Blog, homepage-featured-top, main-blog, Testing and Characterization
Dynamic tensile testing of sheet steels is becoming more important due to the need for more optimized vehicle crashworthiness analysis in the automotive industry. Positive strain rate sensitivity (strength increases with strain rate) as an example, offers a potential for improved energy absorption during a crash event. New systems have been developed in recent years to meet the increasing demand for dynamic testing.
Three important points collectively highlight the need for high-speed testing:
- Tensile properties and fracture behavior change with strain rate.
- Conventional tensile tests using standard dogbone shapes take on the order of 1 to 2 minutes depending on the grade.
- An entire automotive crash takes on the order of 100 milliseconds, with deformation rates 10,000 to 100,000 faster than conventional testing speeds.
Characterizing the response during high-speed testing provides critical information used in crash simulations, but these tests often require upgraded equipment and procedures. Conventional tensile testing equipment may lack the ability to reach the required speeds (on the order of 20 m/s). Sensors for load and displacement must acquire accurate data during tests which take just a few milliseconds.
Higher speed tensile and fracture characterization also aids in predicting the properties of stamped parts, as deformation rates in stamping are 100 to 1,000 times higher than most testing rates.
Steel alloys possess positive strain rate sensitivity, or m-value, meaning that strength increases with strain rate. This has benefits related to improved crash energy absorption.
Characterizing this response requires use of robust testing equipment and practices appropriate for the targeted strain rate. Some techniques involve a tensile or compressive Split Hopkinson (Kolsky) Bar, a drop tower or impact system, or a high-speed servo-hydraulic system. Historically, no guidelines were available as to the testing method, specimen dimensions, measurement devices, and other important issues which are critical to the quality of testing results. As a result, data from different laboratories were often not comparable. A WorldAutoSteel committee evaluated various procedures, conducted several round-robins, and developed a recommended procedure, which evolved into what are now both parts of ISO 26203, linked below.
Published standards addressing tensile testing at high strain rates include:
The specific response as a function of strain rate is grade dependent. Some grades get stronger and more ductile as the strain rate increases (left image in Figure 1), while other grades see primarily a strength increase (right image in Figure 1). Increases are not linear or consistent with strain rate, so simply scaling the response from conventional quasi-static testing does not work well. Strain hardening (n-value) also changes with speed in some grades, as suggested by the different slopes in the right image of Figure 1. Accurate crash models must also consider how strain rate sensitivity impacts bake hardenability and the magnitude of the TRIP effect, both of which are further complicated by the strain levels in the part from stamping.

Figure 1: Two steels with different strength/ductility response to increasing strain rate.A-7
Testing and Characterization
Tensile testing cannot be used to determine bendability, since these are different failure modes. Failure in bending is like other modes limited by local formability in that only the outermost surface must exceed the failure criteria.
ASTM E290A-26, ISO 7438I-8, and JIS Z2248J-5 are some of the general standards which describe the requirements for the bend testing of metals. In a Three-Point Bend Test, a supported sample is loaded at the center point and bent to a predetermined angle or until the test sample fractures. Failure is determined by the size and frequency of cracks and imperfections on the outer surface allowed by the material specification or the end user.
Variables in this test include the distance between the supports, the bending radius of the indenter (sometimes called a pusher or former), the loading angle which stops the test, whether the loading angle is determined while under load or after springback, and the crack size and frequency resulting in failure.
For automotive applications, the VDA238-100V-4 test specification is increasingly used. Here, sample dimension, punch tip radius, roller spacing, and roller radius are all constrained to limit variability in results. Figure 1 shows a schematic of the test.

Figure 1: Schematic of Bend Testing to VDA238-100, with Bending Angle Definition.
This video, courtesy of Universal Grip Company,U-5 describes the support rollers in the VDA238-100 test.
Calculation of the bending angle is not always straightforward. Bending formulas such as that shown within VDA238-100 assume perfect contact between the sheet metal and the punch radius. However, experimental evidence exists showing this contact does not always occur, especially in AHSS grades.
Figure 2 presents one example testing DP600 where the punch radius is larger than the radius on the bent sheet, leading to a physical separation between the punch and sheet.L-12
This physical separation also has implications for standardized bendability characterizations. A common measure of bendability is the punch radius to sheet thickness ratio, rPUNCH/t. In higher strength grades where this punch-sheet-liftoff is likely to occur, this may lead to an overestimation of how safe a design is when the punch radius may be measurably larger (less severe) than the tighter, more extreme radius actually experienced on the sheet.

Figure 2: DP600 After Testing to VDA238-100. Note punch radius is larger than radius in bent sheet resulting in separation.L-12
Furthermore, bending tests do not always result in a round bent sheet shape and constant thickness around the punch tip, especially when testing 980MPa tensile strength steel grades and higher which have low strain hardening capability. Figure 3 shows pronounced flattening and thinning of the sheet below the punch tip after bending, occurring primarily on the side opposite the punch stretched in tension. Efforts to replicate this phenomenon in simulation have failed, since the underlying mechanism is not yet fully understood.

Figure 3: Flattening and Thinning Behavior after Bending.L-12
Results from bend testing are typically reported as the smallest R/T (the ratio between the die radius and the sheet thickness) that results in a crack-free bend. Many steel companies report minimum bend test limits for various grades and certain automakers include minimum bend test requirements in their specifications as well. Different steel companies and automakers may have different bend test methods and/or requirements, so it is important to understand those requirements and procedures to better match the material characteristics with the customer’s design and process expectations. The test methods could involve a bend of 60°, 90°, 180° as well as various radii, die materials, speeds, etc.
Figure 4 shows etched cross sections of different grades bend to either 0T (fold flat) or 0.5T radii for reference purposes.

Figure 4: Etched cross sections of various grades. Top row, left: 0T bend of DP350/600; Top row, right: 0T bend of HSLA450/550; Bottom left: 0.5T bend of TRIP 350/600; Bottom center: 0T bend of TRIP 350/600; Bottom right: 0.5T bend of DP 450/800.K-1
Testing and Characterization
topofpage
The ISO 16630 Hole Expansion Test and the VDA238-100 bend test are among the few standardized tests to characterize local formability, the term which describes when part and process design, in addition to sheet metal properties like strength and elongation, influence the amount of deformation the metal can undergo prior to failure.
Researchers have developed alternate tests to further investigate process parameters and more clearly understand and optimize non-steel related variables. Also important is the investigation of different strain states from the ones seen in the hole expansion and bending tests. Comparisons of the stretched or bent edge performance evaluating different process parameters using the same material help to better define optimum process parameters. Repeating the testing with different AHSS grades confirms if similar trends exist across different microstructures and strengths. Standardization of these alternate tests has not yet occurred, so use caution when comparing specific values from different studies.
Hole Tension Test
Microstructural damage in the shear affected zone reduces edge ductility. Damage has been evaluated with a modified tensile dogbone containing a central hole prepared by shearing or reaming, as shown in Figure 1. In contrast with a hole expansion test using a conical punch, the researchers described this as a Hole Tension test, which determines failure strain as a function of grade and edge preparation.

Figure 1: Hole Tension Test Specimen GeometryP-12
Edge Tension Test
A two-dimensional (2-D) edge tension test, also called Half-A-Dogbone test, also evaluates edge stretchability. There are multiple versions of this type of test, but they all are based on the same concept. Like a standard tensile test, the 2-D edge tension test pulls a steel specimen in tension until failure. Unlike a standard tensile test where both sides of the tensile specimen are milled into a “dog bone”, the 2D tension test uses half of a dogbone with different preparation methods for the straight edge and the edge containing the reduced section (Figure 2). The chosen preparation method for each face is a function of the parameter being investigated (ductility, strain, burr, and shear affected zone for example). Potential edge preparation methods include laser cutting, EDM, water jet cutting, milling, slitting or mechanical cutting at various trim clearances, shear angles, rake angles or with different die materials.

Figure 2: 2-D Edge Tension Test Sample. Note the edges are prepared differently based on the targeted property evaluated.
Side Bending Test
Instead of a dogbone or half-dogbone, some studies use a rectangular strip without a reduced section. Bending performance can be evaluated with a rectangular strip having one finished edge and one trimmed edge while preventing out-of-plane buckling, as shown in Figure 3.G-7
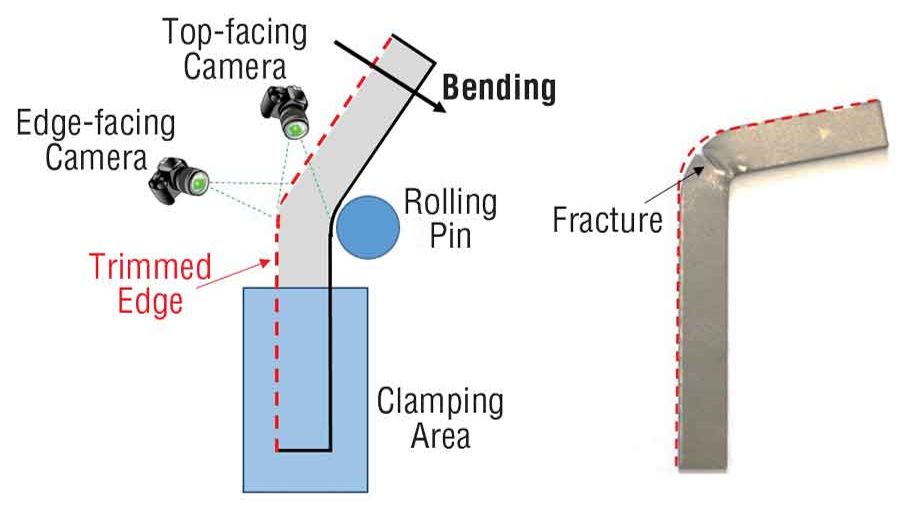
Figure 3: The side-bending test expands a trimmed edge over a rolling pin until detection of the first edge crack.G-7
Half-Specimen Dome Test
Deformation in these three tests occur in the plane of the sheet. Typical hole expansion tests, like production stampings, deform the sheet metal perpendicular to the plane of the sheet. However, hole expansion testing does not always give consistent test results. The half-specimen dome test (HSDT) also attempts to replicate this 3-dimensional forming mode (Figure 4), and appears to be more repeatable likely due to creating a straight cut rather than round hole.
In the HSDT, a rectangular blank is prepared with one edge having the preparation method of interest, like sheared with a certain clearance or laser cut or water-jet cut. The sample is then clamped with the edge to be evaluated over a hemispherical punch. The punch then strains the clamped sample creating a dome shape, with the test stopping with the first crack appears at the edge. Edge stretchability is quantified by measuring dome height or edge thinning or other characteristics.
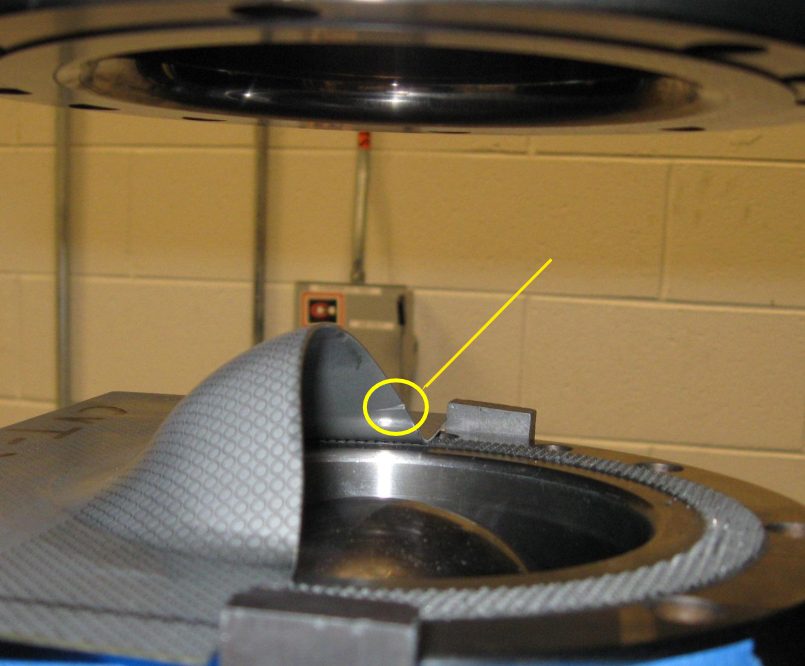
Figure 4: Half-Specimen Dome Test sample. Arrow points to edge crack.S-12
Edge Flange Test
Flanging limits depend on the part contour, edge quality, and material properties. Non-optimal flange lengths – either too long or too short – will lead to fracture. Different tools can assess the influence of flange length, including the one shown in Figure 5 from Citation U-3.

