Blog, homepage-featured-top, main-blog
The leading source for technical best practices on the forming and joining of Advanced High-Strength Steels (AHSS) for vehicle manufacture is released today by WorldAutoSteel, the automotive group of the World Steel Association. The AHSS Application Guidelines Version 7.0 is now online at ahssinsights.org in a searchable database, allowing users to pinpoint information critical to successful use of these amazingly capable steels. WorldAutoSteel members make these Guidelines freely available for use to the world’s automotive community.
“More and more automakers are turning to AHSS to balance the needs for crashworthiness, lighter weight and lower emissions, while still manufacturing cars that are affordable,” says George Coates, Technical Director, WorldAutoSteel. “The AHSS Application Guidelines provides critical knowledge that will help users adapt their manufacturing environment to these evolving steels and understand processes and technologies that lead to efficient vehicle structures.” AHSS constitute as much as 70 percent of the steel content in vehicle structures today, according to automaker reports.
New grades of steel that are profiled in Version 7.0 show dramatically increased strength while achieving breakthrough formability, enabling applications and geometries that previously were not attainable.
“Steel’s low primary production emissions, now coupled with efficient fabrication methods, as well as a strong global recycling and reuse infrastructure all create a solid foundation upon which to pursue vehicle carbon neutrality,” notes Cees ten Broek, Director, WorldAutoSteel. “These Guidelines contain knowledge gleaned from global research and experience, including significant investment of our members who are the designers and manufacturers of these steels.”
Editors and Authors Dr. Daniel Schaeffler, President Engineering Quality Solutions, Inc., for Metallurgy and Forming, and Menachem Kimchi, M.Sc., Assistant Professor – Practice, Materials Science and Engineering, Ohio State University, have drawn from the insights of WorldAutoSteel members companies, automotive OEMs and suppliers, and leading steel researchers and application experts. Together with their own research and field experience, the technical team have refreshed existing data and added a wealth of new information in this updated version.
The new database includes a host of new resources for automotive engineers, design and manufacturing personnel and students of automotive manufacturing, including:
- Hundreds of pages of searchable articles that include nearly 1,000 citations of original technical research papers, providing a rich library for study.
- Search tools and related posts fueled by thousands of industry-specific keywords that enable users to drill down to the information they need.
- Information on the metallurgy and mechanics of AHSS grades.
- An explanation of 3rd Gen AHSS and what makes these grades unique.
- A primer on Press Hardened Steels, one of the most popular AHSS grades in today’s automotive structures.
- Summaries of new research in resistance spot welding for joining AHSS of multiple grades and thicknesses.
- New information on modelling resistance spot welding.
- An expanded solid state welding section.
- New information on RSW joining of dissimilar steels as well as dissimilar materials.
- Articles written by subject-matter experts and product manufacturers.
- Integration of the popular AHSS Insights technical blog.
The new online format enables consistent annual updates as new mastery of AHSS’s unique microstructures is gained, new technology and grades are developed, and data is gathered. Be sure to subscribe to receive regular updates and blogs that represent a world of experience as the database evolves.
You’re right where you need to be to start exploring the database. Click Tutorials from the top menu to get a tour on how the site works so you can make the best of your experience. Come back often–we’re available 24/7 anywhere in the world, no download needed!
1stGen AHSS, AHSS, Steel Grades
Dual Phase (DP) steels have a microstructure consisting of a ferritic matrix with martensitic islands as a hard second phase, shown schematically in Figure 1. The soft ferrite phase is generally continuous, giving these steels excellent ductility. When these steels deform, strain is concentrated in the lower-strength ferrite phase surrounding the islands of martensite, creating the unique high initial work-hardening rate (n-value) exhibited by these steels. Figure 2 is a micrograph showing the ferrite and martensite constituents.
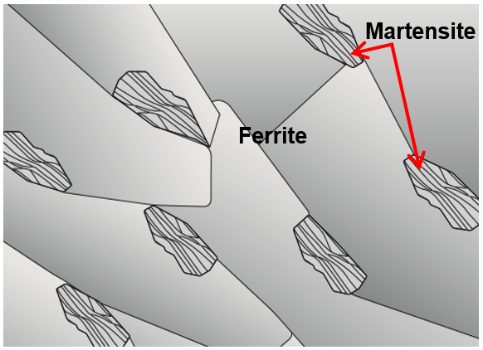
Figure 1: Schematic of a Dual Phase steel microstructure showing islands of martensite in a matrix of ferrite.
