Testing and Characterization
topofpage
The ISO 16630 Hole Expansion Test and the VDA238-100 bend test are among the few standardized tests to characterize local formability, the term which describes when part and process design, in addition to sheet metal properties like strength and elongation, influence the amount of deformation the metal can undergo prior to failure.
Researchers have developed alternate tests to further investigate process parameters and more clearly understand and optimize non-steel related variables. Also important is the investigation of different strain states from the ones seen in the hole expansion and bending tests. Comparisons of the stretched or bent edge performance evaluating different process parameters using the same material help to better define optimum process parameters. Repeating the testing with different AHSS grades confirms if similar trends exist across different microstructures and strengths. Standardization of these alternate tests has not yet occurred, so use caution when comparing specific values from different studies.
Hole Tension Test
Microstructural damage in the shear affected zone reduces edge ductility. Damage has been evaluated with a modified tensile dogbone containing a central hole prepared by shearing or reaming, as shown in Figure 1. In contrast with a hole expansion test using a conical punch, the researchers described this as a Hole Tension test, which determines failure strain as a function of grade and edge preparation.

Figure 1: Hole Tension Test Specimen GeometryP-12
Edge Tension Test
A two-dimensional (2-D) edge tension test, also called Half-A-Dogbone test, also evaluates edge stretchability. There are multiple versions of this type of test, but they all are based on the same concept. Like a standard tensile test, the 2-D edge tension test pulls a steel specimen in tension until failure. Unlike a standard tensile test where both sides of the tensile specimen are milled into a “dog bone”, the 2D tension test uses half of a dogbone with different preparation methods for the straight edge and the edge containing the reduced section (Figure 2). The chosen preparation method for each face is a function of the parameter being investigated (ductility, strain, burr, and shear affected zone for example). Potential edge preparation methods include laser cutting, EDM, water jet cutting, milling, slitting or mechanical cutting at various trim clearances, shear angles, rake angles or with different die materials.

Figure 2: 2-D Edge Tension Test Sample. Note the edges are prepared differently based on the targeted property evaluated.
Side Bending Test
Instead of a dogbone or half-dogbone, some studies use a rectangular strip without a reduced section. Bending performance can be evaluated with a rectangular strip having one finished edge and one trimmed edge while preventing out-of-plane buckling, as shown in Figure 3.G-7
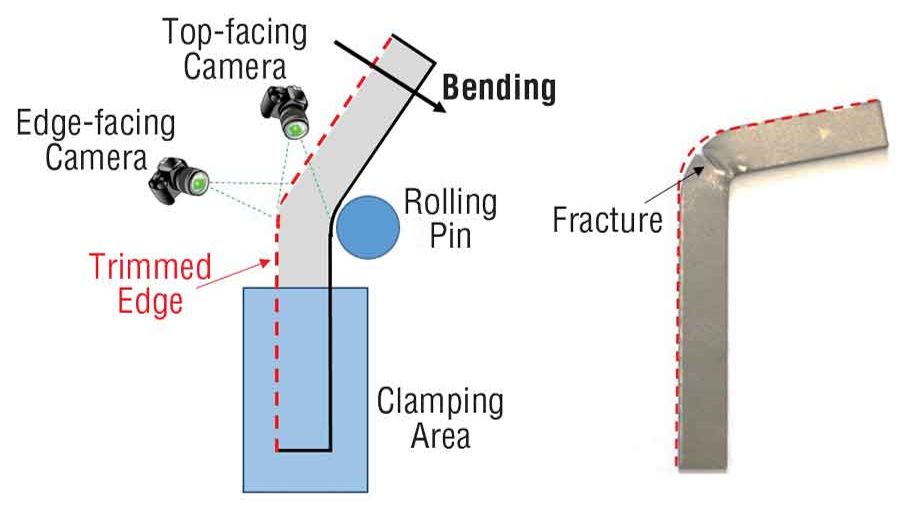
Figure 3: The side-bending test expands a trimmed edge over a rolling pin until detection of the first edge crack.G-7
Half-Specimen Dome Test
Deformation in these three tests occur in the plane of the sheet. Typical hole expansion tests, like production stampings, deform the sheet metal perpendicular to the plane of the sheet. However, hole expansion testing does not always give consistent test results. The half-specimen dome test (HSDT) also attempts to replicate this 3-dimensional forming mode (Figure 4), and appears to be more repeatable likely due to creating a straight cut rather than round hole.
In the HSDT, a rectangular blank is prepared with one edge having the preparation method of interest, like sheared with a certain clearance or laser cut or water-jet cut. The sample is then clamped with the edge to be evaluated over a hemispherical punch. The punch then strains the clamped sample creating a dome shape, with the test stopping with the first crack appears at the edge. Edge stretchability is quantified by measuring dome height or edge thinning or other characteristics.
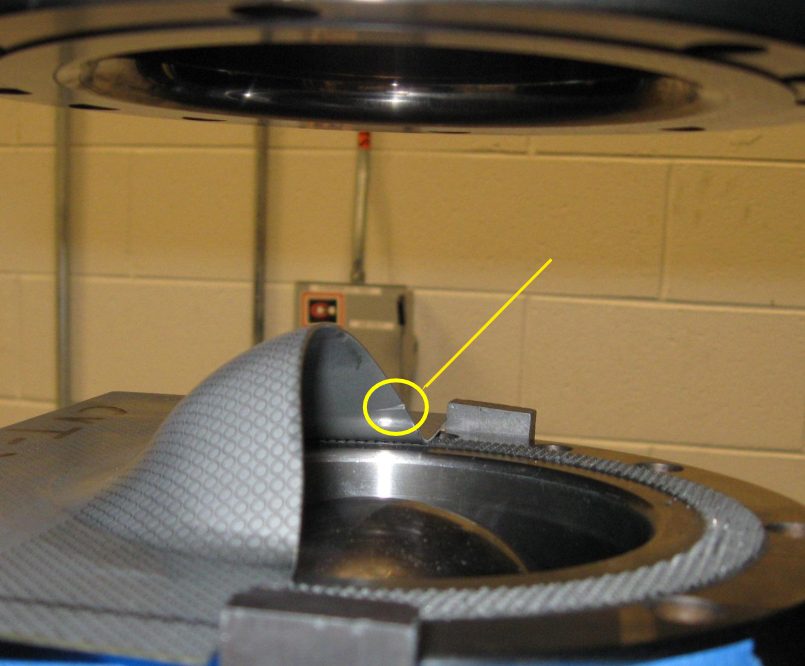
Figure 4: Half-Specimen Dome Test sample. Arrow points to edge crack.S-12
Edge Flange Test
Flanging limits depend on the part contour, edge quality, and material properties. Non-optimal flange lengths – either too long or too short – will lead to fracture. Different tools can assess the influence of flange length, including the one shown in Figure 5 from Citation U-3.

