Blog, homepage-featured-top, main-blog, News
As an organization focused on advancing the advantages of steel to the automotive and future mobility industries, WorldAutoSteel is committed to engaging with future engineers at universities and colleges around the globe.
Our most recent engineering project, Steel E-Motive, was designed to unveil and meet the challenges of future autonomous vehicles that will help the automotive industry reach net zero emissions targets.
For the Steel E-Motive project, we engaged Ricardo plc to collaborate with our technical directors to develop a Level 5 Autonomous Vehicle. The project uncovered a few challenges that were solved by student engineering teams through Senior Capstone Projects.
Here we summarize the Side Door and Door Hinges project, created at Michigan Technological University by the students and faculty members listed herein.
Steel E-Motive Side Door Functionality and Door Hinge Assessment
The MTU Senior Capstone Team members were Gavin Sheffer, Leander Daavettila, Rob Oestreich, Steven Turnbull, Andrew Mitteer, and Jesse Ebenhoeh.
Introduction and Background
The MTU Senior Capstone Design Team, sponsored by WorldAutoSteel and the Auto/Steel Partnership, was challenged to design a new door hinge for the Steel E-Motive side closure mechanism. The current hinge design was referenced, but a few operational issues were identified for this team’s assessment and engineering study.
The door had unconstrained degrees of freedom, allowing it to swing freely about one axis. Thus, the project included a review of the kinematics of the door opening and hinge design for attachment to the A and C pillars.
The previous hinge design interferes with the all-wheel steering, meaning in emergency situations, passengers could get trapped in the vehicle. For SEM1, it was also observed that when the wheels are turned, they would block the doors from opening fully, constraining the passenger exit (Figure 1 below).
An emergency release mechanism was needed to allow users to escape if a crash or electrical failure prevented the doors from opening.
Power requirements and electric motor sizing for the hinge mechanism needed to be defined.
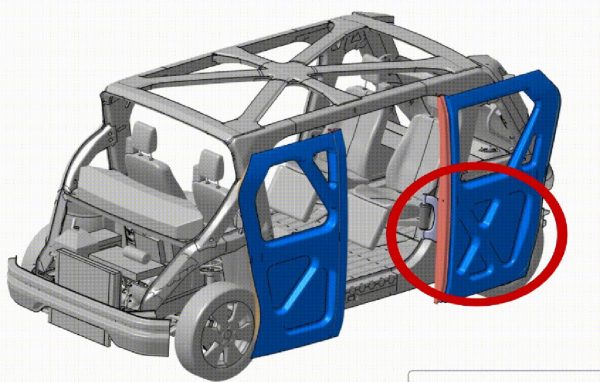
Figure 1: Side door opening constrained by present hinge mechanism and wheel position.
Project Details and Results
MTU’s design solution uses a four-bar linkage hinge design to keep the door parallel to the vehicle’s body to avoid damage to either the door or the body. The team used a 4:1 gear ratio for the drive motor to open the door. Finally, one of the pins in the secondary arm linkage is accessible by passengers and removable, allowing users to manually push the door open in the event of an emergency (see Figure 2).
Their solution includes pressing a button to open and close the door. The stepper motor receives the input from the button and rotates the gears; the gears then rotate the primary arm, which drives the door. The primary arm is mounted to the door in two locations with bolts. The secondary arm is added to the mechanism to create a four-bar linkage, which helps maintain door orientation during operation. An emergency release was designed and added to the secondary arm to release the four-bar linkage. This allows the door to swivel around a turned wheel in the event of an emergency.
