Resistance Spot Welding
In general, if any type of AHSS [Dual-Phase (DP), Transformation-Induced Plasticity (TRIP), Complex Phase (CP), Ferrite Bainite (FB), or Martensitic (MS)] is used for the first time, the user should take the welding schedules applied to mild steel and then:
- Increase the electrode force by 20% or more depending on Yield Strength.
- Increase weld time as appropriate.
If these changes are insufficient, try these additional changes:
- A multi-pulse welding schedule (several pulses or post heating).
- Larger tip diameter and/or change the type of electrode.
- Increase the minimum weld size.
When resistance welded, AHSS require less current than conventional mild steel or HSLA because AHSS have higher electrical resistivity. Therefore, current levels for AHSS are not increased and may even need to be reduced depending on material chemical composition. However, most AHSS grades may require higher electrode forces for equivalent thickness of mild steels because electrode force depends on material strength. If thick mild steel or HSLA steel (of the same thickness) is replaced by an equivalent thickness of AHSS, the same forces may be required during assembly welding.
AHSS often have tighter weld windows (welding parameters that give acceptable welds) when compared to mild steels, as shown in the Figure 1.
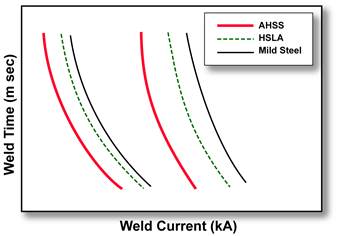
Figure 1: Schematic weld lobes for AHSS, HSLA, and mild steel with a shift to lower currents with increased strength.
The current range (kA) for AHSS of 600-1400MPa during RSW is shown in Figures 2 and 3. The process window for Resistance Spot Welding of AHSS is influenced by the electrode force and welding time used in a major way. The current range increases by an average of 500 A for every additional 500 N of electrode force (Figure 2). The current range also increases by an average of 250 A for each additional 40 ms of welding time (Figure 3). Extra amounts of electrode force and welding time lead to increased current range, allowing for a wider process window.
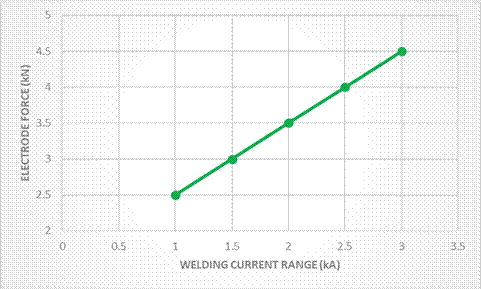
Figure 2: RSW with AHSS, current range for varying electrode force (Cap Type B 16/6, 6-mm tip diameter, single pulse, 340-ms weld time, 250-ms hold time, plug failures.).I-6
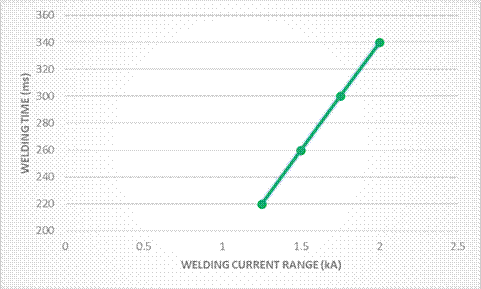
Figure 3: RSW with AHSS, current range for varying weld time (Cap Type B 16/6, 6-mm tip diameter, single pulse, 3.5-kN electrode force, 250-ms hold time, plug failures.).O-1
A more extensive weld studyT-5 of three DP HDGA (45/45 g/m2) coated steels showed similar welding behavior for all three steels. The 1.6-mm-thick steels were DP 340/590, DP 420/780, and DP 550/980. To characterize the welding behavior of the steels, useful current ranges and static weld tensile tests were performed. The useful current range is the difference between the welding current required to produce a minimum button size (Imin) and the current that causes expulsion of weld metal (Imax). In this study, the 4√t as the minimum button diameter was used, where “t” is the nominal sheet thickness. This is generally used in the automotive and steel industries. The weld current range was 2.2 kA for the DP 340/590 and DP 420/780 and 2.5 kA for the DP 550/980 steel (Figure 4). These current ranges are sufficiently wide to weld successfully the DP steels. The study also found no weld imperfections, which means these three DP steels are weldable with simple, easy to use welding parameters.
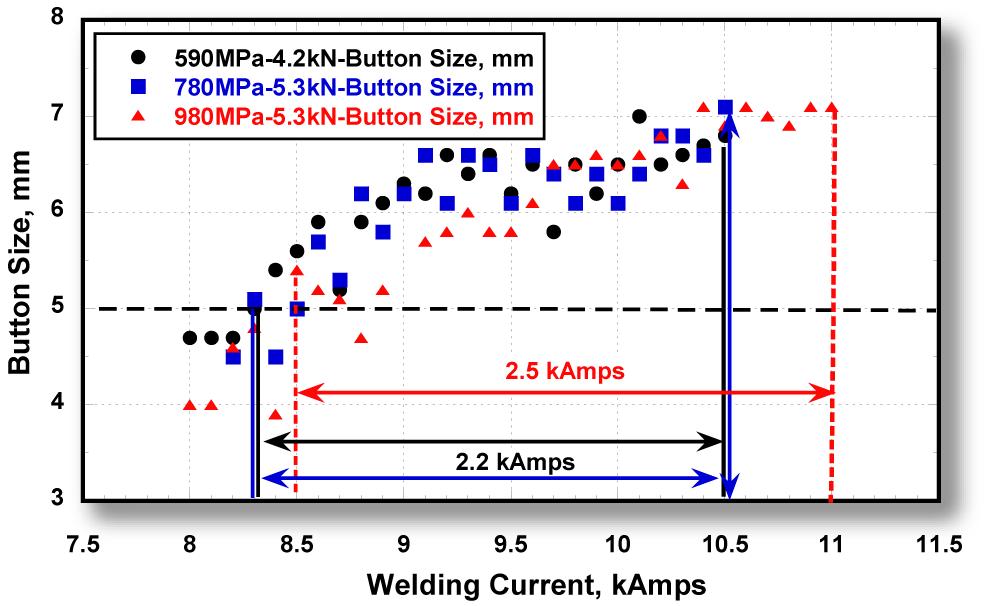
Figure 4: Welding current ranges for 1.6-mm DP HDGA steels with minimum tensile strengths of 590, 780, and 980 MPa.T-5
Average reported weld hardness was 380 HV (Vickers Hardness) for the DP 340/590 and 415 HV for the other two. Again, all three DP steels had similar weld hardness distributions. The study also concluded that weld fracture mode alone is not a good indicator of weld integrity and performance. The load to fracture should be considered more important in judging weld integrity.
A second studyT-6 compared two 1.6-mm-thick HDGA (45/45 g/m2) steels: DP 420/700 and TRIP 420/700. The weld current range for 18 cycles weld time was similar: 1.4 kA for the DP 420/700 and 1.5 kA for the TRIP 420/700. The average weld hardness was 400 HV for both steels. The study concluded that acceptable welds with no imperfections can be produced in both steel grades. Both steel grades are readily weldable with easily adoptable welding parameters. Weld tensile strength differences between the two steels were small and not considered statistically significant.
Weld schedules (Figure 5) with pulsed current profiles for AHSS can have weld-current ranges similar to mild steel. Even though there is no increased tendency for weld expulsion with AHSS avoiding weld expulsion is highly desirable with AHSS. Loss of nugget material can affect weld-nugget size and strength.
