Blanking, Blog, Cutting-Blanking-Shearing-Trimming, homepage-featured-top, main-blog, Tool & Die Professionals
You’ll find this content as part of our page on Laser Blanking, but this month, we want to highlight it in our AHSS Insights blog. We thank Schuler North America for contributing this insightful case study.
Production of Class A quality and structural parts without a blanking die is possible, even for high-volume serial production. Laser blanking enables flexible, cost-effective, and sustainable manufacturing and is capable of reaching 45 parts per minute. DynamicFlow Technology (DFT) from Schuler provides highly productive, die-free blanking with lasers—directly from a continuously running steel coil. DFT combines the advantages of flexible laser cutting with the speed of conventional blanking.
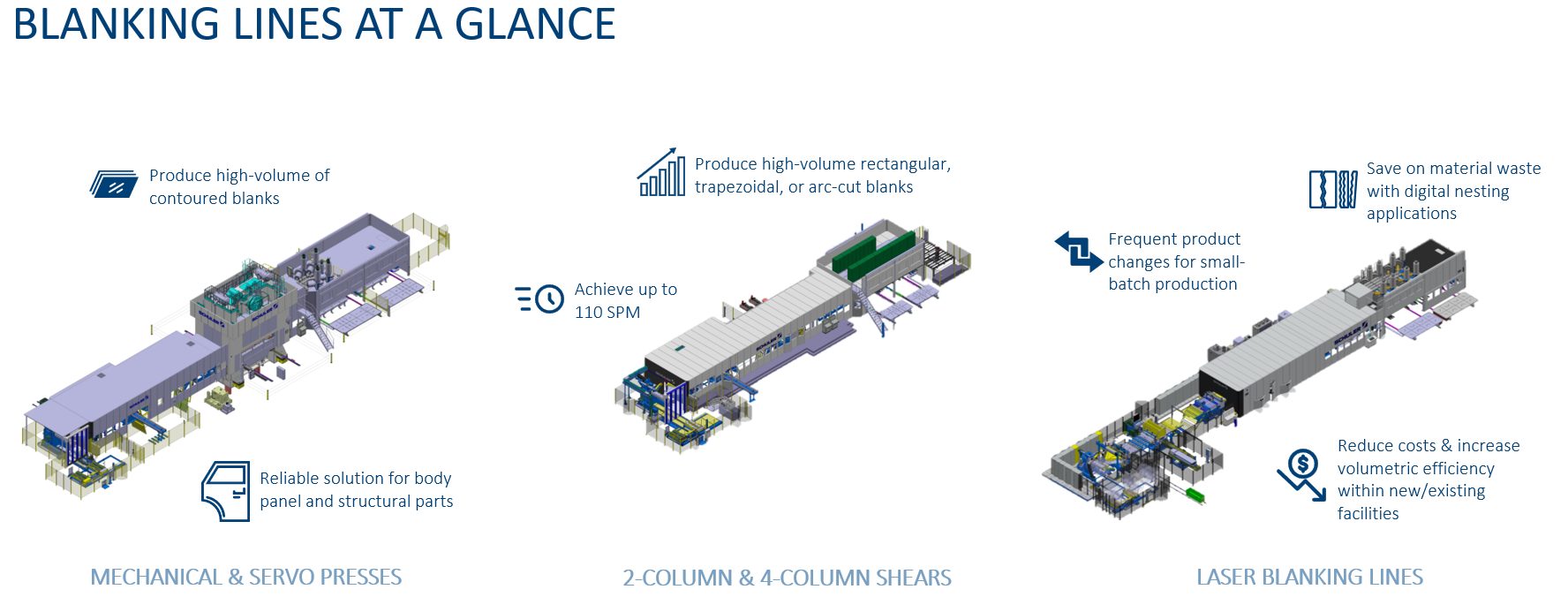
Figure 1 – Laser blanking lines offer additional flexibility over conventional blanking approaches.
Laser blanking technology addresses market challenges such as frequent die changes, the need to increase capacity, and improving plant floor utilization, material utilization, and downstream processes.
LASER BLANKING ELIMINATES FREQUENT DIE CHANGES
It is important to remember that there are no dies with laser blanking technology, and no dies mean no die changes. Overall Equipment Effectiveness (OEE) of up to 80% can be achieved with laser blanking technology. In fact, 4 to 6 million parts per year of various materials are produced with the help of DFT—including mild steel, high-strength steel, and advanced high-strength steel. Even processing press-hardening steels with an aluminum-silicon coating is possible with laser blanking. Surface and cutting quality can be maintained over this spectrum of steel grades. Laser blanking technology can even achieve effective small batch production of Class A outer body panels and structural parts typically up to 3mm thick.
LASER BLANKING INCREASES PLANT OUTPUT
Competitive high-speed and high-output results can be achieved in multiple ways with laser blanking technology. The above-ground coil-fed line, optimized for short setup time, can handle coils with material widths up to 2,150 mm, weighing up to 30 tons. The material transport is smooth and controlled, simplifying setup and leading to uninterrupted processing within the laser cell.
There are three highly dynamic and simultaneously moving laser cutting heads within the laser cell of these lines. These laser cutting heads cut the programmed blank contour from a continuously moving material coil. Cutting speeds can exceed 100 meters per minute. The material is protected against any process contamination throughout the cutting process by custom-designed cutting clearance and material transport.
Figure 2 reveals the high-speed and high-output results for outer body parts. Each part is measured by improved output per minute and hour to achieve an OEE of 80%. Laser blanking lines can achieve up to 45 parts per minute and reduce costs per blank.
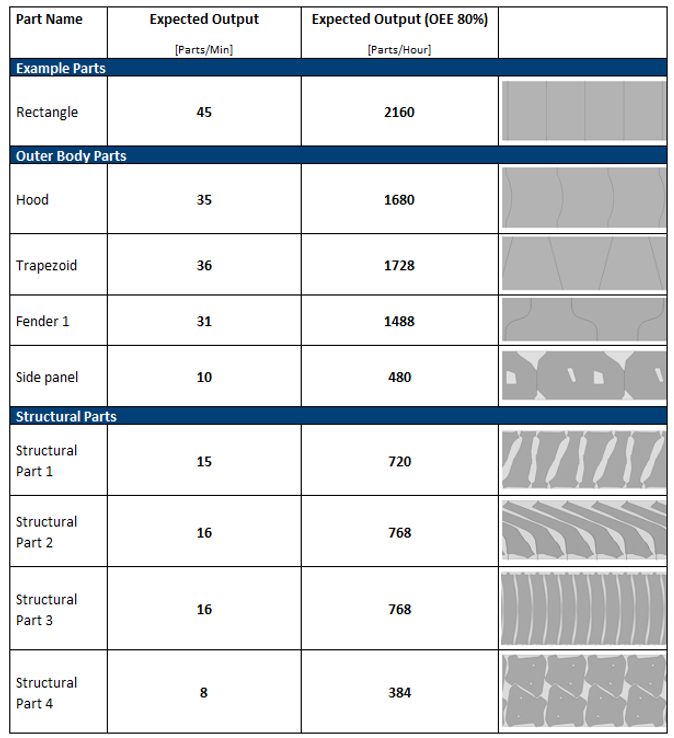
Figure 2: High productivity achieved with laser blanking
LASER BLANKING IMPROVES MATERIAL UTILIZATION
Up to 90% of blank costs are determined by the material price. The most significant leverage would be to reduce scrap and save on materials. Schuler conducted research based on the production of 300,000 cars per year, at 350 kg per car and $1,000 USD per ton of steel to provide a realistic inside look at how much cost savings can be achieved with laser blanking. The result was $1 Million USD saved with just 1% of material savings. This is extremely significant as material costs keep increasing.
