3rd Generation Steels
- TRIP-Assisted Bainitic Ferrite (TBF) and Carbide-Free Bainite (CFB)
- Quenched and Partitioned Grades, Q&P or simply QP
- Medium Manganese Steels, Medium-Mn, or Med-Mn
First Generation Advanced High-Strength Steels (AHSS) are based on a ferrite matrix for baseline ductility, with varying amounts of other microstructural components like martensite, bainite, and retained austenite providing strength and additional ductility. These grades have enhanced global formability compared with conventional high strength steels at the same strength level. However, local formability challenges may arise in some applications due to wide hardness differences between the microstructural components.
The Second Generation AHSS grades have essentially a fully austenitic microstructure and rely on a twinning deformation mechanism for strength and ductility. Austenitic stainless steels have similar characteristics, so they are sometimes grouped in this category as well. 2nd Gen AHSS grades are typically higher-cost grades due to the complex mill processing to produce them as well as being highly alloyed, the latter of which leads to welding challenges.
Third Generation (or 3rd Gen) AHSS are multi-phase steels engineered to develop enhanced formability as measured in tensile, sheared edge, and/or bending tests. Typically, these steels rely on retained austenite in a bainite or martensite matrix and potentially some amount of ferrite and/or precipitates, all in specific proportions and distributions, to develop these enhanced properties.
Individual automakers may have proprietary definitions of 3rd Gen AHSS grades containing minimum levels of strength and ductility, or specific balances of microstructural components. However, such globally accepted standards do not exist. Prior to 2010, one steelmaker had limited production runs of a product reaching 18% elongation at 1000 MPa tensile strength. Starting around 2010, several international consortia formed with the hopes of achieving the next-level properties associated with 3rd Gen steels in a production environment. One effortU-11, S-95 targeted the development of two products: a high strength grade having 25% elongation and 1500 MPa tensile strength and a high ductility grade targeting 30% elongation at 1200 MPa tensile strength. The “exceptional-strength/high-ductility” steel achieved 1538 MPa tensile strength and 19% elongation with a 3% manganese steel processed with a QP cycle. The 1200 MPa target of the “exceptional-ductility/high-strength” was met with a 10% Mn alloy, and exceeded the ductility target by achieving 37% elongation. Another effort based in EuropeR-22 produced many alloys with the QP process, including one which reached 1943 MPa tensile strength with 8% elongation. Higher ductility was possible, at the expense of lower strength.
3rd Gen steels have improved ductility in cold forming operations compared with other steels at the same strength level. As such, they may offer a cold forming alternative to press hardening steels in some applications. Also, while 3rd Gen steels are intended for cold forming, some are appropriate for the hot stamping process.
Like all steel products, 3rd Gen properties are a function of the chemistry and mill processing conditions. There is no one unique way to reach the properties associated with 3rd Gen steels – steelmakers use their available production equipment with different characteristics, constraints, and control capabilities. Even when attempting to meet the same OEM specification, steelmakers will take different routes to achieve those requirements. This may lead to each approved supplier having properties which fall into different portions of the allowable range. Manufacturers should use caution when switching between suppliers, since dies and processes tuned for one set of properties may not behave the same when switching to another set, even when both meet the OEM specification.
There are three general types of 3rd Gen steels currently available or under evaluation. All rely on the TRIP effect. Applying the QP process to the other grades below may create additional high-performance grades.
- TRIP-Assisted Bainitic Ferrite (TBF) and Carbide-Free Bainite (CFB)
- TRIP-Assisted Bainitic Ferrite (TBF) and Carbide-Free Bainite (CFB) are descriptions of essentially the same grade. Some organizations group Dual Phase – High Ductility (DP-HD, or DH) in with these. Their production approach leads to an ultra-fine bainitic ferrite grain size, resulting in higher strength. The austenite in the microstructure allows for a transformation induced plasticity effect leading to enhanced ductility.
- Quenched and Partitioned Grades, Q&P or simply QP
- Quenching and Partitioning (Q&P) describes the processing route resulting in a structure containing martensite as well as significant amounts of retained austenite. The quenching temperature helps define the relative percentages of martensite and austenite while the partitioning temperature promotes an increased percentage of austenite stabile room temperature after cooling.
