homepage-featured-top, main-blog
In this edition of AHSS Insights, George Coates and Menachem Kimchi get back to basics with important fundamentals in forming and joining AHSS.
As the global steel industry continues its development of Advanced High-Strength Steels (AHSS), including 3rd Gen products with enhanced formability, we’re reminded that successful application is still dependent on the fundamentals, both in forming and joining. In this blog article, we address some of those forming considerations, as well as highlighting common joining issues in manufacturing.
Forming Considerations
The somewhat lower formability of AHSS compared to mild steels can almost always be compensated for by modifying the design of the component and optimizing blank shape and the forming process.
In stamping plants, we’ve observed inconsistent practices in die set-up and maintenance, surface treatments and lubrication application. Some of these inconsistencies can be addressed through education, via training programs on AHSS Application Guidelines. These Guidelines share best practices and lessons learned to inform new users on different behaviors of specific AHSS products, and the necessary modifications to assist their application success. In addition to new practices, we’ve learned that applying process control fundamentals become more critical as one transitions from mild steels to AHSS, because the forming windows are smaller and less forgiving, meaning these processes don’t tolerate variation well. If your present die shop is reflective of housekeeping issues, such as oil and die scrap on the floor or die beds, you are a candidate for a shop floor renovation or you will struggle forming AHSS products.
Each stamping operation combines three main elements to achieve a part meeting its desired functional requirements:
There is good news, in that our industry is responding with new products and services to improve manufacturing performance and save costs.
As an example, lubrication application is often overlooked, and old systems may be ineffective. In the forming of AHSS, part temperatures can become excessive, and break down lubricant performance. Figure 1 shows an example of part temperatures from an Ohio State University study conducted with DP 980 steels.O-1

Figure 1: Example Temperature distribution for DP 980 Steel.O-1
Stampers often respond by “flooding” the process with extra lubricant, thinking this will solve their problem. Instead, lubricant viscosity and high temperature stability are the most important considerations in the lubricant selection, and new types exist to meet these challenges. Also, today there are new lubrication controllers that can finely control and disperse wet lubricants evenly across the steel strip, or in very specific locations, if forming requirements are localized. These enable better performance while minimizing lubricant waste (saving cost), a win-win for the pressroom.
Similarly, AHSS places higher demands on tool steels used in forming and cutting operations. In forming applications, galling, adhesive wear and plastic deformation are the most common failure mechanisms. Surface treatments such as PVD, CVD and TD coatings applied to the forming tool are effective at preventing galling. Selection of the tool steel and coating process used for forming AHSS will largely depend on the:
- Strength and thickness of the AHSS product,
- Steel coating,
- Complexity of the forming process, and
- Number of parts to be produced.
New die materials such as “enhanced D2” are available from many suppliers. These improve the balance between toughness, hardness and wear resistance for longer life. These materials can be thru-hardened, and thus become an excellent base material for PVD or secondary surface treatments necessary in the AHSS processing. And new tool steels have been developed specifically for hot forming applications.
Joining Considerations
In high-volume production different Resistance Spot Welding (RSW) process parameters can be used depending on the application and the specifications applied. Assuming you chose the appropriate welding parameters that allows for a large process window, manufacturing variables may ruin your operation as they strongly effect the RSW weld quality and performance.
Material fit-up
One of the great advantages of the RSW process is the action of clamping the material together via the electrode force applied during the process. However due to the pre-welding condition/processing such as the stamping operation, this fit-up issue, as shown in Figure 2, can be very significant especially in welding an AHSS product. In this case the effective required force specified during the process setup for the application is significantly reduced and can result in an unacceptable weld, over-heating, and severe metal expulsion. If the steels are coated, higher probability for Liquid Metal Embrittlement (LME) cracking is possible.

Figure 2: Examples of Pre-Welding Condition/Processing Fit-Up Issues.
For welding AHSS, higher forces are generally required as a large part of the force is being used to force the parts together in addition to the force required for welding. Also, welding parameters may be set for pre-heating with lower current pulses or current up-slope to soften the material for easier material forming and to close the gap.
Electrodes Misalignment
During machine set up, the RSW electrodes need to be carefully aligned as shown in Figure 3A. However, in many production applications, electrode misalignment is a common problem.
Electrode misalignment in the configurations shown in Figure 3B may be detrimental to weld quality of any RSW application. Of course, the electrode misalignment shown in this figure is exaggerated but the point is that it happens frequently on manufacturing welding lines.
