1stGen AHSS, AHSS, Steel Grades
Martensitic steels are characterized by a microstructure that is mostly all martensite, but possibly also containing small amounts of ferrite and/or bainite (Figure 1 and 2). Steels with a fully martensitic microstructure are associated with the highest tensile strength – grades with a tensile strength of 2000 MPa is commercially available, and higher strength levels are under development.

Figure 1: Schematic of a martensitic steel microstructure. Ferrite and bainite may also be found in small amounts.

Figure 2: Microstructure of MS 950/1200
To create MS steels, the austenite that exists during hot-rolling or annealing is transformed almost entirely to martensite during quenching on the run-out table or in the cooling section of the continuous annealing line. Adding carbon to MS steels increases hardenability and strengthens the martensite. Manganese, silicon, chromium, molybdenum, boron, vanadium, and nickel are also used in various combinations to increase hardenability.
These steels are often subjected to post-quench tempering to improve ductility, so that extremely high strength levels can be achieved along with adequate ductility for certain forming processes like Roll Forming.
Figure 3 shows MS950/1200 compared to HSLA. Engineering and true stress-strain curves for MS steel grades are presented in Figures 4 and 5.
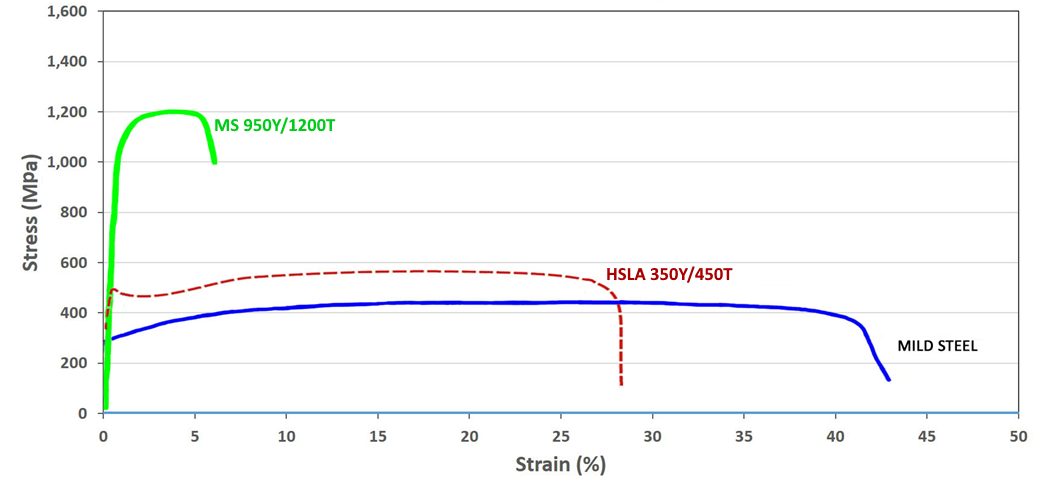
Figure 3: A comparison of stress strain curves for mild steel, HSLA 350/450, and MS 950/1200.

Figure 4: Engineering stress-strain curves for a series of MS steel grades.S-5 Sheet thicknesses: 1.8 mm to 2.0 mm.

Figure 5: True stress-strain curves for a series of MS steel grades.S-5 Sheet thicknesses: 1.8 mm to 2.0mm.
In addition to being produced directly at the steel mill, a martensitic microstructure also can be developed during the hot stamping of press hardening steels.
Examples of current production grades of martensitic steels and typical automotive applications include:
MS 950/1200 |
Cross-members, side intrusion beams, bumper beams, bumper reinforcements |
MS 1150/1400 |
Rocker outer, side intrusion beams, bumper beams, bumper reinforcements |
MS 1250/1500 |
Side intrusion beams, bumper beams, bumper reinforcements |
Some of the specifications describing uncoated cold rolled 1st Generation martensite steel (MS) are included below, with the grades typically listed in order of increasing minimum tensile strength. Different specifications may exist which describe hot or cold rolled, uncoated or coated, or steels of different strengths. Many automakers have proprietary specifications which encompass their requirements.
- ASTM A980M, with Grades 130 [900], 160 [1100], 190 [1300], and 220 [1500]A-23
- VDA 239-100, with the terms CR860Y1100T-MS, CR1030Y1300T-MS, CR1220Y1500T-MS, and CR1350Y1700T-MSV-3
- SAE J2745, with terms Martensite (MS) 900T/700Y, 1100T/860Y, 1300T/1030Y, and 1500T/1200YS-18
Case Study: Using Martensitic Steels
as an Alternative to Press Hardening Steel
– Laboratory Evaluations
Martensitic steel grades provide a cold formed alternative to hot formed press hardening steels. Not all product shapes can be cold formed. For those shapes where forming at ambient temperatures is possible, design and process strategies must address the springback which comes with the high strength levels, as well as eliminate the risk of delayed fracture. The potential benefits associated with cold forming include lower energy costs, reduced carbon footprint, and improved cycle times compared with hot forming processes.
Highlighting product forms achievable in cold stamping, an automotive steel Product Applications Laboratory formed a Roof Center Reinforcement from 1.4 mm CR1200Y1470T-MS using conventional cold stamping rather than roll forming, Figure 6. Using cold stamping allows for the flexibility of considering different strategies when die processing which may result in reduced springback or incorporating part features not achievable with roll forming.

Figure 6: Roof Center Reinforcement cold stamped from CR1200Y1470T-MS martensitic steel.U-1
Cold stamping of martensitic steels is not limited to simpler shapes with gentle curvature. Shown in Figure 7 is a Center Pillar Outer, cold stamped using a tailor welded blank containing CR1200Y1470T-MS and CR320Y590T-DP as the upper and lower portion steels.U-1

Figure 7: Center Pillar Outer stamped at ambient temperature from a tailor welded blank containing 1470 MPa tensile strength martensitic steel.U-1
Another characteristic of martensitic steels is their high yield strength, which is associated with improved crash performance. In a laboratory environment, crash behavior is assessed with 3-point bending moments. A studyS-8 determined there was a correlation between sheet steel yield strength and the 3-point bending deformation of hat shaped parts. Based on a comparison of yield strength, Figure 8 shows that CR1200Y1470T-MS has similar performance to hot stamped PHS-CR1800T-MB and PHS-CR1900T-MB at the same thickness and exceeds the frequently used PHS-CR1500T-MB. For this reason, there may be the potential to reduce costs and even weight with a cold stamping approach, providing appropriate press, process, and die designs are used.

Figure 8: Effect of Yield Strength on Bending Moment. The right image shows the typical yield strength range of CR1030Y1300T-MS and CR1200Y1470T-MS as well as typical yield strength values of several Press Hardened Steels.S-8
Case Study: Martensitic Steels as an Alternative to
Press Hardening Steel – Automotive Production Examples
with Springback Mitigation Strategies
Recent years have seen some applications typically associated with press hardening steels transition to a cold stamped martensitic steel, CR1200Y1470T-MS. One such example is found in the third-generation Nissan B-segment hatchback (2020 start of production), which uses 1.2 mm thick CR1200Y1470T-MS as the material for the Second Cross Member Reinforcement.K-45
Using the carbon equivalent formula Ceq=C+Si/30+Mn/20+2P+4S K-45, the newly developed martensitic grade has a carbon equivalent value of 0.28, which is lower than the 0.35 associated with the conventional PHS grade of comparable tensile strength, 22MnB5 (PHS 1500T). The lower carbon equivalent value is expected to translate into easier welding conditions. Furthermore, conventional mechanical trimming and piercing equipment and techniques work with the cold formable martensitic grade, whereas parts formed from press hardening steels typically require laser trimming or other more costly approaches. An evaluation of delayed fracture found no evidence of this failure mode.
Figure 9 highlights this reinforcement, with its placement on the cross member and in the vehicle shown in red. The varying elevation of this part, combined with a non-uniform cross section at the outermost edges, help control springback, but makes roll forming significantly more challenging if that were the cold forming approach.

Figure 9: Cold-Stamped Martensitic Steel with 1500 MPa Tensile Strength used in the Nissan B-Segment Hatchback.K-57
Unbalanced stresses in stamped parts lead to several types of shape fixability issues collectively called springback. In hat shape wall sections, shape fixing beads sometimes referred to as stake beads (see Post Stretch information at this link) mitigate sidewall curl by imparting a tensile stress state on both the top and bottom sheet surfaces and increasing the rigidity. Springback control to limit flexing down the length of longitudinally curved parts requires a different technique. Here, the root cause is the stress difference between the tensile stress at the punch top and the compressive stress at the flange at bottom dead center of the press stroke. Figure 10 presents schematics of the stress distribution when the punch is located at bottom dead center of the press stroke, and the shape fixability issue after load removal.

Figure 10: Cold-Stamped Martensitic Steel With 1500 MPa Tensile Strength Used in the Lexus NXJ-24
A patented approach known as Stress Reverse Forming™T-44 improved dimensional accuracy in the second-generation Lexus NX (2021 start of production) center roof reinforcement, cold stamped from martensitic steel, CR1200Y1470T-MS.J-24 Figure 11 shows different views of this part.

Figure 11: Left Image: Springback Differences Exist in Coils at the Low and High End of the Strength Specification; Right Image: Stress Reverse Forming™ Process Reduces Sensitivity to Springback (Images Adapted from Citation T-29)
Stress Reverse Forming™T-44 uses the principles of the Bauschinger Effect to reverse the direction of the forming stresses during a restrike forming process to achieve a final part closer to the targeted dimensions.T-29 Parts processed with this two-step approach are first over-formed to a smaller radius of curvature than the final part shape. Removing the part from the tool after this first forming step results in the stress distribution seen in the left image in Figure 10. The unique aspect of this approach comes from the second forming step where the tool shape forces the punch top into slight compression while the lower flange is put into slight tension. The tool shape used in this stage contains a slightly greater radius of curvature than the targeted part shape. As shown in Citation T-29, this process appears to be equally effective at all steel strengths.
Without effective countermeasures, springback increases with part strength. Related to this is the springback difference between coils having strength at the lowest and highest ends of the acceptable property range. This can lead to substantial differences in springback between coils completely within specification. However, after using effective countermeasures such as Stress Reverse Forming™ described in Citation T-29, springback differences between coils are minimized, which leads to increased dimensional accuracy and more consistent stamping performance. This phenomenon is shown schematically in Figure 12. Furthermore, unlike conventional stamping approaches, the amount of springback in parts made with this approach does not increase with steel strength.

