Steel E-Motive represents a fully autonomous ride sharing vehicle concept showcasing the strength and durability of steel with a critical focus on sustainability for reaching net zero emissions targets. The results are comfortable, safe and affordable body structures that support automakers in the continued development of Mobility as a Service (MaaS) ride sharing models.
The program highlights two virtual concepts designed for 2030 to 2035 deployment: SEM1, a four-passenger urban transport, and SEM2, a six-passenger extra-urban commuter, both designed for Level 5 autonomy with no steering wheel or pedal box. Both vehicles have the potential for more than an 85% total lifecycle CO2 emissions reduction by 2035, based on a comparison with a reference 2022 battery electric vehicle (BEV). A rigorous Life Cycle Assessment (LCA) approach was applied throughout the development of the Steel E-Motive concept. Both of these facets are highlighted in Figure 1.
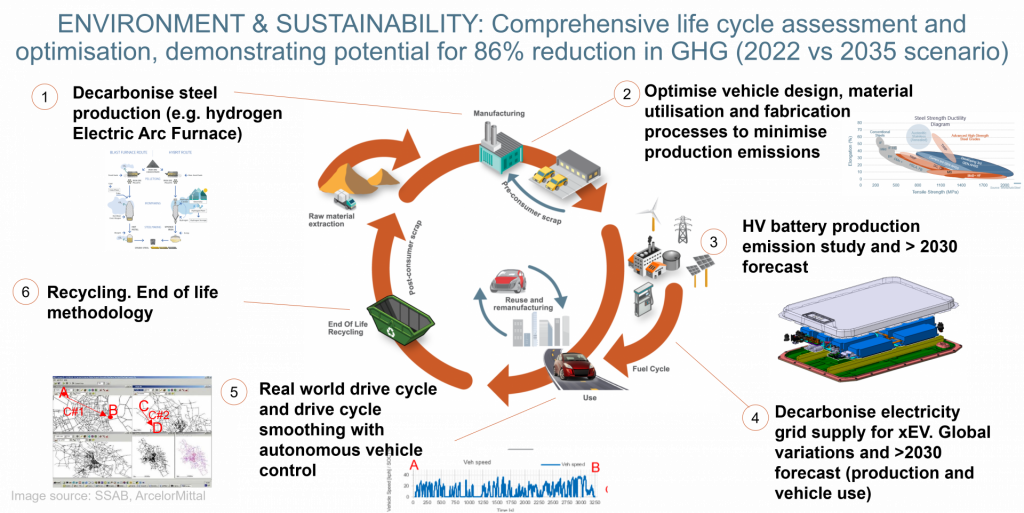
Figure 1: Key Contributors to Life Cycle Emissions Accounting Include Decarbonized Steel Production, Projected Battery and Electrical Grid Performance Improvements, and Operational Contributions of Autonomous MaaS.
Vehicle life cycle performance can vary considerably depending on where the vehicle is manufactured and operated. To account for this, life cycle performance of the Steel E-Motive concept was calculated for Europe, US, China, Japan and India regions.
Steel E-Motive concepts were developed for mixed traffic mode operation – thus safety was paramount. The SEM1 concept vehicle represents one of the world’s first autonomous vehicle engineered to meet global high speed crash regulations that can achieve the IIHS “Good” rating. The battery packaging approach is 37% lighter and 27% lower in cost than average reference battery case structures, and applicable for current BEVs in development. This innovation includes an air gap between the battery modules and removable bottom cover, providing additional security from road debris, and the opportunity for battery inspection and local repair, vs. battery box replacement.
Detailed simulations showed both concepts are manufacturable using global manufacturing and supply infrastructure at costs that can support profitable margins, both for the vehicle manufacturer and mobility service providers. Annual volumes of more than 250,000 vehicles for SEM1 and 90,000 units for SEM2 were contemplated in the projections.
Using the newest steel grades and fabrication processes, Steel E-Motive’s portfolio enables tailoring vehicle properties that achieve significant comfort, safety, and cost advantages with seven key innovations:
- A one-box open body B-pillarless structure provides a wider door aperture for easy ingress/egress, disabilities access and facilitates delivery services.
- A scissor door design integrating side impact protection directly into the door frame creates a compact section for better passenger visibility and improved passenger access while eliminating the body side outer for mass and cost savings.
- The Extended Passenger Protection Zone created with Advanced High Strength Steels provides excellent intrusion protection for rear-facing front passengers.
- The Short Front Crash Zone structure enabled by the use of PHS, MS and laser welded blanks meets the most stringent global crash requirements.
- The Small Offset Crash Glance Beam minimizes cabin intrusion and lowers crash pulse by creating a “glance-off” the barrier – preserving door ring and battery in 64 kph small overlap rigid barrier simulations.
- Hex beam energy absorbers in the rocker minimize side crash intrusion and achieves superior battery protection.
- An industry-first Battery Carrier Frame eliminates the conventional battery case, utilizing the existing floor as the top cover, and features an AHSS triple-skinned bottom cover that seals the battery and provides protection from road debris and jacking errors.
The Steel E-Motive program meets these requirements through extensive use of Advanced High-Strength Steels which offer favorable combinations of strength, ductility, toughness, and fatigue properties.
Different AHSS grade have unique properties which can be beneficial to different parts of a vehicle structure. Dual Phase and Transformation-Induced Plasticity steels are used in vehicle crash zones for their high energy absorption. Intrusion prevention is accomplished through the use of Martensitic and Press Hardened Steels.
The average tensile strength of the body structure is more than 1250 MPa, facilitating a lightweight structurally safe vehicle designed and fabricated to minimize the lifecycle carbon footprint.
The figures below highlight the types and deployment strategy of the steels used in the Steel E-Motive body-in-white. The full spectrum of grades in the portfolio are shown on our Defining Steels page. Of the grades shown in the full portfolio, 18 grades of steel, at 12 different gauges, were used in the primary Bill of Materials (BOM) for SEM1, for an average part sheet steel thickness of 1.2mm.