Figure 5: Tool design to investigate flange length before fracture. Flange height: 40mm in left image, 20mm in right image.U-3
Physical tests using this tool show that optimizing sample orientation relative to the rolling direction leads to longer flange lengths before splitting.U-3 Figure 6 highlights the results from testing DP800.

Figure 6: Flange height limits as a function of orientation in DP800.U-3
Back to the Top
Testing and Characterization
The Hole Expansion test (HET) quantifies the edge stretching capability of a sheet metal grade having a specific edge condition. Many variables affect hole expansion performance. By understanding the microstructural basis for this performance, steelmakers have been able to create new grades with better edge stretch capability.
Multiphase microstructures with large hardness differences between the phases, specifically islands of the very hard martensite surrounded by a softer ferrite matrix, may crack along the ferrite-martensite interface (Figure 1). The larger the size of the initiated damage site (due to edge shearing), the smaller the critical stress required for crack propagation.M-6 The microstructure and damage are key components of the Shear Affected Zone, or SAZ.

Figure 1: Features and mechanisms of damage initiation and propagation in Dual Phase steel.M-6
One metallurgical approach to improve sheared edge stretchability is targeting a homogeneous microstructure. Steel suppliers have engineered product offerings like complex phase steel, where extensive grain refinement (reducing the size of the ferrite and martensite grains) is achieved. Consequently, the size of the initial damage resulting from shearing is reduced, raising the critical stress for crack propagation to higher levels and reducing the likelihood for crack propagation. Additionally, reducing the difference in hardness between the soft ferrite phase and the hard martensite phase improves the hole expansion ratio. Changes in chemistry, hot rolling conditions and intercritical annealing temperatures are some of the methods used to achieve this. Such metallurgical trends can include a single phase of bainite or multiple phases including bainite and removal of large particles of martensite. This trend is shown in Figure 2, adapted from Citation M-11.
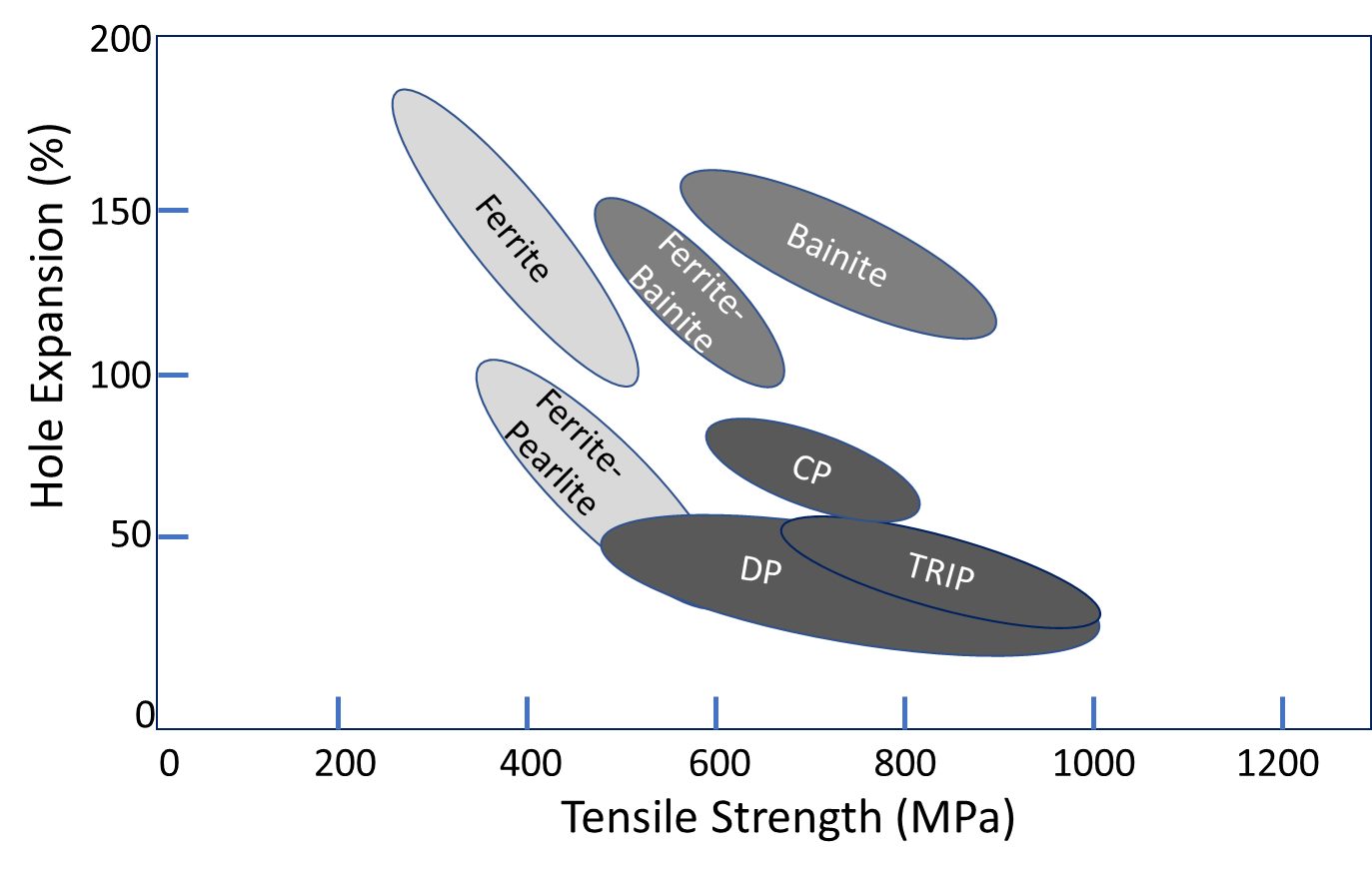
Figure 2: Hole Expansion as a Function of Strength and Microstructure. Adapted from Citation M-11.
An example of the impact of these modifications is shown in a paper published by C. Chiriac and D. HoydickC-10, where a 1 mm DP780 galvannealed steel was modified to produce a grade with improved hole expansion to achieve greater resistance to local formability failures such as edge fracture and shear fracture. These changes were made while retaining the same base metal chemistry and the same fraction of martensite in the structure, and resulted in similar tensile strength and total elongation but with a 50% increase in hole expansion (Table I and Figure 3). The key difference is a lower martensite hardness, and a smaller difference between the hardness of the martensite and ferrite. The modified DP grade has more homogeneous distribution of martensite with smaller ferrite and martensite grains (Figure 4).

Table I: Comparison of a conventional DP780 steel with a similar chemistry modified to improve hole expansion.C-10
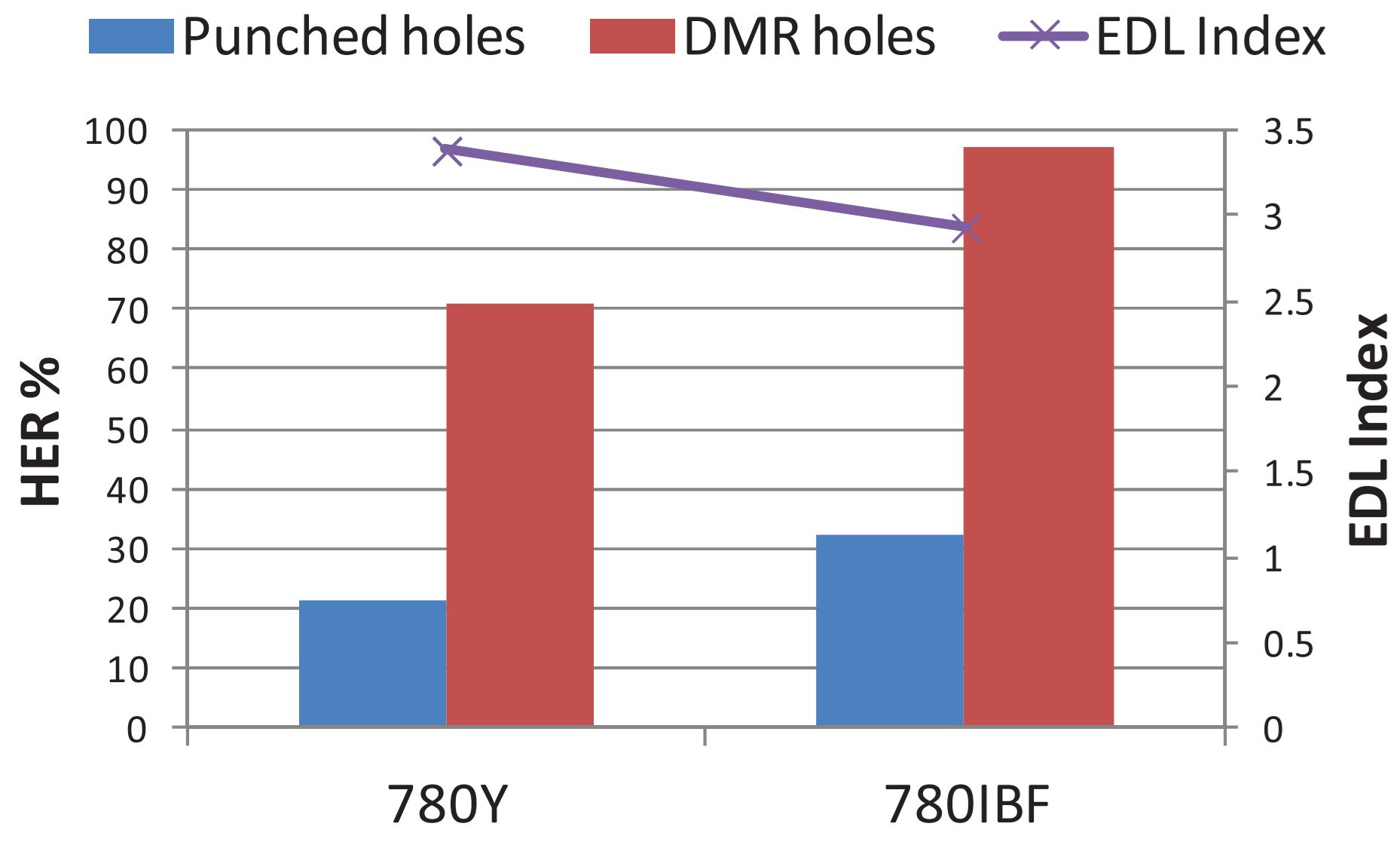
Figure 3: Improvement in Hole Expansion improves with grade modifications and edge quality. DMR = drilled, milled, and reamed hole; EDL = Edge Ductility Loss index, the ratio of the hole expansion of the DMR hole to that of the punched hole.C-10
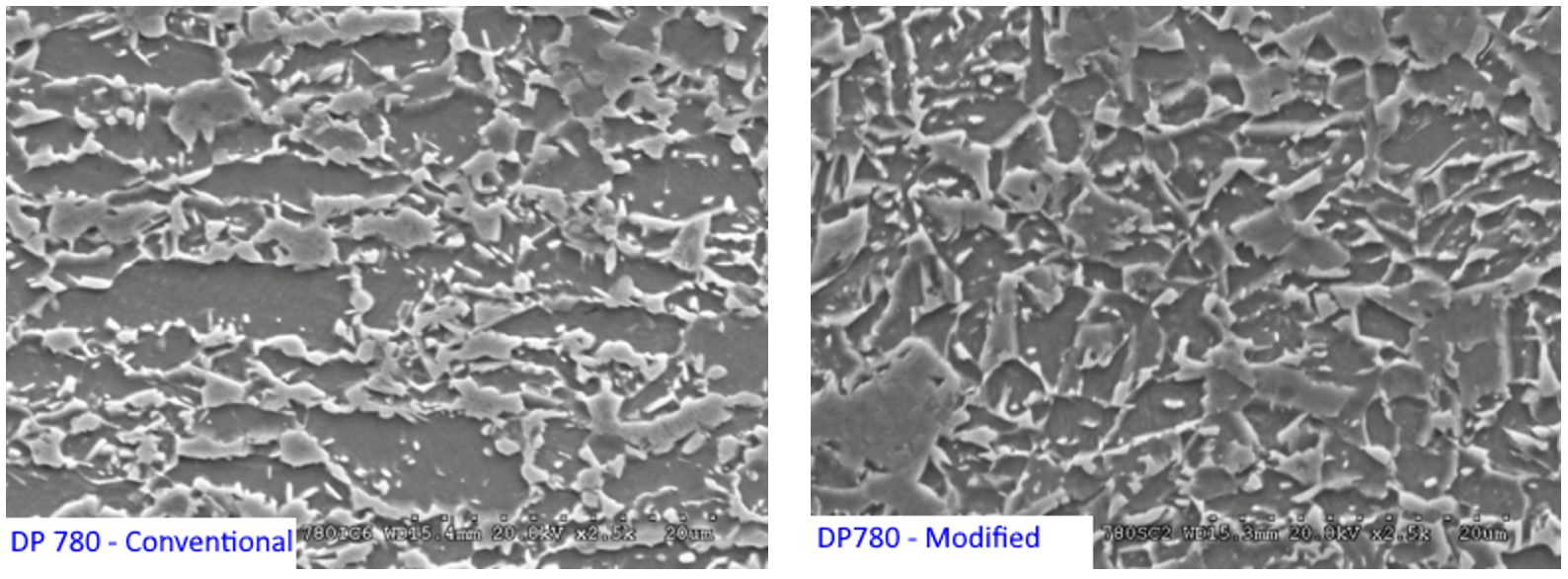
Figure 4: Comparison of the microstructure of a conventional DP780 steel (left) with a similar chemistry modified to improve hole expansion (right). Overall, there is the same fraction of martensite in both grades, but the modified chemistry has finer features.C-10
A presentation at a 2020 conferenceK-16 described a study which compared DP780 from six different global suppliers. Hole expansion tests were done on 1.4 mm to 1.5 mm mm thick samples prepared with either a sheared edge at 13% clearance, a sheared edge with 20% clearance, or a machined edge. Not surprisingly, the machined edge with minimal work hardening outperformed either of the sheared edge conditions. However, when considering only the machined edge samples, the hole expansion ratio ranged from below 30% to more than 70% (Figure 5). Presumably the only difference was the microstructural characteristics of the six DP780 products.

