to this approach results from the transition from one thickness to another with no joints or discontinuities, providing an efficient load path without stress risers. A tailor rolled coil can be either used for blanking operations (for stamping or tubular blanks), or as feedstock into a roll forming line.
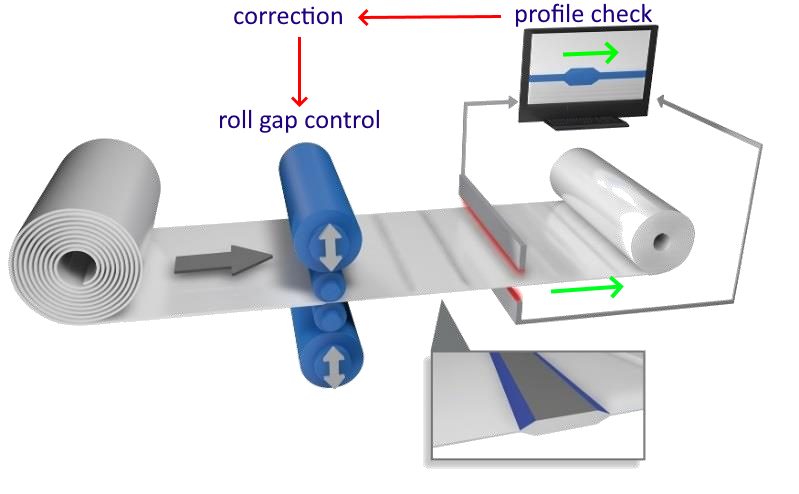
Figure 4: Tailor Rolled Coils vary in thickness down the length of the coil.Z-5
After cold rolling to achieve the targeted thickness variation, coils are annealed to reset the mechanical properties. Tensile properties can be uniform in the blank, with only the thickness varying. Tailored properties are generated by adjusting the incoming coil thickness and the associated thickness reductions, leading to different degrees of recrystallization occurring in the annealing step.Z-14 TRBs used in press hardening do not need to be annealed first, and tailored properties can be produced with the appropriate PHS process.
Tailor Rolled Tubes
Tailor rolled coils are the feedstock to produce variable thickness tailor rolled tubes.
Tailor Welded Tubes
Conventional tube production involves roll forming strips to the desired shape and welding the free ends together to create a closed section. A tailor welded tube production process allows the designer to create complex variations in shape, thickness, strength, and coating (Figure 5)