In these cases, the intendent contact between the electrodes is not achieved and thus the current density and the force density (pressure) required for producing an acceptable weld cannot be achieved. With such conditions, overheating, expulsion, sub-size welds and extensive electrode wear will result. Again, if coated steels are involved, the probability for LME cracking is higher.
Note also that following specifications or recommendations for water cooling the electrode is always important for process stability and extending electrode life.

Figure 4: Sequence of Squeeze Time and Welding Current Initiation.
Squeeze Time
The squeeze time is the time required for the force to reach the level needed for the specific application. Welding current should be applied only after reaching this force, as indicated in Figure 4. All RSW controllers enable the easy control of squeeze time, just as with the weld time, for example. In many production operations, a squeeze time is used that is too low due to lack of understanding of its function. If squeeze time is too low, high variability in weld quality in addition to severe expulsion will be the result.
The squeeze time required for an application depends on the machine type and characteristics (not an actual welding parameter such as weld time or welding current for example).
Some of the more modern force gauges have the capability to produce the curve shown in the Figure so adequate squeeze time will be used. If you do not know what the required squeeze time for your machine/application is, it is recommended to use a longer time.
For more on these topics, browse the Forming and Joining menus of these Guidelines.
Blog, main-blog
Forty years ago, the metal forming community needed to figure out how to stamp a new exotic family of steels making inroads into automotive body construction. These grades, called High Strength Low Alloy steels, were much stronger than the commonplace mild steels, and were more formable than the high-strength options available at that time. Initially, only a few steelmakers were able to offer these new grades, but over time more companies added the equipment and know-how necessary to support their customers with these products. Automakers and their supply chain stampers needed to adapt as an increasing number of parts transitioned to HSLA steels.
Fast-forward a few decades, and metal formers are facing similar challenges. Successful forming and joining of Advanced High-Strength Steels is made easier with processes that are tuned to work with the characteristics associated with these alloys. One such technique to improve formability is to employ Active Binder Force Control.
In conventional stamping, a draw ring applies pressure around the binder in order to control the sheet metal flow into the cavity. The ring may be referred to as a binder plate, draw pad, pressure pad, or blank holder. Creating the restraining force typically is done with urethane springs, coil springs, gas springs (like air or nitrogen), or press cushion systems actuated by gas or hydraulic cylinders.
Where the traditional approach applies binder pressure uniformly throughout the press stroke, modern stamping presses can be equipped with cushions having multipoint-control systems (see Figure 1 example). The associated pressure profile can be adjusted around the panel and throughout the stroke to optimize metal flow, prevent splits and wrinkles, and minimize thinning.

Figure 1. An Example of Multi-Point Press Forming Method.P-31
Incorporating Active Binder Control capabilities has several benefits for the press shop, panel quality, and product design, including:
- A segmented blankholder combined with individually programmable hydraulic cylinders, sometimes called a flexible binder, allows for precise control of one segment independent of the others.
- Pulsating blank holder force has been shown to reduce press tonnage requirements and increase metal flow, with the frequency and amplitude being key variables that must be adjusted based on the grade and thickness of interest.
- Pre-acceleration of the cushion reduces shock loading, which minimizes the press-damaging snap-through loads associated with reverse tonnage.
The merits of a variable blank holder force on AHSS springback were documented in a 2004 conference paper.M-63 With the traditional constant binder force approach, springback in the form of side-wall curl was seen in parts made from either a DP590 grade or a mild steel grade used as a control. Increasing the constant binder force helped to reduce springback in the mild steel part.
In Figure 2, CBF reflects tests conducted with constant binder force. VBF-LH and VBF-MLH reflect variable binder force tests conducted with a low-high force profile sequence and a medium-low-high force profile, respectively.

Figure 2: Variable Binder Force Reduces Springback.M-63
By employing a variable binder force, springback of both the mild steel and the DP 590 material was substantially reduced. Employing either variable binder force approach reduced the thinning from forming the DP 590 material, resulting in a more uniform strain distribution across the entire channel profile (Figure 3).

Figure 3: Uniform Strain Distribution Achieved with Variable Binder Force.M-63
More recently, a presentation from 2018 showed CP 800 panel quality improvements associated with variable blank holder force capabilities.D-33 Panel results from a constant binder force of 300 kN and 400 kN are shown in Figures 4 and 5, respectively. Both exhibit severe wrinkling in the flange. Applying 500 kN binder force was not feasible due to exceeding the press tonnage curve limits throughout the stroke.

