Solid State Welding
High Frequency Welding (HFW) is the main welding technology for manufacturing cold-formed welded steel tubes. Welded tubes are normally made from flat sheet material by continuous roll forming and the High Frequency Induction Welding process. The tubes are widely used for automotive applications, including seat structures, cross members, side-impact structures, bumpers, subframes, trailing arms, and twist beams. A welded tube can be viewed as a sheet of steel having the shape of a closed cross section.
Two features distinguish the welded tube from the original sheet material:
- The work hardening which takes place during the tube-forming process.
- The properties and metallurgy of the weld seam differ from those of the BM in the tubular cross section.
Good weldability is one precondition for successful HF welding. Most DP steels are applicable as feed material for manufacturing of AHSS tubes by continuous roll forming and the HFIW process. The quality and the characteristics of the weld depend on the actual steel sheet characteristics (such as chemistry, microstructure, and strength) and the set-up of the tube manufacturing process. Table 1 provides some characteristics of the HF welds in tubes made of DP 280/600 steel.
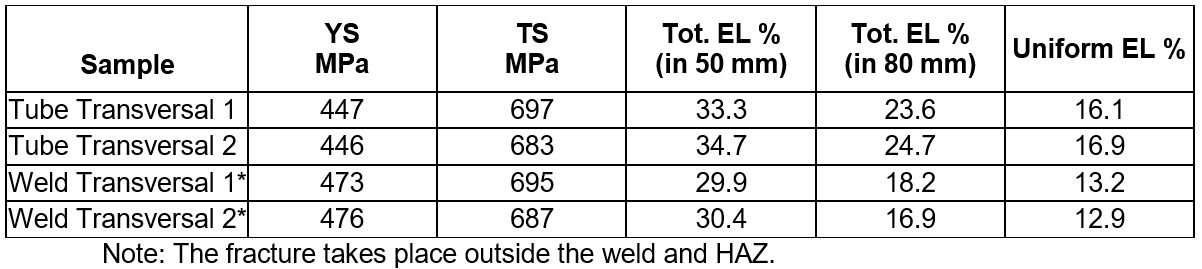
Table 1: Transverse tensile test data for HFIW DP 280/600 tube.R-1
For DP 280/600 the hardness of the weld area exceeds the hardness of the Base Metal (BM) (Figure 1). There is a limited or no soft zone in the transition from HAZ to BM. The nonexistent soft zone yields a HF weld that is stronger than the BM (Table 1). This is an essential feature in forming applications where the tube walls and weld seam are subject to transverse elongation, such as in radial expansion and in hydroforming.
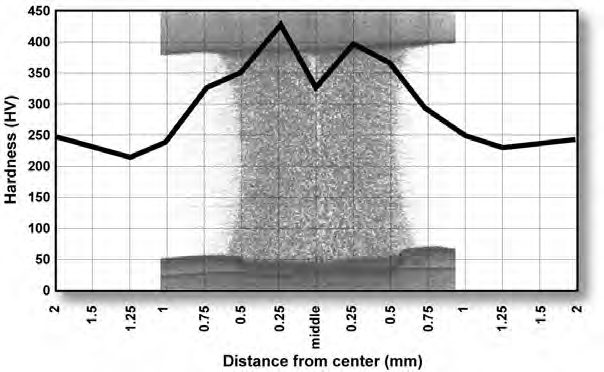
Figure 1: Weld hardness of a HF weld in a DP 280/600 tube.R-1
Figures 2 and 3 contain additional examples of the hardness distribution across HF welds in different materials compared to mild steel.
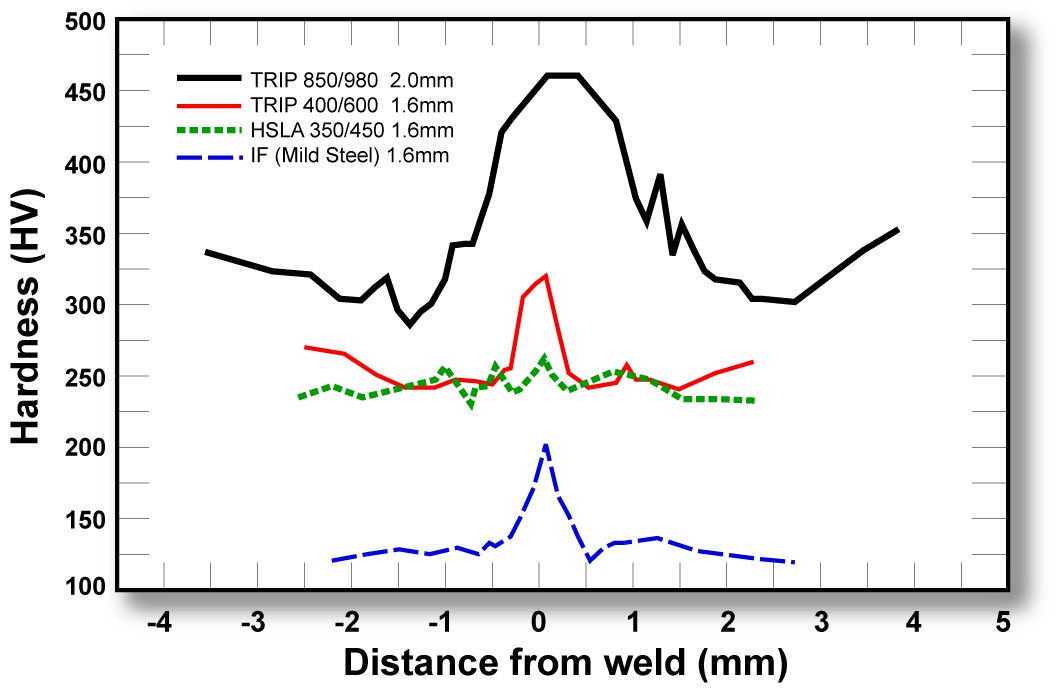
Figure 2: Hardness variation across induction welds for various types of steel.M-1
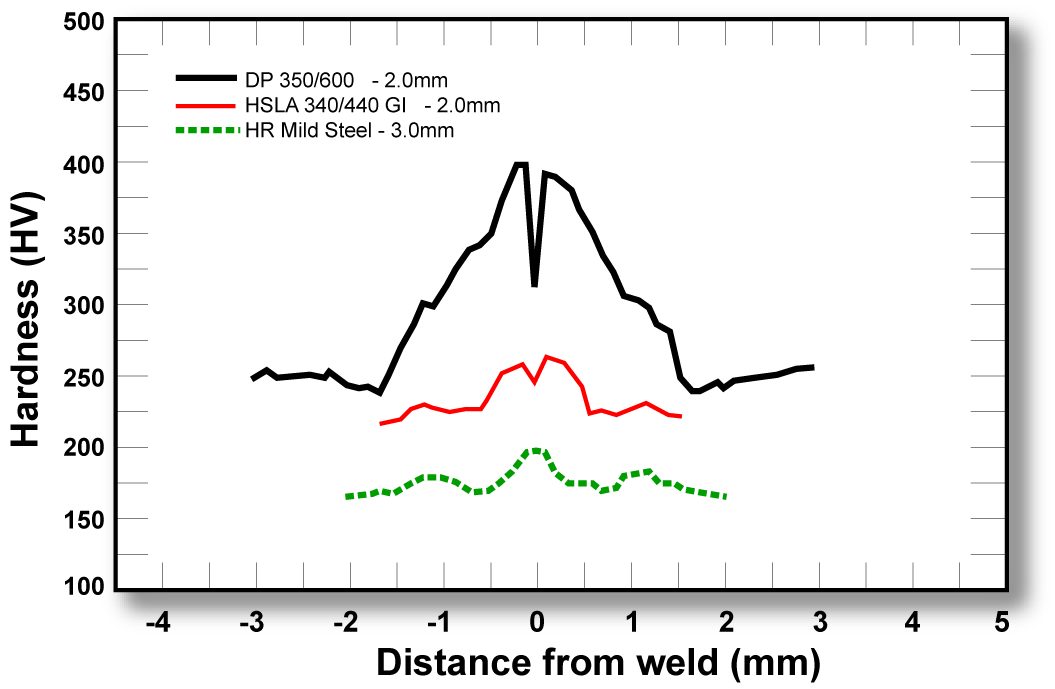
Figure 3: Hardness variation across induction welds of DP 350/600 to mild steel.D-1
Safe Practices
The health and safety of the welding operators, maintenance personnel, and other persons in the welding operations must be considered when establishing operating practices. The design, construction, installation, operation, and maintenance of the equipment, controls, power sources, and tooling should conform to the requirements of the United States Department of Labor in Occupational Safety and Health Standards for General Industry, (29) CFR Part 1910, Subpart Q.1.