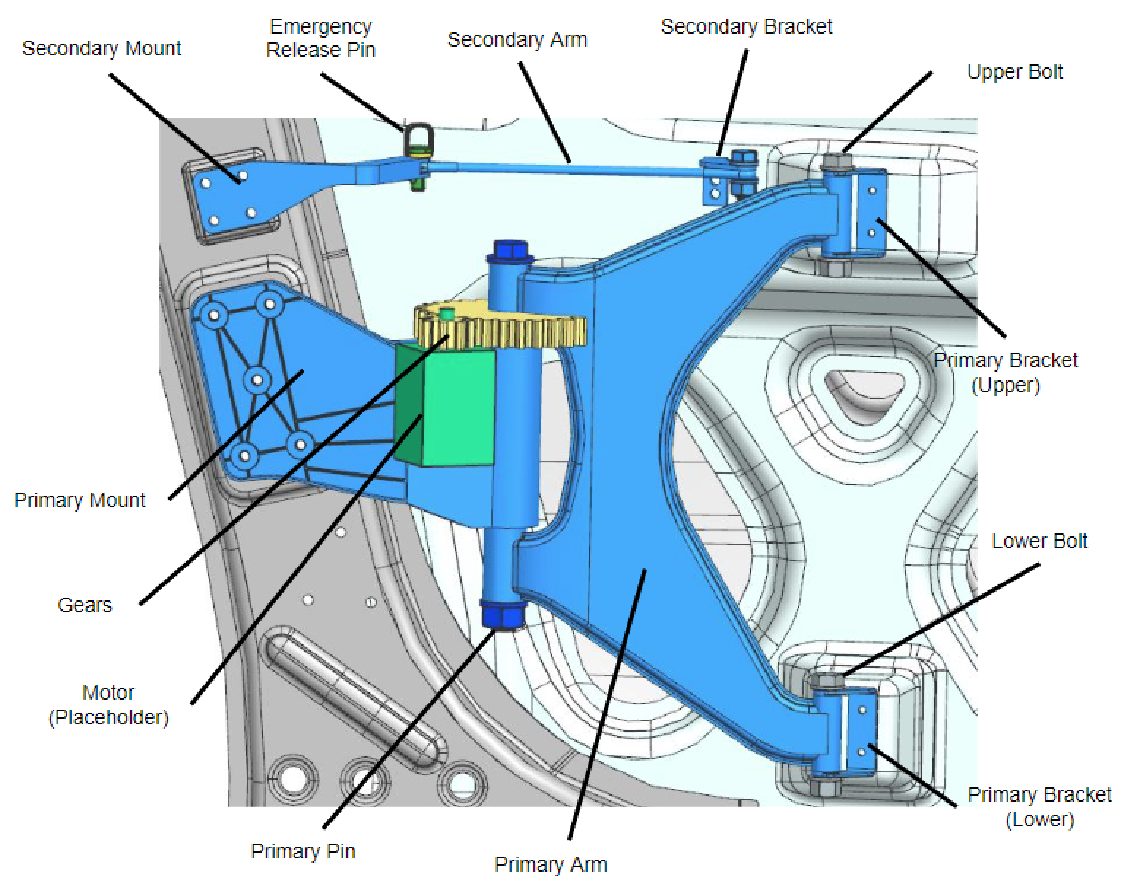
Figure 2: 3D model of the final design less the gear cover for clarity.
The emergency release was designed for safety and manufacturability. The emergency release pin was simplified to utilize off-the-shelf pins. A relay is suggested to cut power to the motor and allow the door to be manually pushed open. A gear cover was added for safety to protect the occupants from getting pinched by the gears. To maintain and service the design, each assembly part was designed to be attached with threaded fasteners. A gear drive was created so we could use a more cost-efficient motor. The gear ratio decreased the amount of torque required. The material was chosen based on strength and sustainability.
Conclusions
The CAD geometry and the quarter-scale prototype met all of our engineering requirements and objectives. The CAD model defines the mass and emergency release mechanism, and the kinematics are verified by the quarter-scale prototype. The FEA simulation verified set and sag under normal and abusive loading conditions.
In identifying specifications required for the full model, the projected production cost for one mechanism is $471. This includes stamped and cast components, off-the-shelf components such as the stepper motor and fasteners, and the assembly cost.
The team compared using AHSS for the components as opposed to an aluminum alloy. Steel components are stronger, half the price of aluminum, and produce 1/3 of the carbon emissions compared to the same amount of aluminum.
The prototype was 3D printed from PLA plastic at a quarter scale. This serves as a model to be shown by Auto/Steel Partnership for future presentations. It was also used to verify the kinematics of the door motion.
Learn more about Steel E-Motive and download the FREE Engineering Report here: Steel E-Motive
Blog, main-blog, News
As robotaxi companies in the USA prepare to launch their autonomous vehicles in more cities, safety is in the spotlight again. And rightly so. Autonomous vehicle safety challenges must be addressed and with the Steel E-Motive Level 5 autonomous concept, we did that.