- Medium Manganese Steels, Medium-Mn, or Med-Mn
- Medium Manganese steels have a Mn content of approximately 3% to 12%, along with silicon, aluminum, and microalloying additions. This alloying approach allows for austenite to be stable at room temperature, leading to the TRIP Effect for enhanced ductility during stamping. These grades are not yet widely commercialized.
TRIP Assisted Grades, like TRIP-Assisted Bainitic Ferrite (TBF)
and Carbide-Free Bainite (CFB)
During the slow cooling of conventional steels, austenite transforms into a microstructure containing alternating regions of ferrite and cementite. Note that cementite is the name given to iron carbide with the composition Fe3C. At higher magnification, this microstructure looks like Mother-of-Pearl, leading to its name of pearlite.
Depending on the chemistry and thermal profile, rapid controlled cooling produces new microstructures which are not achievable with slow cooling, including martensite, austenite, and bainite. Bainite consists of regions of dislocation-rich (higher strength) ferrite separated by austenite, martensite, and/or cementite. These phases within bainite have relatively small hardness differences, leading to improved local formability compared with conventional dual phase or TRIP steels. Producing a fully-bainitic microstructure is challenging, so bainite is usually accompanied by other phases, resulting in ferrite-bainite steels or complex phase.
With an appropriate chemistry and use of specific thermal profiles capable of holding at specific temperatures and even reheating after quenching further reduces the size of these microstructural components, and essentially eliminates the production of the low-ductility cementite (iron carbide). Large “blocky” austenite, characteristic of 1st Generation TRIP steels, is minimized and instead thin fine submicron austenitic laths form (Figure 1).
Figure 1: On the left, the typical bainitic structure showing bainitic ferrite laths with interlath carbideS-96; On the right is the microstructure of TRIP Assisted Bainitic Ferrite / Carbide Free Bainite showing bainitic ferrite laths interwoven with thin films of untransformed retained austenite.C-31 αb is bainitic ferrite and γ is retained austenite. Note the slightly different magnification.
The fine components result in higher strength, similar to fine grain size being associated with increased strength. Since the ferrite is higher strength than conventional bainite due to the fine component size and even greater dislocation density, the component hardness difference is further minimized, leading to additional improvements in local formability. The austenite promotes the TRIP effect, resulting in greater uniform elongation and enhanced global formability. Combined, these features result in calling this microstructure either TRIP Assisted Bainitic Ferrite (TBF) or Carbide Free Bainite (CFB). Some sources suggest this is the same product as “Dual Phase with High Ductility,” abbreviated as DP-HD or simply DH.H-18, A-70, R-23, B-58 TBF, CFB, DP-HD, and DH are used interchangeably.
One potential processing route (Figure 2) may involve intercritically annealing in the two-phase austenite+ferrite region, cooling slightly to promote ferrite formation (1→2), and then quenching (2→3) to a temperature below the start of bainite formation (Bs) while remaining above the Ms temperature, the start of martensitic transformation. Once the targeted amount of bainite has formed in an isothermal overaging step (3→4), the steel is then quenched to room temperature (4→5).
These steels are characterized by a good balance of strength and global formability (as measured by high TSxEL, uniform elongation, and total elongation combined with low YS/TS) against local formability (as measured by bend angle and hole expansion ratio).C-31 A YS/TS ratio of approximately 0.7, similar to DP steels, is a characteristic of these grades.H-59, C-31
These steels exhibit a significant bake hardening response. One study found a BH kick of over 200 MPa after a 4% prestrain and a bake cycle of 30 minutes at 200 °C. The total hardening response (strain hardening plus bake hardening) was almost 800 MPa.T-41 However, in production, this paint bake cycle is not likely to be practical due to paint over curing and the preference for faster cycle times. A different study evaluated TBF700Y/1050T and found after 15 minutes at 195 °C, samples prestrained to 4.5% had a BH kick of 150 MPa, with a total hardening response in excess of 350 MPa.B-60
Challenges exist when producing these grades with a galvanized or galvannealed coating. The relatively higher silicon content needed to suppress carbide formation may lead to difficulties galvanizing and with galvanized surface quality. Replacing silicon with aluminum helps with the coating issues, but makes the thermal cycle more complex. The chosen thermal cycle needs to be appropriate for the selected chemistry and targeted properties, and constrained by the capabilities of the existing mill equipment. Descriptions of the capabilities of equipment used in the production of cold rolled and galvanized AHSS are found elsewhere.K-43, B-59
The 2013 Infiniti Q50 is one of the earliest production applications for TBF 1180, where it formed 4% of the Body-In-White mass. Applications included A- and B-pillar reinforcements, sill reinforcements, and roof rail and side reinforcements. Adjusted welding techniques resulted in the same stress concentration as seen when welding mild steels.I-22, K-44 The same grade applied on the 2015 Nissan Murano in the A-Pillar Inner and reinforcements allowed numerous components to be downgauged from 1.6 mm to 1.2 mm compared with the prior version.C-32 1180TBF represented over 6% of the mass of the 2016 Nissan Maxima body-in-white, primarily applied in the A- and B-Pillar Reinforcements. Typically, 1.4 mm thick 980 grade steel was downgauged to 1.2 mm.C-33
A sample of commercially available TBF1180 was shown to have 946 MPa yield strength, 1222 MPa tensile strength, 18% elongation (JIS sample) , with a 40% hole expansion ratioM-54, which is consistent with the minimum properties listed by one automotive OEM: YS: 850 MPa minimum, TS: 1180 MPa minimum, elongation: 14% JIS minimum, and 30% minimum hole expansion ratio.F-36 Stretch formability as tested using a dome height evaluation was shown to be comparable to a conventional DP980 product, with deep drawability characterized by forming height in a cup draw test being superior to both conventional DP980 and DP1180.
