Laser Welding
This article is a summary of the paper entitled, “IMPROVEMENT OF DELAYED CRACKING IN LASER WELD OF AHSS AND 980GEN3 STEELS”, by Linlin Jiang, Kyle Kram, and Chonghua Jiang.L-62
Researchers from AET Integration, Inc. worked on developing welding techniques that mitigated delayed cracking issues when laser welding Advanced High-Strength Steels (AHSS) and 3rd Gen AHSS. Stitch welds are most likely to have delayed cracking issues therefore the test specimen were cross tension samples with stitch welds. The test was run with ten specimens for each material with the same parameters. The specimen were visually inspected after welding in intervals from 30 min to 12 hours for 48 hours. The specimen were then inspected using X-ray analysis, cross-sectioning, and scanning electron microscope (SEM) analysis. Cracks were observed in the weld schedules used in Figure 1 and 2, and no cracking was observed in the welding schedules developed by researchers as seen in Figure 3 and 4 by altering parameters such as laser power, travel speed, beam oscillation, and defocusing techniques. The techniques are currently patent-pending and were not discussed in the research paper. Further validation tests on 3rd Gen steels is expected in the future.
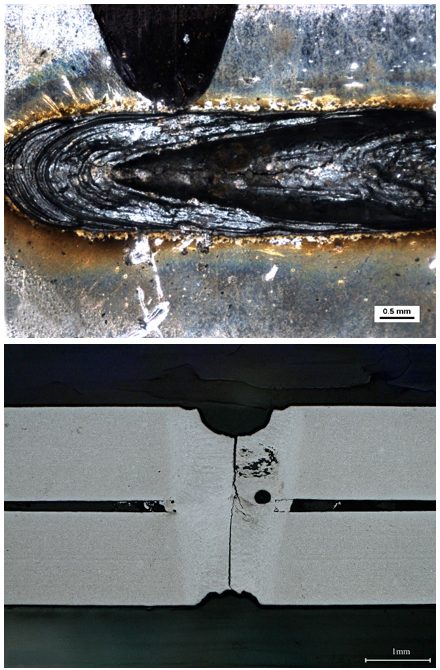
Figure 1: Delayed Crack in Weld of Material A. (Top) Crack from top surface, (Bottom) Cross Section of Crack.L-62
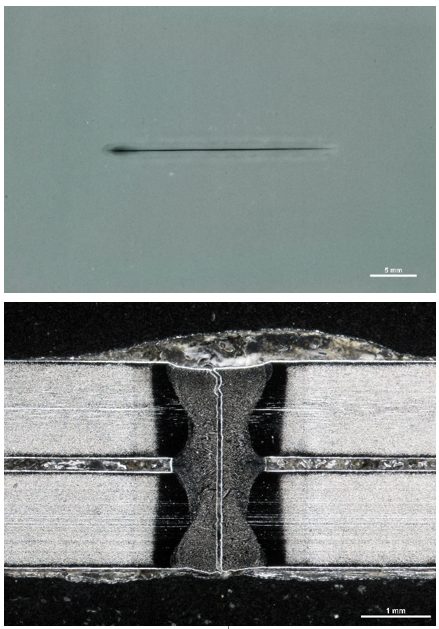
Figure 6: Delayed Cracking in Weld of Material B, (Top) X-ray, (Bottom) Cross section of crack.L-62
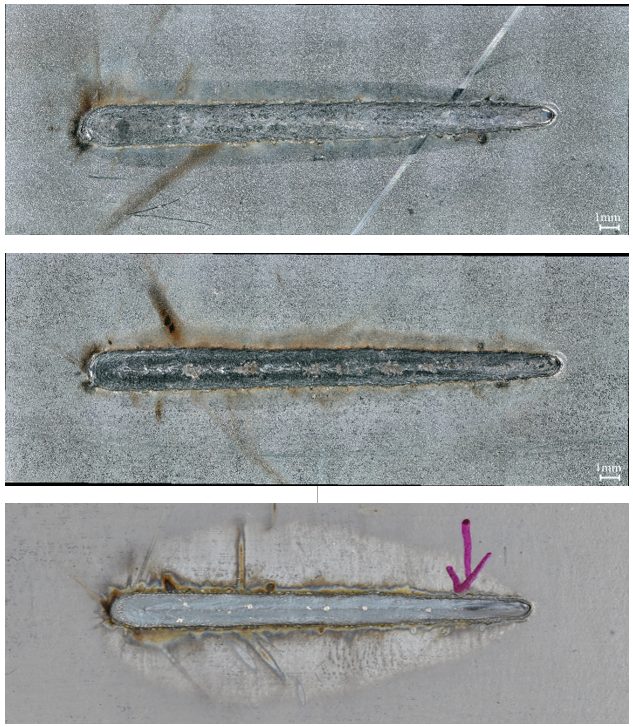
Figure 3: Examples of Visual Inspection Photographs. (Top) Top surface, Material A, (Middle) Top surface, Material B, (Bottom) Top surface, Material C.L-62
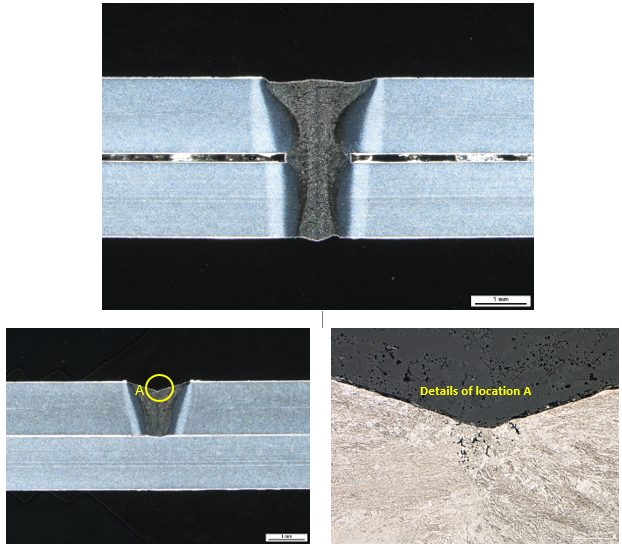
Figure 4: Examples of Cross Section Photographs. (Top) Cross section of weld center, Material A; (Bottom) Cross section of weld crater, Material A.L-62
Laser Welding
This article summarizes the findings of a paper entitled, “Hot cracking investigation during laser welding of high-strength steels with multi-scale modelling approach”, by H. Gao, G. Agarwal, M. Amirthalingam, M. J. M. Hermans.G-4
Researchers at Delft University of Technology (TU Delft) in The Netherlands and Indian Institute of Technology Madras in India attempted to model Hot Cracking susceptibility in TRIP and DP steels. For this experiment, TRIP and DP steels are laser welded and the temperatures experienced are recorded with thermocouples at three positions. Temperatures experienced during welding are measured and used to validate a finite element model which is then used to extract the thermal gradient and cooling rate to be used as boundary conditions in a phase field model. The phase field model is used to simulate microstructural evolution during welding and specifically during solidification. The simulation and experimental data had good agreement with max temperature deviation below 4%.
Summary
Referencing Figure 1 (Figure 6 in the original paper) which shows the microstructure where the dendritic tips meet the wel, centerline, it is observed that TRIP steels reach a solid fraction of 93.7% and DP steels reach a solid fraction of 96.3% meaning that TRIP steels have a larger solidification range than the DP steels. Figure 8 shows the phosphorus distribution where the dendritic tips reach the weld centerline. TRIP steels show a concentration of up to 0.55 wt-% where segregation occurs compared to the original composition of 0.089 wt-%. DP steels show a max of 0.06 wt-% which is significantly lower than the TRIP steels. In addition to phosphorus, Al is seen in high concentration in TRIP steels which contributes to the broder solidification range. A pressure drop is the last factor contributing to the Hot Cracking observed in TRIP steels(figure 2). The pressure drop is due to a lack of extra liquid feeding in the channels and forms a pressure difference from the dendrite tip to root. The pressure drop in TRIP steels is calculates to 941.2 kPa and 10.2 kPa in DP steels. The combination of element segregation, pressure drop, and thermal tensile stresses induced during laser welding results in a higher Hot Cracking susceptibility in TRIP steels as compared to DP steels.