Figure 4: CP800 Panel Formed with Constant Binder Force of 300 kN, and Associated Close-Up of Flange.D-33

Figure 5: CP800 Panel Formed with Constant Binder Force of 400 kN, and Associated Close-Up of Flange.D-33
Figure 6 shows the panel produced with a variable binder force. The chosen profile fit within the press tonnage requirements and minimized wrinkles.

Figure 6: CP800 Panel Formed with Variable Binder Force Ramping from 300 kN to 600 kN, and Associated Close-Up of Flange.D-33
Active drawbead control is an offshoot of these techniques, allowing for the magnitude and timing of drawbead engagement to be optimized for the requirements of each part. A description of using stake beads to minimize springback is available in the Springback article – active drawbead control is one approach to actuate beads.
The initial laboratory studies relating to active binder force control go back nearly 20 years ago. In the coming years, more information will enter the public domain on how metal formers are using these concepts in production. When you look to purchase a servo press, be sure to ask your press manufacturer about programmable cushions.
Blog, main-blog
Several recent studies are forecasting that; “Within the next 10 to 15 years, urban transportation will be dominated by Electric and Automated vehicles”.B-50 Meaning most of us will be driving Battery Electric Vehicles (BEVs) in the not-distant future. In 2011, just eight years ago, there were only three BEVs on the market with 70 to 80 miles range on a single charge. These were the first generation BEVs. Since then, the number of EVs on the market has increased, with significant improvements in range (now approaching 300 miles). BEV 2020 vehicles cover all current segments, from small cars to SUV’s and trucks (Figure 1). These vehicles will be available from most OEMs as well as several new start-up companies. The construction material for body structures of these vehicles is predominantly steel, while some of the premium vehicles ($60,000 to $100,000) are aluminium. And the prevailing OEM message seems to be “anything TESLA can do, we can do better”.
So how will this change the vehicle body structure design, choice of construction material, its implications for manufacturing and assembly, and ultimately, the impact on automotive steel?
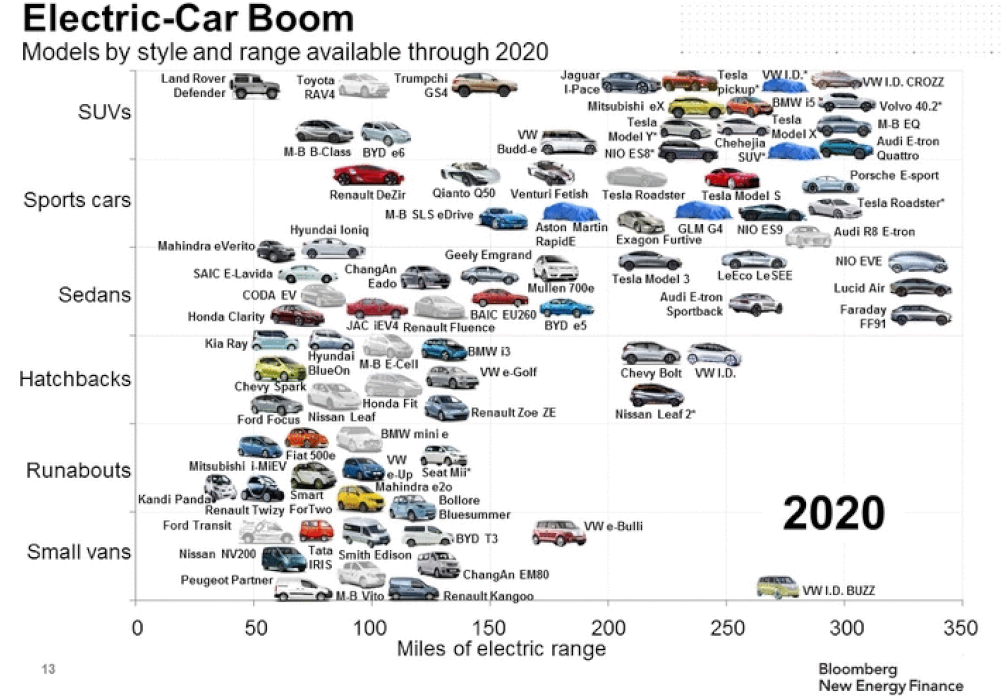
Figure 1: Electric Vehicle Boom – Models by Style and Range Available Through 2020.B-50 CHART SUMMARY: a) Covers all current segments, b) Structures predominantly Steel, c)Some premium vehicles highlight Aluminium, d)Products from most OEMs as well as several new start-up companies.