Figure 5: Tailored tube production allows for differing thickness and strength within the same tube. A) 1-piece cylindrical tube with monolithic properties; B and C) 2-piece tailored tube with property variation down the length of the tube; D) 1-piece conical tube; E) 2-piece conical tube with a patchwork blank.
With hydroforming technology, the next step in tubular components is to bring the sheet metal into a shape closer to the design of the final component without losing tailored blank features (Figure 6).
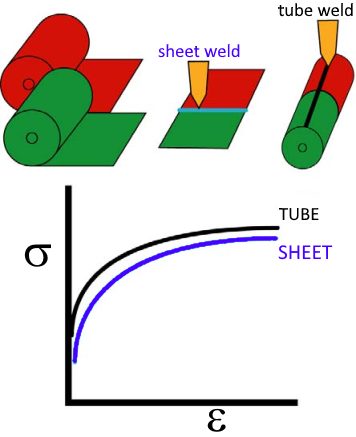
Figure 6: Mechanical properties of tailored tubes are close to the original metal properties in the sheet condition. Hydroforming changes the properties based on the local deformation.G-8
Hydroformed conical tailored tubes offer automotive body engineers an additional approach to crash energy management while achieving a lightweight design. In frontal crash and side impacts the load paths have a key importance on the body design as they have a major bearing on the configuration of the structural members and joints. Figure 7 shows an example of a front-rail hydroformed prototype. The conical tailored tubes for this purpose take advantage of the high work hardening potential of TRIP steel.
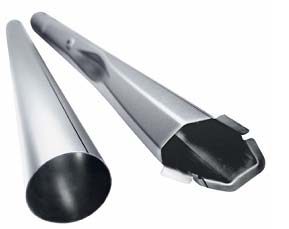
Figure 7: Front-rail prototype based on a conical tube having 40 mm end to end difference in diameter.F-3
Benefits of Tailored Products in Automotive Body Construction
Figure 8 highlights some of the areas within the body structure where companies have considered transitioning to welded tailored blanks. Other tailored products may be suitable in other areas.
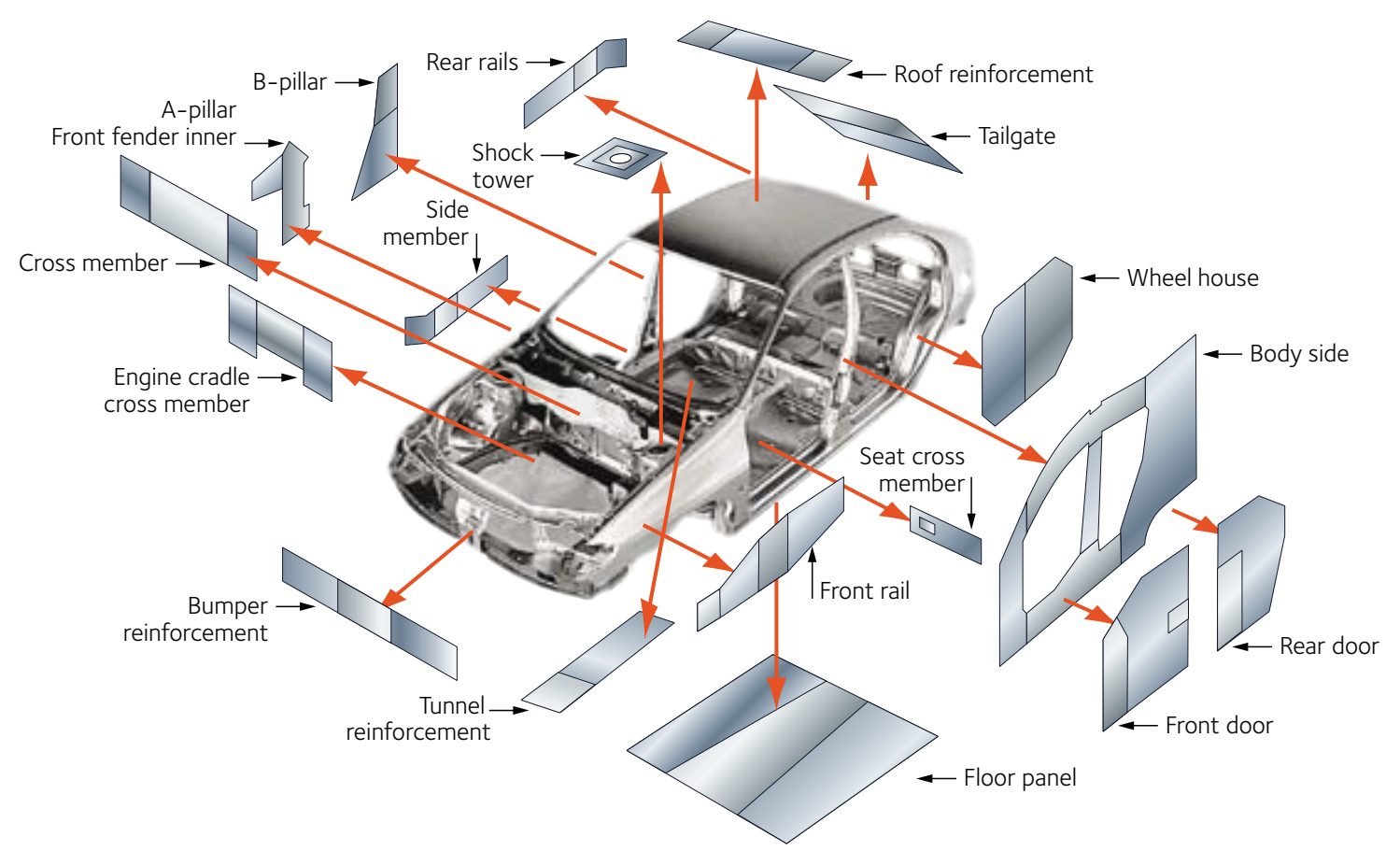
Figure 8: Applications suited for welded tailored blanks.A-31
Tailored products offer numerous advantages over the conventional approach involving the stamping and assembly of individual monolithic blanks which have a single grade, thickness, and coating, including:
Improved materials utilization
- Certain parts, like door rings (Figure 1), window frames, and door inner panels, have large cutout areas contributing to engineered scrap. Converting these to welded tailored blanks allows for optimized nesting of the individual components. Figure 9 presents an example of optimized nesting associated with body side aperture designs using a tailor welded blank. Reduced blank width requirements may allow for additional suppliers or use of master coils yielding slit mults. In the other extreme, blank dimensions larger than rolling mill capabilities are now feasible.
Elimination of reinforcement parts and reduced manufacturing infrastructure requirements
- In areas needing additional thickness for stiffness or crash performance, conventional approaches require stamping both the primary part and an additional smaller reinforcement and then spot welding the two parts together. The tailored product directly incorporates the required strength and thickness. Compared with a tailored product, the conventional approach requires twice the stamping time and dunnage, creates inventory, and adds the spot welding operation. Tolerance and fit-up issues appear when joining two formed parts, since their individual springback characteristics must be accommodated.
Part consolidation
- Similar to the benefits of eliminating reinforcements, tailored products may combine the function of what would otherwise be multiple distinct parts which would need to be joined.
Weight savings
- Conventional approaches to body-in-white construction requires individual parts to have flat weld flanges to facilitate spot welding. Combining multiple parts into a tailored product removes the need for weld flanges, and their associated weight.
Improved NVH, safety, and build quality
- Joining formed parts is more challenging than joining flat blanks first and then stamping. Tailored products have better dimensional integrity. Elimination of spot welds leads to a reduction in Noise, Vibration, and Harshness (NVH). A continuous weld line in tailored products means a more efficient load path.
Enhanced engineering flexibility
- Using tailored products provides the ability to add sectional strength in precise locations to optimize body structure performance.
Easily integrated with advanced manufacturing technologies for additional savings
- Tailored products incorporated into hot stamping or hydroforming applications magnify the advantages described here, and open up additional benefits.
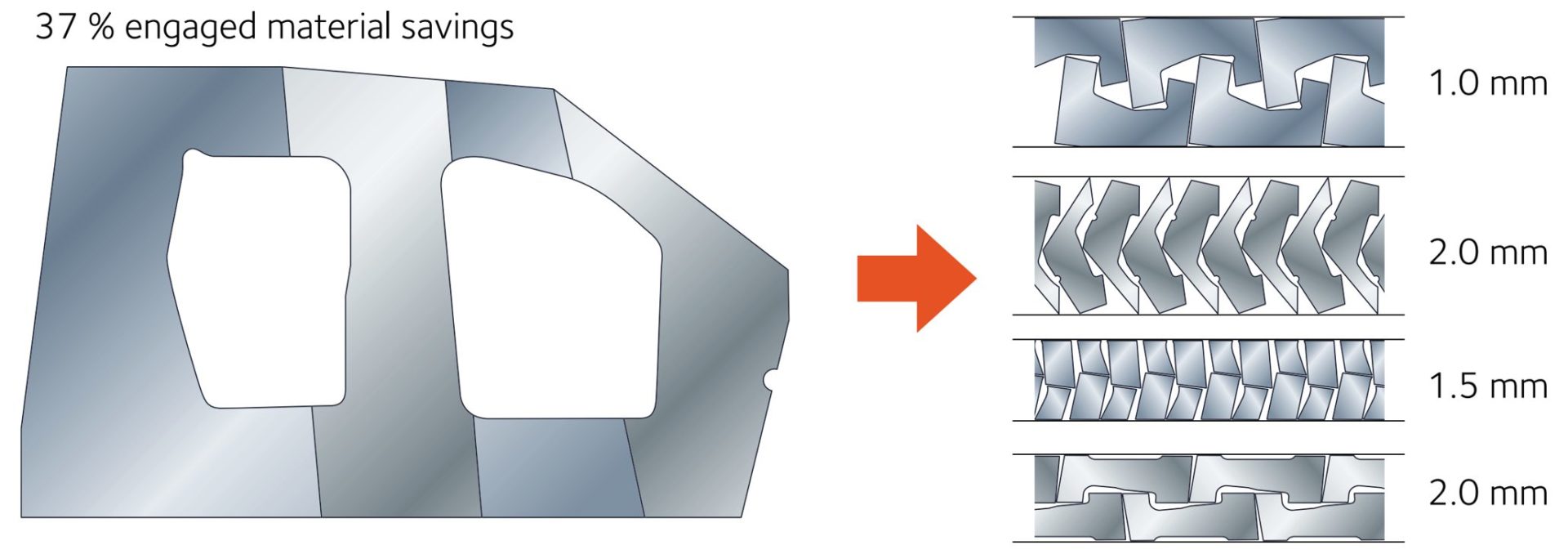
Figure 9: Nesting optimization dramatically reduces engineered scrap.A-31
Design, Usage, and Troubleshooting Guidance
Edge Quality of Component Blanks Used to Create the Welded Blank
Minimal burr, maximized sheared edge stretchability, and maximized tool life are characteristics of good sheared edge quality in conventional blanking operations. When creating sub-blanks for assembly into a laser welded tailored blank, there is an additional critical characteristic: squared edges with high straightness are a prerequisite to avoid local gaps between the blank edges causing undercut in the weld bead and the associated loss of mechanical properties (Figure 10). Conventional shearing operations produce the edge seen in Figure 10a. Precision die blanking with tight clearances, as well as laser blanking, produce edges suitable for the blank welding operation (Figure 10b). Another option is to use a conventional shearing approach to produce a slightly oversize blank, and then use precision shears as the first step in the laser welding line. The advantage to this approach minimizes the impact of edge damage which might occur during transportation.
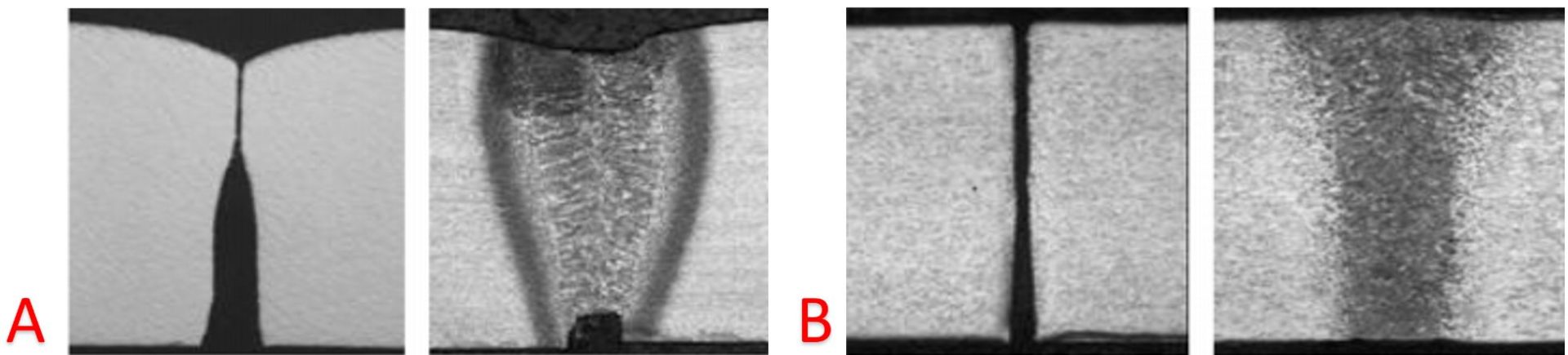
Figure 10: Edge condition and welding result. A) Poor edge resulting in increased residual butt gap and weld undercut; B) Optimum squared edge by precision die blanking or laser welding resulting in flush weld surfaces.S-29
Forming analysis of Welded Blanks
The weld joint and adjacent heat affected zone complicates the forming analysis of welded blanks. There are generally two scenarios that occur: failure perpendicular to the weld and failure parallel to the weld (Figure 10).
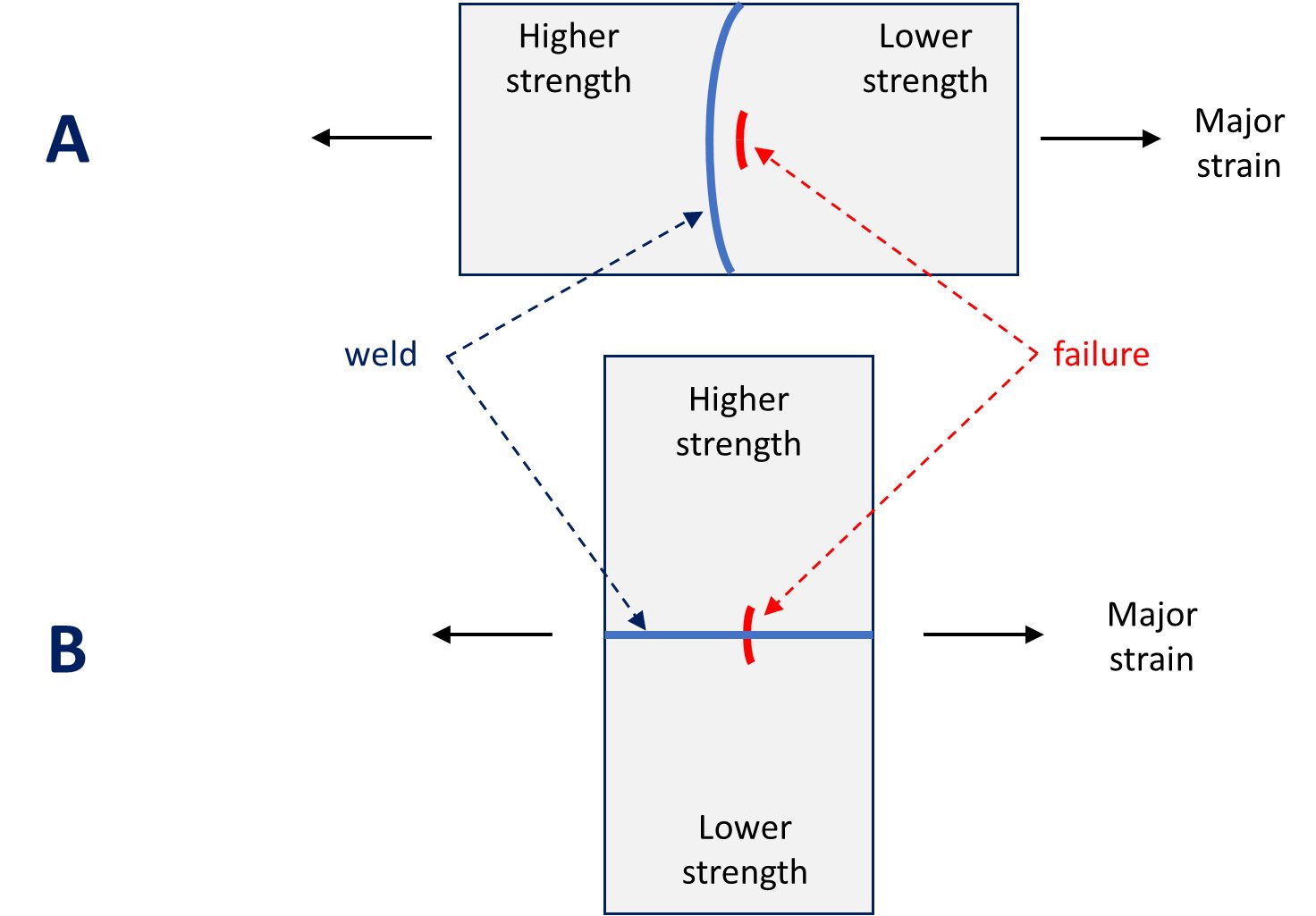
Figure 11: Major strain axis relative to weld line orientation. A) Weld line is perpendicular to the major strain axis; B) Weld line is parallel to the major strain axis.
Consider the scenario in Figure 11A, where the major strain is perpendicular to the weld line orientation. Failure occurs parallel to the weld in the lower strength, more ductile material. The restraining force provided by the higher strength material results in the weld line shifting towards that side.
With the weld seam moving towards the thicker and stronger metal, deformation occurs in thinner and weaker metal. The movement of the weld seam during stamping requires that a blankholder design with appropriate clearances so the welds can move through the blankholder during the drawing process. The punch-cavity clearances must allow for movement as well – otherwise a pinch-point is created and metal flow stops. These clearances are necessary for movement of the heavier gauge metal and the welds, but can also be a source of wrinkling on the lighter gauge side due to the lack of hold-down force in this area. Also, the potential exists for die wear in the locations in contact with weld seam. To counter the weld line motion to the higher strength side, consider allowing greater material flow from that side of the weld through a less severe draw bead design, reduced blankholder pressure or modified blank outline. These strategies help minimize the risk of this type of split.
Now consider the scenario in Figure 11B, where the major strain is parallel to the weld line orientation. Here, fracture occurs perpendicular to the weld line – typically within the weld itself – due to the poorer mechanical properties of the weld with respect to the base material. To avoid splits in the weld, orient the weld away from the major strain direction and away from areas with high strain concentration.
Use of Advanced High Strength Steels in Laser Welded Tailored Products
As sub-blanks are welded together to create the main blank, the beginning or ending of each of the weld lines are not in a steady state condition. As such, the start or stop action of the welding may create a stress riser. After the main blank is built-up, a scalloped cut can remove the affected areas so that only sections of uniform edge quality are formed in subsequent operations.
Laser welding is a high energy density process that focuses the heat in a very localized region as the laser travels at a high speed. This results in a narrow heat affected zone and the rapid quenching leads to the formation of a high-hardness martensite. Increased welding speeds generally require higher energy intensity at the weld which increases peak hardness.
Different welding parameters must be used for advanced high strength steels due to the presence of martensite in the base metal. The microstructure in the heat affected zone is a function of the local time/temperature profile, which changes with distance away from the weld as well as with the composition of the alloy in question. Laser welding some AHSS grades results in tempered martensite in the heat affected zone, leading to a locally softened region. Crash modeling should incorporate the influence of the softened region, which may help dissipate a portion of the crash energy.
However, this softened region creates an area for high strain concentration, leading to premature failure in martensite-containing AHSS grades. Higher strength dual phase steels have more martensite than lower strength dual phase grades, and therefore are more likely to generate HAZ soft zones and reduced formability when used in laser welded blanks. CP and TRIP steels have a lower incidence of HAZ soft zones due to higher alloying content. More information about laser welding is found here.
Blank Stacking, Destacking, and Feeding Problems
Depending on the thickness differences between the component blanks and their relative sizes, embossed dimples on the thinner gauge side can balance the thickness difference and to allow stable coil winding (in the case of tailor welded coil production) or stacking as they are blanked onto a lift. The stack weight and banding of the pallets may contribute to collapsing the dimples, so some companies choose to minimize the stack height.
Automatic destackers and feeders typically require uniform blanks and stacks for trouble-free operation. Dimples and cutouts may interfere with proper operation of overhead vacuum cups or magnetic belts. Moving or deactivating Vacuum cups may be necessary. Dimples should either be outside of the magnetic belt area or have their form away from the belt. Dimples may be a problem for some in-line blank washers and die-lube roll coaters.
Press and Tooling Considerations
When there is a large thickness difference within the component blanks, press tonnage and balance can be a problem. Press tonnage monitors are essential for this type of part, not only for protection of the press equipment, but also for good process control. If press balance is a problem, the tonnage monitors will indicate where the problem is. Supplemental balance devices in the die, such as nitrogen cylinders, may be appropriate, or the stamping may need to move to a larger press.
Tailored products often contain sub-blanks of mixed strength and thickness. The chosen die process must reflect those differences, and account for changes in side-wall curl, springback and drawability characteristics across the part. Mild steel can usually be formed with high strength steel die processes, but high strength steel will not always form satisfactorily with conventional die processes used with mild steels.
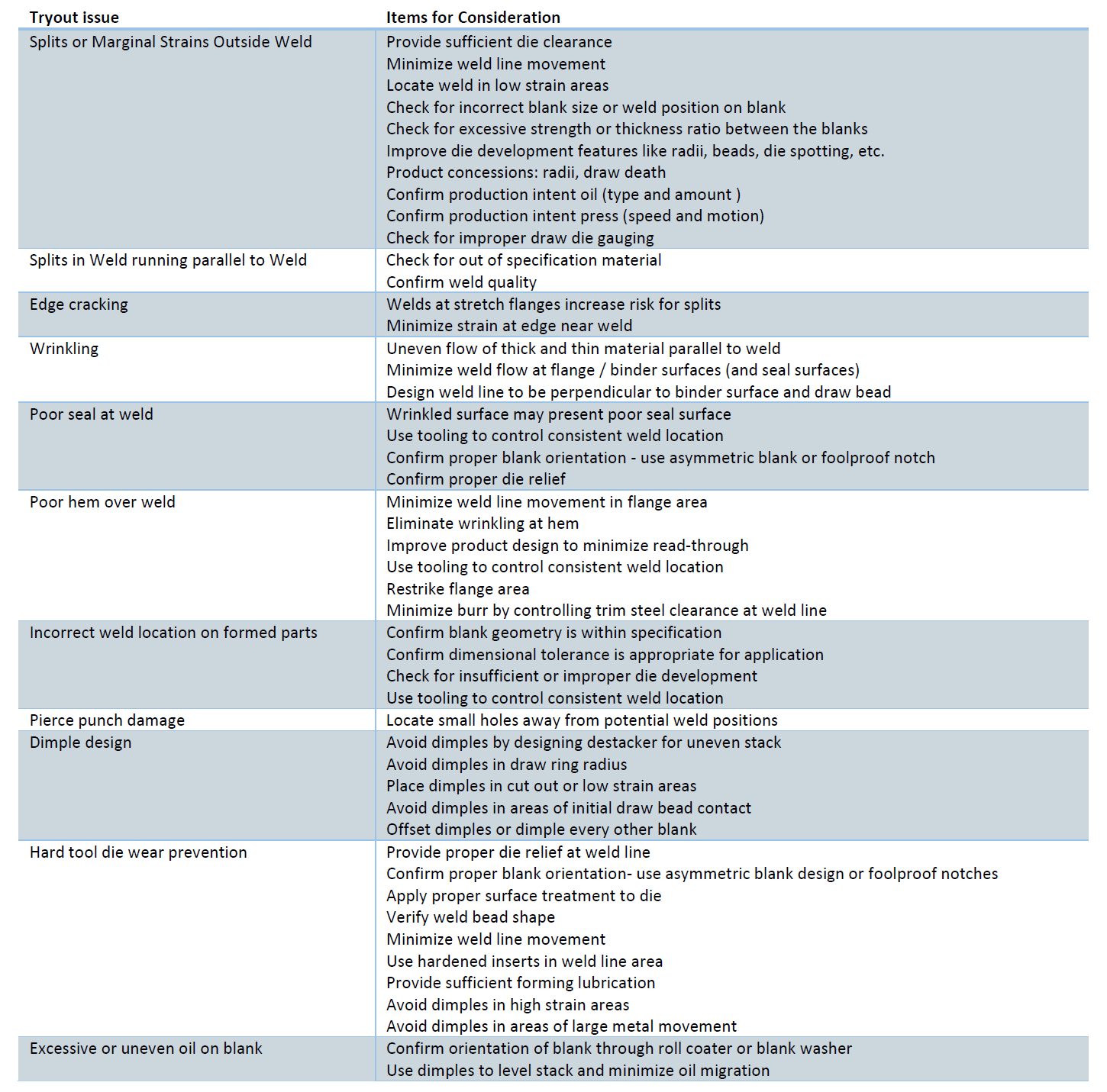
Tailor Welded Blanks Stamping Tryout Issues Checklist.A-20
Case Study: Deploying Tailored Blanks in Electric Vehicles
Many thanks to Isaac Luther, TWB Company, for providing this case study.
Laser-welded blanks (LWBs) allow the combination of different steel grades, thicknesses, and even coating types into a single blank. This results in stamping a single component with the right material in the right place for on-vehicle requirements. This technology allows the consolidation of multiple stampings into a single component.
One example is the front door inner. A two-piece design will have an inner panel and a reinforcement in the hinge area. As shown in Figure 12, a laser welded front door inner incorporates a thicker front section in the hinge area and a thinner rear section for the inner panel, providing on-vehicle mass savings. This eliminates the need for additional components, reducing the tooling investment in the program. This also simplifies the assembly process, eliminating the need to spot weld a reinforcement onto the panel.
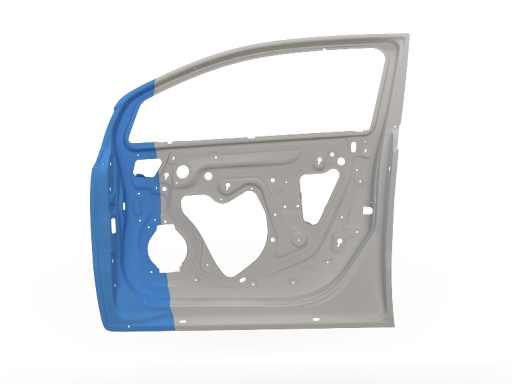
Figure 12: Front Door Inner Stamped from a Laser Welded Blank
Today, large opportunities exist to consolidate components in a BEV in the battery structure. Design strategies vary from different automakers, including how the enclosure is constructed or how the battery mounts into the vehicle. The battery tray can have over 100 stamped components, including sealing surfaces, structural members, and reinforcementsM-68. As an idea, a battery tray perimeter could be eight pieces, four lateral and longitudinal members, and four corners. The upper and lower covers are two additional stamped components, for a total of ten stampings that make up the sealing structure of the battery tray. On a large BEV truck, that results in over 17m of external sealing surfaces.
Part consolidation in the battery structure provides cost savings in material requirements and reduced investment in required tooling. Another benefit of assembly simplification is improved quality. Fewer components mean fewer sealing surfaces, resulting in less rework in the assembly process, where every battery tray is leak-tested.
The deep-drawn battery tub is a consolidated lower battery enclosure and perimeter. This can be seen in Figure 13; a three-piece welded blank incorporates a thicker and highly formable material at the ends and in the center section, either a martensitic steel for intrusion protection or a low-cost mild steel. This one-piece deep-drawn tub reduces the number of stampings and sealing surfaces, resulting in a more optimized and efficient design when considered against a multi-piece assembly. In the previous example of a BEV truck, the deep-drawn battery tub would reduce the external sealing surface distance by 40%. To validate this concept, component level simulations of crash, intrusion, and formability were conducted. As well as a physical prototype built that was used for leak and thermal testing Y-14 with the outcomes proving the validity of this concept, as well as developing preliminary design guidelines. Additional work is underway to increase the depth of the draw while minimizing the draft angle on the tub stamping.
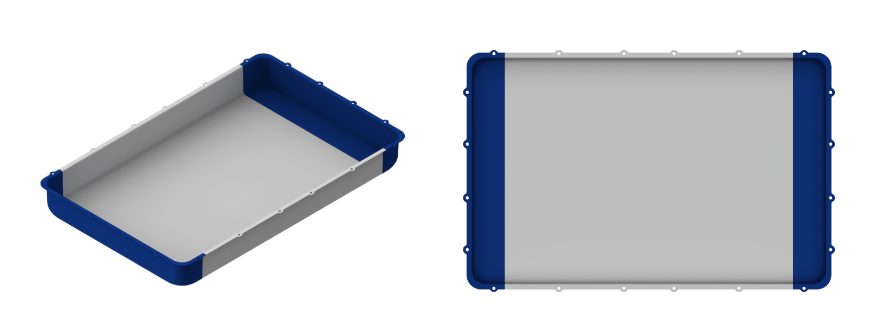
Figure 13: Deep Battery Tub Stamped from a Laser Welded Blank
In most BEVs today, the passenger compartment has a floor structure common in an ICE vehicle. However, the BEV also has a top cover on the battery assembly that, in most cases, is the same size as the passenger compartment floor. In execution of part consolidation, the body floor and battery top cover effectively seal the same opening and can be consolidated into one component. An example is shown below, where seat reinforcements found on the vehicle floor are integrated into the battery top cover, and the traditional floor of the vehicle is removed. Advanced high-strength steels are used in different grades and thicknesses. Figure 14 show what the laser welded battery top cover looks like on the assembly.
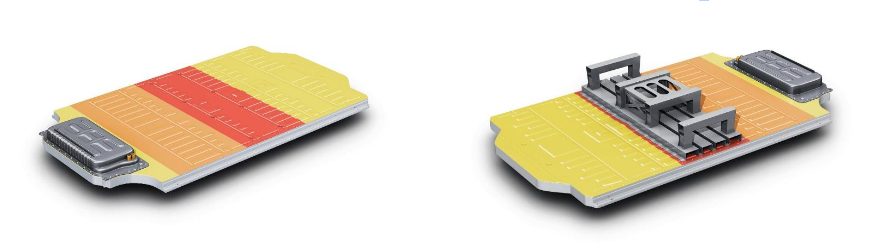
Figure 14: Battery Top Cover from a Laser Welded Blank
Vehicle assembly can also be radically simplified as front seats are mounted on the battery before being installed in the vehicle as shown in Figure 15, the ergonomics of the assembly operation are improved by increased access inside the passenger compartment through the open floor.
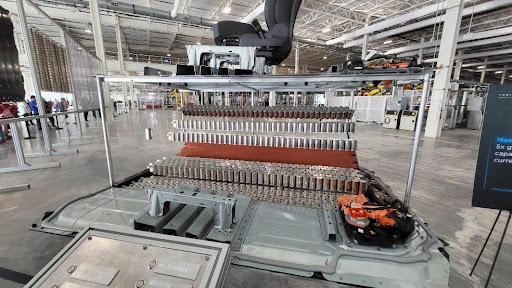
Figure 15: Ergonomics of the Assembly Operation
Cost mitigation is more important than ever before, with reductions in piece cost and investment and assembly costs being important. At the foundation BEVs currently have cost challenges in comparison to their ICE counterparts, however the optimization potential for the architecture remains high, specifically in part consolidation. Unique concepts such as using laser welded blanks for deep-drawn battery tubs and integrated floor/battery top covers are novel approaches to improve challenges faced with existing BEV designs. Laser welded blank applications throughout the body in white and closures remain relevant in BEVs, providing further part consolidation opportunities.
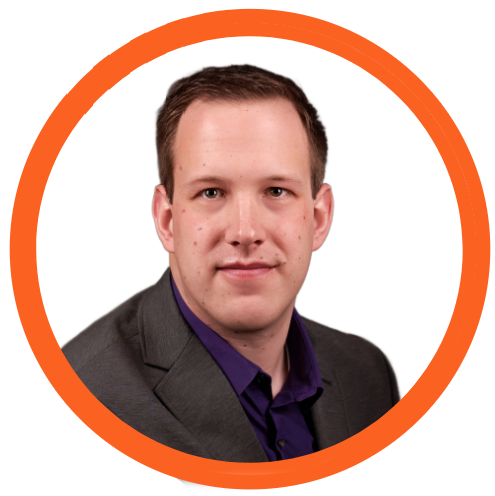
Thanks go to Isaac Luther for his contribution of this case study. Luther is a senior product engineer on the new product development team at TWB Company. TWB Company provides tailor-welded solutions in North America. In this role, Isaac is responsible for application development in vehicle body and frame applications and battery systems. Isaac has a Bachelor of Science in welding engineering from The Ohio State University.
Back to the Top
Press Hardened Steels
Introduction
Some automotive components may require higher stiffness, strength, or energy absorbing capacity in a confined local area. One method to achieve these characteristics is to spot weld separate reinforcement panels to the main component. A strategy for improving energy absorption in high-strength components involves joining a second part made from a more ductile but lower strength material. Neither of these approaches are ideal in terms of manufacturing efficiency and product/process optimization.
Tailored parts are the term given to those parts that may have zones with different thickness, chemistry, or heat treatment, resulting in a reduced number of components, weight reduction, and/or lower costs. These goals are achieved through part consolidation and by reducing or in some cases even eliminating joining operations.
In cold stamping operations, tailored parts (tailored products) are typically produced at the incoming coil or blank level, but are typically called “tailored blanks” or the specific process/product produced:
- Laser Welded Tailored Blanks (LWTB, also known as Tailor Welded Blanks, or TWB) or Tailor Welded Coils (TWC – not common in press hardening),
- Tailor Rolled Blanks (TRB) or Tailor Rolled Coils (TRC),
- Tailor Welded Tubes (TWT) or Tailor Rolled Tubes (TRT), or
- Patchwork Blanks,
In press hardened components, a single component may be press hardened such that it has what are known as soft zones, or areas of lower hardness possessing increased ductility. The tailored processing of these multi-strength parts can be achieved byB-14:
- Controlling the incoming blank temperature, (Tailored Heating, pre-process)
- Controlling the quenching rate, (Tailored Quenching, during process)
- Partially tempering (Tailored Tempering, post-process).
These are typically called tailored parts or tailor processed parts. Lastly it is also possible to combine two techniques, that is, making a tailored part using a tailored blank.
Laser Welded Tailored Blanks (Tailor Welded Blanks)
Laser Welded Tailored Blanks (LWTB) are blanks that are produced by laser butt welding of two or more sub-blanks, as shown in Figure 1. In the industry, the terms Tailor Welded Blanks (TWB) and Laser Welded Blanks (LWB) are also used interchangably.M-46

Figure 1: Steps of making a press hardened laser welded tailored blank (re-created after Citations B-14 and A-8).
Laser welded tailored blanks consist of sub-blanks with:
- Different thicknesses, allowing for use of thinner sheet steels in areas of the component having less rigorous loading requirements. Using thinner sheets saves weight.
- Different grades, optimizing the energy absorption and intrusion resistance characteristics in each area of the same part (such as an automotive B-pillar, see Figure 6b).
- A combination of both.
Laser welded tailored blanks with the same thickness and grade are used to create blanks having dimensions larger than mill rolling or processing capabilities.
Laser welded tailored blanks offer many paths to weight savings and cost reduction, including:
- Reducing the number of parts in the subassembly, such as the need for reinforcements;
- Reducing the number of required forming tools, welding fixtures, etc.; and
- Improved raw material utilization by sub-blank nesting optimization (see Figure 1 and Figure 10c).
The weld area of press hardened laser welded blanks may not transform to martensite, and therefore may show a significant reduction in the hardness. This can be attributed to weld quality and quenching rate.B-47, W-3
Blanked edge geometry of the sub-blanks (notches, underfillings and weld seam pollution) affects weld quality. Separating the blanking into two operations, rough blanking and precision blanking, may improve blanked edge geometry and the resulting weld quality.M-46
As seen in Figure 1, Aluminium-Silicon (AS) coated sub-blanks may require a secondary ablation operation. The AS coating is removed (ablated) near the weld edge, typically by using a laser. When this AS coating is not removed and filler wire is not used, the aluminium from the coating may pollute the weld. When welding two PHS1500 sub-blanks together, an aluminium-polluted weld may have significantly lower hardness, as shown in Figure 2. A part made of such a blank will fail at the weld zone, both in quasi-static and dynamic conditions.E-8

Figure 2: Effect of ablation and filler wire on hardness distribution around the laser weld of equal thickness PHS1500+AS150 (re-created after Citation E-8).
Another common type of laser welded tailored blank is where a press hardening steel (typically PHS1500) is welded to a press quenched steel (PQS 450 or 550). Lower strength and higher ductility should be observed in the PQS. Without ablation, a hardness drop is observed in AS coated welded blank, seen in Figure 3a. In quasi-static tests, fracture was observed in the PQS base metal. In dynamic tests, the part failed at the weld zone. When ablation is applied, a B-pillar with a PQS base absorbs more energy compared to the welded blank without ablation.E-8 In uncoated and Zn-coated steels, ablation is not required since there is no concern about aluminium pollution in the weld.A-68, M-2 Figure 3b shows the hardness distribution in the weld seam of galvanized sub-blanks.