Stress-strain curves of TBF700Y/1050T are found in the literature and presented in Figure 3 for reference. Note that these are random samples from a commercially available product tested at different laboratories, and therefore may not be representative of all products of this grade.
Figure 3: Stress strain curves of commercially available TBF 700Y/1050T. A) YS=775 MPa, TS = 1235 MPa, EL = 10%G-44; B) YS=751 MPa, TS = 1035 MPa, EL = 17%. Also shown is the pre-strain and bake hardening response for 1.0 mm thick blanks, tested after a 20 minute dwell time in a 170 °C furnace.B-60
The 2018 Infiniti QX50 SUV is an example of a vehicle believed to have TBF980 in the body structure.I-23 The product shown is called SHF980, and has a microstructure of approximately 50% ferrite, approximately 10% retained austenite, with the remainder as martensite/bainite, which is consistent with expectations for a TBF product. The thermal processing route to achieve this microstructural balance is consistent with a Quenching & Partitioning process (Figure 4). Both SHF980 and the reference DP980 are shown to have 660 MPa yield strength and 1000 MPa tensile strength. However, where DP980 has 15% elongation, SHF980 has 23% elongation. In addition, SHF980 is capable of 10% greater energy absorption over DP980 at the same thickness.I-23
Figure 4: Production and properties of SHF980, possessing a TBF microstructure.I-23
The highest strength TBF grade commercially available has 1,470MPa minimum tensile strength. Properties in Table 1 are compared with DP1470.
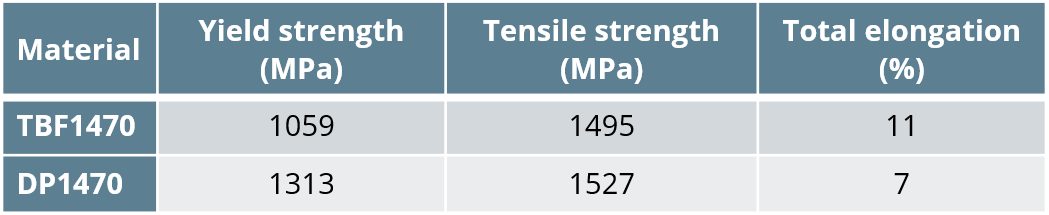
Table 1: Tensile properties of 1.2mm steels with 1470 MPa minimum tensile strength.M-55
Case Study: Production Application Where 3rd Gen Steels
Reduced Weight and Improved Performance
Toyota Motor Europe designed a part requiring a minimum tensile strength of 980 MPa, but when stamped using a conventional AHSS grade, experienced both global formability (necking) failures and local formability (sheared edge) failures (Figure 5). In the search for a grade which blended the high elongation of dual phase grades and the high hole expansion of complex phase grades, Toyota chose TBF980, a TRIP-assisted bainitic ferrite grade with the same yield and tensile strength of a conventional 980 grade but with improved elongation of approximately 14% and hole expansion of approximately 65%.A-1
Also reported were grade and design changes in a production vehicle where the strength of TBF980 allows for a 20% thickness reduction over the prior model. The improved formability of TBF980 facilitated a reduction in packaging space of the component, with the new design being 6% narrower and 20% shorter. Combined, these improvements reduced the vehicle weight by 1 kg.A-1
Figure 5: 980 MPa part with global and local formability failures. Converting the steel to TBF980 eliminated both types of splits. Image adapted from Citation A-1.