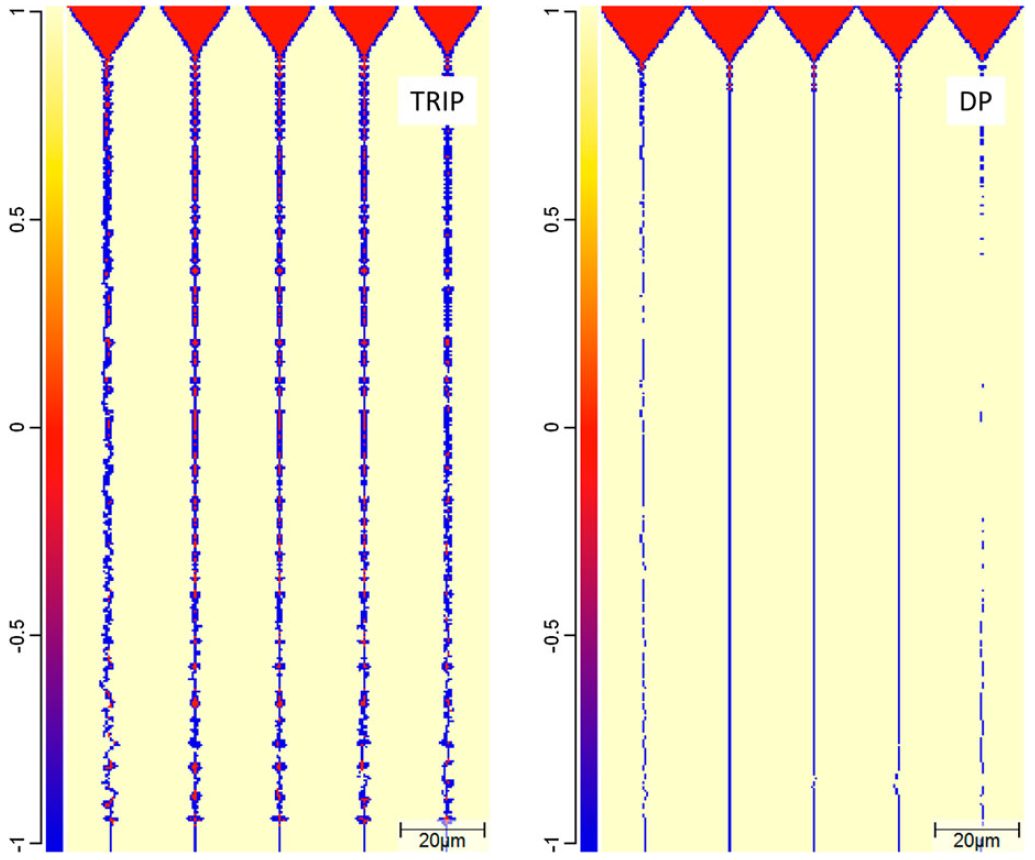
Figure 1: Phase distributions in the TRIP and the DP steel when the dendritic tips reach the weld centreline.G-4
Joining, Laser Welding
Optimizing weld morphology and mechanical properties of
laser welded Al-Si coated 22MnB5 by surface application of
colloidal graphite
Researchers at University of Waterloo discovered the microstructural effects of adding colloidal graphite to Al-Si coated 22MnB5 Press Hardened Steel.K-51 Laser welds were made on 1.5 mm thick Al-Si coated 22MnB5 PHS perpendicular to the rolling direction. Pure colloidal graphite suspended in isopropanol base was applied to the area being welded and the resulting graphite coating after evaporation ranged from 5 µm to 130 μm for testing. Parameters used for the weld are: 4kW power, 6m/min welding speed, beam diameter of 0.3 mm, and laser defocus of 6mm. Samples were then hot stamped by heating for 6 min to 930 ᵒC in a furnace and then water quenched at a cooling rate greater than 30 ᵒC/s.
Al-Si coating is excellent at preventing oxidation and decarburization of high strength steel at elevated temperatures. However, during welding there is diffusion of Al into the fusion zone which stabilizes ferrite at elevated temperature reducing the strength of the welded joint. Colloidal graphite coating decreases the Al content and increases C content of the fusion zone. As shown in Figure 1, The mechanism for reduction in Al content is due the graphite coating acting as an insulator to the Al-Si coating which then causes an ejection of the molten Al-Si coating from the surface. Figure 2 displays a proportional reduction of Al in the fusion zone with increasing graphite coating thickness up to 40 μm where after the reduction in Al is minimal. This is attributed to the initial reduction of Al being caused by the ejection of the molten Al-Si from underneath the graphite coating. Graphite coating greater than 40 µm does not aid in additional ejection of Al-Si and the Al-Si coating already diluted in the weld pool will not be removed.