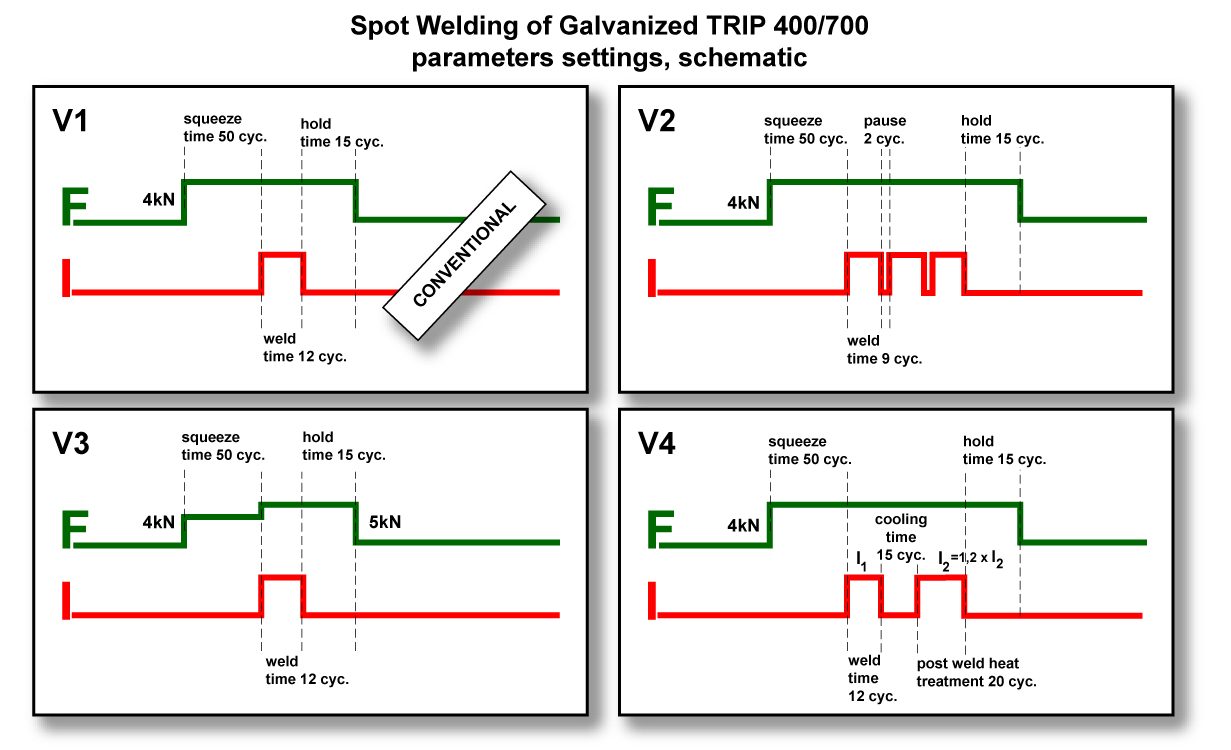
Figure 5: Schematics of optimized weld schedules for AHSS.B-1
Post annealing (tempering pulse weld schedule) of TRIP steel may alter weld fracture mode and weld current range (Figure 6). However, since studies have shown that the occurrence of partial or IF fractures does not necessarily indicate poor weld quality, the use of pulsed current is not required to improve weld quality. Further, the effect of current pulsing on tensile and fatigue properties, as well as the electrode tip life, is not known. Therefore, users should perform their own evaluations regarding the suitability of such modified parameters.
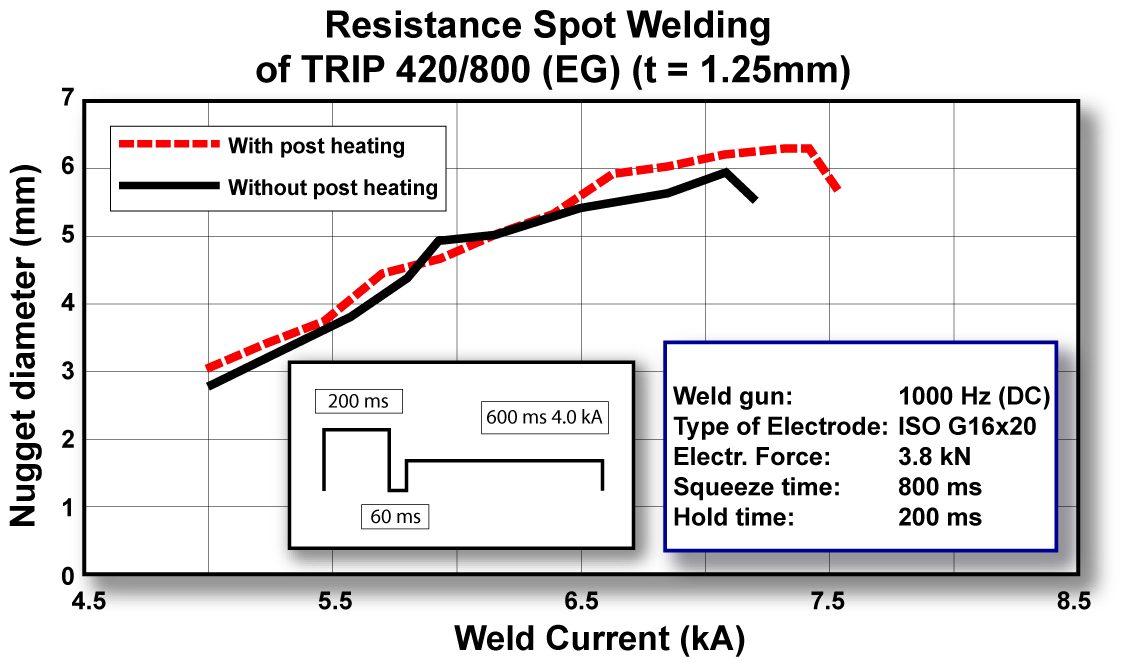
Figure 6: Post annealing may enlarge weld current range.B-1
Additional work using Quench and Partition (Q&P) 980 showed less current required than conventional steels because it has higher electrical resistivity. Due to ultra-high base metal (BM) strength, it needs higher electrode force than conventional steels which have equivalent thickness. The weld lobe of 1.6-mm Q&P 980 is shown in Figure 7 with the pulsed weld time and force of 5.8 kN. The yellow zone of this figure shows the fracture mode of full button (FBF) when peel tested. Some pictures of these weld spots’ fracture mode are captured in Figure 8, for diameters of 6.0 to 7.7 mm.
