Blog, homepage-featured-top, main-blog
Equipment, Responsibilities, and Property Development Considerations When Deciding How A Part Gets Formed
Automakers contemplating whether a part is cold stamped or hot formed must consider numerous ramifications impacting multiple departments. Over a series of blogs, we’ll cover some of the considerations that must enter the discussion.
The discussions relative to cold stamping are applicable to any forming operation occurring at room temperature such as roll forming, hydroforming, or conventional stamping. Similarly, hot stamping refers to any set of operations using Press Hardening Steels (or Press Quenched Steels), including those that are roll formed or fluid-formed.
Equipment
There is a well-established infrastructure for cold stamping. New grades benefit from servo presses, especially for those grades where press force and press energy must be considered. Larger press beds may be necessary to accommodate larger parts. As long as these factors are considered, the existing infrastructure is likely sufficient.
Progressive-die presses have tonnage ratings commonly in the range of 630 to 1250 tons at relatively high stroke rates. Transfer presses, typically ranging from 800 to 2500 tons, operate at relatively lower stroke rates. Power requirements can vary between 75 kW (630 tons) to 350 kW (2500 tons). Recent transfer press installations of approximately 3000 tons capacity allow for processing of an expanded range of higher strength steels.
Hot stamping requires a high-tonnage servo-driven press (approximately 1000 ton force capacity) with a 3 meter by 2 meter bolster, fed by either a roller-hearth furnace more than 30 m long or a multi-chamber furnace. Press hardened steels need to be heated to 900 °C for full austenitization in order to achieve a uniform consistent phase, and this contributes to energy requirements often exceeding 2 MW.
Integrating multiple functions into fewer parts leads to part consolidation. Accommodating large laser-welded parts such as combined front and rear door rings expands the need for even wider furnaces, higher-tonnage presses, and larger bolster dimensions.
Blanking of coils used in the PHS process occurs before the hardening step, so forces are low. Post-hardening trimming usually requires laser cutting, or possibly mechanical cutting if some processing was done to soften the areas of interest.
That contrasts with the blanking and trimming of high strength cold-forming grades. Except for the highest strength cold forming grades, both blanking and trimming tonnage requirements are sufficiently low that conventional mechanical cutting is used on the vast majority of parts. Cut edge quality and uniformity greatly impact the edge stretchability that may lead to unexpected fracture.
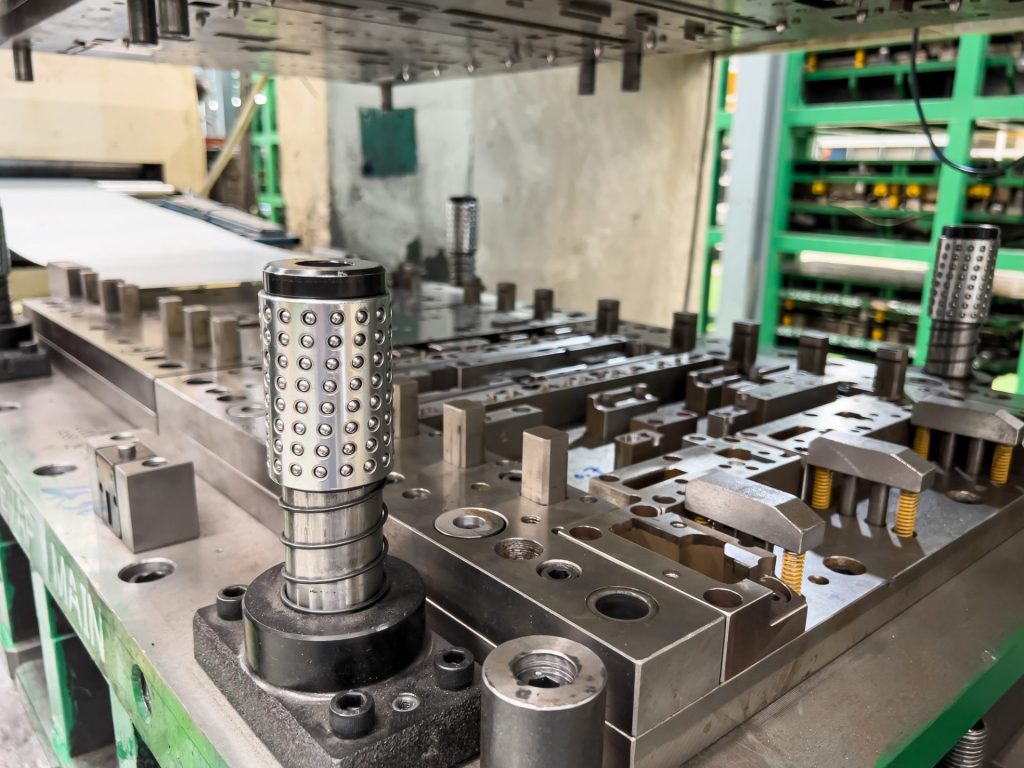
Responsibilities
Most cold stamped parts going into a given body-in-white are formed by a tier supplier. In contrast, some automakers create the vast majority of their hot stamped parts in-house, while others rely on their tier suppliers to provide hot stamped components. The number of qualified suppliers capable of producing hot stamped parts is markedly smaller than the number of cold stamping part suppliers.