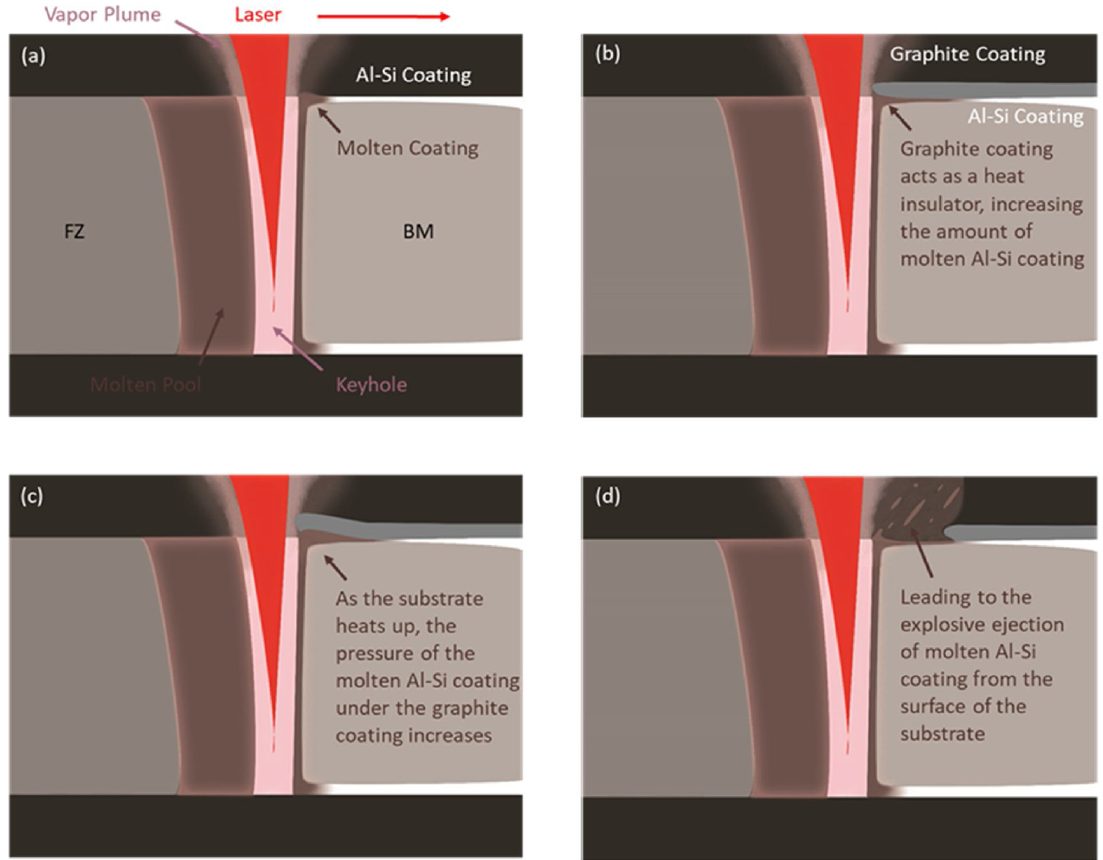
Figure 1: Al-Si ejection mechanism.K-51
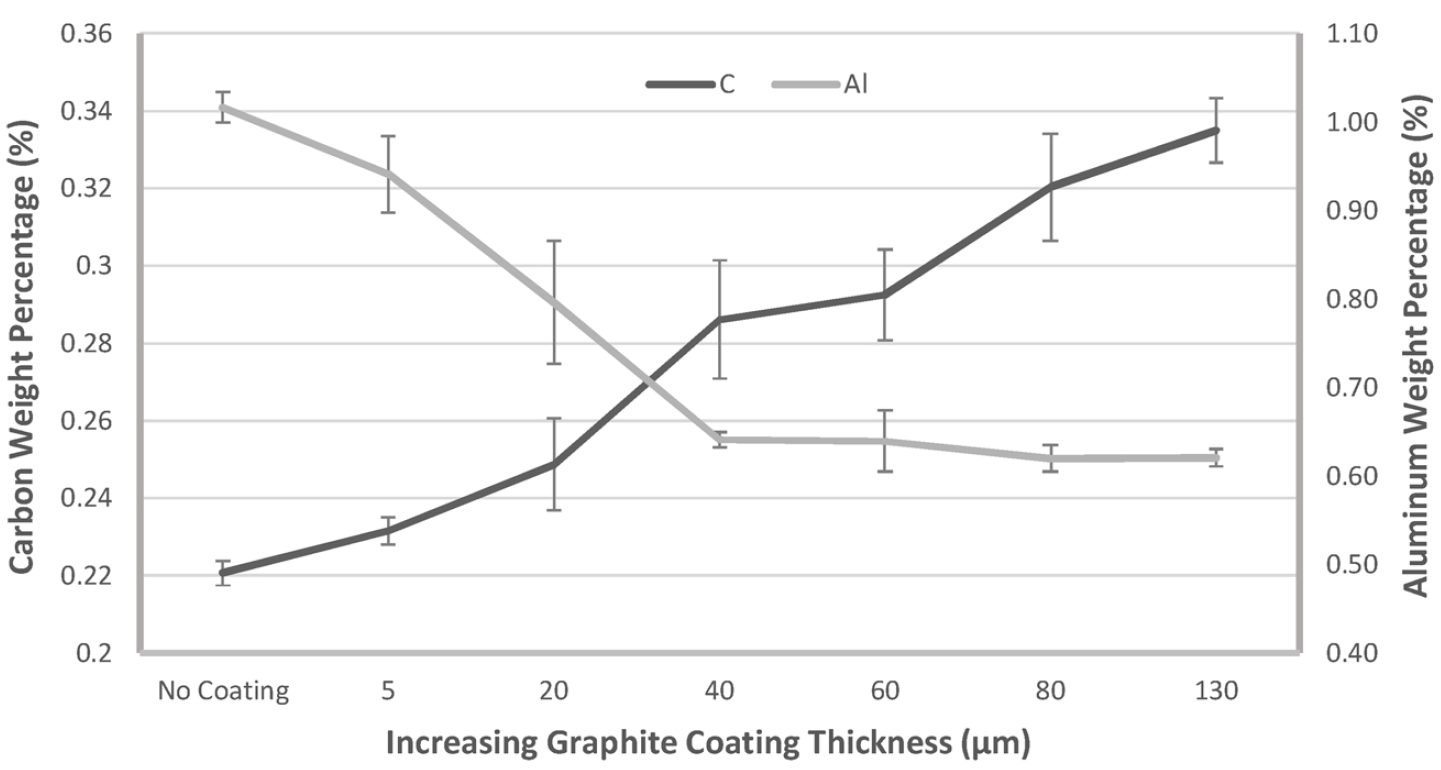
Figure 2: Al and C content in weld with increasing graphite thickness.K-51
Summary
Ferrite concentration in the fusion zone was reduced from approx. 40% with no graphite coating to approx. 2% with 130 μm graphite coating thickness (Figure 3). The increase in C content and reduction in Al content resulted in an increase in austenite being stabilized at elevated temperature rather than ferrite and therefore a larger percentage of martensite results after hot stamping. The average fusion zone hardness increased from 320 HV with no coating to 540 HV with 130 μm coating thickness (Figure 4). The weld strength of the sample with no graphite coating was 1249±15MPa whereas the weld strength with a coating of 130 µm was 1561±7MPa which matches the base metal (Figure 5). With an increase in graphite coating thickness there is an increase in weld strength that can eventually match the base metal strength.
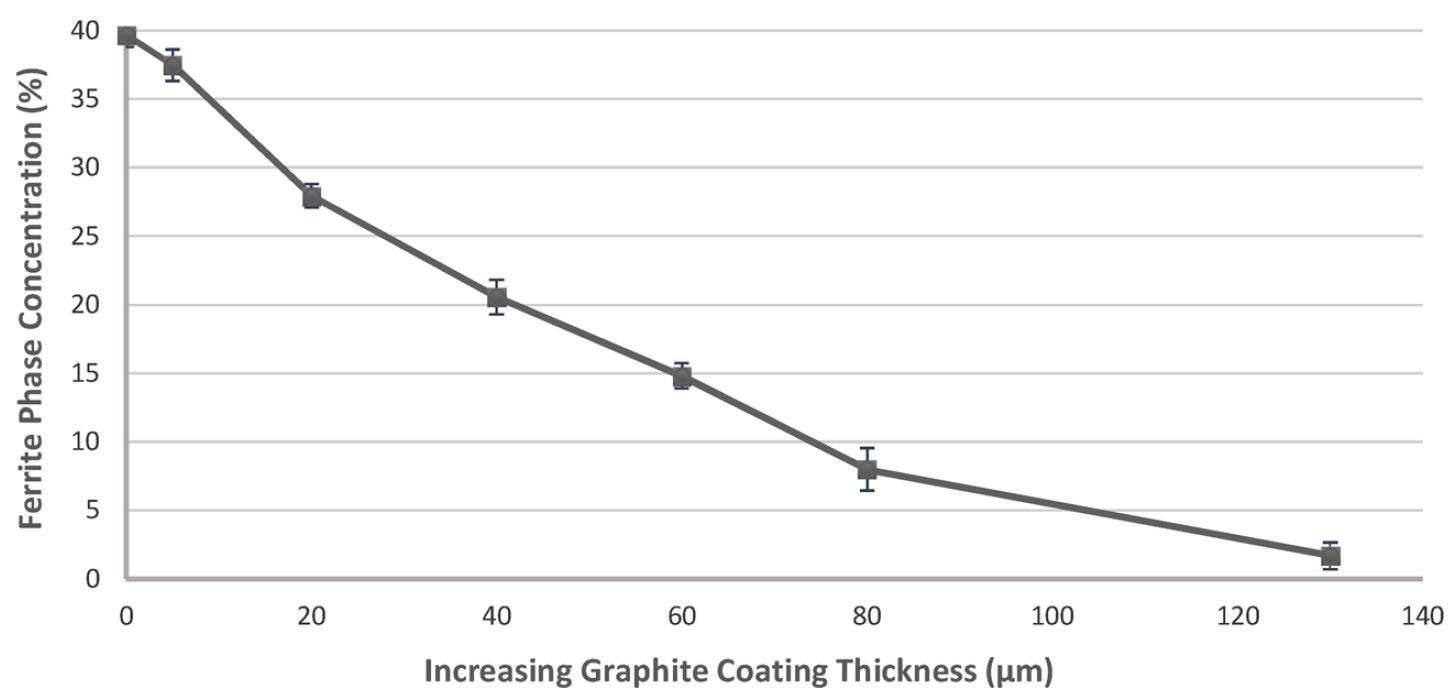
Figure 3: Ferrite concentration in weld.K-51
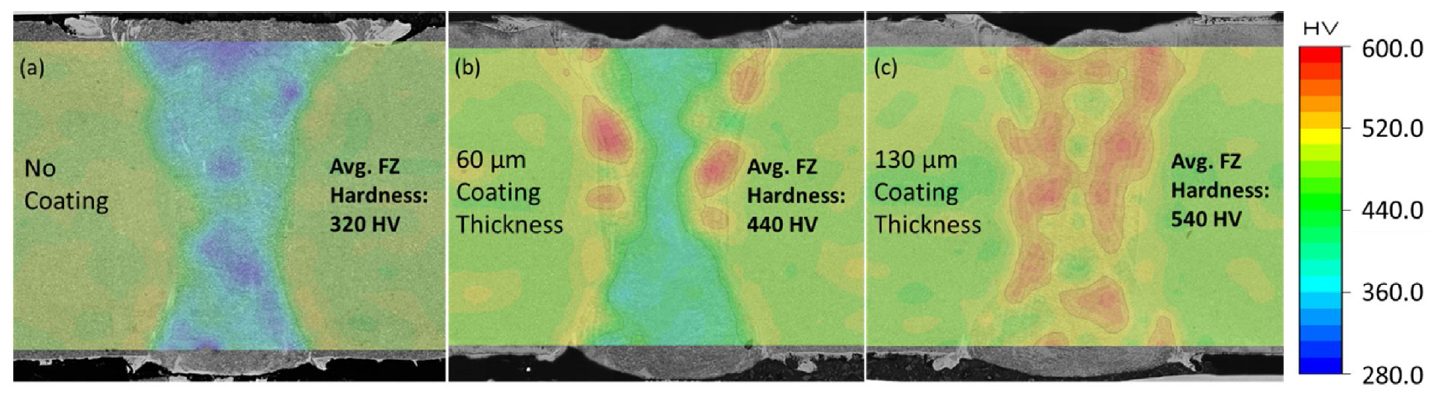
Figure 4: Fusion Zone Hardness vs. Graphite Thickness.K-51
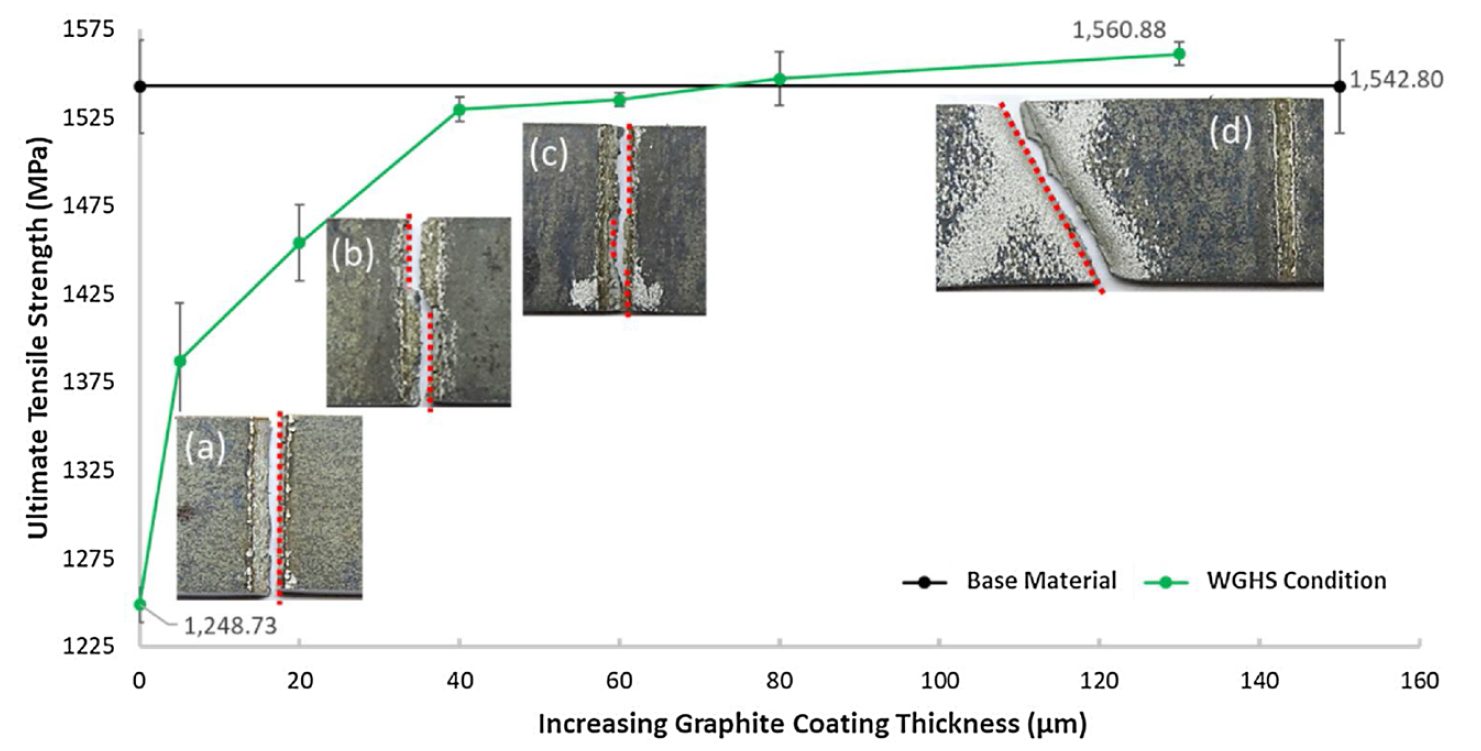
Figure 5: Weld strength vs. Graphite Thickness.K-51
Joining, Laser Welding
In this study by Shanghai Jiao Tong University and General Motors Company on liquid metal Embrittlement (LME)Z-11, hot dipped 1.2mm galvanized QP980 steel sheets with a 6 micron thick zinc rich coating on top of a 2 micron thick transition zone to the base metal were used. The laser welder is tilted 5º ahead of weld pool to avoid back reflection. The welding velocity was varied from 4-6 m/min and laser power from 4-6.5 kW. Referencing Table 1, Schedules #1–4 were intended to investigate effects of laser power on LME cracks using 6 m/min. schedules #4–6 varied velocity with the laser power staying constant at 4.5 kW. In addition, schedules #6 and #7 varied laser power at a relatively lower welding velocity of 4 m/min.