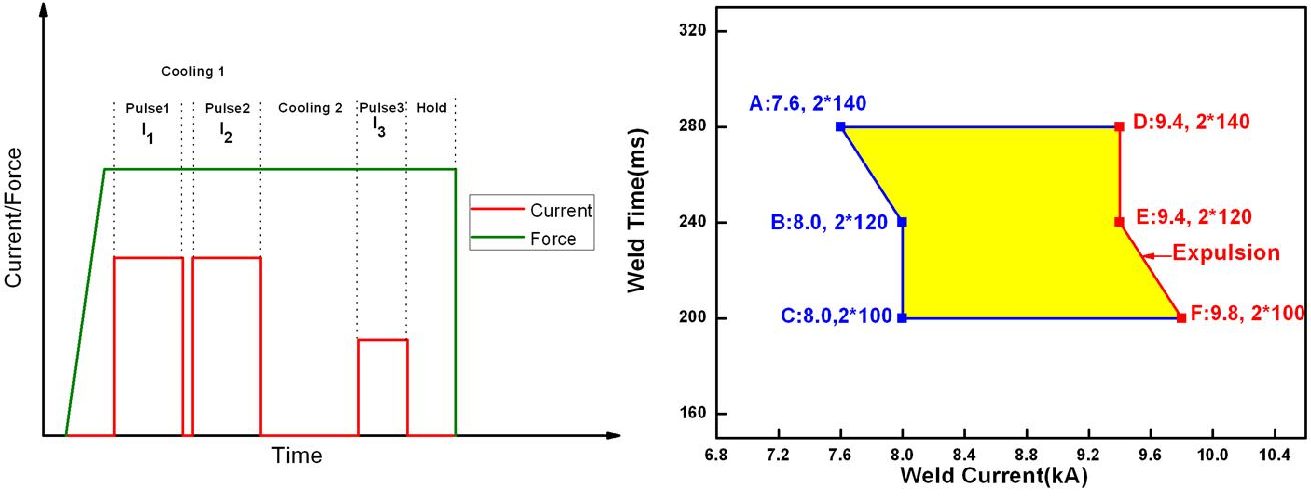
Figure 7: Pulsed current profile and weld lobe of 1_6-mm Q&P 980.B-4
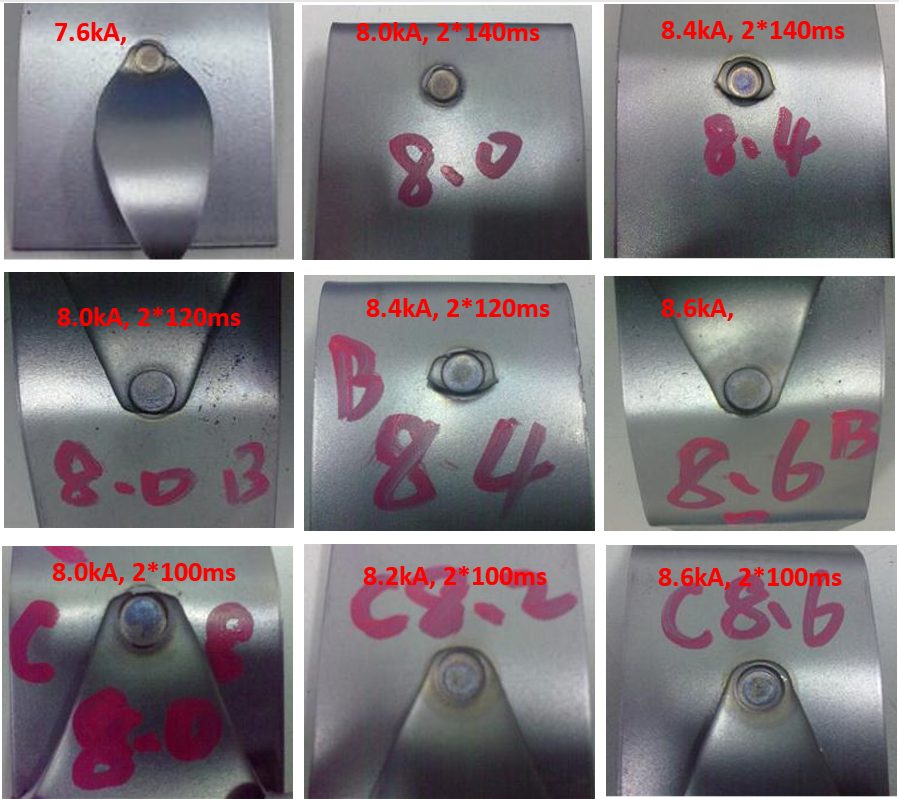
Figure 8: Fracture mode of weld spots in yellow zone.B-4
Hardness measurements and cross sections through the spot weld different zones can be identified as depicted in Figure 9. In a first step, the spot-welded joint can be subdivided into three zones: weld, Heat Affected Zone (HAZ), and BM. The weld is covered by the HAZ, where the melting temperature is not reached but high enough to change the microstructure. This region is dominated by inhomogeneous properties due to the different temperature and cooling gradients. Considering the hardness measurements of AHSS 3 sample, even a softening in the HAZ compared to the BM can be observed. Finally, the HAZ is surrounded by the BM, which does not show any local changes within the structure. These modifications of microstructure in the HAZ and weld are essential for the load-bearing capacity because the strength and ductility are drastically changed in comparison to the BM. Normally a high hardness is related to high strength and less ductility.
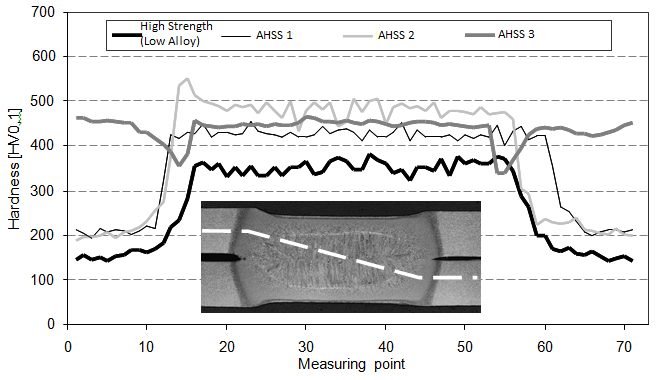
Figure 9: Hardness distribution through spot welds of various strength steels.P-7
Weld spot micrograph and microhardness of 1.6-mm Q&P 980 is shown in Figure 10, in which no weld defects, such as cracks, shrinkage void, pore, no fusion, deep indentation, etc. were found. Hardness testing is typically performed as shown in Figure 11 (diagonal traverse across the weld from BM of top coupon to BM of bottom coupon) using a suitable instrument for micro-indentation hardness testing (Vickers or Knoop).
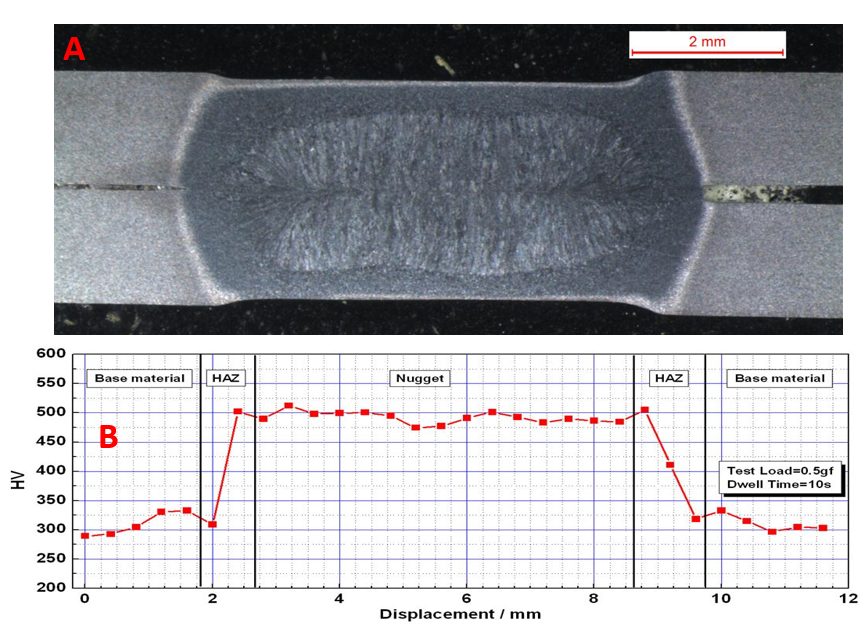
Figure 10: Weld spot micrograph and microhardness of 1.6-mm DP 980.B-4
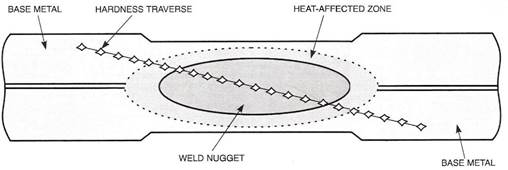
Figure 11: Typical cross-sectioned weld and hardness traverse.A-13
The different hardness values seen in a typical cross-sectioned weld depict different microstructural regions.P-8 Figure 12 shows the temperature distribution of a typical 2T weldment of hot stamped boron steel. At the solidified weld nugget, we see the highest temperatures and steadily decrease toward the unaffected base metal. The weld metal, coarse grain heat affected zone, fine grain heat affected zone, and unaffected base metal are made up of martensitic microstructure. The base metal has this microstructure due to the heat treatment (hot stamping) process. The weld metal, coarse grain heat affected zone, and fine grain heat affected zone are exposed to austenitizing temperature upon welding and are cooled rapidly reforming the martensite microstructure. The subcritical heat affected zone has a unique microstructure of over-tempered martensite. In this region, the peak temperature re below the Ac1, causing the base metal martensitic microstructure to decompose into ferrite and cementite. Micrographs of the different weld regions can be seen in Figure 13.