Hot stamping is more complex than just adding heat to a cold stamping process. Suppliers of cold stamped parts are responsible for forming a dimensionally accurate part, assuming the steel supplier provides sheet metal with the required tensile properties achieved with a targeted microstructure.
Suppliers of hot stamped parts are also responsible for producing a dimensionally accurate part, but have additional responsibility for developing the microstructure and tensile properties of that part from a general steel chemistry typically described as 22MnB5.
Property Development
Independent of which company creates the hot formed part, appropriate quality assurance practices must be in place. With cold stamped parts, steel is produced to meet the minimum requirements for that grade, so routine property testing of the formed part is usually not performed. This is in contrast to hot stamped parts, where the local quench rate has a direct effect on tensile properties after forming. If any portion of the part is not quenched faster than the critical cooling rate, the targeted mechanical properties will not be met and part performance can be compromised. Many companies have a standard practice of testing multiple areas on samples pulled every run. It’s critical that these tested areas are representative of the entire part. For example, on the top of a hat-section profile where there is good contact between the punch and cavity, heat extraction is likely uniform and consistent. However, on the vertical sidewalls, getting sufficient contact between the sheet metal and the tooling is more challenging. As a result, the reduced heat extraction may limit the strengthening effect due to an insufficient quench rate.
For more information, see our Press Hardened Steel Primer to learn more about PHS grades and processing!
Thanks are given to Eren Billur, Ph.D., Billur MetalForm for his contributions to the Equipment section, as well as many of the webpages relating to Press Hardening Steels at www.AHSSinsights.org.
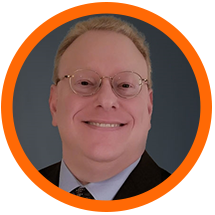
Danny Schaeffler is the Metallurgy and Forming Technical Editor of the AHSS Applications Guidelines available from WorldAutoSteel. He is founder and President of Engineering Quality Solutions (EQS). Danny wrote the monthly “Science of Forming” and “Metal Matters” column for Metalforming Magazine, and provides seminars on sheet metal formability for Auto/Steel Partnership and the Precision Metalforming Association. He has written for Stamping Journal and The Fabricator, and has lectured at FabTech. Danny is passionate about training new and experienced employees at manufacturing companies about how sheet metal properties impact their forming success.
Blog, homepage-featured-top, main-blog
Advanced High-Strength Steel (AHSS) products have significantly different forming characteristics and these challenge conventional mechanical and hydraulic presses. Some examples include the dramatically higher strength of these new steels resulting in higher forming loads and increased springback. Also, higher contact pressures cause higher temperatures at the die-steel interface, requiring high performance lubricants and tool steel inserts with advanced coatings.