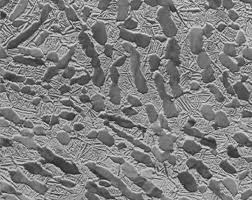
Figure 2: Micrograph of Dual Phase Steel
Hot rolled DP steels do not have the benefit of an annealing cycle, so the dual phase microstructure must be achieved by controlled cooling from the austenite phase after exiting the hot strip mill finishing stands and before coiling. This typically requires a more highly alloyed chemistry than cold rolled DP steels require. Higher alloying is generally associated with a change in welding practices.
Continuously annealed cold-rolled and hot-dip coated Dual Phase steels are produced by controlled cooling from the two-phase ferrite plus austenite (α + γ) region to transform some austenite to ferrite before a rapid cooling transforms the remaining austenite to martensite. Due to the production process, small amounts of other phases (bainite and retained austenite) may be present.
Higher strength dual phase steels are typically achieved by increasing the martensite volume fraction. Depending on the composition and process route, steels requiring enhanced capability to resist cracking on a stretched edge (as typically measured by hole expansion capacity) can have a microstructure containing significant quantities of bainite.
The work hardening rate plus excellent elongation creates DP steels with much higher ultimate tensile strengths than conventional steels of similar yield strength. Figure 3 compares the engineering stress-strain curve for HSLA steel to a DP steel curve of similar yield strength. The DP steel exhibits higher initial work hardening rate, higher ultimate tensile strength, and lower YS/TS ratio than the HSLA with comparable yield strength. Additional engineering and true stress-strain curves for DP steel grades are presented in Figures 4 and 5.
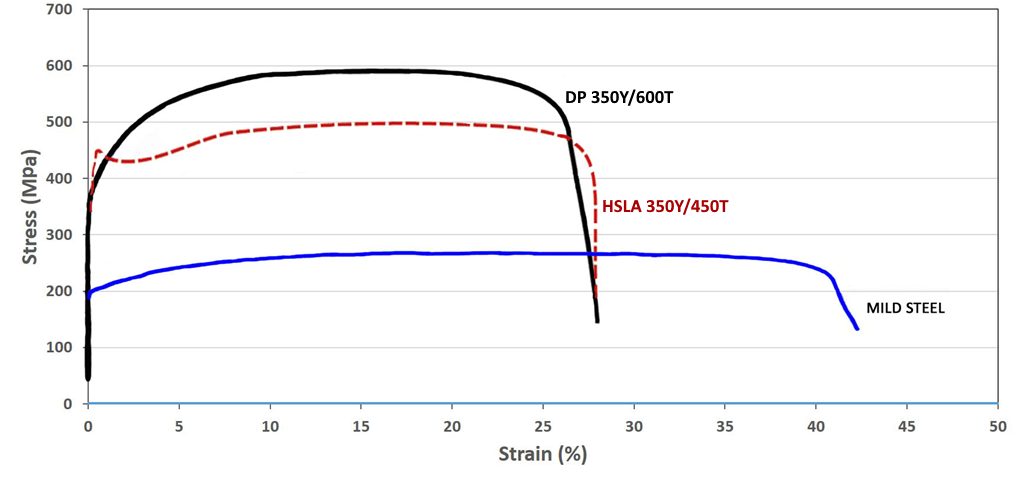
Figure 3: A comparison of stress strain curves for mild steel, HSLA 350/450, and DP 350/600K-1

Figure 4: Engineering stress-strain curves for a series of DP steel grades.S-5, V-1 Sheet thicknesses: DP 250/450 and DP 500/800 = 1.0mm. All other steels were 1.8-2.0mm.

Figure 5: True stress-strain curves for a series of DP steel grades.S-5, V-1 Sheet thicknesses: DP 250/450 and DP 500/800 = 1.0mm. All other steels were 1.8-2.0mm.
DP and other AHSS also have a bake hardening effect that is an important benefit compared to conventional higher strength steels. The extent of the bake hardening effect in AHSS depends on an adequate amount of forming strain for the specific chemistry and thermal history of the steel.
In DP steels, carbon enables the formation of martensite at practical cooling rates by increasing the hardenability of the steel. Manganese, chromium, molybdenum, vanadium, and nickel, added individually or in combination, also help increase hardenability. Carbon also strengthens the martensite as a ferrite solute strengthener, as do silicon and phosphorus. These additions are carefully balanced, not only to produce unique mechanical properties, but also to maintain the generally good resistance spot welding capability. However, when welding the higher strength grades (DP 700/1000 and above) to themselves, the spot weldability may require adjustments to the welding practice.
