Friction Stir Welding
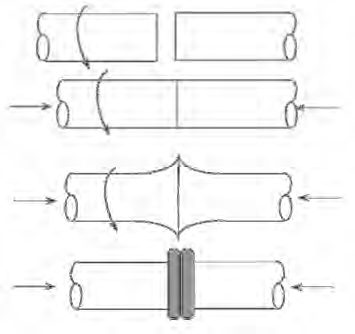
Figure 1: Basic steps of both inertia and CD friction welding.
The Friction Stir Welding family of processes relies on significant plastic deformation or forging action to overcome the barriers to solid-state welding. Frictional heating dominates at the beginning of the process, followed by the heating due to plastic deformation once the forging action begins. The friction welding processes which use rotation of one part against another are inertia and continuous (or direct)-drive friction welding. These are the most common of the friction welding processes and are ideal for round bars or tubes. In both inertia and Continuous-Drive (CD) friction welding, one part is rotated at high speeds relative to the other part (Figure 1). They are then brought together under force creating frictional heating which softens (reduces the YS) the material at and near the joint to facilitate the forging action, which, in turn, produces further heating. Following a sufficient amount of time to properly heat the parts, a high upset force is applied which squeeze the softened hot metal out into the “flash”. Any contaminants are squeezed out as well as the weld is formed. The flash is usually removed immediately after welding while it is still hot.A-11, P-6
Friction Stir Welding
Friction Stir Welding (FSW) is a revolutionary new friction welding process that was developed in the early 1990s by the British Welding Institute (TWI). Whereas processes such as inertia and Continuous-Drive (CD) friction welding are primarily limited to round parts, FSW (Figure 2) produces solid-state friction welds using conventional joint design such as butt joints. FSW relies on the frictional heat created when a special non-consumable pin tool is rotated along the joint against the top of the two pieces being welded. As the process begins, frictional heating softens (or plasticizes) metal at the joint, facilitating a stirring action of plasticized metal. Further heating that is generated by the plastic deformation becomes the main source of heating as the weld progresses. The two videos following provide more insight on the process.
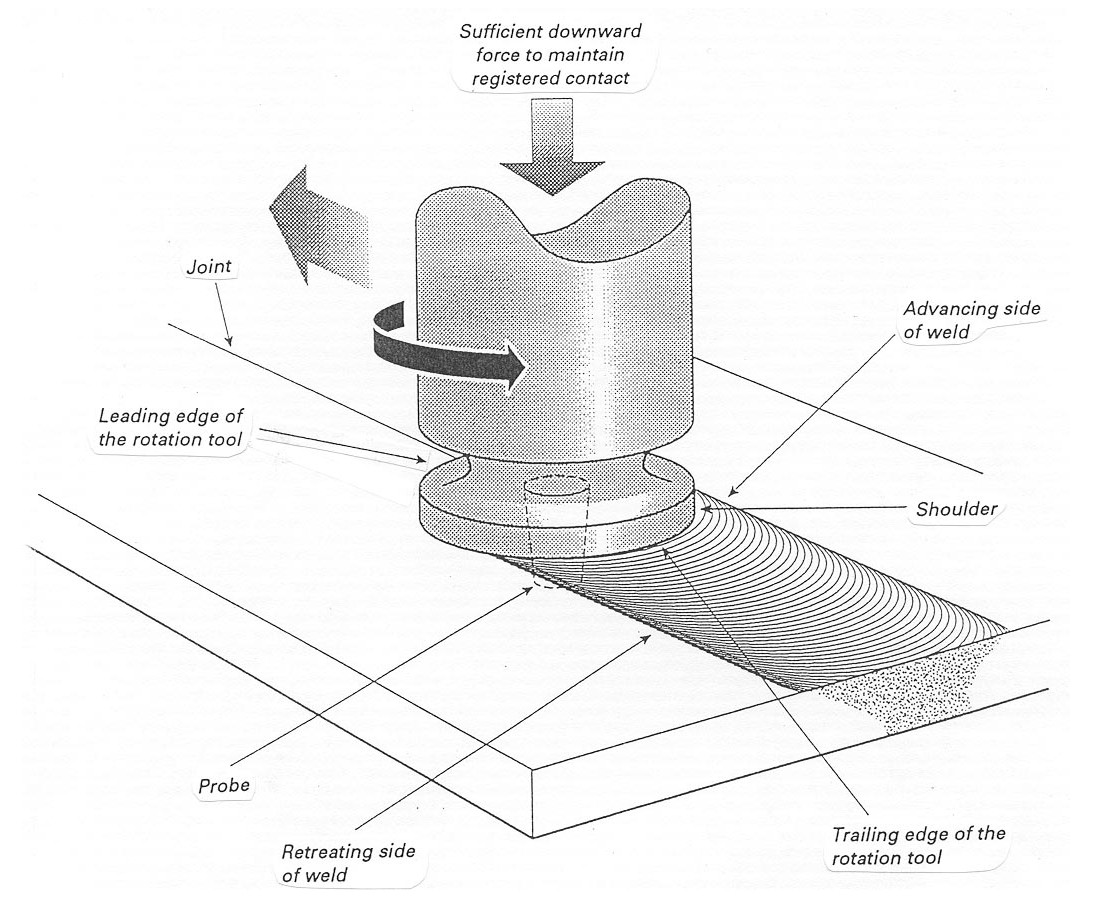
Figure 2: Friction Stir Welding
