Tube Forming
Manufacturing precision welded tubes typically involves continuous roll forming followed by a longitudinal weld typically created by high frequency (HF) induction welding process known as electric resistance welding (ERW) or by laser welding.
Tubular components can be a cost-effective way to reduce vehicle mass and improve safety. Closed sections are more rigid, resulting in improved structural stiffness. Automotive applications include seat structures, cross members, side impact beams, bumpers, engine subframes, suspension arms, and twist beams. All AHSS grades can be roll formed and welded into tubes with large D/t ratios (tube diameter / wall thickness); tubes having 100:1 D/t with a 1mm wall thickness are available for Dual Phase and TRIP grades.

Figure 1: Automotive Applications for Tubular Components.A-35
As roll formed and welded tubes are used with mounting brackets and little else in some Side Intrusion Beams (Figure 2), or they can be used as a precursor to hydroforming, such as the Engine Cradle shown in Figure 3.

Figure 2: Side intrusion beams made from a welded tube with mounting brackets.S-34

Figure 3: The stages of a Hydroformed Engine Cradle: A) Straight Tube, B) After bending; C) After pre-forming; D) Hydroformed Engine Cradle. S-35
The processing steps of tube manufacturing affect the mechanical properties of the tube, increasing the yield strength and tensile strength, while decreasing the total elongation. Subsequent operations like flaring, flattening, expansion, reduction, die forming, bending and hydroforming must consider the tube properties rather than the properties of the incoming flat sheet.
The work hardening, which takes place during the tube manufacturing process, increases the yield strength and makes the welded AHSS tubes appropriate as a structural material. Mechanical properties of welded AHSS tubes (Figure 4) show welded AHSS tubes provide excellent engineering properties. AHSS tubes are suitable for structures and offer competitive advantage through high-energy absorption, high strength, low weight, and cost efficient manufacturing
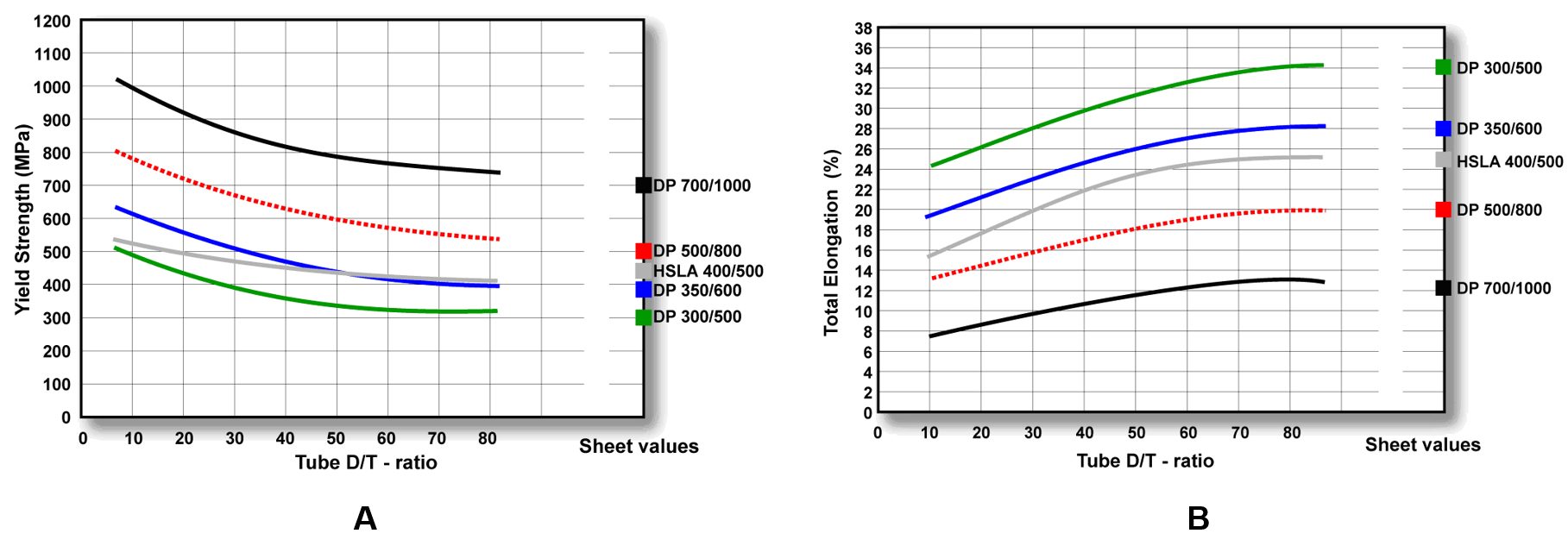
Figure 4: Anticipated Properties of AHSS Tubes; A) Yield Strength, B) Total Elongation.R-1
The degree of work hardening, and consequently the formability of the tube, depends both on the steel grade and the tube diameter/thickness ratio (D/T) as shown in Figure 5. The degree of work hardening influences the reduction in formability of tubular materials compared with the as-produced sheet material. Furthermore, computerized forming-process development utilizes the actual true stress-true strain curve of steel taken from the tube, which is influenced by the steel grade, tube diameter, and forming process.