Many autonomous mobility service companies have relied on two factors when developing their vehicles: active safety systems which help the vehicle avoid or mitigate the extent of a crash, and a maximum vehicle speed limit, which will reduce the extent of injuries to the occupants.
But the fact is that these vehicles are going to be out in mixed-mode traffic situations. There will be accidents – however much we all attempt to do everything possible to avoid them. When we developed the Steel E-Motive (SEM) body structure concepts for fully autonomous ride-sharing electric vehicles, we agreed on two basic principles – that these vehicles would operate at high speeds (top speed of 130 kph) in mixed mode traffic conditions, and that we, therefore, needed to engineer passive safety structures that met global high-speed crash requirements to protect occupants and the battery system in these use-case conditions. In this process, we discovered that no other provider of autonomous ride-sharing electric vehicles had fully shared details of passive safety structures engineered to those same high-speed crash standards. Autonomous vehicle safety had been addressed only on a limited basis.
Fortunately, our vehicle design process benefitted from a massive portfolio of modern advanced high-strength steels (AHSS) available through member companies of WorldAutoSteel. Steel E-Motive (SEM) was developed to show how AHSS can enable sustainable, comfortable, economical, and safe ride-sharing vehicles by 2030.
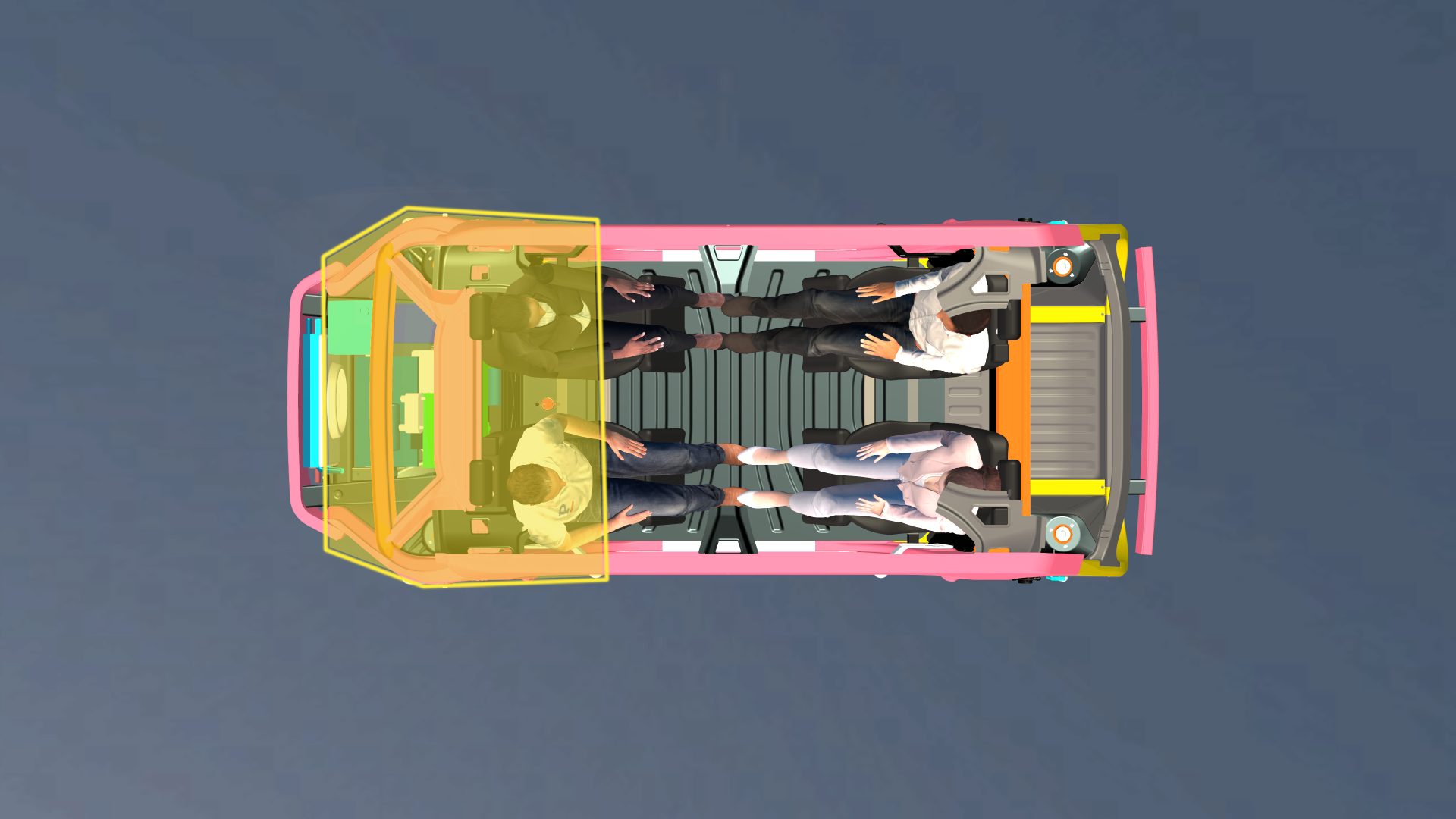
The AHSS Extended Passenger Protection Zone provides excellent cabin intrusion protection and ultimately lower risk of injury. PHS provides formability for challenging geometries, and Martensitic steel (MS) provides the strength to limit intrusion.
Visit this link to download the full engineering report: Steel E-Motive
The result is one of the first robotaxis to fully detail and report compliance to global high-speed safety standards. In developing Steel E-Motive, we targeted conformity with seven US crash standards, including US NCAP (New Car Assessment Program) IIHS and FMVSS (Federal Motor Vehicle Safety Standards) front, side, and rear impact tests while also assessing performance against worldwide protocols, including NHTSA (US) Euro NCAP (European) and China’s GB 38031 standard for battery protection.
As an example, Steel E-Motive achieves the highest IIHS rating of “good.” This is particularly important as IIHS (the US-based Insurance Institute for Highway Safety) is highly regarded for its dedication to reducing deaths, injuries, and property damage from motor vehicle crashes.