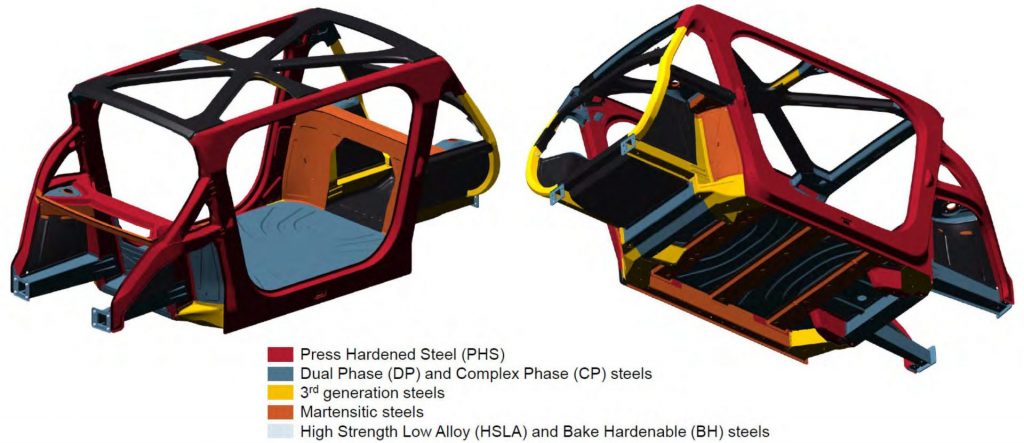
Figure 2: Steel E-Motive SEM1 BIW design and distribution of AHSS
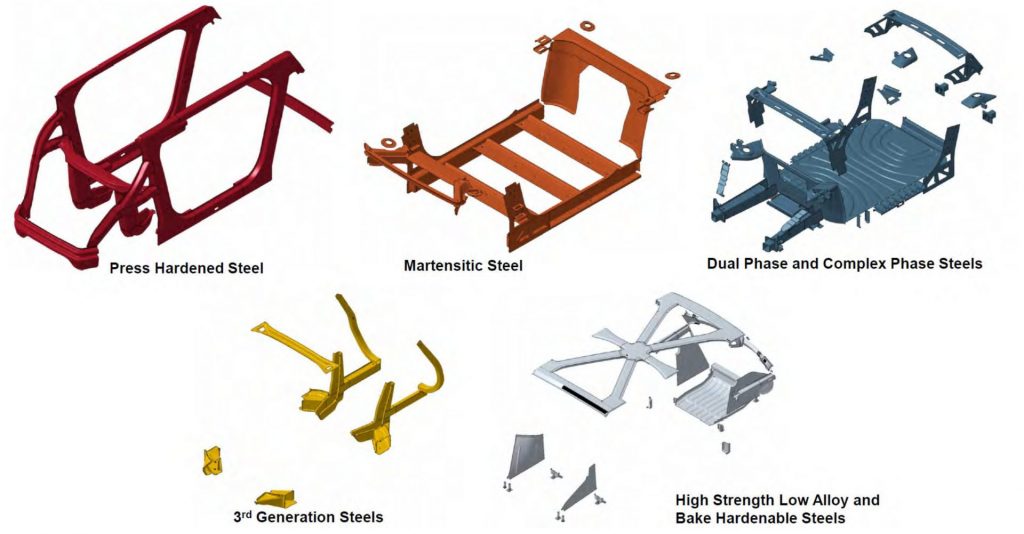
Figure 3: Steel E-Motive BIW AHSS grade allocation
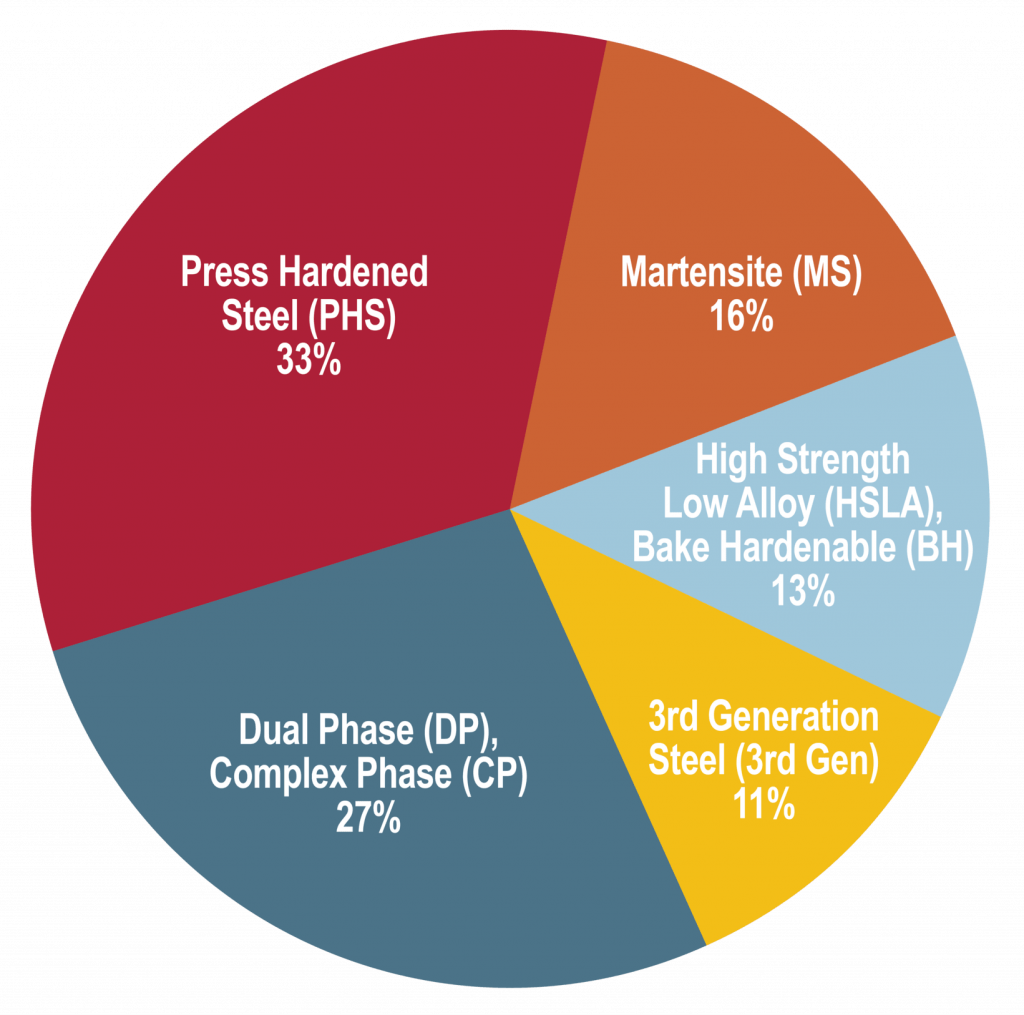
Figure 4: Steel E-Motive BIW AHSS grade distribution
Started in 2008, the FutureSteelVehicle (FSV) program built on more than a decade of work finding ways to decrease vehicle mass, reduce cost and meet comprehensive crash safety standards, all in pursuit of a smaller environmental footprint. FSV validated wide ranging research into the practical use of AHSS, innovative design and manufacturing technologies, and proposed specific examples for electrified vehicles (Figure 1). FSV used Life Cycle Analysis (LCA) to select the steels and manufacturing techniques that result in the lowest total carbon footprint, going beyond accounting only for emissions in the use phase.
