Joining Dissimilar Materials, Laser Welding
Given the use of many different metals in the Body in White construction, it is important to understand the effects of dissimilar welding AHSS. Researchers at Indian Institute of Technology Madras in Chennai, India and Centre of Laser Processing of Materials in Hyderabad, India developed tests to study the resulting microstructure from laser welding 2.5 mm thick DP600 steel to 3 mm thick AA6061 aluminium alloy using a laser beam diameter of 1.5 mm.I-1 They discovered a softening in the steel HAZ due to a tempering effect and an increase in hardness in the aluminum HAZ due to the presence of aluminium intermetallic phases present. Maximum shear strength was observed when the thickness of intermetallics was reduced to 8-11 microns. They concluded that best quality welds were made under power densities and interaction times of 1.98kW/mm2, 0.15s and 2.26 kW/mm2, 0.187s.
The laser power was varied from 3 kW to 4.5 kW and the scanning speed of 8 mm/s, 10 mm/s, and 12 mm/s. Power density and interaction time were two parameters they used to compare trials where:
Power density (Pd) = |
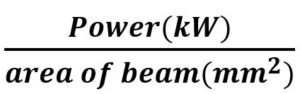 |
and
interaction time (It) = |
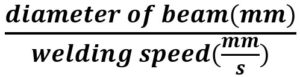 |