The pin tool for FSW consists of a shoulder and pin. The shoulder rests on the surface of the plates and provides most of the frictional heating. The pin partially penetrates the joint of the plates being welded. Within the stir zone itself, the plasticized hot metal flows around the pin and coalesces to form a weld. The primary purpose of the pin is to control the stirring action. A wide variety of pin tool designs and materials have been studied, including the use of Tungsten (W)-based materials, threaded pins, and cupped shoulders. As indicated on Figure 3, a slight push angle (<5 degrees) relative to the travel direction is typically used. Weld travel speeds are much slower than typical arc welding speeds. The process has limited industrial applications since it is still under development, especially in tool development.A-11, P-6
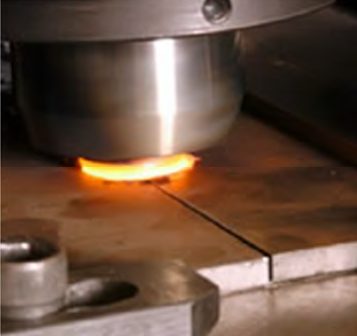
Figure 3: FSW typically uses a slight push angle
The FSW of hard metals (steel, Ti, Ni) has been made possible due to advancements in both tool design and tool materials. Tool material choices for AHSS applications include ceramic-based Polycrystalline Cubic Boron Nitride (PCBN) and refractory based Tungsten-Rhenium alloy (W-Re). PCBN is chosen because it is extremely wear resistant and has good thermal management. W-based material is chosen because it is very tough at room and welding temperatures and it is capable of being used for thick sections of steels.
Mechanical properties for FSW of AHSS cross-weld tensile specimens showed fully consolidated weld joints without discontinuities, but showed a drop-in weld ductility of about 10%, as seen in Figure 4.
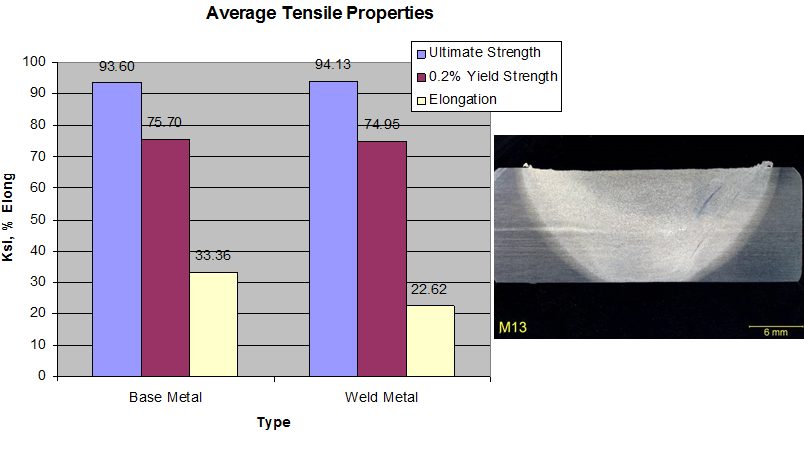
Figure 4: Mechanical properties of FSW for AHSS.
Friction Stir Spot Welding
A variation of the FSW process is Friction Stir Spot Welding. This process was specifically developed for some automotive applications, including joining of AAl), Al-to-steel, and AHSS. The process steps are similar to FSW without the linear movement, thus creating a “spot”-type joint (Figure 5).O-1
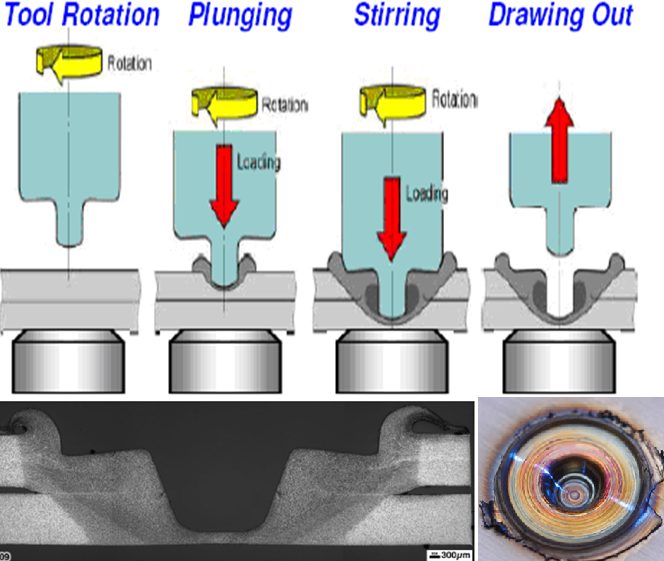
Figure 5: Process steps for friction stir spot welding (top) with the resultant weld profile (bottom).O-2
In summary, the advantages and limitations of friction welding processes are listed below.