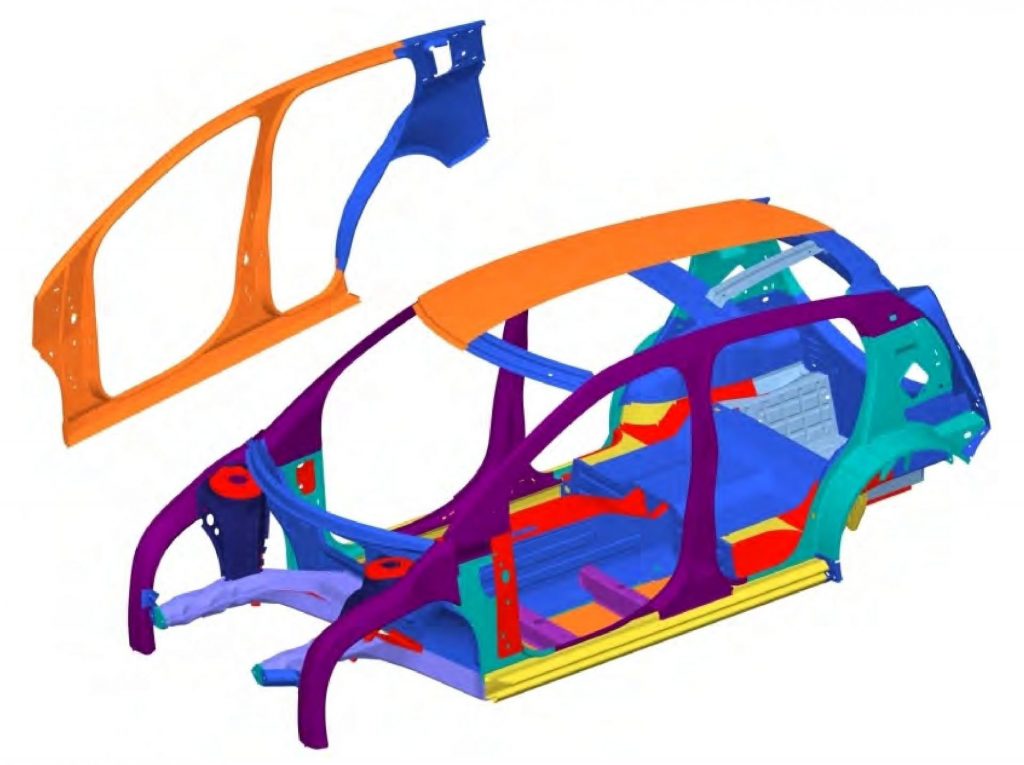
Figure 1: FutureSteelVehicle Battery Electric Vehicle Concept W-11, W-12
FutureSteelVehicle drew from a broad portfolio of steel types and grades, in a range of properties from mild to GigaPascal strength levels, applying a vast array of manufacturing processes. With advanced optimization algorithms, FSV incorporated hundreds of variables in the design process to identify a wide band of solutions. This approach integrated vehicle design, powertrain design and packaging, occupant space, passenger ingress/egress, driver sight angles, NVH, and aerodynamics to achieve a body structure that works in harmony with all vehicle requirements related to more stringent emissions and fuel efficiency standards while meeting safety (crash) standards and affordability.
The FSV project included structural variants for battery electric (BEV), plug-in hybrids (PHEV-20 and PHEV-40) and fuel cell (FCEV) powertrains, these same design attributes can be applied to conventional ICE-powered vehicles as well. Figure 2 highlights the FSV body materials breakdown.
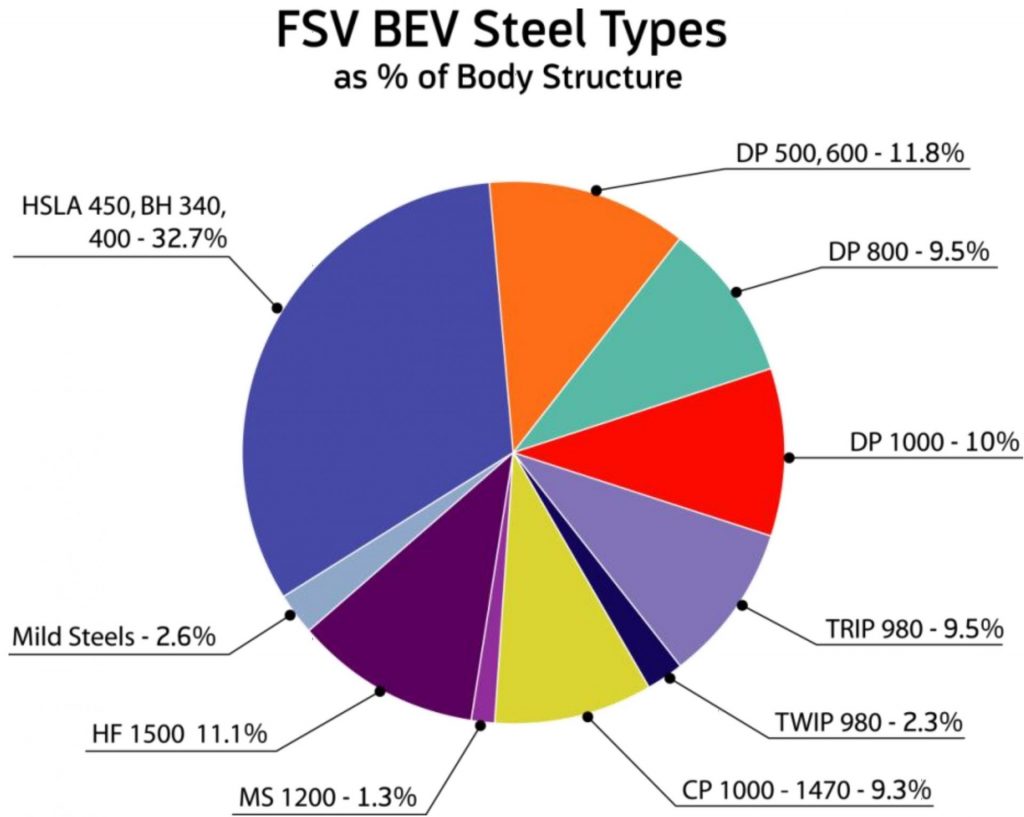
Figure 2: Future Steel Vehicle Body Materials Usage
Lower Weight
Extensive use of a broad portfolio of AHSS grades, coupled with engineering design optimization, enabled a robust body structure that is feasible to produce and achieves 5-star crash performance against all global crash standards, while also exceeding mass reduction targets. A lower weight, mass-efficient body creates opportunities for downsizing sub-systems, including the powertrain, and promotes reductions in overall vehicle mass. As an example, the body structure mass achievement for the FSV BEV variant is 177 kg W-39, including the battery tray – a component unique to a Battery Electric Vehicle. This compares quite favorably with the 2010 VW Polo, at 231 kg, which was recognized as Car of the Year in Europe because of its mass-efficient design but carries a lighter ICE gasoline powertrain. Table 1 highlights some of the benchmarking comparisons.