Examples of current production grades of DP steels and typical automotive applications include:
DP 300/500 |
Roof outer, door outer, body side outer, package tray, floor panel |
DP 350/600 |
Floor panel, hood outer, body side outer, cowl, fender, floor reinforcements |
DP 500/800 |
Body side inner, quarter panel inner, rear rails, rear shock reinforcements |
DP 600/980 |
Safety cage components (B-pillar, floor panel tunnel, engine cradle, front sub-frame package tray, shotgun, seat) |
DP 700/1000 |
Roof rails |
DP 800/1180 |
B-Pillar upper |
Some of the specifications describing uncoated cold rolled 1st Generation dual phase (DP) steel are included below, with the grades typically listed in order of increasing minimum tensile strength and ductility. Different specifications may exist which describe hot or cold rolled, uncoated or coated, or steels of different strengths. Many automakers have proprietary specifications which encompass their requirements.
- ASTM A1088, with the terms Dual phase (DP) steel Grades 440T/250Y, 490T/290Y, 590T/340Y, 780T/420Y, and 980T/550YA-22
- EN 10338, with the terms HCT450X, HCT490X, HCT590X, HCT780X, HCT980X, HCT980XG, and HCT1180XD-6
- JIS G3135, with the terms SPFC490Y, SPFC540Y, SPFC590Y, SPFC780Y and SPFC980YJ-3
- JFS A2001, with the terms JSC590Y, JSC780Y, JSC980Y, JSC980YL, JSC980YH, JSC1180Y, JSC1180YL, and JSC1180YHJ-23
- VDA 239-100, with the terms CR290Y490T-DP, CR330Y590T-DP, CR440Y780T-DP, CR590Y980T-DP, and CR700Y980T-DPV-3
- SAE J2745, with terms Dual Phase (DP) 440T/250Y, 490T/290Y, 590T/340Y, 6907/550Y, 780T/420Y, and 980T/550YS-18
1stGen AHSS, 3rdGen AHSS, AHSS, Steel Grades
topofpage
The microstructure of Transformation Induced Plasticity (TRIP) steels contains a matrix of ferrite, with retained austenite, martensite, and bainite present in varying amounts. Production of TRIP steels typically requires the use of an isothermal hold at an intermediate temperature, which produces some bainite. Higher silicon and carbon content of TRIP steels result in significant volume fractions of retained austenite in the final microstructure. Figure 1 shows a schematic of TRIP steel microstructure, with Figure 2 showing a micrograph of an actual sample of TRIP steel. Figure 3 compares the engineering stress-strain curve for HSLA steel to a TRIP steel curve of similar yield strength.
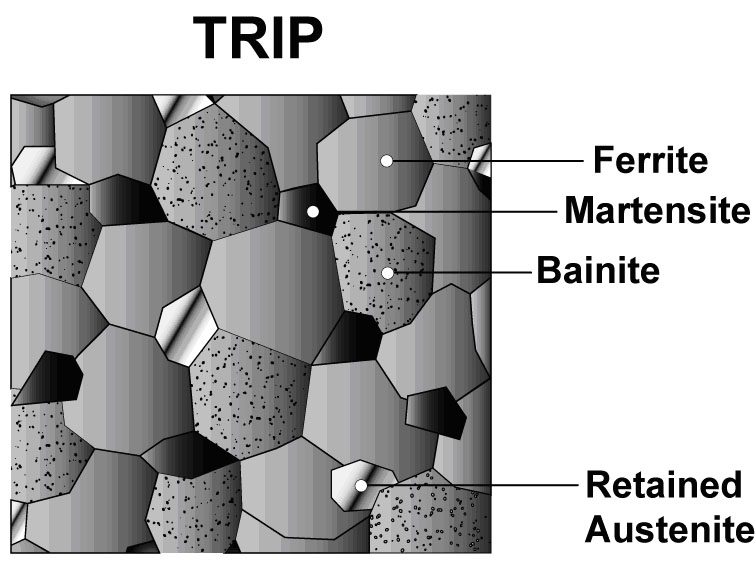
Figure 1: Schematic of a TRIP steel microstructure showing a matrix of ferrite, with martensite, bainite and retained austenite as the additional phases.