The driver for this electrification boom is increasing affordability. The upfront cost of BEVs will become competitive on an unsubsidized basis starting in 2024.F-38 By 2030 in the U.S., almost all light duty vehicle segments will reach cost parity as battery prices continue to fall.B-73 Forecasters, such as McKinsey, Morgan Stanley and Bloomberg, predict that about half of all new vehicle production will be electric somewhere between 2035 and 2040. However, Tesla’s CEO Elon Musk’s prediction is much more aggressive. He expects more than half of new vehicles in the U.S. will be electric within the next 10 years, roughly 10 to 15 years ahead of most other predictions.
The Main Drivers of BEV Cost Reduction
- Lithium-ion battery prices have fallen 75% since 2013, hitting $176/kWh in 2018 (Figure 2). Industry-wide prices fell due to the adoption of new cell designs and the availability of higher energy-density cathodes. Prices are expected to drop further in coming years to below $100 per kWh. Besides the reduction in cost, packaging efficiency and the cell energy density also is improving.
- Package space required by other BEV powertrain systems also is being optimized, e.g., motor, transmission, differential and power electronics. This is yielding significant weight and cost reductions, which are then directly reinvested into lower-cost structural materials, such as Advanced High-Strength Steels (AHSS) versus higher cost Aluminium, to keep the overall price of the vehicle low.
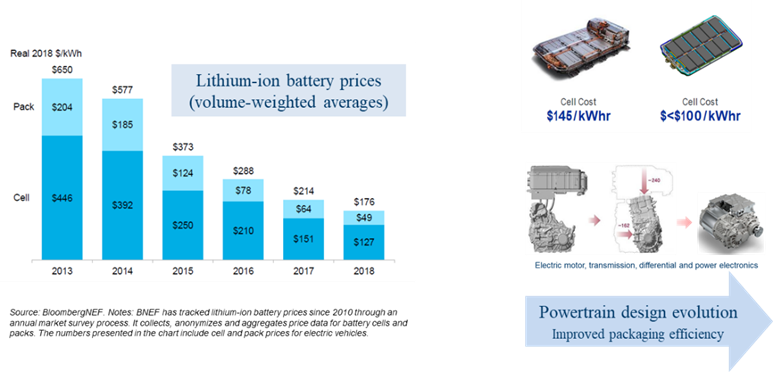
Figure 2: BEV Price Parity with Gas-powered Cars by 2024 – Main Drivers.B-74
BEV to ICE Vehicle Structural Differences and Advantages for Steel
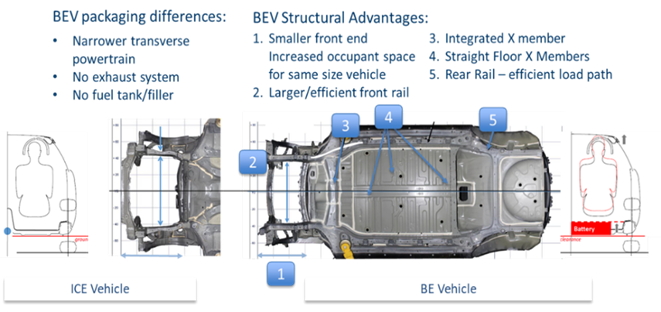
Figure 3: BEV to ICE Vehicle Structural Differences.M-64
BEV packaging differences compared with ICE Vehicles are shown in Figure 3, and include:
- Narrower and compact transverse electric powertrains, leading to shorter front end, with increased occupant space for same size vehicle and larger/efficient front crash rails.
- Lack of an exhaust system eliminates the need for the tunnel, allowing straighter/ efficient cross-members.
- No fuel tank/filler leads to more efficient rear rail load path.
- High voltage electric powertrain and large (300 litres, 500 kg) under-floor battery pack crash protection requirements result in higher safety requirements for BEV front and side structures.