Table 1: FSV Benchmarking |
Vehicle |
Class |
Powertrain |
Curb Weight |
Body Mass |
Fuel Consumption (NEDC) |
FSV – BEV |
B+ |
BEV |
958 kg |
177 kg |
2.42 l/100 km (equiv) |
ULSAB – AVC |
C |
ICE-G |
933 kg |
202 kg |
4.40 l/100 km |
VW Polo |
B |
ICE-G |
1067 kg |
231 kg |
5.70 l/100 km |
Lower Cost
Steel is the most cost-competitive material for car bodies. It is economical to fabricate into components and sub-systems and to assemble into the total body-structure assembly. The resulting cost estimate of $1,115 to manufacture and assemble the complete FSV body validated this proposition and represents no cost penalty compared to vehicles at that time.
Lowest Total Lifetime Emissions
FutureSteelVehicle demonstrated the importance of Life Cycle Assessment as an integral element of a vehicle design process. In combination with optimizing the design for mass, cost, and functionality, FSV integrated into all analyses an accounting for its complete environmental footprint as measured in CO2e. It more appropriately comprehends the entire lifetime carbon footprint of the vehicle, not simply the use phase. This includes the entire fuel production cycle (well to pump), the fuel usage cycle (pump to wheels), the production of raw materials, as well as disposal/recycling.
FSV demonstrated that the coupling of a lightweight, AHSS body structure with a battery-electric powertrain results in a 50 to 70 percent reduction in total life cycle emissions, compared to equivalently sized vehicles with conventional gasoline ICEs W-12. Furthermore, based on the new steels’ light weighting capabilities, steel is the only material to realize emission reductions in all life cycle phases. Table 2 summarizes total vehicle carbon footprint and emissions performance by life cycle phase.
Table 2: FSV comparison between U.S. and Europe energy grids
|
Vehicle/Powertrain
|
Material & Recycling
(kg CO2e)
|
Use Phase
(kg CO2e)
|
Total Life Cycle
(kg CO2e)
|
Polo V ICEg |
1,479
|
32,655
|
34,134
|
FSV BEV USA grid |
1,328
|
13,844
|
15,172
|
FSV BEV Europe grid |
1,328
|
9,670
|
10,998
|
FSV vs. Polo V – USA grid |
– 56% CO2e reduction
|
FSV vs. Polo V – Europe grid |
– 68% CO2e reduction
|
Safety
The FSV design anticipated increasingly stringent crash safety standards over the decade following its release and was designed to meet European and U.S. 5-Star crash safety performance requirements over that time W-12. Using the latest holistic design and material optimization approaches combined with steel’s unmatched capabilities for design and manufacturing efficiency, the final FSV design comprised optimized, mass-efficient shapes that met or exceeded these global crash safety requirements.
Automakers face conflicting constraints when designing new body structures:
- With escalating concerns about human-induced green-house gases, global legislators have passed increasingly stringent vehicle emissions regulations, with even more aggressive targets planned for the coming years. Lighter weight body structures promote reduced vehicle emissions.
- Fuel price increases lead to greater consumer sensitivity to vehicle fuel economy. Lighter weight body structures also promote improved fuel economy.
- One of the easiest ways to reduce vehicle weight is to use thinner metal. To maintain crash performance, this thickness reduction must be accompanied by an increase in the strength of the sheet metal grade. Since thickness and stiffness are related, decreases in thickness must be accompanied by other methods to increase stiffness: either using a high-modulus material like steel, and/or using design features like darts or beads to lock in the shape. The chosen grade must be sufficiently formable to successfully incorporate these features.
- Automaker marketing departments highlight spacious interiors. Greater room can be accomplished by making larger vehicles, but the extra weight does not support mass reduction. On the other hand, use of more formable steels is a cost-effective way to increase packaging efficiency. New vehicle designs with complex geometries are aesthetically pleasing, but are difficult to form and join unless the chosen alloy has the necessary balance between strength and ductility.
- Global crash and safety regulations must be contemplated, especially if one body architecture will be used as the basis for vehicles intended for sale in multiple regions around the world. Increasing sheet metal thickness improves crash performance, so any reduction in thickness must be paired with using high strength grades where the deformation characteristics can be tuned to optimize crash energy management.
- All of these challenges must be addressed with sustainability in mind.
The global steel industry continues to develop new grades of steel defined by ever-increasing strength and ductility, continually reinventing this diverse material to address these challenges faced by automakers. Advanced High-Strength Steels (AHSS) are characterized by unique microstructures and metallurgical properties that allow OEMs to meet the diverse functional requirements of today’s vehicles.
Worldwide working groups within WorldAutoSteel member companies created the AHSS Application Guidelines to explain how and why AHSS steels are different from traditional higher strength steels in terms of press-forming, fabrication and joining for automotive underbody, structural, and body panel applications. This website provides in-depth current information on a wide range of topics related to successful application of these steels.
Automotive companies around the world have adopted different specification criteria. Steel companies have different production capabilities and commercial availability. As a result, the typical mechanical properties provided on this website simply illustrate the broad range of AHSS grades that may be available worldwide.
In addition, regional test procedures will cause a systematic variation in some properties measured on the same steel sample. One example is total elongation, where both measurement gauge length and gauge width are a function of the standard to which the test is conducted (ASTM, DIN, or JIS, also known as ISO I, II, or III), with these differences impacting the measured value. In addition, property requirements can be defined relative to either the rolling direction or transverse direction. Therefore, communication directly with individual steel companies is imperative to determine grade availability along with specific test procedures, associated parameters, and steel properties.
Blog, homepage-featured-top, main-blog, News
WorldAutoSteel has a 30-year legacy of steel demonstration all the way back to the Ultra-Light Steel Auto Body (ULSAB), whose engineering report is still being downloaded from our worldautosteel.org site today. The one you may remember best is the FutureSteelVehicle (FSV), results of which we launched in 2011. FSV demonstrated steel innovation for not only Battery Electric vehicles (BEV) but also Fuel Cell vehicles (FCV). Steel E-Motive is the sixth of our global steel industry programs.
So Why Mobility as a Service?
The Automotive sector is undergoing the most rapid change in 40 years. This transformation shifts our thinking – from the movement of vehicles to the efficient movement of people and goods. Over the past eight years, we have conducted extensive research into global trends such as urbanization, transport emissions reduction, as well as the waning interest in vehicle ownership among the young and old. This is especially prevalent in megacities characterized by pollution, congestion, limited parking and enormous ownership costs. Our research concluded that mobility as a service (MaaS) will grow exponentially in high population areas and would place a significant challenge on vehicle design and manufacturing. Therefore, we needed to make sure we as an industry were active and visible in providing STEEL solutions in this new market place.
Steel E-Motive will demonstrate the benefits of steel, linking the properties of the material to the required architectures and attributes for MaaS vehicles.
This program will demonstrate the benefits of steel, linking the properties of the material to the required architectures and attributes for MaaS vehicles. It connects us with original equipment manufacturers (OEMs) and future mobility providers (FMPs), reinforcing steel’s advantages in strength, durability, sustainability and affordability.