Figure 12: Left Image: Springback Differences Exist in Coils at the Low and High End of the Strength Specification; Right Image: Stress Reverse Forming™ Process Reduces Sensitivity to Springback (Images Adapted from Citation T-29)
1stGen AHSS, AHSS, Press Hardened Steels, Steel Grades
Introduction
Press hardening steels are typically carbon-manganese-boron alloyed steels. They are also commonly known as:
- Press Hardening Steels (PHS)
- Hot Press Forming Steels (HPF), a term more common in Asia
- Boron Steel: although the name may also refer to other steels, in automotive industry boron steel is typically used for PHS
- Hot Formed Steel (HF), a term more common in Europe.
The most common PHS grade is PHS1500. In Europe, this grade is commonly referred to as 22MnB5 or 1.5528. As received, it has ferritic-pearlitic microstructure and a yield strength between 300-600 MPa depending on the cold working. The tensile strength of as received steel can be expected to be between 450 and 750 MPa. Total elongation must be over a minimum of 12% (A80), but depending on coating type and thickness may well exceed 18% (A80), see Figure 1*. Thus, the grade can be cold formed to relatively complex geometries using certain methods and coatings. When hardened, it has a minimum yield strength of 950 MPa and tensile strength typically around 1300-1650 MPa, Figure 1.B-14 Some companies describe them with their yield and tensile strength levels, such as PHS950Y1500T. It is also common in Europe to see this steel as PHS950Y1300T, and thus aiming for a minimum tensile strength of 1300 MPa after quenching.
The PHS1500 name may also be used for the Zn-coated 20MnB8 or air hardenable 22MnSiB9-5 grades. The former is known as “direct forming with pre-cooling steel” and could be abbreviated as CR1500T-PS, PHS1500PS, PHSPS950Y1300T or similar. The latter grade is known as “multi-step hot forming steel” and could be abbreviated as, CR1500T-MS, PHS1500MS, PHSMS950Y1300T or similar.V-9

Figure 1: Stress-Strain Curves of PHS1500 before and after quenching* (re-created after Citations U-9, O-8, B-18).
In the last decade, several steel makers introduced grades with higher carbon levels, leading to a tensile strength between 1800 MPa and 2000 MPa. Hydrogen induced cracking (HIC) and weldability limit applications of PHS1800, PHS1900 and PHS2000, with studies underway to develop practices which minimize or eliminate these limitations.
Lastly, there are higher energy absorbing, lower strength grades, which have improved ductility and bendability. These fall into two main groups: Press Quenched Steels (PQS) with approximate tensile strength levels of 450 MPa and 550 MPa (noted as PQS450 and PQS550 in Figure 2) and higher ductility PHS grades with approximate tensile strength levels of 1000 and 1200 MPa (shown as PHS1000 and PHS1200 in Figure 2).
Apart from these grades, other grades are suitable for press hardening. Several research groups and steel makers have offered special stainless-steel grades and recently developed Medium-Mn steels for hot stamping purposes. Also, one steel maker in Europe has developed a sandwich material by cladding PHS1500 with thin PQS450 layers on both sides.

Figure 2: Stress-strain curves of several PQS and PHS grades used in automotive industry, after hot stamping for full hardening* (re-created after Citations B-18, L-28, Z-7, Y-12, W-28, F-19, G-30).
PHS Grades with Tensile Strength Approximately 1500 MPa
Hot stamping as we know it today was developed in 1970s in Sweden. The most used steel since then has been 22MnB5 with slight modifications. 22MnB5 means, approximately 0.22 wt-% C, approximately (5/4) = 1.25% wt-% Mn, and B alloying.
The automotive use of this steel started in 1984 with door beams. Until 2001, the automotive use of hot stamped components was limited to door and bumper beams, made from uncoated 22MnB5, in the fully hardened condition. By the end of the 1990s, Type 1 aluminized coating was developed to address scale formation. Since then, 22MnB5 + AlSi coating has been used extensively.B-14
Although some steel makers claim 22MnB5 as a standard material, it is not listed in any international or regional (i.e., European, Asian, or American) standard. Only a similar 20MnB5 is listed in EN 10083-3.T-26, E-3 The acceptable range of chemical composition for 22MnB5 is given in Table 1.S-64, V-9

Table 1: Chemical composition limits for 22MnB5 (listed in wt.%).S-64, V-9
VDA239-500, a draft material recommendation from Verband Der Automotbilindustrie E.V. (VDA), is an attempt to further standardize hot stamping materials. The document has not been published as of early 2021. According to this draft standard, 22MnB5 may be delivered coated or uncoated, hot or cold rolled. Depending on these parameters, as-delivered mechanical properties may differ significantly. Steels for the indirect process, for example, has to have a higher elongation to ensure cold formability.V-9 Figure 1 shows generic stress-strain curves, which may vary significantly depending on the coating and selected press hardening process.
For 22MnB5 to reach its high strength after quenching, it must be austenitized first. During heating, ferrite begins to transform to austenite at “lower transformation temperature” known as Ac1. The temperature at which the ferrite-to-austenite transformation is complete is called “upper transformation temperature,” abbreviated as Ac3. Both Ac1 and Ac3 are dependent on the heating rate and the exact chemical composition of the alloy in question. The upper transformation temperature for 22MnB5 is approximately 835-890 °C.D-21, H-30Austenite transforms to other microstructures as the steel is cooled. The microstructures produced from this transformation depends on the cooling rate, as seen in the continuous-cooling-transformation (CCT) curve in Figure 3. Achieving the “fully hardened” condition in PHS grades requires an almost fully martensitic microstructure. Avoiding transformation to other phases requires cooling rates exceeding a minimum threshold, called the “critical cooling rate,” which for 22MnB5 is 27 °C/s. For energy absorbing applications, there are also tailored parts with “soft zones”. In these soft zones, areas of interest will be intentionally made with other microstructures to ensure higher energy absorption.B-14

Figure 3: Continuous Cooling Transformation (CCT) curve for 22MnB5 (Published in Citation B-19, re-created after Citations M-25, V-10).
Once the parts are hot stamped and quenched over the critical cooling rate, they typically have a yield strength of 950-1200 MPa and an ultimate tensile strength between 1300 and 1700 MPa. Their hardness level is typically between 470 and 510 HV, depending on the testing methods.B-14
Once automotive parts are stamped, they are then joined to the car body in body shop. The fully assembled body known as the Body-in-White (BIW) with doors and closures, is then moved to the paint shop. Once the car is coated and painted, the BIW passes through a furnace to cure the paint. The time and temperature for this operation is called the paint bake cycle. Although the temperature and duration may be different from plant to plant, it is typically close to 170 °C for 20 minutes. Most automotive body components made from cold or hot formed steels and some aluminum grades may experience an increase in their yield strength after paint baking.
In Figure 4, press hardened 22MnB5 is shown in the red curve. In this particular example, the proof strength was found to be approximately 1180 MPa. After processing through the standard 170 °C – 20 minutes bake hardening cycle, the proof strength increases to 1280 MPa (shown in the black curve).B-18 Most studies show a bake hardening increase of 100 MPa or more with press hardened 22MnB5 in industrial conditions.B-18, J-17, C-17

Figure 4: Bake hardening effect on press hardened 22MnB5. BH0 is shown since there is no cold deformation pre-strain. (re-created after Citation B-18).
There are two modified versions of the 22MnB5 recently offered by several steel makers: 20MnB8 and 22MnSiB9-5. Both grades have higher Mn and Si compared to 22MnB5, as shown in Table 2.

Table 2: Chemical compositions of PHS grades with 1500 MPa tensile strength (all listed in wt.%).V-9
Both of these relatively recent grades are designed for Zn-based coatings and are designed for different process routes. For these reasons, many existing hot stamping lines would require some modifications to accommodate these grades.
20MnB8 has been designed for a “direct process with pre-cooling”. The main idea is to solidify the Zn coating before forming, eliminating the possibility that liquid zine fills in the micro-cracks on the formed base metal surface, which in turn eliminates the risk of Liquid Metal Embrittlement (LME). The chemistry is modified such that the phase transformations occur later than 22MnB5. The critical cooling rate of 20MnB8 is approximately 10 °C/s. This allows the part to be transferred from the pre-cooling stage to the forming die. As press hardened, the material has approximately 1000-1050 MPa yield strength and 1500 MPa tensile strength. Once bake hardened (170 °C, 20 minutes), yield strength may exceed 1100 MPa.K-22 This steel may be referred to as PHS950Y1300T-PS (Press Hardening Steel with minimum 950 MPa yield, minimum 1300 MPa tensile strength, for Pre-cooled Stamping).
22MnSiB9-5 has been developed for a transfer press process, named as “multi-step”. As quenched, the material has similar mechanical properties with 22MnB5 (Figure 5). As of 2020, there is at least one automotive part mass produced with this technology and is applied to a compact car in Germany.G-27 Although the critical cooling rate is listed as 5 °C/s, even at a cooling rate of 1 °C/s, hardness over 450HV can be achieved, as shown in Figure 6.H-27 This allows the material to be “air-hardenable” and thus, can handle a transfer press operation (hence the name multi-step) in a servo press. This material is also available with Zn coating.B-15 This steel may be referred to as PHS950Y1300T-MS (Press Hardening Steel with minimum 950 MPa yield, minimum 1300 MPa tensile strength, for Multi-Step process).

Figure 5: Engineering stress-strain curves of 1500 MPa level grades (re-created after Citations B-18, G-29, K-22)

Figure 6: Critical cooling rates of 1500 MPa level press hardening steels (re-created after Citations K-22, H-31, H-27)
Grades with Higher Ductility
Press hardened parts are extremely strong, but cannot absorb much energy. Thus, they are mostly used where intrusion resistance is required. However, newer materials for hot stamping have been developed which have higher elongation (ductility) compared to the most common 22MnB5. These materials can be used in parts where energy absorption is required. These higher energy absorbing, lower strength grades fall into two groups, as shown in Figure 7. Those at the lower strength level are commonly referred to as “Press Quenched Steels” (PQS). The products having higher strength in Figure 7 are press hardening steels since they contain boron and do increase in strength from the quenching operation. The properties listed are after the hot stamping process.
- 450–600 MPa tensile strength level and >15% total elongation, listed as PQS450 and PQS550.
- 1000–1300 MPa tensile strength level and >5% total elongation, listed as PHS1000 and PHS1200.

