Press Hardened Steels
Motivation for PHS usage
Finite element analysis was used to determine equivalent performance between different thickness and grade combinations in B-pillars and other crash components.O-10 This study found that a 1.6 mm thick hot stamped PHS1500 B-pillar had similar performance as a B-Pillar cold stamped from 3.1 mm thick mild steel, representing a 42% weight savings, Figure 1. Higher strength PHS grades can save an additional 12% to 15% compared to PHS1500. Thus, it may be possible to achieve more than a 50% weight savings by using PHS2000 rather than mild steel in B-pillar applications.
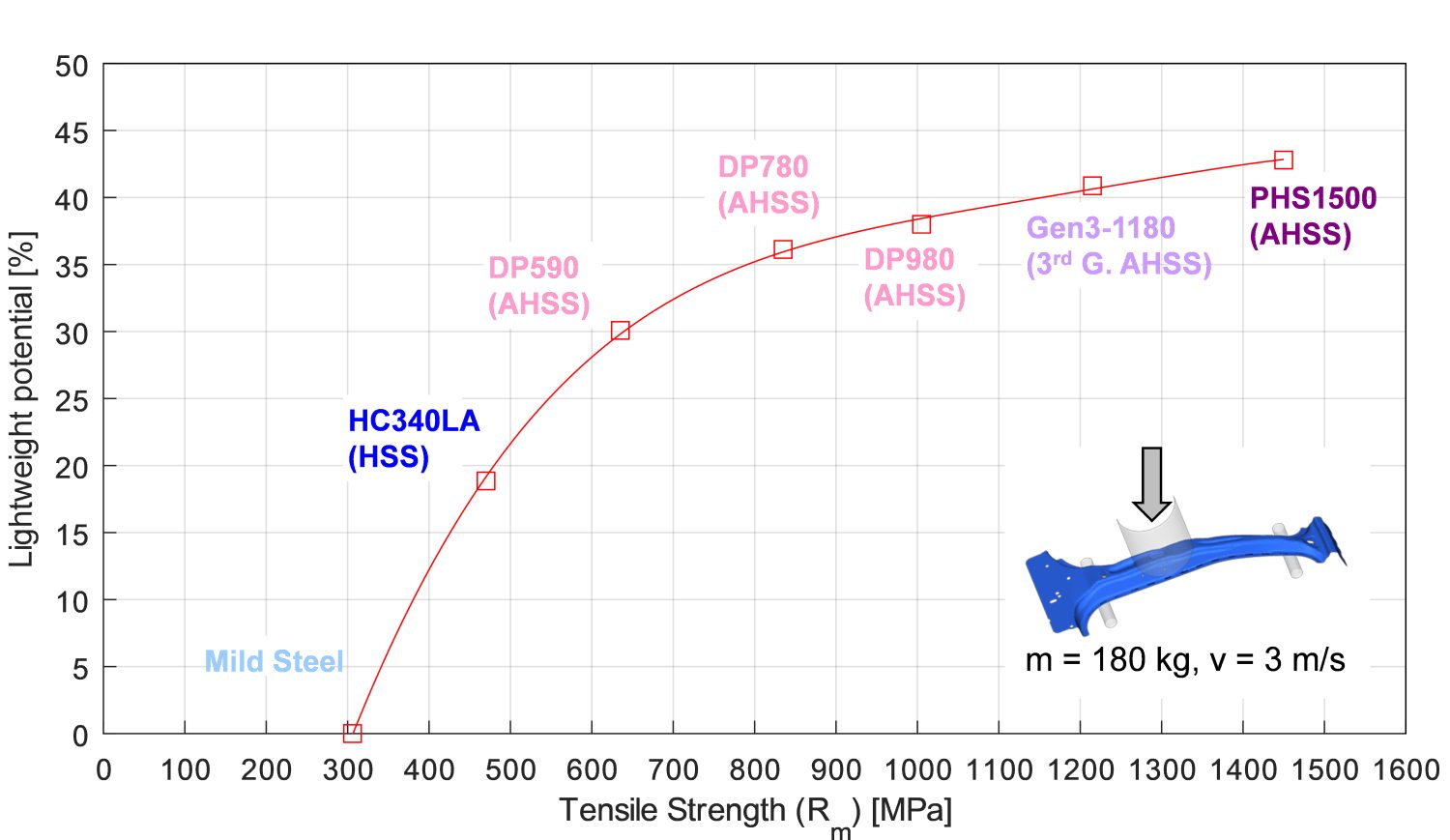
Figure 1: Lightweight potential of several steel grades, compared to mild steel (re-created after Citation O-10)
Weight savings is one reason to choose press hardened steels over cold stamping grades. Although replacing PHS1500 with an 1180 MPa cold formable grade would have a 7% to 8% weight penalty according to the study summarized in Figure 1. In some cases, this may seem like an acceptable trade-off between weight and process. However, press hardening offers several additional advantages over cold stamping of 980-1180 MPa gradesB-42:
- The formability of cold stamping higher-strength AHSS steels (even 3rd Gen AHSS) is substantially lower than press hardening steels at elevated temperatures.
- Repeatable dimensional accuracy in cold stamping of 980 MPa and 1180 MPa grades is challenging due to springback and the natural and inherent variations in the mechanical properties of the incoming sheet.
- Significant wear in cutting and forming tools may be observed, as very high contact pressures may be present.
- Cold stamping higher-strength AHSS requires high-capacity presses (both in terms of tonnage and energy).
- Hard-to-predict edge cracks are commonly observed in higher-strength AHSS.
Brief History of PHS Usage and Milestones
Press hardenable steel production for automotive applications started in 1984. Since this first use through the mid-1990s, door beams were the only press hardened body parts.F-31 Thus, the maximum possible use was limited to 4 parts per car. Depending on a car’s dimensions and the thickness of the sheet, a door beam may weigh between 0.8 kgT-33 to 2.0 kg.M-40 Thus, the total PHS usage at this time was around 3 to 8 kg per car. In a typical mid-size car (D-segment in Europe) the body may weigh around 320 kg without doors and closures, and 420 kg with them.M-41 This results in an estimated usage corresponding to 1% to 2% of the body weight (including doors). By the mid-1990s, several cars had press hardened front and/or rear bumper beams. Thus, the possible maximum usage had been increased to 5 to 6 parts per car.B-43
In 1998, Arcelor patented a coated steel for the press hardening process.L-39 The first automotive application of this coated steel occurred in 2000.V-15 Using coated steel reduces the process cost, since neither the furnace protective atmosphere nor the post-quench sandblasting are requiredV-15, although there is an increase in raw material costs. By 2001, several cars used hot stamped A and/or B-pillars, leading to PHS use in bodies-in-white surpassing 3% for the first time.R-17
In 2002, the first-generation Volvo XC90 had several press hardened and roll form hardened components, making up 6% of the BIW mass. This SUV received 5 stars from EuroNCAP and IIHS frontal and side impact tests.B-44 The IIHS harsh small overlap test resulted in a good score, which is their highest rating.L-18
In 2005, Volkswagen rolled out their (then) new Passat. This car had several components made with a special varnish coating, which facilitated use of a two-step hybrid process. This car represented the first time press hardening was used on numerous components, including the transmission tunnel and the firewall. For the first time, PHS use in the BIW exceeded 15%.W-31
2008 saw two milestones:
Around the same timeframe, steelmakers started to offer their high energy absorbing PQS grades (see PHS with Higher Elongations).P-21
In 2012, PHS usage surpassed 20% barrier, first with the Volvo V40 (2nd gen. 2012-2019) and then with the Audi A3 (3rd gen. 2012-2020) and VW Golf (7th gen. 2012-2019). The percentage hit 28% with VW Golf.B-45 Figure 2 summarizes this growth.