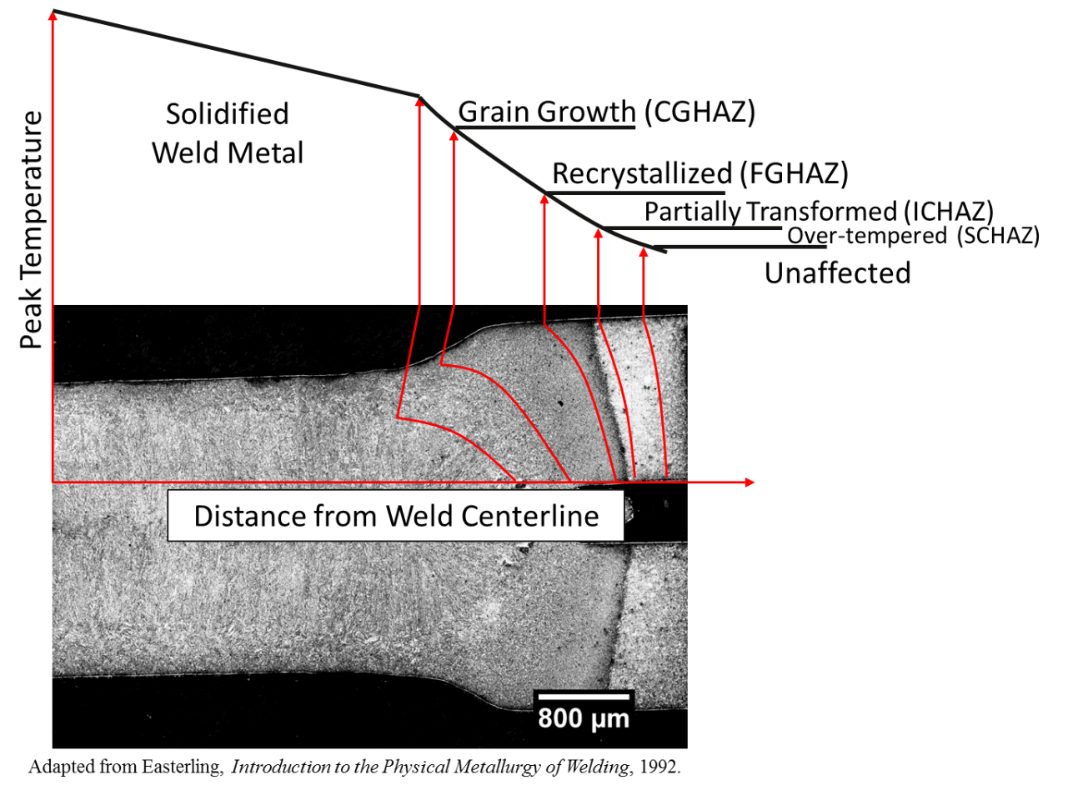
Figure 12: Temperature distribution of a typical 2T RSW of hot stamped boron steel.P-8
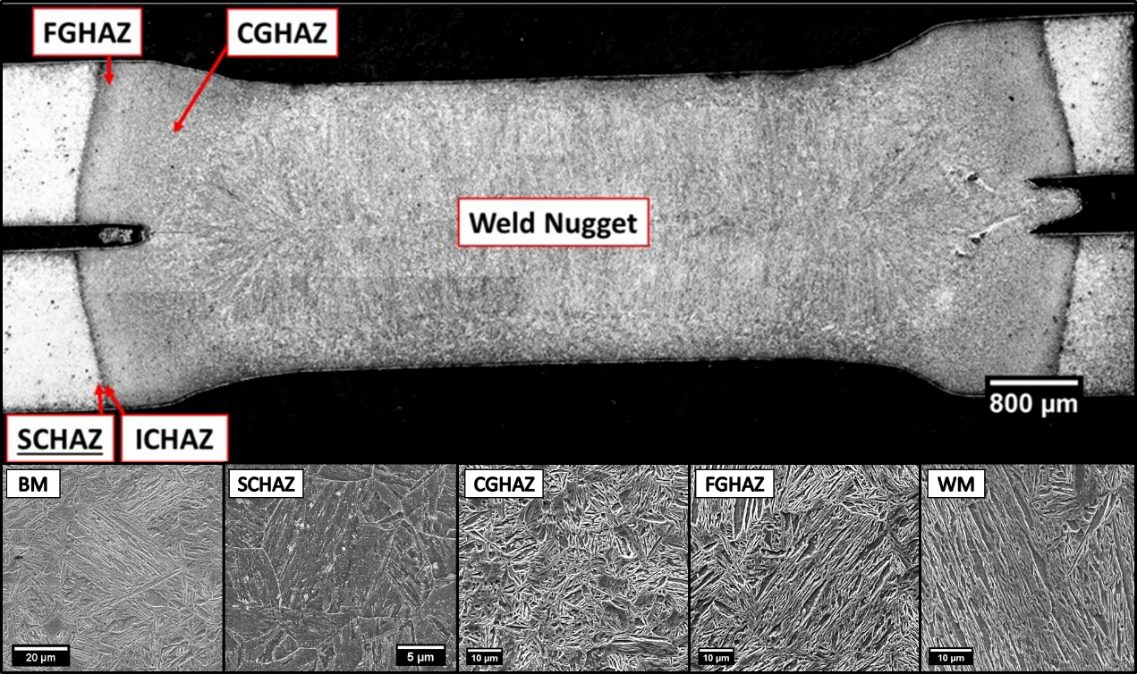
Figure 13: Different microstructures seen throughout the HAZ of a 2T hot stamped boron steel joint.P-8
Resistance Spot Welding, Resistance Welding Processes
The Resistance Spot Welding (RSW) process is often used as a model to explain the fundamental concepts behind most resistance welding processes. Figure 1 shows a standard Resistance Spot Welding arrangement in which two copper electrodes apply force and pass current through the sheets being welded. If the sheets are steel, the resistance to the flow of current of the sheets will be much higher than the copper electrodes, so the steel will get hot while the electrodes remain relatively cool. But another important characteristic exists that is critical to most resistance welding processes – the contact resistance between the parts (or sheets) being welded. As indicated on the figure, the highest resistance to the flow of current is where the sheets meet (“Resistance” 4). This fact allows a weld nugget to begin forming and grow exactly where it is needed – between the sheets.
The figure depicts the flow of current from one electrode to the other as an electrical circuit that contains seven “resistors”. Resistors 1 and 7 represent the bulk resistance of the copper electrodes, Resistors 2 and 6 represent the contact resistance between the electrodes and the sheets, Resistors 3 and 5 represent the bulk resistance of the sheets, and Resistor 4, as mentioned, represents the contact resistance between the sheets. Another fact that works strongly in the favor of resistance welding of steel is that as the steel is heated, its resistivity relative to copper increases even more. So, the initial contact resistance effectively heats the surrounding area which is in turn heated more rapidly because its resistance is higher since it is hotter. As a result, heating and weld nugget formation can occur quite rapidly. A typical weld time for RSW of steel is approximately 1/5 of a second. The current required in resistance welding is much higher than arc welding, and it is in the range of 8-15 kA.