Most production vehicles use new generation, advanced high-strength steels, and technologies. We had no fewer than 64 AHSS materials to select from, enabling us to choose exactly the right steel for every need and purpose in the vehicle, including safety protection. These make a car stronger, more fuel efficient, and safer.
Nearly all vehicles on the road today are made of steel because it has the broadest range of properties while being the most affordable structural material for designing safe vehicles. Steel has a unique capacity to absorb an impact, and, therefore, to diffuse crash energy. It also becomes harder when it’s crushed, which means it will become stronger on impact, retarding further penetration into the vehicle’s passenger zone.
Taking on Autonomous Vehicle Safety Challenges
Here is an outline of how we designed steel’s benefits into the Steel E-Motive (SEM) concept when considering front and side crashes.
SEM features a high-strength front protection zone, which reacts to the crush loads and minimizes intrusion for the occupants in front crashes. The crush zones have been engineered to decelerate the vehicle progressively. The longitudinal mid rails, featuring tailor-welded blanks fabricated with Dual Phase steels, are tuned to give a lower deceleration pulse into the passenger cabin to minimize injury threat. The side crush rails are designed to minimize intrusion into the cabin for occupant protection. Finally, a novel design geometry and Press Hardened Steels enable the new glance beam architecture to force the vehicle off of the Small Offset barrier; the resulting “glance-off” achieves significantly reduced crash energy and pulse into the passenger cabin.
When considering side crashes, we engineered the body structure for the IIHS 60kph deformable barrier test and 30kph side pole test, assessing both occupant and battery protection and achieving the IIHS “good” performance rating. Our side structures are comprised of a large one-piece tailor-welded door ring fabricated with press hardened steels, the TRIP steel B pillar housed in the side scissor doors, and a roll-formed hexagon rocker beam fabricated with Dual Phase steel.
These attain a very safe design, giving good levels of protection for both the occupants and battery modules, exceeding 30mm intrusion clearance at critical measurement points.
SEM was also engineered for rear crash and roof crush, and once again, the robust steel-intensive architecture exceeds crash standard requirements.