Figure 3: Hardness distribution in PHS-PQS laser welded blanks. a) AS coated sub-blanks with and without ablation (re-created after Citation E-8); b) Galvanized sub-blanks without ablation (re-created after Citation M-2). Note that the initial thicknesses of sub-blanks are different.
There are two methods of ablation. Full ablation removes the AS coating and the interdiffusion layer (IDL) in their entirety. In contrast, partial ablation removes only the AS coating, but the IDL remains intact. Full ablation may result in oxidation and decarburization in the weld seam.E-8, W-3
In addition to weld pollution, the hardness drop in the weld seam could also be caused by the local quenching rate. When a welded blank is made using sub-blanks with different thicknesses, misalignment (Δx in Figure 4a) may lower the quenching rate. Misalignment greater than 2 mm could cause over 30% hardness drop, from approximately 500 HV to less than 350 HV.B-47 A filler wire with high-C content could reduce the critical cooling rate, as shown in the Figure 4b. In a particular example using a filler wire containing 0.3% C presented in this image, the critical cooling rate was reduced to approximately 13 °C/s. Due to the high-C content, a 20% increase in the weld seam hardness may be possible,E-8 as indicated in Figure 2.

Figure 4: a) Misalignment of the blank in the die could cause lower quenching rate in the weld seam (re-created after Citation B-47); b) A high-carbon filler wire may reduce the critical cooling rate (re-created after Citation E-8).
The fourth generation Audi A4 (2008-2016 also known as B8) contained some of the earliest applications of press hardened laser welded tailored blanks. The car had five components made of blanks with tailored properties: tunnel reinforcement, left/right B-pillar reinforcements, and left/right rear rails, as shown in Figure 5. As PQS grades were not commercially available at that time, High-Strength Low-Alloy (HSLA) steels were used for energy absorbing applications. As delivered, HX340LAD + AS, had a minimum 340 MPa yield strength. Press hardened parts and their final mechanical properties are shown in Figure 5.S-65

Figure 5: PHS applications in Audi A4 (2008-2016). The car had a total of three different components and five parts using laser welded tailored blanks (figure and table re-created using data and images from Citations S-65, D-11, V-21, W-5, and S-13).
In Citation K-25, using a laser welded tailored blank resulted in the highest energy absorbing capacity of a B-pillar reinforcement. In this study, PHS1500 (22MnB5) was laser welded to a HC340LA (uncoated HSLA steel with minimum 340 MPa incoming yield strength). Such a welded blank could absorb 3.3 kJ energy without fracture, whereas a monolithic (same thickness, same hardness all around) PHS1500 failed at 2.3 kJ (see Figure 6). PHS1500 with soft zones (see the Tailored Properties section below) passed a 2.3 kJ test but failed at 3.3 kJ.

Figure 6: Energy absorbing capacity of B-pillars increase significantly with soft zones or laser-welded ductile material (re-created after Citation K-25).
Conventional High-Strength Steels are not designed for hot stamping process. HSLA 340 and 410 MPa grades (minimum yield strength, as delivered) and CMn440 steel (Carbon-manganese alloyed, minimum 440 MPa tensile strength at delivery) may be softer than their as-delivered condition when heated over austenitization temperature and slowly cooled at 15 °C/s cooling rate. Furthermore, if the local cooling rate is over 60 to 80 °C/s, a significant increase in hardness (see Figure 7) and sharp decrease in elongation may be observed.D-22, T-27

Figure 7: Vickers hardness variation of several cold stamping steels after austenitization and at different cooling rates (re-created using data from Citation D-22).
Development of PQS grades started around 2007, targeting consistent mechanical properties over a wide range of cooling rates. Currently, typical laser welded blank applications of PQS450 and PQS550 in the automotive industry include B-pillars, front rails, and rear rails. One such car with LWTB components is the 2nd generation Volvo XC90 (2014-Present). The car has a total of 152 kg hot stamped parts, with approximately 132 kg of PHS1500 and 20 kg PQS450, comprising 33% and 5% of the BIW (excluding doors and closures), respectively. The XC90 has a total of six hot stamped welded blanks (three left and three right), as seen in Figure 8.L-29, L-8 More details about welded blanks with PQS450 and PQS550 are presented in the Grades with Higher Ductility Section within our article on PQS Grades.

Figure 8: Use of laser welded PQS-PHS grades in the 2nd generation Volvo XC90 (re-created after Citation L-29).
Recently PHS1000 and PHS1200 grades have been developed. The yield and tensile strength of these grades increase with hot stamping, and as such are considered press hardening steels. Y-12, G-30 More details about these grades are presented in the Grades with Higher Ductility Section within our article on PQS Grades. Renault conducted an experimental study in 2021 to replace PHS1500-PQS550 laser welded tailored blanks with those made from a PHS2000-PHS1000 combination. As seen in Figure 9, the new materials can absorb the same amount of energy with less intrusion. At the same level of intrusion, the energy absorbing capacity improves by 30%.B-62

Figure 9: Stroke vs. energy curves of representative sub-assemblies, emulating B-pillar (re-created after Citation B-62).
Laser welded tailored blanks may also be used to create larger blanks that may not be otherwise possible or economically feasible.M-4 Door rings represent one such application for hot stamping, as introduced by ArcelorMittal in 2010.A-17 A prototype door ring was produced in 2012, using four sub-blanks, including one PQS550, as shown Figure 10a. The part measured approximately 1500 mm long and 1250 mm high.B-63, T-1 May 2013 saw the first application of a hot stamped door ring with the introduction of the 3rd generation Acura MDX, running from 2013-2020. The vehicle used a two sub-blank LWB door ring, both PHS1500, with thicknesses of 1.2 mm and 1.6 mm. Through sub-blank nesting optimization, material utilization was improved to 63%. Details can be seen in Figures 10b and 10c.M-46

Figure 10: Door rings. a) one of the earliest concepts from 2010T-1; b) the first mass produced door ring of the 2013 Acura MDX; c) sub-blank nesting to improve the material utilization.M-46
For door ring manufacturing, a higher tonnage press with larger bolster area may be required, as well as a wider furnace and heavier capacity transfer systems. In most hot stamping lines, typically two or four parts are formed and quenched in one stroke (known as 2-out or 4-out) to improve productivity and reduce the total cost per piece. Due to the large size and additional requirements, door ring manufacturing is typically 1-out. However, as the part itself replaces four components (A and B pillars, hinge pillar and rocker reinforcement), it can be as cost effective as a 4-out hot stamping operation.W-6
Although not common, the Acura TLX (1st generation 2015-2021) and Hyundai Santa Fe (since 2018, 4th generation) utilize single piece (not from a welded blank) door rings with 1.4 mm and 1.1 mm thicknesses respectively. B-14, H-4 The 2nd generation Acura TLX (2021-present) has the door-ring of the 1st generation model as a carryover.L-61
Since its inception, laser welded door rings have been used in several Honda / Acura models. The number of sub-blanks was increased to 4 with the 2nd generation Honda Ridgeline (2017-present). This was the first door ring application in a pick-up truck.B-52 The Chrysler Pacifica started production in 2017 with 5 sub-blanks, as shown in Figure 11a, including PQS550 for crash energy absorption.T-19 The 5th generation RAM 1500 pick-up truck, which debuted in 2018, has a six sub-blank door ring, as seen in Figure 11b.R-3 In 2018, Acura RDX became the first car to have inner and outer door rings made of PHS1500 laser welded blanks. As seen in Figures 11c and 11d, five and four sub-blanks were used respectively for the inner and outer door rings, all PHS1500. This design further allowed downgauging and lightweighting.R-26

Figure 11: Laser welded door ring applications: (a) Chrysler Pacifica (SOP 2017) has five sub-blanks (recreated after Citation T-19); (b) RAM 1500 (SOP 2018) has six sub-blanks (re-created after Citation R-3); Acura RDX was the first car to have two door rings: (c) inner and (d) outer, both with four sub-blanks of PHS1500 (re-created after R-26).
Currently, the European Standard for Laser Welded Tailored Blanks (LWTB), EN 10359D-2, covers only LWTBs for cold stamping materials. This standard will be expanded to include press hardened laser welded blanks, with an expected release in 2023.
Tailor Rolled Blanks
Tailor Rolled Blanks (TRB) or variable thickness rolled blanks (VTRB) are produced by a secondary cold rolling of an already cold rolled and possibly coated coil. In this secondary cold rolling, the roll gap is adjusted during the process so that the thickness can be varied (tailored) locally, shown in the left image of Figure 12. TRBs can be an alternative to “same material-different thickness” welded blanks.B-14 Contrary to an LWB, thickness changes are not abrupt, but instead are continuous. Thus, TRBs do not have stress concentration due to the notch effect. Problems associated with weld quality in welded blanks (pollution, geometry, quenching rate, etc.) do not apply to TRBs since welding the blank is not necessary.H-7
Tailor rolled blanks are typically named by their thicknesses from head-to-tail, and symmetrical sections with same thicknesses are written once. For example, the B-pillars of previous generation Ford Focus (2011-2018), as shown in the right image of Figure 12, has five thicknesses in nine zones. This blank would be named as: 1.35-2.30-2.10-2.40-2.70. The process starts with a 2.70 mm thick coil, and thickness reductions up to 50% would be completed during the tailor rolling process. The typical slope in the Thickness Transition Zones (TTZ) are 1:100, meaning 1 mm change in thickness would require a 100 mm long TTZ. Different slopes could also be utilized.Q-7, H-8

Figure 12: Left image: Principle of tailor rolling process (re-created after Citation Z-5); Right image: thickness profile and nesting of a B-pillar in a tailor rolled coil (re-created after Citation Q-7).
The tailor rolling process squeezes and thins any coating, and possibly damages the coating as well.T-4 For this reason, TRBs are typically used in dry areas. Because of similar reasons, in AS coated TRB applications, AS150 (75 g/m2 on each side, Al-Si coating) is preferred instead of thinner coatings such as AS80.
One of the first press hardened TRB applications was the B-pillar reinforcement of the BMW X5 (2nd generation, 2006-2013). The application saved 4 kg/car, compared to a monolithic press hardened part.P-1 Other applications include: heel piece of MQB (Modularer Querbaukasten, translating from German to “Modular Transversal Toolkit) platform cars – covering many VW Group cars with transverse engine orientation, since 2012S-107, front crossmember of MLB Evo (Modularer Längsbaukasten, translating from German to “Modular Longitudinal Matrix) platform cars – covering Audi vehicles with longitudinal engine orientation, since 2015H-44, and roof crossmember of the 10th generation Honda Accord (2017-present).M-7 Many other OEMs use tailor rolled blanks, with a more detailed list presented in Citation B-14.

Figure 13: Several TRB applications in recent vehicles (re-created after Citations H-44, P-1, S-107, and M-7).
Patchwork Blanks
In a patchwork blank, one or more “patch blanks” (reinforcements) are overlapped with a “master blank” and spot welded. The spot-welded blanks are then heated in a furnace and hot stamped as a single piece in one stroke. The final part will have increased thickness in the areas of interest. A patchwork blank may reduce the need for post-forming assemblies of reinforcements, as seen in Figure 14. Since the spot welds are also austenitized and quenched, their hardness distribution is typically better than spot welding after hot stamping, as shown clearly in Figure 15.B-20, U-12, N-3

Figure 14: Master blank and patch geometries of a sample B-pillar: (a) before, and (b) after spot welding, (c) after hot stamping (re-created after Citations B-14 and L-52).

Figure 15: Hardness distribution in a spot weld, comparing when spot welding is done before or after press hardening, (Re-created after Citations B-14 and U-12)
Patchwork blanks allow for the possibility of reducing the number of forming tools and the associated fixed costs. Stamping and post-process joining costs may be reduced as well, leading to a variable cost reduction. Depending on how the part is engineered, a weight savings may be achieved. These benefits come at the expense of the additional blanking operation to create the patch blanks, and the pre-process welding stations.U-12, T-42
Optimizing the initial geometry of the patch blank helps reduce these costs. One approach is to use a one-step inverse simulation in the early planning / feasibility phase. In this method, the initial outline is estimated based on deformation theory of plasticity, requiring only relatively short CPU-times (in the order of a few minutes using a modern PC), with low accuracy (up to 3 mm deviation is common). A trim optimization method is recommended during the design phase of the patch blank blanking dies. In this method, an incremental solver is used with an initially assumed blank outline. Typically, the result of one-step solution is used for the first iteration. The software then compares the outline of the patch after forming and calculates the differences with the desired geometry. Then the initial geometry is modified accordingly, and another forming simulation is carried out. These iterations continue until the deviation is less than the set tolerances. For example, in a B-pillar patch optimization, ±0.25 mm deviation may be achieved in two to three iterations.W-8, Z-12, S-108
Reducing the number of spot welds also reduces the cost of the patch blank. Minimizing the number of spot welds may also reduce the cycle time in welding stations. In some cases, it may also affect the number of spot-welding stations — thus, the initial fixed cost. However, severe wrinkles may form if using an insufficient number of spot welds. Using finite element analysis may assist in finding the optimum number of spot welds for formability.A-19 In some cases, although the part could be hot formed with a smaller number of spot welds without any problems, more spot welds are applied for crash performance.U-12
Some of the earliest patchwork PHS applications were used in the B-pillars of 3rd generation Volvo V70 (2007-2016) and Fiat 500 (2007-present). In the Volvo V70, a total of 46 spot welds were used to create the patchwork blank. Both blanks were uncoated PHS1500, with a 1.4 mm thick master blank and a 2.0 mm thick patch.L-53 In the Fiat 500, the master blank was 2 mm thick, supported by a 1 mm thick patch, both AS coated, as seen in Figure 16a.Z-13 In recent years, patchwork PHS blanks have been used in more car bodies, including but not limited to several parts in the 2nd generation Volvo XC90 (2014-Present)L-29, rear rail of the Fiat 500X (2014-Present)M-45, B-pillar of the Opel Astra K (2015-Present)K-8, B-pillar of the 2nd generation Range Rover EvoqueF-1, and several Subaru models.U-12, A-73
In the rear rail of the Fiat 500X, the master blank is laser welded with 1.5 mm PHS1500 and 1.6 mm PQS450 sub-blanks. The patch blank is a 1.5 mm thick PHS1500.M-45 A similar design with different thicknesses was also used in Fiat Tipo/Egea, as shown in Figure 16b.B-14 For the Opel Astra, the master blank is a 1.3 mm thick PHS1500 with soft zones (see the Tailored Properties discussion below). The patch is a TRB with 1.00-1.95-1.00 thickness distribution.K-8

Figure 16: Sample automotive applications of patchwork PHS: B-pillar reinforcements of (a) 2007 Volvo V70 (re-crated after Citation N-4), (b) 2007 Fiat 500 (re-created after Citation Z-13); and (c) rear rail of 2015 Fiat Tipo/Egea (Citation T-43, recreated after Citation B-14).
Jaguar I-PACE is an aluminium-intensive electric SUV making its debut in 2018. In this car, the B-pillar reinforcement is made up of a patchwork blank. Contrary to most earlier applications, the master blank is a PQS450, which could be joined easily to the rest of the body by mechanical joining. The patch is PHS1500, which improves the side impact and roof crush performance.B-21 In 2018, a global Tier 1 supplier showed the possibility of using PHS2000 master blank and patch for a rear bumper beam.N-6
Improvements in patchwork blank technology includes the weld type and quality. Conventional resistance spot welding has been used in making patchwork blanks. There are studies on using remote laser welding for this purpose as well. In one study, joining a patchwork blank with approximately 50 welds was completed in 35 seconds using 2.2 kW laser power, and in 23 seconds using 2.8 kW.L-54 Another study showed that when laser welding is used with AS-coated blanks, weld strength is reduced by approximately 40% compared to uncoated blanks.G-1
“Overlap patch blanks” are a sub-set of patchwork blanks. As seen in Figure 17a, instead of a master and patch blanks, two (or more) sub-blanks are spot welded over an “overlap region” to create a blank like a laser welded tailored blank. The technology was initially applied in cold stamped components.P-4 Recently an international tier 1 supplier developed door rings and floor panels made from overlap patch blanks that were press hardened. As seen in Figure 17 b and c, a door ring can be created using 5 sub-blanks, including one PQS (shown in green).G-3