Laser blanking is the digital way to cut blanks. All that’s needed to create a blanking program is a drawing to be loaded and a material to be selected. The part-specific program can be created offline and modified at any time. It is designed to create optimal combinations of material utilization and output—resulting in a high level of flexibility that significantly reduces development time for optimal blanks while also allowing for need-based production. This makes production planning easier, and it also opens the door to continuous contour optimizations for the forming process. Additionally, laser cutting does not require any gaps between individual parts due to smart nesting capabilities that cannot be achieved in comparison to die nesting or flatbed laser nesting. The combined smart, flexible nesting functions unlock new potential for material savings. Manufacturers can optimize individual blanks and eliminate the separating strip or connection bridges. Scrap savings in the forming process can also be achieved as there are no geometric restrictions due to cutting dies, and manufacturers can continuously optimize or adapt parts.
Figure 3 showcases the comparison of die nesting (the two graphics on the left) versus a laser-optimized blank contour and material savings via smart, laser blanking line nesting (the two images on the right).
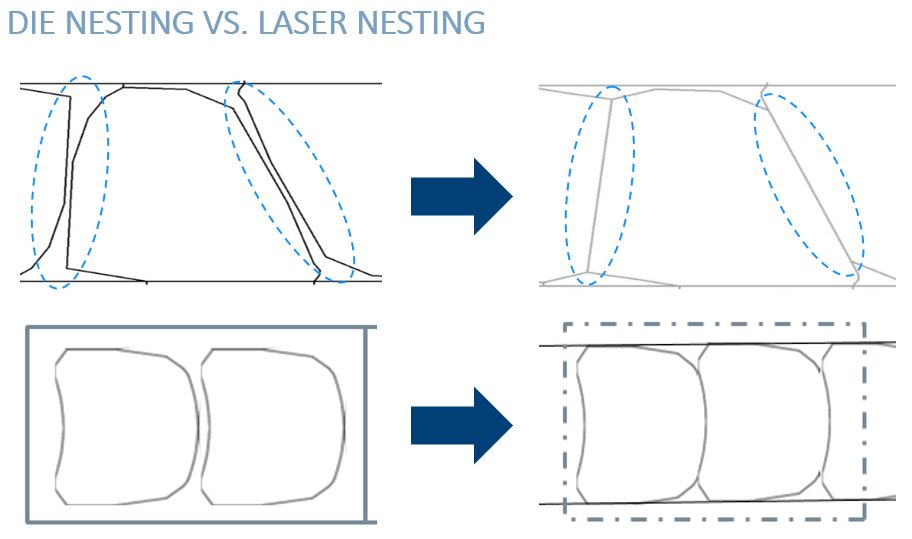
Figure 3: Die nesting (left) compared with laser-optimized blank contours highlighting potential material savings (right)
Overall, laser blanking lines can have an equivalent throughput to conventional blanking lines, but laser blanking lines can achieve up to 10% greater material utilization.
You can read the full Case Study, including how laser blanking reduces infrastructure costs and improves downstream processes here: Laser Blanking Case Study
Schuler will present laser blanking technology, along with a variety of digital tools that create the “Press Shop of the Future” at FABTECH Chicago 2023 (booth # D41306). Tiago Vasconcellos, Sales Director at Schuler North America, will present “How Smart is Your Press Shop?” during FABTECH’s Educational Conference. The presentation will use The Smart Press Shop, a newly formed joint venture between Porsche and Schuler, as an exemplary case study for smart manufacturing standards. Attendees will discover innovative and practical ways to incorporate digitalization into production and become a state-of-the-art stamping facility directly from Schuler.
Schuler offers customized cutting-edge technology in all areas of forming—from the networked press to press shop planning. In addition to presses, Schuler’s products include automation, dies, process know-how, and service for the entire metalworking industry. Schuler’s Digital Suite brings together solutions for networking forming technology and is continuously being developed to further improve line productivity and availability. Schuler customers include automotive manufacturers and suppliers, as well as companies in the forging, household appliance, and electrical industries. Schuler presses are minting coins for more than 180 countries. Founded in 1839 at the Göppingen, Germany headquarters, Schuler has approximately 5,000 employees at production sites in Europe, China and the Americas, as well as service companies in more than 40 countries. The company is part of the international technology group ANDRITZ.
Schuler’s global portfolio of world-renowned brands include BCN (Bliss Clearing Niagara) Technical Services, Müller Weingarten, Beutler, Umformtechnik Erfurt, SMG Pressen, Hydrap Pressen, Wilkins & Mitchell, Bêché, Spiertz Presses, Farina Presse, Liebergeld, Peltzer & Ehlers, Schleicher, and Sovema Group.
Schuler North America (Schuler), headquartered in Canton, Michigan, is the North American subsidiary of Schuler Group. Schuler provides new equipment, spare parts, and a portfolio of lifecycle services for all press systems—including preventative maintenance, press shop design and optimization, turnkey installations, retrofits for existing systems, and localized production and service. Schuler’s best-in-class position in the metalworking and materials industry serves automotive manufacturers and tier suppliers, as well as home appliance, electronics, forging, and other industries.
Tailored Products
topofpage
Types of Tailored Products
Key materials characteristics for formed parts include strength, thickness, and corrosion protection. Tailored products provide opportunities to place these attributes where they are most needed for part function, and remove weight that does not contribute to part performance.
Welded Tailored Blanks (Tailor Welded Blanks)
Welded tailored blanks are a type of tailored product, as are patchwork blanks, tailor welded coils, tailor rolled coils, tailor rolled tubes and tailor welded tubes.
Laser welding is the most common approach to creating these products, but other options like resistance mash seam welding are possible. Mash seam welding requires that the blanks overlap, which adds mass. The heat affected zone (HAZ) for mash seam welds is considerably larger than that of laser welds. Compared with laser welding, the temperature reached when resistance mash seam welding is lower. This may improve formability due to reduced martensite formation, but the larger HAZ and thicker joint may negate this benefit. Non-linear welds are more challenging to produce with the mash seam approach. Welded Tailored Blanks refers to blanks made via either laser welding or mash seam welding. The following discussion centers on blanks and coils joined by lasers.
Butt-welding two or more flat sheets into a single blank creates a laser welded tailored blank (LWTB), also known as a tailor welded blank or laser welded blank (LWB). Steel grades and thickness may be (and usually are) different in the component sheets. Corrosion protection strategies may be different on each component of the welded blank. “Sub blanks” is another name for these component sheets.