![Figure 2: Summary of PHS evolution: total production in million parts per year [REFERENCE 18], number of lines [REFERENCE 38], parts per car (approximate) and, BIW percentage (approximate). (Car body CAD data is taken from REFERENCE 19 and modified for visualization).](https://ahssinsights.org/wp-content/uploads/2021/02/Fig2-1.jpg)
Figure 2: Summary of PHS evolution: total production in million parts per yearO-11, number of linesH-45, parts per car (approximate) and, BIW percentage (approximate). (Car body CAD data is taken from Citation N-20 and modified for visualization).
Since 2015, many European and North American cars have doubled their PHS usage. In Europe, several VolvoS-81, VW GroupH-43, and FordB-16 models have over 30% of their body (in mass) made of PHS. Some cars may have different PHS usage in different countries. For example, PHS makes up 31% of the body structure in the 6th generation VW Polo in Europe, but in Brazil, this number is reduced to 18.5%.V-16
In 2017, Audi started production of the 4th generation A8. In its earlier generations, A8 was 100% aluminum. The car was mostly aluminum in the third generation (2010-2017). This A8 used a two-layer steel B-pillar, with one layer of cold stamped steel and another layer of press hardened steel. PHS usage was around 3% of the BIW, whereas aluminum usage was over 92%F-32. In the 4th generation A8 on the road since 2017, the body now has 17% press hardened steel.H-44 Several other aluminum intensive cars also have press hardened steels in their bodies for improved crash performance.
In North America, PHS usage has increased rapidly in the last decade. It is not uncommon to see over 10% PHS usage in recently introduced cars. For example, whereas the 9th generation (US Spec) Honda Civic introduced in 2011 had only 1% PHS usage, the 10th generation saw the usage increase to 14%.C-22 The 5th generation Ford Explorer (2012-2019) had only 5% press hardened steelM-42, but exceeds 25% in the 6th generation (2019-present).M-40 The new electric SUV Ford Mustang Mach-E is among the highest PHS-using vehicles in North America in 2020, at 29.5% of its BIW.M-43 The latest generation Chrysler Pacifica has over 11%T-19 and Jeep Wrangler over 18%B-17 of the body (excluding doors and closures) made from press hardened steels. Several GM models have also surpassed 10% barrier, such as Chevrolet Bolt EV with 12%.O-12
In addition, Chinese car makers have begun using significant amount of press hardened steels. Figure 3 shows the High-Strength Steel (HSS) usage in Great Wall Motors’ Haval branded SUVs. PHS usage started in the 2014 Haval H2.W-32 The company invested in an in-house PHS line in 2015.A-64 After the investment, PHS usage exceeded 10%.W-32 The third generation Haval H6 was introduced in mid-2020. The car has over 71% HSS, a hot stamped door ring and one of the first applications of PHS2000 steel.V-12 China is currently the biggest producer and market of “New Energy Vehicles” (plug-in hybrid electric, battery electric or fuel cell). Several electric cars built in China have over 10% PHS. The upcoming Dongfeng Voyah iFree is expected to have over 30% PHS in its body-in-white.W-33
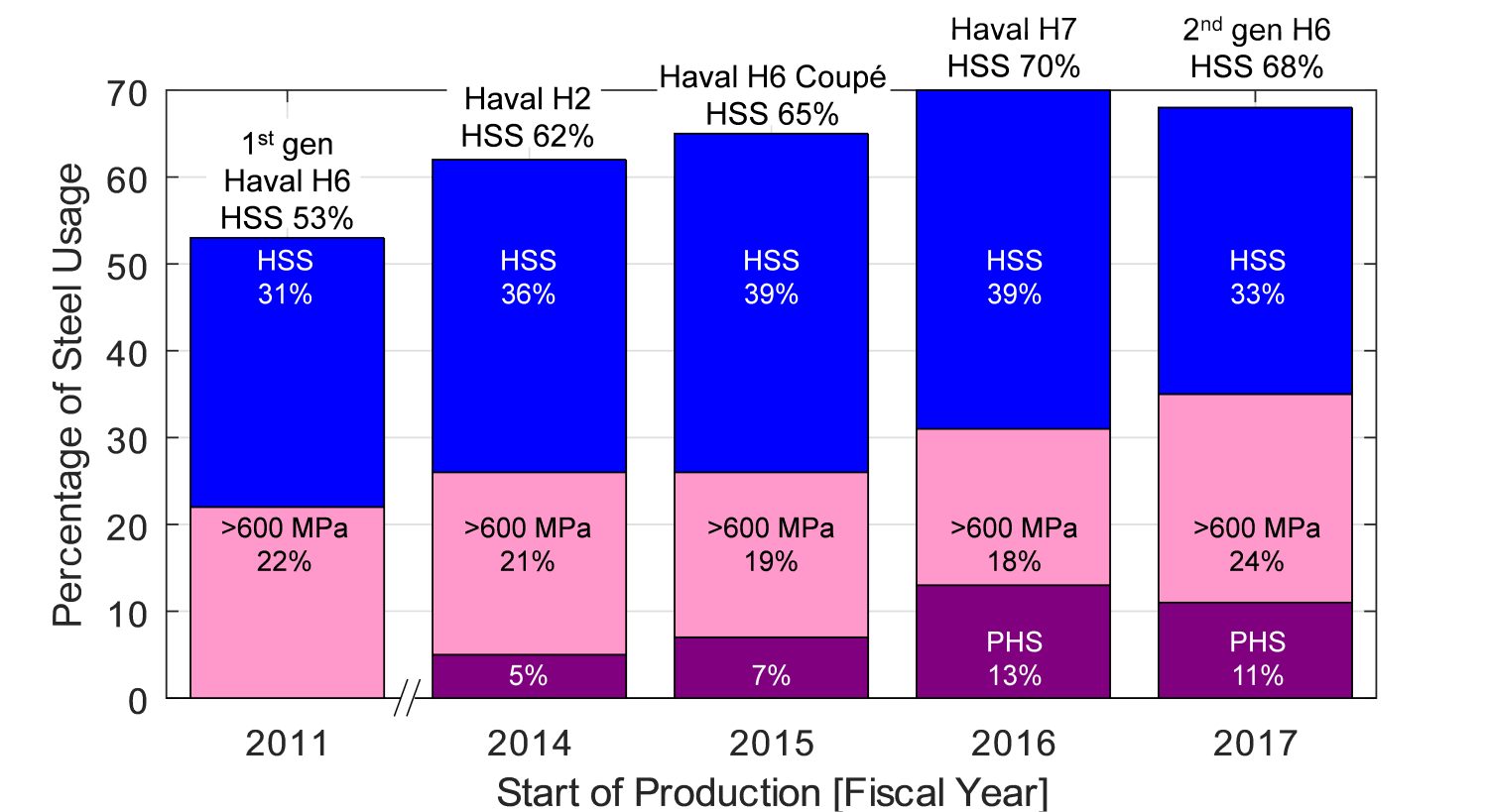
Figure 3: Increase of PHS usage in Great Wall Motors’ Haval branded SUV’s (re-created after Citation W-32)
The increased use of press hardened steel can be attributed to:
- Press hardening grades have high global availability, compared to most other cold formable steels over 980 MPa tensile strength.