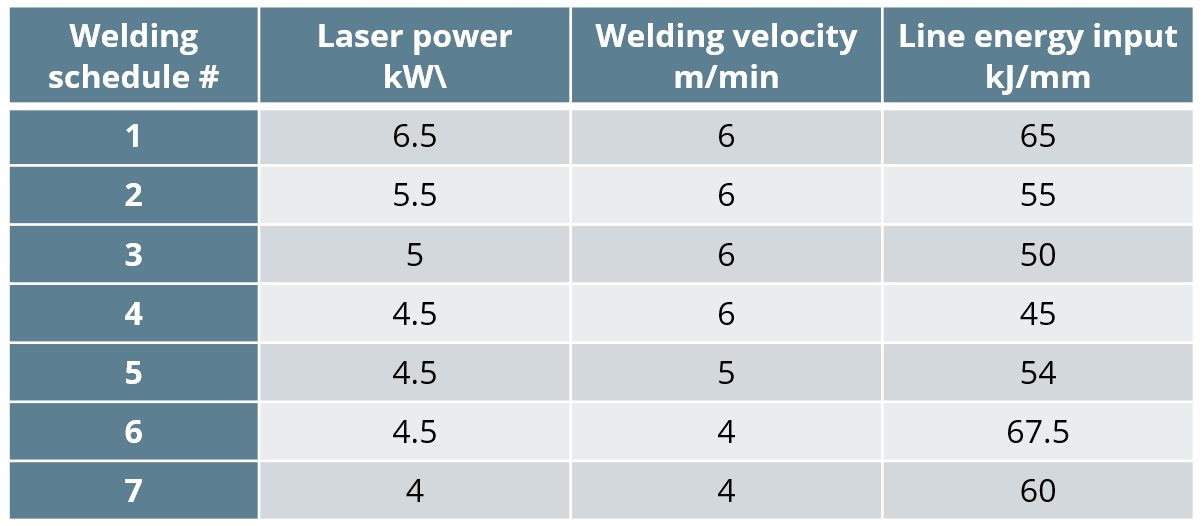
Table 1: Process Parameters.Z-11
Full penetration welds did not result in cracking while partial penetration welds with lower energy density did. The lowest energy density welds resulted in no cracking but the penetration was barely beyond the faying surface. Cracks resembles an inverse “Y” where the cracks initiated at the faying surface and propagated along the direction of solidification towards the weld centerline. Cracks at notch root were wider than centerline crack indicating grain boundary separation. The fracture method is characteristic of quasi-cleavage indicating that the grain boundaries were embrittled by Fe-Zn intermetallics. Crack initiation at the faying surface can be explained by the residual stresses that form highest at the faying surface during cooling. This stress concentration is eliminated with full penetration weld pass as well as in wide and shallow passes as seen in Figure 1.
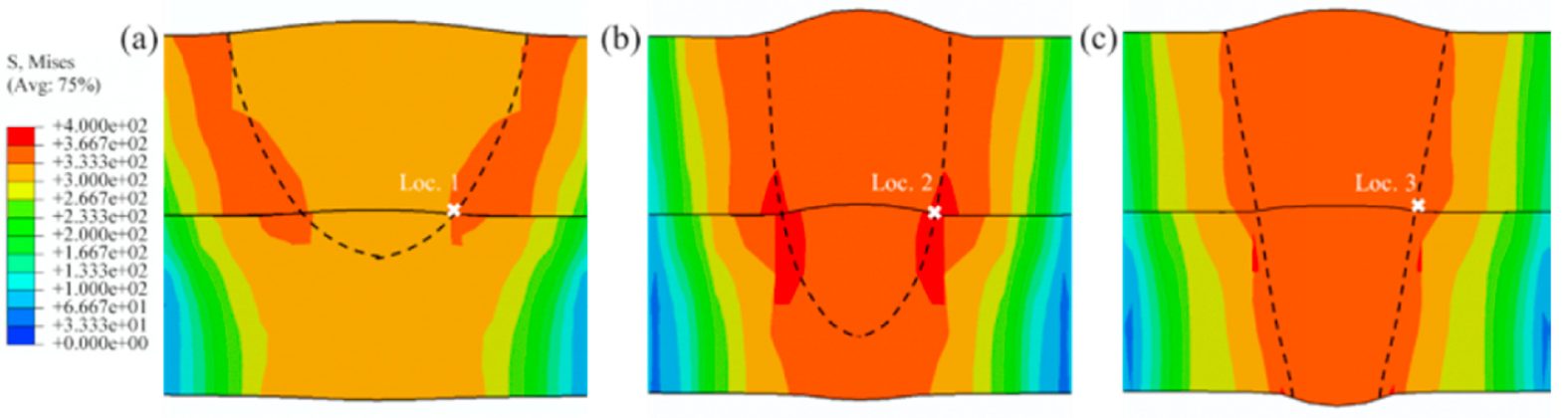
Figure 1: Von Mises Stress Distribution.Z-11
Because the process of laser welding is so short, the vaporized zinc and intermetallics do not have time to outgas completely. The liquid zinc diffuses along the austenite grain boundaries and stabilize ferrite given ferrite has a higher solubility of Zn compared to austenite. The remaining liquid Zn reacts with the ferrite to form the solid Γ-Fe3Zn10 which is a hard brittle intermetallic that can easily induce cracking. Another peritectic reaction occurs with Γ-Fe3Zn10 and liquid zinc forming another brittle intermetallic δ-FeZn10. The stabilized ferrite and intermetallics occur before austenite transform to martensite and remains even after this reaction occurs.