The resulting welding parameters are shown in Table 1 below. Figure 1 shows the microstructure of the fusion boundary and HAZ on the DP600 side of the welded joint. Figure 2 shows the microstructure of the weld interface on the AA 6061 side. Figure 3 displays the hardness data with (a) representing 3.5 kW and 10 mm/s, (b) representing 3.5 kW and 8 mm/s, and (c) representing 4 kW and 8 mm/s. Figure 4 represents the Shear Stress-Strain of the welds given different IMC thickness.
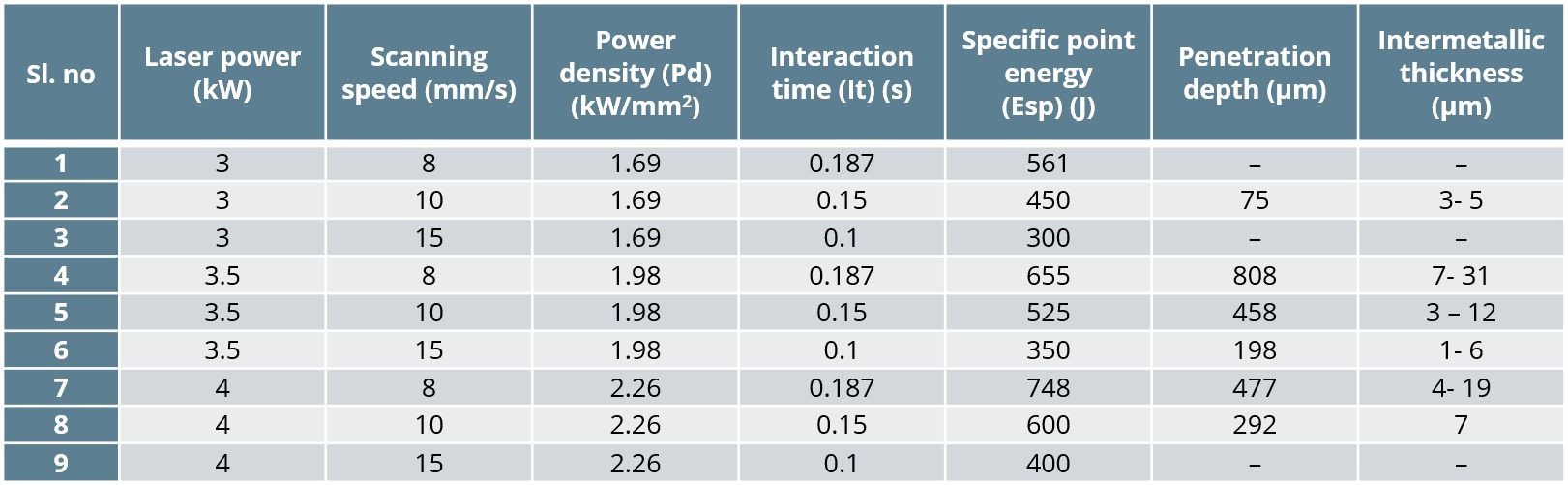
Table 1: Welding Parameters.I-1
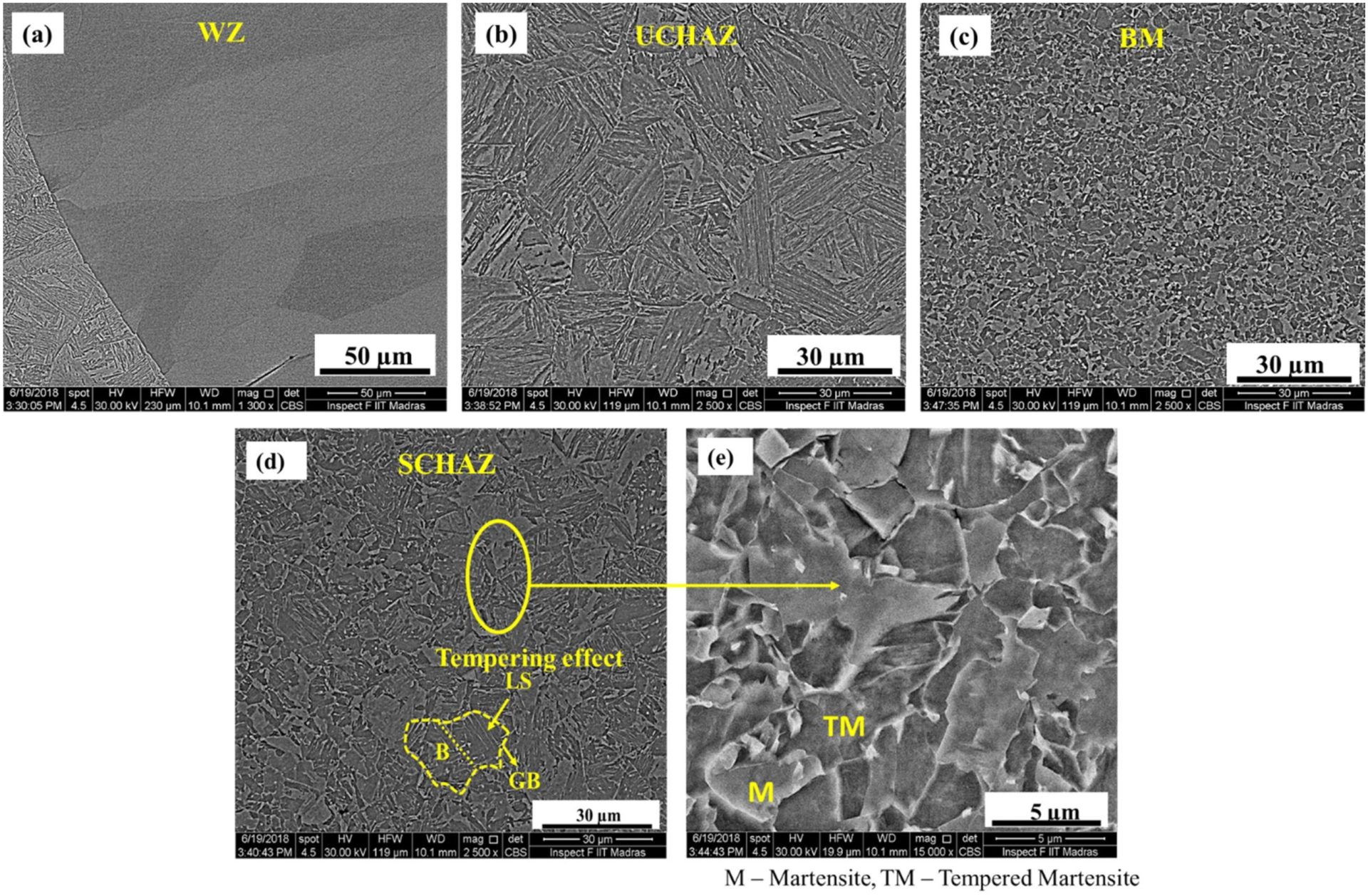
Figure 1: Weld Metal, DP 600 Base Metal and HAZ microstructure.I-1
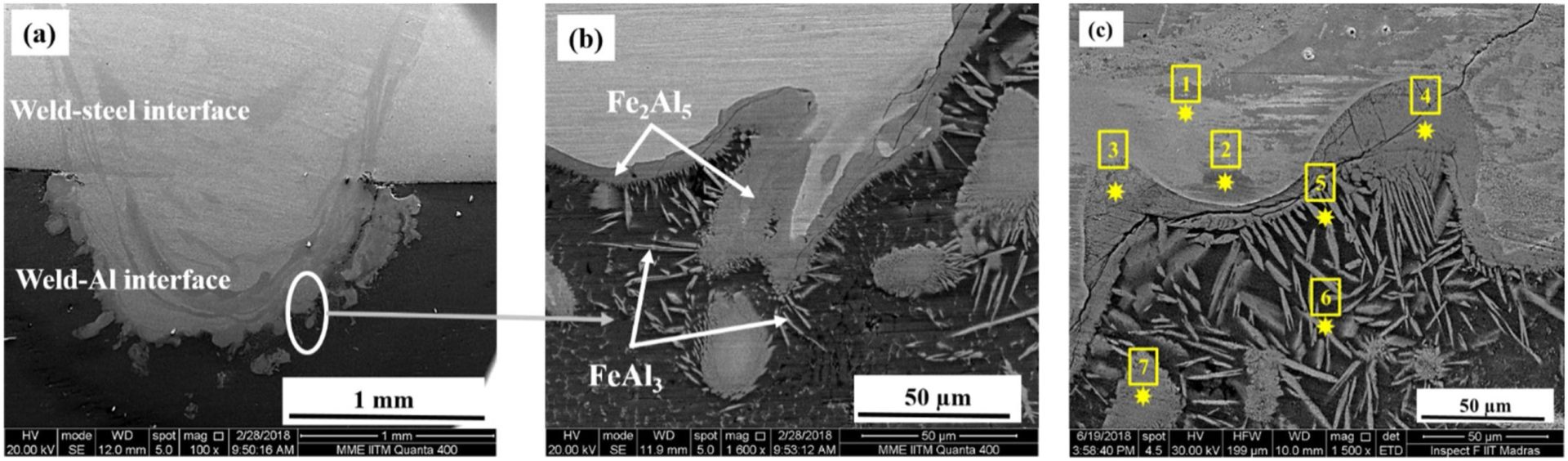