Figure 1 shows a laser welded door ring with multiple grades and thicknesses. This technology allows for a reduction in panel thickness in non-critical areas, thus contributing to an overall mass reduction of the part. The lower strength product in the bottom section of the B-Pillar helps dissipate the crash energy in the event of a side impact, playing a key role in crash energy management.
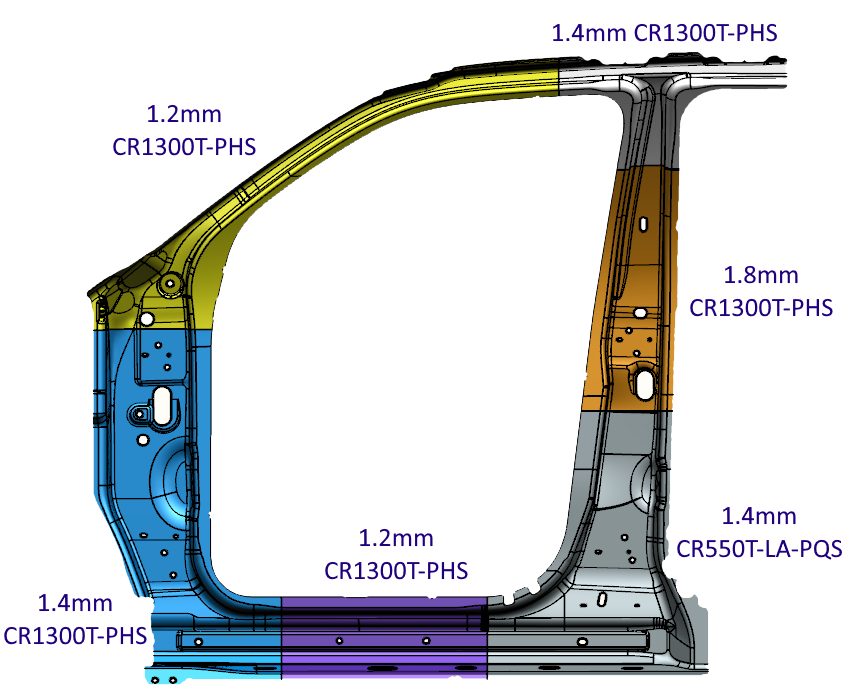
Figure 1: Six-piece Laser Welded Tailored Blank with multiple grades and thickness.R-3
Patchwork Blank
An alternate approach to a laser welded tailored blank involves the creation of what is known as a patchwork blank, consisting of two or more blanks potentially having different thickness or grades. The unique characteristic is that the blanks are placed one on top of the other and (typically) spot welded together while still flat. The patched blank requires only one stamping operation, eliminating the need to join them after forming the components separately. This approach is satisfactory for both cold stamping and hot stamping. The correct number of spot-welds is important in terms of cost and safety. Furthermore, if the components shift relative to one another during the forming operation, the spot welds may shear. There is excellent fit between both parts after forming, allowing for easy application of additional spot welds if needed. Part size, the number and location of reinforcements, and available infrastructure are among the key considerations in deciding between a laser welded or patch blank approach. For example, patchwork blanks may be preferred if the reinforced area is relatively small with complex contours or located within the boundaries of the main blank.
Tailor Welded Coils
Rather than building blanks from individual components, a similar approach is to join entire coils together, edge to edge. These tailor welded coils (Figure 2) are used in coil-fed processes such as blanking, progressive die stamping, transfer press stamping, and roll forming operations. The basic process takes separate coils, prepares their edges for contiguous joining, and laser welds these together into one master coil. The new strip is either directly blanked or re-coiled for future blanking or use as feedstock for a continuous coil-fed stamping or roll forming line (Figure 3). Variations in strength, thickness, and coating occur across the width.
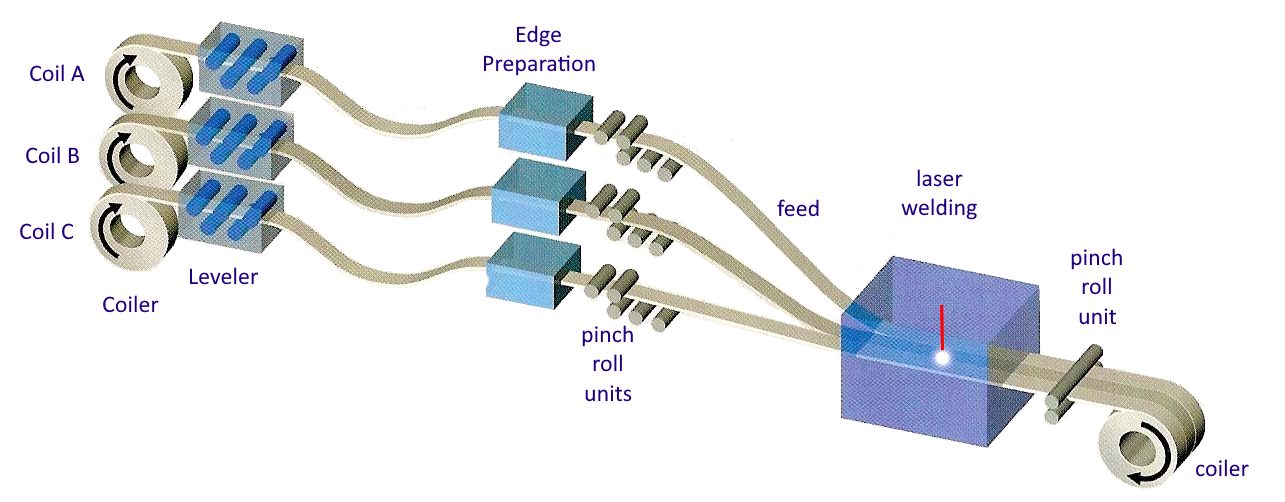
Figure 2: Production Process of Tailor Welded Coils.S-28
![Figure 3: General usage of Tailor Welded Coils [S-28]](https://ahssinsights.org/wp-content/uploads/2020/07/tailor-welded-cole-common-use.jpg)
Figure 3: General usage of Tailor Welded Coils.S-28
Tailor Rolled Coils
Whereas tailor welded coils can vary in properties across the coil width, tailor rolled coils have variable thickness down the length of the coil. Production facilities for tailor rolled coils vary the gap between the rolls used for thickness reduction, allowing for different strip thicknesses in the direction of rolling (Figure 4). Accurate measuring and feedback control technology guarantees the strip thickness tolerances. A significant advantage to this approach results from the transition from one thickness to another with no joints or discontinuities, providing an efficient load path without stress risers. A tailor rolled coil can be either used for blanking operations (for stamping or tubular blanks), or as feedstock into a roll forming line.