The formation of the intermetallics between the grain boundaries decreases ductility and with the combination of the high residual stress and stress concentration at the faying surface, the crack initiates and propagates. The cracking follows the grain growth to the center of the weld. Liquid Zn accumulates at the center of the weld and results in Fe-Zn intermetallics with low ductility that can eventually propagate cracking that occurs at the edge of the weld. Welds that result in a smaller cross-sectional area on the faying surface benefit from the reduction in vaporized Zn that cannot be outgassed while full penetration welds with keyhole mode can allow Zn to out gas from both the top and bottom of the weld as well as increased nugget size decreasing the Zn concentration to where brittle Fe-Zn phases do not form. Full penetration welds are recommended to reduce residual stress as well as allow sufficient outgassing of vaporized Zn in the weld pool.
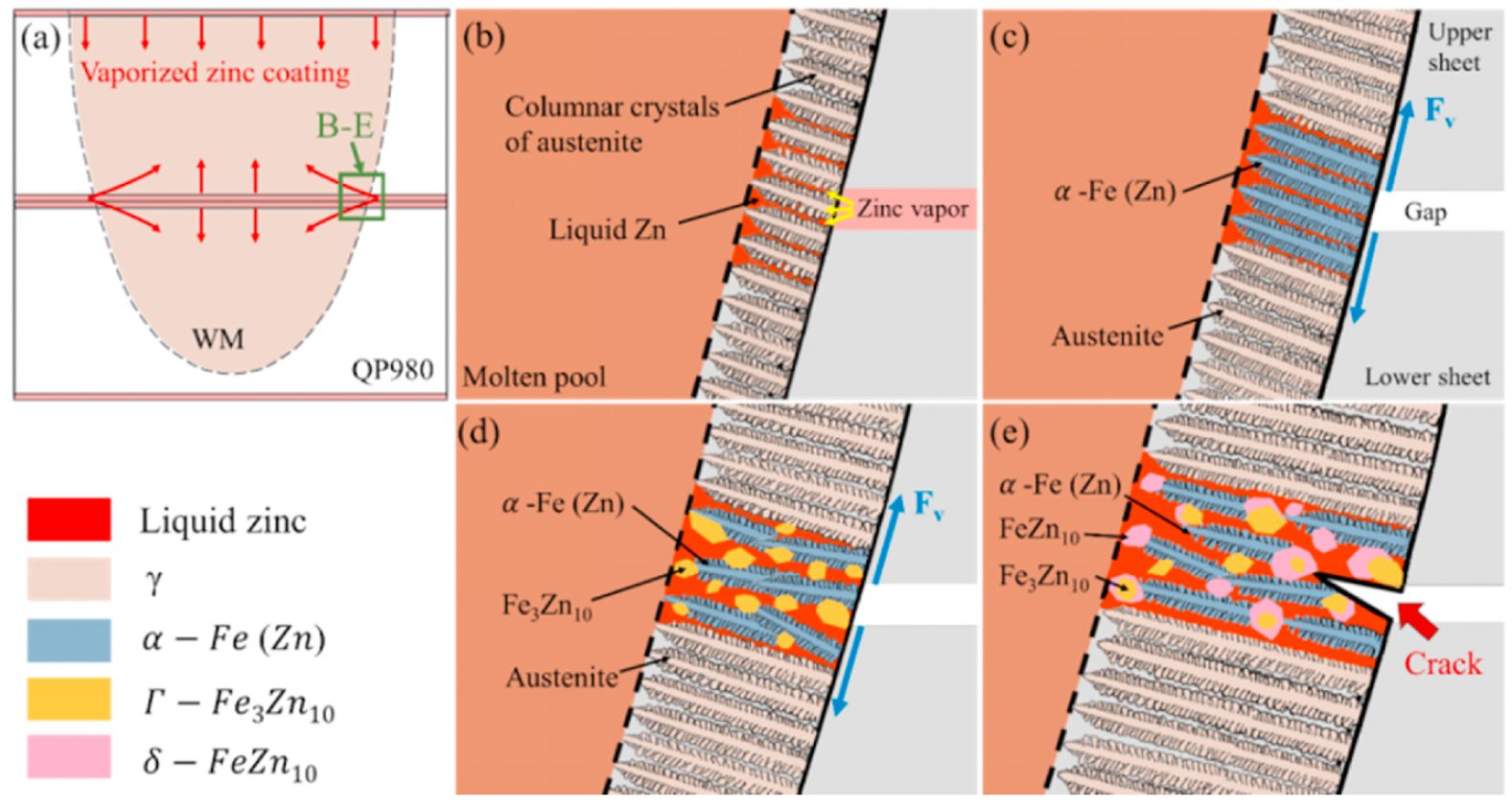
Figure 2: LME illustration.Z-11
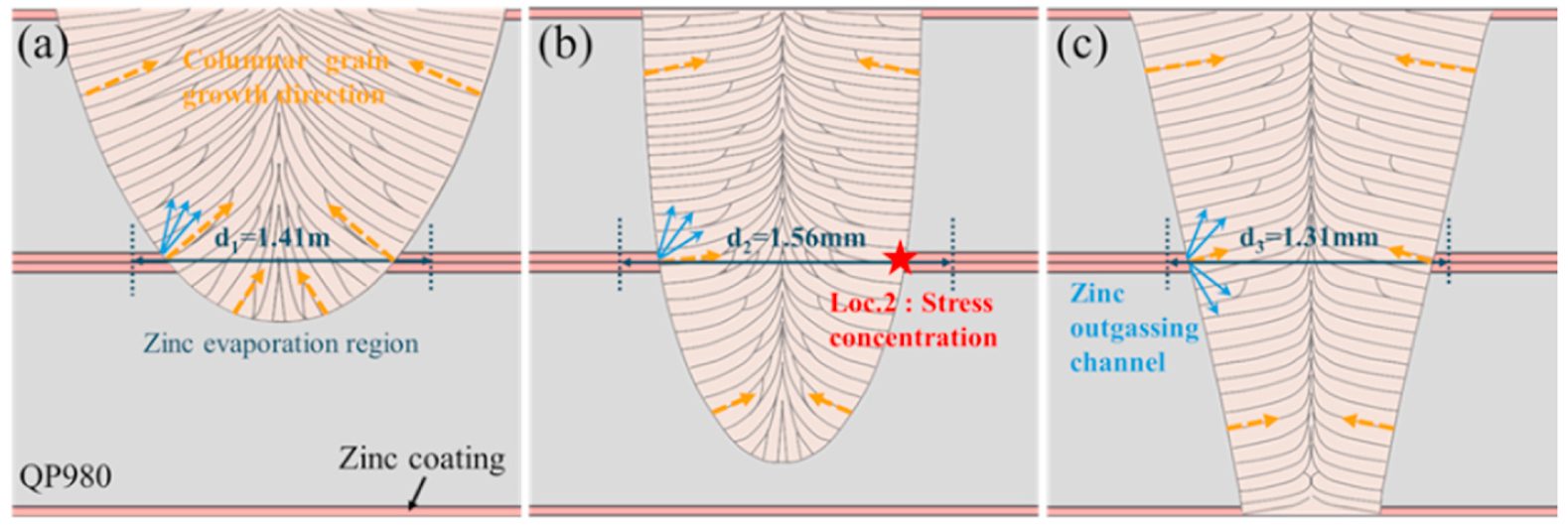
Figure 3: Zn diffusion.Z-11
Summary
LME cracks initiated at the weld notch root on the faying surface and propagated towards the center of the weld along the direction of columnar growth. Brittle intermetallic help induce cracking in the weld metal in addition to restraint from the weld joint. Full penetration welds were found to reduce Zn content from the weld in addition to reducing restraint as compared to partial penetration welds. The full penetration weld allowed for zinc to be outgassed from the weld on both sides reducing the Zn content in the weld to an acceptable level. Full penetration welds also reduced the residual stresses that formed during partial penetration welds due to the restraint on the root side of the weld.
Joining, Laser Welding, Press Hardened Steels
This studyR-25, conducted by the Centre for Advanced Materials Joining, Department of Mechanical & Mechatronics Engineering, University of Waterloo, and ArcelorMittal Global Research, utilized 2mm thick 22MnB5 steel with three different coating thicknesses, given in Table 1. The fiber laser welder used 0.3mm core diameter, 0.6mm spot size, and 200mm beam focal length. The trials were done with a 25° head angle with no shielding gas but high pressure air was applied to protect optics. Welding passes were performed using 3-6kW power increasing by 1 kW and 8-22m/min welding speed increasing by 4m/min. Compared to the base metal composition of mostly ferrite with colonies of pearlite, laser welding created complete martensitic composition in the FZ and fully austenized HAZ while the ICHAZ contained martensite in the intergranular regions where austenization occurred.