Figure 7: Stress-strain curves of several PQS and PHS grades used in automotive industry, after hot stamping for full hardening* (re-created after Citations B-18, Y-12).
Currently none of these grades are standardized. Most steel producers have their own nomination and standard, as summarized in Table 3. There is a working document by German Association of Automotive Industry (Verband der Automobilindustrie, VDA), which only specifies one of the PQS grades. In the draft standard, VDA239-500, PQS450 is listed as CR500T-LA (Cold Rolled, 500 MPa Tensile strength, Low Alloyed). Similarly, PQS550 is listed as CR600T-LA.V-9 Some OEMs may prefer to name these grades with respect to their yield and tensile strength together, as listed in Table 3.
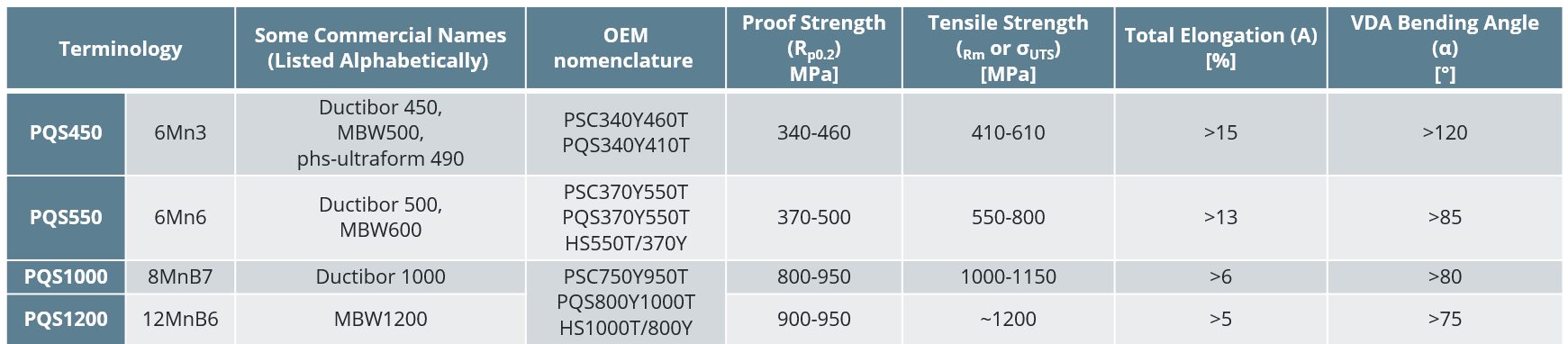
Table 3: Summary of Higher Ductility grades. The terminology descriptions are not standardized. Higher Ductility grade names are based on their properties and terminology is derived from a possible chemistry or OEM description. The properties listed here encompass those presented in multiple sources and may or may not be associated with any one specific commercial grade.Y-12, T-28, G-32
PQS grades have been under development at least since 2002. In the earliest studies, PQS 1200 was planned.R-11 Between 2007 and 2009, three new cars were introduced in Europe, having improved “energy absorbing” capacity in their hot stamped components. VW Tiguan (2007-2016) and Audi A5 Sportback (2009-2016) had soft zones in their B-pillars (Figure 8B and C). Intentionally reducing the cooling rate in these soft zone areas produces microstructures having higher elongations. In the Audi A4 (2008-2016) a total of three laser welded tailored blanks were hot stamped. The soft areas of the A4 B-pillars were made of HX340LAD+AS (HSLA steel, with AlSi coating, as delivered, min yield strength = 340 MPa, tensile strength = 410-510 MPa) as shown in Figure 8A. After the hot stamping process, HX340LAD likely had a tensile strength between 490 and 560 MPaS-65, H-32, B-20, D-22, putting it in the range of PQS450 (see Table 3). Note that there were not the only cars to have tailored hot stamped components during that time.
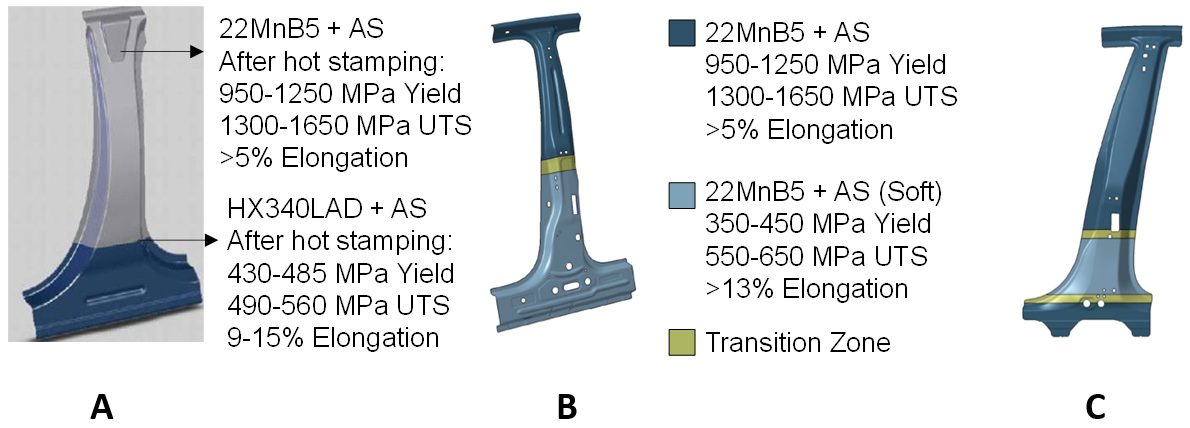
Figure 8: Earliest energy absorbing hot stamped B-pillars: (A) Audi A4 (2008-2016) had a laser welded tailored blank with HSLA material; (B) VW Tiguan (2007-2015) and (C) Audi A5 Sportback (2009-2016) had soft zones in their B-pillars (re-created after Citations H-32, B-20, D-22).
A 2012 studyK-25 showed that a laser welded tailored B-Pillar with 340 MPa yield strength HSLA and 22MnB5 had the best energy absorbing capacity in drop tower tests, compared to a tailored (part with a ductile soft-zone) or a monolithic part, Figure 9. As HSLA is not designed for hot stamping, most HSLA grades may have very high scatter in the final properties after hot stamping depending on the local cooling rate. Although the overall part may be cooled at an average 40 to 60 °C/s, at local spots the cooling rate may be over 80 °C/s. PQS grades are developed to have stable mechanical properties after a conventional hot stamping process, in which high local cooling rates may be possible.M-26, G-31, T-27