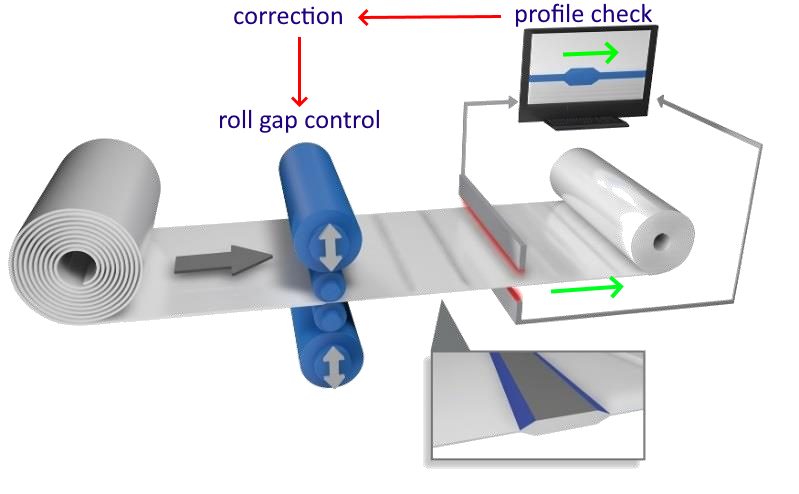
Figure 4: Tailor Rolled Coils vary in thickness down the length of the coil.Z-5
After cold rolling to achieve the targeted thickness variation, coils are annealed to reset the mechanical properties. Tensile properties can be uniform in the blank, with only the thickness varying. Tailored properties are generated by adjusting the incoming coil thickness and the associated thickness reductions, leading to different degrees of recrystallization occurring in the annealing step.Z-14 TRBs used in press hardening do not need to be annealed first, and tailored properties can be produced with the appropriate PHS process.
Tailor Rolled Tubes
Tailor rolled coils are the feedstock to produce variable thickness tailor rolled tubes.
Tailor Welded Tubes
Conventional tube production involves roll forming strips to the desired shape and welding the free ends together to create a closed section. A tailor welded tube production process allows the designer to create complex variations in shape, thickness, strength, and coating (Figure 5)

Figure 5: Tailored tube production allows for differing thickness and strength within the same tube. A) 1-piece cylindrical tube with monolithic properties; B and C) 2-piece tailored tube with property variation down the length of the tube; D) 1-piece conical tube; E) 2-piece conical tube with a patchwork blank.
With hydroforming technology, the next step in tubular components is to bring the sheet metal into a shape closer to the design of the final component without losing tailored blank features (Figure 6).
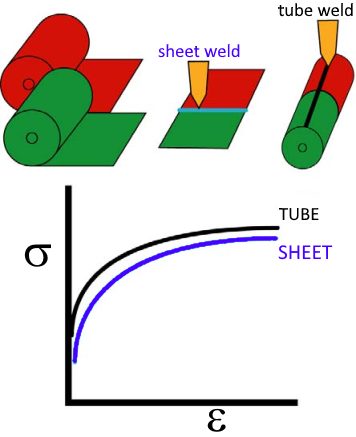
Figure 6: Mechanical properties of tailored tubes are close to the original metal properties in the sheet condition. Hydroforming changes the properties based on the local deformation.G-8
Hydroformed conical tailored tubes offer automotive body engineers an additional approach to crash energy management while achieving a lightweight design. In frontal crash and side impacts the load paths have a key importance on the body design as they have a major bearing on the configuration of the structural members and joints. Figure 7 shows an example of a front-rail hydroformed prototype. The conical tailored tubes for this purpose take advantage of the high work hardening potential of TRIP steel.
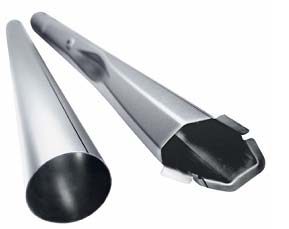
Figure 7: Front-rail prototype based on a conical tube having 40 mm end to end difference in diameter.F-3
Benefits of Tailored Products in Automotive Body Construction
Figure 8 highlights some of the areas within the body structure where companies have considered transitioning to welded tailored blanks. Other tailored products may be suitable in other areas.
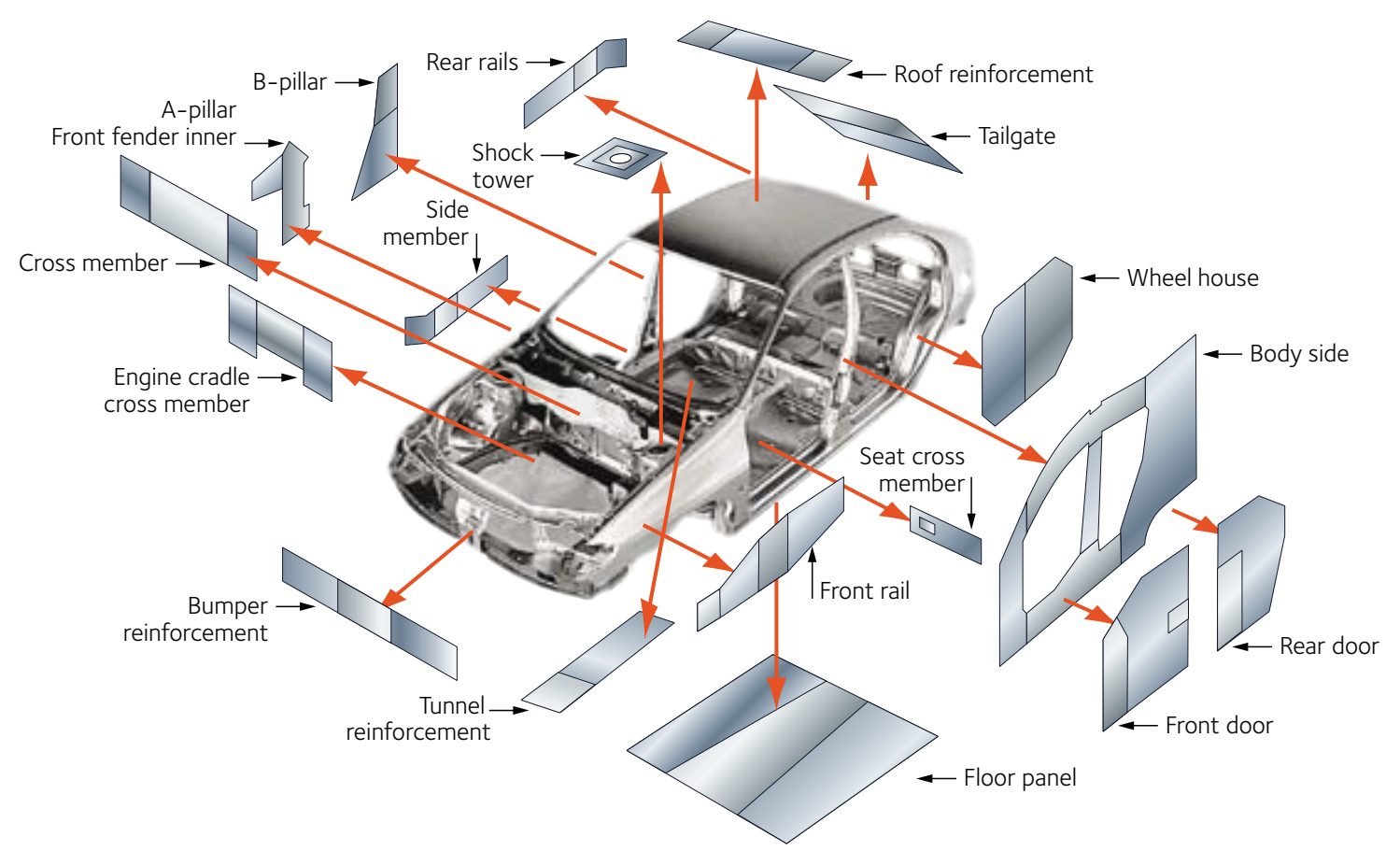
Figure 8: Applications suited for welded tailored blanks.A-31
Tailored products offer numerous advantages over the conventional approach involving the stamping and assembly of individual monolithic blanks which have a single grade, thickness, and coating, including:
Improved materials utilization
- Certain parts, like door rings (Figure 1), window frames, and door inner panels, have large cutout areas contributing to engineered scrap. Converting these to welded tailored blanks allows for optimized nesting of the individual components. Figure 9 presents an example of optimized nesting associated with body side aperture designs using a tailor welded blank. Reduced blank width requirements may allow for additional suppliers or use of master coils yielding slit mults. In the other extreme, blank dimensions larger than rolling mill capabilities are now feasible.