These and other challenges lead to issues with the precision of part formation and stamping line productivity. Using a servo-driven press is one approach to address the challenges of forming and cutting AHSS grades. Recent growth in the use of servo presses in the automotive manufacturing industry parallels the increased use of AHSS in the body structure of new automobiles. Click to read more about the Characteristics of Servo Presses and their Advantages.
Figure 1 shows the difference between the available motions of flywheel-driven mechanical presses verses servo driven mechanical presses. The slide motion of the servo press can be programmed for more parts per minute, decreased drawing speed to reduce quality errors, or dwelling or re-striking at bottom dead center to reduce springback.

Figure 1: Comparison of Press Signatures in Fixed Motion Mechanical Presses and Free-Motion Servo-Driven Presses.M-3
Press Force and Press Energy
Categorizing both mechanical and hydraulic presses requires three different capacities or ratings – force, energy, and power. Historically, when making parts out of mild steel or even some HSLA steels, using the old rules-of-thumb to estimate forming loads was sufficient. Once the tonnage requirements and some processing requirements were known, stamping could occur in whichever press met those minimum tonnage and bed size requirements.
In these cases, press capacity (for example, 1000 kN) is a suitable number for the mechanical characteristics of a stamping press. Capacity, or tonnage rating, indicates the maximum force that the press can apply without damaging its components, like the machine frame, slide-adjusting mechanisms, pitman (connection rods) or main gear bushings.
A servo press transmits force (not energy) the same way as the equivalent conventional press (mechanical or hydraulic). However, the amount of force available throughout the stroke depends on whether the press is hydraulic or mechanically driven. Hydraulic presses can exert maximum force during the entire stroke as tonnage generation occurs via hydraulic fluid, pumps, and cylinders. Mechanical presses exert their maximum force at a specific distance above bottom dead center (BDC), usually defined at 0.5 inch. At increased distances above bottom dead center, the loss of mechanical advantage reduces the tonnage available for the press to apply. This phenomenon is known as de-rated tonnage, and it applies to conventional mechanical presses as well as servo-mechanical presses. Figure 2 shows a typical press-force curve for a 600-ton mechanical press. In this example, when the press is approximately 3 inches off BDC, the maximum tonnage available is only 250 tons – significantly less than the 600-ton rating.

Figure 2: The Press-Force curve shows the maximum tonnage a mechanical press can apply based on the position of the slide relative to the bottom dead center reference distance. This de-rated tonnage applies to both conventional mechanical presses as well as servo-mechanical presses.E-2
Press energy reflects the ability to provide that force over a specified distance (draw depth) at a given cycle rate. Figure 3 shows a typical press-energy curve for the same 600-ton mechanical press. The energy available depends on the size and speed of the flywheel, as well as the size of the main drive motor. As the flywheel rotates faster, the amount of stored energy increases, reflected in the first portion of the curve. The cutting or forming process consumes energy, which the drive motor must replenish during the nonworking part of the stroke. At faster speeds, the motor has less time to restore the energy. If the energy cannot be restored in time, the press stalls. The graph illustrates how the available energy of the press diminishes to 25% of the rated capacity when accompanied by a speed reduction from 24 strokes per minute to 12 strokes per minute.

Figure 3: A representative press-energy curve for a 600 ton mechanical press. Reducing the stroke rate from 24 to 12 reduces available energy by 75%.E-2
Case Study: Press Force and Press EnergyH-3
Predicting the press forces needed initially to form a part is known from a basic understanding of sheet metal forming. Different methods are available to calculate drawing force, ram force, slide force, or blankholder force. The press load signature is an output from most forming-process development simulation programs, as well as special press load monitors. The topic of press force predictions will be covered in this Blog in the months ahead.
Most structural components include design features to improve local stiffness. Typically, forming of the features requiring embossing processes occurs near the end of the stroke near Bottom Dead Center. Predicting forces needed for such a process is usually based on press shop experiences applicable to conventional steel grades. To generate comparable numbers for AHSS grades, forming process simulation is recommended.