Figure 9: Energy absorbing capacity of B-pillars increase significantly with soft zones or laser welded tailored blank with ductile material (re-created after Citation K-25).
PQS grades have been in use at latest since 2014. One of the earliest cars to announce using PQS450 was VolvoXC90. There are six components (three right + three left), tailor welded blanks with PQS450, as shown Figure 10.L-29 Since then, many carmakers started to use PQS450 or PQS550 in their car bodies. These include:
- Fiat 500X: Patchwork supported, laser welded tailored rear side member with PQS450 in crush zonesD-23,
- Fiat Tipo (Hatchback and Station Wagon versions): similar rear side member with PQS450B-14,
- Renault Scenic 3: laser welded tailored B-pillar with PQS550 in the lower sectionF-19,
- Chrysler Pacifica: five-piece front door ring with PQS550 in the lower section of the B-Pillar areaT-29, and
- Chrysler Ram: six-piece front door ring with PQS550 in the lower section of the B-Pillar area.R-3
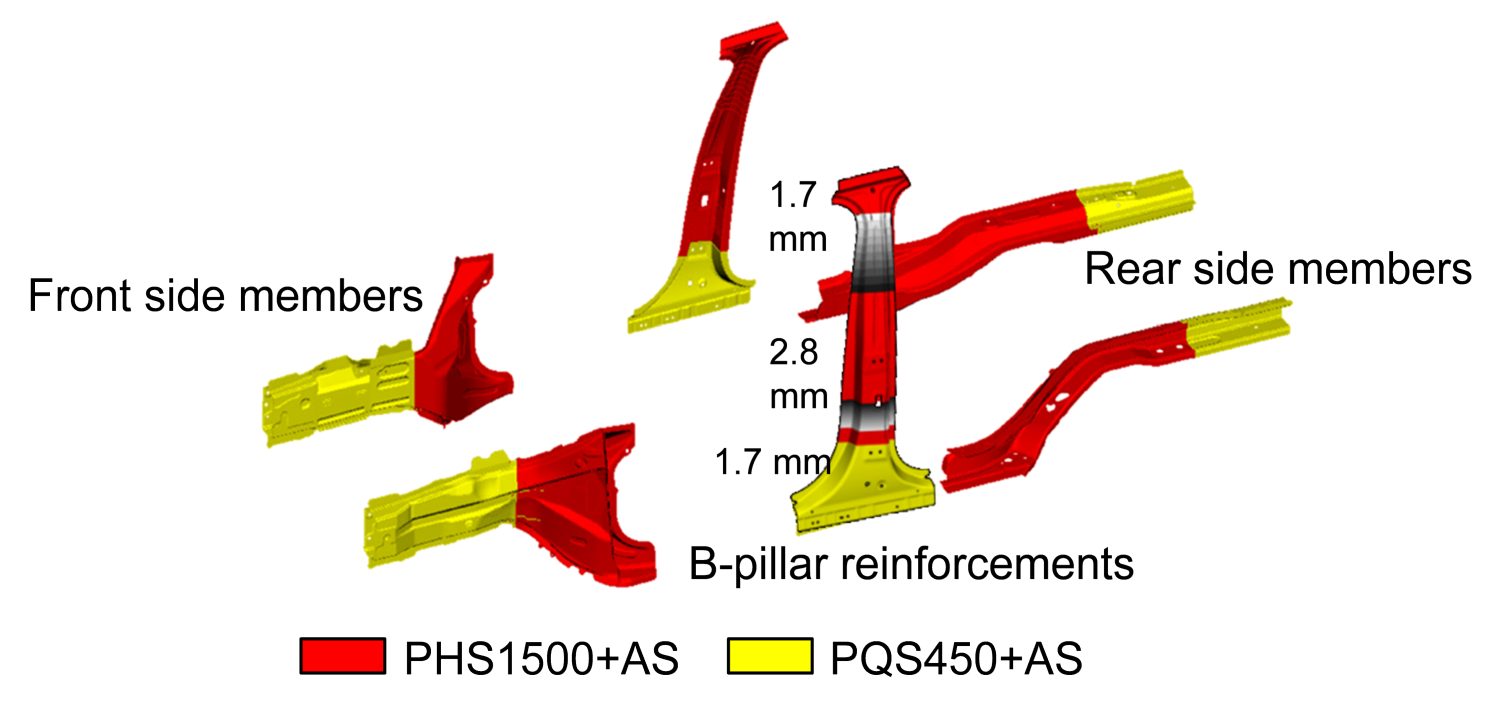
Figure 10: Use of laser welded tailored PQS-PHS grades in 2nd generation Volvo XC90 (re-created after Citation L-29).
Several car makers use PQS grades to facilitate joining of components. The B-Pillar of the Jaguar I-PACE electric SUV is made of PQS450, with a PHS1500 patch that is spot welded before hot stamping, creating the patchwork blank shown in Figure 11A.B-21 Early PQS applications involved a laser welded tailored blank with PHS 1500. Since 2014, Mercedes hot stamped PQS550 blanks not combined with PHS1500. Figure 11B shows such components on the Mercedes C-Class.K-26
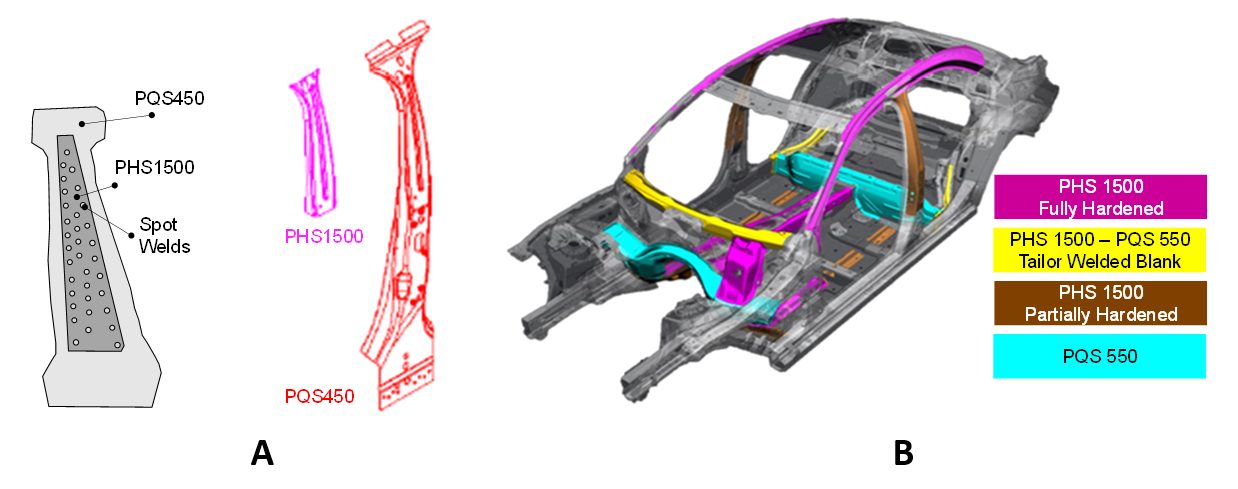
Figure 11: Recent PQS applications: (a) 2018 Jaguar I-PACE uses a patchwork B-pillar with PQS450 master blank and PHS1500 patchB-21, (b) 2014 Mercedes C-Class has a number of PQS550 components that are not laser welded to PHS1500.K-26
PHS Grades over 1500 MPa
The most commonly used press hardening steels have 1500 MPa tensile strength, but are not the only optionsR-11, with 4 levels between 1700 and 2000 MPa tensile strength available or in development as shown in Figure 12. Hydrogen induced cracking (HIC) and weldability problems limit widespread use in automotive applications, with studies underway to develop practices which minimize or eliminate these limitations.
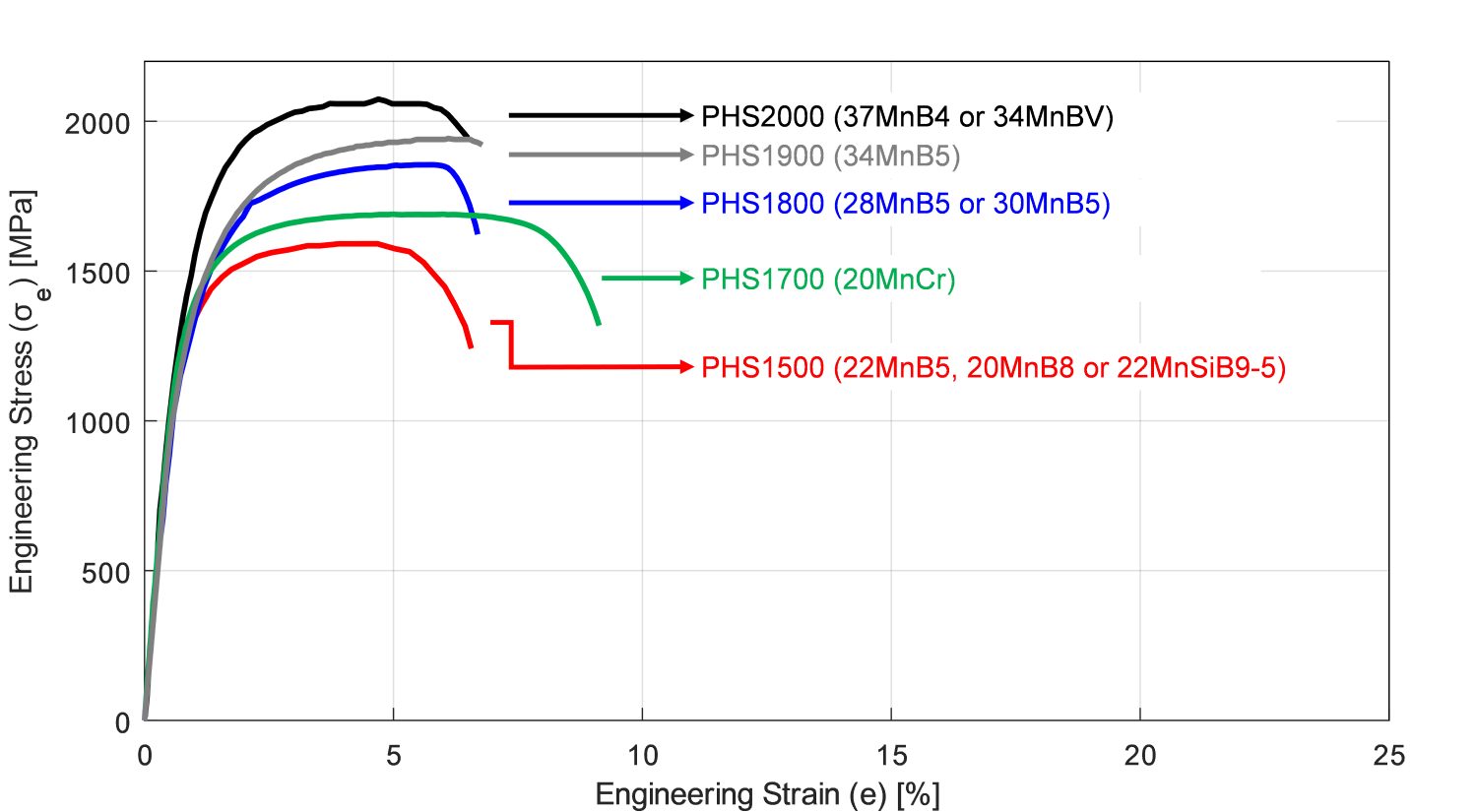
Figure 12: PHS grades over 1500 MPa tensile strength, compared with the common PHS1500 (re-created after Citations B-18, W-28, Z-7, L-30, L-28, B-14).
Mazda Motor Corporation was the first vehicle manufacturer to use higher strength boron steels, with the 2011 CX-5 using 1,800MPa tensile strength reinforcements in front and rear bumpers, Figure 13. According to Mazda, the new material saved 4.8 kg per vehicle. The chemistry of the steel is Nb modified 30MnB5.H-33, M-28 Figure 14 shows the comparison of bumper beams with PHS1500 and PHS1800. With the higher strength material, it was possible to save 12.5% weight with equal performance.H-33

Figure 13: Bumper beam reinforcements of Mazda CX-5 (SOP 2011) are the first automotive applications of higher strength boron steels.M-28