Figure 5: Examples of true stress – true strain curves for AHSS tubes made from Dual Phase Steel with 590 MPa minimum tensile strength.A-36
Bending AHSS tubes follows the same laws that apply to ordinary steel tubes. Splitting, buckling, and wrinkling must all be avoided. As wall thickness and bend radius decrease, the potential for wrinkling or buckling increases.
One method to evaluate the formability of a tube is the minimum bend radius. An empirically derived formulaS-36 for the minimum Centerline Radius (CLR) considers both tube diameter (D) and total elongation (A) determined in a tensile test with a proportional test specimen, and assumes tube formation via rotary draw bending:
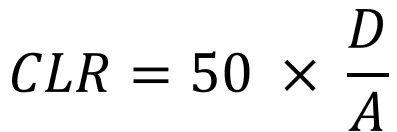
The formula shows that a bending radius equal to the tube diameter (1xD) requires a steel with 50% elongation. Successfully bending low elongation material needs a greater bend radius. Consider, for example, a dual phase steel grade where the elongation of a sample measured off the tube is 12.5%. Here, the minimum bend radius is 4 times the tube diameter. The tube bending method, the use and type of mandrels, and choice of lubrication may all affect the CLR.
The engineering strain on the outer surface can be estimated as the tube diameter (D) divided by twice the Centerline Radius (CLR):

For example, if you are bending a 40 mm diameter tube around a centerline radius of 100mm, the engineering strain on the outer surface is approximately 40/[2*100] = 20%. As a rough estimate, successful bending requires the tube to have a minimum elongation value from a tensile test in excess of this amount. Otherwise, a larger radius or modifications to the forming process is needed.
Springback is related to the elastic behavior of the tube. Yield strength variation between production batches can lead to variation in the amount of springback. A rule of thumb is that a variation of ± 10 MPa in yield strength causes a variation of approximately ± 0.1° in the bending radius. In addition, a high frequency weld which is harder and stronger than the base material causes a maximum of approximately ± 0.1° variation in bending radius.S-36
The bending behavior of tube depends on both the tubular material and the bending technique. The weld seam is also an area of non-uniformity in the tubular cross section, and therefore influences the forming behavior of welded tubes. The recommended procedure is to locate the weld area in a neutral position during the bending operation.
Figures 6 and 7 provide examples of the forming of AHSS tubes. The discussion on Tailored Products describes tailored tubes, which may be further hydroformed.

Figure 6: DP steel bent to 45 degrees with centerline bending radius of 1.5xD using booster bending. Steel properties in the tube: 610 MPa yield strength, 680 MPa tensile strength, 27% total elongation. R-1