Figure 2: Fe-Al interface microstructure.I-1
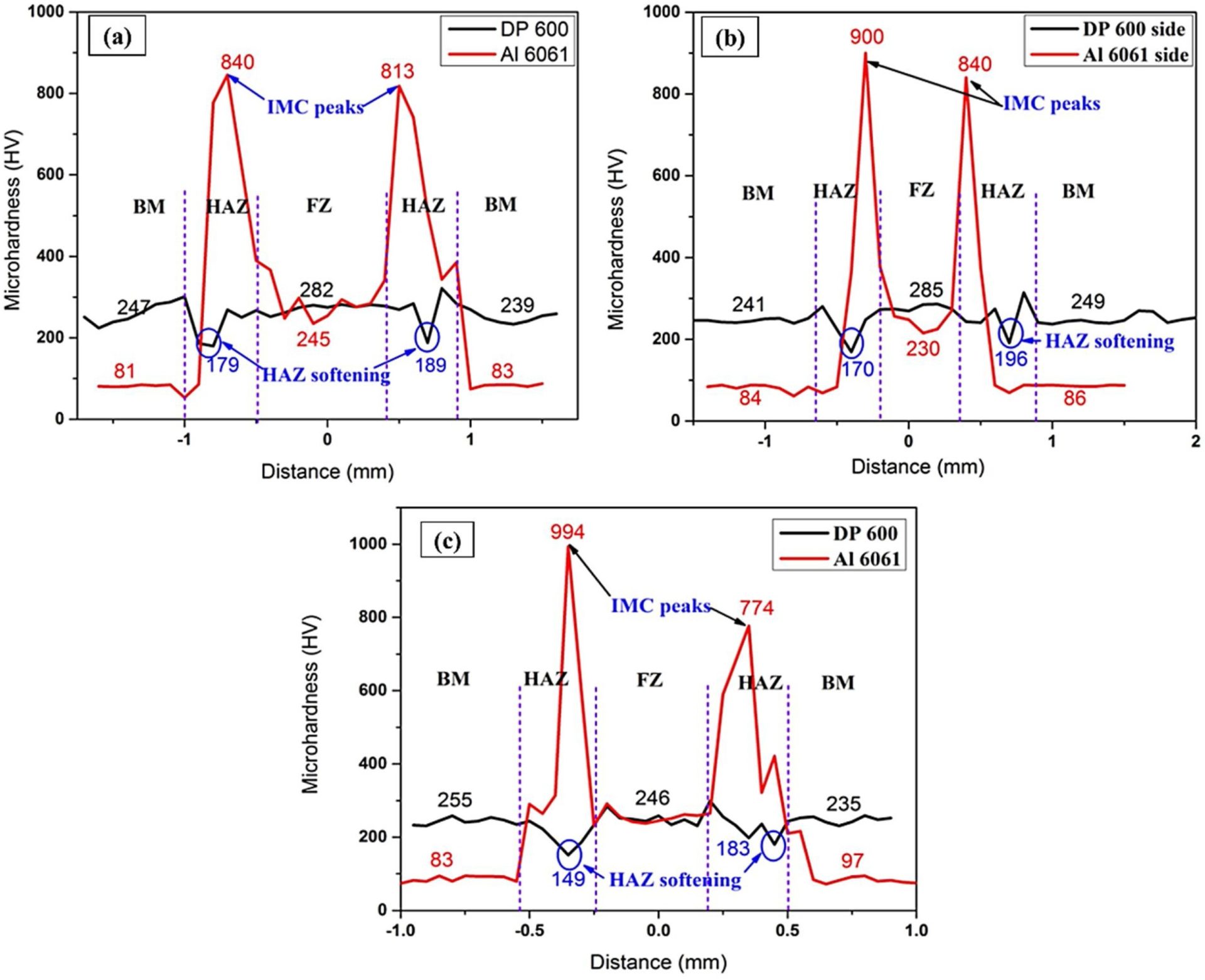
Figure 3: Microhardness Plot.I-1
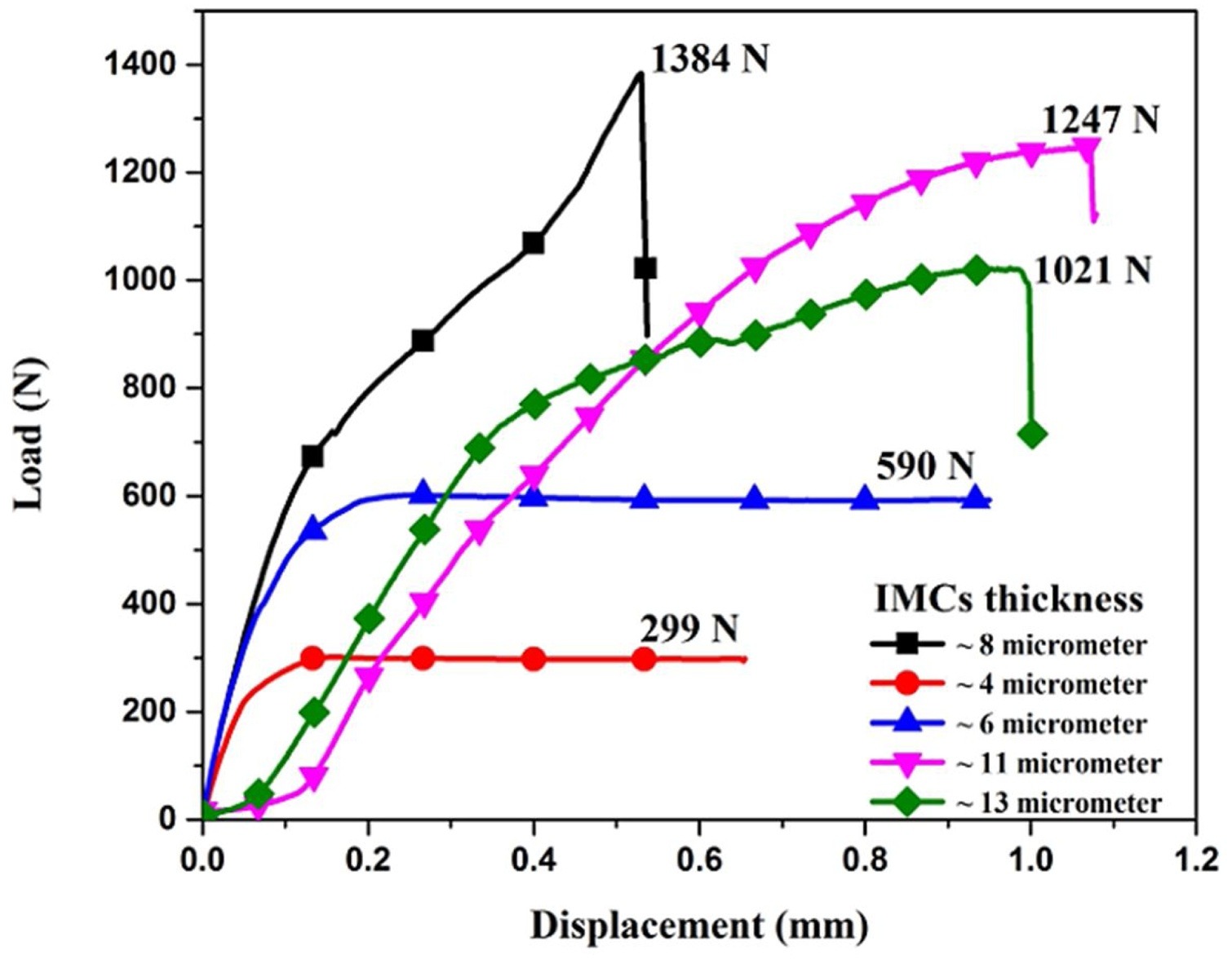
Figure 4: Load vs. Displacement.I-1
High Energy Density Welding
Fundamentals and Principles of High Energy Density Welding
High energy density welding processes are those that focus the energy needed for welding to an extremely small size area. This allows for very low overall heat input to the workpiece, which results in minimal BM degradation, residual stress, and distortion. Welding speeds can be very fast. The two main processes known for extreme energy densities are laser (Figure 1) and Electron Beam Welding (EBW).