Figure 14: Performance comparison of bumper beams with PHS1500 and PHS1800.H-33
PHS 1800 is used in the 2022 Genesis Electrified G80 (G80EV) and the new G90, both from Hyundai Motor. A specialized method lowering the heating furnace temperature by more than 50℃ limits the penetration of hydrogen into the blanks, minimizing the risk of hydrogen embrittlement. L-64.
MBW 1900 is the commercial name for a press hardening steel with 1900 MPa tensile strength. An MBW 1900 B-pillar with correct properties can save 22% weight compared to DP 600 and yet may cost 9% less than the original Dual-Phase design.H-34 Ford had also demonstrated that by using MBW 1900 instead of PHS 1500, a further 15% weight could be saved.L-30 Since 2019, VW’s electric vehicle ID.3 has two seat crossbeams made of MBW 1900 steel, as seen in Figure 15.L-31 The components are part of MEB platform (Modularer E-Antriebs-Baukasten – modular electric-drive toolkit) and may be used in other VW Group EVs.
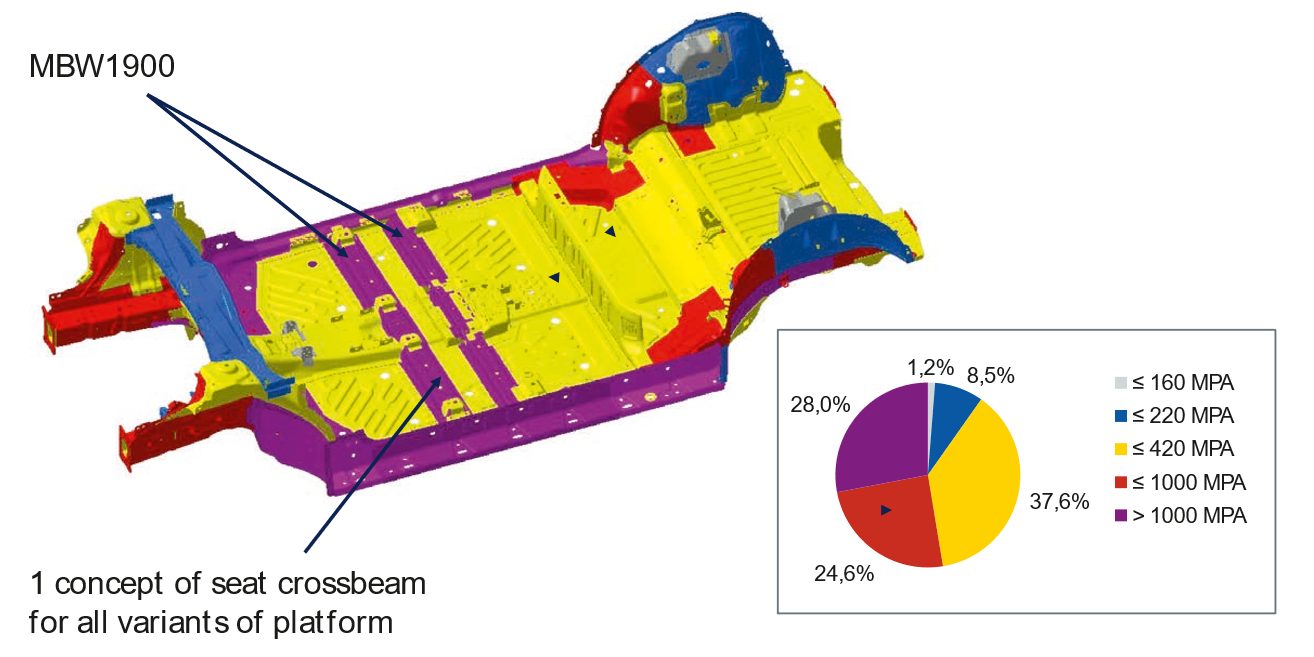
Figure 15: Underbody of VW ID3 (part of MEB platform).L-31
USIBOR 2000 is the commercial name given to a steel grade similar to 37MnB4 with an AlSi coating. Final properties are expected only after paint baking cycle, and the parts made with this grade may be brittle before paint bake.B-32 In June 2020, Chinese Great Wall Motors started using USIBOR 2000 in the Haval H6 SUV.V-12
HPF 2000, another commercial name, is used in a number of component-based examples, and also in the Renault EOLAB concept car.L-28, R-12 An 1800 MPa grade is under development.P-22 Docol PHS 1800, a commercial grade approximating 30MnB5, has been in production, with Docol PHS 2000 in development.S-66 PHS-Ultraform 2000, a commercial name for a Zn (GI) coated blank, is suited for the indirect process.V-11
General Motors China, together with several still mills across the country, have developed two new PHS grades: PHS 1700 (20MnCr) and PHS2000 (34MnBV). 20MnCr uses Cr alloying to improve hardenability and oxidation resistance. This grade can be hot formed without a coating. The furnace has to be conditioned with N2 gas. The final part has high corrosion resistance, approximately 9% total elongation (see Figure 12) and high bendability (see Table 4). 34MnBV on the other hand, has a thin AlSi coating (20g/m2 on each side). Compared with the typical thickness of AlSi coatings, thinner coatings are preferred for bendability (see Table 5).W-28 More information about these oxidation resistant PHS grades, as well as a 1200 MPa version intended for applications benefiting from enhanced crash energy absorption, can be found in Citation L-60.
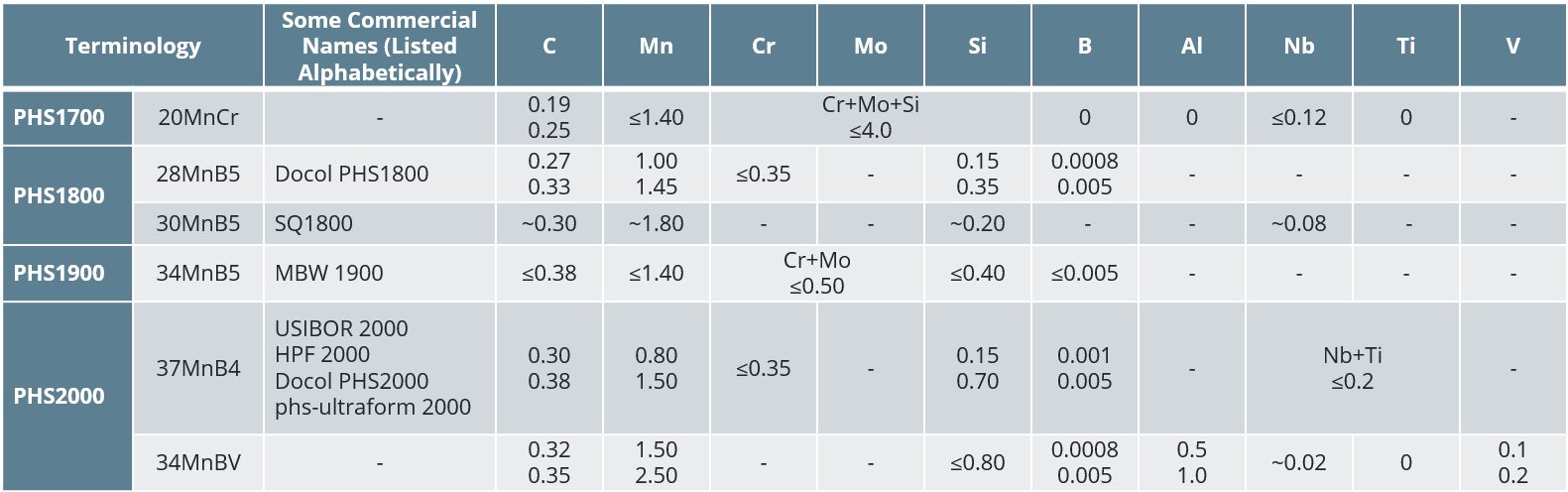
Table 4: Chemical compositions of higher strength PHS grades. “0” means it is known that there is no alloying element, while “-” means there is no information. “~” is used for typical values; otherwise, minimum or maximum are given. The terminology descriptions are not standardized. PQS names are based on their properties and grade names are derived from a possible chemistry or OEM description. The properties listed here encompass those presented in multiple sources and may or may not be associated with any one specific commercial grade.W-28, B-32, H-33, G-33, L-28, S-67, S-66, Y-12, B-33
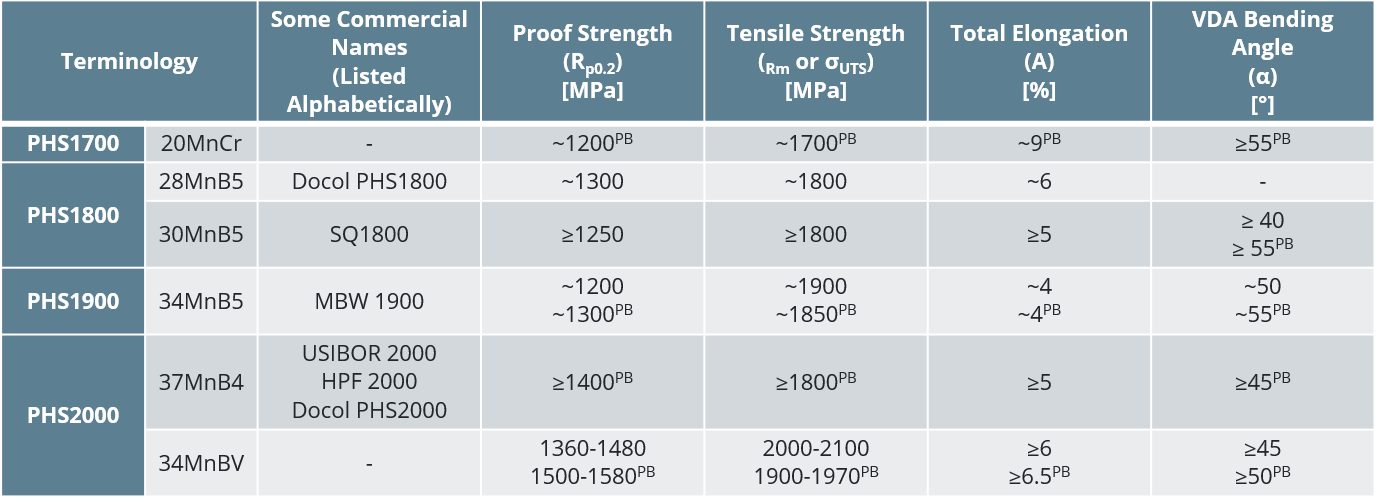
Table 5: Mechanical properties of higher strength PHS grades. “~” is used for typical values; otherwise, minimum or maximum are given. Superscript PB means after paint bake cycle. The terminology descriptions are not standardized. PQS names are based on their properties and grade names are derived from a possible chemistry or OEM description. The properties listed here encompass those presented in multiple sources and may or may not be associated with any one specific commercial grade.W-28, B-32, H-33, G-33, L-28, S-67, S-66, Y-12
Other Steels for Press Hardening Process
In recent years, many new steel grades are under evaluation for use with the press hardening process. Few, if any, have reached mass production, and are instead in the research and development phase. These grades include:
- Stainless steels
- Medium-Mn steels
- Composite steels
Stainless Steels
Studies of press hardening of stainless steels primarily focus on martensitic grades (i.e., AISI SS400 series).M-36, H-42, B-40, M-37, F-30 As seen in Figure 16, martensitic stainless steels may have higher formability at elevated temperatures, compared to PHS1500 (22MnB5). Other advantages of stainless steels are:
- better corrosion resistanceM-37,
- potentially higher heating rates (i.e., induction heating) F-30,
- possibility of air hardening – allowing the multi-step process — as seen in Figure 17a H-42,
- high cold formability – allowing indirect process – as seen in Figure 17b.M-37
Disadvantages include (a) higher material cost, and (b) higher furnace temperature (up to around 1050-1150 °C).M-37, F-30 As of 2020, there are two commercially available stainless steel grades specifically developed for press hardening process.