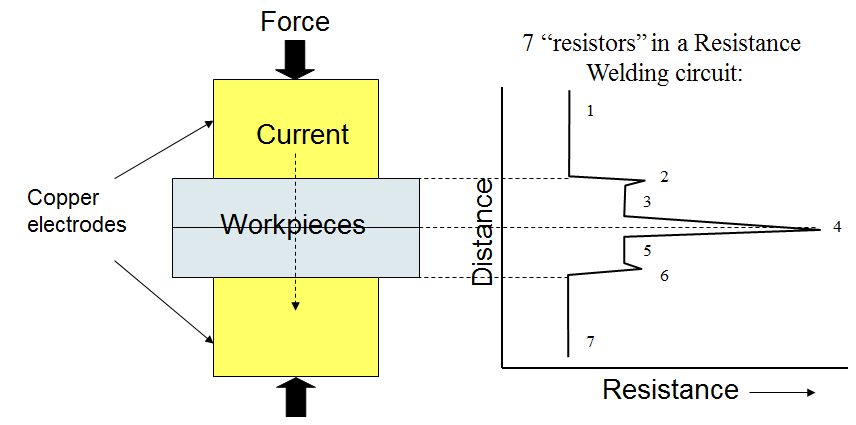
Figure 1: Resistances associated with steel Resistance Spot Welding.
Most welding processes produce welds that provide strong visible evidence of weld quality, so visual examination is often an important approach to verifying the quality of the weld. However, with most resistance welding processes visible examination is not possible due to the “blind” weld location between the sheets or parts being welded. As a result, maintaining weld quality with processes such as Resistance Spot Welding is highly dependent on what is known as a lobe curve (Figure 2), which is basically a process window for Resistance Spot Welding. The lobe curve represents ranges of weld current and time that will produce a spot weld nugget size that has acceptable mechanical properties for the intended application. So, weld quality monitoring with resistance welding processes relies highly on the ability to monitor parameters such as current and time. During production, if a weld is made with parameters that fall outside of the lobe curve, the weld is considered unacceptable. Ultrasonic testing is also often used in the automotive industry for Nondestructive Testing (NDT) of the blind location of Resistance Spot Welding.
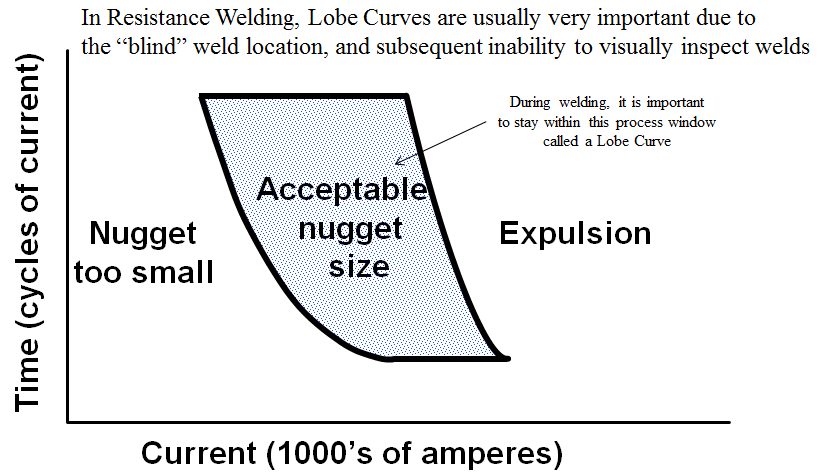
Figure 2: Resistance welding lobe curve.
RSW Electrode Geometry
Electrode geometry is a very important consideration with RSW. Figure 3 shows three common shapes, but there are many more options available including unique custom designs for specific applications. The basic electrode geometry is usually selected to improve the electrical-thermal-mechanical performance of an electrode. This is generally a geometry in which the cross-sectional area increases rapidly with distance from the workpiece, thereby providing a good heat sink. The choice of shape may also include considerations such as accessibility to the part and how much surface marking of the part is acceptable. The diameter of the electrode contact area is also a consideration. Too small an area will produce undersized welds with insufficient strength, while too large an area will lead to unstable and inconsistent weld growth characteristics.
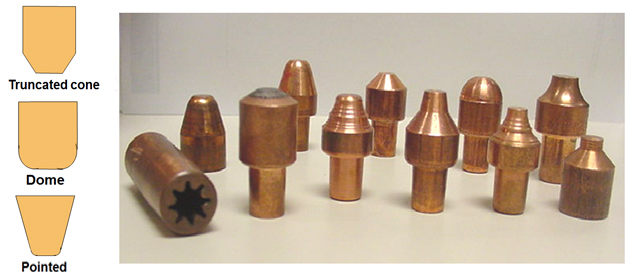
Figure 3: Typical RSW electrode geometries (left), example geometries used by automotive manufacturers (right).
Electrodes must be able to conduct current to the part, mechanically constrain the part, and conduct heat from the part. They must be able to sustain high loads at elevated temperatures, while maintaining adequate thermal and electrical conductivity. The choice of electrode alloy for a given application is often dictated by the need to minimize electrode wear. When electrodes wear, they typically begin to “mushroom”, or grow larger in diameter. Electrode wear is accelerated when there is an alloying reaction between the electrode and the part, a common problem when welding Aluminum (Al) and coated steels. As the electrode diameter increases, the current density decreases, resulting in a decrease in the size of the weld. Since the strength of a spot-welded joint is directly related to the size of the weld nugget, electrode wear can be a big problem.
A range of Copper (Cu)-based or refractory-based electrode materials are used depending on the application. The Resistance Welding Manufacturers Association (RWMA) sorts electrode materials into three groups: A, B, and C. Group A contains the most common Cu-based alloys (see Table 1), Group B contains refractory metals and refractory metal composites, and Group C contains specialty materials such as dispersion-strengthened copper. Within the groups, they are further categorized by a class number. The general rule of thumb is as the class number goes up, the electrode strength goes up but the electrical conductivity goes down. When electrical conductivity goes down, the electrode heats more easily, resulting in premature electrode wear. The choice of electrode material involves many factors, but generally higher strength electrodes will be selected when higher strength materials are being welded. It is also important that the electrical and thermal conductivities of the electrode are much higher than those of the material being welded.