- More OEMs and tier suppliers around the globe are investing in the technology. Thus, available capacity for press hardening has increased significantly in the last decade.
- With the help of commercially available finite element simulation software, more complicated geometries and larger parts can now be designed for press hardening process.
Before the First Automotive Application (1973-1984)
Press hardening, as we know it today, was developed in Luleå, Sweden, by Norrbottens Järnverks AB (abbreviated as NJA, translated as Norrbotten Iron Works). The first patent application was completed in 1973, and awarded in 1977.N-23 In 1975, a six-year long industry-university project was initiated at the Luleå University of Technology, together with Volvo Trucks and NJA. Later in 1978 while the project was ongoing, NJA merged with two other steel companies to form Swedish Steel AB (SSAB).B-45
The technology was first commercialized in agriculture components, where the high strength of press hardened steels are favored for wear resistance. In 1981, Norberg Spades and Tool Plant started the first mass production press hardening process. The company produced over 20,000 spades with a cycle time of approximately 20 seconds, while using uncoated 1.5 mm thick sheets.B-45 In 1982, the rights of the patents were transferred to Plannja AB, which was a subsidiary of SSAB. Plannja, a sheet metal forming company, formed Plannja HardTech to specialize in press hardening.
In 1984, automotive application of press hardened steel started with the Saab 9000 side impact door beams, as seen in Figure 4. A total of 4 parts were used in this car.A-66 The uncoated blanks were almost half the thickness of a cold stamped beam.T-26
![Figure 1: Door beams of the Saab 9000 (1984-1998): (a) A see-through car in Saab Museum [REFERENCE 5], (b) the hot stamped part [REFERENCE 6].](https://ahssinsights.org/wp-content/uploads/2021/02/Fig1-Door-beams-of-the-Saab-9000.jpg)
Figure 4: Door beams of the Saab 9000 (1984-1998): (A) A see-through car in Saab MuseumS-82, (B) the hot stamped part.L-42
More Automotive Applications (1984-2005)
In 1986, Jaguar XJ (XJ40) also used press hardened door beams.L-43 In 1991, Plannja HardTech received a contract from Ford to supply the door beams of Mondeo, a car to be built and sold both in Europe and North America. The production started in 1993.L-43, B-49 Until December 1994, Plannja HardTech was the sole supplier of press hardened components. By the end of 1994, as the patent rights expired, Accra Teknik AB was established for hot forming of profilesB-46 and Benteler started production of door beams for the VW Polo.L-40
The majority of the press hardened parts were door beams through the mid-1990s, with Plannja HardTech producing approximately 6 million beams in 1996. By this time, the demand for bumper beams was also increasing.F-31 In 1996, the new version of the Renault Safrane included a press hardened bumper beam. The steel was uncoated and supplied by Usinor.B-43 By the end of 1996, EuroNCAP (European New Car Assessment Program) was formed, which increased the pressure on the OEMs for improved crashworthiness.T-26 Plannja HardTech was renamed as SSAB HardTech in 1997. In 1998, both the new Volvo S80L-44 and Ford FocusL-43 were equipped with press hardened bumper beams. SSAB HardTech opened its first plant in North America, in 1998, in Mason, Mich.T-26
1998 saw the development of one of the most important breakthroughs in press hardening technology. French steel maker Usinor developed an aluminum-silicon (AlSi) pre-coated steel, commercialized as Usibor 1500 (indicating the typical tensile strength, 1500 MPa).C-24, L-39
In 2000, BMW rolled out its new 3 series convertible. In this vehicle, the A-pillar is made from 3 mm thick uncoated, press hardened sheet. This was the first PHS application at BMW, and one of the first PHS A-pillar reinforcements.S-83, S-84 Accra started delivering roll formed PHS components for the Volvo V70, initially an optional 3rd row seating support. Approximately 10,000 parts/year were supplied.G-28
AlSi coated steel was first hot stamped at a French tier 1 supplier, Sofedit.V-15 This grade was first used in the front bumper beam of 2nd Generation Renault Laguna (2000-2007). Laguna 2 was the first car to receive a 5-star safety rating from Euro NCAP.V-10 AlSi coated blanks were also used in PSA Group’s Citroën C5 (1st Gen: 2001-2007) in the front bumper beam, and the right/left A-pillars. These three parts weighed a total of 4.5 kg, approximately 1% of the total BIW weight, Figure 5A. About one month later, PSA Group started production of the compact hatchback Peugeot 307. This car had five hot stamped components (right/left A-pillar, right/left B-pillar and rear bumper beam). Unlike the Citroën C5, these parts were uncoated. The total weight was 12 kg, corresponding to 3.4% of the BIW weight.R-17, P-27
![Figure 5: Increase in press hardened component usage: (a) 2001 Citroën C5 [REFERENCE 22], (b) 2002 Volvo XC90 [REFERENCE 23] and (c) 2005 VW Passat [REFERENCE 24].](https://ahssinsights.org/wp-content/uploads/2021/02/Fig2-Increase-in-press-hardened-component-usage.jpg)
Figure 5: Increase in press hardened component usage: (A) 2001 Citroën C5P-27, (B) 2002 Volvo XC90L-29 and (C) 2005 VW Passat.H-50
Volvo started producing the XC90 SUV in 2002. The body-in-white with doors and closures weighed 531 kg.B-44 A total of 10 parts, weighing 37 kg are either roll formed or direct stamped PHS. This accounts for approximately 7% of the BIW weight.L-43 During its time, this was the highest use of PHS in car body. In Figure 5B, the press hardened components other than the 2nd row seat frame – which is a load bearing body part – are shown.
Accelerated Use and Globalization (Since 2005)
The use of press hardened parts increased rapidly after the introduction of the VW Passat in 2005. This car had approximately 19% of its BIW (by weight) made from press hardened steels, Figure 5C. Some parts in this car saw the first use of varnish coated blanks in a two-step hybrid process. Three parts were produced using either an indirect or hybrid process, including the transmission tunnel.H-50 In the same year Ford Mustang (5th Gen: 2005-2014) was rolled out. The car had “form fixture hardened” front and rear bumpers, supplied by Accra.G-28 The bumper geometry and the production method are highlighted in Figure 6 at this link.
In 2006, the Dodge CaliberK-37 and BMW X5P-28 were among the first cars to have tailor-rolled and press hardened components in their bodies. Tailor-rolling is a special process where the thickness of the blank is varied by a flexible rolling process, shown in Figure 6A. The incoming blank is a press hardening steel grade at the thickness equal to the targeted thickest portion of the part, and flexibly cold rolled to have a variable thickness distribution. Figure 6B shows the BMW X5 B-pillar.