Elimination of reinforcement parts and reduced manufacturing infrastructure requirements
- In areas needing additional thickness for stiffness or crash performance, conventional approaches require stamping both the primary part and an additional smaller reinforcement and then spot welding the two parts together. The tailored product directly incorporates the required strength and thickness. Compared with a tailored product, the conventional approach requires twice the stamping time and dunnage, creates inventory, and adds the spot welding operation. Tolerance and fit-up issues appear when joining two formed parts, since their individual springback characteristics must be accommodated.
Part consolidation
- Similar to the benefits of eliminating reinforcements, tailored products may combine the function of what would otherwise be multiple distinct parts which would need to be joined.
Weight savings
- Conventional approaches to body-in-white construction requires individual parts to have flat weld flanges to facilitate spot welding. Combining multiple parts into a tailored product removes the need for weld flanges, and their associated weight.
Improved NVH, safety, and build quality
- Joining formed parts is more challenging than joining flat blanks first and then stamping. Tailored products have better dimensional integrity. Elimination of spot welds leads to a reduction in Noise, Vibration, and Harshness (NVH). A continuous weld line in tailored products means a more efficient load path.
Enhanced engineering flexibility
- Using tailored products provides the ability to add sectional strength in precise locations to optimize body structure performance.
Easily integrated with advanced manufacturing technologies for additional savings
- Tailored products incorporated into hot stamping or hydroforming applications magnify the advantages described here, and open up additional benefits.
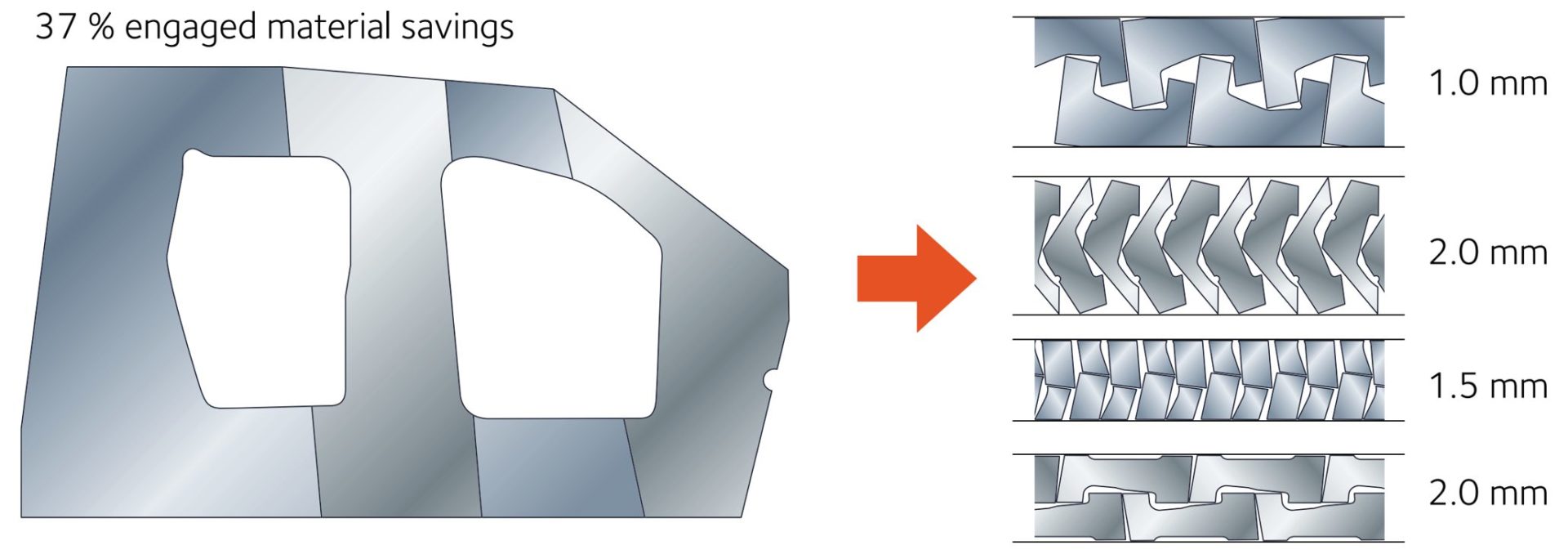
Figure 9: Nesting optimization dramatically reduces engineered scrap.A-31
Design, Usage, and Troubleshooting Guidance
Edge Quality of Component Blanks Used to Create the Welded Blank
Minimal burr, maximized sheared edge stretchability, and maximized tool life are characteristics of good sheared edge quality in conventional blanking operations. When creating sub-blanks for assembly into a laser welded tailored blank, there is an additional critical characteristic: squared edges with high straightness are a prerequisite to avoid local gaps between the blank edges causing undercut in the weld bead and the associated loss of mechanical properties (Figure 10). Conventional shearing operations produce the edge seen in Figure 10a. Precision die blanking with tight clearances, as well as laser blanking, produce edges suitable for the blank welding operation (Figure 10b). Another option is to use a conventional shearing approach to produce a slightly oversize blank, and then use precision shears as the first step in the laser welding line. The advantage to this approach minimizes the impact of edge damage which might occur during transportation.