Quenched and Partitioned Grades, Q&P or simply QP
Quenching and partitioning (Q&P, or QP) describes a multi-step heat treatment which produces high tensile strength, high global ductility (total elongation) and high local ductility (hole expansion and bendability), compared with other similar strength steels. The QP process was first explained in 2003 by Speer et al.S-97, S-98, S-99
Among the unique aspects of the required thermal cycle is that after the first quench from the fully austenitized or intercritical annealing temperature, the steel may be reheated to a higher temperature, and then quenched to room temperature.
Figure 6 provides a general overview of the QP thermal cycle. After austenitization in either the single phase austenite region or the two-phase ferrite+austentite (intercritical annealing), the steel is quenched to a temperature below the start of martensitic transformation (Ms) but above the Mf (temperature at which all austenite has transformed to martensite), as indicated by segment 1→2. In the two-step QP process, the temperature is raised above Ms, shown in segment 2→3. No temperature increase is seen in the one-step QP process, meaning 2=3. Then the steel is held at this partitioning temperature for the appropriate time to generate the targeted microstructure and properties, segment 3→4. Once reached, the steel is quenched again (4→5), this time to a temperature below Mf, the temperature below which all transformation to martensite has occurred.
The QP microstructure contains martensite and austenite. Ferrite is also present if intercritical annealing in the two-phase region is employed rather than in the single-phase austenitic region. The first quench forms a controlled volume fraction of martensite. With a QP chemistry containing C between 0.15 and 0.4%, Mn between 1.5 and 2.5%,and (Al + Si) around 1.5 wt.%, the quenching temperature usually lies in the range 200 to 350 °C.S-100 After raising to the partitioning temperature typically between 300 to 500 °CS-100, an isothermal hold allows carbon from the carbon-supersaturated martensite to diffuse into the untransformed austenite. This enriches the austenite with carbon while similarly depleting the martensite. The carbon enriched austenite increases its room temperature stability. Since the partitioning temperature above that required for martensite formation, some of the martensite transforms to tempered martensite. Tempered martensite provides high strength with more ductility than untempered martensite. After the partitioning step, the final quench results in the formation of fresh martensite.
When stamping parts from this steel, the austenite transforms to newly formed martensite through the TRIP effect, enhancing the ductility and strength. Adjusting the chemistry, quenching temperature, partitioning temperature, and partitioning time affects the amount, morphology, and stability of the retained austenite, leading to a wide range of potential properties.D-32 The microstructure of commercial Q&P steels is composed of martensite (50–80%) formed during quenching, ferrite (20–40%) formed as austenite slowly cools, and dispersed retained austenite (5–10%) stabilized by carbon enrichment during partitioning. Higher strength QP steels will have reduced amounts of ferrite.W-35 This is mostly consistent with a study highlighting commercially produced QP980 and QP1180 which showed that both products have approximately 10-12% retained austenite, with QP980 containing 56% ferrite / 32% martensite and QP1180 containing 21% ferrite / 69% martensite.W-36
There is no standard processing route with defined chemistry and temperatures. The complex thermal cycle needs to be appropriate for the selected chemistry and targeted properties, and constrained by the capabilities of the existing mill equipment. Citation K-43 presents descriptions of the equipment and capabilities used at one location. Process variants exist, such as a one-step approach using the same temperature for the initial quench and the partitioning.S-98 Other modifications allow for production of a Carbide-Free Bainitic structure during the first quench, improving the damage resistance due to additional strain-hardening capacity within the local plasticity deformation zone near the tips of micro-cracks.G-45
The Q&P process is applicable to other products as well, including stainless steelsM-56, M-57, S-101 and Press Hardening Steels.A-71, A-72, X-1 A one-step Q&P approach was applied to a laser welded blank with 22MnB5 and TRIP components, resulting in tailored properties to improve the intrusion resistance and energy-absorption capabilities in the pertinent regions.K-46
Complex phase steels with High Ductility (CP-HD, or CH) have similar microstructural constituents, along with bainite. Although CH steels reach high hole expansion values, they do not have the elongation levels typically associated with QP steels. Still, some sources equate CH and QP steels.H-18
Two levels of Quenched & Partitioned steels are in global production, 980 MPa and 1180 MPa. The enhanced properties of QP steels offer benefits over similar-strength steels of other microstructures. Compared against Dual Phase steel with similar yield and tensile strength, a Quenched & Partitioned steel showed higher uniform elongation, total elongation, work hardening index, and FLC0, highlighted in Table 2 and Figure 7.C-34 A different production supplier of QP980 reports similar strength and elongation properties, with a targeted 23% hole expansion ratio.G-46

Table 2: Tensile properties of production DP980 and QP980.C-34
Figure 7: Comparison of Forming Limit Curves of production DP980 and QP980.C-34
QP980 is seeing expanded use in automotive production. The 2016 Chevrolet Sail from SAIC-GM represented the first application at General Motors.H-60 The 2021 Ford Bronco uses hot dip galvanized QP980 in five components of the front and rear floor assemblies.S-102 Sixty percent of the body structure of the 2021 Jeep Grand Cherokee L is made from AHSS, with some parts stamped from 3rd Gen steels.F-37
Table 3 contains typical mechanical property ranges for industrially produced QP980 and QP1180.W-35 A typical strain–stress curve of QP980 is shown in Figure 8.