![Figure 6: (A) Tailor Rolling Process (REFERENCE Z-5), (B) B-pillar of BMW X5 (2nd Gen: 2006-2013) [REFERENCE 27]](https://ahssinsights.org/wp-content/uploads/2021/02/Fig3-Tailor-Rolling-Process.jpg)
Figure 6: (A) Tailor Rolling ProcessZ-5, (B) B-pillar of BMW X5 (2nd Gen: 2006-2013).P-28
In 2007, Audi A4 had a tailor welded B-pillar, as shown in Figure 7A.H-32, S-65 In the same year, Volkswagen Tiguan (1st Gen: 2007-2015) became the first car to use a tailored part (also known as tailored tempered part, or multi-strength part) (Figure 7B). The B-pillar was quenched in a die, where the lower portion was heated to create a soft zone.B-20 The car had 17% of its BIW hot stamped.T-34
![Figure 7: B-pillars of: (A) Audi A4, which had a tailor welded blank with HSLA in the lower section, whereas (B) VW Tiguan created a tailored part with a soft zone (re-created after [REFERENCE 28, REFERENCE 30]).](https://ahssinsights.org/wp-content/uploads/2021/02/Fig4_PHS-B-pillars-of-various-vehicles.jpg)
Figure 7: B-pillars of: (A) Audi A4, which had a tailor welded blank with HSLA in the lower section, whereas (B) VW Tiguan created a tailored part with a soft zone (re-created after Citations H-32, B-20).
BMW 7 Series (5th Gen: 2008-2015) became the first car to have Zn-coated press hardened components in its body-in-white. The car also contained uncoated parts, as shown in Figure 8. The total PHS usage in this car was approximately 16%.P-20
![Figure 8: PHS usage in BMW 7 Series (5th Gen: 2008-2015) (re-created using [REFERENCE 32]).](https://ahssinsights.org/wp-content/uploads/2021/02/Fig5_PHS-usage-in-BMW-7-Series.jpg)
Figure 8: PHS usage in BMW 7 Series (5th Gen: 2008-2015) (re-created using Citation P-20).
Since 2010, almost all automakers are using hot stamped steel in their car bodies. In 2012, VW Group unveiled the (then) new Audi A3 and VW Golf. Both cars were sharing the modular transverse platform (MQB) and had over 24% of their BIW hot stamped. This number was 28% in the 2012 Golf (7th Generation). As of 2020, there are many global cars built on MQB platform (NAFTA, EU, China), and most of them have over 24% hot stamped components.B-14
As the technology advanced, press hardened components found uses beyond lightweighting. One such application reduced the width of the A-pillars to improve the driver’s vision. Some roof bows need to be removed in cars with a panoramic sunroof. In such designs, safety is maintained by reinforcing the A-pillars and cantrails with press hardened steel.N-21
Press hardening allowed car makers to create unconventional cars. In 2011, Hyundai rolled out the 1st generation Veloster. The car was a 3-door coupé (also known as 2+1, with one door on the driver side and 2 doors on the passenger side), and as such contained axisymmetric front doors. Thus, the car could not have a full B-ring, as illustrated in Figure 9A.B-14, R-19 Another unconventional design was the Ford B-Max subcompact MPV sold in Europe between 2012 and 2017. The car had conventional swing doors in the front and two sliding rear doors. The B-pillar was integrated in the doors and was made of press hardened steels. PHS components (integrated B-pillar in front and rear doors, door beams and cantrail) are shown with blue color in Figure 9B.B-14, L-45
![Figure 9: Unconventional car designs with PHS: (A) Hyundai Veloster, asymmetric 2+1 doors coupé (re-created after [REFERENCE 35]), and (B) Ford B-Max, sub-compact MPV with integrated B-pillars in the doors [REFERENCE 36].](https://ahssinsights.org/wp-content/uploads/2021/02/Fig6_Unconventional-car-designs-with-PHS.jpg)
Figure 9: Unconventional car designs with PHS: (A) Hyundai Veloster, asymmetric 2+1 doors coupé (re-created after Citation R-19), and (B) Ford B-Max, sub-compact MPV with integrated B-pillars in the doors.L-45