The HF power source also must conform to the requirements of the Federal Communication Commission (FCC) as stated in Title 47, Part 15 concerning the radio frequency emissions from industrial, scientific and medical sources. Responsibility for complying with FCC standards is undertaken by the power source manufacturer and does not pose a problem for the end user of the equipment, if the power source is installed following the manufacturer’s recommendations. Information manuals provided by the manufacturers of equipment must be consulted, and recommendations for safe practices must be strictly followed. State, local, and company safety regulations also must be followed. The American Welding Society (AWS) document Safety in Welding, Cutting, and Allied Processes, ANSI Z49.1: 2012 covers safe practices specifically for the welding industry.
Voltages produced by HF power sources with solid-state inverter power sources (as high as 3,000 V) and voltages produced vacuum-tube oscillators (as high as 30,000 V) can be lethal. Proper care and precautions must be taken to prevent injury while working on HF generators and related control systems.
Modern power sources are equipped with safety interlocks on access doors and automatic safety grounding devices that prevent operation of the equipment when access doors are open. The equipment should never be operated with panels or high- voltage covers removed or with interlocks and grounding devices bypassed.
HF currents are more difficult to ground than low- frequency currents, and ground lines should be as short as possible to minimize inductive reactance. All leads between the power source and the contacts or induction coil should be totally enclosed in an insulated or grounded structure and constructed in a way that minimizes Electromagnetic Interference (EMI). Also, care should be taken to prevent the HF magnetic field around the coil and leads from induction heating of the adjacent metal mill components.
The weld area should be protected so that operating personnel cannot come in contact with any exposed contacts or induction coils while these devices are energized. Injuries to personnel from direct contact with HF voltages, especially at the upper range of welding frequencies, may produce severe local tissue damage.
Solid State Welding
Fundamentals and Principles of HF Welding
High Frequency (HF) welding processes rely on the properties of HF electricity and thermal conduction, which determine the distribution of heat in the workpieces. HF contact welding and high-frequency induction welding are used to weld products made from coil, flat, or tubular stock with a constant joint symmetry throughout the length of the weld. Figure 1 illustrates basic joint designs used in HF welding. Figures 1 (A) and (B) are butt seam welds; Figure 1 (C) is a mash seam weld produced with a mandrel, or backside/inside bar. Figure 1 (D) is a butt joint design in strip metal; and Figure 1 (E) shows a T-joint. Figures 1 (F) and (G) are examples of helical pipe and spiral-fin tube joint designs. Figure 1 (J) illustrates a butt illustrates a butt joint in pipe, showing the placement of the coil. Figure 4.L-6 (K) shows a butt joint in bar stock.
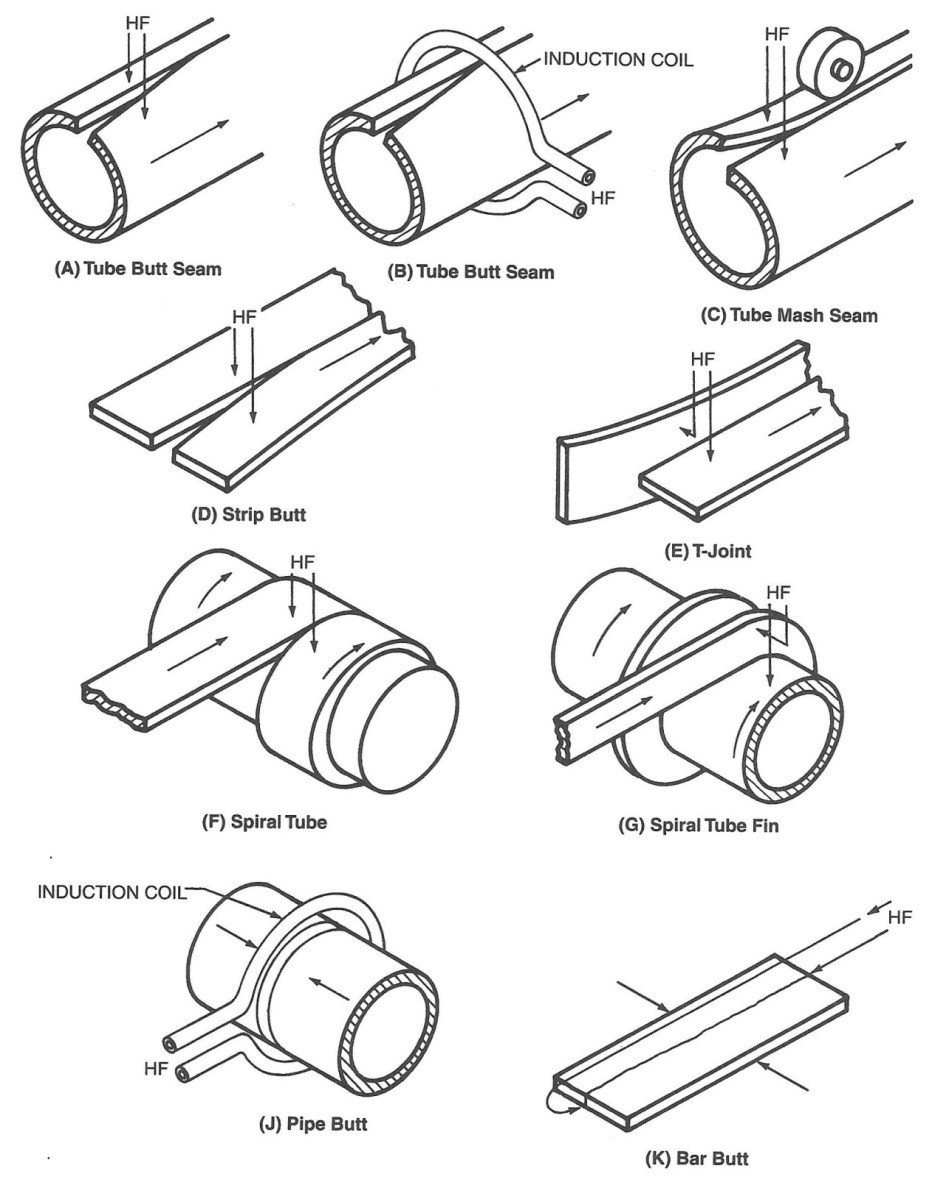
Figure 1: Basic joint designs for HF welds in pipe, tube, sheet, and bar stock.
HF current in metal conductors tends to flow at the surface of the metal at a relatively shallow depth, which becomes shallower as the electrical frequency of the power source is increased. This commonly is called the skin effect. The depth of electrical current penetration into the surface of the conductor also is a function of electrical resistivity, and magnetic permeability, the values of which depend on temperature. Thus, the depth of penetration also is a function of the temperature of the material. In most metals, the electrical resistivity increases with temperature; as the temperature of the weld area increases, so does the depth of penetration. For example, the resistivity of low-carbon steel increases by a factor of five between room temperature to welding temperature. Metals that are magnetic at room temperature lose the magnetic properties above the Curie temperature. When this happens, the depth of penetration increases drastically in the portion of metal that is above the Curie temperature while remaining much shallower in the metal that is below the Curie temperature. When these effects are combined in steel heated at a frequency of 400 kHz, the depth of current penetration is 0.05 mm (0.002 in.) at room temperature, while it is 0.8 mm (0.03 in.) at 800°C (1470°F). The depth of current penetration for several metals as a function of frequency is shown in Figure 2.