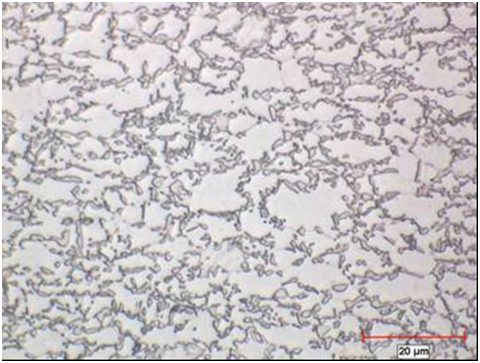
Figure 2: Micrograph of Transformation Induced Plasticity steel.
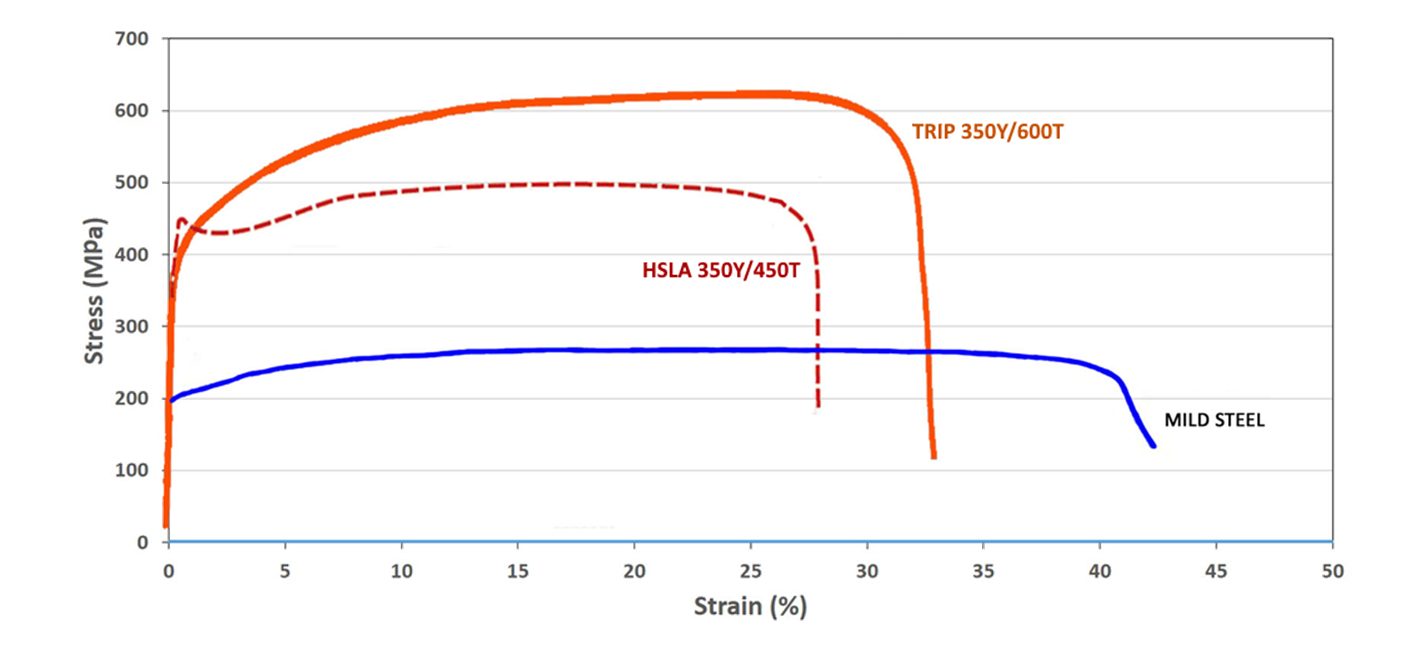
Figure 3: A comparison of stress strain curves for mild steel, HSLA 350/450, and TRIP 350/600.K-1
During deformation, the dispersion of hard second phases in soft ferrite creates a high work hardening rate, as observed in the DP steels. However, in TRIP steels the retained austenite also progressively transforms to martensite with increasing strain, thereby increasing the work hardening rate at higher strain levels. This is known as the TRIP Effect. This is illustrated in Figure 4, which compares the engineering stress-strain behavior of HSLA, DP and TRIP steels of nominally the same yield strength. The TRIP steel has a lower initial work hardening rate than the DP steel, but the hardening rate persists at higher strains where work hardening of the DP begins to diminish. Additional engineering and true stress-strain curves for TRIP steel grades are shown in Figure 5.