- Safety. The BEV body structure load path requirements are ideal for AHSS application. The floor cross members, without the presence of the tunnel, are straight and can use very high-strength martensitic roll formed sections. Cross members can be stamped from 3rd Generation Steels offering Giga-Pascal strength and over 20% elongation. For frontal crash load management and to minimize passenger/battery compartment intrusions for increased safety, 3rd Generation steels offer the most mass/cost efficient solution. The very high strengths offered by AHSS and UHSS for the safety-critical structural members such as the rocker, rails, cross members and pillars, greatly enhance the required protection of the BEV powertrain and high energy/voltage battery systems. The battery enclosure construction greatly benefits from AHSS usage, providing protection from road-debris impacts from below the vehicle, along with fire protection into the passenger compartment. Advanced steels also enable reduced section sizes for the occupant compartment, required for improved panoramic visibility, without compromising occupant safety and comfort.
- Cost. For widespread adoption of BEVs to occur, the overall cost of the vehicle must be affordable, and its range must be above the ‘range anxiety limit’ of most drivers. Various surveys indicate this range to vary greatly from 75 miles to over 400 miles. Using steel for the vehicle structure leads to the lowest cost BEV, just as with ICE-based vehicles. The vehicle range can be increased through lightweighting and/or by increasing the size of the battery; a cost comparison of these two options is shown in Figure 4. With battery cost reduction approaching $100 per kWh, lightweighting is cost effective at approximately US$2.00 per kg saved. Lightweighting is still very important and the latest steel grades, in particular 3rd Generation steels, offer the most cost-effective lightweighting option. In comparison, if we consider lightweighting with aluminium, the cost is typically in the order of US$6.00 per kg saved. This could be cost effective if the battery cost is over $250 per kWh, which was the case a decade ago. We can see the evidence of this in OEM decisions at that time. For example, the 2011 Nissan Leaf BEV closures were aluminium; but the latest 2019 Nissan leaf BEV closures are steel.
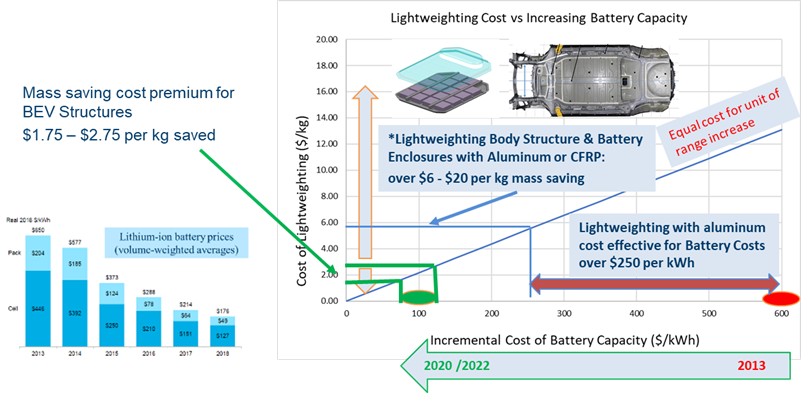
Figure 4: BEV Range Increase – Lightweighting Cost versus Battery Cost 2020 – 2022.M-64
Battery Electric Vehicles – Boom or Bust for AHSS?
For the increased safety required for BEVs to protect the high voltage systems, the structural load paths are ideally suited for the Giga Pascal level strengths offered by AHSS and UHSS. The Battery Enclosure structure offer an additional 85 kg per vehicle opportunity, an increase of approximately 10% sheet metal over ICE vehicles. Also, using advanced steels the BEV structure can take full advantage of well-established body shop practices for manufacturing and assembly, such as stamping, roll forming and spot welding. With future increased focus on BEV affordability, safety and sustainability, steel offers the best solutions and flexibility to address these key challenges.
Blog, main-blog
Here at WorldAutoSteel, we have been studying the changes in the automotive industry for several years, focusing particularly on ride sharing, autonomous, electric vehicles and steel’s role in that marketplace. George Coates, Technical Director for WorldAutoSteel and The Phoenix Group, has been leading that effort and today contributes an article on the disruption of future mobility to the industry and the great opportunities we see for steel in meeting the challenges providers will face. We hope you enjoy the read, and we welcome your thoughts and comments. What changes and impacts do you envision for vehicle manufacture? How do you feel about the world of autonomy?