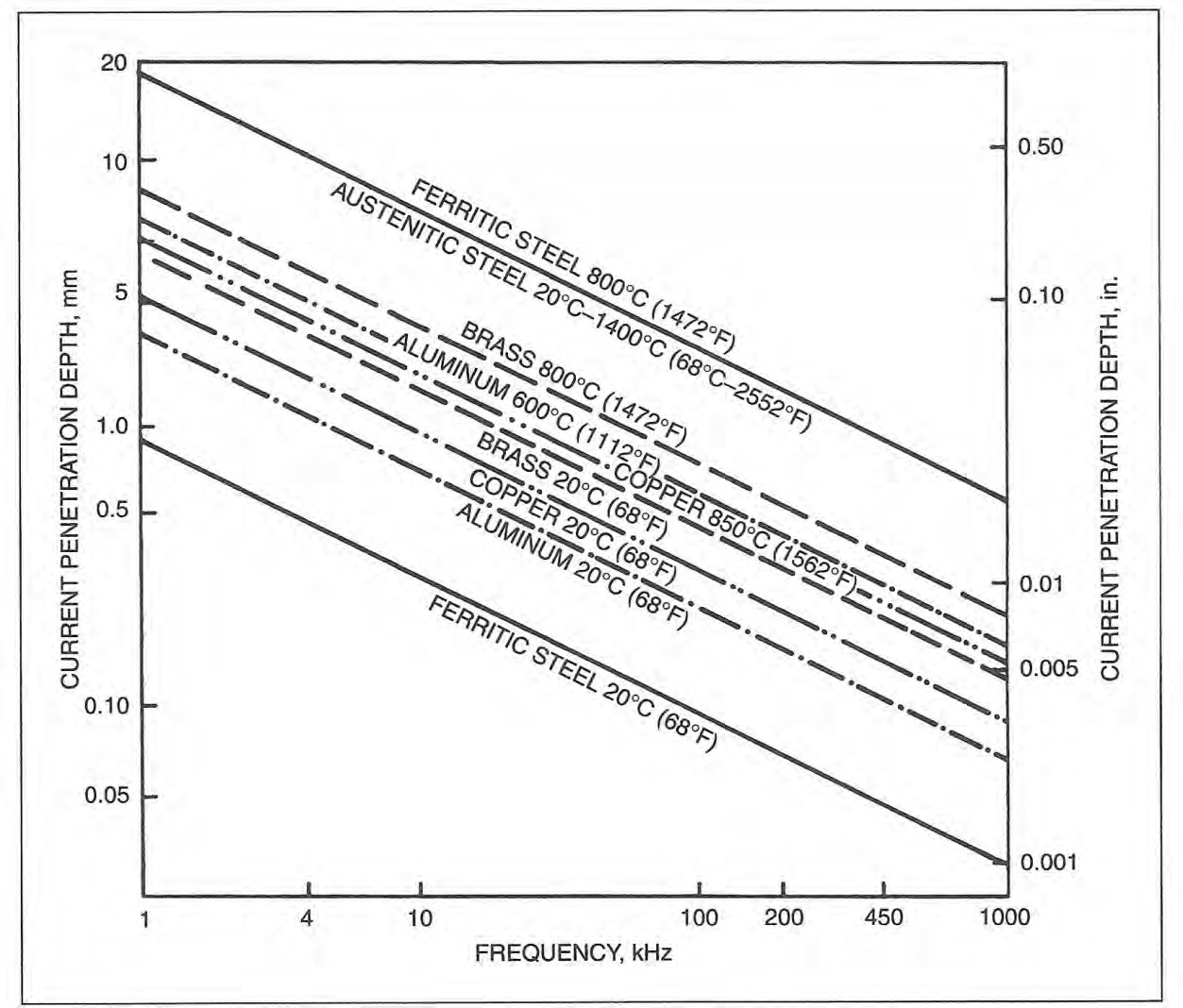
Figure 2: Effect of frequency on depth of penetration into various metals at selected temperatures.
The second important physical effect governing the HF welding process is thermal conduction of the heat generated by the electric currents in the workpiece. Control of the thermal conduction and of the penetration depth provides control of the depth of heating in the metal. Because thermal conduction is a time-dependent process, the depth to which the heat will conduct depends on the welding speed and the length of the electrical current path in the workpiece. If the current path is shortened or the welding speed is increased, the heat generated by the electric current in the workpiece will be more concentrated and intense. However, if the current path is lengthened or the welding speed is reduced, the heat generated by the electric current will be dispersed and less intense. The effect of thermal conduction is especially important when welding metals with high thermal conductivity, such as Cu or Al. It is not possible to weld these materials if the current path is too long or the welding speed is too slow. Changing the electrical frequency of the HF current can compensate for changes in welding speed or the length of the weld path, and the choice of frequency, welding speed, and path length can adapt the shape of the HAZ to optimize the properties of the weld metal for a particular application.A-11, A-15
Advantages/Disadvantages of HF Welding
A wide range of commonly used metals can be welded, including low-carbon and alloy steels, ferritic and austenitic stainless steels, and many Al, Cu, Ti, and Ni alloys.
Because the concentrated HF current heats only a small volume of metal at the weld interface, the process can produce welds at very high welding speeds and with high energy efficiency. HF can be accomplished with a much lower current and less power than is required for low-frequency or direct-current resistance welding. Welds are produced with a very narrow and controllable HAZ and with no superfluous cast structures. This often eliminates the need for Post-Weld Heat Treatment (PWHT).
Oxidation and discoloration of the metal and distortion of the workpiece are minimal. Discoloration may be further reduced by the choice of welding frequency. Maximum speeds normally are limited by mechanical considerations of material handling, forming and cutting. Minimum speeds are limited by material properties, excessive thermal conduction such that the heat dissipates from the weld area before bringing it to sufficient temperature, and weld quality requirements. The high process speed may also become a disadvantage if process settings are incorrect, as scrap can be generated at very high rates.
Considering the high processing speeds, with the high equipment cost required for HF welding, it is important to understand the amount of product needs for economic justification.
The fit-up of the surfaces to be joined and the way they are brought together are important if high-quality welds are to be produced. However, HF welding is far more tolerant in this regard than some other processes.
Flux is almost never used but can be introduced into the weld area in an inert gas stream. Inert gas shielding of the weld area generally is needed only for joining highly reactive metals such as Ti or for certain grades of stainless steel.A-11, A-15
Induction Seam Welding of Pipe and Tubing
The welding of continuous-seam pipe and tubing is the predominant application of HF induction welding. The pipe or tube is formed from metal strip in a continuous-roll forming mill and enters the welding area with the edges to be welded slightly separated. In the weld area, the open edges of the pipe or tube are brought together by a set of forge pressure rolls in a vee shape until the edges touch at the apex of the vee, where the weld is formed. The weld point occurs at the center of the mill forge rolls, which apply the pressure necessary to achieve a forged weld.
An induction coil, typically made of Cu tubing or Cu sheet with attached water- cooling tubes, encircles the tube (the workpiece) at a distance equal to one to two tube diameters ahead of the weld point. This distance, measured from the weld point to the edge of the nearest induction coil, is called the vee length. The induction coil induces a circumferential current in the tube strip that closes by traveling down the edge of the vee through the weld point and back to the portion of the tube under the induction coil. This is illustrated in Figure 3.

Figure 3: HF induction seam welding of a tube.
The HF current flows along the edge of the weld vee due to the proximity effect (see Fundamentals), and the edges are resistance-heated to a shallow depth due to the skin effect.
The geometry of the weld vee is such that its length usually is between one and one half to two tube diameters long. The included angle of the vee generally is between 3 and 7 degrees. If this angle is too small, arcing between the edges may occur, and it will be difficult to maintain the weld point at a fixed location. If the vee angle is too wide, the proximity effect will be weakened causing dispersed heating of the vee edges, and the edges may tend to buckle. The best vee angle depends on the characteristics of the tooling design and the metal to be welded. Variations in vee length and vee angle will cause variations in weld quality.
The welding speed and power source level are adjusted so that the two edges are at the welding or forge temperature when they reach the weld point. The forge rolls press the hot edges together, applying an upset force to complete the weld. Hot metal containing impurities from the faying surfaces of the joint is squeezed out of the weld in both directions, inside and outside the tube. The upset metal normally is trimmed off flush with the BM on the outside of the tube, and sometimes is trimmed from the inside, depending on the application for the tube being produced.A-11, A-15
The HF contact welding process provides another means of welding continuous seams in pipe and tubing. The process essentially is the same as that described above for induction welding and is illustrated in Figure 4. The major difference is that sliding contacts are placed on the tube adjacent to the unwelded edges at the vee length. With the contact process, the vee length generally is shorter than that used with the induction process. This is because the contact tips normally can be placed within the confines of the forge rolls where the induction coil must be placed sufficiently behind the forge rolls, so that the forge rolls are not inductively heated by the magnetic field of the induction coil. Because of the shorter vee lengths achievable with the contact process, an impeder often is not necessary, particularly for large-diameter tubes where the impedance of the current path inside the tube has significant inductive reactance.

Figure 4: Joining a tube seam with HFRW using sliding contacts. Note: Vee length extends from point of welding to sliding contacts.