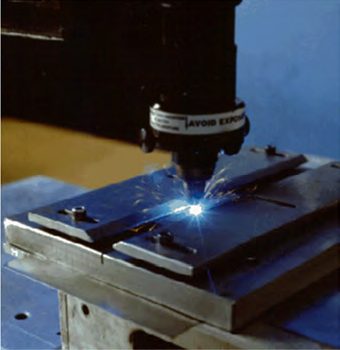
Figure 1: Laser welding.
As shown in Figure 2, energy densities of focused laser and electron beams can approach and exceed 104 kw/cm2. These energy densities are achieved through a combination of high power and beams that are focused to an extremely small diameter. Diameters as small as a human hair (0.05 mm) are possible. PAW[KH1] offers greater energy density than conventional arc welding processes and is sometimes referred to as the “poor man’s laser”.
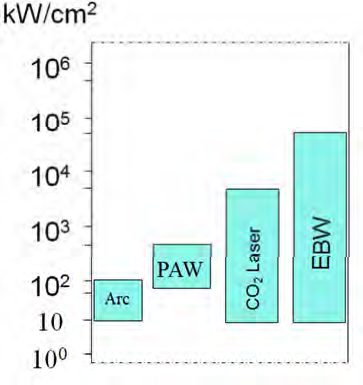
Figure 2: Power densities of various welding processes.