Figure 16: Tensile strength and total elongation variation with temperature of (a) PHS1500 = 22MnB5M-38 and (b) martensitic stainless steel.M-36

Figure 17: (a) Critical cooling rate comparison of 22MnB5 and AISI SS410 (re-created after Citation H-42), (b) Room temperature forming limit curve comparison of DP600 and modified AISI SS410 (re-created after Citation M-37).
Final mechanical properties of stainless steels after press hardening process are typically superior to 22MnB5, in terms of elongation and energy absorbing capacity. Figure 18 illustrates engineering stress-strain curves of the commercially available grades (1.6065 and 1.4064), and compares them with the 22MnB5 and a duplex stainless steel (Austenite + Martensite after press hardening). These grades may also have bake hardening effect, abbreviated as BH0, as there will be no cold deformation.B-40, M-37, F-30

Figure 18: Engineering Stress-Strain curves of press hardened stainless steels, compared with 22MnB5 (re-created after Citations B-40, M-37, F-30, B-41).

Table 6: Summary of mechanical properties of press hardenable stainless steel grades. Typical values are indicated with “~”. (Table generated from Citations B-40, M-37, F-30.)
Medium-Mn Steels
Medium-Mn steels typically contain 3 to 12 weight-% manganese alloying.D-27, H-30, S-80, R-16, K-35 Although these steels were originally designed for cold stamping applications, there are numerous studies related to using them in the press hardening process as well.H-30 Several advantages of medium-Mn steels in press hardening are:
- Austenitization temperature may be significantly lower than compared to 22MnB5, as indicated in Figure 19.H-30, S-80 Thus, using medium-Mn steels may save energy in heating process.M-39 Lower heating temperature may also help reducing the liquid-metal embrittlement risk of Zn-coated blanks. It also may reduce oxidation and decarburization of uncoated blanks.S-80
- Martensitic transformation can occur at low cooling rates. Simpler dies could be used with less or no cooling channels. In some grades, air hardening may be possible. Thus, multi-step process could be employed.S-80, B-14
- Some retained austenite may be present at the final part, which can enhance the elongation, through the TRIP effect. This, in turn, improves toughness significantly.S-80, B-14

Figure 19: Effect of Mn content on equilibrium transformation temperatures (re-created after Citations H-30, B-14)
The change in transformation temperatures with Mn-alloying was calculated using ThermoCalc software.H-30 As seen in Figure 19, as Mn alloying is increased, austenitization temperatures are lowered.H-30 For typical 22MnB5 stamping containing 1.1 to 1.5 % Mn, furnace temperature is typically set at 930 °C in mass production. The multi-step material 22MnSiB9-5 has slightly higher Mn levels (2.0 to 2.4 %), so the furnace temperature could be reduced to 890 °C. As also indicated in Table 7, the furnace temperature could be further lowered in hot forming of medium-Mn steels.
A study in the EU showed that if the maximum furnace temperature is 930 °C, which is common for 22MnB5, natural gas consumption will be around 32 m3/hr. In the study, two new medium-Mn steels were developed, one with 3 wt.% Mn and the other with 5 wt% Mn. These grades had lower austenitization temperature, and the maximum furnace set temperature could be reduced to 808 °C and 785 °C, respectively. Experimental data shows that at 808 °C natural gas consumption was reduced to 19 m3/hr, and at 785 °C to 17 m3/hr.M-39 In Figure 20, experimental data is plotted with a curve fit. Based on this model, it was estimated that by using 22MnSiB9-5, furnace gas consumption may be reduced by 15%.

Figure 20: Effect of maximum furnace set temperature (at the highest temperature furnace zone) on natural gas consumption (raw data from Citation M-39)
Lower heating temperature of medium-Mn steels may also help reducing the liquid-metal embrittlement risk of Zn-coated blanks. It also may reduce oxidation and decarburization of uncoated blanks.S-80
Medium-Mn steels may have high yield-point elongation (YPE), with reports of more than 5% after hot stamping. Mechanical properties may be sensitive to small changes in temperature profile. As seen in Figure 21, all studies with medium-Mn steel have a unique stress-strain curve after press hardening. This can be explained by:
- differences in the chemistry,
- thermomechanical history of the sheet prior to hot stamping,
- heating rate, heating temperature and soaking time, and
- cooling rate.S-80

Figure 21: Engineering Stress-Strain curves of several press hardened medium-Mn steels, compared with 22MnB5. See Table 7 for an explanation of each tested material (re-created after Citations S-80,L-37, W-30, L-38).

Table 7: Summary of mechanical properties of press hardenable Medium-Mn grades shown in Figure 18. Typical values are indicated with “~”. Toughness is calculated as the area under the engineering stress-strain curve. Items 4 and 5 also were annealed at different temperatures and therefore have different thermomechanical history. Note that these grades are not commercially available.L-38, W-30, L-37, S-80
Composite Steels
TriBond ® is the name given to a family of steel composites.T-32 Here, three slabs (one core material (60 to 80% of the thickness) and two cladding layers) are surface prepared, stacked on top of each other, and welded around the edges. The stack is hot rolled to thickness. Cold rolling could also be applied. Initially, TriBond ® was designed for wear-resistant cladding and ductile core materials.
The original design was optimized for hot stamping.B-14 The core material, where bending strains are lower than the outer layers, is made from generic 22MnB5 (PHS1500). Outer layers are made with PQS450. The stack is cold rolled, annealed and AlSi coated.Z-9 Two grades are developed, differing by the thickness distribution between the layers, as shown in Figure 22.R-14

Figure 22: Sample microsections of the conventional hot stamping grade PHS1500+AS, the high strength composite Tribond® 1400 and the high energy absorbing composite Tribond® 1200. The Tribond® 1200 microsection is experimental and is taken from Citation R-14. The other two images are renditions created by the author for explanation purposes. (re-created after Citations R-14, R-15)
Total elongation of the composite steel is not improved, compared to PHS1500, as shown in Figure 23. The main advantage of the composite steels is their higher bendability, as seen in Table 8. Crashboxes, front and rear rails, seat crossmembers and similar components experience axial crush loading in the event of a crash. In axial crush, Tribond® 1200 saved 15% weight compared to DP780 (CR440Y780T-DP). The bending loading mode effects B-pillars, bumper beams, rocker (sill) reinforcements, side impact door beams, and similar components during a crash. In this bending mode, Tribond® 1400 saved 8 to 10% weight compared to regular PHS1500. Lightweighting cost with Tribond® 1400 was calculated as €1.50/kgsaved.G-37, P-26

Figure 23: Engineering Stress-Strain curves of core layer, outer layer and the composite steel (re-created after Citation P-26).

Table 8: Summary of composite steels and comparison with conventional PHS and PQS grades. Typical values are indicated with “~”. (Table re-created after Citation B-14).
* Graphs in this article are for information purposes only. Production materials may have different curves. Consult the Certified Mill Test Report and/or characterize your current material with an appropriate test (such as a tensile, bending, hole expansion, or crash test) test to get the material data pertaining to your current stock.
For more information on Press Hardened Steels, see these pages:
Back To Top
1stGen AHSS, AHSS, Steel Grades
Dual Phase (DP) steels have a microstructure consisting of a ferritic matrix with martensitic islands as a hard second phase, shown schematically in Figure 1. The soft ferrite phase is generally continuous, giving these steels excellent ductility. When these steels deform, strain is concentrated in the lower-strength ferrite phase surrounding the islands of martensite, creating the unique high initial work-hardening rate (n-value) exhibited by these steels. Figure 2 is a micrograph showing the ferrite and martensite constituents.
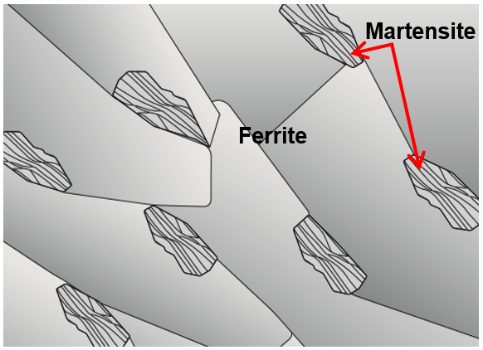
Figure 1: Schematic of a Dual Phase steel microstructure showing islands of martensite in a matrix of ferrite.
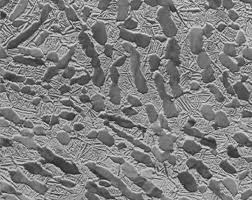
Figure 2: Micrograph of Dual Phase Steel
Hot rolled DP steels do not have the benefit of an annealing cycle, so the dual phase microstructure must be achieved by controlled cooling from the austenite phase after exiting the hot strip mill finishing stands and before coiling. This typically requires a more highly alloyed chemistry than cold rolled DP steels require. Higher alloying is generally associated with a change in welding practices.
Continuously annealed cold-rolled and hot-dip coated Dual Phase steels are produced by controlled cooling from the two-phase ferrite plus austenite (α + γ) region to transform some austenite to ferrite before a rapid cooling transforms the remaining austenite to martensite. Due to the production process, small amounts of other phases (bainite and retained austenite) may be present.
Higher strength dual phase steels are typically achieved by increasing the martensite volume fraction. Depending on the composition and process route, steels requiring enhanced capability to resist cracking on a stretched edge (as typically measured by hole expansion capacity) can have a microstructure containing significant quantities of bainite.
The work hardening rate plus excellent elongation creates DP steels with much higher ultimate tensile strengths than conventional steels of similar yield strength. Figure 3 compares the engineering stress-strain curve for HSLA steel to a DP steel curve of similar yield strength. The DP steel exhibits higher initial work hardening rate, higher ultimate tensile strength, and lower YS/TS ratio than the HSLA with comparable yield strength. Additional engineering and true stress-strain curves for DP steel grades are presented in Figures 4 and 5.
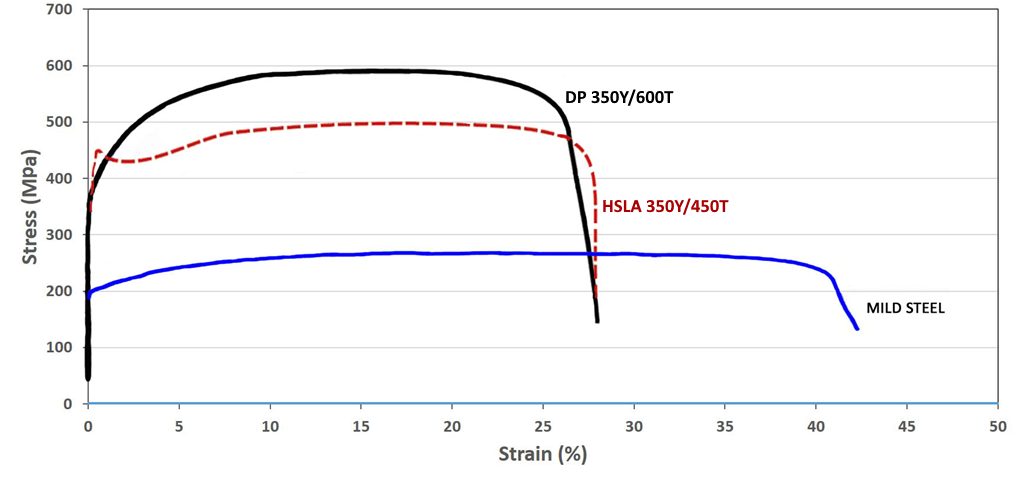
Figure 3: A comparison of stress strain curves for mild steel, HSLA 350/450, and DP 350/600K-1

Figure 4: Engineering stress-strain curves for a series of DP steel grades.S-5, V-1 Sheet thicknesses: DP 250/450 and DP 500/800 = 1.0mm. All other steels were 1.8-2.0mm.