An impeder, which is made from a magnetic material such as ferrite, generally is required to be placed inside the tube. The impeder is positioned so that it extends about 1.5 to 3 mm (1/16 to 1/8 in.) beyond the apex of the vee and the equivalent of one to two workpiece diameters upstream of the induction coil. The purpose of the impeder is to increase the inductive reactance of the current path around the inside wall of the workpiece. This reduces the current that would otherwise flow around the inside of the tube and cause an unacceptable loss of efficiency. The impeder also decreases the magnetic path length between the induction coil and the tube, further improving the efficiency of power transfer to the weld point. The impeder must be cooled to prevent its temperature from rising above its Curie temperature, where it becomes nonmagnetic. For ferrite, the Curie temperature typically is between 170 and 340°C (340 and 650°F).A-11, A-15
Back To Top
Friction Stir Welding
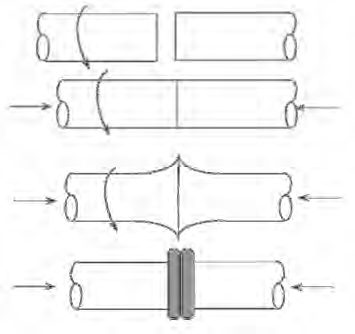
Figure 1: Basic steps of both inertia and CD friction welding.
The Friction Stir Welding family of processes relies on significant plastic deformation or forging action to overcome the barriers to solid-state welding. Frictional heating dominates at the beginning of the process, followed by the heating due to plastic deformation once the forging action begins. The friction welding processes which use rotation of one part against another are inertia and continuous (or direct)-drive friction welding. These are the most common of the friction welding processes and are ideal for round bars or tubes. In both inertia and Continuous-Drive (CD) friction welding, one part is rotated at high speeds relative to the other part (Figure 1). They are then brought together under force creating frictional heating which softens (reduces the YS) the material at and near the joint to facilitate the forging action, which, in turn, produces further heating. Following a sufficient amount of time to properly heat the parts, a high upset force is applied which squeeze the softened hot metal out into the “flash”. Any contaminants are squeezed out as well as the weld is formed. The flash is usually removed immediately after welding while it is still hot.A-11, P-6
Friction Stir Welding
Friction Stir Welding (FSW) is a revolutionary new friction welding process that was developed in the early 1990s by the British Welding Institute (TWI). Whereas processes such as inertia and Continuous-Drive (CD) friction welding are primarily limited to round parts, FSW (Figure 2) produces solid-state friction welds using conventional joint design such as butt joints. FSW relies on the frictional heat created when a special non-consumable pin tool is rotated along the joint against the top of the two pieces being welded. As the process begins, frictional heating softens (or plasticizes) metal at the joint, facilitating a stirring action of plasticized metal. Further heating that is generated by the plastic deformation becomes the main source of heating as the weld progresses. The two videos following provide more insight on the process.
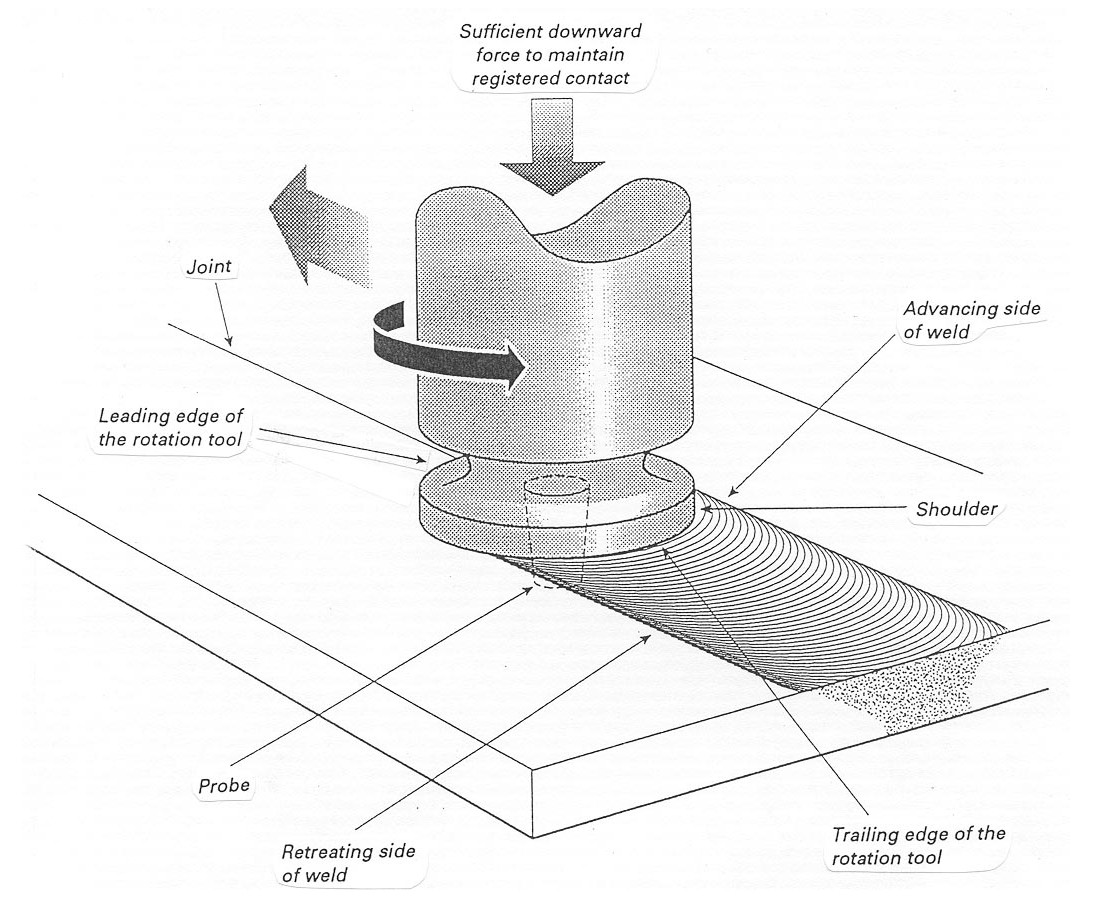
Figure 2: Friction Stir Welding
The pin tool for FSW consists of a shoulder and pin. The shoulder rests on the surface of the plates and provides most of the frictional heating. The pin partially penetrates the joint of the plates being welded. Within the stir zone itself, the plasticized hot metal flows around the pin and coalesces to form a weld. The primary purpose of the pin is to control the stirring action. A wide variety of pin tool designs and materials have been studied, including the use of Tungsten (W)-based materials, threaded pins, and cupped shoulders. As indicated on Figure 3, a slight push angle (<5 degrees) relative to the travel direction is typically used. Weld travel speeds are much slower than typical arc welding speeds. The process has limited industrial applications since it is still under development, especially in tool development.A-11, P-6
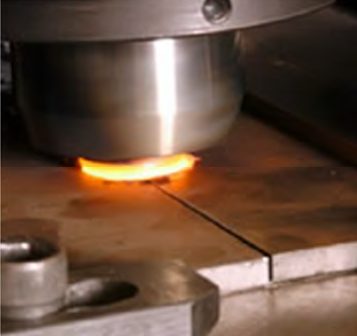
Figure 3: FSW typically uses a slight push angle
The FSW of hard metals (steel, Ti, Ni) has been made possible due to advancements in both tool design and tool materials. Tool material choices for AHSS applications include ceramic-based Polycrystalline Cubic Boron Nitride (PCBN) and refractory based Tungsten-Rhenium alloy (W-Re). PCBN is chosen because it is extremely wear resistant and has good thermal management. W-based material is chosen because it is very tough at room and welding temperatures and it is capable of being used for thick sections of steels.
Mechanical properties for FSW of AHSS cross-weld tensile specimens showed fully consolidated weld joints without discontinuities, but showed a drop-in weld ductility of about 10%, as seen in Figure 4.