High energy density processes produce weld profiles of high depth-to-width ratio, as compared to other welding processes (Figure 3). As a result, much greater thicknesses can be welded in a single pass, especially with EBW. The figure also illustrates the fact that high energy density processes can produce a weld with minimal heating to the surrounding area as compared to the other processes. However, the high depth-to-width ratio weld profile is much less forgiving to imperfect joint fit-up than the profile produced by arc welding processes.
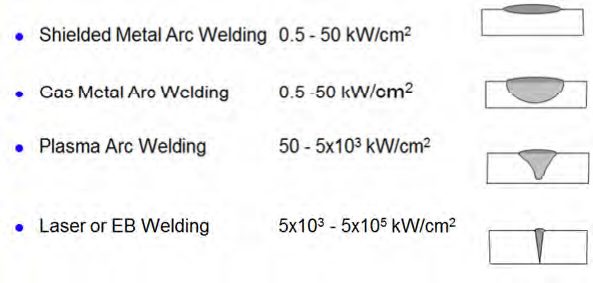
Figure 3: Comparison of typical weld profiles.
Laser and EBW processes are used in a wide variety of industry sectors. Very high weld speeds are possible and the welds are usually aesthetically pleasing. Laser welding is very adaptable to high-speed production so it is common in the automotive sector. The ability to precisely locate welds on smaller sensitive components with minimal heat input makes laser welding very attractive to the medical products industry.
When welding with high energy density processes, the laser or EB is focused along the joint line of the workpieces to be welded. The extreme power density of the beam not only melts the material, but causes evaporation. As the metal atoms evaporate, forces in the opposite direction create a significant localized vapor pressure. This pressure creates a hole, known as a keyhole, by depressing the free surface of the melted metal. The weld solidifies behind the keyhole as it progresses along the joint (Figure 4). This method of welding known as keyhole welding is the most common approach to laser and EB, and produces the characteristic welds of high depth-to-width ratio. There are some cases where the keyhole mode is not used. This mode is known as conductive mode welding. Conductive mode welds have a weld profile closer to that of an arc weld A-11, P-6
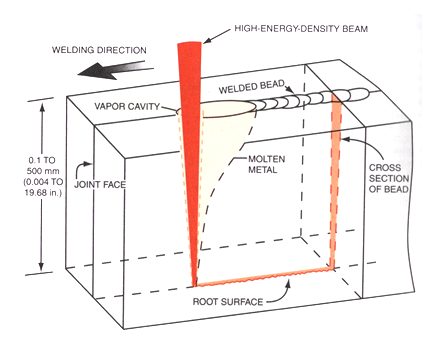
Figure 4: Keyhole mode welding.
Blog, main-blog
In static or dynamic conditions, the spot weld strength of Advanced High-Strength Steels (AHSS) may be considered as a limiting factor. One solution to improve resistance spot weld strength is to add a high-strength adhesive to the weld. Figure 1 illustrates the strength improvement obtained in static conditions when crash adhesive (in this case, Betamate 1496 from Dow Automotive) is added. The trials were performed with 45-mm-wide and 16-mm adhesive bead samples.

Figure 1: Tensile Shear Strength and Cross Tensile Strength on DP 600.A-16
Another approach to improve the strength of welds is done by using laser welding instead of spot welding. Compared to spot welding, the main advantage of laser welding, with respect to the mechanical properties of the joint, is the possibility to adjust the weld dimension to the requirement. One may assume that, in tensile shear conditions, the weld strength depends linearly on the weld length as indicated in the results of a trial A-16, shown in Figure 2.

Figure 2: Tensile-shear strength on laser weld stitches of different length.A-16
However, a comparison of spot weld to laser weld strength cannot be restricted to the basic tensile shear test. Tests were also conducted to evaluate the weld strength in both quasi-static and dynamic conditions under different solicitations, on various AHSS combinations. The trials were performed on a high-speed testing machine, at 5 mm/min for the quasi-static tests and 0.5 m/s for the dynamic tests (pure shear, pure tear or mixed solicitation, as shown in Figure 3). The strength at failure and the energy absorbed during the trial were measured. Laser stitches were done at 27mm length. C- and S-shape welds were performed with the same overall weld length.