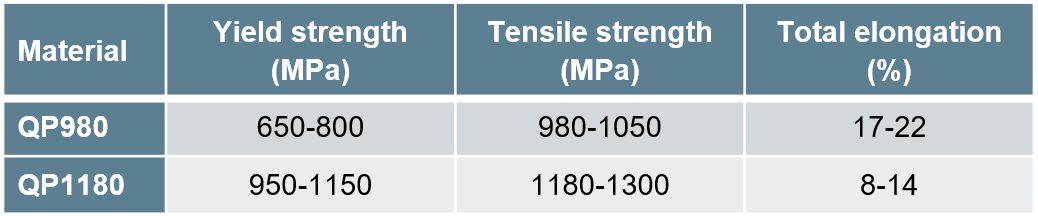
Table 3: Typical mechanical property ranges for industrially produced QP980 and QP1180.W-35
Figure 8: Stress-strain curve of industrially produced QP980.W-35
Of course, there are additional characteristics beyond strength and elongation that impact successful use in manufactured products. Typical forming-limit curves for cold rolled QP980, DP780, and DP 980 steels are shown in Figure 9, highlighting that the formability of QP980 is comparable to that of DP780.
Figure 9: Forming-limit curves for 1 mm thick Q&P 980, DP 780, and DP 980.W-35
Figure 10 contains the results of high strain rate tensile testing, confirming that QP980 has positive strain rate sensitivity and therefore has the potential for improved crash energy absorption.
Figure 10: True stress-strain curves for QP980 generated at different strain rates.W-35
Sheared-edge ductility is also a concern in AHSS grades. Hole expansion of QP1180, QP980, and DP980 is compared in Figure 11, with similar results seen in QP980 and DP980. QP1180 had the highest hole expansion, possibly because of its microstructure containing components of relatively uniform hardness.
Figure 11: Hole expansion of QP1180, QP980, and DP980, generated from either punched or machined holes.W-35
The bending under tension test was used to determine the critical R/t value below which the risk for shear fracture increases. These experiments showed that critical R/t values of QP980 were close to those of other steels having 600 MPa tensile strength.W-35
Similar springback was observed in QP980 and DP980 when a 5 mm radius was used in the bending-under-tension test, with QP980 exhibiting less springback when a 12.7 radius die was used instead.W-35
General Motors provided stress-strain curves for production QP700/1180 tested at different strain rates (Figure 12), showing increases in strength and ductility as strain rates increase.H-60
Figure 12: Engineering stress-strain curves for QP700Y/1180T at different strain rates.H-60
A recent conference highlighted several applications (Figure 13) where thinner gauge QP980 replaced DP590 in General Motors vehicles.W-37
Figure 13: Replacing DP590 with QP980 allows for downgauging.W-37
The same presentationW-37 showed the example of QP980 replacing press hardening steels in B-pillar reinforcements and door anti-intrusion beams in a First Auto Works vehicle, Figure 14.