In Citation H-3, stamping simulations evaluated the forming of a cross member having a hat-profile with an embossment formed at the end of the stroke (Figure 4). The study simulated press forces and press energy involved for drawing and embossing a channel section from four steel grades approximately 1.5 mm thick: mild steel, HSLA 250/350, HSLA 350/450, and DP 350/600. Figures 5A and 5B clearly show that the embossing phase rather than the drawing phase dominates the total force and energy requirements, even though the punch travel for embossing is only a fraction of the drawing depth.

Figure 4: Cross section of a component having a longitudinal embossment to improve local stiffness.H-3
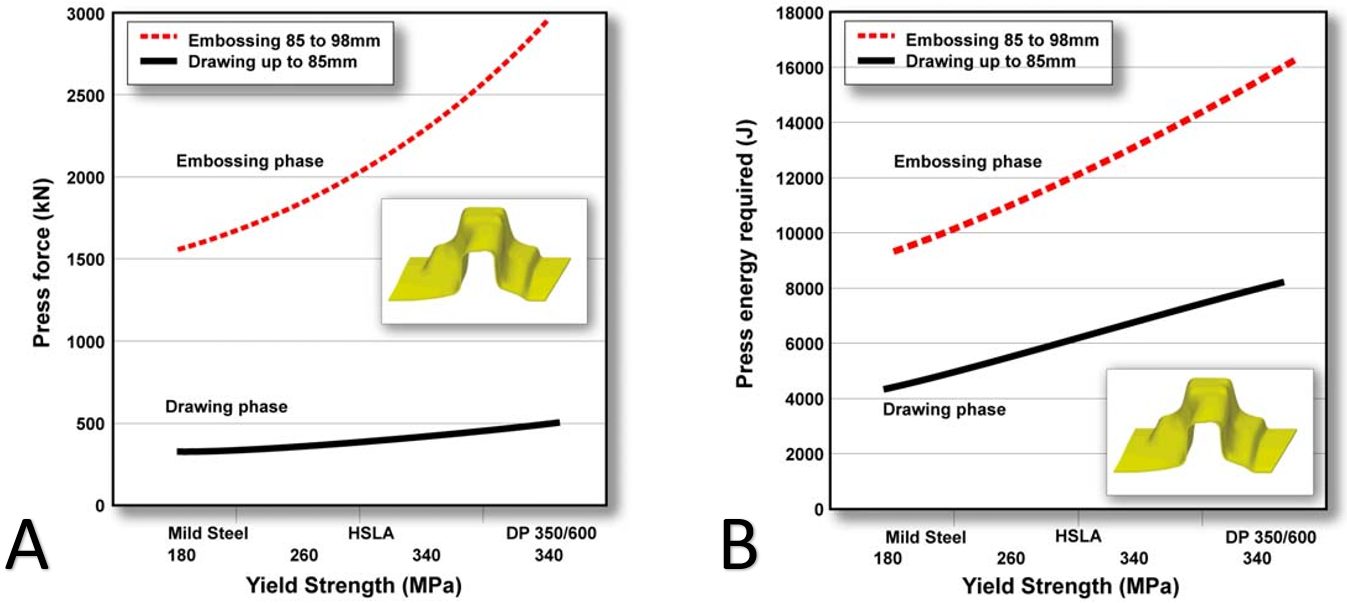
Figure 5: Embossing requires significantly more (A) force and (B) energy than drawing, even though the punch travel in the embossing stage is much smaller.H-3
Figures 6 and 7 highlight the press energy requirements, showing the greater energy required for higher strength steels. The embossment starts to form at a punch displacement of 85 mm, indicated by the three dots in Figure 6. The last increment of punch travel to 98 mm requires significantly higher energy, as shown in Figure 7. Note that compared with mild steel, the dual phase steel grade requires significantly more energy to form the part to home with the 98 mm travel.