Figure 17: Overlap patch blanks: (a) schematic of a B-pillar blank (re-created after B-75), (b) door ring concept from outer view, and (c) inner view.G-3
One of the benefits of using overlap patch blanks is the ability to build up larger welded blanks of Al-Si coated steel without the need to employ ablation technology. The overlapped sub-blanks can be resistance spot welded together, thereby avoiding the risk of aluminum polluting the weld pool that ablation would otherwise mitigate.
Patches can be engineered to increase stiffness in critical locations, and the spot welds provide easy adjustment to both the blank and weld as needed.
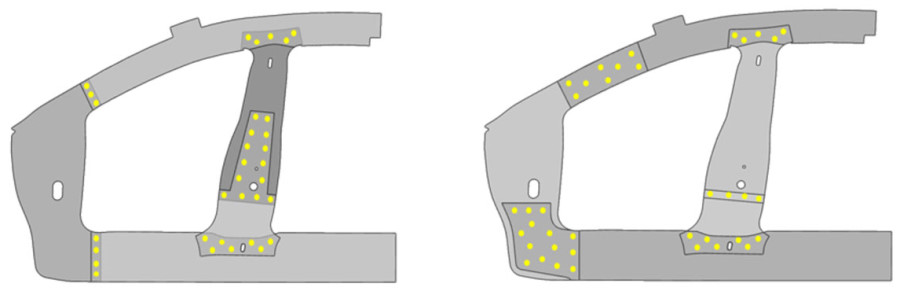
Figure 18: Overlap patch blanks created with resistance spot welding eliminates the need to use laser welding and ablation techniques.S-111
Tailored Properties
Tailored properties is a term used for the technology to make a part with hard and soft zones. Hard zones are nearly 100% martensitic, whereas soft zones have a lower percentage of martensite. This type of part may be called a “multi-strength part”. In Europe, the term “tailored tempering” may be used to denote a part with tailored properties. In this article, tailored tempering describes a part which was press hardened as a whole and later locally softened to modify properties in specific areas.
Soft zones may be used for several reasons:
- To improve crashworthiness: Local areas with higher ductility aid in crash energy absorption. An example B-pillar is shown in Figure 6. This type of usage is very common in B-pillars, front rails, and rear rails, as shown in Figure 8. The first application for this purpose was realized in the B-pillar of the first-generation VW Tiguan (2007-2018).S-13 The technology is also used in rear rails. Both applications are shown in Figure 19. The technology is also used in rear rails of 10th generation Honda Civic (2015-present)C-22, and 10th generation Honda Accord (2017-present). In this particular application, shown in Figure 20, soft zones were designed such that the rear frame would deform in a pre-defined manner and absorb the crash energy efficiently.C-22, M-7, K-52 Tailored parts are used for improved energy absorption in numerous models from Audi, BMW, Ford, Honda, Mercedes and others.B-14

Figure 19: Rear rail assembly of Honda Civic (10th gen., 2015-Present): (a) Isometric view of the assembly, (b) bottom view of the frame, during rear crash condition (re-created after Citation K-52). A similar design was also employed in Honda Accord.M-7

Figure 20: Example uses of soft zones for improved energy absorption: (a) first application was in 1st generation (2007-2018) VW Tiguan’s B-pillars (re-created after Citations V-22 and M-8), (b) a more recent application in 2013 Ford Escape’s rear rails (known as Ford Kuga in EU, sold between 2013 and 2019) (re-created after Citation M-59).
- To improve weld/joint strength: When base metal hardness is over 350 HV, the heat affected zone (HAZ) in the spot weld may be the weakest point of an assembly.B-20 Several other studies have proven the hardness drop and early fractures around spot weld of fully hardened parts, as summarized in Figure 21. When flanges are induction tempered (see the Tailored Tempering discussion below, a B-pillar assembly may absorb 30% more energy than a fully hardened B-pillar.H-61, F-2 In multi-material mix cars, such as the 2nd generation Audi Q7 (2015-present), “soft flanges” can be used for mechanical joining the PHS B-pillar reinforcement to aluminium components. Hemming of aluminium, around the PHS, can also be used to join the components.H-62

Figure 21: When spot welding is done on a soft zone: (a) hardness distribution would not have a soft HAZ, and (b) early fractures at spot welds are not observed (re-created after Citations B-14, H-61, and B-64).
- For secondary bending operations: Tailored tempering (softening areas of interest after a fully hardened press hardening process) may be used in bumper beams, where a secondary bending may be required to form an inner flange.L-40
- To facilitate trimming/piercing: Although not very common, local soft zones may reduce the force/energy requirements and improve the cutting tool life if hard trimming will be used.L-55
There are three methods to create the soft zones leading to tailored properties:B-14
- Tailored heating during austenitization of the blank (typically achieved in the furnace),
- Tailored quenching after austenitization (can be achieved in tempering stations or in the forming die),
- Tailored tempering after fully hardening a part (after the press hardening process).
1) Tailored Heating (Pre-Process)
In tailored heating, areas of interest (the soft zones) are not fully austenitized. The critical heating temperature has been reported as 750 °C by several researchers. When heated below 750 °C and hot stamped, the part has a tensile strength of approximately 600 MPa and over 15% total elongation. As seen in Figure 22, mechanical properties will stay relatively constant with heating temperatures between 650 and 750 °C. Above this critical heating temperature, hardness (almost directly proportional with tensile strength) may increase significantly.K-53

Figure 22: Effect of blank heating temperature on hardness and converted tensile strength of PHS1500 (re-created after Citation K-53).
There are several methods to achieve tailored heating. In the direct process, where an undeformed blank is being heated, there were four main methods proposed:
- Using a divided furnace,
- Masking soft zones in furnace,
- Heating by segmented contact plates, and
- Conduction heating with controlled current flow.
A divided roller hearth furnace may have gas or electric heating for the first half of its length, ensuring a uniform temperature distribution during heating. In the second half of the furnace length (soaking zone), there may be several electric heating zones across the furnace width direction that can be set to different temperatures. To simplify the schematic, Figure 23 shows a two-zone divided furnace. In the soaking zone, five-zone furnaces were already available as early as 2011. By 2018, furnaces with 32 zones were industrially used to make parts for several German OEMs.H-47, E-12, O-13

Figure 23: Divided furnace concept (simplified with two zones): (a) temperature setting in the furnace affects the temperature distribution in the soft and hard zones; (b) in the tailored soaking area, up to 32 zones may be realized (re-created after Citations B-14, E-12, and O-13).
As heating of the blank in furnace is mostly achieved by radiation, an insulating mask may reduce the local temperature in the soft zones. Ceramic insulators or machined steel blocks may be used for masking purposes. Areas that are not masked will be heated above the austenitization temperature, whereas the masked areas will be at lower temperatures.N-3 Figure 24 shows a schematic of the process. In addition to masking duty, the inlay should have enough heat capacity to absorb the heat from the blank. When steel inlays (masks) are used, they should be thicker than the blank to have the necessary heat capacity. Stainless steels could be used to avoid scaling of the steel inlay.B-65, B-66

Figure 24: (a) Using masking for tailored heating (re-created after Citations B-14 and N-3); (b) an example mask and blank from Citation K-54.
Although not commonly used for mass production, it was proven that contact plates may be used in tailored heating. Blanks are isolated from the environment during contact plate heating, significantly reducing oxidation on uncoated blanks. Fraunhofer IWU in Chemnitz, Germany, has developed a lab-scale contact plate heater that can generate soft zones. In the hard zones (those heated over 900 °C), the heating rate may be as high as 300 °C/s. The heater and a sample blank are shown in Figure 25.S-109, G-48

Figure 25: Tailored heating in contact plate heating: (a) right after the heating before the discharge, (b) a tailor heated blank with dimensions and approximate temperatures (re-created after Citation S-109).
Two different strategies were developed to generate tailored heat blanks using conductive heating while ensuring no current passes through the targeted soft zones.M-60 These approaches are applicable only to rectangular blanks. Researchers in Hanover University improved the technology to heat non-rectangular blanks with tailored temperature distribution. In a sample (non-rectangular) B-pillar blank, temperature was kept at 950 °C in the heated zones and approximately at 700 °C in the soft zones. Significant temperature drops were observed in the proximity of electrodes, resulting in non-uniform heating.B-67 Neither of the techniques are used in mass production for tailored parts.
In the indirect hot stamping process, the parts are formed prior to heating. Thus, it is not practical to apply any of the earlier strategies to get a cold zone in the part. For such components, soft zones are generated by using machined steel blocks known as absorption masses, which have high heat capacity to absorb the heat from the blank. As seen in Figure 26, correctly sized absorption masses keep the soft zones below 750 °C. When quenched, these areas have approximately 500 MPa tensile strength, over 20% total elongation (A50) and over 150° bending angle according to VDA bending test. The tailored parts have narrow transition zones, and are spot weldable, both in hard and soft zones. The technology is used in the B-pillar reinforcements of several BMW models.M-2, K-53, R-27

Figure 26: Tailored heating of galvanized PHS1500 in the indirect process: (a) Blank temperature evolution in hard and soft zones, in a roller hearth furnace using absorption mass in the soft zone; (b) hardness distribution and approximate tensile strength in hard and soft zones (re-created after Citation K-53).
Tailored heating technologies are beneficial for their energy efficiency, as the soft zones are heated to lower temperatures. The technology may be applied to uncoated and Zn-coated blanks; however, AS-coated blanks are at risk for incomplete coating diffusion in the soft zones. For these reasons, similar technologies (excluding conduction heating) also are used in a secondary heating device after the furnace.O-13 These techniques are listed in the Intermediate Pre-Cooling section below.
2) Tailored Quenching
In tailored quenching methods, the whole blank is austenitized in the furnace and the cooling rate is controlled such that the soft zones cannot develop high percentages of martensite. This can be achieved by two main process routes:
- Intermediate pre-cooling, where a secondary furnace is employed where the temperature of hard zones is maintained, but soft zones are allowed to cool.
- In-die cooling, where a fully austenitized blank with uniform temperature distribution is placed on the tool, but the part is cooled at different cooling rates through several process routes.
Intermediate Pre-Cooling
Complete coating diffusion does not occur in AS-coated blanks subjected to tailored heating profiles. To ensure the full coating diffusion and uniformity of the coating all around the blank, the blanks must be fully austenitized. One of the earliest approaches kept the hard zones in the roller hearth furnace, while extending the soft zones out of the furnace. This technology produced a part with two zones only, with a linear transition zone (Figure 27). AS-coating is fully developed for weldability and e-coat adhesion. Tailored properties are reproducible. For this furnace-extending method, no extra investment is necessary other than automation programming.L-56

Figure 27: Simplest pre-cooling technology: extending the soft zones out of the furnace. (a) Schematic of extending out of furnace (not to scale, from Citation B-55), (b) B-pillars made by this technology.A-74
Intermediate pre-cooling can also be done in a divided furnace. In this case, contrary to Figure 23a, the uniform heating temperature is set over 885 °C. The soft zone area is then set to a lower temperature and thus pre-cooled. The rear rails of the 2013 Ford Escape shown in Figure 20b are produced with this technique.M-59
Most of the tailored heating strategies discussed so far are suitable only for larger soft zone areas, but not for small areas. Intermediate pre-cooling by extending out of furnace and pre-cooling using a divided furnace strategy can only produce a two-zone tailored part, such as in Figure 28b. Since 2011, there has been an interest in producing three-zone tailored parts. By 2015, the Audi Q7 employed a three zone B-pillar with soft flanges for joining purposes. Soft spot weld areas are also under development.H-62, A-74, B-68

Figure 28: Tailored B-pillar evolution: (a) monolithic, (b) two-zones tailored, (c) three-zones tailored, (d) soft flanges, (e) soft spots (re-created after Citations A-74, B-68, P-3).
To address these challenges, several intermediate cooling systems have been developed. AP&T uses multi-layer furnaces, with an addition of a TemperBox®. The blanks are austenitized in the multi-layer furnace. Before being fed into the press, the blanks are first moved into another layer (the TemperBox®) where re-heating is done with masking. Masked areas cool below 700 °C, whereas the unmasked areas are re-heated to 930 °C. The cycle time varies between 30 and 70 seconds, depending on the thickness of the blanks (Figure 29). For continuous production, one TemperBox® supports five-chamber furnaces.K-41

Figure 29: Time-temperature evolution in the TemperBox®.K-41
Similar technologies have been developed by other furnace makers: Schwartz has developed a thermal printer which can be a stand-alone unit or installed at the end of a roller hearth furnace.L-56 EBNER has developed their PACC module, which can be integrated to a roller hearth furnace and cools the areas of interest by contact cooling.O-13
In-Die Tailored Cooling
In this process, the blanks are fully austenitized in the furnace, but the cooling rate is locally adjusted. Areas with a local cooling rate over 27 °C/s are expected to transform to nearly 100% martensite. In soft zones, cooling rates should be lower than this critical number. The cooling rate is a function of the thermal contact conductance (see Figure 31a) and the temperature gradient (ΔT) between the tool surface and the blank. Thus, lower cooling rates can be achieved byB-14, M-61:
- Heated die inserts,
- Die relief method, or
- Local die inserts with low thermal conductivity.
If a segment of the die is heated, sections of the blank in contact with this area have a smaller temperature gradient (ΔT), leading to reduced heat flow and lower cooling rates. In addition, sometimes this phenomenon occurs unintentionally if the dies are not cooled efficiently and hot spots are observed.B-14
In the automotive industry, heated die inserts are used typically between 300 °C and 550 °C. Typically electric cartridge heaters are used, Figure 30a. If the inserts are heated over 420 °C (the martensite start temperature for 22MnB5), no martensite formation occurs while the blank is in contact with the dies. For productivity purposes, sheets should stay in the dies as short as possible. After industrial quenching times (10-15 seconds), soft zones may still have phase transformation during air cooling in the exit conveyor. This may cause distortion in the final part. One simulation study found that 80 seconds of air cooling was needed to transform all the austenite into other phases.B-14, M-61, B-69, B-70

Figure 30: Tailored parts with heated die inserts: (a) Simulation model with cooling channels in hard zones and heating in soft zones, (b) phase transformation may continue in soft zones.B-70
This process has been applied as early as 2009 (if not earlier) in the Audi A5 Sportback.B-20 The car had a three-zone B-pillar, similar to the sketch in Figure 28c. Since then, several complicated geometries have been realized in an industrial scale with “heated die insert” technology. In 2015, the 10th generation Honda Civic was equipped with complicated rear rails, shown in Figure 19. These components are also made with heated inserts.C-22 Also debuting in 2015, the Audi Q7 was equipped with B-pillar reinforcements with soft band and soft flanges (similar to Figure 28d).H-62 As of 2021, heated dies appear to be one of the most common process routes to create tailored parts.
Another method to get lower cooling rates is to reduce the contact pressure or introduce an air gap between the blank and the die. As seen in Figure 31a, as the contact is lost, thermal contact conductance (hc, the amount of heat passing through the unit area of blank to the tool) is reduced significantly. For example, at 5 MPa contact pressure, hc is equal to 1.5 kW/m2°K. As soon as the contact is lost, the value is less than 0.3 kW/m2°K.B-70 A Schematic showing an “air gap” design for soft flanges is presented in Figure 31c and compared with a conventional die in Figure 31b.C-4

Figure 31: (a) Thermal contact conductance is less than 0.3 kW/m2°K, once there is an air gap (own work, raw data from Citations O-14 and M-62); (b) schematic of a conventional press hardening die, (c) introducing air gap to obtain soft flanges.C-4
Use of insulated die inserts is another method to obtain tailored cooling. These reduce the heat flow from the blank to the die. Typical hot forming tool steels have a heat conductivity of 27-32 W/m2°K. When ceramic insulators with less than 6 W/m2°K conductivity are used (Figure 32a), the inserts will heat over 200 °C after a few strokes. In the meantime, tool steel temperature is around 60 °C, as they can dissipate more heat energy. The strength in the soft zones may be as low as 650 MPa, corresponding to approximately 200 HV hardness.K-55 The method may not be feasible for mass production, as the first few parts will not have the same strength/elongation level until a “steady-state” is achieved, shown in Figure 32b and 32c. In real production conditions, the production may be halted for maintenance, safety, or work hours reasons.

Figure 32: Insulating inserts: (a) experimental die set at TU Graz, (b) hardness distribution of the first part, (c) hardness distribution after a few cycles (re-created after Citations B-14 and K-55).
3) Tailored Tempering (Post-Process Annealing)
The last method for obtaining tailored properties is to produce soft zones by annealing a fully hardened part. This can be done by induction or laser, as seen in Figure 32. Post-process annealing is relatively simple to implement, as the blank is heated and quenched uniformly in press hardening line. Annealing is added as a follow-up operation, which adds cost, but gives flexibility. The number of soft zones, their geometries and mechanical properties can be varied during the project timeline. Soft zones could be adjusted for different cars/variants that share the same component but require different soft zones.B-14, G-48, J-22
With this approach, however, final properties of soft zones may vary significantly depending on the temperature-time curves. Several studies have shown yield strength may spread from 450 MPa to 1300 MPa, and tensile strength between 550 and 1350 MPa. In addition, geometric distortion may also occur, since the heating and cooling is done in a local area. Finally, surface and coating conditions may change, affecting weldability, corrosion resistance and/or e-coat adhesion.L-40, M-61, B-72
BMW has been using induction annealed B-pillars in their 3-Series Sedan/Touring (2011-2019) and X5 SUV (2013-2018)R-27, and possibly other vehicles. Volvo has studied the technology with induction annealing, Figure 33a.H-61 Benteler has been using induction annealing for secondary bending of bumper beams.L-40 Gestamp evaluated laser tempering on prototype parts, Figure 33b.B-71