Electric-powered vehicle sales are accelerating, reflecting industry investment, and will soon achieve market domination from the combustion engine. In megacities, where congestion, pollution, and exorbitant vehicle ownership costs reign, Autonomous cars will replace drivers, and ride-sharing will become the norm. As we look into the future and recognize the need for these vehicles to offer comfortable, safe, affordable, and sustainable transportation, we will still be designing them by harnessing the unique properties of steel.
Visit this link to download the full engineering report: Steel E-Motive
AHSS, Blog, homepage-featured-top, Joining, main-blog, News, Resistance Spot Welding, RSW of Dissimilar Steel, Steel Grades, Tool & Die Professionals
Urbanization and waning interest in vehicle ownership point to new transport opportunities in megacities around the world. Mobility as a Service (MaaS) – characterized by autonomous, ride-sharing-friendly EVs – can be the comfortable, economical, sustainable transport solution of choice thanks to the benefits that today’s steel offers.
The WorldAutoSteel organization is working on the Steel E-Motive program, which delivers autonomous ride-sharing vehicle concepts enabled by Advanced High-Strength Steel (AHSS) products and technologies.
The Body structure design for this vehicle is shown in Figure 1. It also indicates the specific joint configuration of 5 layers AHSS sheet stack-up as shown in Table 1. Resistance spot welding parameters were developed to allow this joint to be made by a single weld. (The previous solution for this welded joint is to create one spot weld with the bottom 3 sheets indicated in the table and a second weld to join the top 2 sheets, combining the two-layer groups to 5T stack-up.)
NOTE: Click this link to read a previous AHSS Insights blog that summarizes development work and recommendations for resistance spot welding 3T and 4T AHSS stack-ups: https://bit.ly/42Alib8
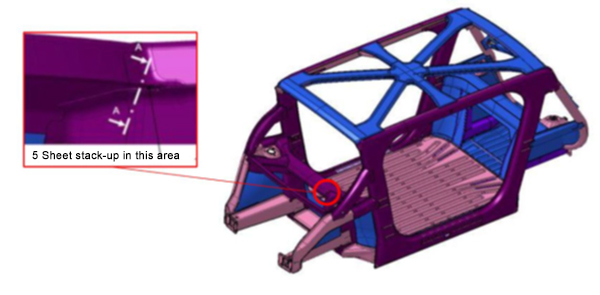
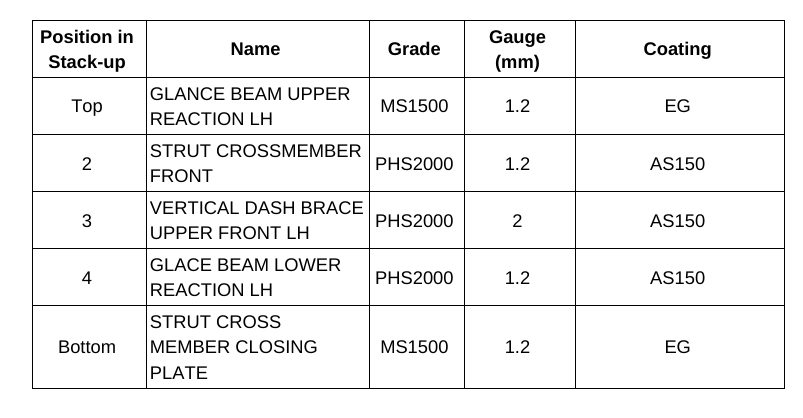
Table 1. Provided materials organized in stack-up formation showing part number, name, grade, gauge in mm, and coating type. Total thickness = 6.8 mm
The same approach of utilizing multiple current pulses with short cool time in between the pulses was shown to be most effective in this case of 5T stack-up. It is important to note that in some cases, the application of a secondary force was shown to be beneficial, however, it was not used in this example.
To establish initial welding parameters simulations were conducted using the Simufact software by Hexagon. As shown in Figure 2, the final setup included a set of welding electrodes that clamped the 5-layer AHSS stack-up. Several simulations were created with a designated set of welding parameters of current, time, number of pulses, and electrode force.