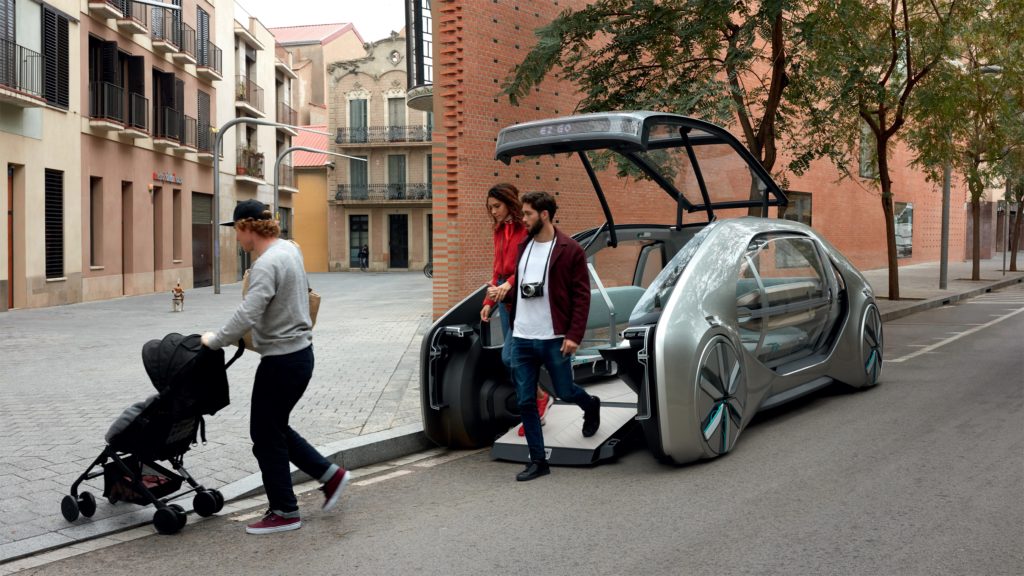
Renault’s Future Mobility concept, the E-Z Go
We’re approaching a critical milestone in automotive history when what we know as normal is about to change significantly. Future Mobility describes the revolution that’s already begun. We’re rethinking transportation from the movement of a vehicle to a more efficient concept for moving people and things. We’re about to discover the social advantages of connected, autonomous, shared and electric vehicles. And we’re completely changing the way we view transportation.
By 2030, electric vehicles (EVs) will be mainstream—not just within the premium segment, as they are today. EV’s will be popular and available across all vehicle variants and prolific in the commercial vehicle industry and in public transportation. Owners and fleet providers will experience the lower costs of electricity, lower maintenance costs, and the lower overall total cost of ownership (TCO). Fully autonomous or self-driving vehicles will introduce design freedom never experienced before, with the removal of the steering wheel, foot pedals and conventional dashboard. Communication and comfort will be re-imagined, with a vehicle that’s no longer designed around the driver but designed to serve the needs and comfort of the occupants, who are now users instead of owners.
With the rise of mobility services such as Uber, Didi, and a host of others, vehicle ownership is fast becoming an option. In a very short time, especially in urban areas such as China’s mega-cities, it is becoming cost-efficient to subscribe to a monthly ride share service for all of your transportation needs.
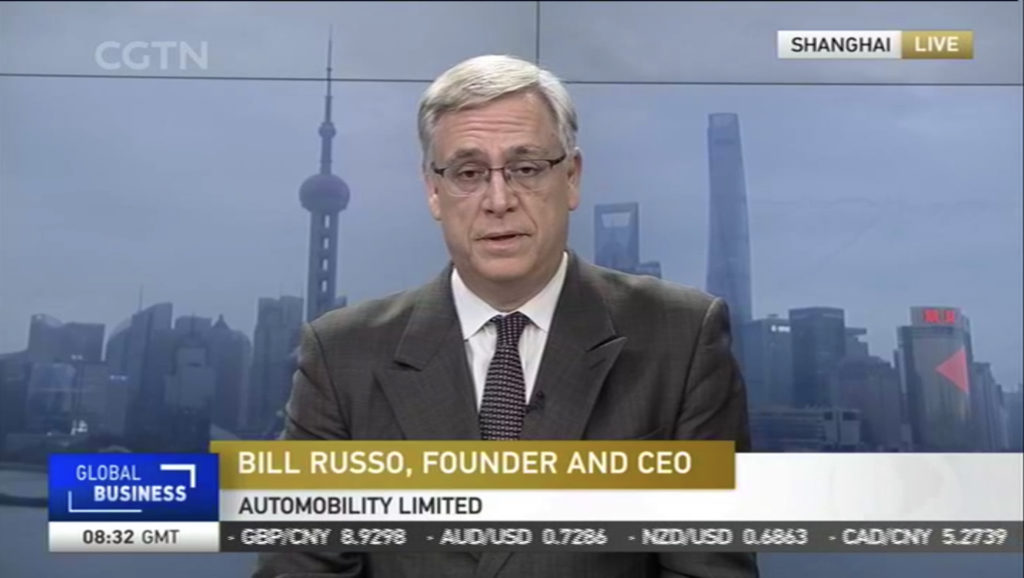
Bill Russo, CEO, Automobility LTD
Bill Russo, CEO of China-based Automobility, in a December 2018 article, Competing in the Digital Internet of Mobility, notes that the digital connectivity of these vehicles will open up profit opportunities well beyond the vehicle hardware. He says “An expanded understanding of mobility use cases and tailoring of the mobility hardware ‘form factor’ to the particular mobility need will be a way to create a value proposition that is rooted in the unique riding experience. In the user-centric world where users are passengers, the focus shifts from traditional driver-centric design to a user-centric productivity space. Instead of traveling in the cockpit, we will move in business class or economy class, depending on our preferences and budget.” Cities will be re-imagined in new social opportunities associated with autonomy, as these vehicles will serve the under-served, and infrastructures will shift in purpose to move people, as opposed to moving vehicles.