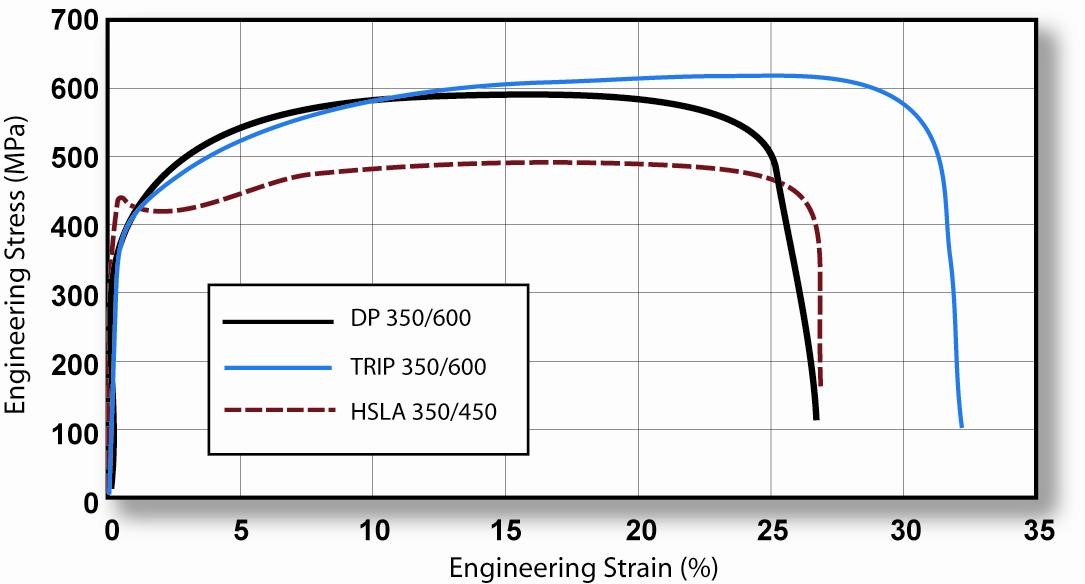
Figure 4: TRIP 350/600 with a greater total elongation than DP 350/600 and HSLA 350/450. K-1
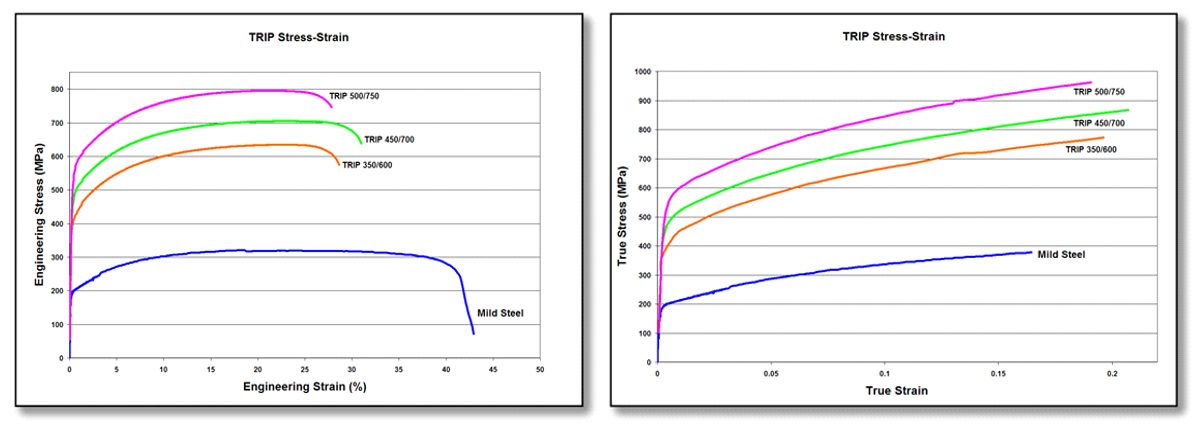
Figure 5: Engineering stress-strain (left graphic) and true stress-strain (right graphic) curves for a series of TRIP steel grades. Sheet thickness: TRIP 350/600 = 1.2mm, TRIP 450/700 = 1.5mm, TRIP 500/750 = 2.0mm, and Mild Steel = approx. 1.9mm. V-1
The strain hardening response of TRIP steels are substantially higher than for conventional HSS, resulting in significantly improved formability in stretch deformation. This response is indicated by a comparison of the n-value for the grades. The improvement in stretch formability is particularly useful when designers take advantage of the improved strain hardening response to design a part utilizing the as-formed mechanical properties. High n-value persists to higher strains in TRIP steels, providing a slight advantage over DP in the most severe stretch forming applications.
Austenite is a higher temperature phase and is not stable at room temperature under equilibrium conditions. Along with a specific thermal cycle, carbon content greater than that used in DP steels are needed in TRIP steels to promote room-temperature stabilization of austenite. Retained austenite is the term given to the austenitic phase that is stable at room temperature.