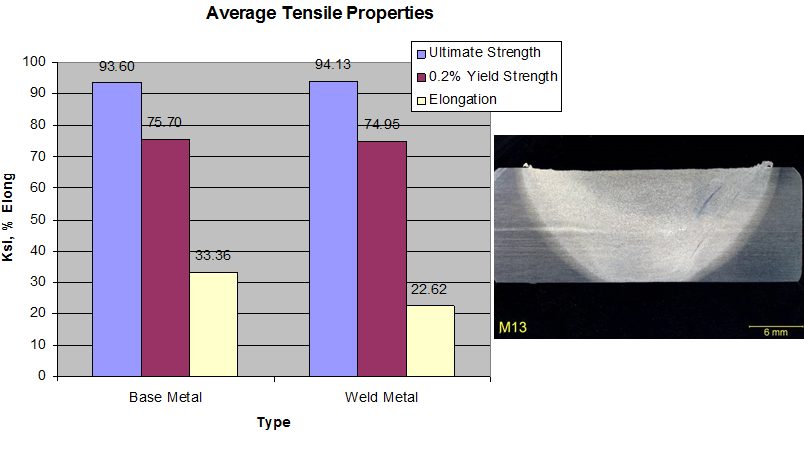
Figure 4: Mechanical properties of FSW for AHSS.
Friction Stir Spot Welding
A variation of the FSW process is Friction Stir Spot Welding. This process was specifically developed for some automotive applications, including joining of AAl), Al-to-steel, and AHSS. The process steps are similar to FSW without the linear movement, thus creating a “spot”-type joint (Figure 5).O-1
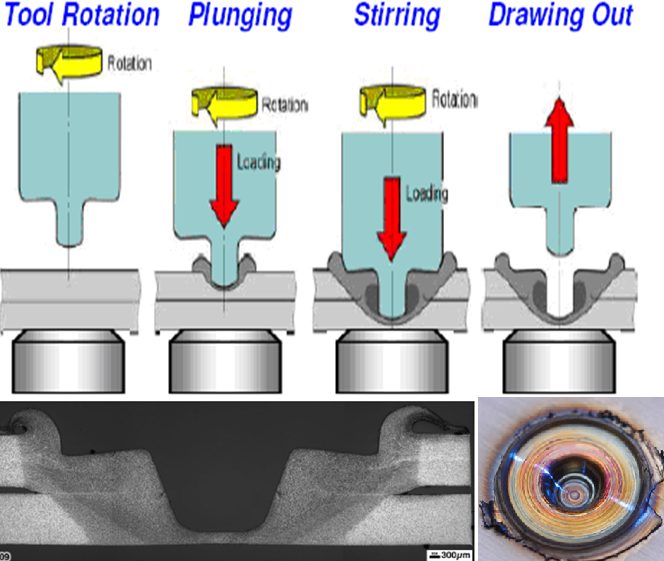
Figure 5: Process steps for friction stir spot welding (top) with the resultant weld profile (bottom).O-2
In summary, the advantages and limitations of friction welding processes are listed below.
- Advantages:
- No melting means no chance for solidification-related defects
- Filler materials are not needed
- Very few process variables result in a very repeatable process
- In the case of CD friction welding, can be deployed in a production environment
- Fine grain structure of friction welds typically exhibits excellent mechanical properties relative to the BM, especially when welding Al
- No special joint preparation or welding skill required
- Limitations:
- Equipment is very expensive
- Limited joint designs, and in the case of CD and inertia welding, parts must be symmetric
- FSW is very slow, and not conducive to high-speed
Solid State Welding
Introduction
Solid-State welding refers to a family of processes that produce welds without the requirement for molten metal. Solid-state welding theory emphasizes that the driving force for two pieces of metal to spontaneously weld (or form a metallic bond) to each other exists if the barriers (oxides, contaminants, and surface roughness) to welding can be eliminated. All solid-state welding processes are based on this concept, and use some combination of heat, pressure, and time to overcome the barriers. Approaches include friction, diffusion, explosion, and ultrasonic welding.
Since there is no melting, there is no chance of forming defects such as porosity or slag inclusions which are only associated with fusion welding processes. Solid-state welding processes also require no filler materials, and in some cases, can be quite effective at welding dissimilar metals that cannot be welded with conventional processes due to metallurgical incompatibilities. The equipment is typically very expensive, and some processes involve significant preparation time of the parts to be welded. Most of these processes are limited to certain joint designs, and some of them are not conducive to a production environment. Non Destructive Testing processes do not always work well with solid-state welding processes because of the difficulties of distinguishing a true metallurgical bond with these techniques.
In this section you’ll find examples of three types of solid state welding processes: Friction, High-Frequency for tubes and pipe and Magnetic Pulse. Generally these are characterized as follows. Click to the specific menu for details.
Friction Welding Processes
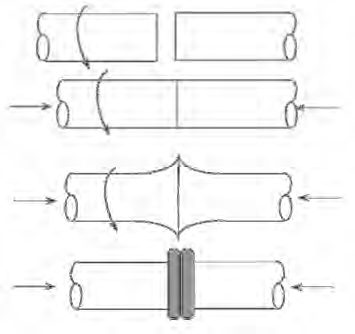
Figure 1: Basic steps of both inertia and CD friction welding.
This family of processes relies on significant plastic deformation or forging action to overcome the barriers to solid-state welding. Frictional heating dominates at the beginning of the process, followed by the heating due to plastic deformation once the forging action begins. The friction welding processes which use rotation of one part against another are inertia and continuous (or direct)-drive friction welding. These are the most common of the friction welding processes and are ideal for round bars or tubes. In both inertia and Continuous-Drive (CD) friction welding, one part is rotated at high speeds relative to the other part (Figure 1). They are then brought together under force creating frictional heating which softens (reduces the YS) the material at and near the joint to facilitate the forging action, which, in turn, produces further heating. Following a sufficient amount of time to properly heat the parts, a high upset force is applied which squeeze the softened hot metal out into the “flash”. Any contaminants are squeezed out as well as the weld is formed. The flash is usually removed immediately after welding while it is still hot.A-11, P-6
High Frequency Tube/Pipe Welding
HF welding processes rely on the properties of HF electricity and thermal conduction, which determine the distribution of heat in the workpieces. HF contact welding and high-frequency induction welding are used to weld products made from coil, flat, or tubular stock with a constant joint symmetry throughout the length of the weld.
Magnetic Pulse Welding (MPW)
MPW is a solid-state process that uses electromagnetic pressure to accelerate one workpiece to produce an impact against another workpiece. The metallic bond created by this process is similar to the bond created by explosion welding. MPW, also known as electromagnetic pulse or magnetic impact welding, is highly regarded for the capability of joining dissimilar materials.
Blog, RSW Joint Performance Testing
top-of-page
Results of a Three-Year LME Study
WorldAutoSteel releases today the results of a three-year study on Liquid Metal Embrittlement (LME), a type of cracking that is reported to occur in the welding of Advanced High-Strength Steels (AHSS).The study results add important knowledge and data to understanding the mechanisms behind LME and thereby finding methods to control and establish parameters for preventing its occurrence. As well, the study investigated possible consequences of residual LME on part performance, as well as non-destructive methods for detecting and characterizing LME cracking, both in the laboratory and on the manufacturing line (Figure 1).
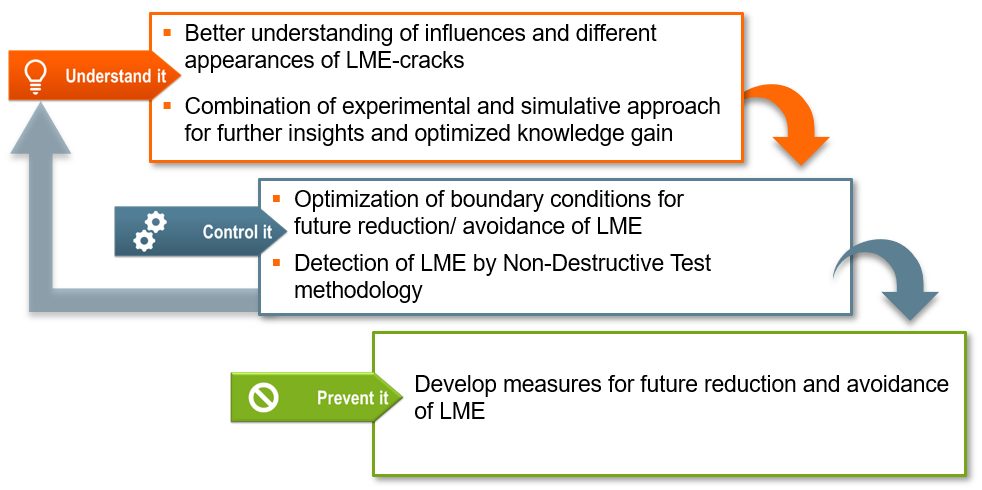
Figure 1: LME Study Scope
The study encompassed three different research fields, with an expert institute engaged for each:
- Laboratory of Materials and Joining Technology (LWF) Paderborn University, Paderborn, Germany, for experimental research,
- The Institute de Soudure, Yutz, France, for investigations regarding non-destructive testing, and
- Fraunhofer Institute for Production Systems and Design Technology (IPK), Berlin, Germany, for the development of a simulation model to accurately replicate welding conditions resulting in LME.