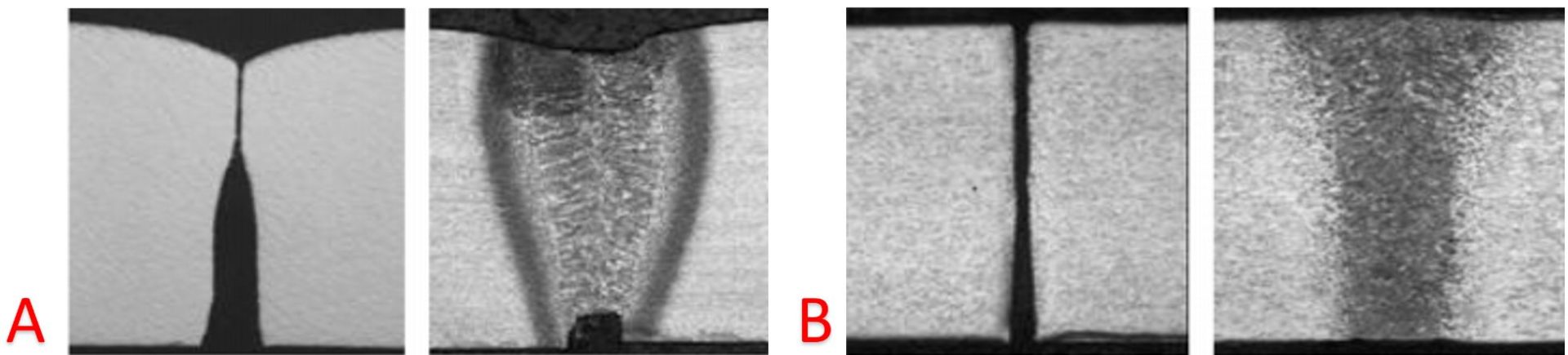
Figure 10: Edge condition and welding result. A) Poor edge resulting in increased residual butt gap and weld undercut; B) Optimum squared edge by precision die blanking or laser welding resulting in flush weld surfaces.S-29
Forming analysis of Welded Blanks
The weld joint and adjacent heat affected zone complicates the forming analysis of welded blanks. There are generally two scenarios that occur: failure perpendicular to the weld and failure parallel to the weld (Figure 10).
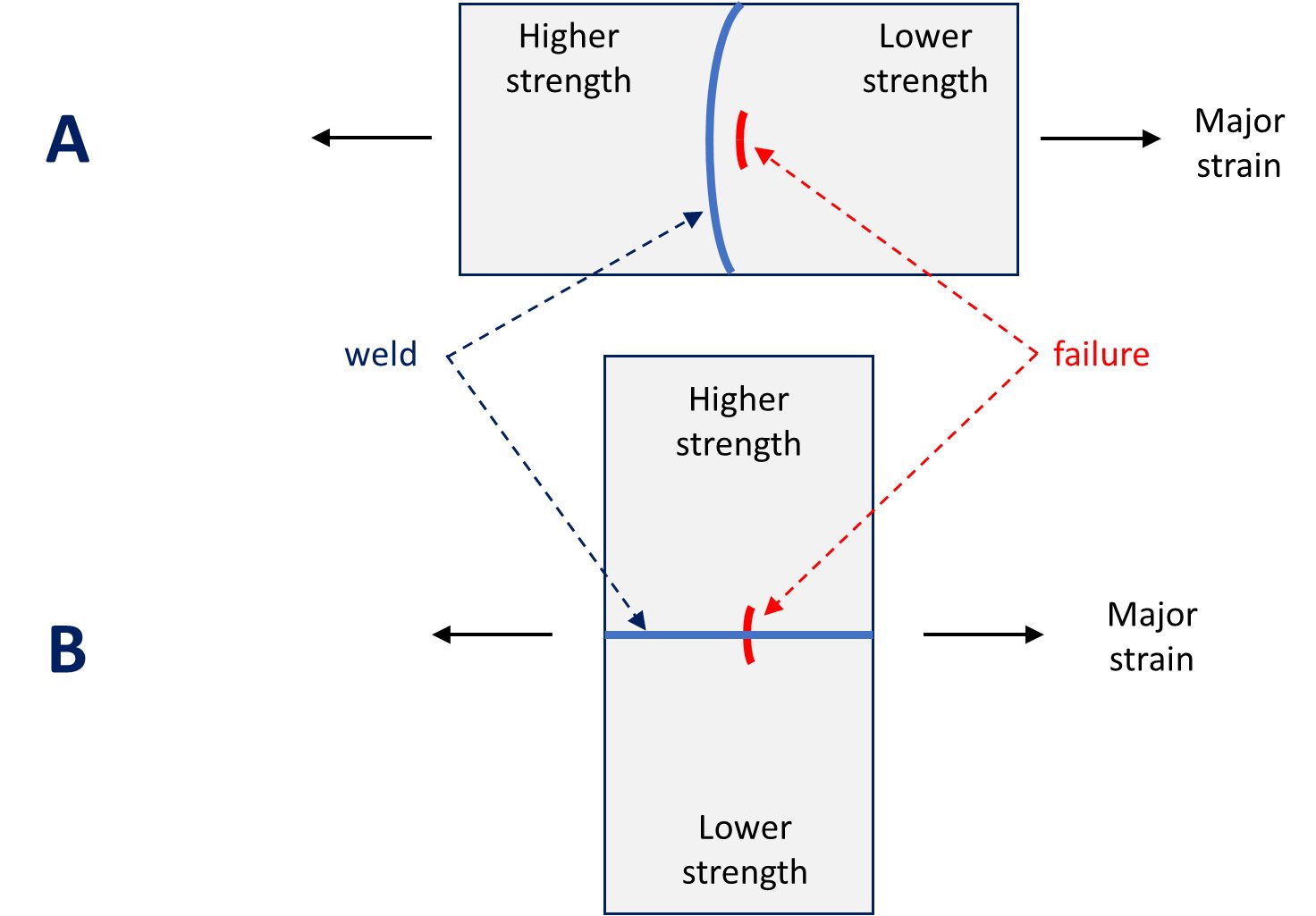
Figure 11: Major strain axis relative to weld line orientation. A) Weld line is perpendicular to the major strain axis; B) Weld line is parallel to the major strain axis.
Consider the scenario in Figure 11A, where the major strain is perpendicular to the weld line orientation. Failure occurs parallel to the weld in the lower strength, more ductile material. The restraining force provided by the higher strength material results in the weld line shifting towards that side.
With the weld seam moving towards the thicker and stronger metal, deformation occurs in thinner and weaker metal. The movement of the weld seam during stamping requires that a blankholder design with appropriate clearances so the welds can move through the blankholder during the drawing process. The punch-cavity clearances must allow for movement as well – otherwise a pinch-point is created and metal flow stops. These clearances are necessary for movement of the heavier gauge metal and the welds, but can also be a source of wrinkling on the lighter gauge side due to the lack of hold-down force in this area. Also, the potential exists for die wear in the locations in contact with weld seam. To counter the weld line motion to the higher strength side, consider allowing greater material flow from that side of the weld through a less severe draw bead design, reduced blankholder pressure or modified blank outline. These strategies help minimize the risk of this type of split.
Now consider the scenario in Figure 11B, where the major strain is parallel to the weld line orientation. Here, fracture occurs perpendicular to the weld line – typically within the weld itself – due to the poorer mechanical properties of the weld with respect to the base material. To avoid splits in the weld, orient the weld away from the major strain direction and away from areas with high strain concentration.
Use of Advanced High Strength Steels in Laser Welded Tailored Products
As sub-blanks are welded together to create the main blank, the beginning or ending of each of the weld lines are not in a steady state condition. As such, the start or stop action of the welding may create a stress riser. After the main blank is built-up, a scalloped cut can remove the affected areas so that only sections of uniform edge quality are formed in subsequent operations.