Figure 5: Tool design to investigate flange length before fracture. Flange height: 40mm in left image, 20mm in right image.U-3
Physical tests using this tool show that optimizing sample orientation relative to the rolling direction leads to longer flange lengths before splitting.U-3 Figure 6 highlights the results from testing DP800.

Figure 6: Flange height limits as a function of orientation in DP800.U-3
Back to the Top
Forming Modes
top-of-page
The usual mode of bending is curvature around a straight-line radius (Figure 1). Through the thickness is a gradient of strains from maximum outer fiber tension (the outermost surface) through a neutral axis to inner fiber compression (the surface closest to the punch or bend axis). No strain occurs along the bend axis in the direction parallel to the bend axis, and therefore is in plane strain. The discussion below considers only bulk deformation, and excludes the implications of any edge effects. Bend testing procedures are linked here.

Figure 1: Typical bend where the outer surface is in tension, and the inner surface is in compression. A neutral axis lies in between.S-23
When sheet metal flows through draw beads or over the die radius into the punch opening, it is bent, straightened, and in the case of draw beads re-bent in the opposite direction. The net strain after this process may be relatively small. However, each of the sequential bending and unbending steps strain hardens the sheet metal, which reduces the ability for further deformation of the metal in subsequent operations.
Deformation at the outer surface during three-point bending depends on the stretchability capacity of the metal. The failure strain in the bend is related to the total elongation of conventional steel, but AHSS grades with multiphase microstructures such as DP and TRIP experience shear fracture that severely reduces the bendability before failure occurs. A higher total elongation helps sustain a larger outer fiber stretch of the bend before surface fracture, thereby permitting a smaller bend radius. Since total elongation decreases with increasing strength for a given sheet thickness, the minimum design bend radius must be increased (Figure 2).