Figure 5: Variation in hole expansion performance from DP780 from 6 global suppliers.K-56
The microstructural differences that enhance local formability characteristics may be detrimental to global formability characteristics and vice versa. Conventional dual phase steels, with a soft ferrite matrix surrounding hard martensite islands, excel in applications where global formability is the limiting scenario. These steels have a low YS/TS ratio and high total elongation. However, the interface between the ferrite and martensite is the site of failures that limit the sheared edge extension of these grades. On the other end of the spectrum, fully martensitic grades are the highest strength steels available. These have a high YS/TS ratio, and low total elongation. Having only a single phase helps these grades achieve surprisingly high hole expansion values considering the strength, as seen in Figure 6.
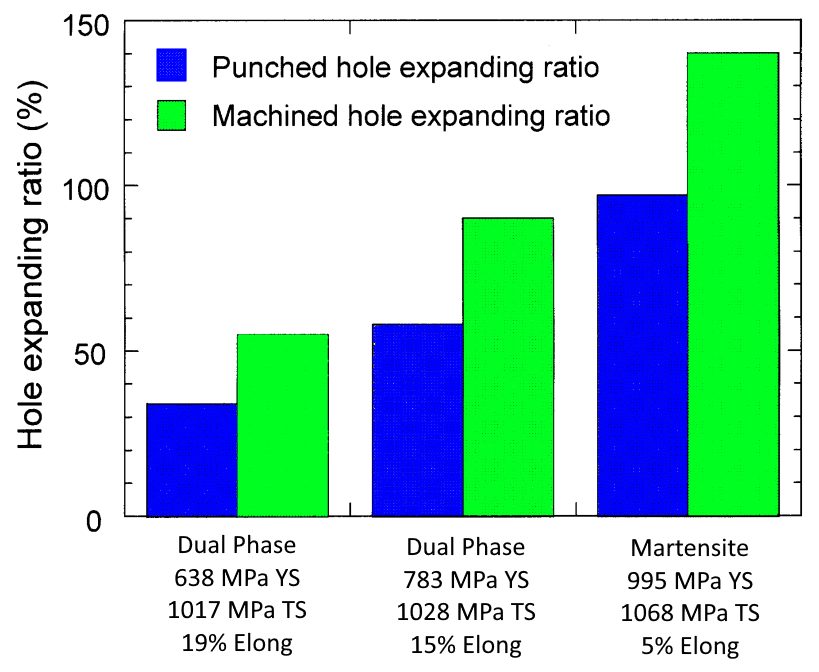
Figure 6: Hole Expansion as a Function of Edge Quality and Microstructure. Adapted from Citation.H-7
Knowing that a higher volume fraction of martensite is needed to increase strength, combined with the awareness that minimizing the hardness differences between microstructural phases is needed to increase hole expansion (Figure 7), allows steelmakers to fine-tune their chemistry and mill processing to target specific balances of strength, tensile elongation, and cut edge expandability as measured in a tensile test.
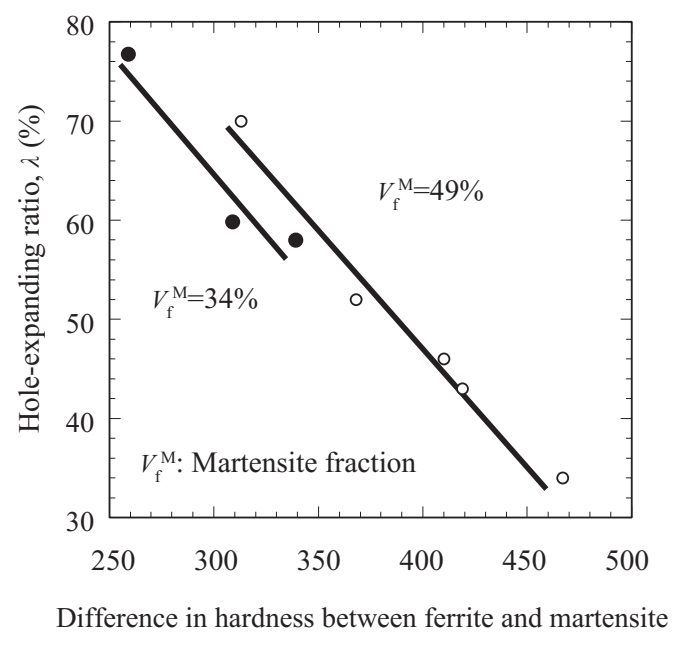
Figure 7: Improved Hole Expansion by Reducing the Hardness Difference between Ferrite and Martensite.H-8
This expands the selection of grades from which manufacturers can choose. Traditional material selection and identification may have been based on tensile strength to satisfy structural requirements – DP980 is a dual phase steel with 980MPa minimum tensile strength. However, newly engineered grade options offer users an extra level of refinement depending on the functional needs of the part. Products can be specified as needing high tensile elongation, high hole expansion, or a balance of these two. In the example shown in Figure 8, note that all 3 grades have nearly identical tensile strength.
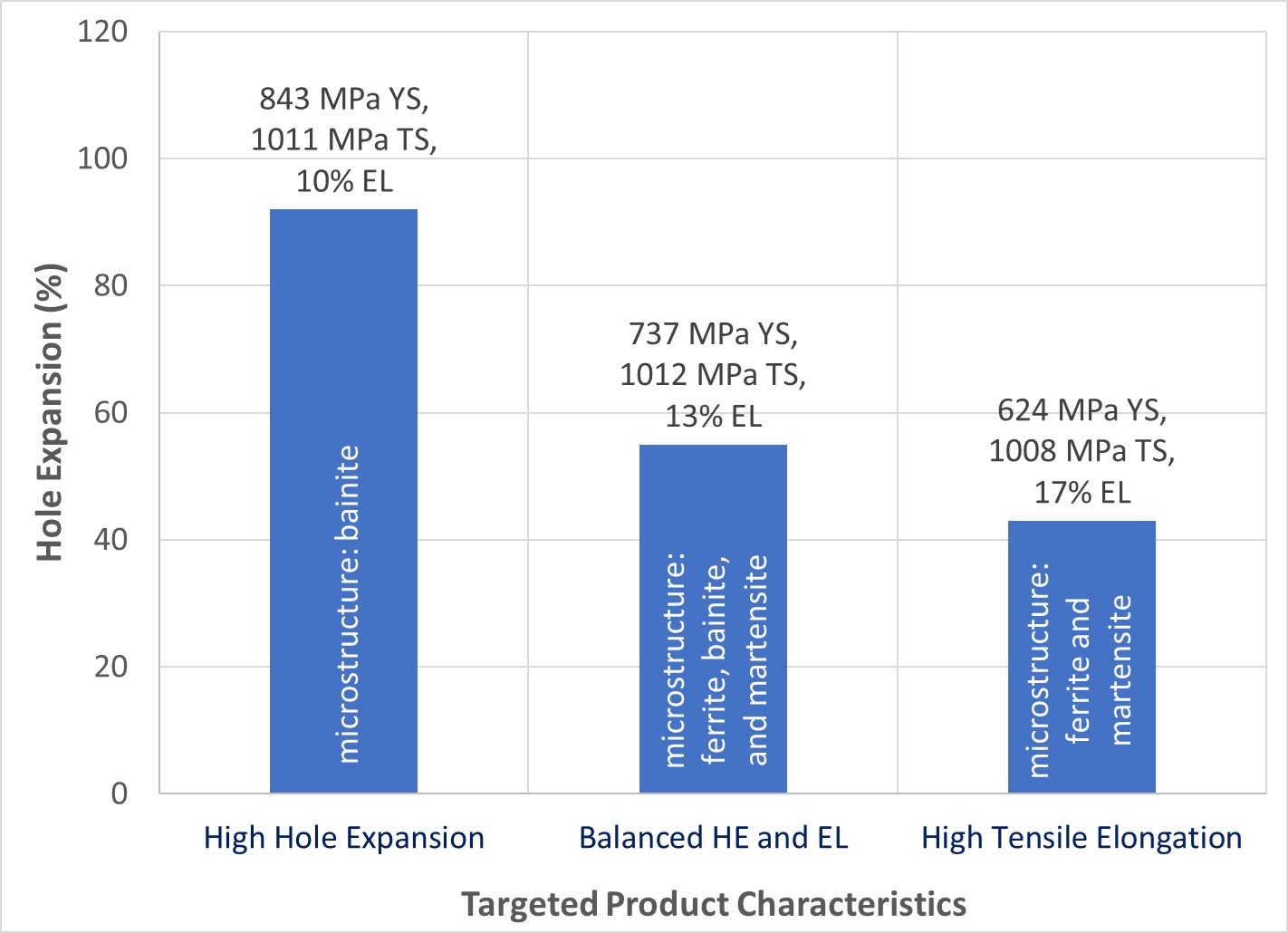
Figure 8: Engineered Microstructures Achieve Targeted Product Characteristics. (Data from Citations N-8 and F-5)
The influence of microstructure and the hardness differences between the phases is also seen in the hole expansion values of AHSS grades at strengths below 980 MPa. A study from 2016 shows the impact of a small amount of martensite on a ferrite-bainite microstructure.N-9 Both products compared had a microstructure of 80% ferrite. In one product, the remaining phase was only bainite, while the other had both martensite and bainite. The presence of just 8% martensite was sufficient to decrease the hole expansion capacity by 40%. (Figure 9).
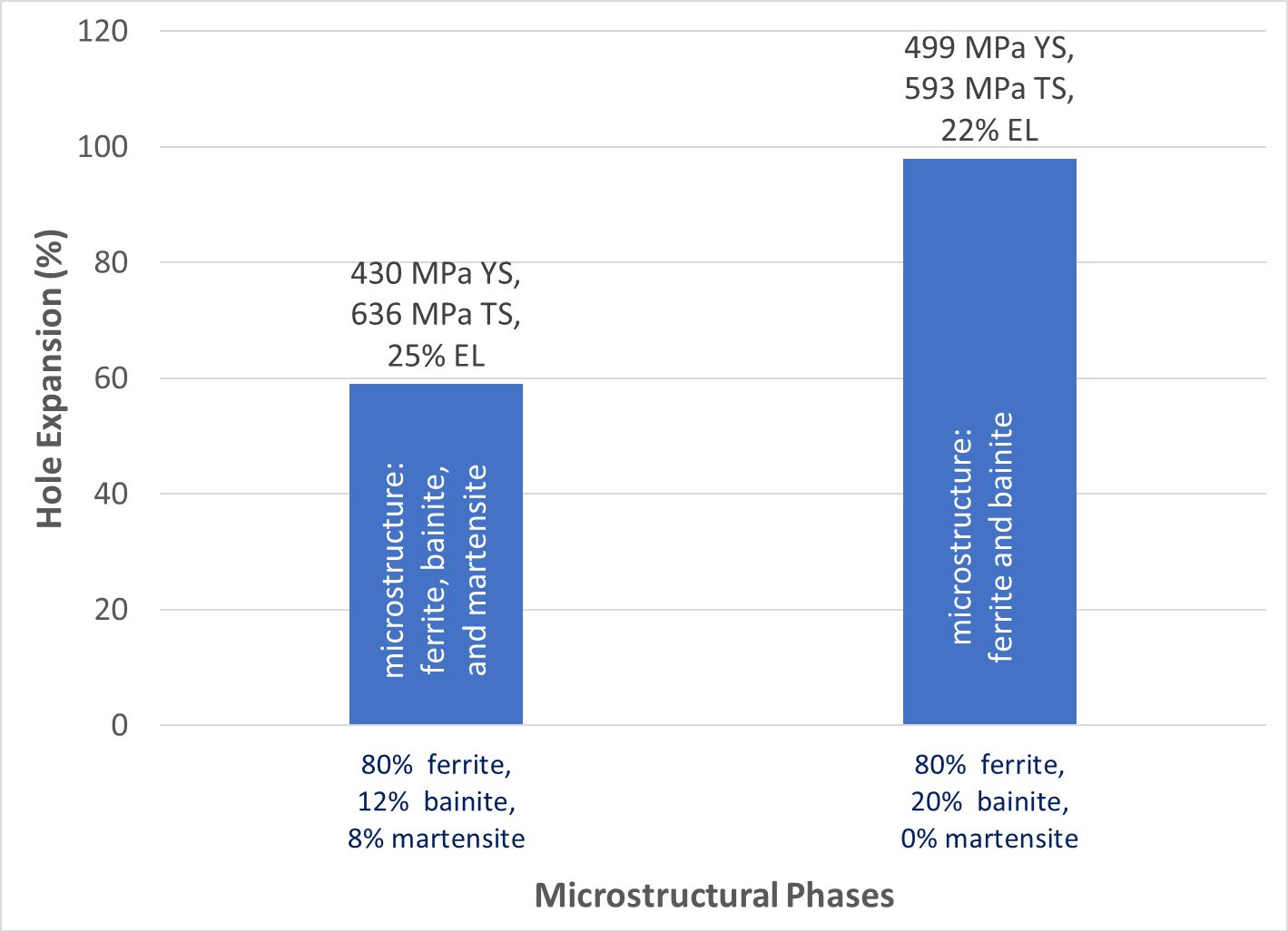
Figure 9: High Hardness Differences in Microstructural Phases Decrease Edge Ductility at All Strength Levels. Adapted from Citation N-9.
Rolling direction may also influence edge fracture sensitivity on some multiphase AHSS grades. When testing a sample, edge fractures may occur first at the hole edge along the rolling direction, which corresponds to a tensile axis in the transverse direction. If the chosen grade exhibits this behavior, locate stretch flanges perpendicular to the rolling direction when possible during die and process development to increase resistance to edge fracture. If this is not practical, identify locations where inserting scallops/notches in the stretch flange will not negatively impact the part structure, fit or die processing.
During die development and die try-out, it is important to use the production-intent AHSS grade – not just one that has the same tensile strength. Blank orientation relative to the rolling direction in these trials must also be production-intent. Often the blank die is the last completed die, so prototype blanks may be prepared by laser, EDM, water jet or even by hand during tryout. These cutting methods will have different sheared edge extension, as measured by the hole expansion test, compared with the production-intent shearing. These differences may be sufficiently significant to prevent replication of production conditions in tryout.
Testing and Characterization