Where does steel fit?
The steel industry plans to be right in the middle of this revolutionary change. Fleet owners who provide ride hailing and ride sharing services need to manage the total cost of ownership, while maximizing the user experience for added revenue. To be profitable, they’ll want durable, lasting structures that are affordable to own, provide the user motion as well as emotional comfort, while being efficient to operate, and environmentally friendly – and steel is the only material that meets all these requirements.
On Camera Now: George Coates, Technical Director, WorldAutoSteel and Phoenix Group from worldautosteel on Vimeo.
As always, steel is needed for the crash safety structures, and now add battery protection. Our market intelligence shows that due to the high cost to municipalities and regional governments, autonomous-only vehicles will be limited to dedicated areas for a long time to come. Meanwhile, vehicle-to-vehicle and vehicle-to-infrastructure connectivity will result in dramatic improvements in accident avoidance and reduced fatalities.
Because it will take many years before all vehicles on the road have these technologies in play, the need for passive safety will remain for the foreseeable future. Developing a structural design for the passenger compartment becomes challenging, since there’s a now a need to strike a balance between occupant safety and the occupant freedom. This is enabled by removing the driver and controls from the interior. Steel will be needed to provide the unique properties of both crash energy absorption and deflection, while also managing the loads associated with passengers in multiple and diverse seating configurations. Steel has the ability to provide needed strength while keeping the material thin, which lends more room in the passenger cabin for new seating arrangements and more seats. And battery housings made from steel will provide structural integrity for crash management, while also preventing battery pack damage and leakage.
Lightweighting will continue to be important in an effort to balance smaller battery sizes with maximum range. The steel industry has been and will continue to develop products, such as the ever-growing family of Advanced High-Strength Steels (AHSS), to meet both the mass reduction and the safety targets, affordably. With content innovation and the amazing flexibility of the Iron (Fe) element, researchers still have vast development possibilities for new steels that are stronger, more formable and cost effective.
Blog, main-blog
Introduction
The introduction of Advanced High-Strength Steel (AHSS) to light vehicle body structure applications poses a significant challenge to organizations involved in vehicle repair. AHSS grades are typically produced by non-traditional thermal cycles and contain microstructural constituents whose mechanical properties can be altered by exposure to elevated temperatures. This temperature sensitivity can alter the mechanical behavior during repair welding or flame straightening, thus seriously affecting the structural performance of the AHSS components after the repair.
The American Iron and Steel Institute, with automotive partners – FCA US LLC, Ford Motor Company, General Motors Company – and I-CAR, have completed studies examining the mechanical behavior of various AHSS products after exposure to typical repair arc welding and flame straightening temperature cycles. Recommended practices for repairing components made of these materials were also developed. The studies evaluated many of the AHSS grades being applied and built into vehicle structures today.
AHSS Thermal Evaluation
Several steel grades were evaluated for their sensitivity to thermal exposure taking place during heating to soften the material for straightening, typically by flame. The test results, conclusions and recommendations contained herein are the consensus views of the team members.
A time-temperature test matrix was developed to represent the various thermal conditions encountered during repair welding and flame straightening as shown in Table 1. Individual steel performance result discussions are based on this test matrix and discussed by grade category and specific type.

Table 1: Time-Temperature Test Matrix.