Figure 33: Post-process tailored annealing can be done by: (a) inductionH-61, and/or (b) laser.B-71
Post Hardening Processing: Trimming
Options include setting the trim line with a developed blank, laser cutting, soft zones, hard trimming, and hot cutting.
A developed blank might be appropriate for areas which can accommodate larger tolerances.
Soft zone development to aid in easier trimming and joining is discussed in the prior section.
Laser trimming leads to improved fatigue strength and raises the failure strains, but suffers from relatively long cycle times, high capital investment and maintenance cost. More powerful high-end lasers measurably reduce cycle times.
Hard trimming is not usually the best long-term option for high volume applications since the hardness of the PHS part is about the same as the hardness of trim steels. A harder, more wear resistant tool steel would now fail by chipping.
Hard trimming creates burrs, large shear zone, and microcracks in the fracture zone. Each of these lowers the fracture strain required for failure, which lowers component crashworthiness.
Trimming of fully hardened PHS needs extra consideration since the scale formed on uncoated PHS leads to abrasive wear and Al-Si coatings may stick to the tool creating galling conditions. A PVD coating improves wear resistance. World-class operations which use hard trimming specify advanced powder metallurgy tool steels with advanced tool coatings.
In-die hot cutting may occur after heating but before forming, and is usually limited to approximately 90° cuts. Microstructural changes occurring during the heating and cooling cycle influences flange position tolerances.
Hot cutting may also occur after forming but before quenching. This approach requires less force and causes reduced damage to the tooling and dies since the steel is softer to cut. One challenge is that the formed part is cooling during the cutting operation, with the part changing dimensions as it cools. Hot cutting improves cycle time and may reduce capital investment. Grains of fine ferrite rather than martensite form at hot sheared edge, reducing the delayed fracture risk associated with hydrogen embrittlement.
Honda developed this process to both trim the part as well as create holes during hot stamping to replace time- and energy-intensive laser cutting. (Figure 33, Figure 34). Their approach uses a high-speed hydraulic system, and further reduces cooling time by spraying the part with water. The first production application was the 2012 Honda N-Box Center Pillar Reinforcement. H-49, S-112
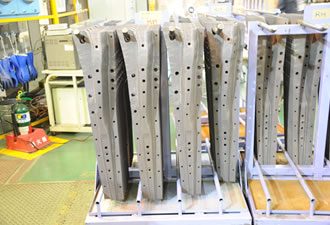
Figure 33: Honda N-Box Center Pillar Reinforcement created with In-Die Trimming during Hot Stamping. H-49
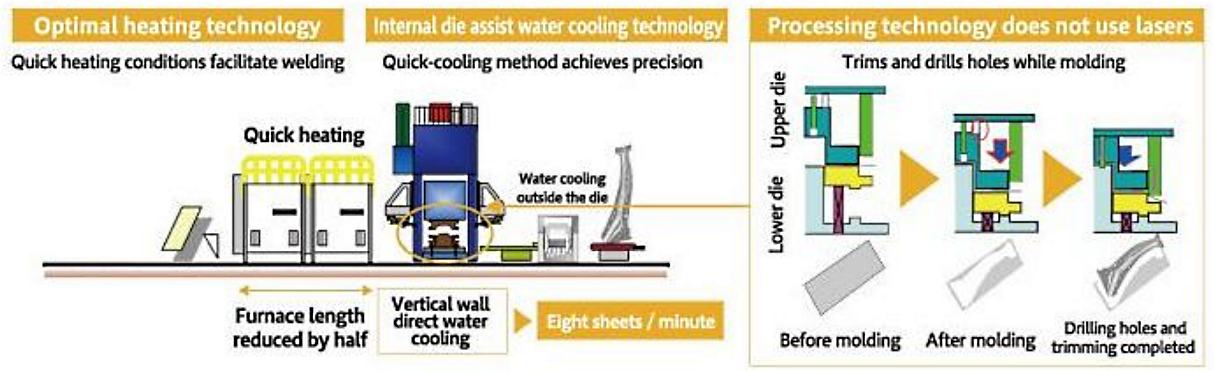
Figure 34: Internal Die Trimming Process at Honda.H-49
Back To Top
Springback
Overview
Forming a part at room temperature creates elastic stresses, which will require some form of springback correction to bring the stamping back to part print. Forming at sufficiently high temperatures, such as with press hardening steels, allows for stress relief before the part leaves the die.
Springback correction can take many forms. The first approach is to apply an additional process that changes the elastic stresses to a less damaging form. One example is a post-stretch operation that reduces sidewall curl by changing the tensile-to-compressive elastic stress gradient through the thickness of the sidewall to all tensile elastic stresses though the thickness. Another example is over-forming panels and channels so that the release of elastic stresses brings the part dimensions back to part print instead of becoming undersized.
A second approach is to modify the process and/or tooling to reduce the level of elastic stresses created during the forming operation. An example is to reduce sidewall curl by replacing sheet metal flowing through draw beads and over a die radius with a simple 90 degree bending operation.
A third approach for correcting springback problems is to modify product design to resist the release of the elastic stresses. Here, mechanical stiffeners added to the part design lock in the elastic stresses and maintain desired part shape.
The approaches to springback correction described below are applicable to all higher strength steels, and typically will address both angular change and sidewall curl. AHSS grades having high flow stress in the formed part may require one or more of these approaches for satisfactory dimensional accuracy.
Minimizing springback through compensation in the first draw stage is more effective and less expensive than attempting to correct for existing springback in subsequent re-strike or re-forming operations. Approaches for improved dimensional accuracy include:
- Minimizing bending/unbending as the metal flows to the final part shape reduces distortion and tool wear.
- Reaching minimum strain levels across the panel minimizes springback and sidewall curl.
- Accounting for tool material loss during recuts helps ensure sufficient tool stiffness to counteract the higher press forces required with AHSS grades.
- Keeping the depth of AHSS channel-shaped parts as uniform as possible avoids forming distortions. Gradual shape transitions will minimize distortions, especially in areas of metal compression. Designing radii so there are only gradual transitions avoids stress risers and minimizes distortions. Minimize stretch/compression flanges wherever possible.
- If die and process design cannot relieve all elastic stresses, then creating a uniformly distributed residual stress pattern across the sheet and through the thickness will help eliminate the source of mechanical multiplier effects and thus lead to reduced springback problems.
Correcting Springback by Changing the Elastic Stress Distribution: Post-Stretch (Stake Beads, Hybrid Beads, and Active Binder Force Control)
One of the most effective techniques for significant reduction of both angular change and sidewall curl is a post-stretch operation. Applying an in-plane tensile force after all operations in which the sheet metal is bent and unbend over draw beads and across die radii can change the through-thickness tensile-to-compressive elastic stress gradients to all tensile elastic stresses.
When the part is still in the die, the outer surface of the bend over the punch radius is in tension (Point A in Figure 1), while at the same time the inner surface is in compression (B). After the punch retracts and the part is no longer under load, the tensile elastic stresses (A) tend to shrink the outer layers and the compressive elastic forces (B) tend to elongate the inner layers. These opposite forces form a mechanical advantage to magnify the angular change. The differential stress ∆σ is the driver for the dimensional change. Note that this reversal in stress direction after removal of the applied load is the same root cause that results in snap-through reverse tonnage reactions when punching higher strength steels.

Figure 1: Sheet metal bent over a punch radius has elastic stresses of the opposite sign creating a mechanical advantage to magnify angular change. Similar effects create sidewall curl for sheet metal pulled through draw beads and over die radii. When the part is no longer under load, it will change shape to relieve these elastic stresses.
In the case of side wall curl, this differential stress ∆σ increases as the sheet metal is work hardened going through draw beads and around the die radius into the wall of the part.
To correct this angular change and sidewall curl, apply a tensile stress to the flange end of the wall to generate a minimum tensile strain of 2% within the sidewall of the stamping. Figure 2 describes the sequence of events. The initial elastic states are tensile (A1) and compressive (B1). When approximately 2% tensile strain is added to A1, the strain point work hardens and moves up slightly to A2. However, when 2% tensile strain is added to B1, the compressive elastic stress state first decreases to zero, then climbs to a positive level and work hardens slightly to point B2. The neutral axis is moved out of the sheet metal. The stress differential ∆σ now approaches zero. Instead of bending or curving outward, the wall simply shortens by a small amount similar to releasing the load on a tensile test sample. This shortening of the wall length can be easily corrected by an increased punch stroke.

Figure 2: The large stress differential shown in Figure 1 is significantly reduced by applying a 2% tensile strain.
Post-Stretch with Stake Beads
Two die design methods currently in use can create the desired minimum 2% post-stretch on the sidewall of AHSS parts, both of which utilize what are commonly referred to as stake beads.
The first method involves retractable beads located in machined slots in the lower blankholder. The upper blankholder has machined stake bead pockets. Adjustable stop blocks located directly under the retractable stake beads can be shimmed to alter the timing when the stake bead engages the stamping, if required.
At the targeted punch stroke position, the retractable beads hit the stop blocks which forces them into the sheet metal flange. This creates a blank locking action while the punch continues to deform the part. As the die opens, the stake beads retract, and the cycle repeats itself from press stroke to press stroke. Adjustability of the draw bead height has advantages, particularly during initial die tryout.
As the retractable beads are inserts, removing them for hardening, coating, polishing, etc., is much easier than moving an entire die to perform bead work. Duplicate inserts can also be made, even utilizing alternative tool steels to increase durability. Locating the retractable stake bead on the blankholder, however, can lead to a larger required blank size. Die construction costs for retractable stake beads are also higher due to the additional machining required.
It is important to have adequate structural die support to avoid breaking the die. Significantly greater lateral thrust forces can cause catastrophic die failure if the stake beads are located too close to the punch opening. This is also true for many other die components, so die construction standards for mild and HSLA steels may not apply to AHSS.
An alternate approach is to locate the stake beads on the punch. Stake beads are machined directly in the punch casting, with the stake bead pockets machined into the upper die cavity. This approach may allow for a reduced blank size, since less material is needed outside the punch opening to accommodate both the draw bead and the stake bead. Figure 3 shows a DP590 B-pillar draw panel with draw beads located on the blankholder and stake beads located on the punch just inboard of the draw beads.

Figure 3: DP590 B-pillar with draw beads on the blankholder and stake beads on the punch. Yellow arrows point to the stake beads; blue arrows point to the draw beads located closer to the edge of the draw panel.
Figure 4 shows a draw die punch with stake beads machined at the very edge of the punch opening, along with the upper die with the stake bead pockets machined out.

Figure 4: Left Image – Stake beads machined into the punch of this DP780 die; Right Image: Stake bead pockets machined into the upper draw die. Note that there are no draw beads on this blankholder.
Draw beads control metal flow in draw dies. However, draw beads may become less functional when forming higher strength sheet steels having higher work hardening characteristics. Here, bending and straightening when pulling the sheet through the punch opening radius, combined with bearing on the binder surface, may be sufficient to control metal flow.
The punch and upper binder in Figure 4 have no draw beads, and instead exhibit stake beads that engage late in the press stroke. This solution is lower in cost but provides limited flexibility since the beads are machined directly into the die. In contrast, Figure 5 shows a die with removable stake bead inserts located on the punch. This approach has improved adjustability, but the added expense of machining the die and installing stake bead inserts.

Figure 5: This die has adjustable stake beads located on the punch as inserts, and do not retract during every press stroke. Note also that there are no draw beads on the blankholder.A-6
A third option to achieve the post forming 2% strain on the part with stake beads involves an additional die or die station. After nearly fully forming the part in the first die, a second die locks the remaining flange in place and further deforms the part by the additional 2%. This approach is expensive since it requires construction of an additional die, or if processed in a progressive die, adding this extra station increases the size and complexity of the progressive die.
Ensuring dimensional precision may require a restrike operation after trimming. In addition to sharpening the radii, the restrike die may provide the sidewall stretch (post-stretch) of approximately 2% required to eliminate curl.
Studies have shown that the height and geometry of the stake bead can impact springback control. Insufficient stretching below the targeted 2% post-stretch may not sufficiently address springback. If the restraining force of the stake bead is too great, it could lead to fracture at the bead or punch opening radius.
Adjusting the stake bead geometry around the part creates an unbalanced post-stretching configuration. Researchers applied this approach to counteract springback in a 3rd Generation steel, with more shallow beads used on deeper drawn sections of the tested part.J-11
The magnitude of springback is a function of the uniformity of the stress distribution through the thickness direction the wall of the formed sheet. An optimized combination of draw beads and stake beads promotes a uniform stress distribution through the thickness, which leads to improved springback control (Figures 6 and 9). Successful simulation provides a range of acceptable combinations of draw bead and stake bead heights.Z-15

Figure 6: A combination of draw beads and stake beads promote a uniform stress distribution through the thickness, leading to improved springback control.Z-15
Press Force and Energy Considerations when using Stake Beads
These post-stretch forming operations normally require significantly higher forming forces and energy requirements to be effective for several reasons.
Any sheet metal will work harden after going through draw beads. Since AHSS grades work harden to a greater degree than conventional high strength steels, the AHSS grades have significantly higher yield strength once the blank has passed over the draw beads. As stake beads are located inboard of draw beads, the stake bead must now deform material with a much higher yield strength due to the work hardening created by the bending and straightening of the material from being pulled through the draw bead.
Since stake beads engage late in the press stroke, their use has similar implications as creating embossments as discussed in a Press Energy case study in the Press Requirements page. This Case StudyH-3 shows that the last increment of punch travel required to finish embossing requires significantly higher energy for AHSS versus conventional mild or HSLA steel. In the current discussion on stake beads, inducing an additional 2% post forming strain into the part will also require higher forming forces and energy requirements, since the forming process work hardened and strengthened the sidewalls. Even if the press has sufficient force and energy characteristics, avoid necking down and tearing the sheet metal as it bends over the punch radius.
Case Studies: Using Stake Beads to Reduce Springback L-1
This case study evaluated springback on specially constructed dies tested using several grades of conventional and advanced high strength steels, including HSLA, dual phase, and TRIP grades with tensile strength ranging from 450 MPa to 980 MPa. One die used the conventional approach, allowing for metal to flow from the flange without a bead. The second die had a recessed square stake bead in the flange that created a post-stretch condition near the end of the stroke. As expected, the post-stretch die resulted in dramatically lower springback (Figure 7). In addition, springback on parts made with this die was not a function of the sheet metal tensile strength, making for a more robust process.

Figure 7: Comparison of two DP 450/750 parts, where stake beads in the bottom part minimized springback. Both images are different angles of the same parts.L-1
Post-Stretch with Hybrid Beads
As seen in the prior figures, the stake beads geometry plays an important role in restricting the metal flow when stretching the sidewalls during the last stages of the punch stroke. This approach requires a larger blank to accommodate the bead, and must be used in a press with sufficient tonnage to set the bead.
A modified approach significantly reduces the blank size requirements as well as lowers the required tonnages to create the bead. It uses stinger beads to penetrate the sheet metal as well as create a wave shape in the deformed region which restricts metal flow. This so-called hybrid bead takes up less than 25% of the bead surface area compared with a conventional stake bead, allowing for a measurably smaller blank. There is no bending over tight bead radii, eliminating the splitting risk at the bead. The restricted metal motion across the beads further minimizes the stress differential between the two sheet steel surfaces, which eliminates a significant root cause of sidewall curl.
Figure 8 highlights the influence a hybrid bead has on springback of a 3rd Generation Steel having a minimum tensile strength of 980MPa.

Figure 8: Hybrid bead dramatically reduces springback in a 3rd Generation steel having 980 MPa minimum tensile strength, while taking up less space and requiring reduced tonnage than stake beads.A-6
Animations of the process sequence is presented in Figures 9 and 10, with more information available in Citations J-12 and W-19.
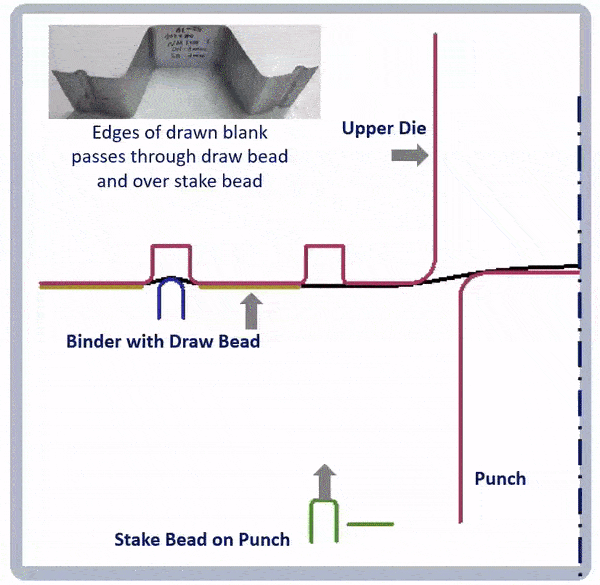
Figure 9: Animation showing a combination of draw beads and stake beads to reduce springback.A-6
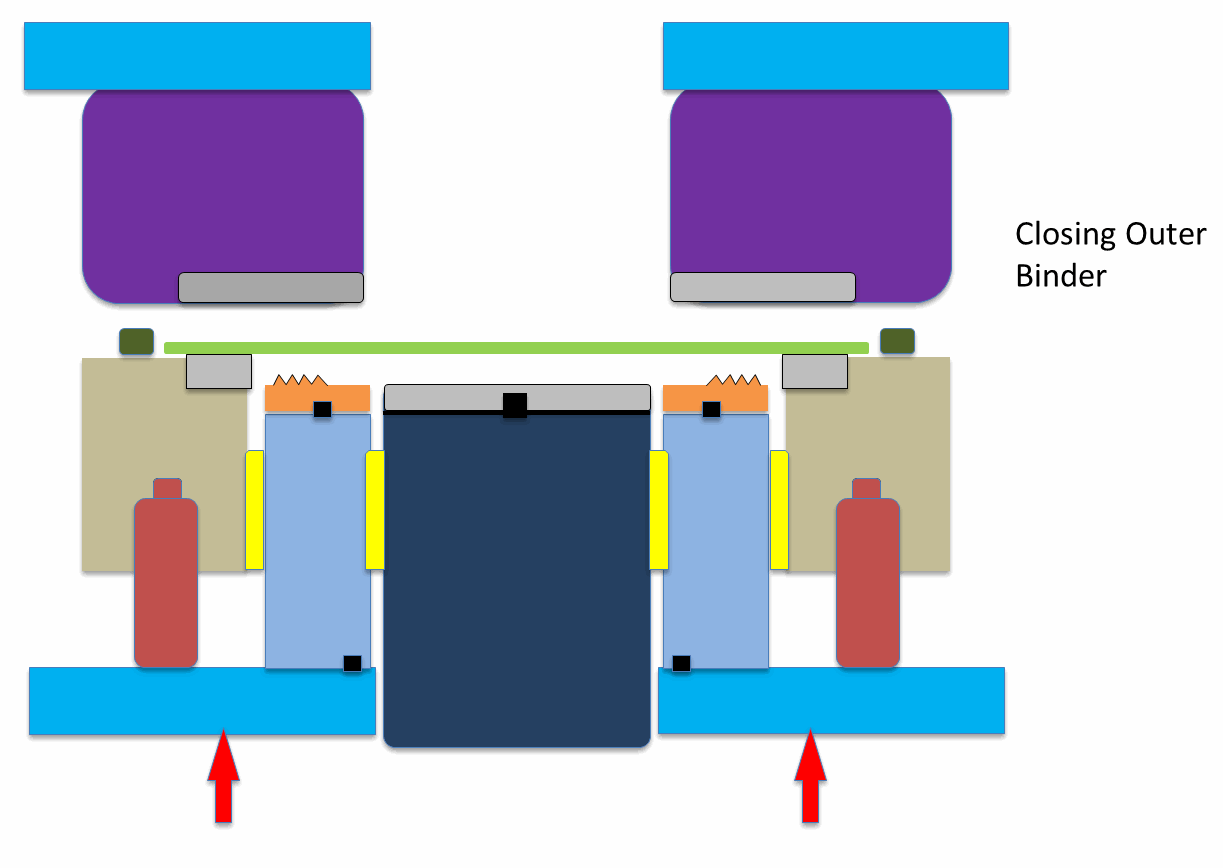
Figure 10: Animation showing application of hybrid beads to reduce springback.A-6
Post-Stretch with Active Binder Force Control
While most stamping processes apply binder pressure uniformly throughout the press stroke, modern stamping presses can be equipped with cushions having multipoint-control systems. Adjusting the associated pressure profile around the panel and throughout the stroke optimizes metal flow, prevent splits and wrinkles, and minimize thinning. This active binder force control capability allows for application of increased blank holder force at any point of the stroke, including at the end to achieve the targeted 2% post-stretch needed to minimize springback. (See the AHSS Insights blog by Dr. Daniel Schaeffler from Engineering Quality Solutions, Inc.)
Beyond simply increasing the blank holder force at the end of the stroke, varying the pressure sequence during the stroke may be beneficial as well. DP 340/590 steel was stamped using a constant binder force, an increasing binder force starting low and finishing high, and a third approach where the initial part of the stroke formed the part with a medium binder force which dropped for most of the stroke but increased at the end to apply the sidewall tension. This third approach resulted in the least angular change and sidewall curl, as seen in Figure 11.

Figure 11: DP 340/590 stamped with constant binder force (top), low-to-high binder force (middle), and medium-to-low-to-high binder force (bottom).P-14
Many angular change problems initiate when constructing the tooling either to part print or without sufficient springback compensation. Achieving targeted dimensions may require over-forming or over-bending.
Use rotary bending tooling where possible instead of flange wipe dies. Rotary bending allows for easy adjustment of the bending angle to correct for changes in springback due to variations in steel properties, die set, lubrication, and other process parameters. In addition, the tensile loading generated by the wiping shoe is absent.
However, if over-bending with flange wipe dies is the chosen approach to minimize angular change, use die radii less than the part radius and use back relief for the die and punch (Figure 12). This approach intentionally subjects the bending radius to compressive stresses between the punch and die. The squeezing and associated thinning at the bend radius results in plastic deformation of the sheet steel, with little elastic recovery after unloading from the press.