The term local formability describes when part and process design, in addition to sheet metal properties like strength and elongation, influence the amount of deformation the metal can undergo prior to failure. Cutting, punching or other methods of obtaining a trimmed blank or an internal hole results in cracks, rough edges, work-hardening and other edge damage – all of which influences edge quality. The challenges of capturing all of the factors that influence edge quality makes the prediction of fracture severity and cut edge expansion very difficult and usually impossible. The many variables highlight the need for a standardized test method. However, restricted sample preparation and testing variables in these standards do not reflect the variety of conditions encountered in production environments. Use caution when comparing results generated under different conditions.
Hole Expansion Testing
The Hole Expansion test (HET) quantifies the edge stretching capability of a sheet metal grade having a specific edge condition. Higher values of the hole expansion ratio are associated with grades and forming methods more likely to have improved local formability characteristics.
Steel producers study hole expansion capacity to create new products with targeted edge stretching performance through modifications of chemistry, rolling and thermal practices. Product designers use the hole expansion test to determine if the chosen steel grade has the inherent forming characteristics to meet their targeted shape with their chosen forming system. If they are not compatible, the chosen grade must change or aspects of the forming process must change, or possibly both.
ISO 16630 is the primary standard used which describes the test method and constraints.I-9 Others, like JIS Z 2256J-6 are based on the ISO standard, with only minor differences, if any. This standard specifies use of a 10mm diameter hole created with a 12% clearance. The sample containing the hole is clamped in place, and a conical punch having a 60 degree apex angle expands that initial hole (Figure 1). The test stops after observation of a through-thickness crack or upon experiencing a load-drop exceeding a critical threshold (Figure 2). The hole expansion ratio (HER), also known as the Hole Expansion Capacity (HEC), is simply the percent expansion of the diameter of the initial hole, typically shown as the Greek letter lambda, λ.
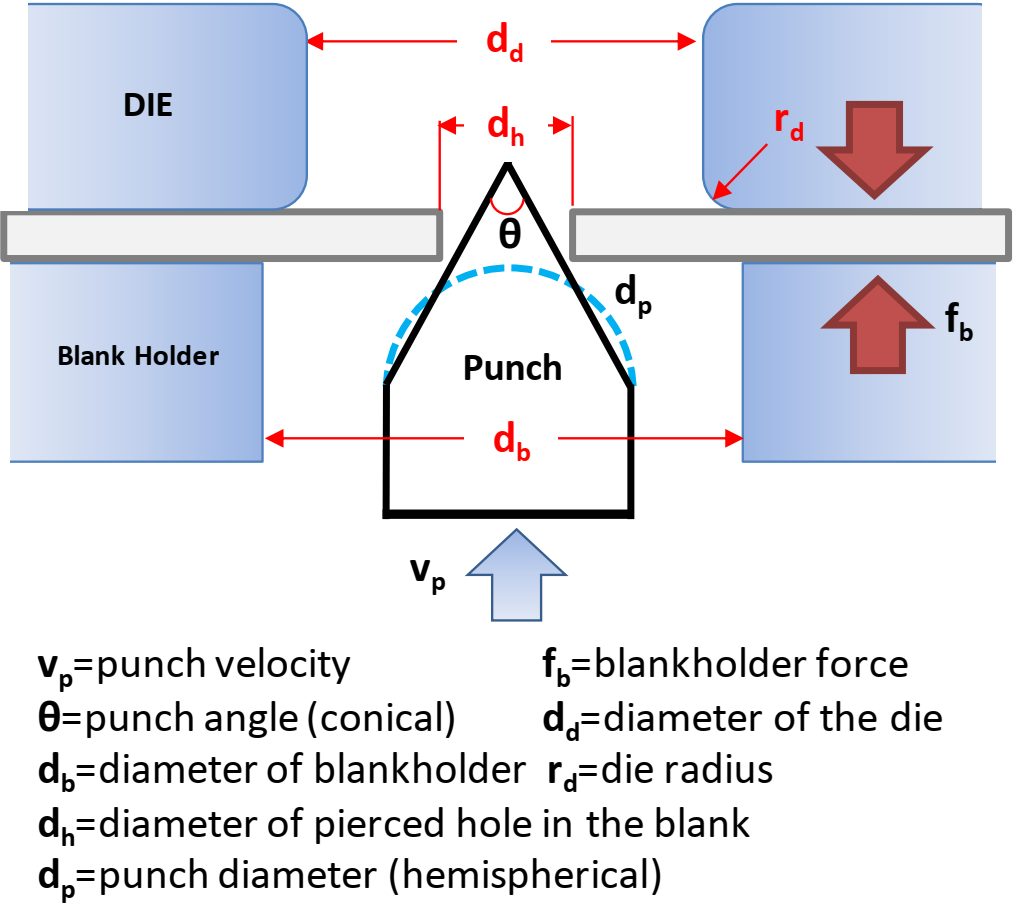
Figure 1: Schematic of Hole Expansion Test.A-10
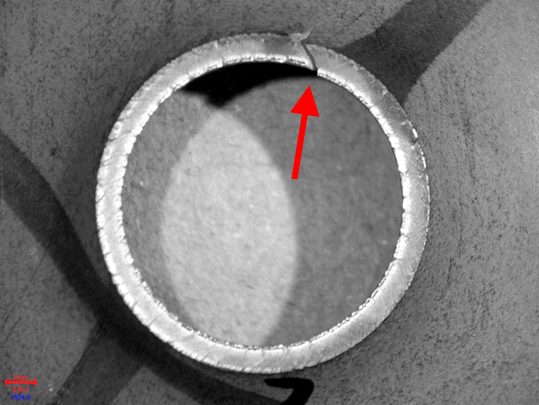
Figure 2: Expanded Edge at the end of a Hole Expansion Test performed using a conical punch. The arrow points to the through-thickness crack that ended the test.E-2
The sample preparation and testing requirements of ISO 16630 are well-defined for good reason. Factors known to influence the hole expansion ratio include:
Even with these rigorously defined procedures, the test results can be heavily influenced by specimen preparation technique, specific test parameters, and human subjectivity – in other words, poor gage R&R (repeatability and reproducibility). For example a group of European steel researchers reported “an unacceptably large difference between labs” with regard to hole expansion testing. They ultimately concluded that the “difference is too large for the method to be useful in practice”.
A-76
Testing sheet steels of different thicknesses in a laboratory setting requires having multiple punches and/or dies of different diameter to maintain a consistent clearance, which is based on a percentage of the sheet thickness tested.
In production, the punch-to-die clearance can change during the life of the part, both from tooling wear as well as press misalignment. There is the additional risk that clearance can vary around the perimeter of the cut section, leading to inconsistent performance. Increasing sheet metal strength magnifies this issue.
The method used to create the free edge influences the edge quality. Improved edge quality and reduced mechanical work hardening of the edge is achieved by laser cutting, EDM cutting, water jet cutting, or fine blanking processes, and will typically improve the hole expansion ratio. Trim steel clearances, shear angles, tool steel types, and sharpness also impact hole expansion test results.
In the example shown in Figure 3, the hole expansion ratio is reduced from 280% for a milled or water jet edge down to 80% for a traditional cut edge. If clearances further increase – which could happen without proper tooling maintenance over the life of the part – the ability to expand a cut edge further decreases.
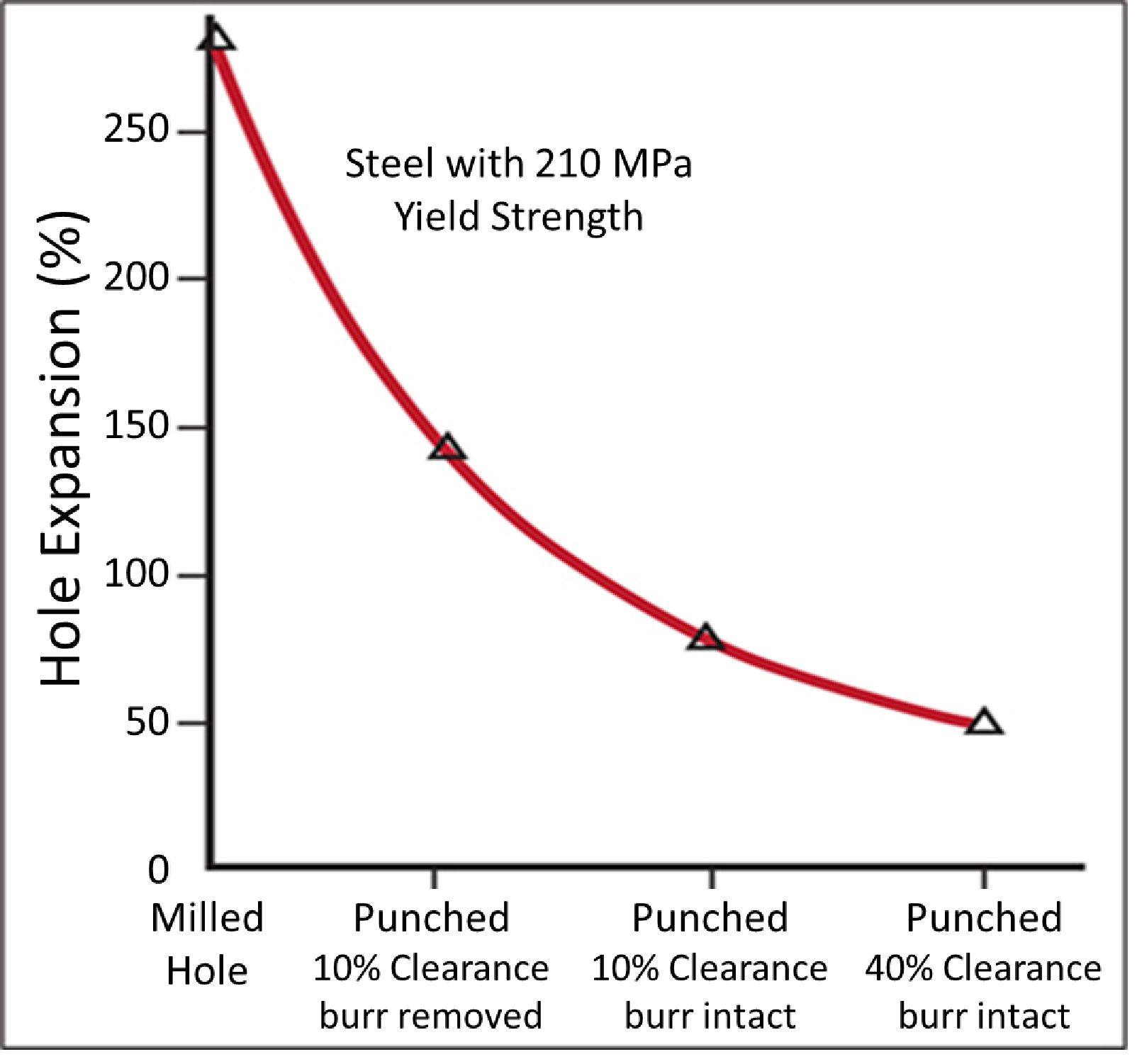
Figure 3: Hole Expansion Capacity Decreased as Edge Quality Decreases. (Based on data from Citation H-1.)
Figure 4 highlights the effect of punched vs machined holes, showing the edge damage from punching lowers the hole expansion capability. This edge damage becomes a key component of what is known as the Shear Affected Zone, or SAZ. DP steels and TRIP steels have a large hardness difference between the constituent phases, and therefore are associated with lower hole expansion ratios than HSLA and CP steels, where the phases are of more similar hardness. The influence of the metallurgical phase hardness difference is explored here. Detailed studies of sheared edge stretchability as a function of clearance, edge preparation, and grade are shown in Citations K-6 and K-10.