An autonomous BEV structure aligns perfectly with steel’s best attributes, however most new concepts trial alternative materials. The global steel industry is investing significantly in product and fabrication development to continually prepare for the next challenge. High Strength and Advanced High-Strength Steel (AHSS) portfolios have grown from the 11 highlighted in the ULSAB program, to more than 60 grades available for use in designing and optimizing Steel E-Motive’s autonomous BEV architecture. Third Generation AHSS (3rd Gen AHSS) will have a prominent role in Steel E-Motive’s body-in-white, taking strength levels ever higher while improving manufacturability. And our industry continues to evolve Press Hardened Steels (PHS) with strength levels upwards of 2000 MPa.
Finally, efficient fabrication processes such as roll stamping, press hardening, and hydroforming use less steel and therefore contribute lower vehicle production emissions. These are the details being highlighted in Steel E-Motive, where we hope to demonstrate that only Steel can make it Real.
Steel E-Motive: A game changing, world first?
Many OEM’s and mobility service providers follow the typical vehicle development process where they adapt an existing vehicle structure to the new vehicle requirements. We don’t have that in Steel E-Motive We believe Steel E-Motive is one of the world’s firsts.
- The first for a Level 5 autonomous vehicle that is compliant with global high-speed crash requirements.
- The first autonomous vehicle to be a conventional high-volume stamped steel body construction, creating an affordable platform for the mobility service provider.
- First to offer a competitive, robust, and sustainable MaaS solution.
For engineers, being first is very exciting but a little nerve wracking – there are no benchmarks out there. There is less to “hang on to.” We’re on our own. Target setting is more challenging; we are the benchmark. Time will tell if we make it to the automotive hall of fame.
We are producing concepts for two BEVs based on a single modular platform. SEM1 (Figure 1) is a front-wheel drive short wheelbase urban version for inter-city travel for four passengers. It has a compact design and vehicle footprint, comparable in footprint to a European B/C segment size. SEM2 (Figure 2) is an all-wheel drive, long wheelbase extra urban version designed to carry up to six passengers. It has an adaptable interior volume that can result in additional luggage capacity compared to SEM1.

Figure 1: SEM1 Vehicle Specifications (© WorldAutoSteel 2022)
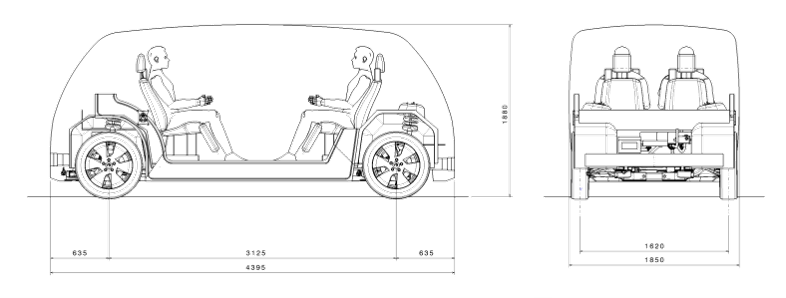
Figure 2: SEM2 Vehicle Specifications (© WorldAutoSteel 2022)
Body in White Steel Usage
Steel E-Motive benefits from a broad portfolio of steel grades and fabrication process, as identified by our member steel experts. The design is nearly finalized, and material selections are being evaluated against various performance targets with the representative structure shown in Figure 3 with high PHS usage at this stage in the design (as of May 2022). This is mainly driven by the safety requirements. Steel E-Motive BIW steel and steel technologies include:
- Right steel grade in the right place
- Significant proportion of >1500MPa grades, primarily for occupant and battery intrusion zones
- Mixture of stamped, roll formed, roll stamped, press hardened steel and hydroformed parts
- Spotweld, laser weld and structural adhesive

Figure 3: Steel E-Motive’s Body-in-White Steel usage as of May 2022. (© WorldAutoSteel 2022)
At the Core of the Steel E-Motive Concept Is an Innovative Battery Design
Figure 4 shows Steel E-Motive’s battery frame design’s construction:
- Battery modules and cooling plates are mounted to an AHSS carrier frame (off-line).
- The carrier frame is mounted to the body structure (in general assembly).
- The BIW floor acts as the top cover and provides sealing.
- The AHSS bottom cover plate provides impact protection.
This design provides significant cost and weight savings, as well as improved NVH. This extremely efficient package does not compromise safety and enables a flat floor with a lower step-in height.
Figure 4: Steel E-Motive Battery package assembly. (© WorldAutoSteel 2022)
Competitive Body Stiffness with an Open B-Pillarless Body Structure
With clean sheet design, and generally less package constraints in a Level 5 vehicle, our design teams have had more freedom to engineer and optimize the crash and stiffness structural loadpaths. We used topology, optimization, and Virtual Reality tools to determine the most efficient structural loadpaths (Figure 5). The results informed the joint designs and enabled optimization of the joining and structural adhesives. These steps and the advantage of steel’s high modulus resulted in impressive performance.
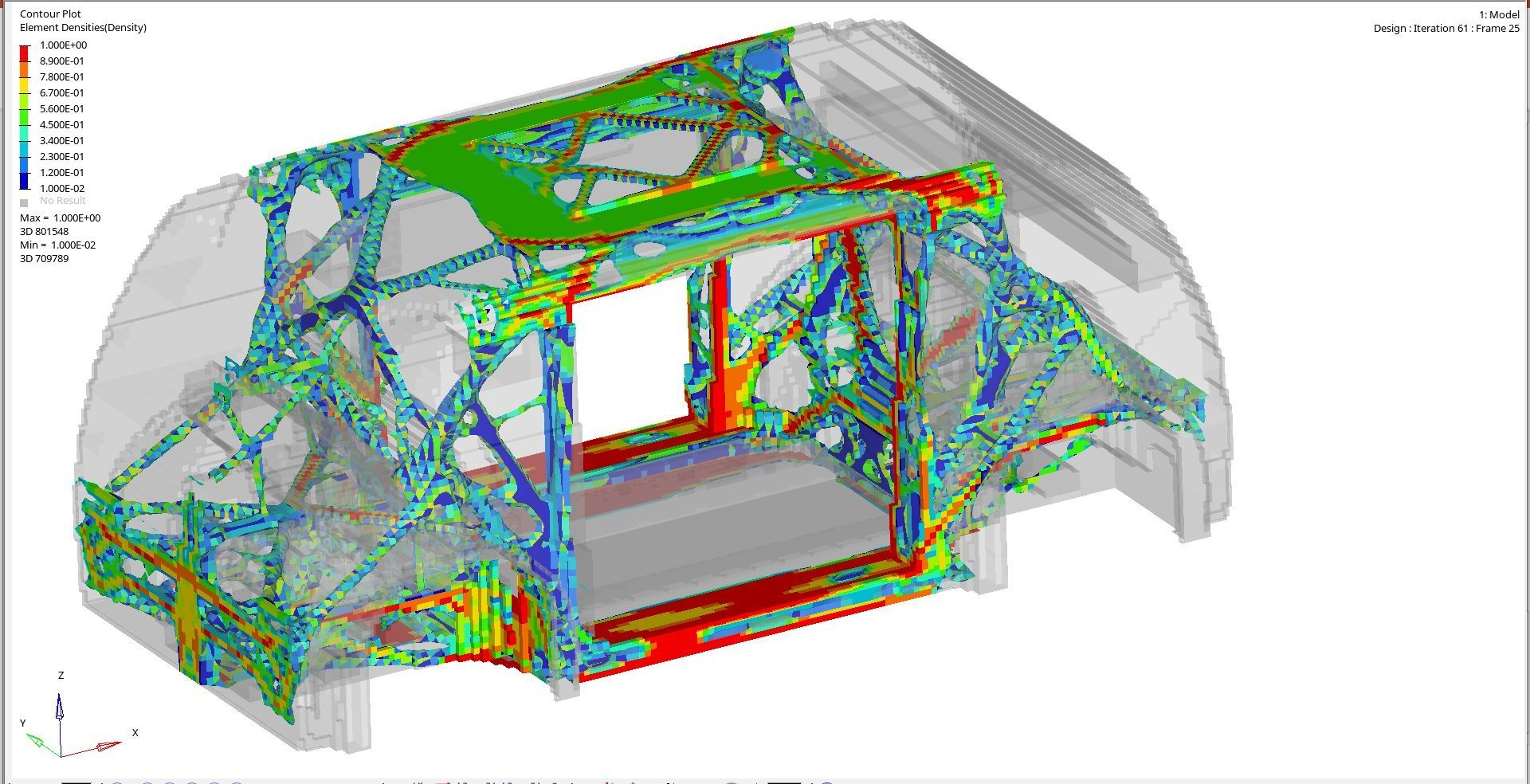
Figure 5: Topology Load Path Optimization. (© WorldAutoSteel 2022)
The approach for achieving body stiffness was as follows. Results are shown in Figure 6 following.