Steel Performance
Conventional Steels
Interstitial free (IF) and high strength low alloy (HSLA) steels are conventional steel products which are essentially a single phase ferrite microstructure and obtain their strength by the addition of chemical elements. These steels have been used in body structures and closures for many years and are well-known to be repairable without substantial performance degradation by arc welding and flame straightening. For repair processes, this means conventional steels can be subjected to heat during repair with the finished repaired component having mechanical properties greater than the properties of the as-received steel. However, it is recommended heating is kept below 750 degrees Celsius to ensure no degradation in properties (Figure 1).

Figure 1: Ultimate tensile strength of Grade 4 IF and HSLA 340 steel after exposure to simulated repair thermal cycles.
Advanced High-Strength Steels
Dual Phase (DP) Steel
DP steels range in strength from 500 MPa to 1200 MPa and obtain their properties from the introduction of a martensitic phase into the ferrite microstructure. The ferrite phase provides formability, while the martensitic phase provides the improved strength. This category of steel grades obtains its microstructure, and thus its mechanical properties through a combination of alloying elements and thermomechanical processing. The processing involves some holding time at elevated temperatures and cooling at specific rates.
Two grades of DP steel were tested, DP 600 and DP 780. The number indicates the ultimate tensile strength (UTS) level of the material in MPa and is the common way to name these grades. UTS for both grades decreases with elevated temperature at a much faster rate than for conventional steels and is illustrated by DP 600 in Figure 2. At temperatures above 650 degrees Celsius the strength suddenly increases then upon additional heating decreases. This behavior is a result of changing the microstructure created during the original thermomechanical processing of the material. Once the microstructure is changed, it is very difficult to return it to its original state in a repair shop environment. Therefore, it is not recommended to subject DP steels to any kind of elevated temperature process for straightening or removing dents. The recommended repair procedure is to remove and replace the DP component. OEM repair guidelines and procedures should be referenced for approved cut and weld lines for replacement.
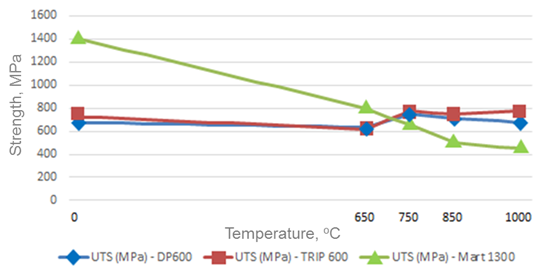
Figure 2: Ultimate tensile strength of advanced high-strength steels after exposure to simulated repair thermal cycles.
Transformation Induced Plasticity (TRIP) Steels
TRIP steels have a similar range of strength as DP steels, 500 MPa to 1200 MPa, while providing improved formability. The improved formability is obtained with the introduction of additional phases of austenite and bainite into the microstructure. These phases improve the work hardening properties of steel and provide additional energy absorption characteristics. TRIP steel microstructures are obtained in a similar manner as DP steels, and therefore have similar behaviors when heating.
TRIP 600 and 780 were evaluated in the studies and confirmed the expected results as demonstrated by TRIP 600 in Figure 2. Heating during repair of TRIP steel will also adversely affect their mechanical properties and thus the performance of the as repaired component may be compromised. OEM recommended repair procedures are similar to DP steels.
Martensitic Steel (MS)
MS steels typically have a microstructure of 100 percent martensite and have tensile properties greater than 980 MPa. Martensite is the strongest microstructural phase in steel and is obtained by alloying and rapid controlled cooling. This grade is used in areas where exceptional strength and anti-intrusion are needed, including such applications as the A-pillars, B-pillars, rockers and rails.
The effect of heat on MS 1300 is shown in Figure 2. Like other AHSS, it is adversely affected by heat and the performance of the as repaired component may be compromised. Thus, heat should be used only as outlined in OEM repair procedures.
Summary
The steel industry, working closely with automotive OEMs and the repair community, have developed and validated repair procedures applicable to the new AHSS used in today’s vehicles. Each OEM has taken the results from the AHSS repairability studies and developed their own repair guidelines.
The steel industry continues to develop AHSS grades with strength levels at and above 1000 MPa. These microstructures contain martensite and will be affected by heat exposure during repair as shown in previous studies. Collaborative studies will continue to update repair procedures for higher strength AHSS, including DP, MS and Press Hardened grades, and new 3rd Gen. AHSS as they are introduced.