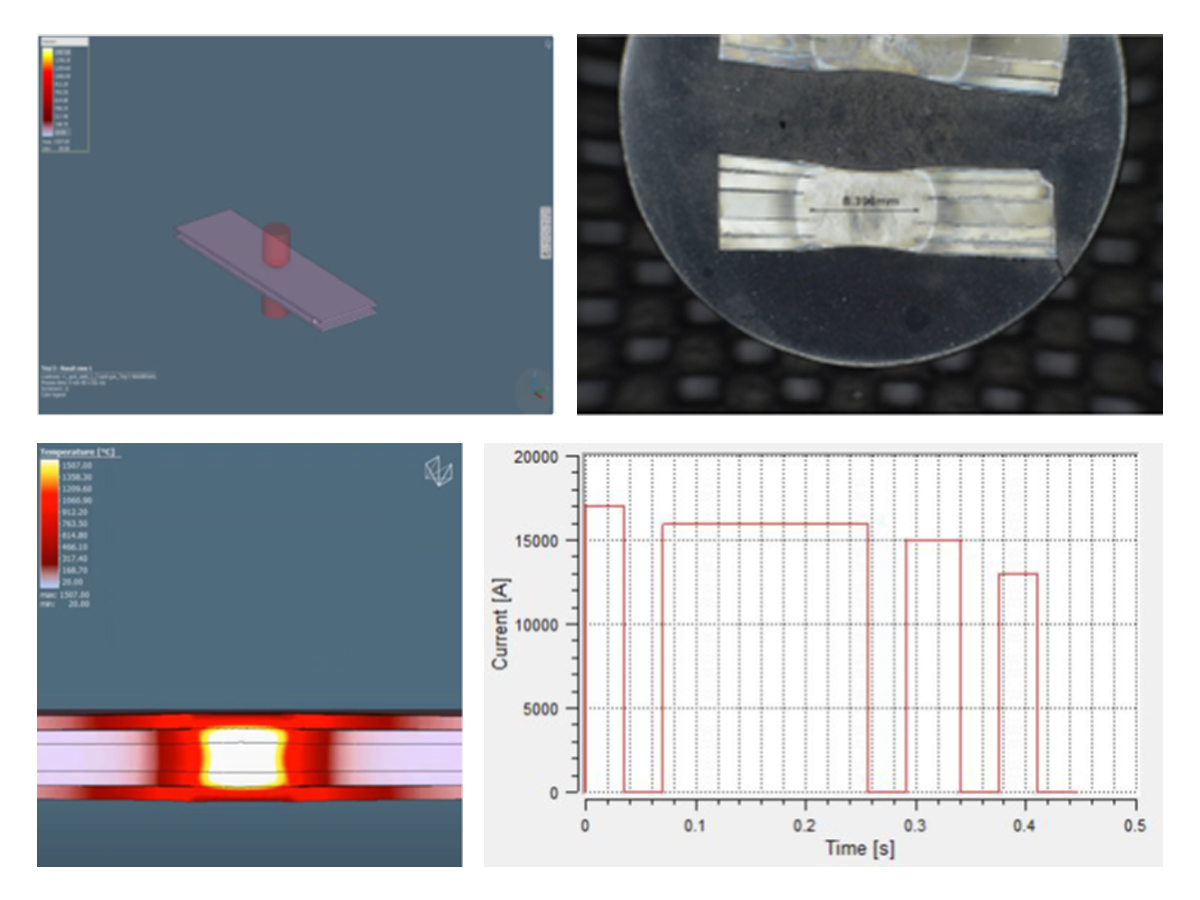
Figure 2. Example of simulation and experimental results showing acceptable 5T resistance spot weld (Meets AWS Automotive specifications)
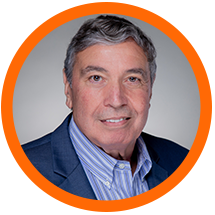
Thanks is given to Menachem Kimchi, Associate Professor-Practice, Dept of Materials Science, Ohio State University and Technical Editor – Joining, AHSS Application Guidelines, for this article.
Citations
Citation U-13.
Peter Ulintz, Precision Metalforming Association. This section originally appeared in the September 2023 issue of MetalForming Magazine under the title “Stronger AHSS Knowledge Required for Metal Stampers”. Reproduced with the permission of MetalForming Magazine.