A door ring, as seen in Figure 10, is a single piece that covers the A and B-pillars, hinge pillar, and front portion of the rocker reinforcement. In 2013, the Acura MDX (3rd Gen: 2013-2020) became the first car to have a hot stamped door ring. The part was a tailor welded blank of two sub-blanks, as shown in Figure 10a. The design saved about 6.2 kg weight per car and had high material utilization ratio thanks to sub-blank nesting optimization.A-67, M-46 Currently several Honda (& Acura) and FCA models have hot stamped door rings. One of the most recent applications was in 2017 Chrysler Pacifica with 5 sub-blanks, as shown in Figure 10b. This car also has a PQS550 sub-blank at the lower B-pillar region.D-28
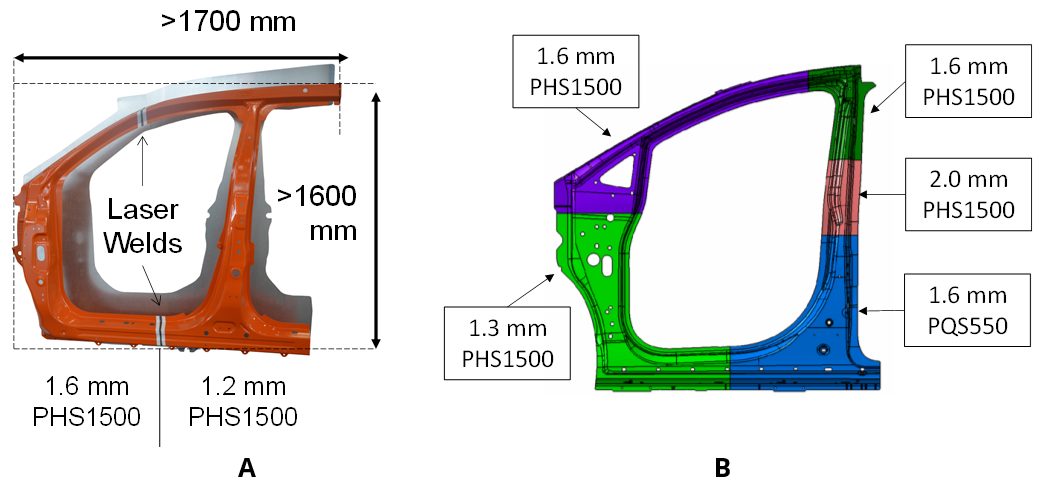
Figure 10: Hot stamped door rings: (A) First application in 2013 Acura MDX had 2 sub-blanks, (B) a more recent application in 2017 Chrysler Pacifica has 5 sub-blanks with PQS550 at the lower B-pillar (re-created after Citations B-14, A-67, D-28)
Since 2013, tubular “hardened steels” are also found in car bodies. One of the first applications was in Mazda Premacy (Mazda 5 in some markets). In this case, a special 3-D hot bending and quenching (3DQ) was employed. The same process was also used in making the A-pillars of the Acura NSX (Honda NSX in some markets, 2016-present), as seen in Figure 11a.H-29 Since 2018, tubular parts formed with internal pressure — form blow hardened parts — are being used in Ford Focus (4th Generation) and Jeep Wrangler (4th Generation). In the European version of the Ford Focus, a tailor rolled tube with thicknesses between 1.0 and 1.8 mm is used, as depicted in Figure 11b.B-16, B-17
![Figure 11: Tubular hardened steel usage in A-pillars of: (A) 2015 Acura NSX [REFERENCE 40], (B) 2018 Ford Focus [REFERENCE 41].](https://ahssinsights.org/wp-content/uploads/2021/02/Fig8_PHS-Tubular-hardened-steel-usage-in-A-pillars.jpg)
Figure 11: Tubular hardened steel usage in A-pillars of: (A) 2015 Acura NSXH-29, (B) 2018 Ford Focus.B-16
PHS Use in xEVs: Hybrid Electric, Battery Electric, Plug-in
Hybrid Electric, & Fuel Cell Electric Vehicles
The first commercially available Hybrid Electric Vehicle (HEV) was the Toyota Prius (1st Gen: 1997-2003). The second-generation Prius (2003-2009) had very few press hardened components, as shown with red color in Figure 12A. This was the first time Toyota used hot stamped components.M-47 The third generation Prius (2009-2015) had approximately 3% of its BIW press hardened. In the 4th generation Prius released in 2015, the share of >980 MPa steels has risen to 19%.U-10 Figure 12B shows the press hardened parts in this latest Prius.K-38
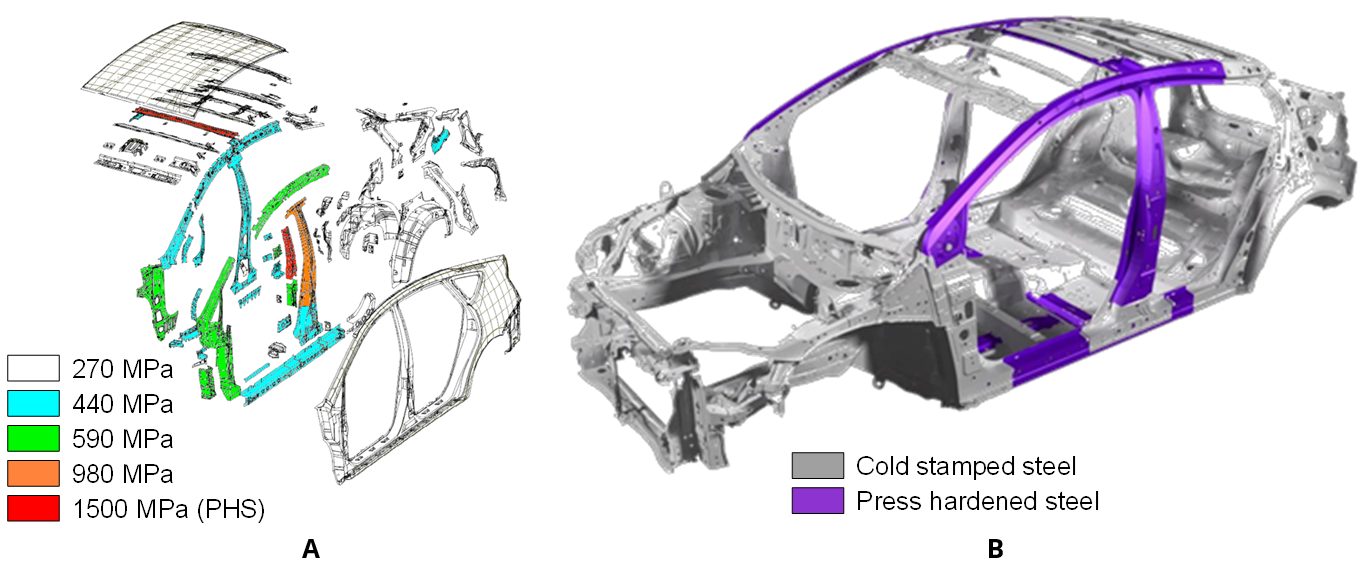
Figure 12: PHS usage in Toyota Prius: (A) 2nd generation (2003-2009) and (B) 4th generation (2015-present) (re-created after Citations M-47, K-38)
Tesla started production of Battery Electric Vehicles (BEV) in 2008, with the Tesla Roadster. This was a low volume vehicle with aluminum and carbon fiber body. Relatively higher volume vehicles, Model S and Model X had aluminum bodies, with PHS reinforcements in the pillars and the bumpers. Model S is known to have a roll-formed PHS bumper beam. High volume Model 3 and Model Y have a significant amount of press hardened components in their bodies.T-35
In 2011, General Motors started production of its first Plug-in Hybrid Electric Vehicle (PHEV), the Chevrolet Volt (known as Opel Ampera in EU and Vauxhall Ampera in the UK). This car had six hot stamped components, including A and B pillars, accounting for slightly over 5% of the BIW mass.P-29
In 2013, Chevrolet modified its supermini car Spark to have a BEV variant. The Spark with internal combustion engine weighed around 1040 kg and had good results from all IIHS tests. In the roof crush test, the car’s upper body was able to carry a total of 4615 kg, approximately 4.4 times of its weight. The EV version, on the other hand, had to carry the weight of the batteries and weighed around 1350 kg. The under body was modified to protect the battery from impacts. The upper body had to be modified to improve the load the roof can withstand in the roof strength test. PHS was used both in upper and underbodies, accounting for 14% of the BIW (Figure 13).H-51
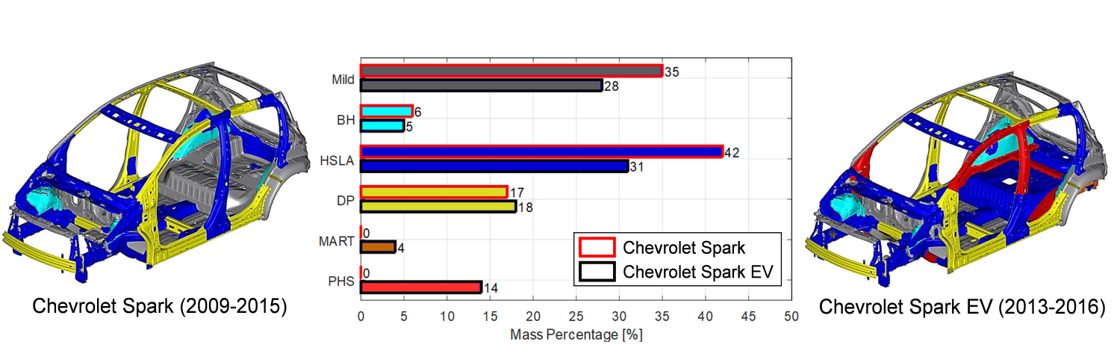
Figure 13: Distribution of different steel families in Chevrolet Spark and Spark EV (re-created after Citation H-51).