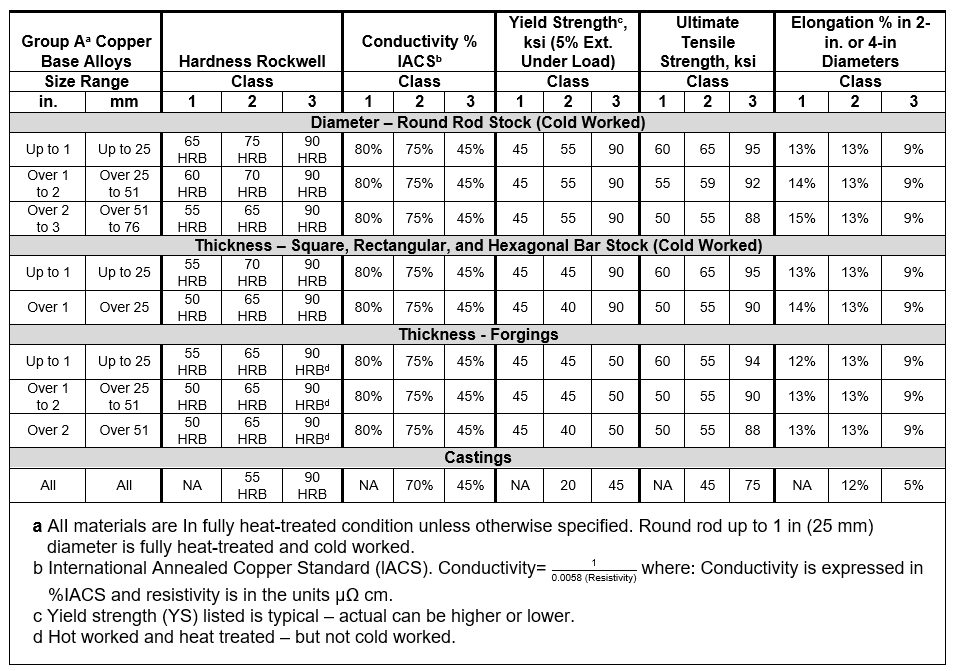
Table 1: Minimum mechanical and physical properties of Cu-based alloys for RWMA electrodes.A-18
The two most commonly used electrodes are the Class 1 and 2 electrodes of Group A. Class 1 electrodes [99% copper, 1% cadmium; 60 ksi UTS (forged); conductivity 92% International Annealed Copper Standard (IACS)] offer the highest electrical and thermal conductivity, and are typically used for spot welding Al alloys, magnesium alloys, brass, and bronze. Class 2 [99.2% copper, 0.8% chromium; 62 ksi UTS (forged), 82% IACS] electrodes are general-purpose electrodes for production spot and seam welding of most materials. IACS refers to a copper standard to which the electrodes are compared. Pure Cu has an IACS number of 100%.A-11, P-6, O-1
Joining, Resistance Welding Processes
Fundamentals and Principles of Resistance Welding
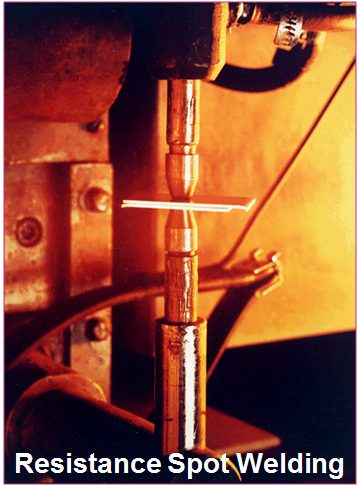
Figure 1: Resistance Spot Welding
Resistance welding processes represent a family of industrial welding processes that produce the heat required for welding through what is known as joule (J = I Rt) heating. Much in the way a piece of wire will heat up when current is passed through it, a resistance weld is based on the heating that occurs due to the resistance of current passing through the parts being welded. Since steel is not a very good conductor of electricity, it is easily heated by the flow of current and is an ideal metal for resistance welding processes. There are many resistance welding processes, but the most common is Resistance Spot Welding (RSW) (Figure 1). All resistance welding processes use three primary process variables – current, time, and pressure (or force). The automotive industry makes extensive use of resistance welding, but it is also used in a variety of other industry sectors including aerospace, medical, light manufacturing, tubing, appliances, and electrical.
Types of Resistance Welding
In addition to RSW, three other common resistance welding processes are Resistance Seam (RSEW), Projection (RPW), and Flash Welding (RFW) (Figure 2). The RSEW process uses two rolling electrodes to produce a continuous-welded seam between two sheets. It is often the process of choice for welding leak tight seams needed for automotive fuel tanks. RPW relies on geometrical features machined or formed on the part known as projections to create the required weld current density. RFW is very different from the other processes in that it relies on a rapid succession of high-current-density short current pulses which create what is known as flashing. During flashing, molten metal is violently expelled as the parts are moved together. The flashing action heats the surrounding material which allows a weld to be created when the parts are later brought together with significant pressure. Other important resistance welding processes which are not shown include High-Frequency Resistance Welding (HFRW) (used for producing the seams in welded pipe), and Resistance Upset Welding (RUW).
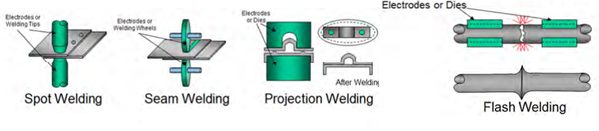
Figure 2: Common resistance welding processes.
In summary, most resistance welding processes offer the following advantages and limitations:
- Advantages:
- Can weld most metals, but works best with steel
- Extremely fast welding speeds are possible (a typical spot weld is produced in 1/5 of a second)
- Very good for automation and production because of the “self-clamping” aspect of the electrodes
- No filler materials required
- RSW and RSEW are ideal for welding of thin sheets
- Limitations:
- Equipment is much more expensive than arc welding equipment
- Welds cannot be visually inspected (except for RFW and RUW welds)
- The requirement for extremely high currents creates high power line demands
- Equipment is not portable
- Mechanical properties such as tensile and fatigue of welds made from processes such as spot welding can be poor due to the sharp geometrical features at the edge of the weld
- Electrode wear
Joining Dissimilar Materials, Resistance Welding Steel to Aluminium
Recently research at the Ohio State University is developing methods that combine the benefits of ultrasonic welding and resistance spot welding. Y. Lu and co-workersL-10 developed the ultrasonic plus resistance spot welding process (U+RSW). In this process thin aluminium sheet was joined with steel sheet via ultrasonic welding, followed by RSW between the aluminium side of previously sheet and aluminium sheet as shown in Figure 1. In this study they used 1-mm-thick AA6061-T6 to 0.9-mm-thick AISI 1008 steel with 0.4-mm-thick AA6061-T6 as the insert.
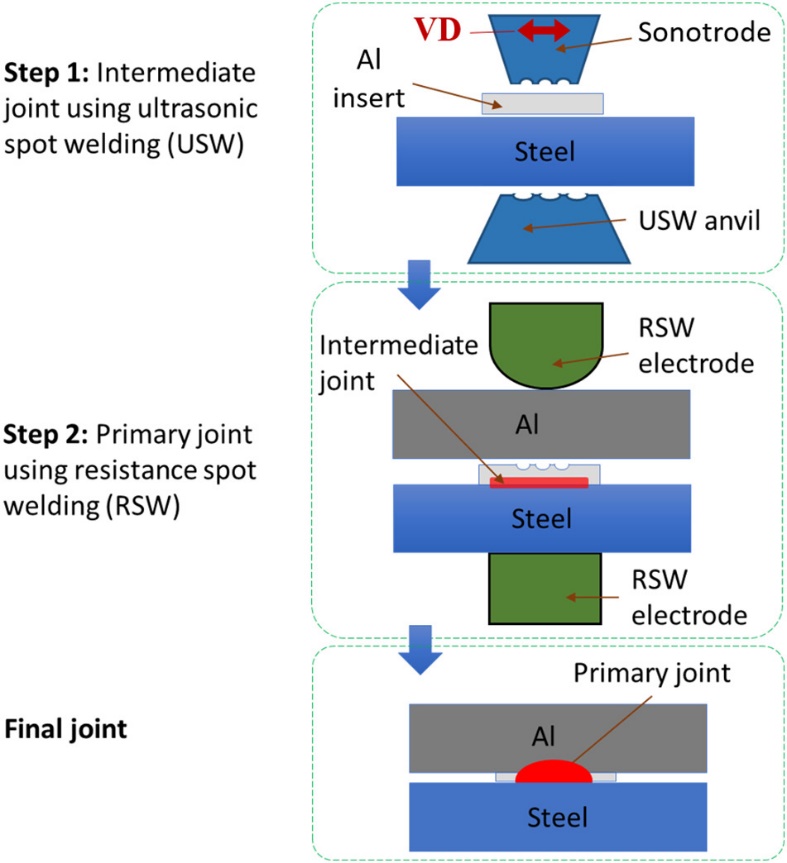
Figure 1: Schematic diagram of U + RSW process. VD is the sonotrode’s vibration direction for USW of intermediate joint.L-10
The U+RSW method showed improved mechanical properties (Figure 2), tensile shear strength and energy absorbed prior to failure. It has shown a relatively thin intermetallic layer.