Higher contents of silicon and/or aluminum accelerate the ferrite/bainite formation. These elements assist in maintaining the necessary carbon content within the retained austenite. Suppressing the carbide precipitation during bainitic transformation appears to be crucial for TRIP steels. Silicon and aluminum are used to avoid carbide precipitation in the bainite region.
The carbon level of the TRIP alloy alters the strain level at which the TRIP Effect occurs. The strain level at which retained austenite begins to transform to martensite is controlled by adjusting the carbon content. At lower carbon levels, retained austenite begins to transform almost immediately upon deformation, increasing the work hardening rate and formability during the stamping process. At higher carbon contents, retained austenite is more stable and begins to transform only at strain levels beyond those produced during forming. At these carbon levels, retained austenite transforms to martensite during subsequent deformation, such as a crash event.
TRIP steels therefore can be engineered to provide excellent formability for manufacturing complex AHSS parts or to exhibit high strain hardening during crash deformation resulting in excellent crash energy absorption.
The additional alloying requirements of TRIP steels degrade their resistance spot-welding behavior. This can be addressed through weld cycle modification, such as the use of pulsating welding or dilution welding. Table 1 provides a list of current production grades of TRIP steels and example automotive applications:
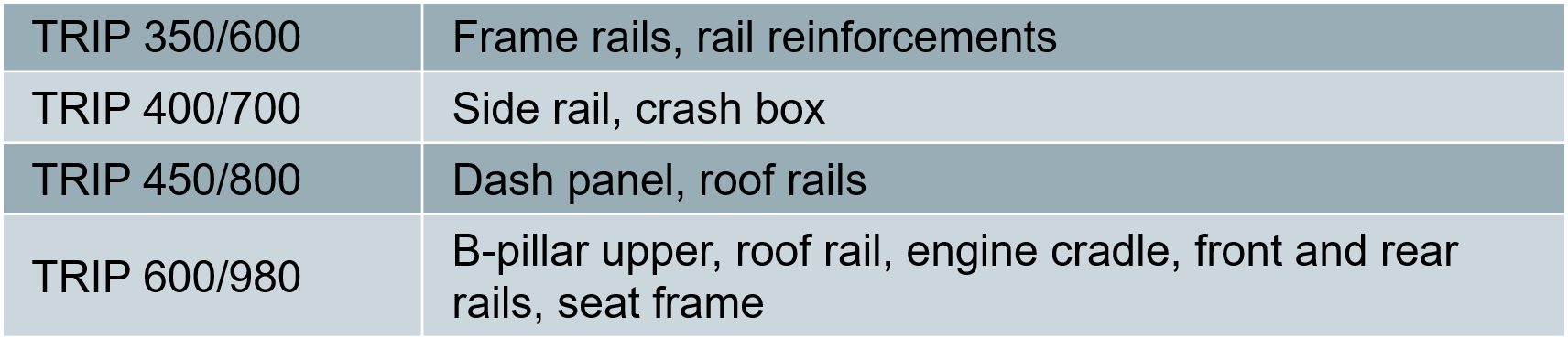
Table 1: Current Production Grades Of TRIP Steels And Example Automotive Applications.
Some of the specifications describing uncoated cold rolled 1st Generation transformation induced plasticity (TRIP) steel are included below, with the grades typically listed in order of increasing minimum tensile strength and ductility. Different specifications may exist which describe hot or cold rolled, uncoated or coated, or steels of different strengths. Many automakers have proprietary specifications which encompass their requirements.
• ASTM A1088, with the terms Transformation induced plasticity (TRIP) steel Grades 690T/410Y and 780T/440YA-22
• JFS A2001, with the terms JSC590T and JSC780TJ-23
• EN 10338, with the terms HCT690T and HCT780TD-18
• VDA 239-100, with the terms CR400Y690T-TR and CR450Y780T-TRV-3
• SAE J2745, with terms Transformation Induced Plasticity (TRIP) 590T/380Y, 690T/400Y, and 780T/420YS-18
Transformation Induced Plasticity Effect
Austenite is not stable at room temperature under equilibrium conditions. An austenitic microstructure is retained at room temperature with the combined use of a specific chemistry and controlled thermal cycle. Deformation from sheet forming provides the necessary energy to allow the crystallographic structure to change from austenite to martensite. There is insufficient time and temperature for substantial diffusion of carbon to occur from carbon-rich austenite, which results in a high-carbon (high strength) martensite after transformation. Transformation to high strength martensite continues as deformation increases, as long as retained austenite is still available to be transformed.