Figure 6: Energy needed to form the component increases for higher strength steel grades. Forming the embossment begins at 85 mm of punch travel, indicated by the 3 dots.H-3

Figure 7: Additional energy required to form the embossment increases for higher strength steel grades.H-3
It is not only embossments that require substantially more force and energy at the end of the stroke. Stake beads for springback control engage late in the stroke to provide sidewall stretch. Depending on the design of the forming process, the steel into which the stake beads engage may have passed through conventional draw beads for metal flow control, and therefore are work-hardened to an even higher strength. This leads to greater requirements for die closing force and energy. Certain draw-bead geometries which demand different closing conditions around the periphery of the stamping also may influence closing force and energy requirements.
A more detailed Press Requirements article contains additional information and case studies. Read it here >>>
Press Requirements
For a stamping operation, knowing the press tonnage required to produce a part is essential. Running a part in a press without enough capacity can cause press fatigue, damage and significant downtime. Also, an operation that must run a part in a much larger press than anticipated in order to get enough tonnage will see decreases in throughput and efficiency, resulting in increased cost. Therefore, it is critical to be able to predict a part’s stamping tonnage requirements early in the design phase of the component and the stamping process. This is even more important with the continual developments in Advanced High-Strength Steels (AHSS) that the steel industry has made. These steels offer similar formability of traditional high-strength steels with twice the strength or more, as shown in Figure 1. In this article, I will explain why typical rules of thumb that appeared to work in the past are no longer applicable and touch on how the automotive and steel industries are addressing the changes.

Figure 1: AHSS add to the spectrum of options available for automotive body construction.A-69
Tonnage Requirements and Press Capacity
When discussing the press capacity requirements, it is typical to mainly refer to ‘tonnage’ as the measurable needed. Tonnage is the peak load required during a stamping operation. The tonnage rating for a press refers to the peak load that the press can safely deliver without causing damage to the press frame, ram, bushings, etc. For a mechanical press, the peak tonnage is only available at the bottom of the stroke.
Besides peak load requirements, it is also important to understand the total energy required to form a part. It is typical for the force available from a mechanical press just a few inches off bottom to be 50% of the press tonnage rating. For drawing operations that may start several inches off bottom, it is important to predict the part tonnage requirements through the entire stroke and to compare that with the force curve from the press manufacturer. Integrating this press force curve over the entire stroke is a measure of the total energy capacity of the press. Many times, when a press stalls at bottom dead center, the issue may not be that the peak load of the press was exceeded, rather the full amount of energy that was stored in the flywheel had been expended. More information about press force and press energy are found on our page highlighting Press Requirements.
A few years ago, I saw an example of energy vs. tonnage requirements. The part was a relatively thick gage AHSS frame bracket. The design was a simple flanged hat section. In plan view, the part was only about 6-inch x 6-inch with the depth of the hat being about 4-inch. Based on the tonnage require to flange, trim and pierce a hole, the part should have easily been able to fit in a small 600-ton press. However, in order to have enough energy to produce the part, this small die was placed in the center of the 180-inch bed of a 1200-ton press. Not only was it ergonomically difficult for the operator, but the large press burden rate was much higher, and the speed was much slower than that of the smaller press, causing a significant cost increase.
Furthermore, it is good to know how off-center the load required to form a part is. Obviously, the die setter will center the die under the ram. However, most parts are not symmetric, causing the load going into the ram, bushings and press frame to be biased to one side or the other. This becomes more exaggerated in a large transfer press that may have a major draw operation at the entry end and a minor trim operation at the exit end.
Putting this all together, having the ability to predict not only the peak load required to form a part, but also the total energy through the stroke and the off-center bias gives us the ability to design a stamping process that is safe and efficient. Also, in lean manufacturing terms, a predicted through-stoke force curve provides a good baseline defining the basic condition of the die. Comparing this to actual force curves and evaluating any changes over time will help to develop preventive maintenance schedules and will offer many new capabilities with servo presses as they become more prevalent.