Figure 2: Larger bend radius is needed as the total elongation decreases.S-23
The ratio of punch radius to sheet thickness, or the r/t ratio, allows for calculation of the amount of elongation on the outermost surface. This value can be compared against the total elongation of the metal as determined in a tensile test, or against the minimum elongation value allowed in the specification. If the part geometry will not allow for sufficient elongation for the selected metal grade, then either the part, process, or steel grade must change. [Note that this is not a perfect assessment, since elongation in a tensile test is measured relative to a 50 or 80 mm gauge length, which is likely different than the dimensions of the bent section.]
For design and springback control, usually a smaller r/t ratio is desirable. However, this may not be suitable in terms of formability. Increased material strength usually is associated with a reduction in total elongation, which in turn means a successful bend requires a larger r/t ratio.
For equal strengths, most AHSS grades have higher total elongations than conventional HSLA steels. However, several AHSS grades have limited local formability based on their microstructure, and may be at risk for cracking during edge expansion.
Cracking in production stamping conditions at stress levels below what is predicted with Forming Limit Diagrams may be attributed to these local formability failures. As an illustration, physical bend tests and simulations were performed for both HSLA and DP780 steels.S-11 The HSLA global formability failure aligned with simulation predictions (Figure 3), and was accompanied by a visible neck (Figure 4). In contrast, the DP780 showed no visible neck at the failure site (Figure 5) and no correlation between the simulation and actual test results (Figure 6).
Like hole expansion, bending limits in AHSS products are further lowered by shear fracture associated with the interfaces between the ductile ferrite and the hard martensite phase in the microstructure. This reduction becomes more severe as the strength increases, since increasing strength is achieved by increasing the volume of the hard martensite phase. More about shear fracture is found here.

Figure 3: Forming simulation of HSLA with strong correlation to actual testing.S-11

Figure 4: Close-up of visible necking before tensile failure in HSLA.S-11

Figure 5: Comparison of forming simulation with actual testing of the DP780. Note lack of correlation.S-11

Figure 6: Close-up of local formability failure on DP780 with no visible necking before failure.S-11
Rotary Bending
One way to address springback involves the use of rotary benders. Rotary benders transfer the vertical movement of a press stroke into a precise, rotary forming motion. A rocker or rotating die can simultaneously hold, bend, and overbend the sheet past 90° to counter material springback (Figure 7).
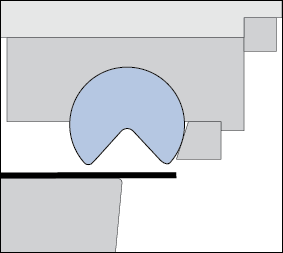
Figure 7: The rotation of the rocker bends the sheet metal around the anvil with less pressure than needed for wipe toolsD-8
Use rotary bending tooling where possible instead of flange wipe dies. Rotary bending allows for easy adjustment of the bending angle to correct for changes in springback due to variations in steel properties, die set, lubrication, and other process parameters. In addition, the tensile loading generated by the wiping shoe is absent.
There are four sequential steps to the process:
1) Downward pressure from the rocker clamps the part with the bending lobes before bending starts
2) Induced rotation of the rocker bends material around the anvil
3) The rocker bends the sheet metal past final angle to compensate for springback
4) The rocker releases the sheet metal to allow springback to desired angle
Using rotary benders to roll darts into the part during bending provides another way to reduce springback and stiffen the part (Figure 8).
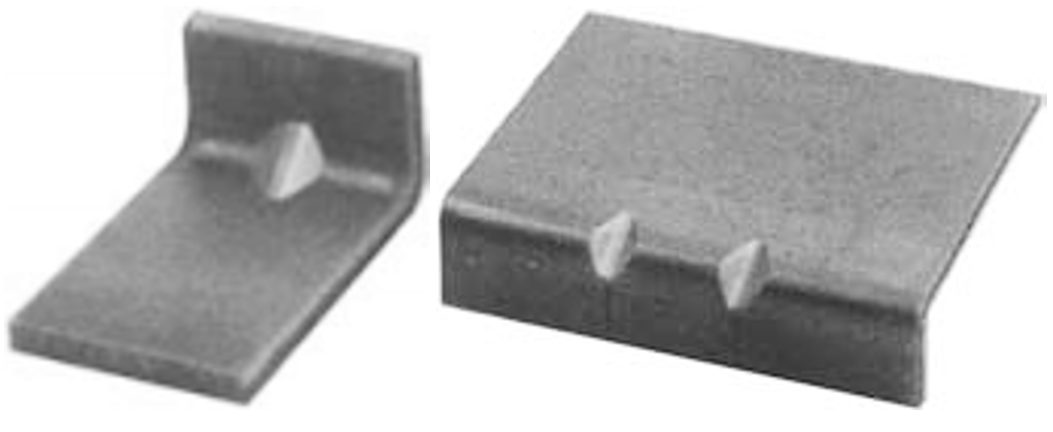
Figure 8: Stiffening darts can be created as part of the rotary bending operation.R-7
Back to the Top
Cutting, Cutting-Blanking-Shearing-Trimming
A cut edge has four distinct zones with different characteristics:
- Rollover – The plastically deformed zone bent as the cutting tools contact the edge of the sheet surface.
- Burnish – The zone where the cutting tools penetrate into the sheet metal, prior to any fracturing. The sheet metal stresses are such that the surface compresses into the cutting tool, which gives it a flat, smooth, and shiny appearance. The shear zone is another name for this region.
- Fracture – The zone where the cutting steels fracture the sheet metal, leading to separation from the remainder of the sheet. The surface of this region is rougher than the burnish zone, and is at an angle from the cutting direction.
- Burr – The metal elongated and pushed out on the trailing edge of the cut.
The cutting process also deforms the metal near the shear face, creating what is known as the shear affected zone (SAZ). The degree and influence of this deformation is a function of the cutting process (shearing, water jet, laser, and so on) as well as the steel microstructure and strength. Many studies conclude plastic deformation within the SAZ is a key contributor to sheared edge stretching failures.
The Shear Affected Zone is the area of work-hardened steel and microstructural damage behind the sheared edge. The deformation pattern in the SAZ includes a large shear-induced rotation of the grains that increases with proximity to the sheared edge. An etched cross-section such as that shown in Figure 1 highlights the grain rotation and gives a visual indication of the size of the zone.