Figure 3: Sample geometry for quasi-static and dynamic tests.A-16
The weld strength at failure is described in Figure 4, where major axes represent pure shear and tear (Figure 4). For a reference spot weld corresponding to the upper limit of the weldability range, globally similar weld properties can be obtained with 27mm laser welds. The spot weld equivalent length of 25-30 mm has been confirmed on other test cases on AHSS in the 1.5- to 2 mm thickness range. It has also been noticed that the spot weld equivalent length is shorter on thin mild steel (approximately 15-20 mm). This must be considered when shifting from spot to laser welding on a given structure. There is no major strain rate influence on the weld strength; the same order of magnitude is obtained in quasi-static and dynamic conditions.

Figure 4: Quasi-static and dynamic strength of welds, DP 600 2 mm+1.5 mm.A-16
The results in terms of energy absorbed by the sample are seen in Figure 5. In tearing conditions, both the strength at fracture and energy are lower for the spot weld than for the various laser welding procedures. In shear conditions, the strength at fracture is equivalent for all the welding processes. However, the energy absorption is more favorable to spot welds. This is due to the different fracture modes of the welds; for example, interfacial fracture is observed on the laser welds under shearing solicitation. Even if the strength at failure is as high as for the spot welds, this severe failure mode leads to lower total energy absorption.

Figure 5: Strength at fracture and energy absorption of Hot Rolled 1500 1.8-mm + DP 600 1.5-mm samples for various welding conditions.A-16
Figure 6 represents the energy absorbed by omega-shaped structures and the corresponding number of welds that fail during the frontal crash test (here on TRIP 800 grade). It appears clearly that laser stitches have the highest rate of fracture during the crash test (33%). In standard spot welding, some weld fractures also occur. It is known that AHSS are more prone to partial interfacial fracture on coupons, and some welds fail as well during crash tests. By using either Weld-Bonding or adapted laser welding shapes, weld fractures are mitigated, even in the case of severe deformation. As a consequence, higher energy absorption is also observed.

Figure 6: Welding process and weld shape influence on the energy absorption and weld integrity on frontal crash tests.A-16
Up to a 20% improvement can be achieved in torsional stiffness, where the best results reflected the combination of laser welds and adhesives. Adhesive bonding and weld- bonding lead to the same stiffness improvement results due to the adhesive rather than the additional welds. Figure 7 shows the evolution of the torsional stiffness with the joining process. Optimized laser joining design leads to the same performances as a weld bonded sample in fracture modes, shown in Figure 8.
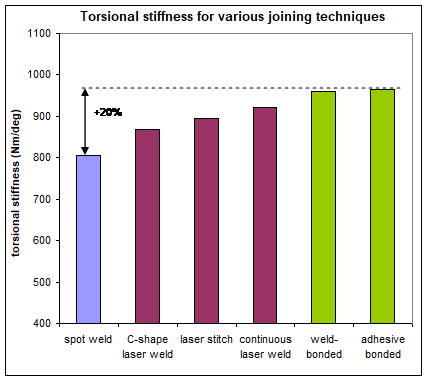
Figure 7: Evolution of the torsional stiffness with the joining process.A-16

Figure 8: Validation test case 1.2-mmTRIP 800/1.2-mm hat-shaped TRIP 800.
Top-hat crash boxes were tested across a range of AHSS materials including DP 1000. The spot weld’s energy absorption increased linearly with increasing material strength. The adhesives were not suitable for crash applications as the adhesive peels open along the entire length of the joint. The weld bonded samples perform much better than conventional spot welds. Across the entire range of materials there was a 20-30% increase in mean force when weld bonding was used; the implications suggesting a similarly significant improvement in crash performance. Furthermore, results show that a 600 MPa weld bonded steel can achieve the same crash performance as a 1000 MPa spot-welded steel. It is also possible that some down gauging of materials could be achieved, but as the strength of the crash structure is highly dependent upon sheet thickness, only small gauge reductions would be possible. Figure 9 shows the crash results for spot-welded and weld bonded AHSS.

Figure 9: Crash results for spot-welded and weld bonded AHSS.