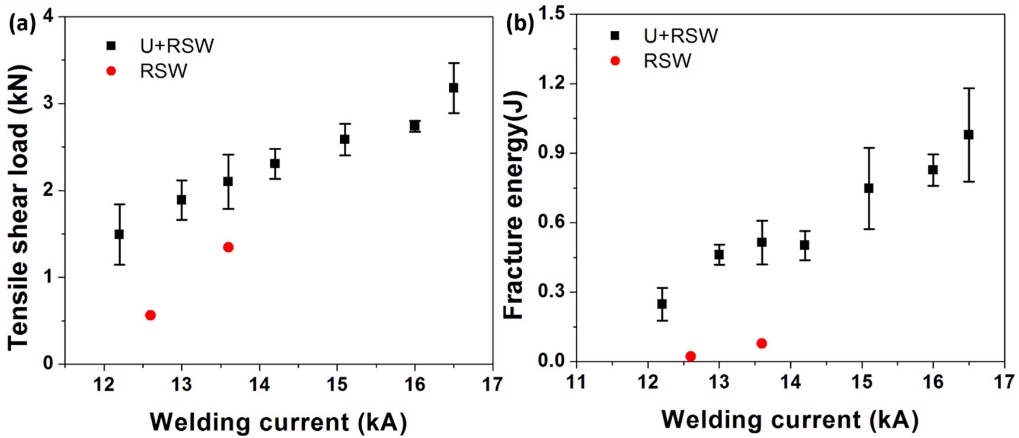
Figure 2: Effect of welding current on tensile shear strength and fracture energy of welded dissimilar joints of AA6061 to AISI 1008 steel. The welding time and the electrode force for RSW were kept constant at 0.083 s and 3.56 kN, respectively.L-10
Another research group have developed ultrasonic resistance welding process (URW), that apply in situ ultrasonic waves during the resistance spot welding process.S-17 The schematics of the process is shown in the Figure 3. Al-6061T6 and electrogalvanized TRIP 780 with dimensions of 70Lx 25Wx 1.6T mm3 and 70Lx 25Wx 1.3T mm3 respectively were used in this study.
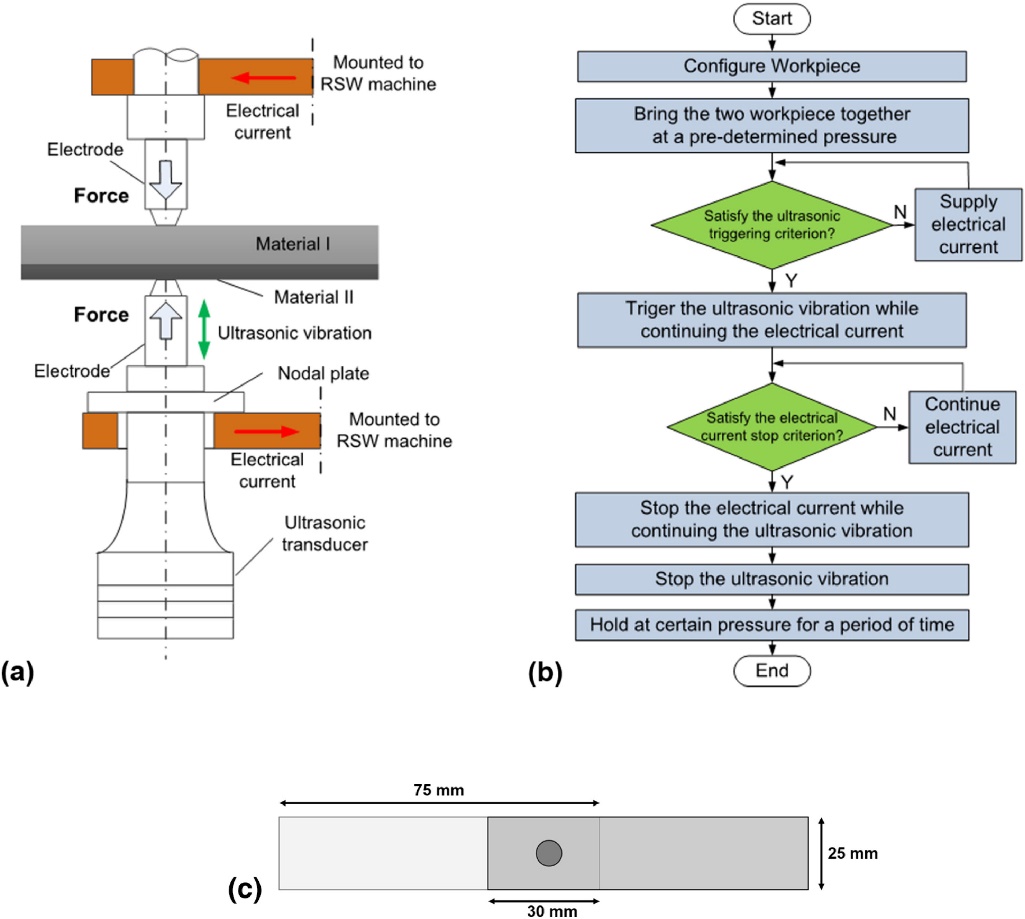
Figure 3: URW Setup (a) Schematic illustration; (b) Flowchart of the URW process.S-17
The URW process have shown improved mechanical properties and defect free interface compared to the RSW process. In situ ultrasonic vibration facilitated the breakdown of the surface oxide and contaminants, which modifies contact resistance and heat generation rate accordingly. If melting occurs, ultrasonic vibration promoted wetting of the molten aluminium over the steel interface and resulted in the formation of defect-free, fully bonded interface as shown in Figure 4. Figure 5 compares the mechanical properties between the RSW & URW process. Comparing URW with traditional RSW, up to 300% increase in strength and more than 150% increase in displacement to failure is reported. SEM images of the fractured surface revealed that ultrasonic waves eliminated the eggcrate morphology generally observed in the RSW welds fractured surface, which is a typical representative of solidification cracking.