3rdGen AHSS, AHSS, Blog, General, main-blog, Metallurgy, News, Steel Grades
The Steel E-Motive program–commissioned by WorldAutoSteel in partnership with Ricardo plc–has developed the world’s first fully autonomous electric vehicle body structure concept purpose-fit for ride-sharing. This global steel industry initiative showcases the strength and durability of steel with an eye on playing a pivotal role in reaching net zero emissions targets.
Download the Steel E-Motive Engineering Report
Here, we break down the many benefits of the Steel E-Motive concept that only Advanced High-Strength Steel (AHSS) can enable.
Steel E-Motive Was Conceived as a Level 5 Autonomous Vehicle
The Steel E-Motive concept is designed to be a Level 5 autonomous vehicle, so it does not include any driver interfaces. The design features a spacious, airy cabin with rear-facing front-passenger seat configurations. The B-pillarless structure and unique battery system design offer easy ingress and egress.
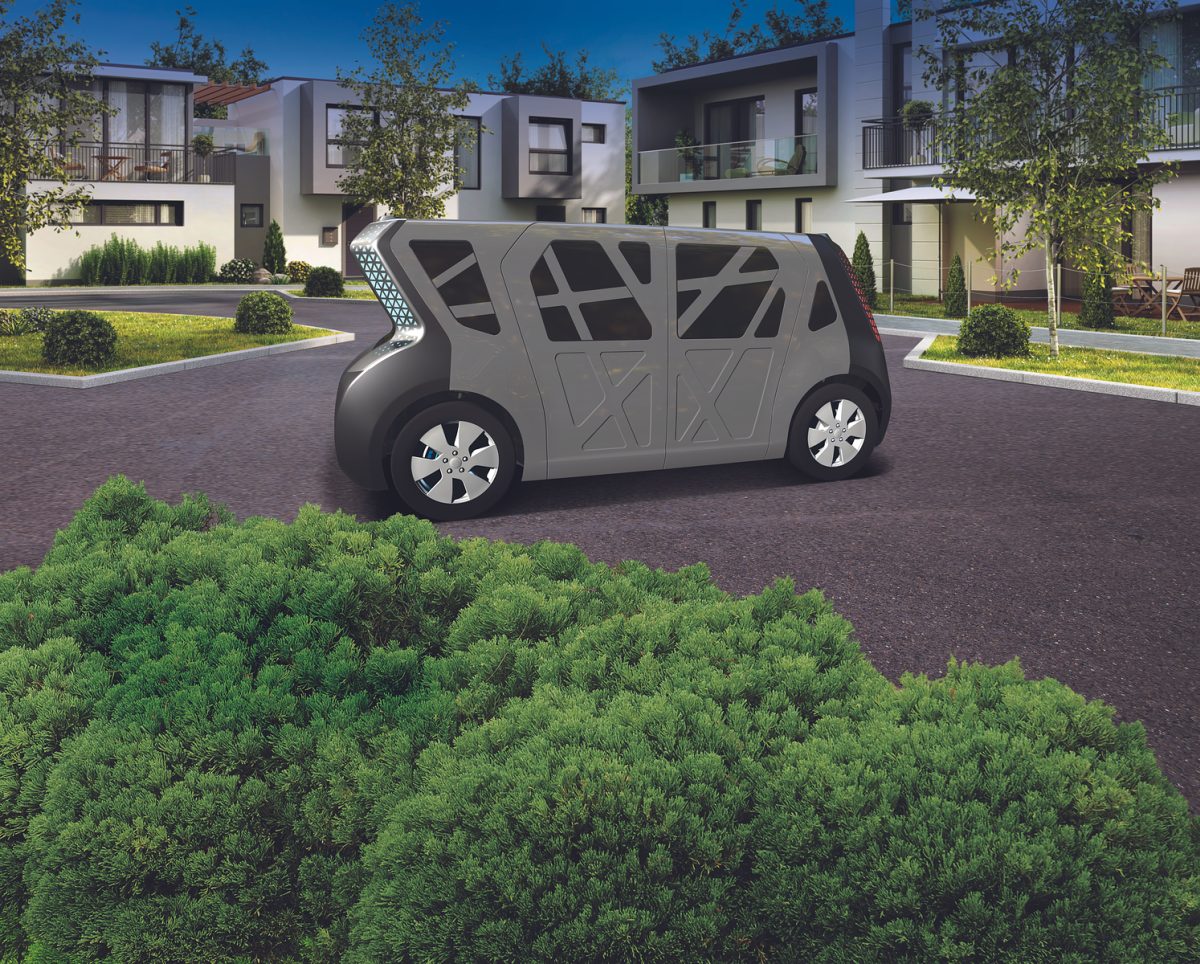
The Steel E-Motive concept is designed to be a Level 5 autonomous vehicle.