A portfolio containing 13 anonymized AHSS grades, including dual phase (DP), martensitic (MS) and retained austenite (RA) with an ultimate tensile strength (UTS) of 800 MPa and higher, was used to set up a testing matrix, which enabled the replication of the most relevant and critical material thickness combinations (MTC). All considered MTCs show a sufficient weldability under use of standard parameters according to SEP1220-2. Additional MTCs included the joining of various strengths and thicknesses of mild steels to select AHSS in the portfolio. Figure 2 provides the welding parameters used throughout the study.
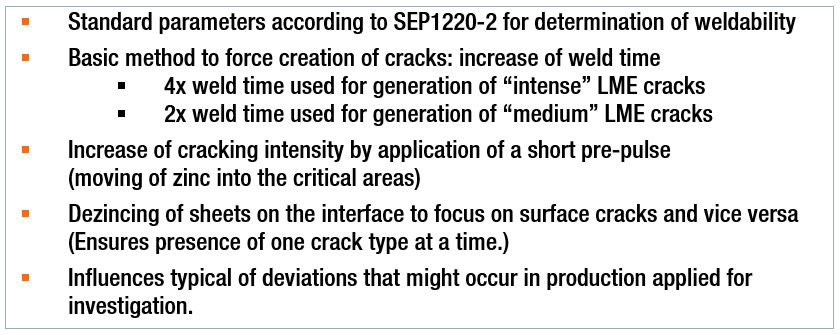
Figure 2: Study Welding Parameters
In parallel, a 3D electro-thermomechanical simulation model was set up to study LME. The model is based on temperature-dependent material data for dual phase AHSS as well as electrical and thermal contact resistance measurements and calculates local heating due to current flow as well as mechanical stresses and strains. It proved particularly useful in providing additional means to mathematically study the dynamics observed in the experimental tests. This model development was documented in two previous AHSS Insights blogs (see AHSS Insights Related Articles below).
Understanding LME
The study began by analyzing different influence factors (Figure 3) which resembled typical process deviations that might occur during car body production. The impact of the influences was analyzed by the degree of cracking observed for each factor. A select number of welding set-ups from these investigations were rebuilt digitally in the simulation model to replicate the process and study its dynamics mathematically. This further enabled the clarification of important cause-effect relationships.

Figure 3: Overview of All Applied Influence Factors (those outlined in yellow resulted in most frequent cracking.)
Generally, the most frequent cracking was observed for sharp electrode geometries, increased weld times and application of external loads during welding. All three factors were closely analyzed by combining the experimental approach with the numerical approach using the simulation model.
Destructive Testing – LME Effects on Mechanical Joint Strength
A destructive testing program also was conducted for an evaluation of LME impact on mechanical joint strength and load bearing capacity in multiple conditions, including quasi-static loading, cyclic loading, crash tests and corrosion. In summary of all load cases, it can be concluded that LME cracks, which might be caused by typical process deviations (e.g. bad part fit up, worn electrodes) have a low intensity impact and do not affect the mechanical strength of the spot weld. And as previously mentioned, the study analyses showed that a complete avoidance of LME during resistance spot welding is possible by the application of measures for reducing the critical conditions from local strains and exposure to liquid zinc.
Controlling LME
In welding under external load experiments, the locations of the experimental crack occurrence showed close correlation with the strains and remaining plastic deformations computed by the simulation model. It was observed that the cracks form at the location of the highest plastic strains, and material-specific threshold values for critical strains were derived. The threshold values then were used to judge the crack formation at elongated weld times.
At the same time, the simulation model pointed out a significant difference in liquid zinc diffusion during elongated weld times. Therefore, it is concluded that liquid zinc exposure time is a second highly relevant factor for LME formation.
The results for the remaining influence factors depended on the investigated MTCs and were generally less significant. In more susceptible MTCs (AHSS welded with thick Mild steel), no significant cracking occurred when welded using standard process parameters. Light cracking was observed for most of the investigated influences, such as low electrode cooling rate, worn electrode caps, electrode positioning deviations or for gap afflicted spot welds. More intense cracking (higher penetration depth cracking) was only observed when welding under extremely high external loads (0.8 Re) or, even more, as a consequence of highly increased weld times.
For the non-susceptible MTCs, even extreme situations and weld set-ups (such as the described elongated weld times) did not result in significant LME cracks within the investigated AHSS grades.
Methods for avoidance of LME also were investigated. Changing the electrode tip geometry to larger working plane diameters and elongating the hold time proved to eliminate LME cracks. In the experiments, a change of electrode tip geometry from a 5.5 mm to an 8.0 mm (Figure 4) enabled LME-free welds even when doubling the weld times above 600 ms. Using a flat-headed cap (with small edge radii or beveled), even the most extreme welding schedules (weld times greater than 1000 ms) did not produce cracks. The in-depth analysis revealed that larger electrode tip geometries clearly reduce the local plastic deformation around the indentation. This plastic strain reduction is particularly important, as longer weld times contribute to a higher liquid zinc exposure interval, leading to a higher potential for LME cracks.
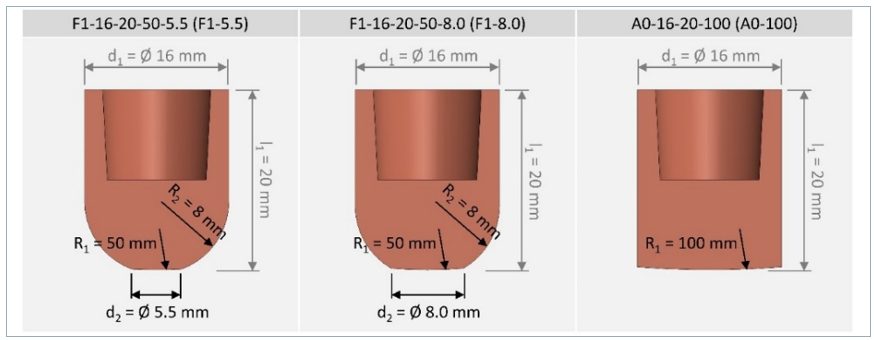
Figure 4: Electrode Geometries Used in Study Experiments
It was also seen that as more energy flows into a spot weld, it becomes more critical to parameterize an appropriate hold time. Depending on the scenario, the selection of the correct hold time alone can make the difference between cracked and crack-free welds. Insufficient hold times allow liquid zinc to remain on the steel surface and increased thermal stresses that form after the lift-off of the electrode caps. Elongated hold times reduce surface temperatures, minimizing surface stresses and thus LME potential.
Non-Destructive Testing: Laboratory and Production Capabilities
A third element of the study, and an aid in the control of LME, is the detection and characterization of LME cracks in resistance spot welds, either in laboratory or in production conditions. This work was done by the Institute of Soudure in close cooperation with LWF, IPK and WorldAutoSteel members’ and other manufacturing facilities. Ten different non-destructive techniques and systems were investigated. These techniques can be complementary, with various levels of costs, with some solutions more technically mature than others. Several techniques proved to be successful in crack detection. In order to aid the production source, techniques must not only detect but also characterize cracks to determine intensity and the effect on joint strength. Further work is required to achieve production-level characterization.