Figure 1: Shear Face Components and Shear Affected Zone.K-1
Work hardening in the SAZ leads to a way to quantify the depth of the SAZ: by creating a hardness profile with readings starting at the edge and progressing deeper into the metal. The end of the SAZ occurs when the hardness readings level off to the bulk hardness.
Figure 2 compares the edge and hardness readings for CP800 and DP780, showing the depth of the SAZ for DP780 is about 41% of the initial sheet thickness of 1.56 mm, and the depth of the CP800 SAZ is 20% of the initial 2.90 mm sheet thickness.P-12

Figure 2: A) Sheared edge and SAZ of CP800; B) Sheared edge and SAZ of DP780; C) CP800 microstructure away from edge; D) DP780 microstructure away from sheared edge; E) hardness profile for the two sheared edges in the rolling direction.P-12
Plastic deformation from cutting and subsequent edge expansion forms micro-voids and creates other microstructural damage. The voids grow and combine with neighboring voids to create micro-cracks, which in turn combine with other micro-cracks resulting in the cracks that cause fractures in stampings.
Void nucleation in DP steels occurs through two mechanisms: decohesion of the ferrite-martensite interface or fracture of martensite islands.P-12, A-27, A-28 Figure 3 shows an example of both.

Figure 3: Aligned voids along loading direction. White solid square shows interface damage between martensite and ferrite. White dashed circles show voids formed by cracking of martensite.A-28
The study in Citation P-12 compared CP800 and DP780. The CP800 microstructure contains ferrite, bainite, and martensite. The DP780 microstructure has more martensite, with a larger strength differential between the phases, which combines to result in a lower nucleation strain and accelerated void nucleation compared with CP800. The DP grade has a larger SAZ, further promoting nucleation, growth, and coalescence of voids. This results in failure at a lower strain and leads to the lower edge stretchability of the DP780 compared to the CP800 alloy.P-12 The ductility of bainite restrains void initiation at high strains, which may play a role in improved sheared edge performance.S-24, S-25
Fracture initiation energy, a measure of fracture toughness correlates with hole expansion and stretch-flangeability as shown in Figure 4.Y-5

Figure 4: Correlation between fracture initiation energy and hole expansion ratio of various metals. Steels A – D are AHSS grades with Tensile strength ranging from 725 – 1000 MPa.Y-5
In addition to microstructural damage and fracture mechanics, simulation models improve in accuracy when the incorporating the effect of the temperature increase in the localized deformation zone. Simulation of the blanking of AISI 1050 shows a temperature at the cut edge of 440 °C. The edge temperature may be even higher in AHSS grades due to their higher strength.A-29

Figure 5: 1.27mm AISI 1050 steel blanked with 15% clearance. The simulation shows temperature, with the cut face getting as hot as 440 °C.A-29
When factoring in the considerations described here, simulation accuracy of hole expansion and sheared edge stretching improves significantly. Citations L-13 and L-14 provide additional background information about the Shear Affected Zone.