Recent years have seen many BEVs developed and marketed in North America, EU and China markets. Table 1 shows PHS usage in some of these vehicles. For the car bodies listed, only the Nissan Leaf does not have any components made from PHS.T-36 The Jaguar I-PACE, with an aluminum intensive car body, has an innovative PQS-PHS patchwork B-pillarB-21, shown in detail in Figure 9a on the PHS Grades page. Most others have PHS usage over 10% of their BIW mass. Renault ZOET-37, Chevrolet BoltO-12 and Opel Corsa-eS-85 are all subcompact cars (B-segment in EU) with steel intensive bodies. Chevrolet Bolt has aluminum doors and closures.O-12 Nissan Leaf and VW ID.3 are compact cars (C-Segment), both have steel intensive bodies. The 1st generation Nissan Leaf had aluminum doors and closuresT-36 and VW ID.3 used extruded aluminum to protect the battery from side impacts [54]. The Audi e-tronE-9, Jaguar I-PACEB-21 and Aiways U5S-86 are medium size SUVs with significant aluminum usage, yet all have some percentage of PHS in their bodies. Polestar 1 is a plug-in hybrid sports car, built-in China and sold under the Volvo Car performance brand, Polestar. The car’s upper body is almost exclusively carbon fiber reinforced polymer (CFRP), whereas the under body is 93% steel, including significant amount of PHS.N-22 ORA R1 is a small city car (A-segment), produced by Great Wall Motors.S-86 The car was the 3rd best-selling EV in China in October 2020.M-48 Voyah, a new brand of Dongfeng Motors, will be releasing an upcoming SUV called the iFree.W-33
In December 2020, Hyundai announced their new electric platform, E-GMP. The platform will utilize press hardened steel components to secure the batteries.H-52
Another xEV technology is Fuel Cell Electric Vehicle (FCEV), which uses hydrogen as fuel to generate electricity. One of the first FCEV cars was the 2009 Honda FCX Clarity. The car was not sold, but leased in limited numbers. There were less than 50 cars leased in the US.V-18
Since 2015, Toyota has been selling its Mirai FCEV. The car has to carry high pressure hydrogen tanks (2 in the 1st generation and 3 tanks in the 2nd generation), battery, and electric motor. The car is similar in size with Camry, but is about 350 kg (770 lbs) heavier. The first generation Mirai had only B-pillars, cantrails and lateral floor members press hardened.T-38 The second generation has a number of parts with PHS in its under body as well.T-39
The second-generation Honda Clarity FCV was introduced in 2016. This BIW has approximately 14% press hardened components, by weight.K-39 In 2018, Hyundai Nexo became the first fuel-cell car to be tested by EuroNCAP and received 5 stars. The car has A and B pillars, rocker reinforcements, and several under body components made from PHS, as seen in Figure 14.H-53
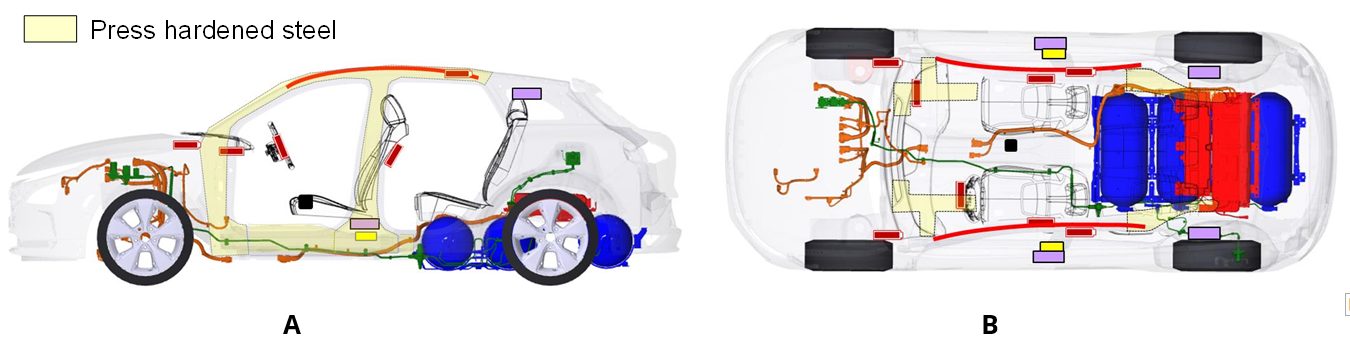
Figure 14: Press hardened steel usage in Hyundai Nexo Fuel Cell vehicle: (A) side view and (B) top view (re-created after Citation H-53).
PHS Use in Commercial Vehicles
Press hardening steels improves safety and contributes to lightweighting in passenger vehicles with conventional internal combustion engines and xEVs. In commercial vehicles, lightweighting can help to increase the payload, as typically these vehicles are limited by their gross vehicle weight (GVW = curb weight + payload). Electrification (HEV, PHEV or BEV) in commercial vehicles further increases the need for press hardened steels in these vehicles.
In Europe, van type commercial vehicles are popular. There are at least 4 distinct classes of panel vans. The smallest ones are typically based on sub-compact (B-segment) car platforms. These cars may be between 3.8 and 4.2 m long. Vans like Fiat Fiorino and Ford Transit Courier, shown in Figure 15a, can be classified as subcompact. Compact vans are based on C-segment cars and could be sold as commercial or passenger cars. Fiat Doblo (sold as Ram Promaster City, in NAFTA), Ford Transit Connect (shown in Figure 15b), Opel Combo, Peugeot Rifter, Renault Kangoo, VW Caddy are in this segment. These vehicles may have short or long wheelbase (SWB and LWB) versions. Typical lengths are between 4.4 and 4.5m in SWB; and 4.7-4.85m in LWB. Small vans include Fiat Talento, Ford Transit Custom (shown in Figure 15c), Mercedes Vito/V-Klass, Opel Vivaro/Zafira Life, Peugeot Expert/Traveler, Renault Trafic, and VW Transporter/Caravelle. These cars can be sold as vans or minibuses, with 4.6 to 5.3m length options. Lastly, the largest volume and heaviest payload can be carried in full-size vans. Fiat Ducato (Ram ProMaster in NAFTA), Ford Transit, Mercedes Sprinter (Freightliner Sprinter in US), Peugeot Boxer, Renault Master and VW Crafter (shown in Figure 15d) (length data is taken from Wikipedia.org). With new generation commercial vans, over 15% PHS is now also common in Europe.