Conventional Rule-of-Thumb Calculations Lead to Inaccurate Press Tonnage Predictions, Especially in AHSS
In 1989, I worked for an automotive stamping supplier as a college intern. One of my tasks was to do basic calculations of part size and tonnage requirements that were used by the process engineers to design the die process and quote the manufacturing and die costs to produce the part. The rule of thumb estimates used at that time were simple calculations for the peak load. Tonnage for trim and pierce operations were dependent on the length of line of trim, material thickness and the shear strength of the material. Tonnage for forming operations were dependent on the size of the form, material thickness and material tensile strength. These calculations typically over-predicted the tonnage requirement, but because of the relative low strength steels used, as compared to today’s AHSS, most times, the limiting factor was the overall part size that dictated the size of the press to be used rather than the tonnage requirement.
So why do we hear today that these same rules of thumb do not work, or worse, that they now under predict the tonnage requirements? To understand this, let us look at a few guidelines I used over 30 years ago.
For piercing a hole: Tonnage = d * t * 80 Equation 1
In this equation d is the punch diameter in inches, t is the material thickness in inches, and it gives the tonnage in tons. This was a very simple and effective way to estimate the tonnage of all the holes pierced. Let us look at how this rule of thumb was derived. The equation is a simplification of the fact that the actual calculation is the length of line doing the work, in this case the circumference of a circle, multiplied by the material thickness and the material’s shear strength (ꚍ). The generic equation for any type of piercing or trimming is Tonnage = P * t * ꚍ where P is the perimeter or length of line of the trim, t is the material thickness and ꚍ is the shear strength of the material. A typical estimate for the shear strength (ꚍ) is 60% of the tensile strength (T) for the material. Therefore, the equation development for a simple hole piercing looks like:
Generic trim equation: |
Tonnage = P * t * ꚍ |
Equation 2 |
Specific for a round hole: |
Tonnage = πd * t * 0.6T |
|
Simplifying: |
Tonnage = d * t * 0.6Tπ |
|
Mild steel T = 300 MPa = 43.5 ksi: |
0.6 * 43.5 * 3.14 = 82 |
|
Pierce a round hole: |
Tonnage = d * t * 80 |
|
Now that we know how the rule of thumb was derived, we can point out some possible sources of error. First, the equation uses the full thickness of the material. In reality, a typical trim operation for steel consists of 20% to 50% trimming and the remainder is breakage. The press only needs to produce load for the trimming portion. Second, the shear strength of the material is not a fixed percentage of the tensile strength. The actual shear strength should be measured for each specific grade as the microstructure differences of the AHSS will affect the material strength in shear. Lastly any of these errors are multiplied since today’s AHSS material has an overall tensile strength of three, four or even five times that of mild steel – taking any error in this estimate and magnifying it. To see this, we can take a look at a simple example of piercing a 1-inch hole in 1.5 mm thick mild steel. The steel tensile strength has a range of 40 ksi to 55 ksi (280 MPa to 380 MPa). If we look at Equation 1 with the high- and low-end assumptions, we see:
Equation 1 estimate |
Tonnage = 1 * 0.06 * 80 = 4.8 tons |
Equation 2 minimum |
Tonnage = 3.14 * 0.06(20%) * 0.6(40) = 0.9 tons |
Equation 2 maximum |
Tonnage = 3.14 * 0.06(50%) * 0.6(55) = 3.1 tons |
In this very simple example, we see sources of error that could lead to an estimate of 0.9 to 4.8 tons to pierce a single hole. A similar exercise could be taken on a drawing operation. In this situation, most rules of thumb attempt to use the perimeter or surface area of the part, the material thickness and the material tensile strength to predict the tonnage needed. Sources for error in this type of calculation include: 1) Using the perimeter of the draw area, tending to under predict; 2) Using the surface area of the part, tending to overpredict; and 3) Using the tensile strength of the material, also tending to over predict as it assumes the material is stretched right to the level of splitting. Correction factors have been developed overtime, but it is still easy to see there are many possible sources of error in these types of calculations.