Laser welding is a high energy density process that focuses the heat in a very localized region as the laser travels at a high speed. This results in a narrow heat affected zone and the rapid quenching leads to the formation of a high-hardness martensite. Increased welding speeds generally require higher energy intensity at the weld which increases peak hardness.
Different welding parameters must be used for advanced high strength steels due to the presence of martensite in the base metal. The microstructure in the heat affected zone is a function of the local time/temperature profile, which changes with distance away from the weld as well as with the composition of the alloy in question. Laser welding some AHSS grades results in tempered martensite in the heat affected zone, leading to a locally softened region. Crash modeling should incorporate the influence of the softened region, which may help dissipate a portion of the crash energy.
However, this softened region creates an area for high strain concentration, leading to premature failure in martensite-containing AHSS grades. Higher strength dual phase steels have more martensite than lower strength dual phase grades, and therefore are more likely to generate HAZ soft zones and reduced formability when used in laser welded blanks. CP and TRIP steels have a lower incidence of HAZ soft zones due to higher alloying content. More information about laser welding is found here.
Blank Stacking, Destacking, and Feeding Problems
Depending on the thickness differences between the component blanks and their relative sizes, embossed dimples on the thinner gauge side can balance the thickness difference and to allow stable coil winding (in the case of tailor welded coil production) or stacking as they are blanked onto a lift. The stack weight and banding of the pallets may contribute to collapsing the dimples, so some companies choose to minimize the stack height.
Automatic destackers and feeders typically require uniform blanks and stacks for trouble-free operation. Dimples and cutouts may interfere with proper operation of overhead vacuum cups or magnetic belts. Moving or deactivating Vacuum cups may be necessary. Dimples should either be outside of the magnetic belt area or have their form away from the belt. Dimples may be a problem for some in-line blank washers and die-lube roll coaters.
Press and Tooling Considerations
When there is a large thickness difference within the component blanks, press tonnage and balance can be a problem. Press tonnage monitors are essential for this type of part, not only for protection of the press equipment, but also for good process control. If press balance is a problem, the tonnage monitors will indicate where the problem is. Supplemental balance devices in the die, such as nitrogen cylinders, may be appropriate, or the stamping may need to move to a larger press.
Tailored products often contain sub-blanks of mixed strength and thickness. The chosen die process must reflect those differences, and account for changes in side-wall curl, springback and drawability characteristics across the part. Mild steel can usually be formed with high strength steel die processes, but high strength steel will not always form satisfactorily with conventional die processes used with mild steels.
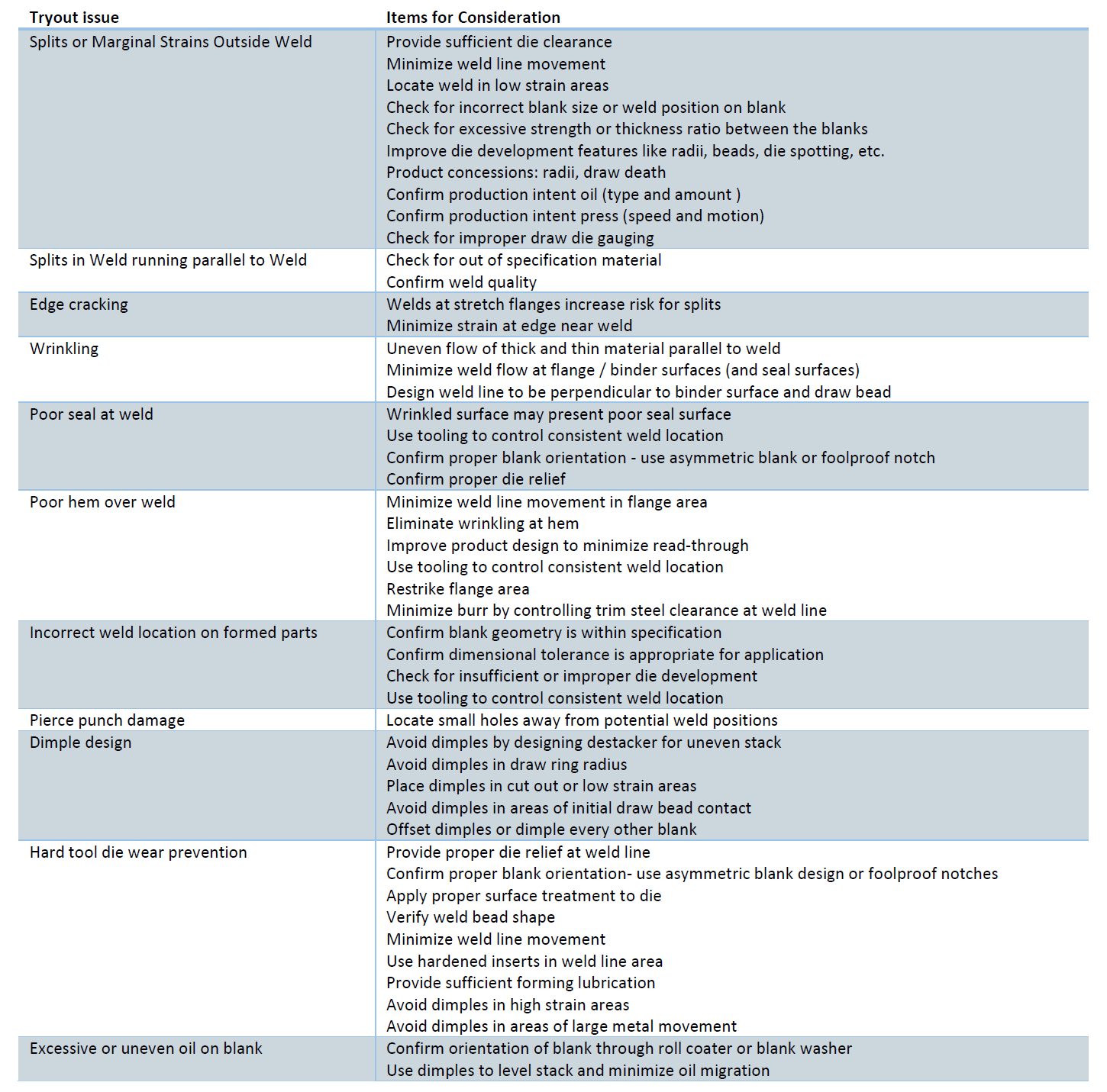
Tailor Welded Blanks Stamping Tryout Issues Checklist.A-20
Case Study: Deploying Tailored Blanks in Electric Vehicles
Many thanks to Isaac Luther, TWB Company, for providing this case study.
Laser-welded blanks (LWBs) allow the combination of different steel grades, thicknesses, and even coating types into a single blank. This results in stamping a single component with the right material in the right place for on-vehicle requirements. This technology allows the consolidation of multiple stampings into a single component.
One example is the front door inner. A two-piece design will have an inner panel and a reinforcement in the hinge area. As shown in Figure 12, a laser welded front door inner incorporates a thicker front section in the hinge area and a thinner rear section for the inner panel, providing on-vehicle mass savings. This eliminates the need for additional components, reducing the tooling investment in the program. This also simplifies the assembly process, eliminating the need to spot weld a reinforcement onto the panel.