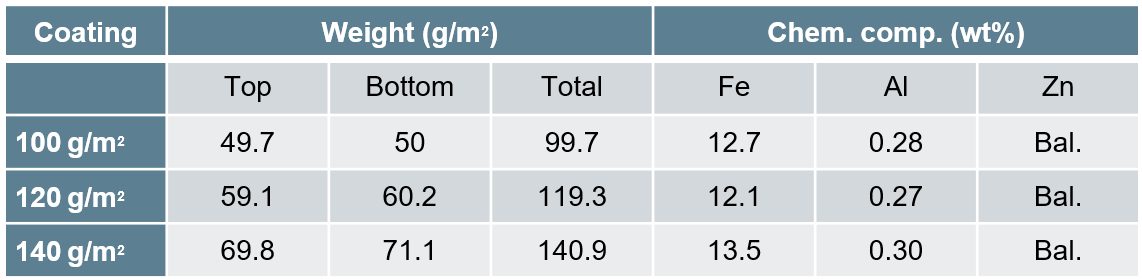
Table 1: Galvanneal Coatings.R-25
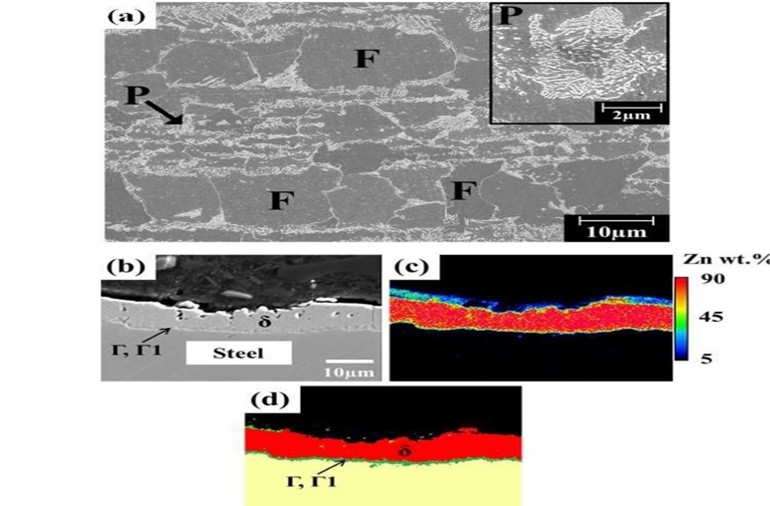
Figure 1: Base metal microstructure(P=pearlite, F=ferrite, Γ=Fe3Zn10, Γ1=Fe5Zn21 and δ=FeZn10).R-25
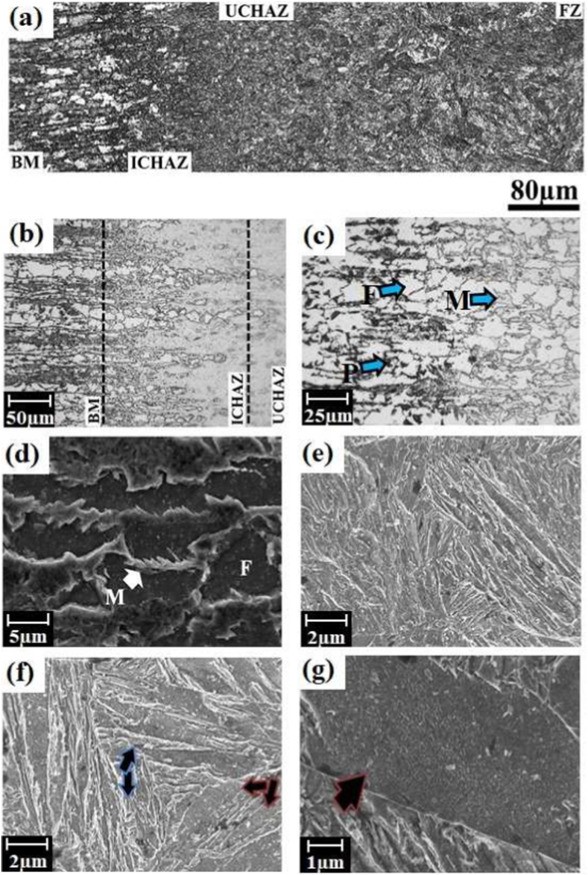
Figure 2: Welded microstructure — (a) overall view, (b) HAZ, (c) ICHAZ at low and (d) high magnifications, (e) UCHAZ (f) FZ, and (g) coarse-lath martensitic structure (where M; martensite, P: pearlite, F: ferrite).R-25
Given the lower boiling temperature of Zn at 900 °C as compared to Fe, the interaction of the laser with the Zn plasma that forms upon welding affects energy deliverance and depth of penetration. Lower coating weight of (100 g/m2) resulted in a larger process window as compared to (140 g/m2). Increased coating weight will reduce process window and need higher power and lower speeds in order to achieved proper penetration as shown in Figure 3 and Figure 4. Depth of penetration due to varying welding parameters was developed:
d=(H-8.6+0.08C)/(0.09C-4.8)
[d= depth of penetration(mm), H= heat input per unit thickness(J/mm2), C= coating weight(g/m2)]
Given the reduction in power deliverance, with an increase in coating weight there will be an expected drop in FZ and HAZ width. Regardless of the coating thickness, the HAZ maintained its hardness between BM and FZ. No direct correlation between coating thickness and YS, UTS, and elongation to fracture levels were observed. This is mainly due to the failure location being in the BM.
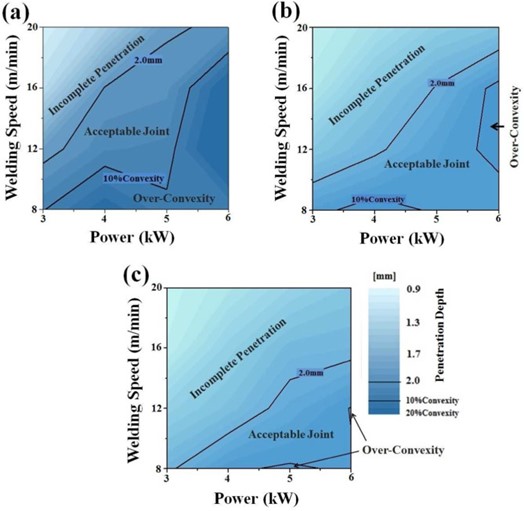
Figure 3: Process map of the welding window at coating weight of (a) 100 g/m2, (b) 120 g/m2, and (c) 140 g/m2.R-25
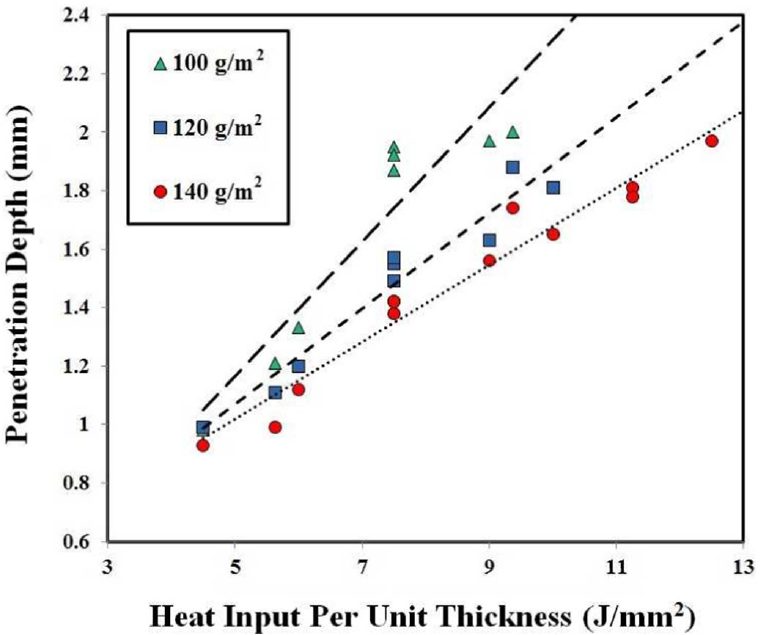
Figure 4: Heat input per unit thickness vs depth of penetration.R-25
Joining Dissimilar Materials, Laser Welding
Given the use of many different metals in the Body in White construction, it is important to understand the effects of dissimilar welding AHSS. Researchers at Indian Institute of Technology Madras in Chennai, India and Centre of Laser Processing of Materials in Hyderabad, India developed tests to study the resulting microstructure from laser welding 2.5 mm thick DP600 steel to 3 mm thick AA6061 aluminium alloy using a laser beam diameter of 1.5 mm.I-1 They discovered a softening in the steel HAZ due to a tempering effect and an increase in hardness in the aluminum HAZ due to the presence of aluminium intermetallic phases present. Maximum shear strength was observed when the thickness of intermetallics was reduced to 8-11 microns. They concluded that best quality welds were made under power densities and interaction times of 1.98kW/mm2, 0.15s and 2.26 kW/mm2, 0.187s.