![Figure 15: European panel vans of different sizes: (A) Ford Transit Courier (sub-compact) [REFERENCE 66], (B) Ford Transit Connect (Compact) [REFERENCE 67], (C) Ford Transit Custom (Small) [REFERENCE 68], and (D) Volkswagen Crafter (Full-size) [REFERENCE 69].](https://ahssinsights.org/wp-content/uploads/2021/02/Fig12_European-panel-vans-of-different-sizes.jpg)
Figure 15: European panel vans of different sizes: (A) Ford Transit Courier (sub-compact)G-40, (B) Ford Transit Connect (Compact)C-25, (C) Ford Transit Custom (Small)B-51, and (D) Volkswagen Crafter (Full-size).V-19
In North America, pick-up trucks are popular for both commercial and leisure uses. Most OEMs offer pick-up trucks in three different segments: compact, mid-size and full-size. The US Environmental Protection Agency (EPA), on the other hand, classifies trucks as small and standard. Almost all of these pick-up trucks are built as body-on-frame construction with 3 main components: (1) a ladder frame carrying the powertrain and suspension, (2) a cab where the occupants sit and (3) a box which would carry the goods. Honda Ridgeline is one of the exceptions, a standard-size (EPA class) truck with a unibody construction, meaning it does not have a separate frame.B-52
For full-size trucks, the first use of PHS at Ford started with 12th generation F-series in 2009. The largest cab option (commonly called a crew-cab) used a press hardened B-pillar, as shown in Figure 17A. The total weight of PHS components was estimated to be around 8.5 kg, approximately 3% of the total cab weight.M-49 In its 13th generation, Ford switched to an aluminum intensive (92% Al) cab, which did not use PHS in the cab.K-40 However, in the ladder frame of some F-series trucks, additional load transfer parts can be found, as shown in Figure 16C. These parts are produced by the form fixture hardening method. In 2015, trucks without these parts (such as seen in Figure 16A) received a marginal score at IIHS small overlap test. Those with the additional parts (highlighted in Figure 16B) received the “Top Safety Pick” designation.I-19, M-50
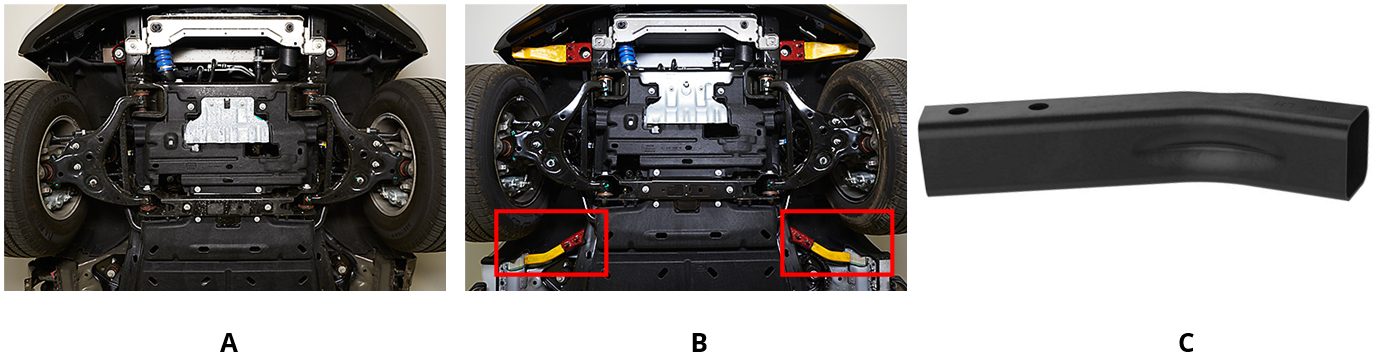
Figure 16: Undercarriage view of Ford F-Series: (A) Extended cab, and (B) Crew cab. (C) The tubular parts are made by form fixture hardening process (re-created after Citations I-19, M-50)
In 2015, Chevrolet Colorado (and its badge engineered version GMC Canyon) was introduced. This mid-size truck has A and B-pillars hot stamped, accounting for 6% of the cab weight. The truck’s B-pillar reinforcement was a tailor rolled blank with thickness varying between 1.0 and 2.0 mm.M-51 Toyota Tacoma, a direct competitor to Colorado in size, also has press hardened steels in its A and B-pillars.H-54
![Figure 17: Hot stamped steel usage in truck cabs: (A) 12th generation Ford F-150 (2009-2015) [REFERENCE 71], (B) 2nd generation Chevrolet Colorado (2014-present) [REFERENCE 75]. *Percentage values are for cab only.](https://ahssinsights.org/wp-content/uploads/2021/02/Fig14_Hot-stamped-steel-usage-in-truck-cabs.jpg)
Figure 17: Hot stamped steel usage in truck cabs: (A) 12th generation Ford F-150 (2009-2015)M-49, (B) 2nd generation Chevrolet Colorado (2014-present).M-51 *Percentage values are for cab only.
In 2017, the 2nd generation Honda Ridgeline became the first truck to have a hot stamped door ring, Figure 18A. As opposed to most other pickup trucks, Ridgeline has a unibody design – with no separate frame. Thus, the body and the cab have to be reinforced and weighs about 593 kg. Door rings are tailor welded from 4 sub-blanks, all PHS1500, and weigh approximately 17 kg per side.B-52 In 2018, FCA started production of the 5th generation RAM 1500. This truck also has press hardened door rings, as well as other PHS components in the under and upper body, accounting for almost 15% of the cab and box weight (Figure 18B). These door rings are made from a 6-piece tailor welded blank, with a thickness range between 1.2 and 1.8 mm. A PQS550 sub-blank is used as the lower B-pillar section.R-3
![Figure 18: PHS door rings are found in (A) 2017 Honda Ridgeline [REFERENCE 70] and (B) 2019 RAM 1500 [REFERENCE 77]. *Percentage values include cab and box.](https://ahssinsights.org/wp-content/uploads/2021/02/Fig15_PHS-door-rings-1.jpg)
Figure 18: PHS door rings are found in (A) 2017 Honda RidgelineB-52 and (B) 2019 RAM 1500.R-3 *Percentage values include cab and box.
PHS has also found several uses in heavy commercial trucks. The cab of the 2nd generation Scania truck weighs around 388 kg (including doors). 4% of the cab is made of PHS to pass ECE R29 safety tests. A-pillars have soft zones to further improve toughness of the spot welds.B-53 The Mercedes Actros truck has a roll formed PHS rear bumper, with a rectangular closed profile of 100 x 60 mm and a wall thickness of 3.5 mm. Crossmembers of the frame are also made with the same process.H-55
There are several electric commercial vehicles in production and in development. In Europe, the Mercedes e-Sprinter and VW e-Crafter are commercially available. Ford e-Transit (which will be also sold in NAFTA) is under development. The body is not modified in either the VW e-Crafter nor the Ford e-Transit.V-20, H-56 The battery is attached to the under body with additional elements. Typically, payloads are reduced due to the battery weight. The two battery options offered for the e-Sprinter are one with a long range at the expense of reduced payload and another allowing for increased payload but reduced range.M-52
The Tesla Cybertruck and Rivian R1T are electric trucks launching soon in the United States. Tesla will use an exoskeleton model: instead of thin skin panels reinforced with PHS, the Cybertruck has thick stainless steel skin panels without reinforcements.B-54 Rivian is known to use ultra-high-strength steels in their car bodies, most probably including PHS.R-20
Supply
By 2015, hot stamping industry was a 6 billion USD industryV-17 with approximately 100 companies involved.B-14 The industry can be divided into 5 layers:
- Raw materials: steel mills, service centers, cold rolling companies (including tailor rolled blanks), tailor welded blank companies, blanking companies, and similar.
- Tool makers: die makers, die spotting companies, and similar.
- Equipment suppliers: press, furnace, automation, cooling system, laser cutting machinery, and similar.
- Tier suppliers: Tier 1 or Tier 2 suppliers, typically for automotive OEMs.
- OEMs: Original equipment manufacturers, or the vehicle producers themselves.
Raw Material Suppliers
SSAB was the first PHS steel producer, and supplied PHS steel to the first Tier 1 PHS stamping company – which was SSAB subsidiary SSAB HardTech AB. Until 1994, HardTech was the only press hardened component supplier and produced approximately 3 to 4 million door beams per year.F-31, T-26 At the time, the estimated total PHS steel supply was on the order of a few thousand tons per year. At the end of 1994, Accra was established as the second Tier 1 supplier.B-46 The company, at least initially, also sourced their steel from SSAB.G-28
Benteler started supplying hot stamped parts to Volkswagen in 1994.L-40 Benteler specified a narrow standard for 22MnB5, commonly known as BTR165 (or sometimes shortened as BTR). Several OEMs use this abbreviation for uncoated PHS steels.