Alloys capable of the TRIP effect are characterized by a high ductility – high strength combination. Such alloys include 1st Gen AHSS TRIP steels, as well as several 3rd Gen AHSS grades like TRIP-Assisted Bainitic Ferrite, Carbide Free Bainite, and Quench & Partition Steels.
Back to the Top
1stGen AHSS, AHSS, Steel Grades
Complex Phase (CP) steels combine high strength with relatively high ductility. The microstructure of CP steels contains small amounts of martensite, retained austenite and pearlite within a ferrite/bainite matrix. A thermal cycle that retards recrystallization and promotes Titanium (Ti), Vanadium (V), or Niobium (Nb) carbo-nitrides precipitation results in extreme grain refinement. Minimizing retained austenite helps improve local formability, since forming steels with retained austenite induces the TRIP effect producing hard martensite.F-11
The balance of phases, and therefore the properties, results from the thermal cycle, which itself is a function of whether the product is hot rolled, cold rolled, or produced using a hot dip process. Citation P-18 indicates that galvannealed CP steels are characterized by low yield value and high ductility, whereas cold rolled CP steels are characterized by high yield value and good bendability. Typically these approaches require different melt chemistry, potentially resulting in different welding behavior.
CP steel microstructure is shown schematically in Figure 1, with the grain structure for hot rolled CP 800/1000 shown in Figure 2. The engineering stress-strain curves for mild steel, HSLA steel, and CP 1000/1200 steel are compared in Figure 3.

Figure 1: Schematic of a complex phase steel microstructure showing martensite and retained austenite in a ferrite-bainite matrix.

Figure 2: Micrograph of complex phase steel, HR800Y980T-CP.C-14

Figure 3: A comparison of stress strain curves for mild steel, HSLA 350/450, and CP 1000/1200.
DP and TRIP steels do not rely on precipitation hardening for strengthening, and as a result, the ferrite in these steels is relatively soft and ductile. In CP steels, carbo-nitride precipitation increases the ferrite strength. For this reason, CP steels show significantly higher yield strengths than DP steels at equal tensile strengths of 800 MPa and greater. Engineering and true stress-strain curves for CP steel grades are shown in Figure 4.
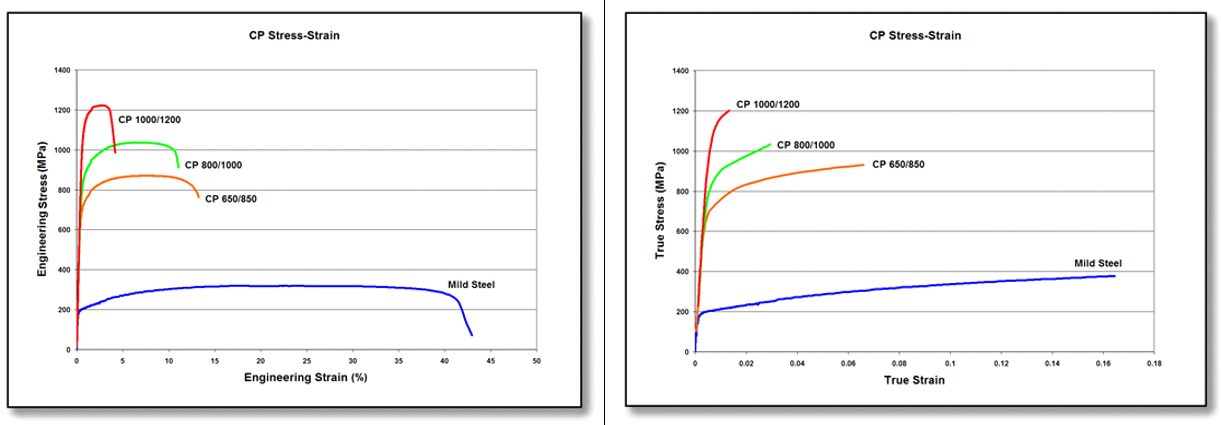
Figure 4: Engineering stress-strain (left graphic) and true stress-strain (right graphic) curves for a series of CP steel grades. Sheet thickness: CP650/850 = 1.5mm, CP 800/1000 = 0.8mm, CP 1000/1200 = 1.0mm, and Mild Steel = approx. 1.9mm.V-1
Examples of typical automotive applications benefitting from these high strength steels with good local formability include frame rails, frame rail and pillar reinforcements, transverse beams, fender and bumper beams, rocker panels, and tunnel stiffeners.