The study report provides detailed technical information concerning the experimental findings and performances of each technique/system and the possible application cost of each. Table 1 shows a summary of results:
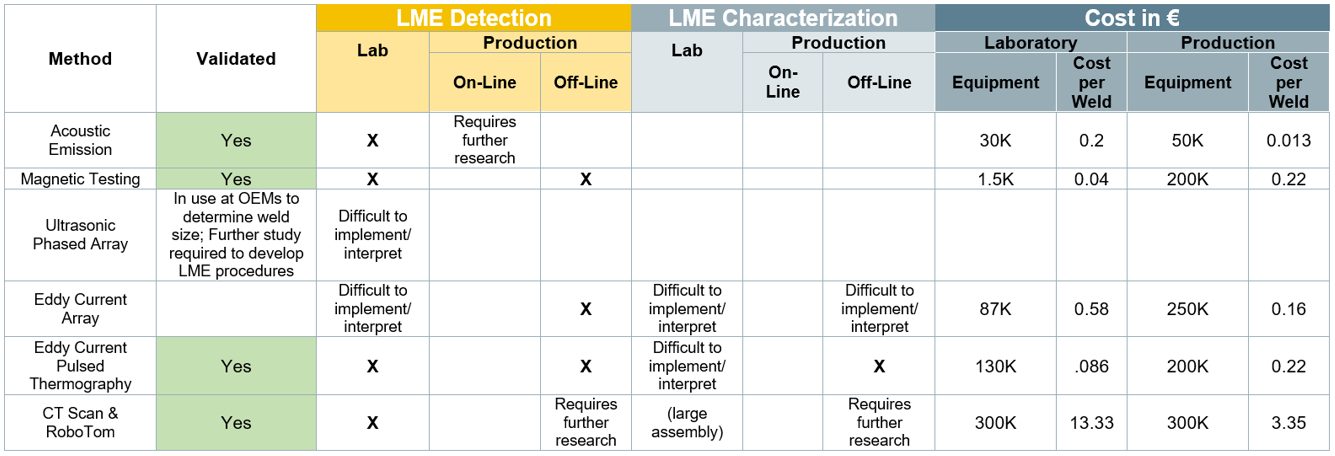
Table 1: Summary of NDT: LME Detection and Characterization Methods
Preventing LME
Suitable measures should always be adapted to the specific use case. Generally, the most effective measures for LME prevention or mitigation are:
- Avoidance of excessive heat input (e.g. excess welding time, current).
- Avoidance of sharp edges on spot welding electrodes; instead use electrodes with larger working plane diameter, while not increasing nugget-size.
- Employing extended hold times to allow for sufficient heat dissipation and lower surface temperatures.
- Avoidance of improper welding equipment (e.g. misalignments of the welding gun, highly worn electrodes, insufficient electrode cooling)
In conclusion, a key finding of this study is that LME cracks only occurred in the study experiments when there were deviations from proper welding parameters and set-up. Ensuring these preventive measures are diligently adhered to will greatly reduce or eliminate LME from the manufacturing line. For an in-depth review of the study and its findings, you can download a copy of the full report at worldautosteel.org.

LME Study Authors
The LME study authors were supported by a committed team of WorldAutoSteel member companies’ Joining experts, who provided valuable guidance and feedback.
Related Articles: More on this study in previous AHSS Insights blogs:
Journal Publications:
- Julian Frei, Max Biegler, Michael Rethmeier, Christoph Böhne & Gerson Meschut (2019) Investigation of liquid metal embrittlement of dual phase steel joints by electro-thermomechanical spot-welding simulation, Science and Technology of Welding and Joining, 24:7, 624-633, DOI: 10.1080/13621718.2019.1582203
- Christoph Böhne, Gerson Meschut, Max Biegler, Julian Frei & Michael Rethmeier (2020) Prevention of liquid metal embrittlement cracks in resistance spot welds by adaption of electrode geometry, Science and Technology of Welding and Joining, 25:4, 303-310, DOI: 10.1080/13621718.2019.1693731
-
Auto/Steel Partnership LME Testing and Procedures
Back To Top
Manufacturing Issues
Spot Welding of Three Steel Sheets with Large Thickness Ratios
Car parts such as side panels are fabricated by spot welding three steel sheets together. When the outer steel sheet is a thin sheet of mild steel and the reinforcement steel sheets are thick sheets of HSS (that is, when there is a large thickness ratio between the sheets), it is often difficult to spot weld such sheets together. The term “thickness ratio” as used herein refers to the total thickness of the three steel sheets divided by the thickness of the thinnest steel sheet. Nuggets obtained by spot welding of three steel sheets are illustrated in Figure 1 (a). In the spot welding of three steel sheets with a large thickness ratio, it is difficult to form a nugget at the interface between thin and thick steel sheets, as shown in Figure 1 (b). The reason for this is that in spot welding, because of heat removal by the water-cooled electrode, the fusion progresses from the thickness center of the three steel sheets toward the outside, except for the heat generated by contact resistance at the steel sheet surfaces in the early stages of welding time. In addition, in view of the dimensional accuracy of actual members, it is necessary to set appropriate welding conditions when there is a gap between steel sheets. In practice, the proper welding current range is as shown in Figure 2. However, the welding current range is often narrower in one-step spot welding.
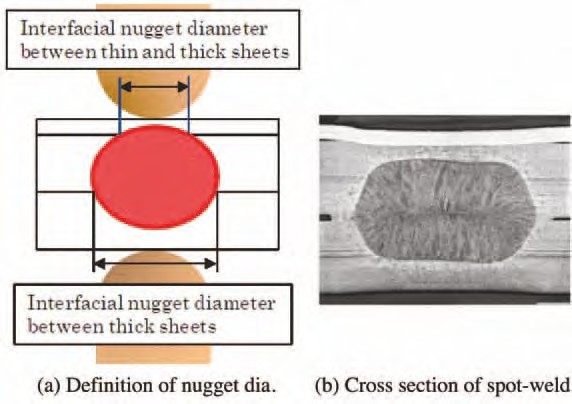
Figure 1: Three sheets spot welded.N-5
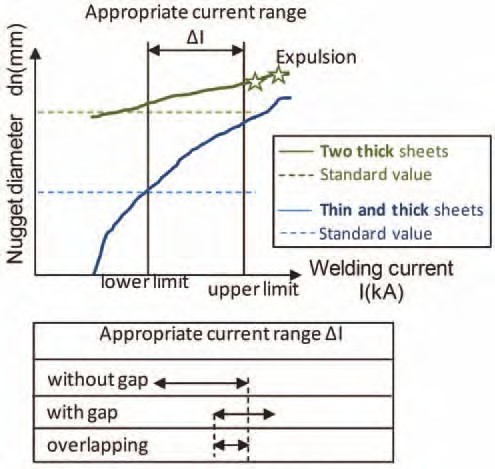
Figure 2: Weldability lobe of three sheets spot welded.
As a means of solving the above problem when there is no gap between the steel sheets, a method has been proposed in which the diameter of the electrode tip at the thin-sheet side is reduced and the welding force and current are varied during the welding time. In addition, a two- step pulsating current welding method (Figure 3) has been proposed in which neither the electrode diameter nor the welding force are changed. This method is described briefly below. Initially, during the first welding step, a relatively large welding current is passed to generate heat by using the contact resistance at the interface between the thin and thick steel sheets and that between the thick steel sheets. This method does not positively use the contact resistance that is effective when the electrode force is low. Since the method can be applied even under a high electrode force, it is particularly effective when there is a gap between the steel sheets to be welded together.
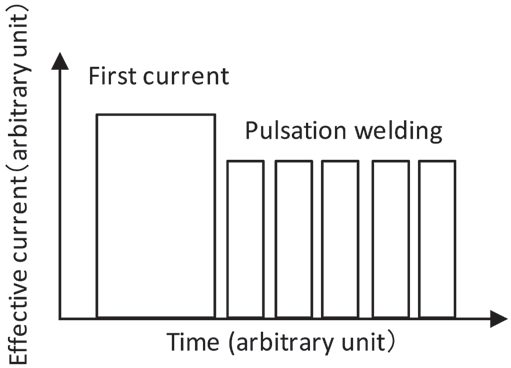
Figure 3: Welding current pattern.
An experiment was conducted by using the above technology. The materials used were a 0.6- mm-thick sheet of mild steel and two 1.6-mm-thick sheets of HSS (980 MPa class). Spacers 1.4-mm thick were inserted at intervals of 40 mm between the thin and thick steel sheets and between the thick steel sheets. A servomotor-driven, single-phase AC welder was used for the test. The electrode used was a Cr-Cu dome radius type with a 40-mm tip upper radius and 6-mm tip lower diameter. The welding force was 3.43 kN. To evaluate the diameter of fusion at the interface between the thin and thick sheets, which determines the proper current range, a chisel test was conducted at the interface and evaluated the plug diameter.
The test results are illustrated in Figure 4. The horizontal axis represents the first step welding current for one-step welding (welding time t1 = 18 cycles) and the second-step welding current for two-step welding (first welding time t1 = 18 cycles, second welding time t2 = 8 cycles) or pulsation welding [t1 = 18 cycles, t2 = (5-cycle heat/2-cycle cool) × 5]. For one- or two-step welding, the welding current range was less than 1 kA. Conversely, with pulsation, it was possible to secure a proper welding range of 3 kA or more (about 1.8 kA when there was no gap between the steel sheets).