Figure 7: Hydroformed Engine Cradle made from a dual phase steel welded tube by draw bending with centerline bending radius of 1.6xD and a bending angle greater than 90 degrees. Steel properties in the tube: 540 MPa yield strength, 710 MPa tensile strength, 34% total elongation. R-1
Key Points
- Due to the cold working generated during tube forming, the formability of the tube is reduced compared to the as-received sheet.
- The work hardening during tube forming increases the YS and TS, thereby allowing the tube to be a structural member.
- Successful bending requires aligning the targeted radii with the available elongation of the selected steel grade.
- The weld seam should be located at the neutral axis of the tube, whenever possible during the bending operation.
Joining
The unique physical characteristics of Advanced High Strength Steels (AHSS) present some challenges to welding and bonding processes. AHSS differ from mild steels by chemical composition and microstructure, and it’s important to note that their microstructures will change from welding operations. For example, intensive localized heat associated with some welding processes causes a significant change in the local microstructure, and hence affect properties. Due to fast Cooling Rates (CR) typical in welding, it is normal to see martensite and/or bainite microstructures in the weld metal and in the Heat-Affected Zone (HAZ).
When joining AHSS, production process control is important for successful assembly. Manufacturers with highly developed joining control methodology will experience no major change in their operations. Others may require additional checks and maintenance. In certain instances, modifications to equipment or processing methodologies may be required for successful joining of AHSS.
The coating methods for AHSS are similar to those for mild steels. Welding of either AHSS or mild steels with coatings will generate fumes. The amount and nature of fumes will depend on the coating thickness, coating composition, joining method, and fillers used to join these materials. The fumes may contain some pollutants. The chemical composition of fumes and the relevant exhaust equipment must meet appropriate regulatory standards. Thicker coatings and higher heat inputs cause more fumes. Additional exhaust systems should be installed. While welding AHSS (with or without metallic or organic coatings and oiled or not oiled) gases and weld fumes are created similar to mild steels. The allowed fumes or gases must comply with respective national rules and regulations.
Joining Processes
Considering recent developments of hybrid approaches to welding, there are now over 100 types of welding processes available for the manufacturer or fabricator to choose from. The reason that there are so many processes is that each process has its list of advantages and disadvantages that make it more or less appropriate for a given application. Arc welding processes offer advantages such as portability and low cost but are relatively slow and use a considerable amount of heating to produce the weld. High energy density processes such as laser welding generally produce low heat inputs and fast welding speeds, but the equipment is very expensive and joint fit-up needs to be ideal. Solid-state welding processes avoid many of the weld discontinuities produced by those requiring melting (fusion), but they may be expensive and often are restricted to limited joint designs. Resistance welding processes are typically very fast and require no additional filler materials but are often limited to thin sheet applications or very high-production applications such as in the automotive industry.
Most welding processes produce a weld (metallic bond) using some combination of heat, time, and/or pressure. Those that rely on extreme heat at the source such as arc and high energy density processes generally need no pressure and relatively small-to-medium amounts of time. This section introduces joining processes that are applicable to HSS automotive applications, while describing unique process attributes.
Resistance Spot Welding
Judging Weldability Using Carbon Equivalence (CE)
Existing Carbon Equivalent (CE) formulas for Resistance Spot Welding (RSW) of steels do not adequately predict weld performance in AHSS. Weld quality depends on variables such as thickness, strength, loading mode, and weld size. New formulae are proposed by various entities. Because there is no universally accepted formula, use of any one CE equation is not possible and users should develop their own CE equations based on their experience.
Part Fit-Up
Resistance welding depends on the interfacial resistance between two sheets. Good and consistent fit-up of parts is important to all resistance welding. Part fit-up is even more critical to the welding of AHSS due to increased YS and greater springback. In case of poor or inconsistent part fit-up, large truncated cone electrodes are recommended for both AHSS and conventional steels. The larger cap size will have large current range, which might compensate for the poor part fit-up. Also, progressive electrode force and upslope can be used to solve poor part fit-up.
Joining, Resistance Welding Processes
Fundamentals and Principles of Resistance Welding
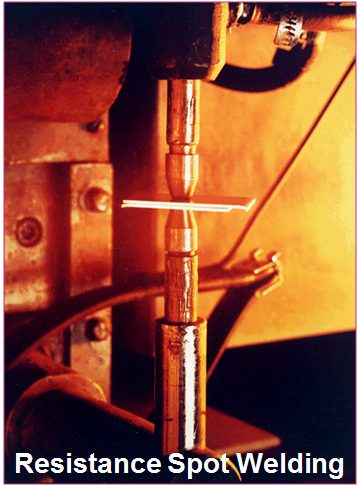
Figure 1: Resistance Spot Welding
Resistance welding processes represent a family of industrial welding processes that produce the heat required for welding through what is known as joule (J = I Rt) heating. Much in the way a piece of wire will heat up when current is passed through it, a resistance weld is based on the heating that occurs due to the resistance of current passing through the parts being welded. Since steel is not a very good conductor of electricity, it is easily heated by the flow of current and is an ideal metal for resistance welding processes. There are many resistance welding processes, but the most common is Resistance Spot Welding (RSW) (Figure 1). All resistance welding processes use three primary process variables – current, time, and pressure (or force). The automotive industry makes extensive use of resistance welding, but it is also used in a variety of other industry sectors including aerospace, medical, light manufacturing, tubing, appliances, and electrical.
Types of Resistance Welding
In addition to RSW, three other common resistance welding processes are Resistance Seam (RSEW), Projection (RPW), and Flash Welding (RFW) (Figure 2). The RSEW process uses two rolling electrodes to produce a continuous-welded seam between two sheets. It is often the process of choice for welding leak tight seams needed for automotive fuel tanks. RPW relies on geometrical features machined or formed on the part known as projections to create the required weld current density. RFW is very different from the other processes in that it relies on a rapid succession of high-current-density short current pulses which create what is known as flashing. During flashing, molten metal is violently expelled as the parts are moved together. The flashing action heats the surrounding material which allows a weld to be created when the parts are later brought together with significant pressure. Other important resistance welding processes which are not shown include High-Frequency Resistance Welding (HFRW) (used for producing the seams in welded pipe), and Resistance Upset Welding (RUW).
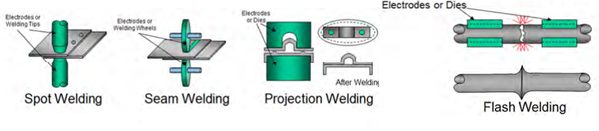
Figure 2: Common resistance welding processes.
In summary, most resistance welding processes offer the following advantages and limitations:
- Advantages:
- Can weld most metals, but works best with steel
- Extremely fast welding speeds are possible (a typical spot weld is produced in 1/5 of a second)
- Very good for automation and production because of the “self-clamping” aspect of the electrodes
- No filler materials required
- RSW and RSEW are ideal for welding of thin sheets
- Limitations:
- Equipment is much more expensive than arc welding equipment
- Welds cannot be visually inspected (except for RFW and RUW welds)
- The requirement for extremely high currents creates high power line demands
- Equipment is not portable
- Mechanical properties such as tensile and fatigue of welds made from processes such as spot welding can be poor due to the sharp geometrical features at the edge of the weld
- Electrode wear