Designed to Exceed Future Mobility Safety Standards
Modern Advanced High-Strength Steels innovations allow the Steel E-Motive autonomous vehicle to exceed current global high-speed crashworthiness standards. By using AHSS, the Steel E-Motive vehicle is the first to acknowledge compliance with NHTSA and IIHS safety standards publicly.
For example, the 4-passenger B-sized urban concept SEM1 introduced a new front-end passenger protection zone. This design features the small overlap Glance Beam, which forces the car to “glance” off the barrier and reduces passenger cabin intrusion. It also lowers the crash pulse and ultimately minimizes passenger injury. Advanced High-Strength Steels also offer strong battery protection and preserve door ring integrity in this autonomous vehicle.
The Evolution of Advanced High-Strength Steel
Over the past quarter century, vehicle concept projects have showcased the continuous advancement of steel. In 1998, global steelmakers introduced the Ultralight Steel Auto Body, which used one of the earliest forms of AHSS. This project demonstrated steel’s ability to reduce weight without compromising safety.
By 2010, we introduced the Future Steel Vehicle concept. Using 27 AHSS materials, the body structure design reduced mass by over 35%. Steel materials enable these massive reductions while allowing the design to meet global crash and durability requirements.
The Steel E-Motive concepts benefit from no fewer than 64 materials under the AHSS umbrella. The “infinite tunability” of AHSS allows product customization by designers and engineers to select exactly the right steel for every need and purpose in the vehicle.
Key Attributes of the Steel E-Motive Autonomous Vehicle
From lowering the carbon footprint to massively reducing weight, the Steel E-Motive vehicle offers first-of-its-kind benefits for future mobility made possible by AHSS.
Steel allows the vehicle to reduce weight without sacrificing strength. For example, 66% of the Steel E-Motive autonomous vehicle structures’ materials have an Ultimate Tensile Strength of at least 1,000 MPa, and these materials’ weighted average tensile strength is 1259 MPa.
By using 33% Press Hardened Steels and 11% 3rd Generation AHSS, the design includes complex geometries fully formed by hot and cold-stamped gigapascal steels.
In another example, 43% of the Steel E-Motive structure is fabricated from material-efficient processes such as press hardening, hydroforming, roll forming, and roll stamping. With these processes, the steel body design maximizes material utilization and minimizes scrap rate. This means less material is produced, lowering the structure’s carbon footprint. These achievements reduce manufacturing costs to support a profitable margin both for the vehicle manufacturer and the mobility service provider.
Using AHSS, the Steel E-Motive autonomous vehicle’s body structure mass is 25% lower than benchmark vehicles of a similar volumetric footprint. Additionally, Steel E-Motive realizes a 27% lower battery frame cost than a fully enclosed battery design, with 37% mass savings.
In conclusion, the Steel E-Motive program stands as a remarkable testament to the innovative potential of steel in shaping the future of mobility and autonomous vehicles. With its groundbreaking design, the Steel E-Motive concept paves the way for Level 5 autonomous electric vehicles prioritizing safety, sustainability, and efficiency.
Harnessing the unique attributes of AHSS, this global steel industry initiative also showcases the remarkable evolution of steel materials over the years. From Ultralight Steel Auto Body to Future Steel Vehicle, the journey of AHSS has been one of continuous improvement, leading to Steel E-Motive’s exceptional achievements in weight reduction, enhanced safety, and minimized environmental impact.
As we venture into an era of net-zero emissions and advanced mobility solutions, the Steel E-Motive concept proudly positions steel as a driving force in shaping a cleaner, safer, and more connected future.
Download the Steel E-Motive Engineering Report