Figure 5: True stress-strain curves for a series of DP steel grades.S-5, V-1 Sheet thicknesses: DP 250/450 and DP 500/800 = 1.0mm. All other steels were 1.8-2.0mm.
DP and other AHSS also have a bake hardening effect that is an important benefit compared to conventional higher strength steels. The extent of the bake hardening effect in AHSS depends on an adequate amount of forming strain for the specific chemistry and thermal history of the steel.
In DP steels, carbon enables the formation of martensite at practical cooling rates by increasing the hardenability of the steel. Manganese, chromium, molybdenum, vanadium, and nickel, added individually or in combination, also help increase hardenability. Carbon also strengthens the martensite as a ferrite solute strengthener, as do silicon and phosphorus. These additions are carefully balanced, not only to produce unique mechanical properties, but also to maintain the generally good resistance spot welding capability. However, when welding the higher strength grades (DP 700/1000 and above) to themselves, the spot weldability may require adjustments to the welding practice.
Examples of current production grades of DP steels and typical automotive applications include:
DP 300/500 |
Roof outer, door outer, body side outer, package tray, floor panel |
DP 350/600 |
Floor panel, hood outer, body side outer, cowl, fender, floor reinforcements |
DP 500/800 |
Body side inner, quarter panel inner, rear rails, rear shock reinforcements |
DP 600/980 |
Safety cage components (B-pillar, floor panel tunnel, engine cradle, front sub-frame package tray, shotgun, seat) |
DP 700/1000 |
Roof rails |
DP 800/1180 |
B-Pillar upper |
Some of the specifications describing uncoated cold rolled 1st Generation dual phase (DP) steel are included below, with the grades typically listed in order of increasing minimum tensile strength and ductility. Different specifications may exist which describe hot or cold rolled, uncoated or coated, or steels of different strengths. Many automakers have proprietary specifications which encompass their requirements.
- ASTM A1088, with the terms Dual phase (DP) steel Grades 440T/250Y, 490T/290Y, 590T/340Y, 780T/420Y, and 980T/550YA-22
- EN 10338, with the terms HCT450X, HCT490X, HCT590X, HCT780X, HCT980X, HCT980XG, and HCT1180XD-6
- JIS G3135, with the terms SPFC490Y, SPFC540Y, SPFC590Y, SPFC780Y and SPFC980YJ-3
- JFS A2001, with the terms JSC590Y, JSC780Y, JSC980Y, JSC980YL, JSC980YH, JSC1180Y, JSC1180YL, and JSC1180YHJ-23
- VDA 239-100, with the terms CR290Y490T-DP, CR330Y590T-DP, CR440Y780T-DP, CR590Y980T-DP, and CR700Y980T-DPV-3
- SAE J2745, with terms Dual Phase (DP) 440T/250Y, 490T/290Y, 590T/340Y, 6907/550Y, 780T/420Y, and 980T/550YS-18
1stGen AHSS, 3rdGen AHSS, AHSS, Steel Grades
topofpage
The microstructure of Transformation Induced Plasticity (TRIP) steels contains a matrix of ferrite, with retained austenite, martensite, and bainite present in varying amounts. Production of TRIP steels typically requires the use of an isothermal hold at an intermediate temperature, which produces some bainite. Higher silicon and carbon content of TRIP steels result in significant volume fractions of retained austenite in the final microstructure. Figure 1 shows a schematic of TRIP steel microstructure, with Figure 2 showing a micrograph of an actual sample of TRIP steel. Figure 3 compares the engineering stress-strain curve for HSLA steel to a TRIP steel curve of similar yield strength.
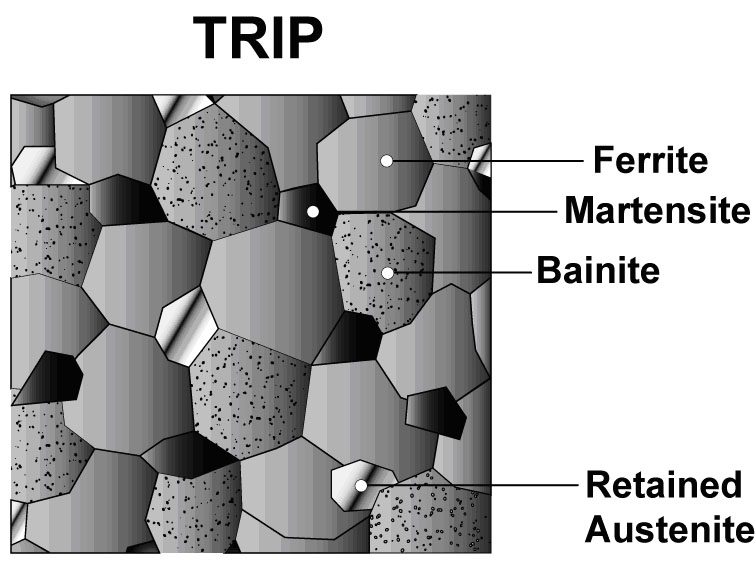
Figure 1: Schematic of a TRIP steel microstructure showing a matrix of ferrite, with martensite, bainite and retained austenite as the additional phases.
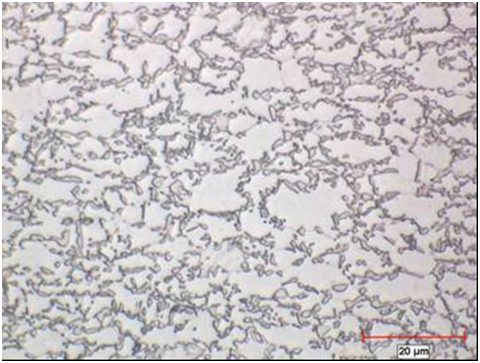
Figure 2: Micrograph of Transformation Induced Plasticity steel.
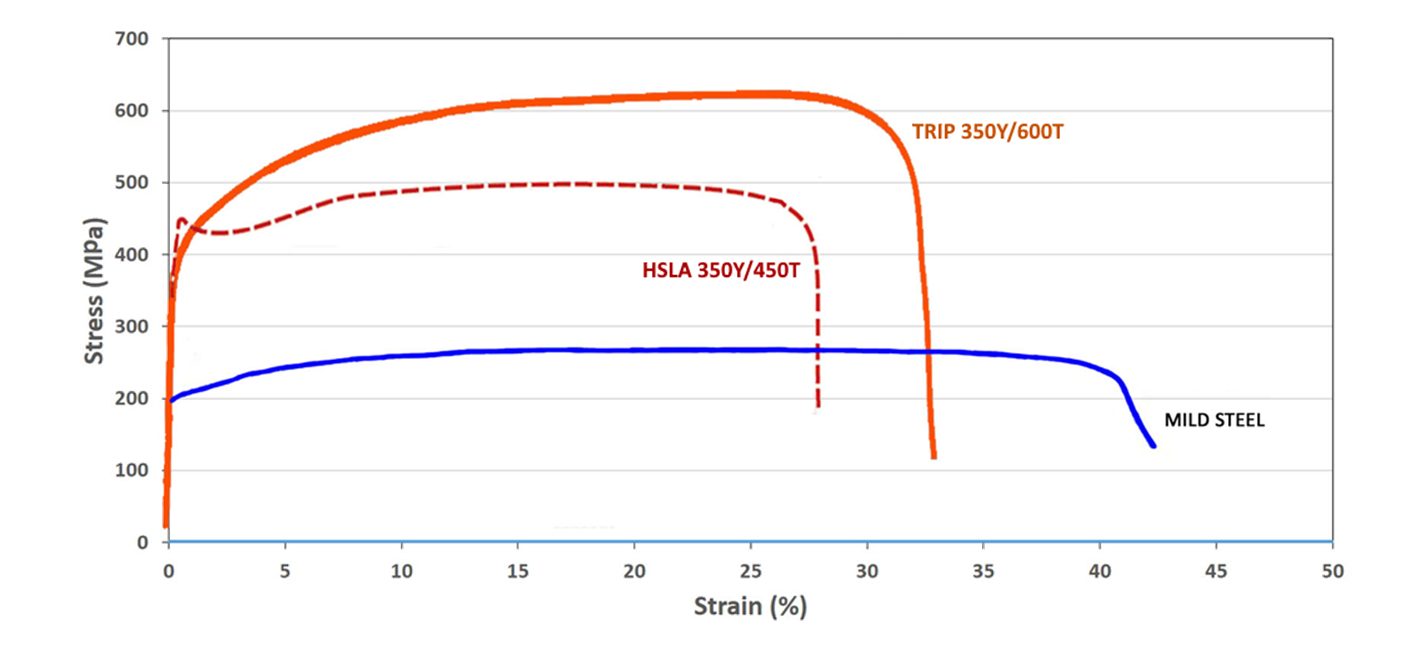
Figure 3: A comparison of stress strain curves for mild steel, HSLA 350/450, and TRIP 350/600.K-1
During deformation, the dispersion of hard second phases in soft ferrite creates a high work hardening rate, as observed in the DP steels. However, in TRIP steels the retained austenite also progressively transforms to martensite with increasing strain, thereby increasing the work hardening rate at higher strain levels. This is known as the TRIP Effect. This is illustrated in Figure 4, which compares the engineering stress-strain behavior of HSLA, DP and TRIP steels of nominally the same yield strength. The TRIP steel has a lower initial work hardening rate than the DP steel, but the hardening rate persists at higher strains where work hardening of the DP begins to diminish. Additional engineering and true stress-strain curves for TRIP steel grades are shown in Figure 5.
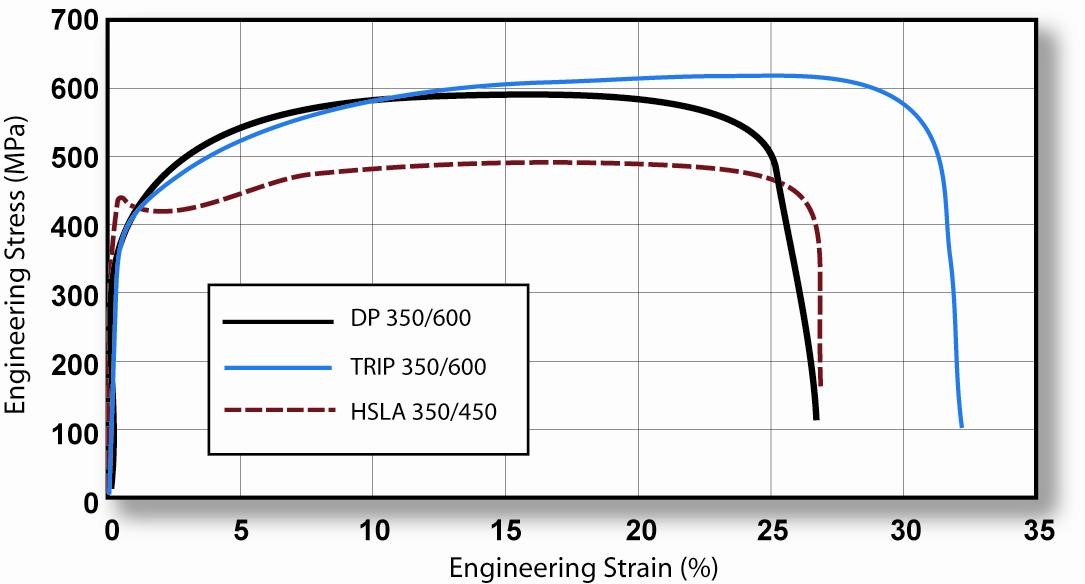
Figure 4: TRIP 350/600 with a greater total elongation than DP 350/600 and HSLA 350/450. K-1