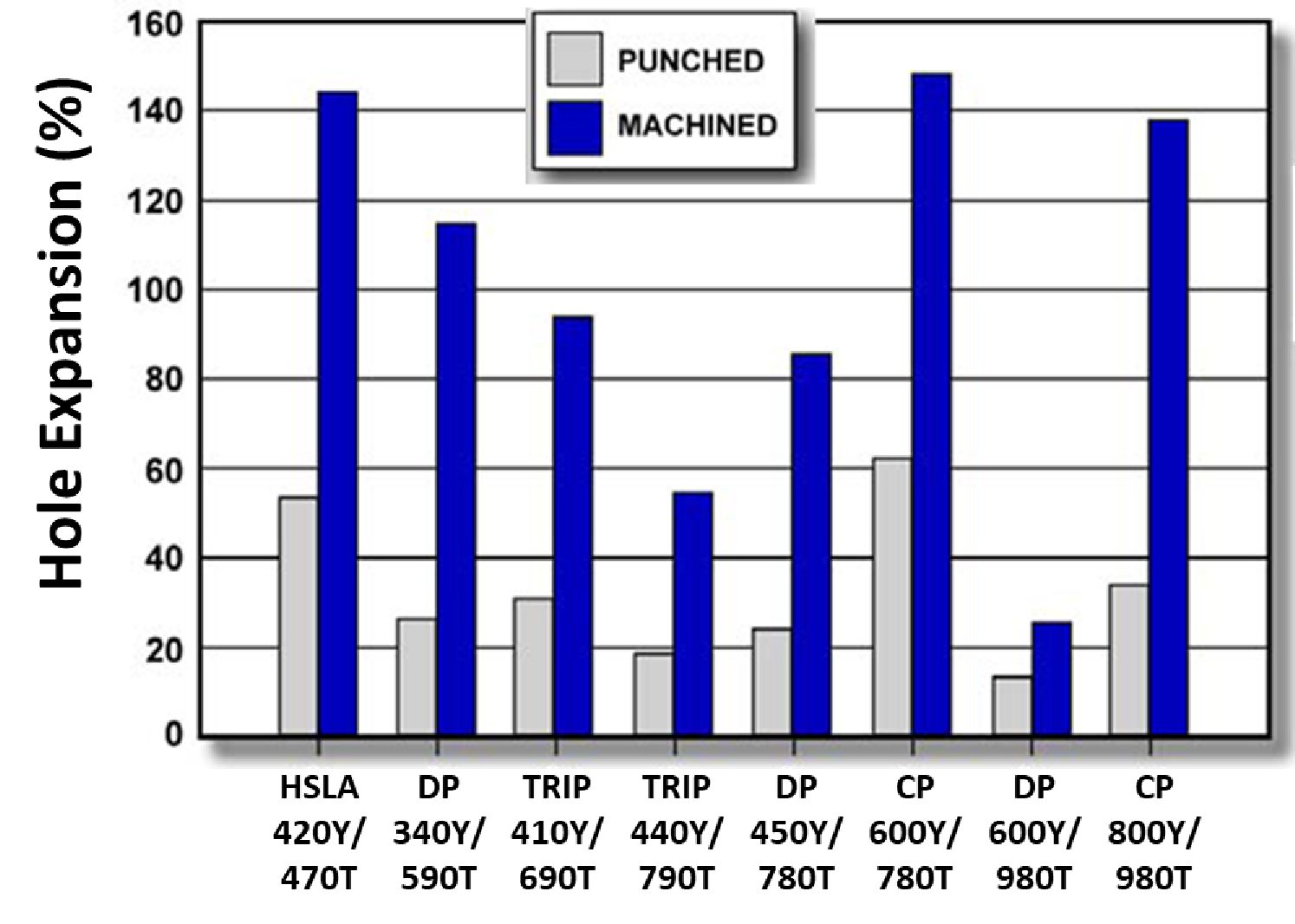
Figure 4: Hole expansion test results comparing punched and machined holes showing effect of damage to edge stretchability. (Based on data from Citation V-1.)
Over time, the targeted edge quality degrades and targeted clearance changes without proper attention. A study documented in Citation C-1 evaluated the hole expansion ratio created by hole punching tools as they wore in a production environment. Tools evaluated were made from 60 HRC uncoated Powder Metallurgy tool steels. Data in Figure 5 show the percent hole expansion from newly ground punches and dies (Sharp Tools) and from used production punches and dies (Worn Tools). The radial clearance was 0.1 mm. A rust preventative oil was applied to the steels during the punching; a lubricant oil was applied during hole expansion. Tool wear and possible micro-chipping resulted in a poor edge condition. The clearance was not significantly affected, but the steel edges suffered cold work which dramatically affected their hole expansion results.
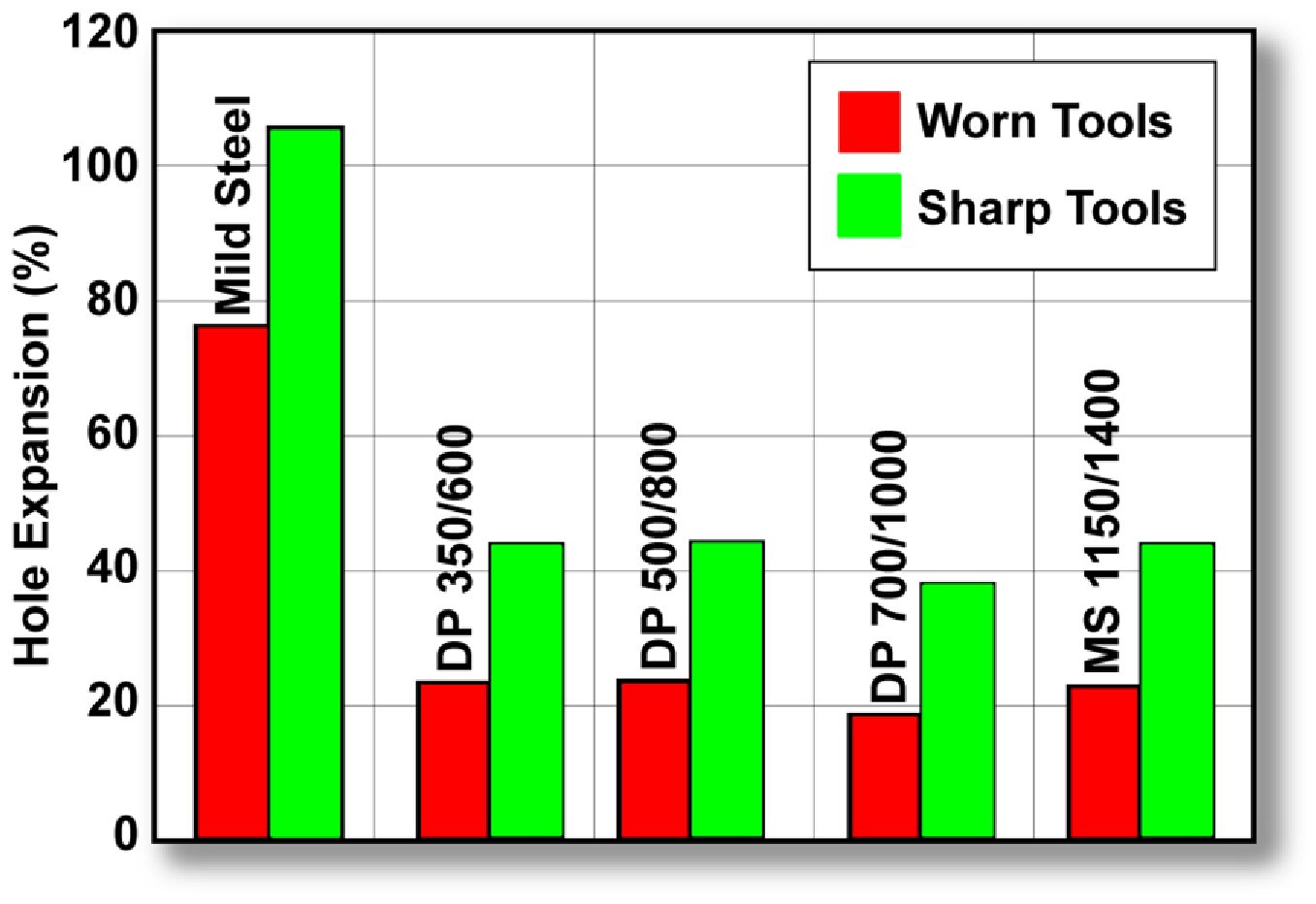
Figure 5: Impact of production tooling condition on hole expansion performance. (tests conducted w 50 mm diameter conical punch).C-1
Conclusions from Citation C-1 include:
- The best quality edge condition will produce the best results
- Tooling must remain sharp and damage-free to maintain the consistency in edge conditions.
- The burr should be in contact with the punch rather than on the freely-expanding side
- Hard and wear resistant tools, such as those produced from coated powder metallurgy (PM) tool steels, are highly recommended.
Additional information on tool materials can be found here and other articles in that category.
The ISO 16630 specificationI-9 eliminates one variable by prescribing the use of a 10 mm diameter hole, but it is important to understand that starting hole diameter influences the degree to which that hole can be expanded. A study that included mild steels to AHSS grades evaluated the effect of starting hole diameter.I-10 All steels were 1.2mm, punched with a clearance of 12.5%, and expanded with a conical punch having a 60° apex angle. As the starting diameter increases, the degree to which the hole can be expanded decreases, Figure 6. Note that as the strength increases, this effect appears to be minimized.
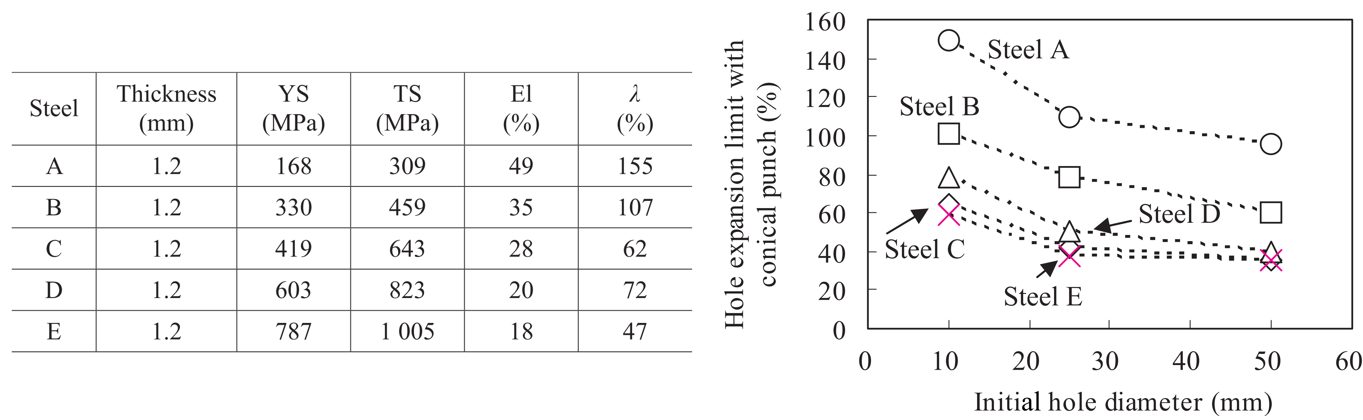
Figure 6: Hole Expansion Ratio Decreases as Initial Hole Diameter Increases.I-10
Increasing the starting hole diameter may help to distinguish between different grades.K-11 Similar hole expansion performance exists between DP980 and TRIP780 under ISO 16630 test conditions (punched 10 mm hole). It is easier to discern better performance in the TRIP780 product when performing a similar test with a 75 mm diameter punched hole (Figure 7).
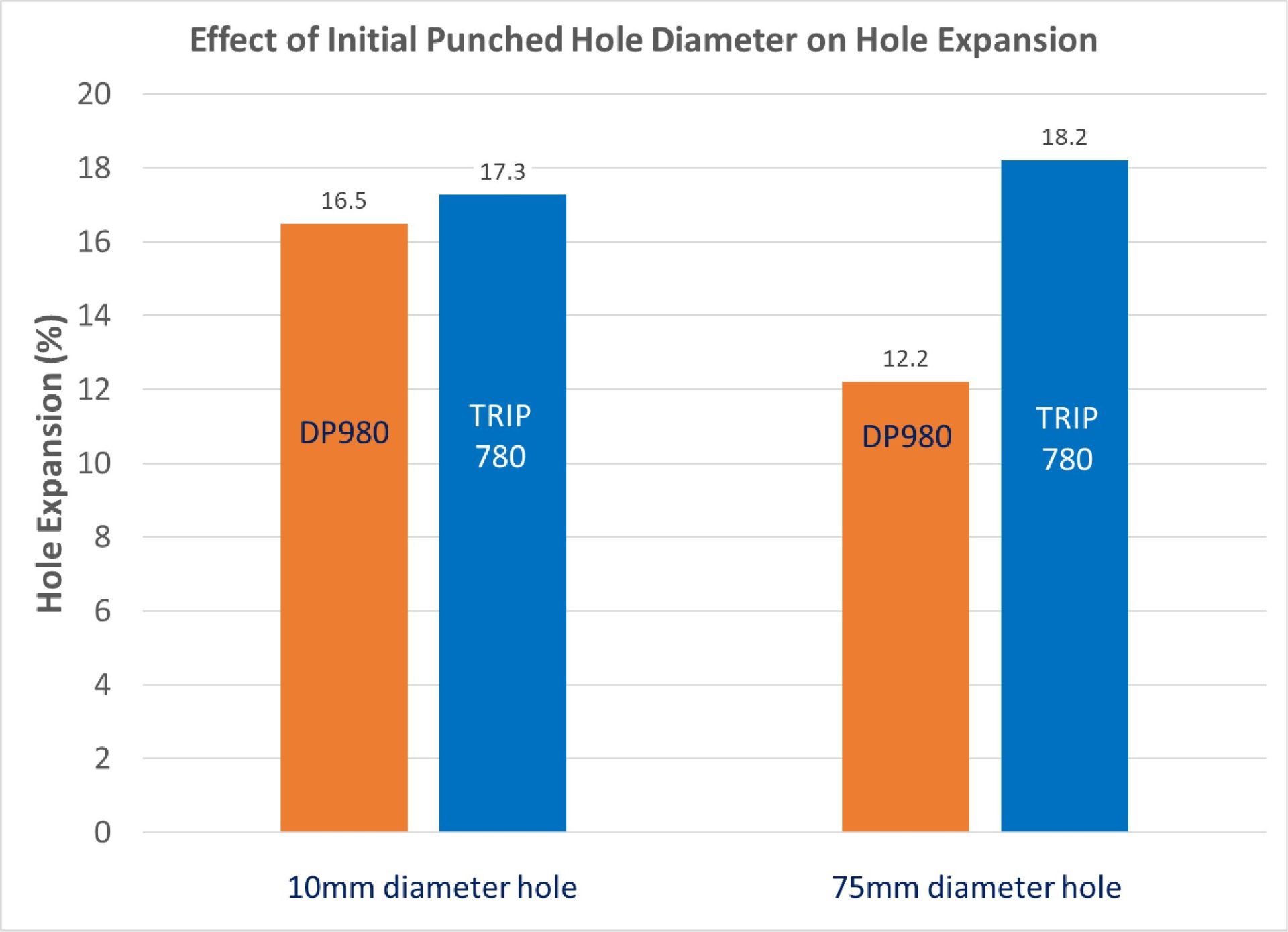
Figure 7: Effect of Initial Punched Hole Diameter on Hole Expansion. (Based on Data from Citation K-11.)
The position of the burr relative to the punch affects performance in a hole expansion test. Detrimental effects of an expanding edge are minimized If the burr is on the punch side. Having the burr on the punch side, rather than the freely expanding side, minimizes the detrimental effects of the expanding edge. The primary reason is the outer surface is in a greater degree of tension than the surface next to the punch.
Figure 8 examines the effect of edge condition and clearance on DP 590 expanded with a conical punch.K-10 The data suggests that there could be up to a 20% increase in sheared edge extension capability just related to the burr position on holes punched with conventional clearances. This should be considered in die processing materials and designs sensitive to edge expansion.
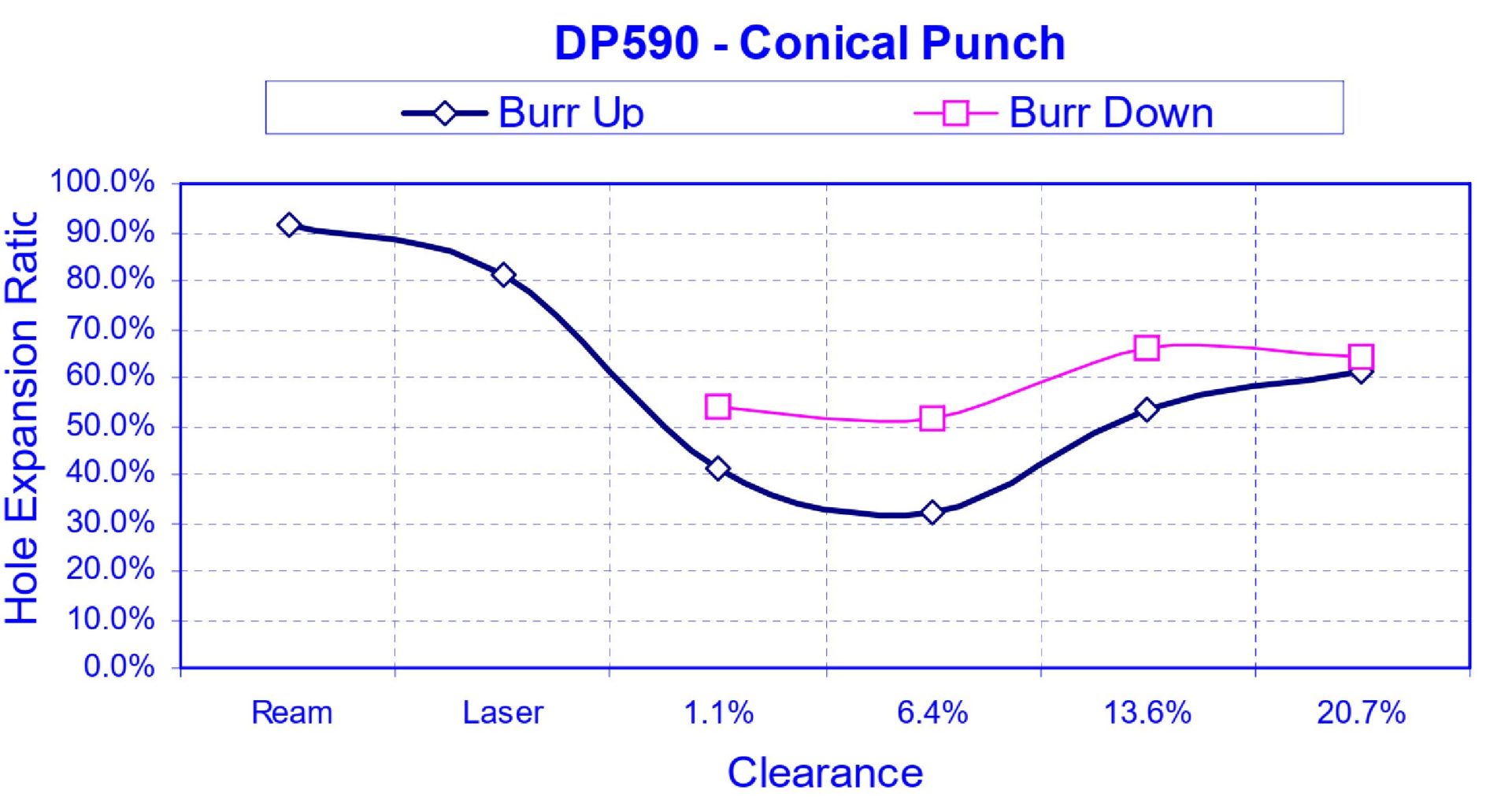
Figure 8: The Effect of Burr Orientation on Hole Expansion as a Function of Clearance on DP590. “Burr Up” means away from the punch; “Burr Down” means in contact with the punch.K-10
Shown in Figure 9 is the influence of burr orientation and material grade.K-10 The 50XK grade shown is HSLA 350Y/450T, where there is a significant improvement in the measured hole expansion related to the position of the burr relative to the punch. The magnitude of this difference decreases as strength increases, but persists for all grades tested.
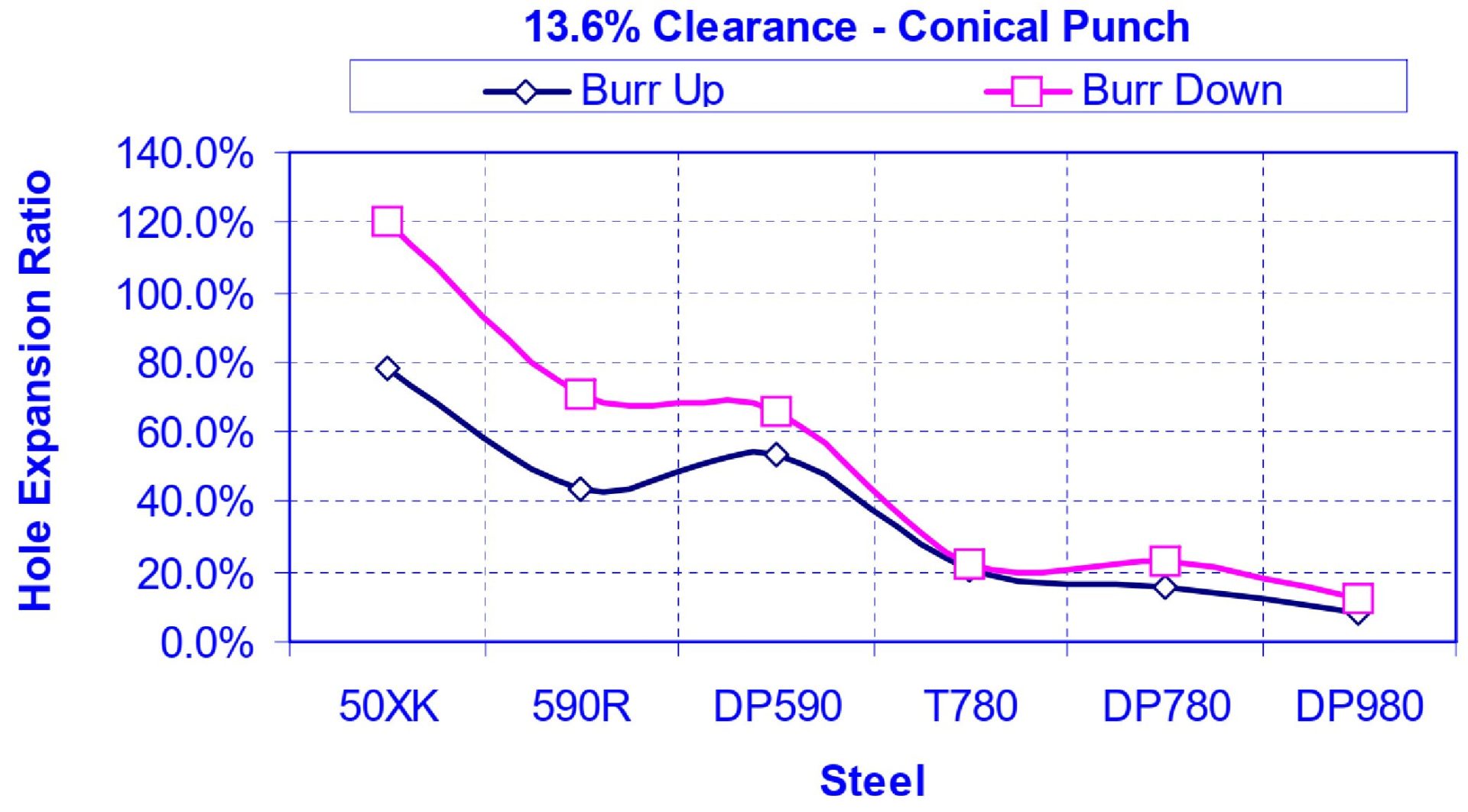
Figure 9: The Effect of Burr Orientation on Hole Expansion as a Function of Different High Strength Steel Grades “Burr Up” means away from the punch; “Burr Down” means in contact with the punch.K-10