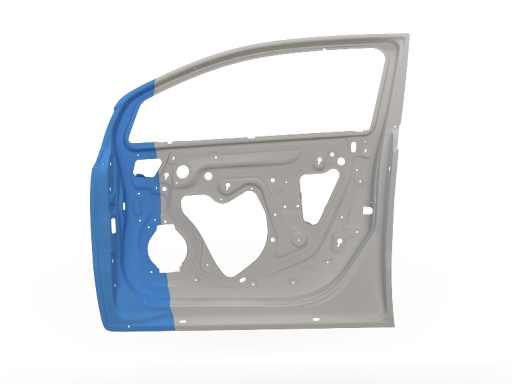
Figure 12: Front Door Inner Stamped from a Laser Welded Blank
Today, large opportunities exist to consolidate components in a BEV in the battery structure. Design strategies vary from different automakers, including how the enclosure is constructed or how the battery mounts into the vehicle. The battery tray can have over 100 stamped components, including sealing surfaces, structural members, and reinforcementsM-68. As an idea, a battery tray perimeter could be eight pieces, four lateral and longitudinal members, and four corners. The upper and lower covers are two additional stamped components, for a total of ten stampings that make up the sealing structure of the battery tray. On a large BEV truck, that results in over 17m of external sealing surfaces.
Part consolidation in the battery structure provides cost savings in material requirements and reduced investment in required tooling. Another benefit of assembly simplification is improved quality. Fewer components mean fewer sealing surfaces, resulting in less rework in the assembly process, where every battery tray is leak-tested.
The deep-drawn battery tub is a consolidated lower battery enclosure and perimeter. This can be seen in Figure 13; a three-piece welded blank incorporates a thicker and highly formable material at the ends and in the center section, either a martensitic steel for intrusion protection or a low-cost mild steel. This one-piece deep-drawn tub reduces the number of stampings and sealing surfaces, resulting in a more optimized and efficient design when considered against a multi-piece assembly. In the previous example of a BEV truck, the deep-drawn battery tub would reduce the external sealing surface distance by 40%. To validate this concept, component level simulations of crash, intrusion, and formability were conducted. As well as a physical prototype built that was used for leak and thermal testing Y-14 with the outcomes proving the validity of this concept, as well as developing preliminary design guidelines. Additional work is underway to increase the depth of the draw while minimizing the draft angle on the tub stamping.
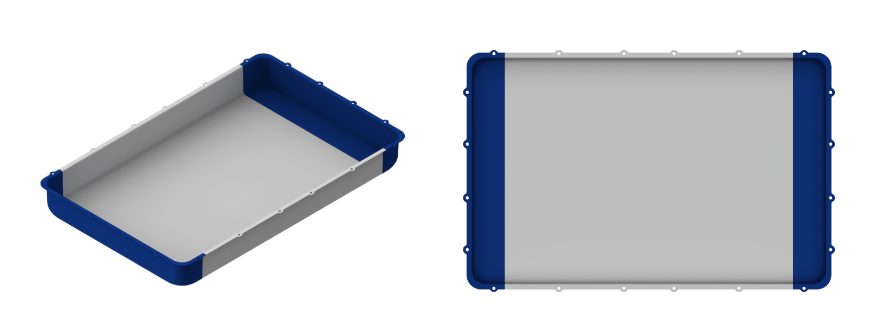
Figure 13: Deep Battery Tub Stamped from a Laser Welded Blank
In most BEVs today, the passenger compartment has a floor structure common in an ICE vehicle. However, the BEV also has a top cover on the battery assembly that, in most cases, is the same size as the passenger compartment floor. In execution of part consolidation, the body floor and battery top cover effectively seal the same opening and can be consolidated into one component. An example is shown below, where seat reinforcements found on the vehicle floor are integrated into the battery top cover, and the traditional floor of the vehicle is removed. Advanced high-strength steels are used in different grades and thicknesses. Figure 14 show what the laser welded battery top cover looks like on the assembly.
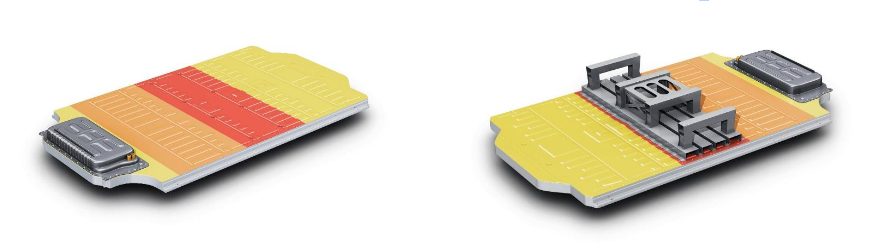
Figure 14: Battery Top Cover from a Laser Welded Blank
Vehicle assembly can also be radically simplified as front seats are mounted on the battery before being installed in the vehicle as shown in Figure 15, the ergonomics of the assembly operation are improved by increased access inside the passenger compartment through the open floor.
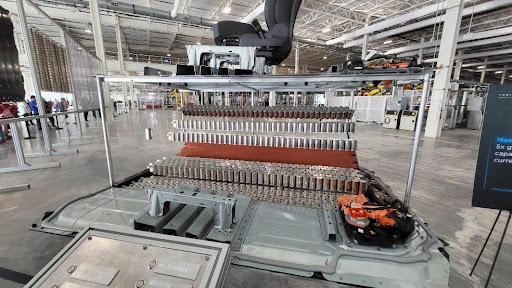
Figure 15: Ergonomics of the Assembly Operation
Cost mitigation is more important than ever before, with reductions in piece cost and investment and assembly costs being important. At the foundation BEVs currently have cost challenges in comparison to their ICE counterparts, however the optimization potential for the architecture remains high, specifically in part consolidation. Unique concepts such as using laser welded blanks for deep-drawn battery tubs and integrated floor/battery top covers are novel approaches to improve challenges faced with existing BEV designs. Laser welded blank applications throughout the body in white and closures remain relevant in BEVs, providing further part consolidation opportunities.
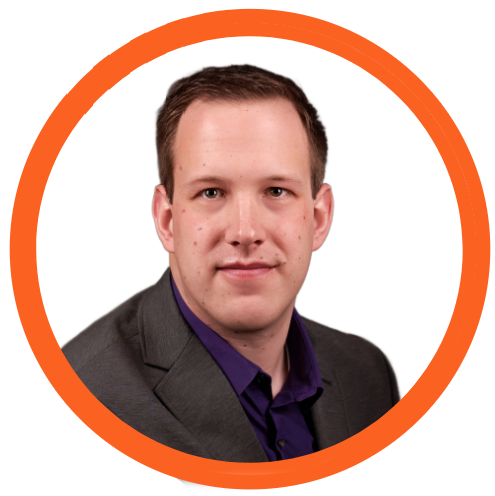
Thanks go to Isaac Luther for his contribution of this case study. Luther is a senior product engineer on the new product development team at TWB Company. TWB Company provides tailor-welded solutions in North America. In this role, Isaac is responsible for application development in vehicle body and frame applications and battery systems. Isaac has a Bachelor of Science in welding engineering from The Ohio State University.
Back to the Top