Figure 14: QP980 may replace press hardening steels in some safety applications.W-37
Medium Manganese Steels, Medium-Mn, or Med-Mn
Manganese has a lower density than iron, so using alloys with higher amounts of manganese truly creates lightweight products. 1st Generation steels typically contain no more than around 2% Mn. 2nd Generation TWIP steels have about 20% Mn. Lean medium-manganese (MedMn) steels typically use between 3% and 12% manganese along with silicon, aluminum, and microalloying additions.R-16, D-27, S-80, K-35 Aluminum in these steels further lowers the density.
No standard chemistry or processing route exists, but several studies use a thermal cycle similar to that seen with Q&P steels. This approach leads to a complex multiphase fine-grained microstructure. Compared with QP steels at the same strength levels, the higher manganese levels of Med-Mn steels promote greater amounts of retained austenite, and therefore greater ductility through the TRIP Effect. One study showed a combination of 1400 MPa tensile strength and a total elongation of 18%.S-103
One difference from the thermal cycle to produce QP steels used by some researchers to process Med-Mn steels is that after intercritical (two-phase) annealing, the quench is to room temperature rather than simply below Ms, the start of martensitic transformation.S-80 This is facilitated by the high levels of manganese, which adjusts the Mf below room temperature. Quenching a steel containing 0.25% C, 8.23% Mn, 1.87% Si, 0.05% Ni, and 0.24% Mo to room temperature and subsequently partitioning at 300 °C led to tensile strengths greater than 1800 MPa combined with total elongations of approximately 15%.S-80
In addition to lowering the Mf (martensite finish) level below room temperature, the manganese levels are sufficiently high enough that the coils after hot rolling may be either partially or fully martensitic. This phenomenon means that it may be possible to produce hot rolled Med-Mn steels.
Another production method called Austenite-Reverted Transformation (ART) annealing results in a large percentage of retained austenite in medium manganese steels. The fully or partially martensitic hot or cold rolled coil is heated to the single phase austenite region or the intercritical two phase austenite+ferrite region where the martensite reverts to austenite – hence the name of the process. The austenite nucleates on the former sites of fine martensitic features. This approach results in a final product with extremely fine features. During annealing, diffusion of both carbon and manganese occurs, which determines both the phase fraction and stability of the retained austenite. Processing of Fe–0.3C–11.5Mn–5.8Al resulted in a microstructure with 60% retained austenite.B-59
Multi-step thermal treatments are one approach to control the relative proportions of martensite, ferrite, and austenite. One example, termed “double-soaking” (DS), aims for substantial Mn-enrichment of austenite in a first soaking step followed by a second soaking step at a higher temperature which leads to a greater fraction of martensite in the final product. The brief second soak is long enough to allow the carbon to partition, but not long enough for manganese partitioning to occur, producing regions of higher and lower Mn within the austenite. The higher-Mn regions allow for greater amounts of austenite in the final product, while the lower-Mn regions transform to martensite, leading to TRIP-effect ductility and high strength.S-80, G-47 In an industrial environment, the initial soak may be done in a batch anneal furnace, with the brief second soak targeted for the time and temperature available in continuous annealing or galvanizing lines.
Still another production method proposed is known as Deforming and Partitioning (D&P). This route uses a warm rolling followed by cold rolling to generate an extremely high dislocation density. A subsequent partitioning treatment relieves the residual stresses from rolling and stabilizes the retained austenite via carbon enrichment. Figure 15 shows a representative Deforming and Partitioning thermal cycle. A D&P MedMn steel with a composition of 0.47C–10Mn–2Al–0.7V reached a yield strength of 2.2 GPa (2,200 MPa) and a uniform elongation of 16%.H-65
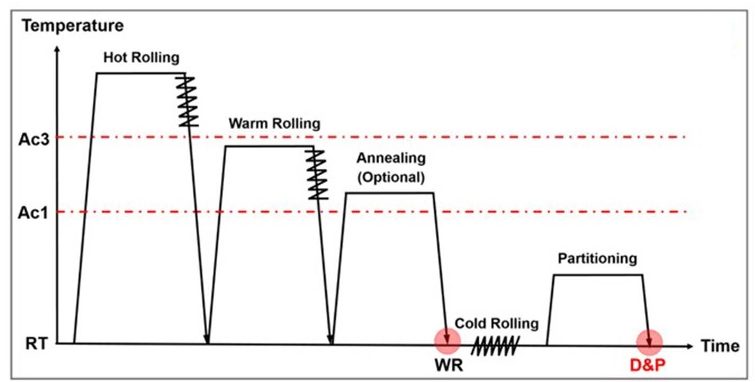
Figure 15: Representative Deforming and Partitioning (D&P) thermal cycle.H-65
Medium-manganese steels with Mn contents between 3 wt.% and 10 wt.% have a microstructure consisting of an ultra-fine grained ferritic matrix (grain size < 1 μm) with up to 40 vol.% retained austenite.K-47 A chemistry of Fe-7.9Mn-0.14Si-0.05Al-0.07C resulted in 39% retained austenite with the processing route evaluated.Z-10
Properties are dependent on all aspects of the chosen chemistry and thermal cycle. With an appropriate approach, the steel may exhibit both a transformation-induced plasticity (TRIP) effect and a twinning-induced plasticity (TWIP) effect.