Some of the specifications describing uncoated cold rolled 1st Generation complex phase (CP) steel are included below, with the grades typically listed in order of increasing minimum tensile strength and ductility. Different specifications may exist which describe hot or cold rolled, uncoated or coated, or steels of different strengths. Many automakers have proprietary specifications which encompass their requirements.
- ASTM A1088, with the terms Complex phase (CP) steel Grades 600T/350Y, 780T/500Y, and 980T/700Y A-22
- EN 10338, with the terms HCT600C, HCT780C, and HCT980C D-18
- VDA239-100, with the terms CR570Y780T-CP, CR780Y980T-CP, and CR900Y1180T-CPV-3
1stGen AHSS, AHSS, Steel Grades
Ferrite-Bainite (FB) steels are hot rolled steels typically found in applications requiring improved edge stretch capability, balancing strength and formability. The microstructure of FB steels contains the phases ferrite and bainite. High elongation is associated with ferrite, and bainite is associated with good edge stretchability. A fine grain size with a minimized hardness differences between the phases further enhance hole expansion performance. These microstructural characteristics also leads to improved fatigue strength relative to the tensile strength.
FB steels have a fine microstructure of ferrite and bainite. Strengthening comes from by both grain refinement and second phase hardening with bainite. Relatively low hardness differences within a fine microstructure promotes good Stretch Flangable (SF) and high hole expansion (HHE) performance, both measures of local formability. Figure 1 shows a schematic Ferrite-Bainite steel microstructure, with a micrograph of FB 400Y540T shown in Figure 2.

Figure 1: Schematic Ferrite-Bainite steel microstructure.

Figure 2: Micrograph of Ferrite-Bainite steel, HR400Y540T-FB.H-21
The primary advantage of FB steels over HSLA and DP steels is the improved stretchability of sheared edges as measured by the hole expansion test. Compared to HSLA steels with the same level of strength, FB steels also have a higher strain hardening exponent (n-value) and increased total elongation. Figure 3 compares FB 450/600 with HSLA 350/450 steel. Engineering and true stress-strain curves for FB steel grades are shown in Figure 4.

Figure 3: A comparison of stress strain curves for mild steel, HSLA 350/450, and FB 450/600.
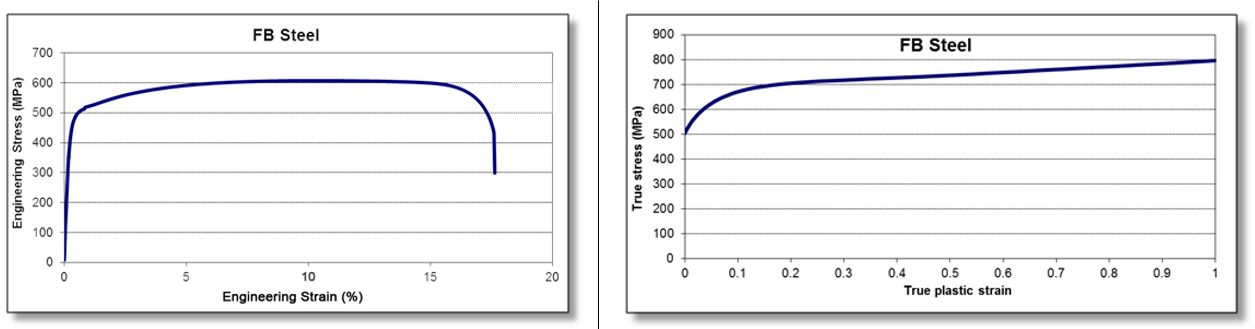
Figure 4: Engineering stress-strain (left graphic) and true stress-strain (right graphic) curve for FB 450/600.T-10
Examples of typical automotive applications benefitting from these high strength highly formable grades include automotive chassis and suspension parts such as upper and lower control arms, longitudinal beams, seat cross members, rear twist beams, engine sub-frames and wheels.
Some of the specifications describing uncoated hot rolled 1st Generation ferrite-bainite (FB) steel are included below, with the grades typically listed in order of increasing minimum tensile strength and ductility. Different specifications may exist which describe uncoated or coated versions of these grades. Many automakers have proprietary specifications which encompass their requirements.
- EN 10338, with the terms HDT450F and HDT580F D-18
- VDA239-100, with the terms HR300Y450T-FB, HR440Y580T-FB, and HR600Y780T-FB V-3
- JFS A2001, with the terms JSC440A and JSC590AJ-23