- Topology load path optimization
- Appropriate section size, profiles, part integration and flange / joint design
- Strut towers integrated with key body members, such as A-pillars, vertical dash brace
- Contribution from structural battery frame and battery cover closing, roof structure trusses
- Rigidly connected front and rear subframes
- Optimized joining and use of structural adhesives
- Capitalizing on the Inherent high modulus of steel
Figure 6: SEM Torsional Rigidity animation. (© WorldAutoSteel 2022)
Static torsional stiffness 38,000Nm/deg
Global trimmed BIW modes >28Hz
Local attachment static stiffness ten times bushing stiffness
Front Crash Structure Engineered to Balance the Requirements of 56kph USNCAP FFB, IIHS ODB, IIHS SORB and EuroNCAP MPDB Load cases
One of the most challenging aspects of the Steel E-Motive program has been achieving the front crash performance that minimizes occupant injury. The challenge has been compounded by the overall compact size of the vehicle and the short front overhang dimensions, meaning less space to manage and balance the required crush energy with intrusion resistance.
For the IIHS 25% Small Overlap test, we worked from the outset to achieve a barrier “glance off.” The goal is to deflect the vehicle off the barrier by the time the barrier reaches the hinge pillar. This results in a reduced amount of vehicle kinetic energy converted to crush energy. The vehicle continues after the impact with some onward velocity and kinetic energy. This strategy results in reduced intrusion to the passenger compartment and a much lower vehicle pulse (below 20g), which translates into lower occupant injury. We are very excited by this outcome, as in our benchmarking we have not seen many (if any) vehicles of this size managing to achieve a glance off for this test. Figures 7 and the bullets following provide a look at the results.
Figure 7: IIHS 25% Small Overlap test. (© WorldAutoSteel 2022)
- IIHS “good” rating achieved (based on predicted intrusions).
- Our strategy for IIHS Small Overlap test was to achieve a “glance off” the barrier, which is a significant challenge given the vehicle’s short front overhang.
- Front suspension engineered to detach on impact. This is important for achieving glance off.
- Glance off results in some continued onward vehicle velocity after the impact.
- This results in reduced crush energy, lower vehicle pulse and intrusions = enhanced occupant protection
Figure 8 points out features of the front crash structure. Most of the crush energy in FFB and ODB is absorbed by conventional longitudinal mid-rails, which are made of cold stamped, tailor welded blank Dual Phase steels. The plan view angle of the longitudinals has been optimized to provide load reaction early in the SORB event while remaining largely inside of the SORB barrier.
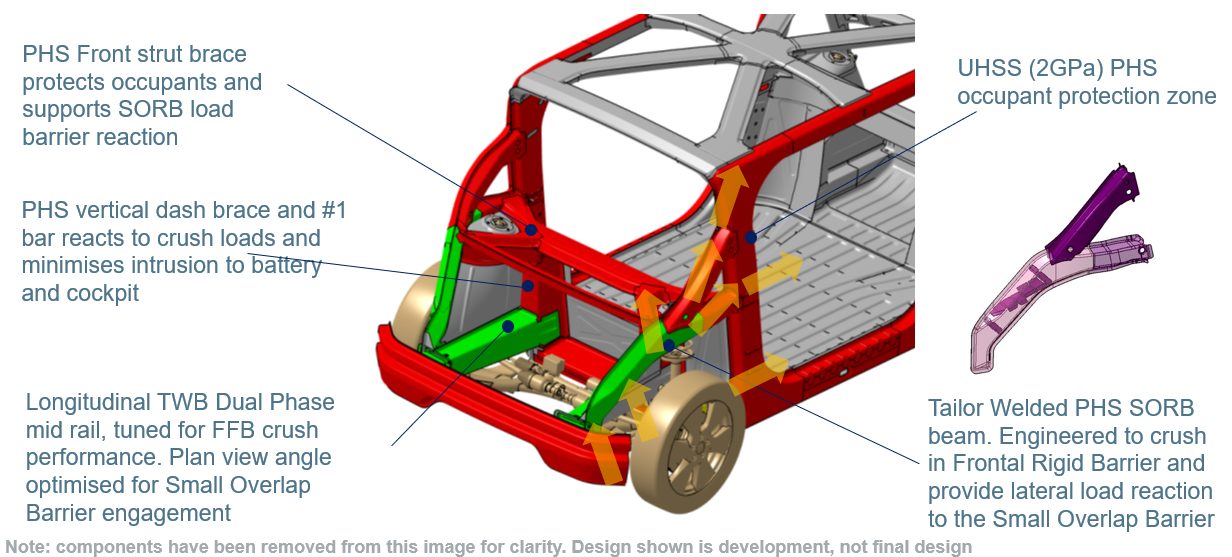
Figure 8: Front crash structure engineered to balance the requirements of 56kph USNCAP FFB, IIHS ODB, IIHS SORB and EuroNCAP MPDB load cases. (© WorldAutoSteel 2022)
Following in Figures 9 and 10 are animations of the FFB results:
|
Figure 9: USNCAP 56kph Rigid Barrier – Top View. (© WorldAutoSteel 2022) |
|
Figure 10: USNCAP 56kph Rigid Barrier – Side View. (© WorldAutoSteel 2022) |
MaaS vehicles will need to accommodate quick ingress and egress as well as provide comfort and safety for the occupants. Consequently, we have flipped the front occupant around to a rear facing configuration and provided a B-Pillarless wide door aperture to enable comfortable and quick access for passengers. This changes the approach required for occupant protection in a front crash. Effectively we are dealing with a high-speed rear impact situation for the occupant. Current rear impact tests cover lower speed rear end shunts. Figure 11 notes the key points and challenges that Steel E-Motive is designed to meet.