Figure 12: Providing back relief on the flange steel and lower die aids over-bending.A-2
Cross section design for longitudinal rails, pillars, and cross members impacts the effectiveness of springback compensation methods. The rail cross section in sketch A of Figure 13 does not allow the use of over-bending for springback compensation in the forming die. In addition, this design likely leads to severe sidewall curl in AHSS channel-shaped cross sections. Minimize these quality issues by designing a cross section that allows for over-bending during forming, as shown in sketch B. Reduced sidewall curl is another benefit of this cross-sectional design. Springback allowance must increase as strength increases. Typical wall opening angles are 3-degrees for Mild steel, 6 degrees for DP 350/600 and 10 degrees for DP 850/1000 or TRIP 450/800. In addition, the cross section in sketch B will have the effect of reducing the impact shock load when the draw punch contacts the AHSS sheet. The vertical draw walls shown in sketch A require higher binder pressures and higher punch forces to maintain process control.

Figure 13: Changing a rail cross section from A to B allows easier over-bending for springback control.N-3
Producing closed box sections involves welding two channel sections together at their flanges. Hat-sections with 90-degree corners such as seen in sketch A of Figure 14 will experience many production problems since each component will have issues with sidewall curl and angular change. The hexagonal section in sketch B will reduce sidewall curl and twist problems, while permitting over-bend for springback compensation in the stamping dies.

Figure 14: Changing the design of a closed cross section from A to B leads to a reduction in springback problems.N-3
Adding extra stages to the forming process allows for secondary operations to return a sprung part back to nominal dimensions. For example, Figure 15 shows a process where a crown existing in the first step when forming a channel section uses a second die for flattening and eliminating sidewall springback.

Figure 15: Schematic showing how flattening a crown corrects angular springback.A-3
As a related process, multiple stage forming (Figure 16) is an option to minimize springback and improve dimensional accuracy when stamping rails or other parts with a hat-shaped cross section consisting of right angles. This processing approach creates a design which avoids re-working previously-formed (and therefore work hardened) sections.
In the first operation, all 90-degree radii and mating surfaces are formed using “gull-wing” processes with over bending to compensate for springback. The larger radius in the top of the hat section gets flattened in the second stage. Certain cases may require an over bending of the flat top section.
Multiple-stage forming also helps when forming parts having small geometrical features of severe geometry that can be formed only in the re-strike operation. A part that has a variable cross section in combination with small geometrical features may need a coining operation in the second or last stage of the forming process. This may be the only way to control the geometry.

Figure 16: Two-stage forming produces a dimensionally accurate hat section with relatively small radii.R-1
Correcting Springback by Reducing or Minimizing the Elastic Stresses
The process design, and therefore the tooling design, can drastically affect the level of the elastic stresses in the part.
As an example, different blankholder actions provide four possible processes to form a hat-profile channel, each with different dimensional accuracy (Figure 17). The four processes are:
- Draw: the conventional forming type with continuous blankholder force and all blank material undergoing maximum bending and unbending over the die radius. This forming mode creates maximum sidewall curl.
- Form-draw: a forming process in which application of the blank holder force occurs between the middle and last stage of forming. It is most effective to reduce the sidewall curl because this approach minimizes bend unbend deformation at the beginning of the stroke prior to application of any blank holder force. Applying a large tensile stress during the last stage of forming creates the post-stretch condition to further minimize curl.
- Form: a process where the flange is created during in the last stage of forming and the material undergoes only a slight amount of bend-unbend deformation. Depending on the part geometry, the lack of a blankholder may lead to wrinkles.
- Bend is a simple bending process to reduce the sidewall curl, which avoids the bend and unbend sequence associated with sidewall curl. However, this approach likely leads to an angular change in the sidewall.

Figure 17: Four processes for generating a channel for bumper reinforcement create different levels of elastic stress and springback.K-5
Correcting Springback by Locking in the Elastic Stresses
Where part design allows, geometrical features like darts, beads, and stiffeners prevent the release of the elastic stresses and reduce various forms of springback. Minimize twist by adding strategically placed vertical beads, darts, or other geometric stiffeners in the shorter length wall to equalize the length of line.
Applying these features in a restrike operation may not be possible due to equipment or design limitations, since the yield strength of the sheet metal increases after work hardening. In the case of AHSS grades, this work hardening leads to a dramatic increase in strength.
Any elastic stress locked into the panel remains in the part as residual or trapped stresses. Subsequent forming, trimming, punching, heating, or other processes may unbalance the residual stress and change the part shape. For these reasons, the full process needs to be simulated, incorporating both material and geometrical changes occurring in all prior operations.
Figures 18 to 22 present examples of how elastic stresses can be locked into the part to control for springback.

Figure 18: Geometrical stiffeners like flanges or beads lock elastic stresses into the part, fixing the part shape.A-2

Figure 19: B-pillar using stiffening darts to control springback.A-41

Figure 20: Step flange locks in elastic stresses on a draw wall.A-41

Figure 21: Hat section showing the effects geometrical features have on controlling springback. Angular change and sidewall curl are noticeably less pronounced on the left side having the vertical beads, compared with the right side where no springback mitigation methods were employed.K-14

Figure 22: DP600 front rail upper reinforcement with vertical beads designed into the part geometry for springback control.F-9
An American Iron and Steel Institute study defined several tool and process parameters that reduced angular change and side wall curl (Figures 23 and 24). As expected, angular change and curl increase with yield strength. Tighter clearances, smaller punch radii, and higher drawbead restraining forces reduced both types of springback.S-47

Figure 23: The effect of tool parameters in angular change. The lower values are better.S-47

Figure 24: The effect of tool parameters in sidewall curl. Higher values of radius of curl are better.S-47
Figure 25 highlights the importance of keeping the die clearance as tight as allowed by formability and press capability. Unwanted bending and unbending work hardens the sheet metal and promotes increases in springback.

Figure 25: Reducing die clearance restricts additional bending and unbending as the sheet metal comes off the die radius, minimizing angular change.Y-2
Figure 26 illustrates that angular change increases dramatically for higher strength steels as the bend radius increases. Minimizing angular change requires designing the punch radius as sharp as formability and product/style allows. However, with AHSS grades, sharp radii may promote the local formability failure mode of shear fracture. Inside product feature radii should be a minimum of 3T for any AHSS grade having a tensile strength at or above 590 MPa. Die radii at draw beads, punch openings, etc., where the material is pulled under tension over a radius should be at least 5T for any AHSS grade over 590 MPa. Minimum bend radii requirements may be even greater as strength levels continue to increase, roll forming excluded. To avoid problems due to specifying the wrong AHSS grade for the wrong application, bend testing and hole expansion testing should be used in conjunction with close communication with the steel supplier when selecting the proper die radius for the intended AHSS material. In addition, sharp radii contribute to excessive thinning at the tangent to the radius when global formability failures are of concern.

Figure 26: Angular change increases with yield strength and bend radius at a constant thickness.S-2
Case Study in Springback Reduction Strategies
Automakers face conflicting constraints of lightweighting while improving safety performance. The B-Pillar Inner plays a significant role in meeting ever-increasing roof crush and side impact performance requirements. A studyM-17 published in 2007 showed the tooling and design changes made when transitioning from HSLA 340/440 to DP 550/980. These changes, shown in Figure 27, include adding sidewall beads to control springback, along with geometry to improve section stiffness.

Figure 27: Strategies to reduce springback in a DP 550/980 B-Pillar Inner.M-17
Another approach is highlighted in a Webinar from 2020.S-105 When forming hat-shaped sections, sidewall curl is minimized by using a cam to form the sidewall-flange area, followed by a more conventional sidewall stretch at the end (Figure 28). The animation in Figure 29 shows the process.S-6