Studies indicate that Medium Manganese steels are also suitable for use in press hardening applications. A studyL-63 indicates that an alloy with 0.14 %C – 7.0 %Mn rivals conventional 22MnB5 PHS1500 in strength, but has more ductility. After hot forming and processing through a typical paint bake cycle, 22MnB5 exhibited a tensile strength of 1510 MPa, a uniform elongation of 4.6%, and a total elongation of 7.3%. The MedMn steel showed values of 1565 MPa, 9.6% and 11.7% respectively. These enhanced properties are suspected to be associated with the high volume fraction (15%) of retained austenite found in the Medium Manganese steels.
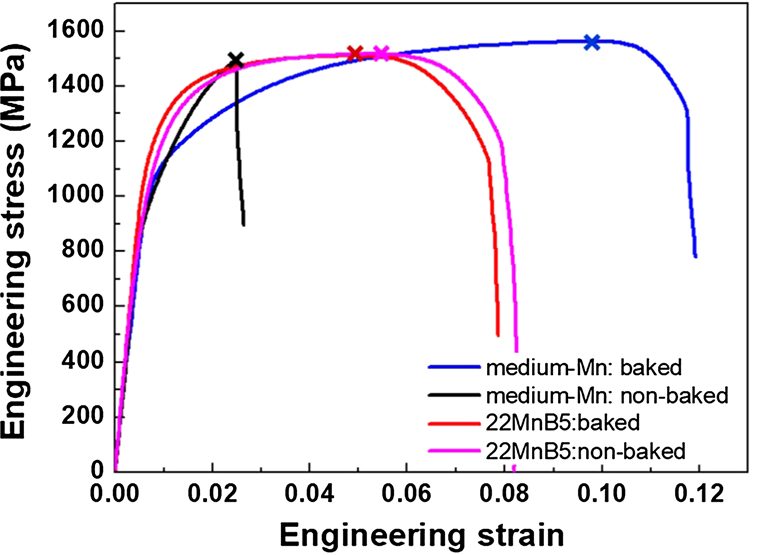
Figure 16: Engineering stress–strain curves of the medium-Mn martensitic steel and 22MnB5. L-63
Unlike TBF and QP steels, Medium-Manganese steels may exhibit discontinuous yielding, also known as yield point elongation or Lüders bands. Depending on chemistry and processing, these may extend beyond 5% engineering strain.
Medium manganese steels are not yet widely commercialized. They were the focus of an entire issue of a technical journal.M-58 The lead Editorial presents an overview of prior studies and highlights areas of interest.R-16
Consortia Activities
The European Commission through the European Research Executive Agency has funded a multi-year study called WarP-AHSS, which stands for Warm Press-Formed Zinc-Coated Third Generation Advanced High Strength Steels with High Crash and Corrosion Resistance and Minimized Microcracking.
The WarP-AHSS project seeks to develop end-to-end processing of warm press-formed parts from zinc-coated Medium Manganese Steels. This approach is expected to reduce the reheating and warm press-forming temperatures, making the process greener and energy-efficient, while allowing the use of zinc-coated sheets without liquid metal embrittlement-induced micro-cracking during warm-forming.
Partners in the WarP-AHSS research project include a steelmaker, an automaker, a university, and two research institutions. The project runs from October 2023 through March 2027.
The European Research Executive Agency has funded another multi-year study, Sup3rForm, that seeks to optimize the production and use of both 3rd Generation Q&P and medium-Mn steels. The Sup3rForm consortium, coordinated by Eurecat Technology Centre, is made up of eight partners, including steelmakers, an automaker, tier suppliers, and universities. Sup3rForm runs from July 2023 through December 2026.