The laser power was varied from 3 kW to 4.5 kW and the scanning speed of 8 mm/s, 10 mm/s, and 12 mm/s. Power density and interaction time were two parameters they used to compare trials where:
Power density (Pd) = |
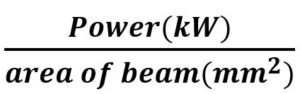 |
and
interaction time (It) = |
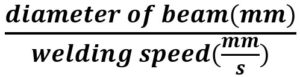 |
The resulting welding parameters are shown in Table 1 below. Figure 1 shows the microstructure of the fusion boundary and HAZ on the DP600 side of the welded joint. Figure 2 shows the microstructure of the weld interface on the AA 6061 side. Figure 3 displays the hardness data with (a) representing 3.5 kW and 10 mm/s, (b) representing 3.5 kW and 8 mm/s, and (c) representing 4 kW and 8 mm/s. Figure 4 represents the Shear Stress-Strain of the welds given different IMC thickness.
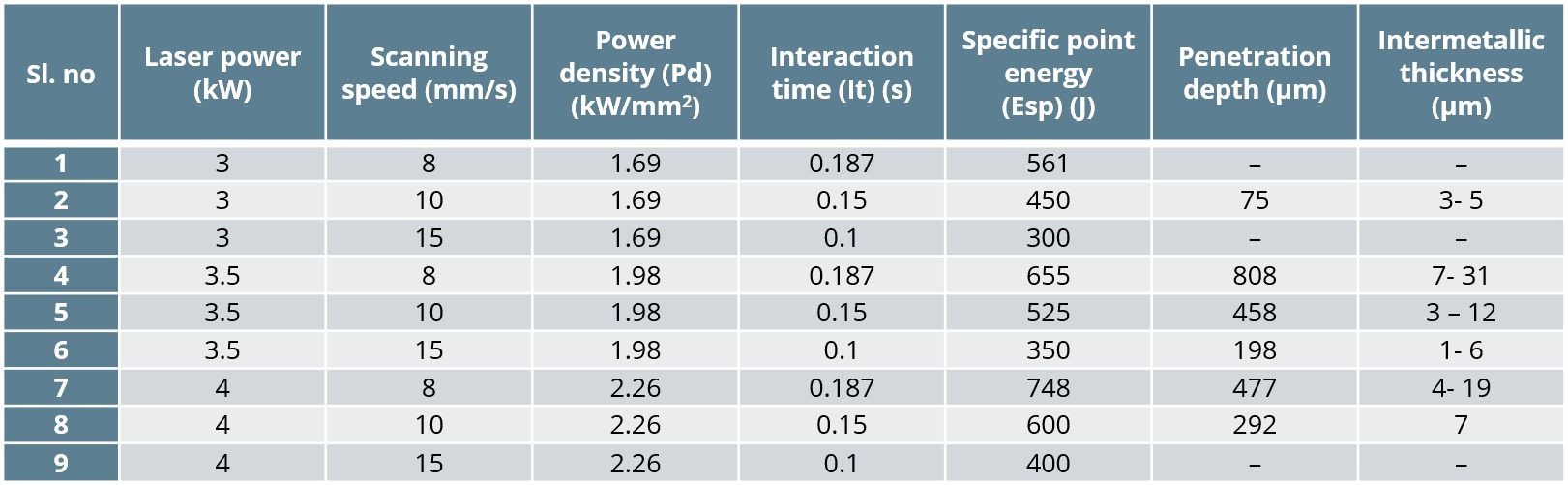
Table 1: Welding Parameters.I-1
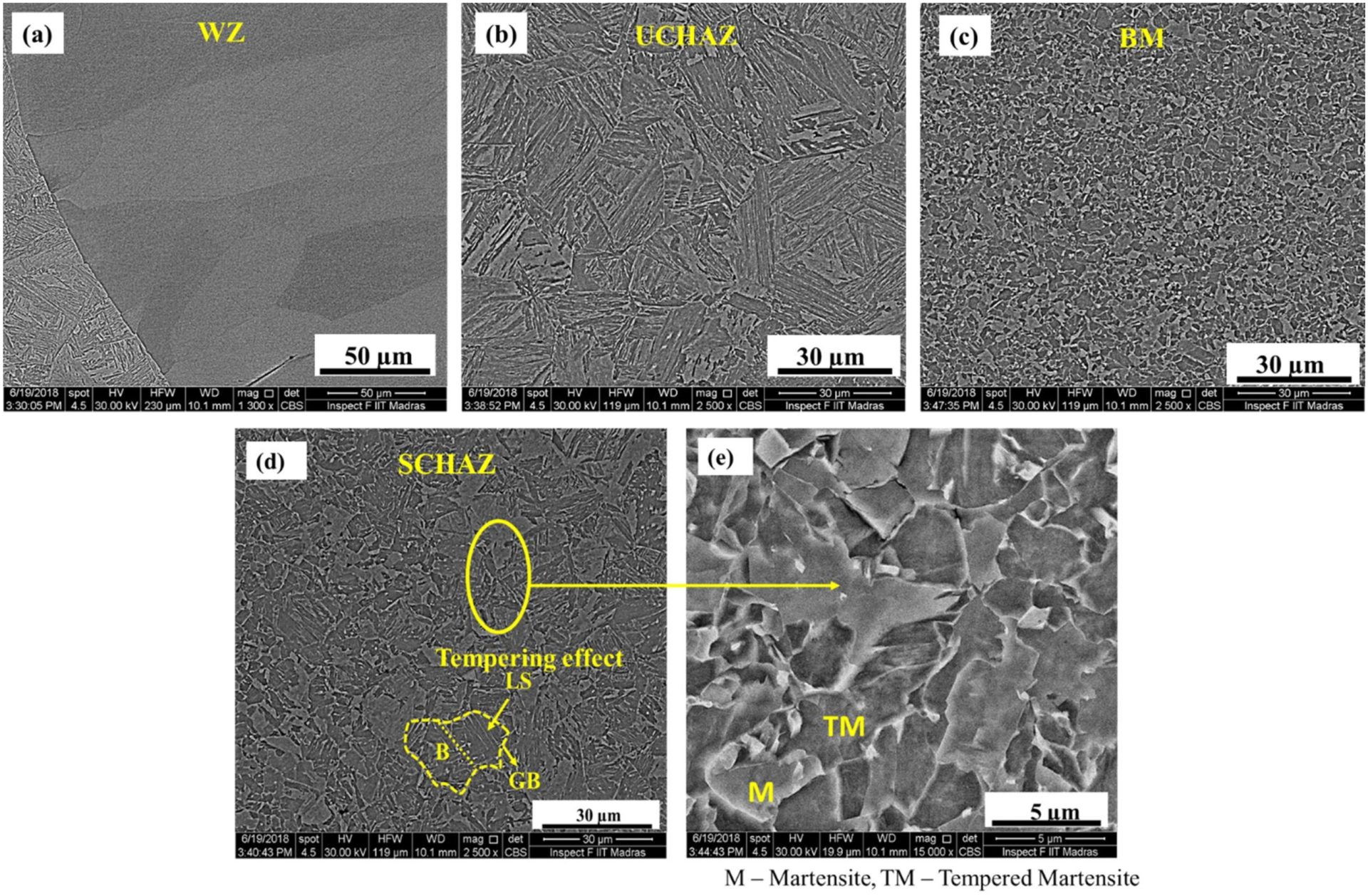
Figure 1: Weld Metal, DP 600 Base Metal and HAZ microstructure.I-1
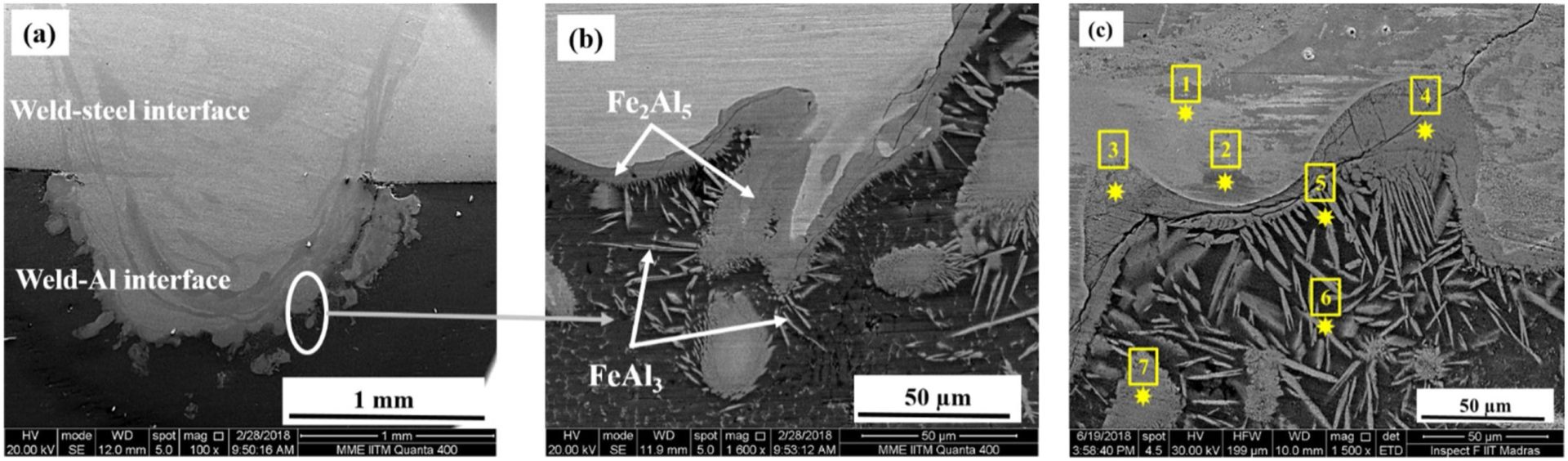
Figure 2: Fe-Al interface microstructure.I-1
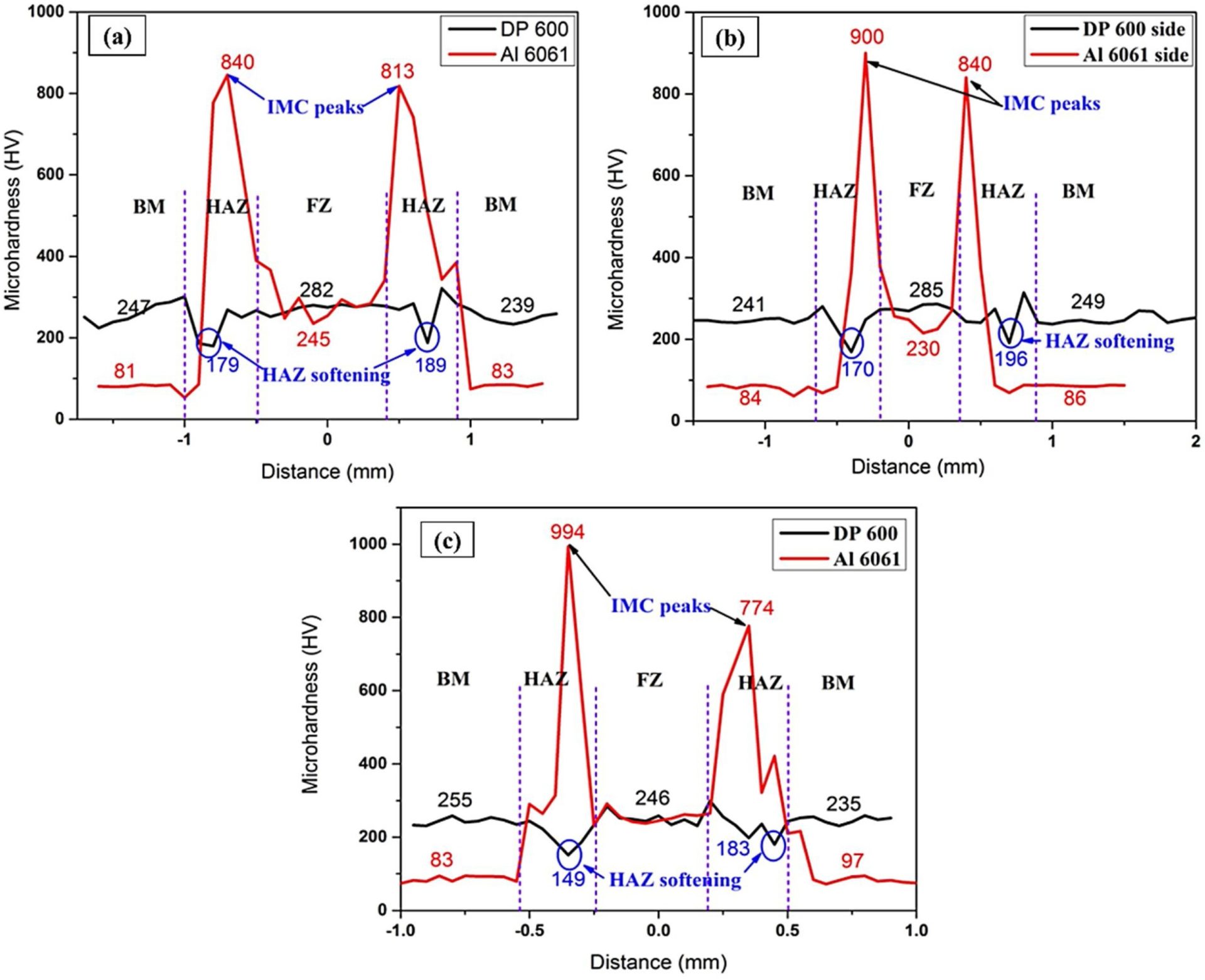
Figure 3: Microhardness Plot.I-1
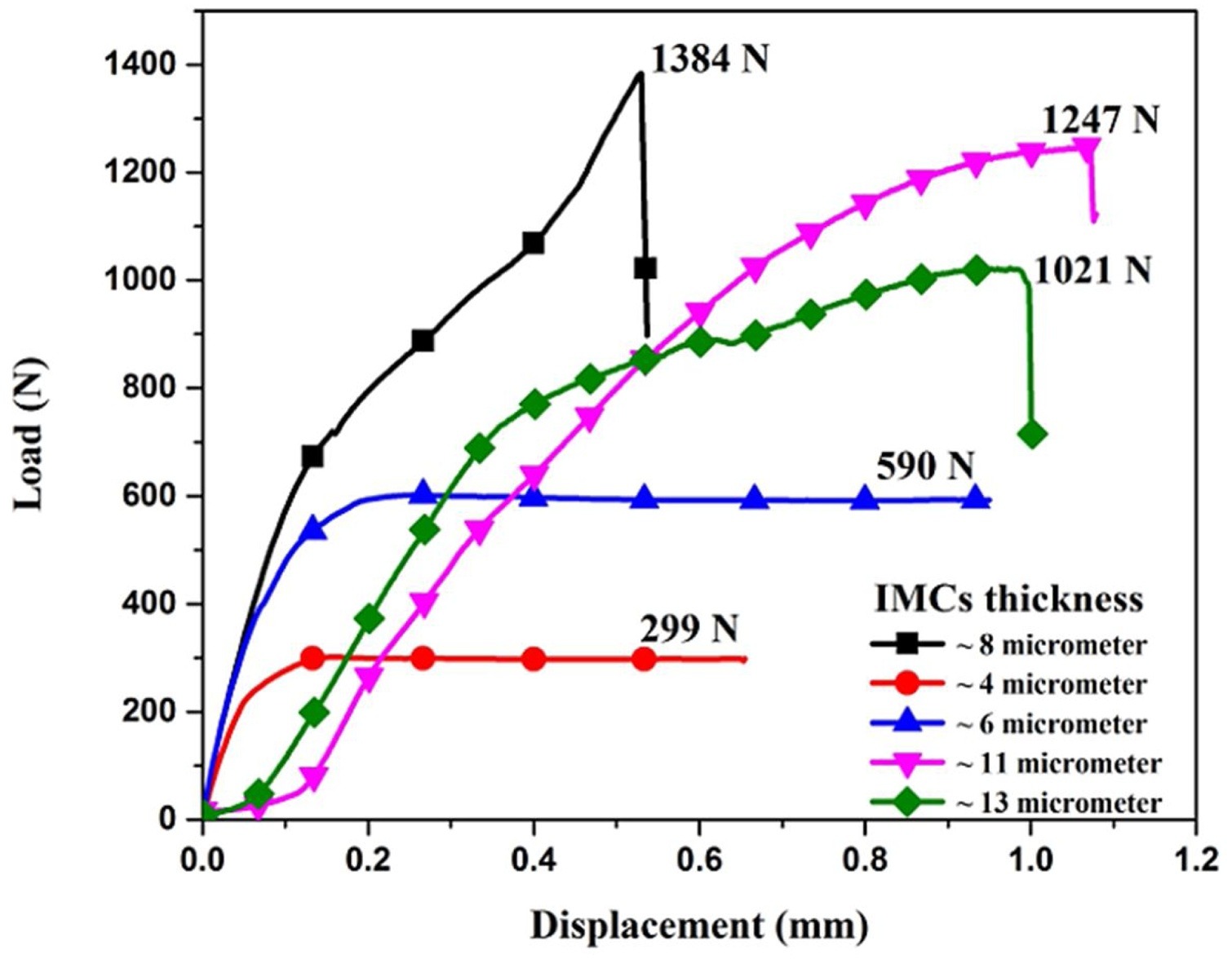
Figure 4: Load vs. Displacement.I-1