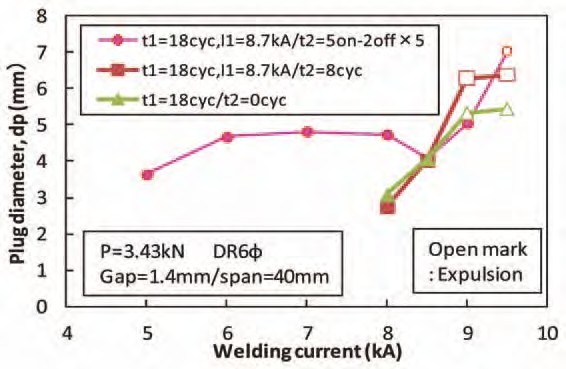
Figure 4: Current ranges for different welding current patterns.
In addition to the two-step pulsating current welding method (Figure 4 above), preheating the sheets at 20-25% of the normal current before beginning the impulses can be effective when joining three layers of extremely different thicknesses. Figure 5 shows a weld cross section using preheating prior to three impulses.
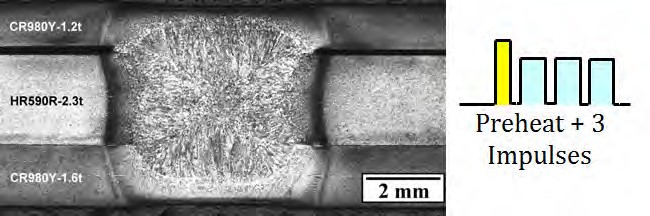
Figure 5: Cross section of three sheet spot weld including preheating prior to pulsations.C-6
Another solution to RSW three sheets is when the Fusion Zone (FZ) formation process is controlled by setting the welding current and welding force during welding in multiple steps; this is referred to as Intelligent Spot Welding. (ISW). Using this approach, nugget formation between a thin sheet and thick sheet becomes possible when reduced welding force is applied. In Step 1 of the welding process, a FZ is reliably formed between the thin sheet and thick sheet by applying conditions of low welding force, short welding time, and high current. In the subsequent Step 2, a FZ is formed between the two thick sheets by apply high welding force and a long welding time. The results are shown in Figure 6, in which welding is performed with the edge of three steel sheets positioned directly under the electrodes, and the behavior of FZ formation at the edge of the sheets was observed with a high-speed video camera. Condition (a) is welding under a constant welding force and condition (b) is ISW. In condition (a), a nugget was formed between the two thick sheets, but the nugget failed to grow to the thin sheet-thick sheet joint, and the two sheets were not welded. However, condition (b) shows that nuggets have formed between both the thin and thick sheet and between the two thick sheets. The optimal welding current range for Step 2 can be determined from nugget formation between the two thick sheets, resulting in a wide available current range equal to or greater than that in joint welding of two thick sheets.
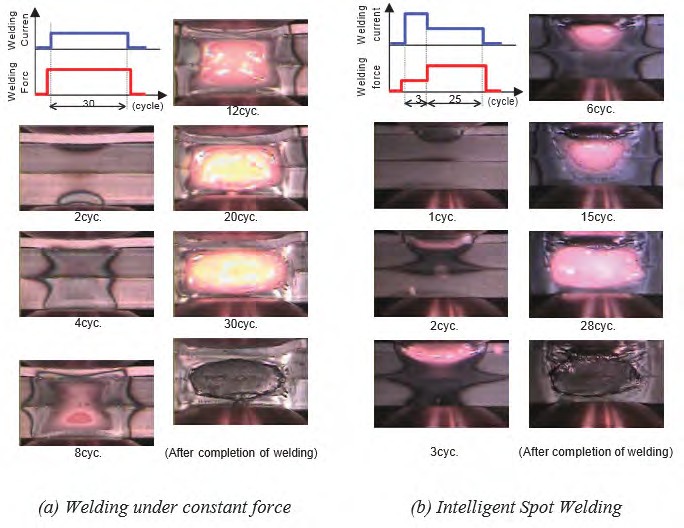
Figure 6: Results of observation of FZ formation phenomenon in RSW of three-sheet joint by high-speed video camera.J-1
Application of Spot Welding to Hollow Members
In spot welding of car bodies, the so-called direct spot welding (in which the welding current is passed while two or more steel sheets are pressed against each other) by the welding electrodes is used most commonly. However, for those parts with closed cross sections, it may become necessary to drill a working hole through which the electrodes for direct spot welding of the steel sheets can be passed. In this case, the decline in rigidity of the drilled part being compensated for by using a thicker steel sheet or providing a reinforcing member will inevitably increase the weight of the car body. Therefore, attempts were made to reduce the steel sheet thickness (weight) and secure the required stiffness simultaneously without drilling any hole in the steel sheets. Indirect spot welding was used, in which the steel sheets are pressed and welded by a couple of electrodes from one side at the same time. Because the steel sheets are pressed by electrodes from one side, the weld sinks and the area of contact between the steel sheets increases (the current density decreases) if an excessive force is applied, making it difficult to perform fusion welding. Conversely, if an excessively large current is applied, the local current density between the electrodes increases because of a shunt current, causing a crack or explosion.
Studies were made for various welding conditions for the combination of a hollow member with a 1.6-mm wall thickness and a sheet-formed member with a 0.7-mm thickness. By using an electrode with a specially designed tip and a DC power supply in combination, indirect spot welding could be performed of the above members without requiring any special pattern of conduction or pressing, even in the presence of a gap between the members or the presence of shunts (existing welding points). An example of the cross section of an indirect spot weld is illustrated in Figure 1, which clearly indicates that a sufficiently large nugget was formed.
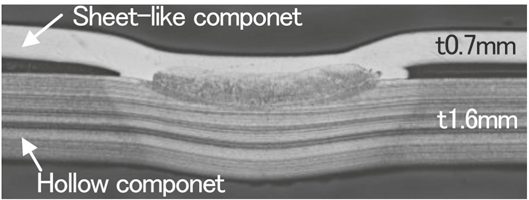
Figure 1: Cross section of indirect spot weld for hollow and sheet-like components.
For the indirect RSW with single-side access of the welding electrode, the variable controls of electrode force and current during welding were developed to promote the weld nugget formation. Experiments as well as numerical simulations were conducted to study the welding phenomena and optimize the welding process. It was verified that the nugget was stably formed with the developed process even when shunting was large. Figure 2 describes the effect of variable current and force on the promotion of weld nugget formation.
At the first stage with low welding current and high electrode force, the electric conduction with sufficient load at weld preheats the sheet, which promotes contacting area between the electrode and upper sheet and thus inhibits the expulsion from the surface. Meanwhile, contacting area between upper and lower sheets is also promoted forming the stable conduction path. Subsequently, at the second stage with high welding current and low electrode force, the nugget formation is effectively promoted with a heated region concentrated at the center in weld, avoiding the further penetration of welding electrode into the upper sheet and thus maintaining the current density.
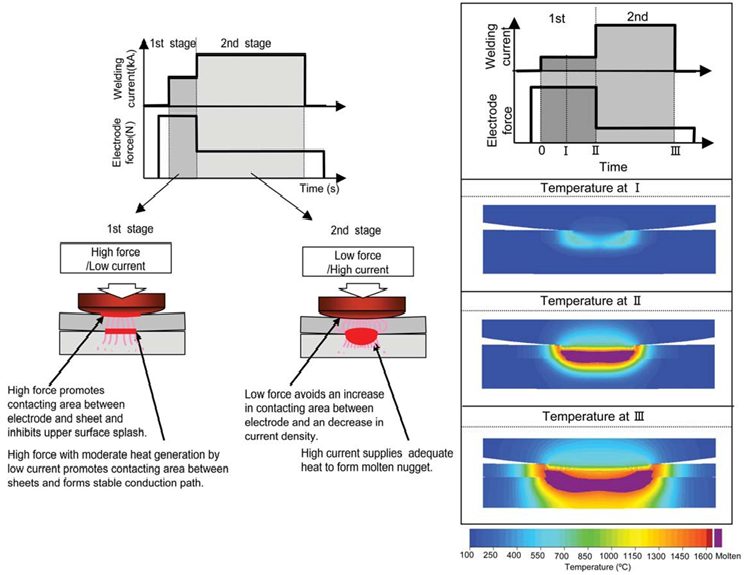
Figure 2: Concept of nugget formation process of variable current and force control for single-sided RSW.J-1
Back To Top