Figure 28: Cam bending of sidewall-flange area minimizes springback.S-105
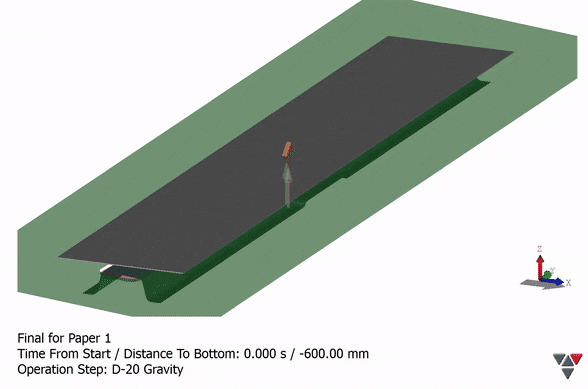
Figure 29: Animation of hat-section forming process to minimize springback.S-6
Compressive Stress Superposition for Springback Reduction
As explained above, springback and curl initiate when there are tensile stresses on one surface and compressive stresses on the other surface of the sheet. One of the keys to springback reduction is balancing these stresses through the sheet thickness.
A patented process known commercially as Smartform® relies on compressive stress superposition to achieve this stress balance. B-76 , L-65, B-77,, V-23
Achieving compressive stress superposition uses a two-step process where in the first preform step, the blank is formed into a “U” shape having a similar contour to the finished component, and then a sizing step to adjust the dimensional accuracy. This second step compresses the sheet metal during sizing rather than making it thinner from a drawing operation.
In the preforming stage (OP20), geometrical flexibility in the design of the tool surface exists, as the final component contour is not set until the sizing calibration stage (OP30). This allows for enlarged radii and wall angles to be used as countermeasures to prevent wrinkling and cracks.
Since the preform is not drawn, the starting blank can be cut to almost the same size as its final geometry before it is formed, reducing the number of trimming operations in the die process, as well as the amount of material used. Reportedly, an average of 15 percent materials savings occurs relative to conventional types of forming, with the actual savings being dependent on the size and complexity of the component.
Another benefit: resulting from the way the stress balance is achieved, this technology is relatively insensitive to variations in sheet metal properties, leading to a highly robust process.
Compressive stress superposition has been shown to work for steels having minimum specified tensile strength of 590 MPa through 1180 MPa.
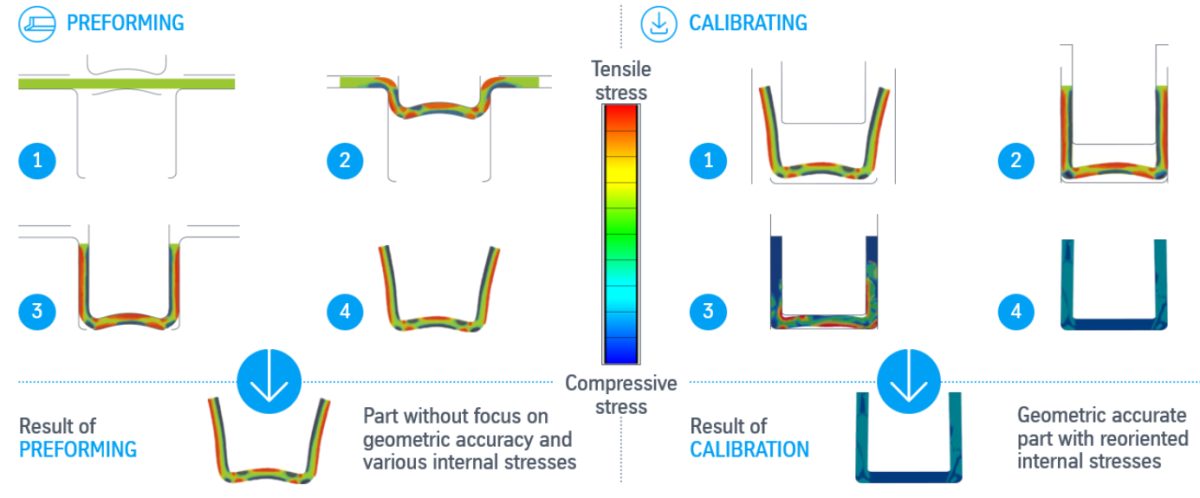
Figure 30: Compressive Stress Superposition Stress Conditions. Left: Preforming (OP20). Right: Sizing and Calibration (OP30). L-65
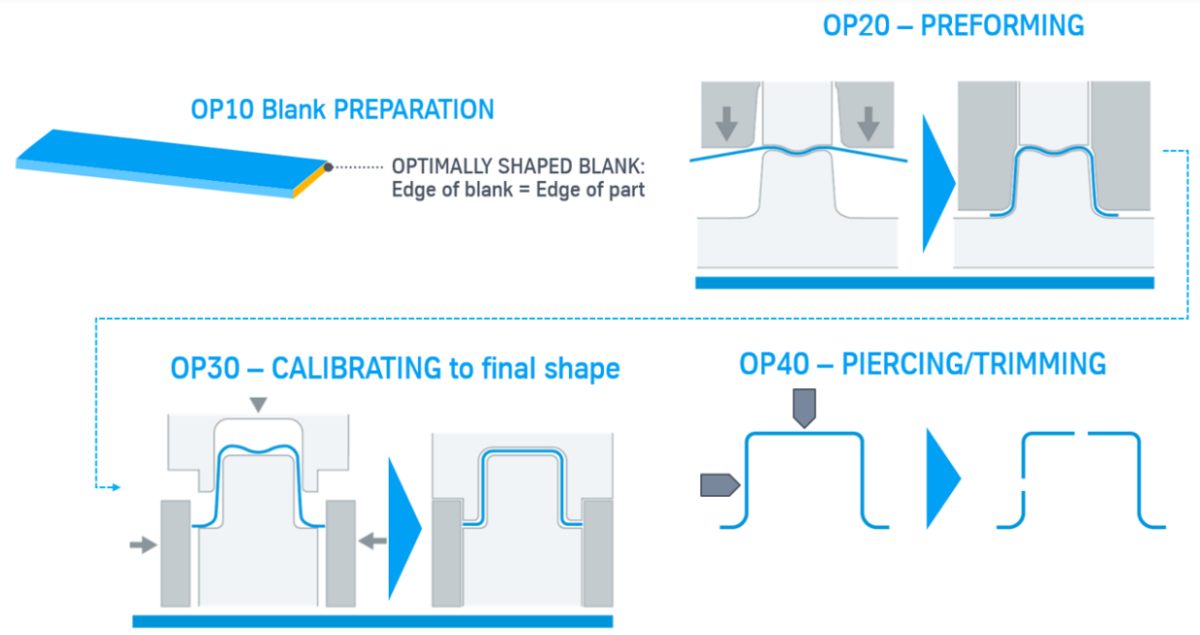
Figure 31: Compressive Stress Superposition Die Process.L-65
Key Points
Several process and design modifications remove (or at least minimize and stabilize) the different modes of springback found in channels and similar configurations:
- Open wall angles achieved with minimized metal flow over die radii minimize angular change and sidewall curl.
- Overbending accounts for angular change, allowing the part to spring back to the targeted dimensions. Subjecting the bending radius to compressive stresses at the bottom of the press stroke plastically deforms the sheet metal, minimizing the elastic stresses associated with springback. Note that this approach is less successful in addressing sidewall curl.
- Applying in-plane tension to the side walls after forming reduces springback. Methods include using stake-beads, hybrid beads, or active binder force control. However, with higher strength steels, it may be difficult to achieve sufficient stretch to the sidewall by simply increasing the blank holding force. Preventing metal flow into the wall during post-stretching may require lock beads. Bead geometry affects blank size and press requirements.
- Geometric stiffeners like darts, beads, and flanges lock elastic stresses in place preventing springback from occurring. Subsequent forming or trimming operations may relieve these stresses, resulting in dimensional distortion. In addition, the selected press must have the load and energy requirements to form these features.
Design the part and tool in such a way that springback is desensitized to variations in material, gauge, tools and forming processes (a robust system and process) and that the effects of springback are minimized rather than attempt to compensate for it.
The accuracy of forming simulation programs to predict springback continues to improve, especially if it incorporates a complete material characterization and the chosen model is appropriate for the challenges of the specific part and forming method. Even without full accuracy, springback simulations can predict the trend and test the effectiveness of proposed countermeasures. In all cases, verify predictions against physical measurements.
Back To Top
Press Hardened Steels
In its simplest explanation hot stamping consists of five operations: (1) blanking (or cutting-to-length), (2) forming, (3) heating, (4) cooling (quenching) and (5) trimming/piercing. Each process route listed below has a distinct order or type of these operations.
In most sources, hot stamping is explained with only two processes: Direct hot stamping (also known as Press Hardening) and indirect hot stamping (also known as Form Hardening). While this used to be accurate, there are currently at least 10 processes for part manufacturing:
- Direct Process (Blanking > Heating > Forming > Quenching > Trimming)
- Indirect Process (Blanking > Forming & Trimming > Heating > Quenching > Trimming)
- Hybrid Process (Blanking > 1st Forming > Heating > 2nd Forming > Quenching > Trimming)
- Pre-cooled Direct Process (Blanking > Heating > Pre-cooling > Forming > Quenching > Trimming)
- Multi-Step Process (Blanking > Heating > Pre-cooling > Forming and Trimming > Air Quenching)
- Form Fixture Hardening (Roll Forming > Cut-to-length > Heating > Bending forming > Quenching > Trimming / piercing)
- Roll Form PHS (Roll Forming > Heating > Quenching > Cut-to-length > Trimming & piercing)
- Form Blow Hardening / Hot gas metal forming (Cut-to-length tube or roll formed / welded profile > Heating > Pressure forming > Quenching > Piercing)
- 3DQ (Cut-to-length tube > Local induction heating > 3-D Bending > Direct Water Quenching > Piercing)
- STAF (Cut-to-length tube > Cold preforming > Heating > Pressure Forming > Quenching > Piercing)
The video below explains some of these processes and how they are employed at Gestamp Automoción. Here, Paul Belanger, Director of Gestamp’s North American R&D Center, was interviewed by Kate Bachman, the Editor of STAMPING Journal®. Thanks are given to Paul and Kate, as well as FMA, Fabricators & Manufacturers Association®, for permission to reproduce this video.
Direct Process
The most common process route in hot stamping is still the direct process (also known as press hardening).D-20 Here, previously cut blanks are heated typically in a roller hearth or a multi-chamber furnace to over 900 °C to create a fully austenitic microstructure. Depending on the material handling system, transfer from the furnace to the press may take up 6 to 10 seconds.B-14 During this time, the blank may cool down to 700 °C.G-24 Forming is done immediately after the blanks are transferred on the die, and should be completed before the blank cools below 420 °C.G-24, K-18 The blanks are formed in hot condition (state ❷ in Figure 1), and quenched in the same die to achieve the required properties. For 22MnB5 steel, if the quenching rate is over 27 °C/s, the part will transform to almost 100% martensite. For productivity purposes, higher cooling rates are often realized.K-18 Typical cycle times for a direct process with the 22MnB5 chemistry could be between 10 and 20 seconds, depending on the thickness.B-14 Global R&D efforts target improvements in cycle time.
The process is typically used for bare/uncoated steels or AlSi coated steels. Zn coated blanks are not suitable for direct process, as pure Zn melts around 420 °C and GA (Zn-Fe) coatings around 530-780 °C. (see Figure 3)G-25 If forming is done with liquid Zn over the blank, microcracks may fill with Zn and lower the fatigue strength of the final part significantly.K-20 A recently developed alloy minimizes these concerns, as explained in the “Pre-cooled Direct Process” section below.
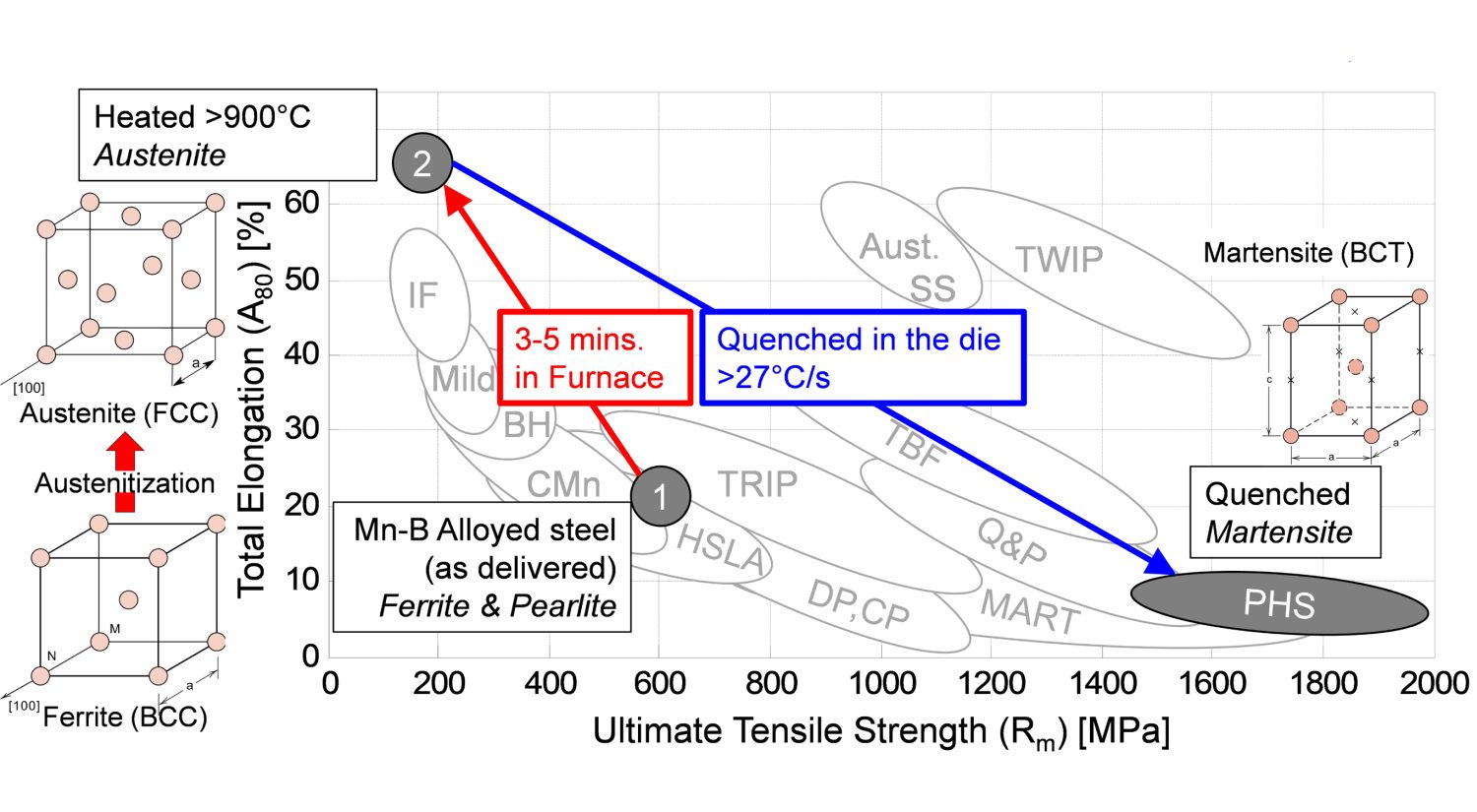
Figure 1: Summary of hot stamping processes. In direct process forming is done at state ❶, in indirect process at ❷B-14
Typical Al-Si coatings prevent scale formation and decarburization at elevated temperatures. The aluminum-rich coating contains 7% to 11 wt.% Si, and acts as a barrier to offer corrosion resistance during service.F-14 In automotive industry, typical coating weights are AS150 (75 g/m2 coating on each side) or AS80 (40 g/m2 coating on each side).A-51 Refer to our page on Al-Si coatings for more details.
When using uncoated blanks, controlled atmosphere in the furnace helps avoid excessive decarburization and scale formation. Surface scale locally changes the critical cooling rate, alters the metal flow and friction, and leads to premature tool wear. Without a controlled atmosphere, a surface conditioning step like shot blasting may be required after forming to remove the scale.A-52 Varnish coatings may also be used with direct hot stamping.
Formed parts must be trimmed and pierced to final geometry. In the direct process, the most common trimming method is laser cutting. The capital expense and cycle times associated with laser trimming factor into overall part cost calculations. In most plants, for every hot stamping line, there are 3 to 5 laser trimming machines.B-14
The grades used with the direct process may be referred to as PHS950Y1500T-DS (Press Hardening Steel with minimum 950 MPa yield, minimum 1500 MPa tensile strength, for Direct [Hot] Stamping).
Indirect Process
(Blanking > Forming & Trimming > Heating > Quenching > Surface Conditioning)
Typically used for galvanized blanks, indirect hot stamping, also known as form hardening, starts by cold forming the part (at ❶ in Figure 1) in a transfer press or a tandem transfer line. The direct process is limited in that only one forming die can be used. However, the indirect process can accommodate multiple die stations, allowing for the production of more complicated geometries, even those with undercuts. The part has almost the final shape exiting the cold forming press, where piercings and trimming could also be completed. The formed parts are then heated in a special furnace and quenched in a second die set.B-14,K-21,F-15
BMW 7 Series (2008-2015, codenamed F01) was the first car to have Zn-coated indirect hot stamped steel in its body-in-white.P-20 Zn-based coatings are favored for their cathodic protection. Zn-coated blanks may develop a thin oxide layer during heating, even if a protective atmosphere is used in the furnace. This layer helps preventing evaporation of the Zn (pure Zn evaporates at 907 °C at 1 atm. pressure), but must be removed before welding and painting. To achieve this, sandblasting, shot blasting or dry-ice (CO2) blasting are typically used.F-14, F-15 The grades for indirect process may be referred to as PHS950Y1500T-IS (Press Hardening Steel with minimum 950 MPa yield, minimum 1500 MPa tensile strength, for Indirect [Hot] Stamping).
The indirect process cannot be applied to Al-Si coated blanks, as they have a hard but brittle intermetallic layer which would crack during cold deformation.F-14
Hybrid (2-Step) Process
(Blanking > 1st Forming > Heating > 2nd Forming > Quenching > Trimming > Surface Conditioning)
In this process, as summarized in Figure 2, some of the forming occurs at the cold stage [❶ in Figure 1]. The semi-formed part then is heated in the furnace, significantly deformed to a final shape [❷ in Figure 1] and subsequently quenched in the same die. This process had found greater use in Europe, especially for deep drawn parts such as transmission tunnels. To avoid scale formation in the furnace and hot forming, a special varnish-type coating is commonly used. The final part must be surface cleaned with a process like shot blasting before welding to remove the varnish coating.S-63 Since the early 2010s, the process has been replaced by the direct process of Al-Si-coated blanks.N-15
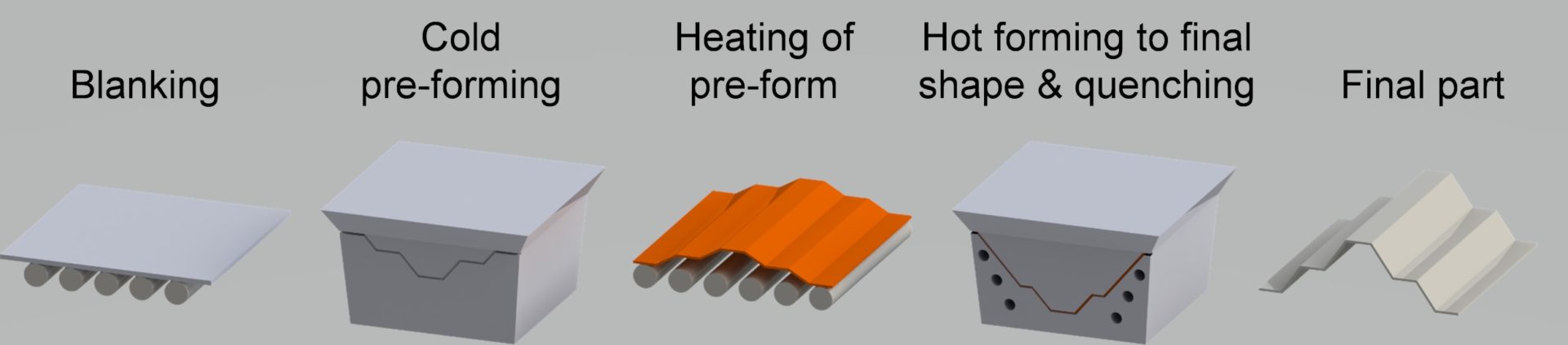
Figure 2: Summary of “hybrid process” where deformation is done both at cold and hot conditions.B-14
Pre-Cooled Direct Process
(Blanking > Heating > Pre-cooling > Forming > Quenching > Trimming > Surface conditioning)
A galvannealed (GA) coating primarily contains zinc and iron, and solidifies at temperatures between 530 °C and 782 °C, depending on the zinc content, as shown in Figure 3. Liquid Metal Embrittlement (LME) is not a concern if forming is done in the absence of liquid zinc.G-25 Hensen et al. conducted several studies heating galvannealed 22MnB5 blanks to 900 °C, but forming after a pre-cooling stage. As seen in Figure 4, the microcrack depth is significantly reduced when the forming starts at lower temperatures.H-26