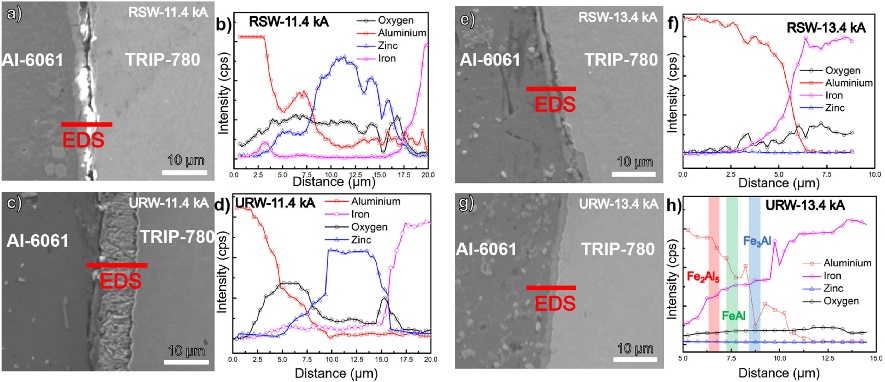
Figure 4: EDS line Scan of Al-6061 & TRIP 780 across interface for RSW at 11.4 kA (a-b) & at 13.4 kA (e-f) and for URW at 11.4 kA (c-d) & at 13.4 kA (g-h).S-17
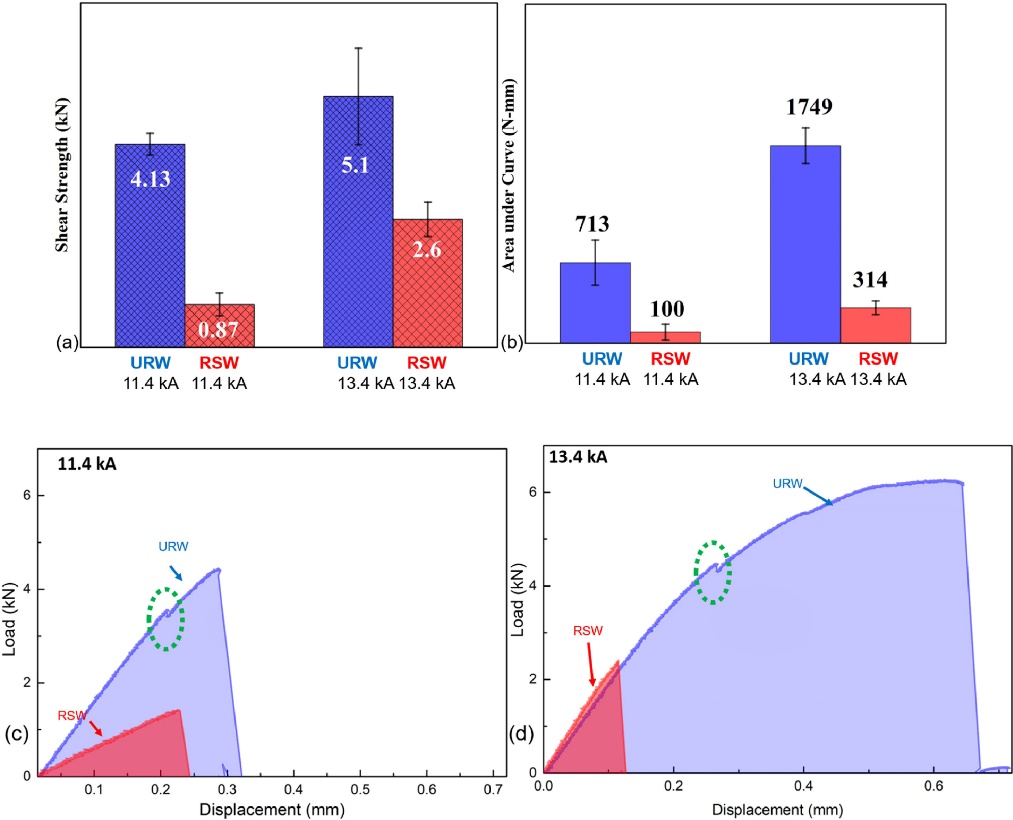
Figure 5: Tensile test results (a) Joint shear strength from 11.4 kA (30 cycles) & 13.4 kA (20 cycles); (b) Energy absorption calculated via area under load-displacement curve for 11.4 kA (30 cycles) & 13.4 kA (20 cycles); (c-d) load-displacement curve for 11.4.S-17
Joining Dissimilar Materials
Multi-material design approach involves using High-Strength Steels and low-density materials, such as aluminium. The key idea is to utilize the right material for the right application in such a way that it should fulfill the service requirements and achieve mass efficiency at the same time. However, it is challenging to fully utilize multi-material design concepts due to joining issues.
Joining is considered a backbone of any manufactured assembly, since the ultimate reliability and integrity of the manufactured product relies on these joints. Dissimilar materials are difficult to join due to the difference in the physical and thermal properties. For example, one of the most desired combinations is aluminium to steel joints, which is challenging due to the large mismatch in the mechanical properties as shown in Table 1. This Joining section is dedicated specifically to the key joining issues between aluminium and steel.
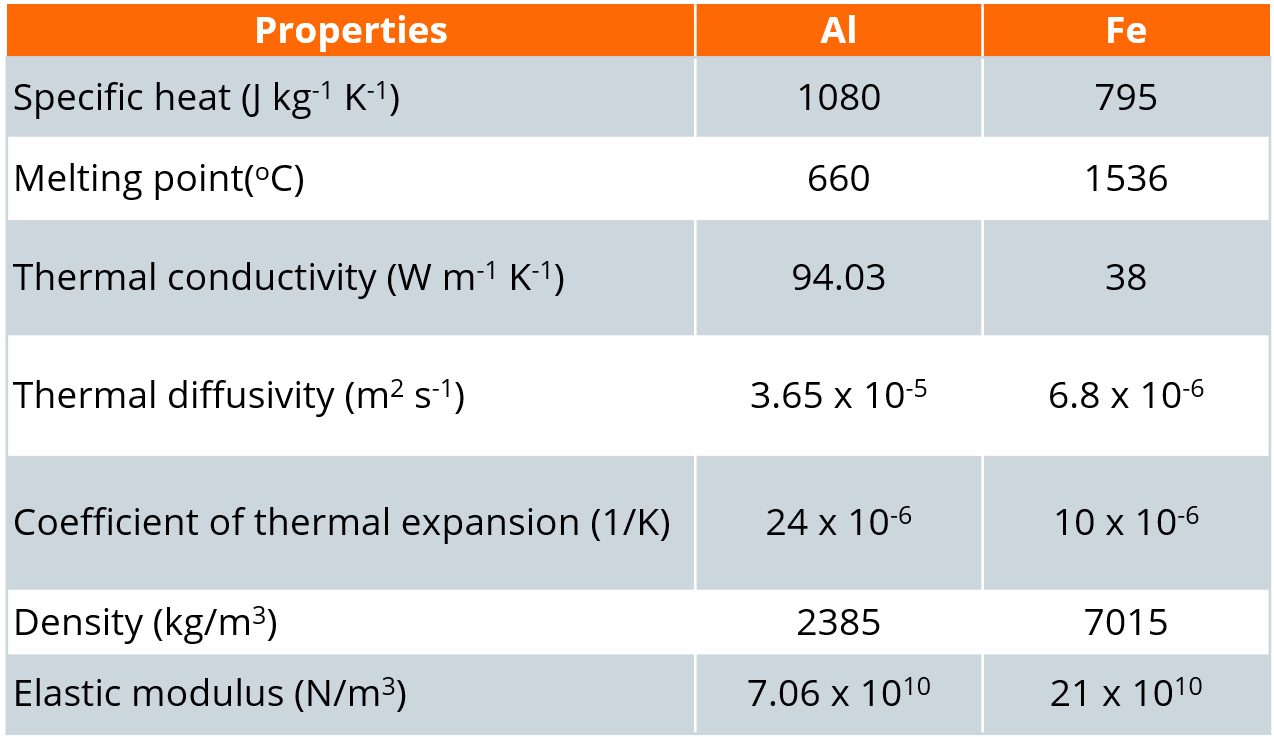
Table 1: Aluminium vs. Steel Material Mechanical Properties
Currently there are three approaches to joining dissimilar materials: solid-state joining, partial solid-state joining and arc joining. During solid state welding, the peak temperature of the process remains below the melting temperatures of the materials to be joined. Examples include diffusion bonding, ultrasonic welding, magnetic pulse welding, friction stir welding and vaporizing foil actuator welding. In partial solid-state welding processes, the peak temperature goes beyond the melting temperature of one of the materials to be joined (e.g. arc brazing & resistance spot welding). The last process (arc welding) has a peak temperature above the melting temperature of both materials to be joined. Practically it is not used anywhere however, it can be utilized in certain applications where the mismatch between the physical properties of the materials to be joined is little.
Among various joining processes, resistance spot welding (RSW) is one of the most widely used joining process in the automotive and aerospace industry due to its ease of automation and high productivity. Browse the topics below to learn more about joining dissimilar materials.