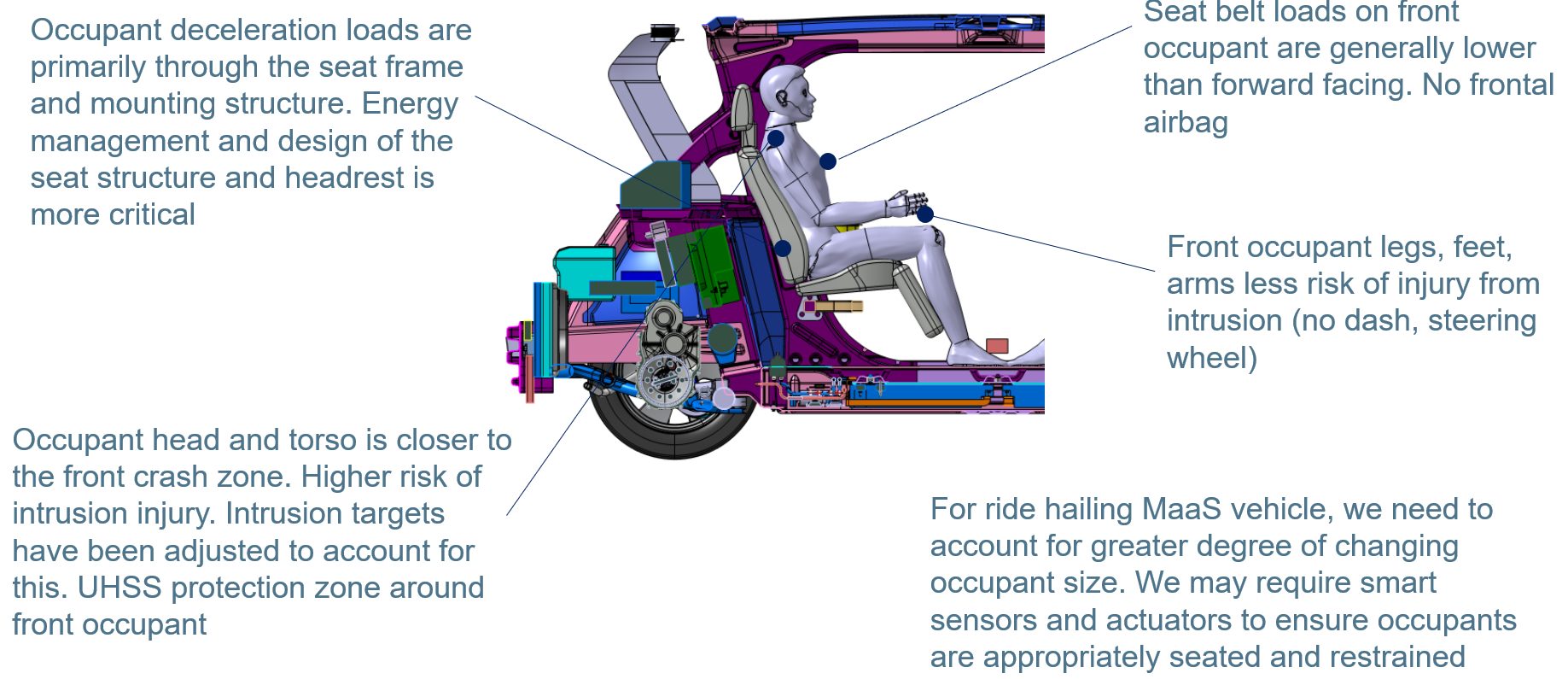
Figure 11: Different approach and considerations are required for the protection of rear facing front occupants. We are effectively addressing a high-speed rear impact event. (© WorldAutoSteel 2022)
Side Crash Structure Consists of Absorption and Intrusion Prevention Zones, Compensating for Large Body Aperture
The side structure includes roll-stamped martensitic door waist rail beams and a one-piece Tailor Welded Blank, Press Hardened Steel door ring outer. A- and C-pillars in line with occupants provide good side impact protection. (You can learn more about the door design in our May blog).
In the section AA schematic in Figure 12 the TRIP690 hydroformed tube interlocking door B-pillar is shown (wrapped over the rocker and cantrail). The load travels through the side impact crush “hex” beam, which is a two-piece roll formed DP590 component.
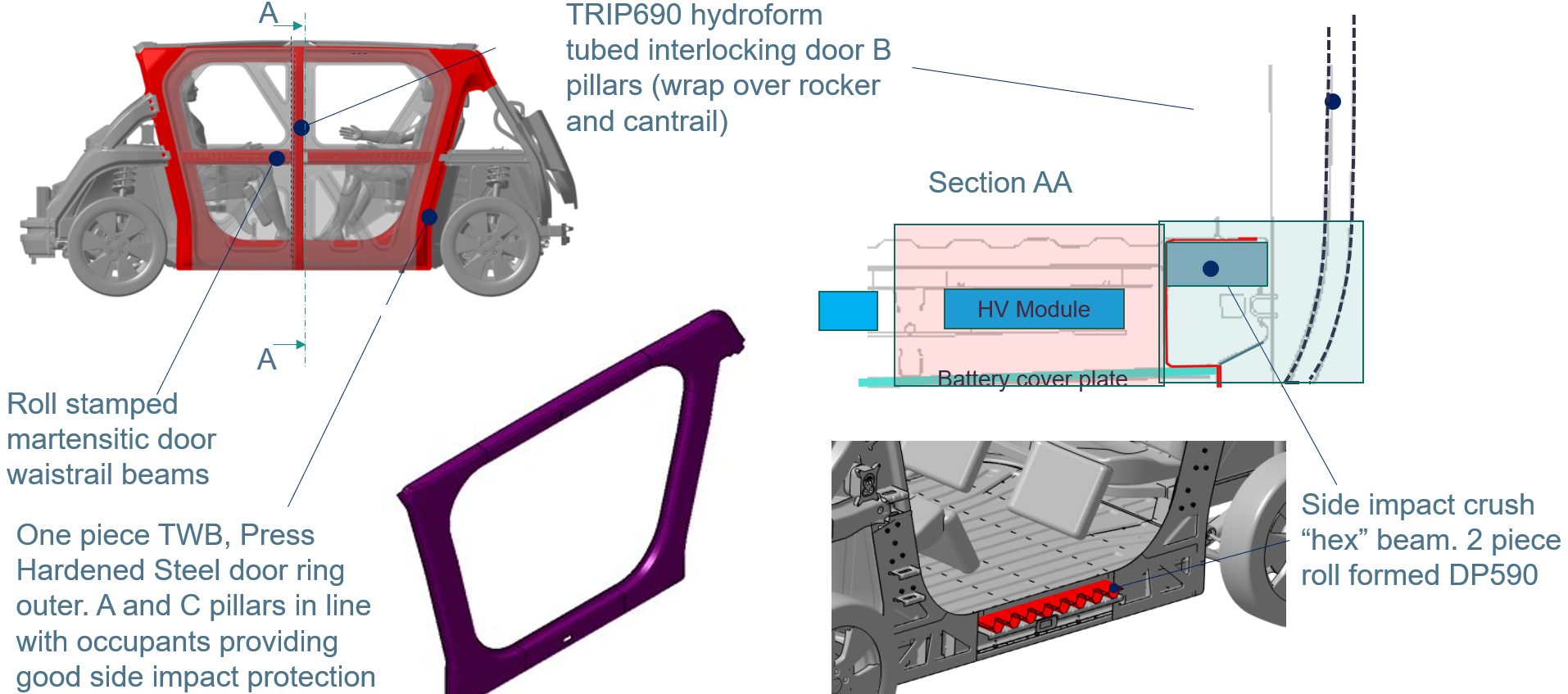
Figure 12: Side crash structure consists of absorption and intrusion prevention zones, compensating for large body aperture. (© WorldAutoSteel 2022)
Steel E-Motive Design Demonstrates Good Side Crashworthiness and Good Levels of Occupant and Battery Protection
In addition to occupant protection tests, additional side impact load cases have been simulated to ensure optimal battery protection. The design maintains a less than 30 mm clearance to the battery.