The shape of the punch used to expand the hole impacts the degree to which it can be expanded. Figure 10 shows generalizations of the three most-common shapes: a conical punch, a flat punch, and a hemispherical punch.
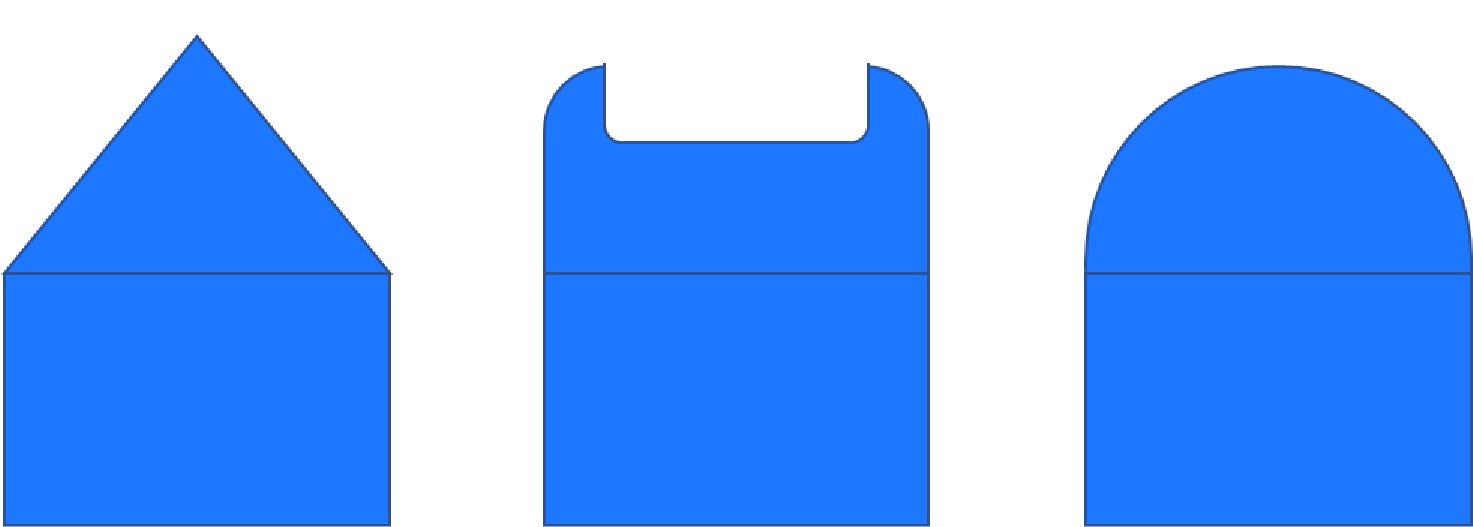
Figure 10: Sketches of Punches Used for Hole Expansion: Conical, Flat, and Hemispherical.
Metal motion and appearance changes depending on the type of punch used. Using a conical punch leads to the shape shown in Figure 11a, with a flat punch leading to the appearance shown in Figure 11b.S-3 The operations are sometimes described as hole expansion when accomplished with a conical punch, and hole extrusion with use of a flat punch.
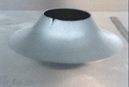
Figure 11a: Sample appearance after testing with conical punch.S-3
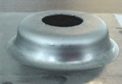
Figure 11b: Sample appearance after testing with flat punch.S-3
The ISO 16630 hole expansion test specifies the use of a conical punch with a 60 degree apex angle. Here, the free edge undergoes stretching and bending. Using a flat punch instead of a conical punch eliminates the bending component, and all deformation is from only edge stretching. These strain state differences lead to different sheared edge extension performance, with greater expansion prior to cracking achieved with holes expanded using a conical punch. This improved performance with conical rather than flat punches has been attributed to the presence of the bending component.N-10 Edge condition does not appear to influence hole expansion capability when a flat bottom punch is used.
Shown in Figures 12 to Figure 15 are the effects of burr orientation and punch type, which vary as a function of metal grade. Figure 16 compares the performance of reamed holes when expanded with either conical or flat punches. Where the tested grades perform similarly when expanded with a flat punch, the conical punch leads to exceptional performance of reamed holes of 3 of the 4 grades. The relatively poor performance of the DP780 grade may be due to the hardness differences between the ferrite and martensite components, noting that there is more martensite in DP780 than DP 600. In the study from which the data was taken, the complex phase steels had a yield/tensile ratio of approximately 87%, while for the dual phase grades the yield/tensile ratio was approximately 60%.P-13
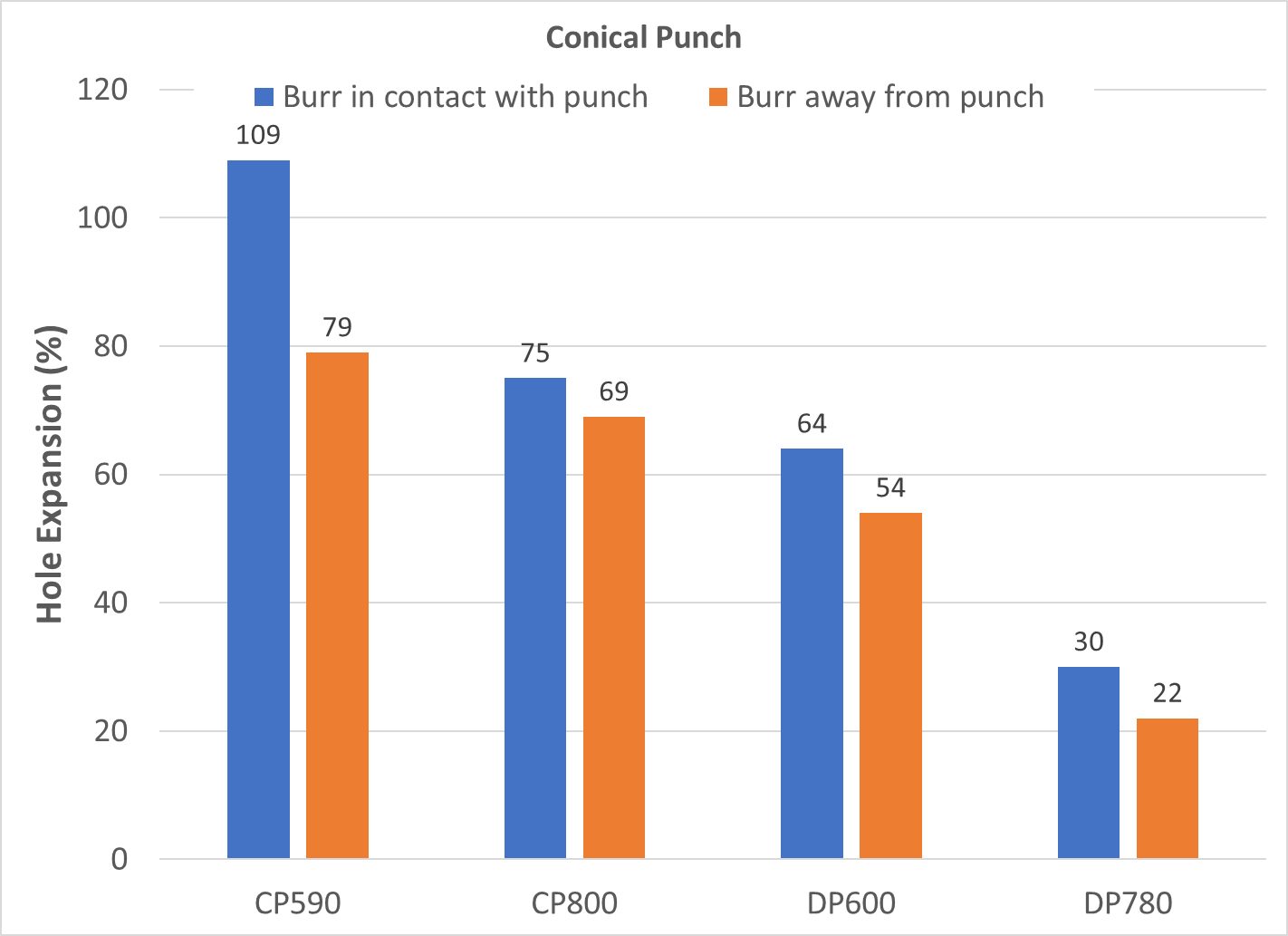
Figure 12: Effect of Burr Orientation on Hole Expansion from a Conical Punch. (Based on Data from Citation P-13.)
![Figure 13: Effect of Burr Orientation on Hole Expansion from a Flat Punch [Based on Data from Reference 11]](https://ahssinsights.org/wp-content/uploads/2020/07/Pasted-into-Hole-Expansion-Testing-Intro-31.jpg)
Figure 13: Effect of Burr Orientation on Hole Expansion from a Flat Punch. (Based on Data from Citation P-13.)
![Figure 14: Effect of Punch Type on Hole Expansion of Sheared Holes with Burr In Contact With The Punch [Based on Data from Reference 11]](https://ahssinsights.org/wp-content/uploads/2020/07/Pasted-into-Hole-Expansion-Testing-Intro-32.jpg)
Figure 14: Effect of Punch Type on Hole Expansion of Sheared Holes with Burr In Contact With The Punch. (Based on Data from Citation P-13.)
![Figure 15: Effect of Punch Type on Hole Expansion of Sheared Holes with Burr Facing Away From The Punch [Based on Data from Reference 11]](https://ahssinsights.org/wp-content/uploads/2020/07/Pasted-into-Hole-Expansion-Testing-Intro-33.jpg)
Figure 15: Effect of Punch Type on Hole Expansion of Sheared Holes with Burr Facing Away From The Punch. (Based on Data from Citation P-13.)
![Figure 16: Effect of Punch Type on Hole Expansion of Reamed Holes [Based on Data from Reference 11]](https://ahssinsights.org/wp-content/uploads/2020/07/Pasted-into-Hole-Expansion-Testing-Intro-34.jpg)
Figure 16: Effect of Punch Type on Hole Expansion of Reamed Holes. (Based on Data from Citation P-13.)
Figure 17 compares the simulation results from expanding a perfect edge (no burr, no strain) with a conical punch on the left and a spherical punch on the right.W-2 The color scale, based on a “damage” parameter, shows that a spherical punch results in a more uniform distribution of damage, especially at the edge. This suggests that the impact of burr orientation on hole expansion is less significant for this punch geometry.
Flanging with a conical punch causes high circumferential strain and high damage values at the outer edge. The inner edge of the sheet initially presses against the punch, and later stretches during flanging. Since cracks initiate at the fracture zone, using a conical punch with the burr facing the punch leads to a greater hole expansion capability than when having the burr in contact with a spherical punch.
Fracture initiates at the edge, and orienting the burr so that it is in contact with the punch leads to a greater hole expansion value.