AHSS Magnifies Press Tonnage Prediction Challenges
We can see that there are inherent challenges with the old school rules of thumb, but why are they so exaggerated with today’s AHSS? There are a number of reasons.
- Strength: The strength of today’s cold stamped steels is quite incredible. Where a mild steel may have a tensile strength of 280 MPa, it is now common to cold stamp dual phase (DP) steels and 3rd Generation steels with up to 1180 MPa. In addition, new materials having a tensile strength of 1500 MPa with enough elongation to allow for cold stamping are starting to enter the market. This five-fold increase in strength acts as a multiplying factor for any errors in traditional predictions.
- Formability: The formability of AHSS has also increased dramatically. Today a DP 590 steel and even a 980 3rd Generation steel can have nearly the same elongation as a high-strength low alloy (HSLA) steel of 30 years ago. This affords the part designers the ability to incorporate more complex forms into a part including using darts and beads to increase a part’s stiffness, tight radii and deeper draws. All of these add to the tonnage used and are generally not part of the old school rule of thumb calculations.
- Springback Corrections: Springback is linearly related to the yield strength of a material. Therefore, stamping AHSS grades require more features to be added to the die process to control springback. These may include draw beads (used to control material flow early in the press stroke), stake beads (used at the bottom of the stroke to minimize springback) and tighter radii (Figure 2). These features are typically off product, in the addendum, and are easily ignored by typical rule of thumb calculations.

Figure 2: Draw and Stake Bead PlacementA-6
- Hardening Curves: The complex microstructure of AHSS offers many advantages to increase formability. All AHSS grades produce microstructural phase transformations during the stamping process. This allows the lower yield strength in the as-rolled material, which aids in formability, to increase during the stamping operation. This yield strength increase can be as much as 100 MPa. Models that estimate these hardening curves of the material are ignored when doing hand calculations.
- Other Considerations: Lastly the typical rule of thumb calculations, as we have discussed, only consider the part characteristics. They generally do not include the other sources that consume energy during the stamping process including off-product feature (beads, pilot holes, etc.), spring stripper pressure, pad pressure from nitrogen springs or air cushions, driven cams and part lifters. Many of these could be ignored 30 years ago with mild steels, but they become more significant with the strength of today’s AHSS.
Accurate Tonnage Predictions Require Accurate and Complete Inputs
The answer in recent years is to rely more on simulations using finite element analysis (FEA) software. Care must be taken when using these sophisticated software packages. Many times, the software is blamed when inaccurate press tonnage predictions are given. However, we know that if any of the characteristics mentioned above are ignored, the user will develop a very precise but very inaccurate tonnage prediction.
Next Steps
The issue with accurately predicting press requirements is industry-wide and has been around for decades. The recent advances in AHSS have multiplied the sources of errors that exist in the past rules of thumb and from the incorrect usage of advanced software packages. Many people within the steel and automotive industries are working on improving the reliability of these predictions including the Auto/Steel Partnership (A/SP). A/SP, founded in 1987, is a partnership between automotive OEMs, steel mills and affiliate suppliers. A/SP has teamed up with formability software suppliers to collaborate on this subject. A/SP’s project will work to measure sources of error and develop guidelines to address these in the areas of material characterization, modeling techniques and numerical analysis techniques. A/SP’s efforts, including this project, looks to bridge the gap between research laboratories and the shop floor.
What can stamping manufacturers do? First, prepare for the digital manufacturing era (often call the 4th Industrial Revolution) by keeping press tonnage monitors in good working order. Also, consider upgrading to systems that can capture full through-stroke force curves. Secondly, do not go it alone. Engage with organizations like A/SP, OEMs and steel mills. When evaluating new parts using AHSS, get the steel mill involved early, even in the die design phase. All steel mills have teams of application engineers to help OEMs and their suppliers to transition into using the newest grades of steel – they want stampers to succeed and have the tools and data to help.
Back To Top