In reviewing the design according to IIHS standards and based on the predicted intrusions, we are confident this vehicle would achieve an IIHS “good” rating. See Figures 13 and 14 following:
Figure 13: USNCAP 32kph side pole (battery protection). (© WorldAutoSteel 2022)
In addition to occupant protection test, additional side pole load cases to ensure battery protection
>30mm clearance to battery maintained
Figure 14: IIHS 60kph side barrier II (occupant protection). (© WorldAutoSteel 2022)
IIHS “good” rating (based on predicted intrusions).
Total Cost of Ownership: Vehicle and Body Is Designed for Conventional Fabrication and Assembly Processes
The Steel E-Motive body has been designed with low cost in mind to provide the foundation for a lower total cost of ownership for fleet owners. The steel body design is optimized to maximize material utilization and minimize scrap rate. Steel E-Motive is suitable for >250,000 units/year production and is compatible with existing global automotive manufacturing facilities using conventional press and fabrication tools. We are also using Life Cycle Assessment as an integral part of the engineering process to ensure that Steel E-Motive is responsible for the lowest possible emissions throughout its entire life cycle. We will report on environmental performance and sustainability as a part of our final results.
Steel E-Motive Key Outcomes
The Steel E-Motive program is delivering an exciting futuristic vehicle, optimized from the ground up for autonomous MaaS application. We are addressing key challenges through careful design, application of simulation tools and efficient use of the latest Advanced High-Strength Steels and fabrication processes. Steel’s inherent characteristics of low production emissions, lightweighting capabilities for mass efficiency, infinite recyclability and product durability underscores its suitability as an integral part of stakeholder strategies to offer sustainable mobility solutions, today and in the future.
Be sure to follow us on our journey as we enter our final months of design, engineering and reporting by subscribing at the Steel E-Motive website. We welcome your questions about this program using the Comment box below.
Images are not for use without permission. Contact steel@worldautosteel.org.
About
WorldAutoSteel will consider appropriate articles from expert sources for publication on our AHSS Insights blog. In order to be considered, you must meet the requirements set forth below. Please keep in mind, however, that we do not pay for, or charge for, posting guest blogs. But we are more than willing to consider articles that are relevant to educating on best practices and new processes in the forming and joining of Advanced High-Strength Steels (AHSS) in vehicle applications.
If you still have questions about being a Guest Blogger for WorldAutoSteel after reading this page, you may contact the AHSS Guidelines Editor, Lori Jo Vest
Fundamentals
Please keep in mind the following fundamentals before you start writing your blog.
- Your submission must contain references to Advanced High-Strength Steel (AHSS) in vehicle applications. Note that the name of our blog is AHSS Insights, therefore, readers will be expecting to expand their AHSS knowledge base.
- Your submission must be geared towards a technical audience, with appropriate data references. Our audiences include automotive engineers that specialize in design, materials, manufacturing and the environment. We generally do not accept thought-starter type guest blogs.
- Your submission must not be a marketing piece for your organization, proprietary products or services, nor should it contain marketing messages and solicitations. Our readers are smart people. They will appreciate and gain much more insight into your company by simply demonstrating your expertise and showing your products’ purpose in AHSS use, than they would in a sales pitch.
- It should contain information pertinent to our audiences on an aspect of AHSS, such as AHSS characteristics, use, metallurgy, forming or joining. It also may address vehicle or steel industry life cycle assessment or other environmental issues related to automotive and AHSS use.
- Your submission must include graphic references. You may decide what kind of graphics you would like to add such as charts, videos, infographics, etc. We welcome videos as long as they do not include a sales pitch. Graphics need to be submitted as PNG or SVG files, and videos must be a standard format, such as MP4 or WMV.
Submission Requirements
Please meet the following submission requirements before you submit your entry for consideration.
- Submissions should be approximately 1,000 words in length, and include graphics.
- Please include a title.
- Graphics should be provided as separate 72 dpi (PNG or SVG) files, if possible, and sourced appropriately, especially if you do not specifically own the rights. Videos should be 720p resolution.
- Please clearly provide any reference sources in the following format: Author, full title of the work, year published, and if available and it will add to the blog’s content value, provide an internet link to the work.
- Please notify us with your intention to submit with an brief abstract of the information you will cover. This will help us determine if it is a good fit and enable us to potentially provide provisional approval.
- Your first draft must be submitted a minimum of 30 business days prior to any agreed upon publish date. This allows our team to have ample time for review, give you feedback and pursue any required further editing. It also provides time for translation to our Chinese blog edition.
- As your blog will be translated to the Chinese language and published on our channels in China, please do not use English jargon that will be difficult to translate.
We will notify you in advance as to when your entry is scheduled to publish. We strongly encourage you to use your social contact network to share the blog article. Your shares should include our blog hashtag, #AHSSblog.
Submitting Video and Animation Assets
We are always looking for video and animations to help support existing articles with visual information. If you think you have something that would enhance an article, please contact us at the email link above. You can send us a link to what you have, and we will review it. Note, the video must be owned by you in order to be considered and not contain any sales pitches. If we agree to use it, we’ll need to receive the original video file so that it can be uploaded directly to our site. You/your company will receive full citation as a the source of the video. Have a look at our Roll Forming page to see an example of how we have used a video received from Shape Corp.
We look forward to receiving your submission. It is our pleasure to collaborate on AHSS education with you. Thank you!