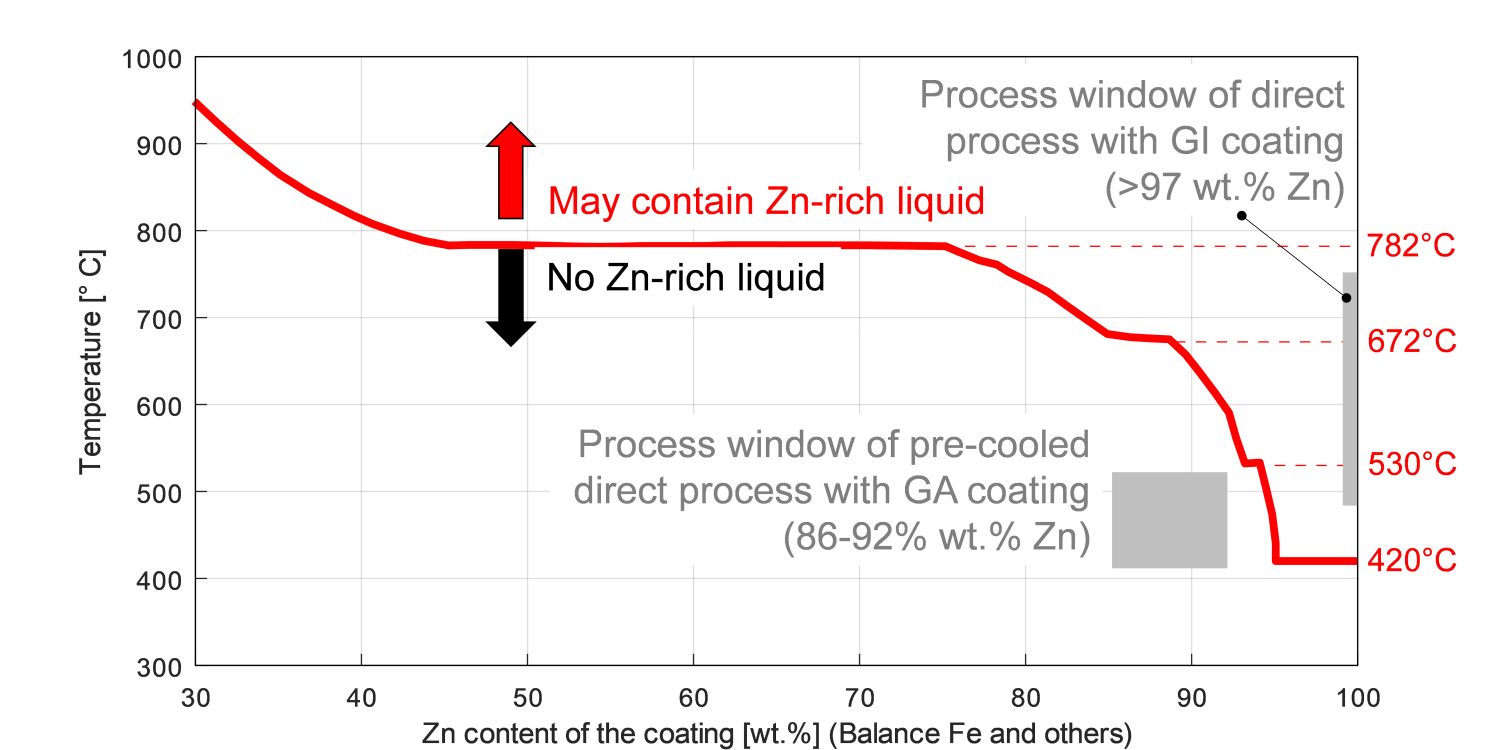
Figure 3: Temperature limit to ensure absence of Zn-rich liquid (re-created after Citations G-25 and G-26)
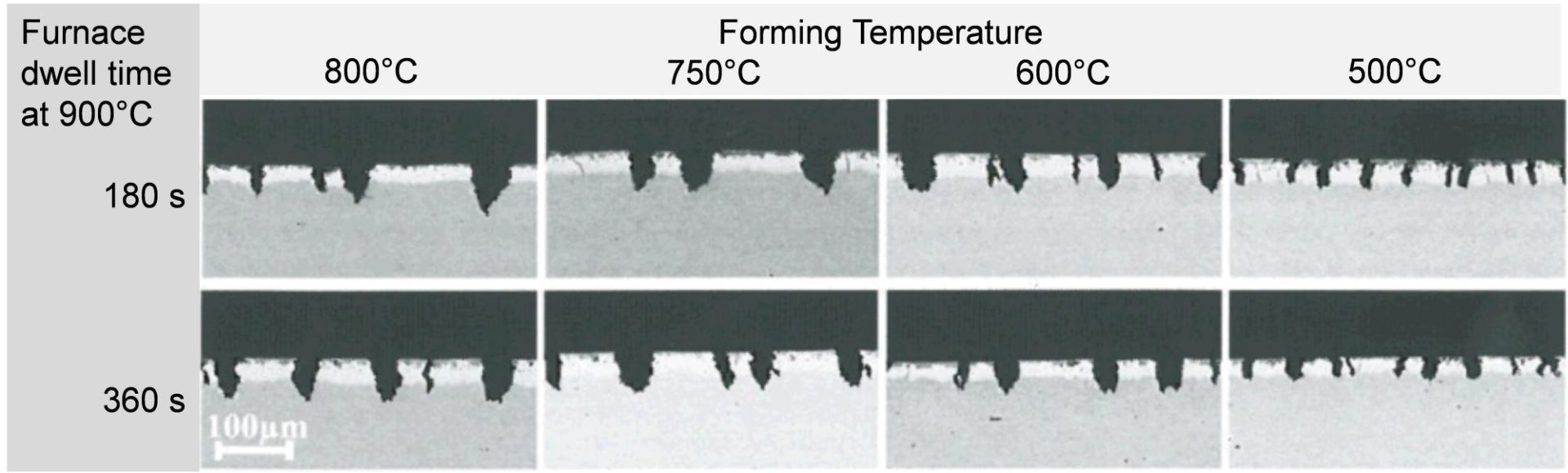
Figure 4: Crack depth reduces significantly if the forming is done at lower temperature (re-created after Citation H-26)
In the pre-cooled direct process, the blank is heated above the austenitization temperature (approximately 870-900 °C), and kept in the furnace for a minimum soaking time of 45 seconds. Once the blank leaves the furnace, it is first pre-cooled to approximately 500 °C and then formed. Typical 22MnB5 cannot be formed at this temperature due to two reasons: (1) its formability would be reduced and (2) forming could not be completed before the start of martensite formation at approximately 420 °C).K-22, V-8
The development of a “conversion-delayed” hot stamping grade (see PHS Grades with approximately 1500 MPa TS), commonly known as 20MnB8, addresses these concerns. This steel has lower carbon (0.20%, as the number 20 in 20MnB8 implies), but higher Mn (8/4 = 2%). . This chemistry modification slows the kinetics of the phase transformation compared with 22MnB5 – the critical cooling rate of 20MnB8 is approximately 10 °C/s. This allows the part to be transferred from pre-cooling stage to the forming die.
In the pre-cooled direct process, first the blank is heated to over 870-900 °C and soaked for at least 45 seconds. Then the blank is transferred to “pre-cooling stage” in less than 10 seconds. Precooling must be done at a rate over 20 °C/s, until the blank is cooled to approximately 500 °C. Then the part is transferred from the pre-cooling device to the press in less than 7 seconds. The forming is done in one hit in a hydraulic or servo-mechanical press, which can dwell at the bottom. The cooling rate after pre-cooling is advised to be over 40 °C/s. The final part may have zinc oxides and surface cleaning is required.K-22, V-8 The grade may be referred to as PHS950Y1500T-PS (Press Hardening Steel with minimum 950 MPa yield, minimum 1500 MPa tensile strength, Pre-cooled and Stamped).
Recently, several researchers have shown that pre-cooling may be used for drawing deeper partsO-6 or to achieve better thickness distribution of the final part.G-24 Since formed parts are typically removed from the press at approximately 200 °C, a pre-cooled part may require shorter time to quench, thus increasing the parts per minute.G-24
Multi-Step Process
(Blanking > Heating > Pre-cooling > Forming and Trimming > Air Quenching)
22MnSiB9-5 (see PHS Grades with approximately 1500 MPa TS) is a new steel grade developed by Kobe SteelH-27 for a transfer press process, named as “multi-step”. This steel has higher Mn and Si content, compared to typical 22MnB5. As quenched, the material has similar mechanical properties with 22MnB5. As of 2020, there is at least one automotive part mass produced with this technology and is applied to a compact car in Germany.G-27 Although critical cooling rate is listed as 2.5 °C/s, even at a cooling rate of 1 °C/s, hardness over 450HV can be achieved.H-27 This critical cooling rate allows the material to be “air-hardenable” and thus, can handle a transfer press operation (hence the name multi-step) in a servo press. This material is available only with Zn coating and requires a pre-cooling step before the transfer press operation.B-15 The grade may be referred to as PHS950Y1500T-MS (Press Hardening Steel with minimum 950 MPa yield, minimum 1500 MPa tensile strength, for Multi-Step process).
(Roll Forming > Heating > Quenching > Cut-to-length > Trimming & piercing)
Also known as inline hardening, this process is used to make profiles with constant cross sections and linear shapes. It is also possible to have closed profiles (tubes and similar) with this technology by adding a laser welding to the line (see Figure 5a). The process has been successfully used in many car bodies. Typical uses are: cross members, roof bows, side impact door beams, bumpers (with no sweep), front crash components and similar.G-28, H-28, F-16
![Figure 5: Roll form PHS: (a) steps of the line [24], (b) photo of the induction heated area.G-28](https://ahssinsights.org/wp-content/uploads/2020/12/Figure-5-Roll-form-PHS.jpg)
Figure 5: Roll form PHS: (a) steps of the lineH-28, (b) photo of the induction heated area.G-28
The heating is typically done with induction heating, see Figure 5b. In one of the installations, the first induction coil operates at 25 kHz and the second at 200 kHz. The total heating power was approximately 700 kW and the line can run as fast as 6 m/s. It was found that if lubrication, speed and bending radius can be optimized, AlSi coated blanks could also be cold roll formed. However, they are not suitable for induction heating and may require a different process, such as form fixture hardening.K-23
Recently, voestalpine developed a Zn-coated steel for roll forming applications. This process also uses induction heating and water cooling. As the deformation is done at cold condition, the parts do not suffer from liquid metal embrittlement (LME).K-22
(Roll Forming (or tube blank) > Cut-to-length > Heating > Bending & forming > Quenching > Trimming / Piercing)
The main difference between roll form PHS and form fixture hardening is the secondary “hot bending and forming” in the press. Here, cold roll formed profiles are cut-to-length and heated in a furnace. Heated profiles are then transferred to a press die, where sweep bending and/or further forming operations are completed. The parts are subsequently quenched in the same press die, similar to direct process. A typical line layout can be seen in Figure 6a. The secondary forming makes variable sections possible, as seen in Figure 6b. As the parts are cold roll formed and furnace heated, uncoated, Zn-coated and AlSi-coated (with precautions not to crack AlSi) blanks may be used in this process.H-28, K-23
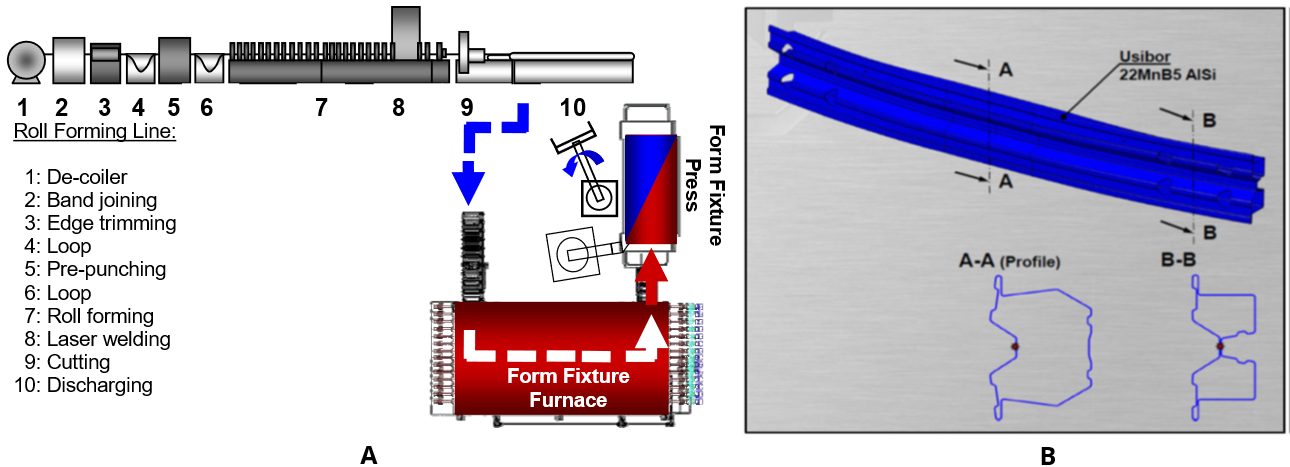
Figure 6: Form fixture hardening: (a) schematic of a lineK-23, (b) bumper beam of Ford Mustang (2004-2014) made by this process.L-26
Form fixture hardening parts have been used in low volume cars such as Porsche 911 or Bentley Mulsanne. In some cars, form fixture hardening was used to manufacture the A-pillar of the convertible (cabriolet) versions of high-volume cars, especially in Europe. Most of these applications involved uncoated boron alloyed tubes (similar to 22MnB5).H-28 The 5th generation Ford Mustang (2004-2014) had form fixture hardened bumper beams in the front and rear, as seen in Figure 6b.L-26 The form fixture hardening process allows for use of AlSi coatings, since the steel goes through a furnace rather than an induction hardening step. Special care must be taken in cold roll-forming process to ensure the AlSi coating is not damaged.K-23
(Cut-to-length tube or roll formed and welded profile > Heating > Pressure forming > Quenching > Piercing)
In hot gas metal forming, the tube or roll formed closed profile is heated first and placed onto a die set. The ends of the tube are sealed and pressurized gas or granular medium is forced inside the tubular blank. The forming forces are applied by the high pressure built inside the tube.C-16 It is also possible to end-feed material as in the case of (cold) tube hydroforming. After the deformation, the part is quenched either with water (form blow hardening) or by the air inside and the surface of the tool cavity (hot gas metal forming). In the latter case, similar to direct process, a water-cooling channel system inside the die inserts are typically required.K-23
Fraunhofer IWU has developed a hot gas metal forming setup in which both forming and quenching are done by compressed air. As shown in Figure 7a, the internal pressure can be increased to 70 MPa (700 bars) in only 6 seconds. The tools are cooled with internal cooling channels, Figure 7b. The parts produced with this technique have hardness values between 460 and 530 HV. Crashbox and camshafts are among the parts produced.L-27, N-16
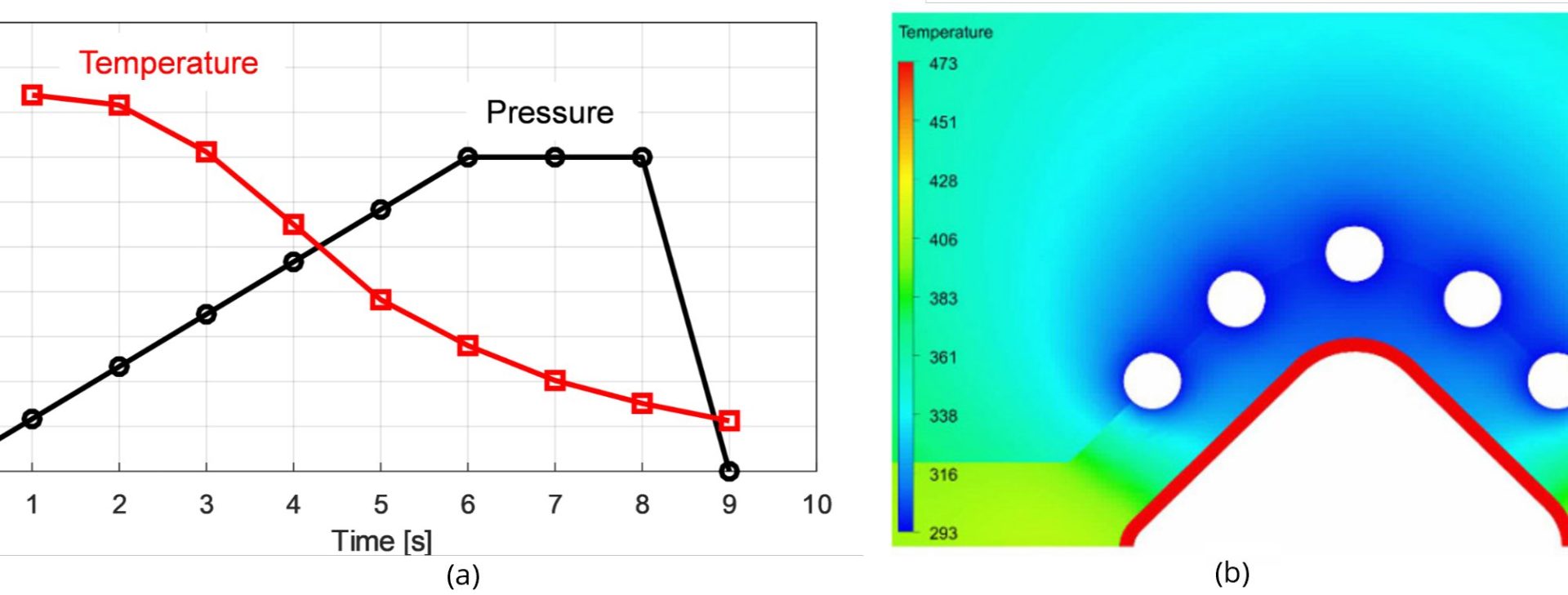
Figure 7: Blow forming and quenching with air: (a) change of pressure in the tube and temperature of the tube, (b) simulation of heat transfer to the dies and cooling channels (recreated after Citation N-16)
In 2011, Spanish car maker SEAT published a study on form blow hardening process. In this study, they replaced the A-pillar and cantrail assembly of the SEAT León (Mk2, SOP 2005) with one form blow hardened part. The results were summarized asO-7:
- 7.9kg weight reduction per car,
- Sheet material utilization increased from 40 to 95%,
- Number of components in the assembly on one side of the car reduced from 5 to 2, and the roof rail was eliminated.
One advantage of this technology is the possibility to use the same die set for different wall thickness tubes. By doing so, parts can be produced for different variants of a car (i.e., coupe and cabrio, or North American spec. vs. emerging market spec.). This information applies to monolithic (i.e., same thickness throughout the tube) and tailor rolled/welded tubes as well.F-16 In 2017, tubular parts are hot gas formed by using 1900 MPa PHS tubes for customer trials.F-17
Since 2018, form blow hardening is being used in the Ford FocusB-16 and Jeep Wrangler.B-17 In the Ford Focus, a tailor rolled tube with thicknesses between 1.0 and 1.8 mm is used in Europe, whereas in China it is a monolithic (same thickness everywhere) 1.6 mm thick tube.F-16
3-Dimensional Hot Bending and Quenching (3DQ)
(Cut-to-length tube > Local induction heating > 3-D Bending > Direct Water Quenching > Piercing)
In the 3DQ process, a tubular profile with constant cross section is quickly heated by induction heaters. By using movable roller dies, the part is bent. As the material is fed, water is sprayed on the induction heated portion of the tube to quench and harden it. The schematic of the process and the material strength through the process is illustrated in Figure 8. It is also possible to replace the movable roller dies with an industrial robot to bend and twist the tubular part.T-25
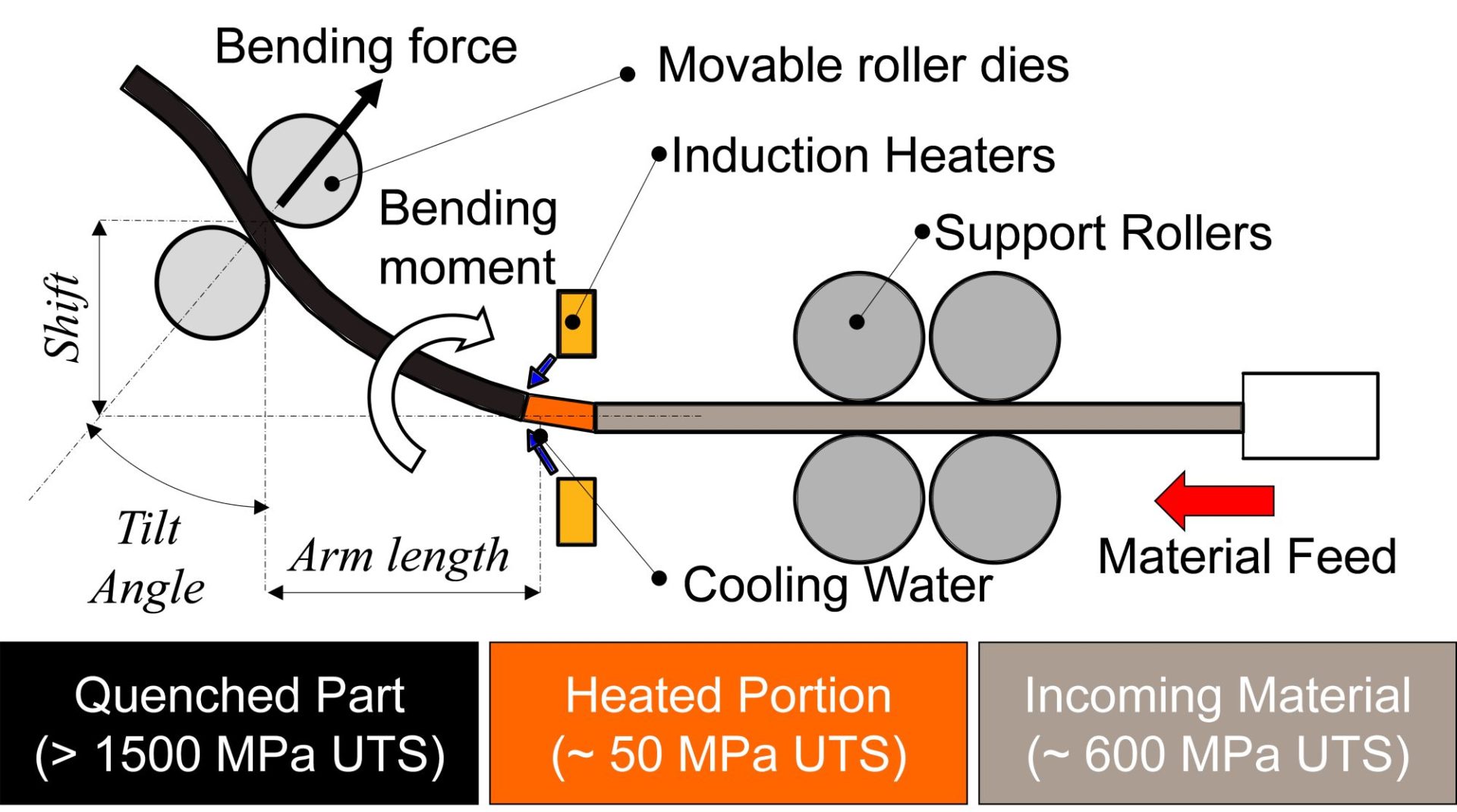
Figure 8: Schematic of 3DQ system (re-created after Citation T-25)
In January 2013, Mazda announced that the ISOFIX connection in the rear seats of a Premacy MPV (known as Mazda 5 in some markets) model was produced by this method, as shown in Figure 9a.M-24 In 2016, Honda started production of the sports car NSX (known as Acura NSX in some markets). This vehicle’s A-pillars were produced by 3DQ process, as shown in Figure 9b.H-29
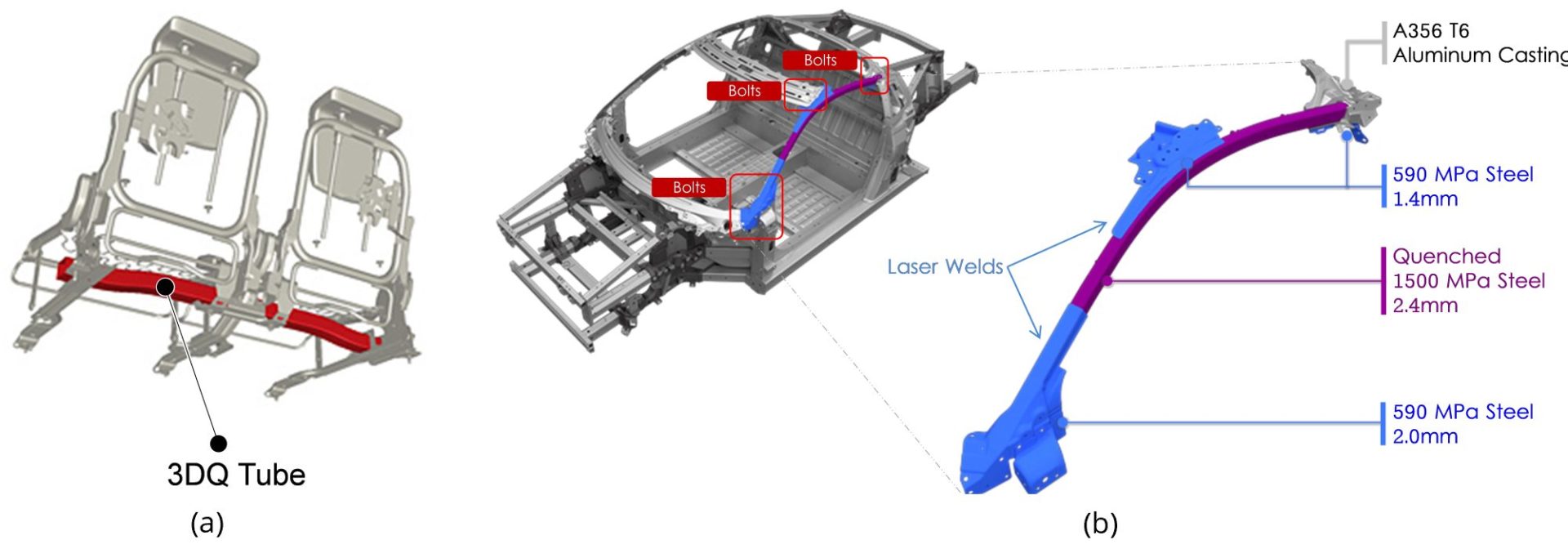
Figure 9: 3DQ applications: (a) Seat reinforcement of Mazda 5/PremacyM-24, (b) Acura NSX’s A-pillar.H-29
The technology has been used on uncoated blanks. In 2019, an academic study showed the feasibility of using Zn coated blanks in the 3DQ process.R-10
Steel Tube Air Forming process (STAF)
(Cut-to-length tube > Cold bending > Heating > Press Forming > Pressure Forming > Quenching > Piercing)
Steel Tube Air Forming process (STAF) is a modified and enhanced version of hot gas metal forming. In the STAF process, a metal tube is bent in a small press at room temperature. The preformed tube is transferred to the main press, where it is heated to the critical temperature using electrical conduction (Joule heating) by passing current through the tube. The first step creates the flanges where the press closes on the partially air blow formed tube. In the second step, air pressure completes the process by forming the desired cross section and overall shape.
As seen in Figure 10, the parts made with the STAF process can have a flange area for further welding/joining to other car body components. Some peripheral parts can be integrated into a single STAF part, improving productivity and manufacturing cost. The continuous closed cross section is created without the need for spot welding, improving stiffness and further reducing manufacturing costs. These factors combine to result in mass savings compared with conventional hot formed components, as indicated in Figure 11. F-18, F-41, F-42

Figure 10: The Steel Tube Air Forming process compared with other manufacturing approaches. STAF integrates flange formation without the need for additional spot welding.F-42 HSS stands for High-Strength Steel and may refer to conventional HSS or Advanced High-Strength Steels (AHSS).

Figure 11: The STAF process may reduce part count, assembled weight, and manufacturing complexity compared with other manufacturing approaches.F-41
The following video, kindly provided by Sumitomo Heavy Industries, highlights the STAF process along with associated benefits.F-41
Back To Top