Figure 17: Distribution of damage values in simulated hole expansion tests conducted with a conical punch (left image) and a hemispherical punch (right image).W-2
Improving Hole Expansion with New Punch Shapes
As explained above, the degree to which a sheared edge can be stretched before fracture is a function of many parameters, including the shape of the punch. Also contributing is the hardness uniformity of the microstructural phases, where grades with components having high hardness differences are associated with relatively lower hole expansion capability.
Researchers evaluated the effects of punch design and clearance on hole expansion capability of dual phase and ferrite-bainite steels, each with a tensile strength of approximately 780 MPa.L-47
In addition to a conventional flat punch face, other punch types studied were those with a beveled face, a humped shape, and a newly designed punch which combines the benefits of the prior two types. A chamfered or beveled punch is known to reduce punch forces and reverse snap-through loads, while at the same time improve edge quality and hole expansion by minimizing the hardness increases found in the shear affected zone.
Use of the humped punch (Figure 18) led to hole expansion improvements of up to 10%, compared with a conventional flat punch when testing either the DP or FB products. When comparing the edge characteristics, the humped punch results in an increased rollover zone. The authors attributed this to the hump geometry imposing axial tension on the steel during punching, thereby increasing stress triaxiality. Increases in stress triaxiality results in a reduction in effective stress even at the same average stress. This in turn lowers the plastic deformation at the sheared edge which minimizes edge fracture. For these reasons, the increases in stress triaxiality associated with the humped punch promotes higher levels of hole expansion.