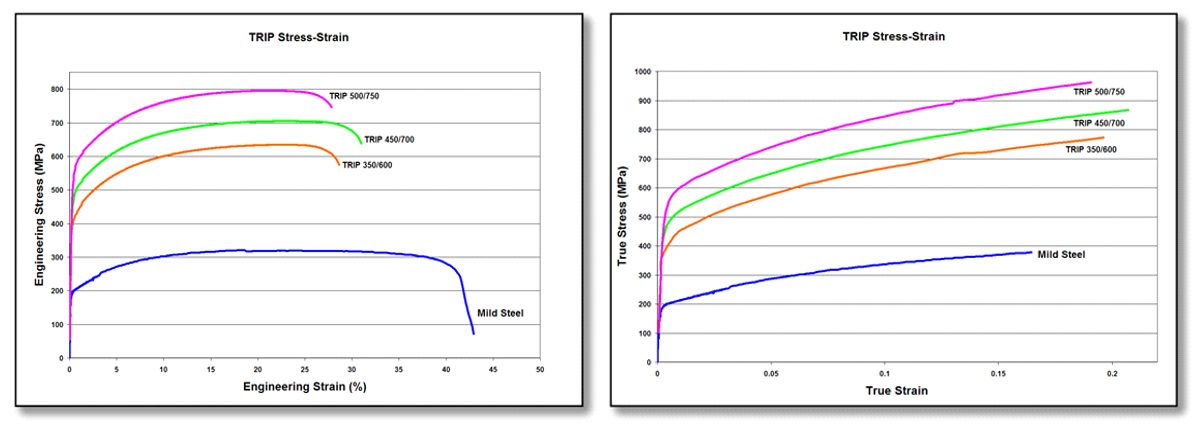
Figure 5: Engineering stress-strain (left graphic) and true stress-strain (right graphic) curves for a series of TRIP steel grades. Sheet thickness: TRIP 350/600 = 1.2mm, TRIP 450/700 = 1.5mm, TRIP 500/750 = 2.0mm, and Mild Steel = approx. 1.9mm. V-1
The strain hardening response of TRIP steels are substantially higher than for conventional HSS, resulting in significantly improved formability in stretch deformation. This response is indicated by a comparison of the n-value for the grades. The improvement in stretch formability is particularly useful when designers take advantage of the improved strain hardening response to design a part utilizing the as-formed mechanical properties. High n-value persists to higher strains in TRIP steels, providing a slight advantage over DP in the most severe stretch forming applications.
Austenite is a higher temperature phase and is not stable at room temperature under equilibrium conditions. Along with a specific thermal cycle, carbon content greater than that used in DP steels are needed in TRIP steels to promote room-temperature stabilization of austenite. Retained austenite is the term given to the austenitic phase that is stable at room temperature.
Higher contents of silicon and/or aluminum accelerate the ferrite/bainite formation. These elements assist in maintaining the necessary carbon content within the retained austenite. Suppressing the carbide precipitation during bainitic transformation appears to be crucial for TRIP steels. Silicon and aluminum are used to avoid carbide precipitation in the bainite region.
The carbon level of the TRIP alloy alters the strain level at which the TRIP Effect occurs. The strain level at which retained austenite begins to transform to martensite is controlled by adjusting the carbon content. At lower carbon levels, retained austenite begins to transform almost immediately upon deformation, increasing the work hardening rate and formability during the stamping process. At higher carbon contents, retained austenite is more stable and begins to transform only at strain levels beyond those produced during forming. At these carbon levels, retained austenite transforms to martensite during subsequent deformation, such as a crash event.
TRIP steels therefore can be engineered to provide excellent formability for manufacturing complex AHSS parts or to exhibit high strain hardening during crash deformation resulting in excellent crash energy absorption.
The additional alloying requirements of TRIP steels degrade their resistance spot-welding behavior. This can be addressed through weld cycle modification, such as the use of pulsating welding or dilution welding. Table 1 provides a list of current production grades of TRIP steels and example automotive applications:
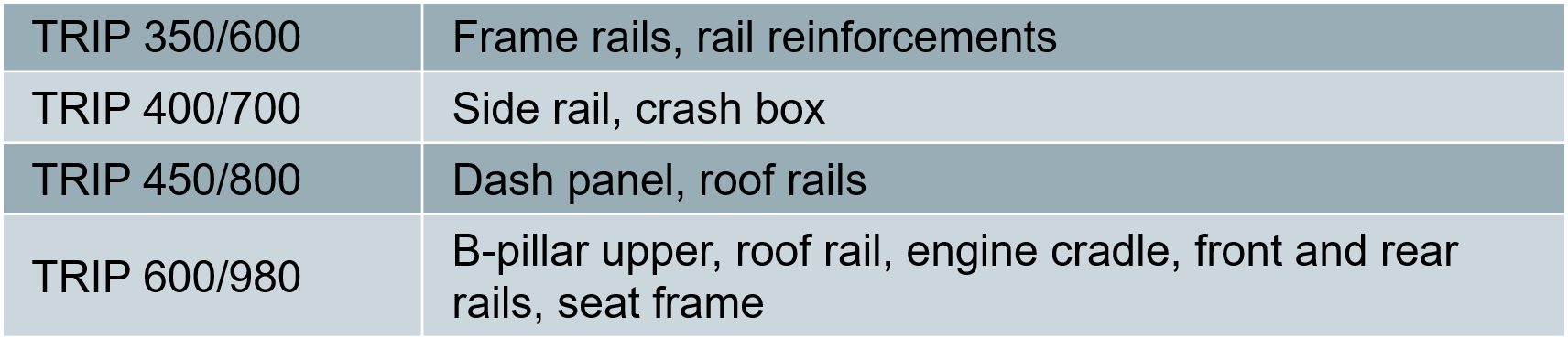
Table 1: Current Production Grades Of TRIP Steels And Example Automotive Applications.
Some of the specifications describing uncoated cold rolled 1st Generation transformation induced plasticity (TRIP) steel are included below, with the grades typically listed in order of increasing minimum tensile strength and ductility. Different specifications may exist which describe hot or cold rolled, uncoated or coated, or steels of different strengths. Many automakers have proprietary specifications which encompass their requirements.
• ASTM A1088, with the terms Transformation induced plasticity (TRIP) steel Grades 690T/410Y and 780T/440YA-22
• JFS A2001, with the terms JSC590T and JSC780TJ-23
• EN 10338, with the terms HCT690T and HCT780TD-18
• VDA 239-100, with the terms CR400Y690T-TR and CR450Y780T-TRV-3
• SAE J2745, with terms Transformation Induced Plasticity (TRIP) 590T/380Y, 690T/400Y, and 780T/420YS-18
Transformation Induced Plasticity Effect
Austenite is not stable at room temperature under equilibrium conditions. An austenitic microstructure is retained at room temperature with the combined use of a specific chemistry and controlled thermal cycle. Deformation from sheet forming provides the necessary energy to allow the crystallographic structure to change from austenite to martensite. There is insufficient time and temperature for substantial diffusion of carbon to occur from carbon-rich austenite, which results in a high-carbon (high strength) martensite after transformation. Transformation to high strength martensite continues as deformation increases, as long as retained austenite is still available to be transformed.
Alloys capable of the TRIP effect are characterized by a high ductility – high strength combination. Such alloys include 1st Gen AHSS TRIP steels, as well as several 3rd Gen AHSS grades like TRIP-Assisted Bainitic Ferrite, Carbide Free Bainite, and Quench & Partition Steels.
Back to the Top