By 1996, Usinor (the French steel company which later merged with Spanish steel producer Aceralia and Luxembourg-based Arbed to form Arcelor) is known to supply uncoated PHS grade to Renault.B-43 In 1998, Usinor developed the AlSi coatingL-39, which would be commercialized in 2000 with the USIBOR 1500® name.V-15
In 2003, the annual European usage of press hardening steel was estimated to be between 60,000 and 80,000 tons.H-46 While the AlSi coated steel usage was only 5,000 tons/year in 2006, it increased to 220,000 tons/year by 2009. Five steel mills had the capability to produce AlSi coated PHS material in 2009, with three owned by ArcelorMittal, and one each by ThyssenKrupp and Nippon Steel. The latter two companies were running under an ArcelorMittal license.V-15
Earlier projections of future PHS usage have almost always underestimated the growth rate. In 2009, it was projected that in 2013, AlSi coated steel usage would be close to 700,000 tons/year.V-15 In reality, nine steel mills produced AlSi coated steel in 2013, with the total production exceeding 850,000 tons. In 2013, it was estimated 3 million tons would be achieved by 2020.E-8 Consumption surpassed the 3 million tons threshold in 2018 (Figure 19).B-32
![Figure 19: Press hardening steel demand had surpassed the previous estimates [REFERENCE 10, REFERENCE 12, REFERENCE 13]](https://ahssinsights.org/wp-content/uploads/2021/02/Fig1_Press-hardening-steel-demand.jpg)
Figure 19: Press hardening steel demand had surpassed the previous estimates.V-15, E-8, B-32
Once the steel coils are produced, they are typically sent to steel service centers, where the coils could be slit and/or cut to length. Some service centers may also have blanking lines and laser welding capabilities capable of producing tailored blanks using PHS and/or PQS grades.
In 2014, ArcelorMittal Tailored Blanks (AMTB) had at least three ablation lines for PHS/PQS grades, giving them an annual capacity of producing 3 million tailor welded blanks.E-8 By 2015, the total PHS TWB market was estimated to be 8.4 million blanks. WISCO Tailored Blanks (now known as Baosteel Tailored Blanks) was supplying approximately two thirds of the demand.B-47 By 2019, AMTB had invested in four additional ablation lines.J-20 Estimates of their capacity now exceeds 7 million welded blanks per year.
Tailor rolled blanks (TRB) are mostly supplied by the German company Mubea. An estimated 6,000,000 hot stamped TRB components have been produced per year in 2017. As of 2020, Mubea operates 8 tailor-rolling lines in 3 continents.
Tier Suppliers
Currently there are over 500 press hardening lines around the world. Approximately 10% of them are run by OEM’s. A minority of the lines are run for die tryout, R&D and training purposes by steel mills, die makers and equipment manufacturers. There are over 60 tier supplier companies, running approximately 75% of the all press hardening lines. Three big tier suppliers are currently operating over 40% of all the lines, as shown in Figure 20.
![Figure 20: Distribution of press hardening lines (REFERENCE 31]](https://ahssinsights.org/wp-content/uploads/2021/02/Fig2_Distribution-of-press-hardening-lines.jpg)
Figure 20: Distribution of press hardening lines.H-49
In 2003, there were 15 lines in Europe. This number increased to 42 lines in 2009H-46 and over 60 lines by 2012.B-48 According to Billur Metal Form’s Hot Stamping Lines DatabaseH-49, there are over 180 lines in EU27+Turkey, as of 2020.
The first Tier supplier for press hardened components was HardTech, initially with lines located in Luleå Sweden. The first North American line was also established by HardTech in 1998 in Mason, MI, USA. By 2011, there were already 51 lines in North America.B-48 The number is now over 130 according to Billur Metal Form’s Hot Stamping Lines Database.H-49
In 2011, over 85 percent of the press hardening lines were in Europe or North America. China, Korea and the rest of the world had only 19 lines.B-48 Only 5 hot stamping lines existed in China in 2010, but the number increased rapidly to 40 by 2015.M-44 By 2020, the total number of lines in China has well surpassed 100. South Korea is home to over 40 hot stamping lines in 2020.
Figure 21 is a plot containing parts produced per year (in millions) shown in red and the number of PHS lines globally in blue, showing that they track well at least through approximately 2017. This leads to the conclusion that until that time, the average hot stamping line produced 1 million parts per year. The divergence beginning around 2017 may indicate productivity improvements, since the annual parts produced are outpacing the number of additional lines commissioned. However, since post-2015 production numbers are from an estimate made in 2015, current values may suggest different line productivity trends.
![Figure 21: Number of hot stamping lines and parts produced per year (literature data from REFERENCE 16, REFERENCE 18, REFERENCE 19, REFERENCE 20; database information is from REFERENCE 31]](https://ahssinsights.org/wp-content/uploads/2021/02/Fig3_PHS-Number-of-hot-stamping-lines-and-parts-produced-per-year.jpg)
Figure 21: Number of hot stamping lines and parts produced per year (literature data from Citations B-48, A-52, H-47, O-11; database information is from Citation H-49)
Original Equipment Manufacturers
Volkswagen was the first OEM to invest in an in-house press hardening line. By September 2004, there were already 6 press hardening lines within the VW Kassel plant.K-36 The lines were designed to work with the Direct PHS Process, as well as the two-step Hybrid PHS Process. The 6th Generation Passat started production in March 2005. The car had a total of 15 press hardened parts: 12 through the direct process and 3 using the two-step hybrid process, with varnish coatings.W-31 Since 2010, only Al-Si coated blanks have been used with the direct process within Volkswagen. As of 2020, there are a total of 14 press hardening lines at VW: 11 in Kassel and 3 in Wolfsburg. Many current Volkswagen models have over 25% press hardened components in their bodies.
Fiat became the second OEM to invest in press hardening. In 2008, their Cassino plant had five press hardening lines. The lines were accompanied by two trimming presses and eight laser cutting machines.R-18 Fiat models typically have around 5% to 15% of their body components formed using of press hardened steels, as seen in Figure 22.M-45 In 2013, Fiat Group’s Alfa Romeo brand started production of the 4C sport car. In this vehicle, an underbody aerodynamic component was hot formed Al 6016, which also was produced on a press hardening line (not necessarily in-house).C-23
![Figure 22: Press hardened component usage in Fiat group cars (re-created after REFERENCE 2]](https://ahssinsights.org/wp-content/uploads/2021/02/Fig4_PHS-usage-FIAT.jpg)
Figure 22: Press hardened component usage in Fiat group cars (re-created after Citation B-14)
In 2009, BMW became the third OEM to have in-house press hardening lines. Contrary to VW and Fiat, BMW uses zinc-coated blanks formed using the Indirect Process. Their first car to have in-house press hardened components was the BMW 5 GT (F07, 2009-2017).G-38 In the latest generation 5 series (G30, 2016-present), the PHS usage has surpassed 22% of the body-in-white mass.A-65
Other OEM’s having in-house press hardening lines include (but not limited to):
- Audi: 2 lines in Ingolstadt, since 2009; 2 more lines in Münchsmünster, since 2013.
- Honda: 1 line in Japan, operating since 2012.
- SEAT: 3 lines in Martorell.
- Proton: 1 line in Malaysia, since 2012.
- Toyota: 1 line in Japan.
- Volvo: 2 lines in Olofström Sweden, since 2014.
- Renault: 1 line in Valladolid Spain; 1 more in Douai France, both running since 2014.B-14
- Ford: 2 lines in China, 2 in Saarlouis, Germany and 3 in Woodhaven, MI, USA.
- Great Wall Motors: 1 line in Xushui Baoding, China, running since 2015.G-39
- Opel, 1 line in Kaiserslaitern Germany, started operation on 15 January 2021.L-41
Some OEMs may have access to press hardening lines within their subsidiary tier suppliers. These include Toyota through Toyotetsu and Hyundai through the lines within Hyundai Steel. These are included under “Others” in Figure 20.
Back To Top