Figure 18: Humped punch design used in Citation L-47.
A newly designed punch which combines a beveled and humped design (Figure 19) increases hole expansion by more than 30% in both dual phase and ferrite-bainite steels (Figure 20). As explained above, the newly designed punch is effective in promoting stress triaxiality and minimizing the plastic deformation near the sheared edge. Furthermore, the beveled design improves the shear affected zone (SAZ) characteristics, leading to improved sheared edge expandability as measured in a hole expansion test.

Figure 19: New punch design incorporating features of beveled and humped punches.L-47
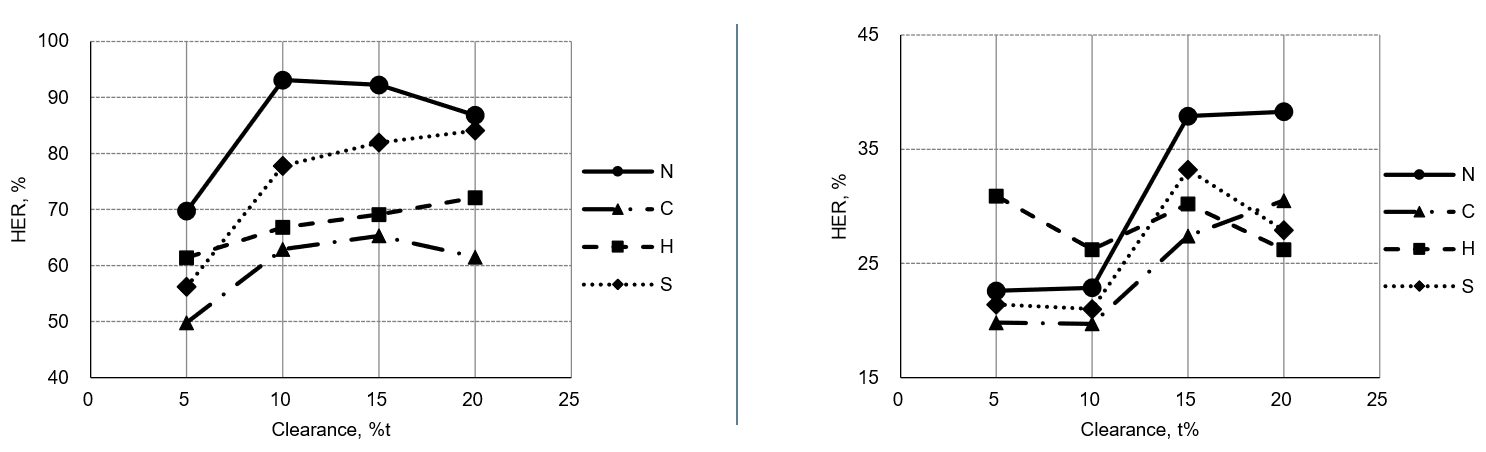
Figure 20: Effect of punch type and clearance on the hole expansion ratio of 780 MPa tensile strength steels. Left graph represents ferrite-bainite steel; right graph represents a dual phase steel. Legend: N=new punch design; C=conventional; H=humped; S=shear (beveled).L-47
Correlation of Hole Expansion Ratio with Tensile Properties
The complexities of hole expansion testing, as well as relatively few laboratories with the necessary test equipment and expertise, have led researchers to look for a correlation between the hole expansion ratio and conventionally measured properties obtained from a tensile test like the yield and tensile strength, uniform and total elongation, n-value, and r-value. Researchers even studied manipulations such as the yield-to-tensile ratio, tensile strength multiplied by uniform elongation, and n-value multiplied by r-value. Unfortunately, none of these properties or combinations have suitable correlation with the hole expansion ratio.
Recent work has shown a promising correlation between the hole expansion ratio and the true thinning strain at fracture. Our article on true fracture strain, describes this in greater detail.
Testing and Characterization
Delayed cracking caused by hydrogen embrittlement results in decreased toughness, ductility, and load-bearing capacity of a material. It is a concern with some Advanced High-Strength steel (AHSS) grades.
Three triggers must be present for there to be an embrittlement risk:
- Use of a susceptible material, such as steel with tensile strength above approximately 1000 MPa and/or the presence of retained austenite in the microstructure,
- An environment or processing step where hydrogen is available to diffuse into the steel, and
- Presence of a high stress condition, either from forming or during product usage and life cycle.
The interaction between hydrogen and the steel crystallographic structure in the presence of these conditions limits the ability of the steel to deform under load. The steel part will fracture at a lower stress than is anticipated under other conditions. Of particular concern is that fracture may not occur at the time of stamping, since hydrogen can diffuse out of the lattice over time.
High strain areas on parts formed from AHSS are at increased risk for delayed cracking, since the distorted crystallographic lattice allows for an increased hydrogen solubility. Cut edges are especially troublesome, since the shearing operation work hardens the steel (increasing strength) and damages the microstructure (increasing strain).
AHSS grades that contain retained austenite are also at increased risk for delayed cracking from hydrogen embrittlement. Stamping strains provide the driving force for the TRIP effect, where austenite coverts to martensite. The austenite crystallographic lattice allows for increased hydrogen solubility, so the TRIP effect creates a hydrogen-rich high strength martensite – conditions that promote a greater risk of embrittlement.
Sources of hydrogen include:
- Breakdown of mill or press applied lubricants,
- Annealing or heat treating atmospheres, and
- Electrochemical operations in steel mills or vehicle production such as pickling, electrogalvanizing, welding, phosphate coating, and paint pretreatment, such as e-coating.
Actions to minimize the risk of hydrogen embrittlement includes not over-pickling the surface prior to coating (since pickling uses an acid), heat treating in dew-point controlled atmospheres (below -10 °C or even lower for higher strength grades), and using the e-coating operation as a means to degas the steel.
Global steelmakers take alloying and processing approaches that are specific to their particular infrastructure and equipment. The same grade from two different steelmakers will likely use different alloying approaches. This may lead to different hydrogen embrittlement risks, as well as different tensile property ranges. Use caution when switching suppliers for all AHSS grades.
The procedures to characterize delayed fracture resistance typically involve using a machined sample, pre-strained and placed in an acidic solution for a defined time. SAE J3215S-94 is one such procedure.
Note that cracking in simulative tests does not necessarily indicate that parts made from that material would crack in an automotive environment due to the specific conditions that need to be present for hydrogen embrittlement to occur. When selecting any AHSS, results from simulative tests should be considered in conjunction with the forming and processing history of the steel, the strain state of the formed and processed part, and the operating environment of the part.