- Advantages:
- No melting means no chance for solidification-related defects
- Filler materials are not needed
- Very few process variables result in a very repeatable process
- In the case of CD friction welding, can be deployed in a production environment
- Fine grain structure of friction welds typically exhibits excellent mechanical properties relative to the BM, especially when welding Al
- No special joint preparation or welding skill required
- Limitations:
- Equipment is very expensive
- Limited joint designs, and in the case of CD and inertia welding, parts must be symmetric
- FSW is very slow, and not conducive to high-speed
Solid State Welding
Introduction
Solid-State welding refers to a family of processes that produce welds without the requirement for molten metal. Solid-state welding theory emphasizes that the driving force for two pieces of metal to spontaneously weld (or form a metallic bond) to each other exists if the barriers (oxides, contaminants, and surface roughness) to welding can be eliminated. All solid-state welding processes are based on this concept, and use some combination of heat, pressure, and time to overcome the barriers. Approaches include friction, diffusion, explosion, and ultrasonic welding.
Since there is no melting, there is no chance of forming defects such as porosity or slag inclusions which are only associated with fusion welding processes. Solid-state welding processes also require no filler materials, and in some cases, can be quite effective at welding dissimilar metals that cannot be welded with conventional processes due to metallurgical incompatibilities. The equipment is typically very expensive, and some processes involve significant preparation time of the parts to be welded. Most of these processes are limited to certain joint designs, and some of them are not conducive to a production environment. Non Destructive Testing processes do not always work well with solid-state welding processes because of the difficulties of distinguishing a true metallurgical bond with these techniques.
In this section you’ll find examples of three types of solid state welding processes: Friction, High-Frequency for tubes and pipe and Magnetic Pulse. Generally these are characterized as follows. Click to the specific menu for details.
Friction Welding Processes
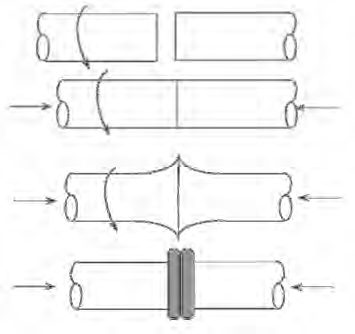
Figure 1: Basic steps of both inertia and CD friction welding.
This family of processes relies on significant plastic deformation or forging action to overcome the barriers to solid-state welding. Frictional heating dominates at the beginning of the process, followed by the heating due to plastic deformation once the forging action begins. The friction welding processes which use rotation of one part against another are inertia and continuous (or direct)-drive friction welding. These are the most common of the friction welding processes and are ideal for round bars or tubes. In both inertia and Continuous-Drive (CD) friction welding, one part is rotated at high speeds relative to the other part (Figure 1). They are then brought together under force creating frictional heating which softens (reduces the YS) the material at and near the joint to facilitate the forging action, which, in turn, produces further heating. Following a sufficient amount of time to properly heat the parts, a high upset force is applied which squeeze the softened hot metal out into the “flash”. Any contaminants are squeezed out as well as the weld is formed. The flash is usually removed immediately after welding while it is still hot.A-11, P-6
High Frequency Tube/Pipe Welding
HF welding processes rely on the properties of HF electricity and thermal conduction, which determine the distribution of heat in the workpieces. HF contact welding and high-frequency induction welding are used to weld products made from coil, flat, or tubular stock with a constant joint symmetry throughout the length of the weld.
Magnetic Pulse Welding (MPW)
MPW is a solid-state process that uses electromagnetic pressure to accelerate one workpiece to produce an impact against another workpiece. The metallic bond created by this process is similar to the bond created by explosion welding. MPW, also known as electromagnetic pulse or magnetic impact welding, is highly regarded for the capability of joining dissimilar materials.
Resistance Spot Welding, Resistance Welding Processes
The Resistance Spot Welding (RSW) process is often used as a model to explain the fundamental concepts behind most resistance welding processes. Figure 1 shows a standard Resistance Spot Welding arrangement in which two copper electrodes apply force and pass current through the sheets being welded. If the sheets are steel, the resistance to the flow of current of the sheets will be much higher than the copper electrodes, so the steel will get hot while the electrodes remain relatively cool. But another important characteristic exists that is critical to most resistance welding processes – the contact resistance between the parts (or sheets) being welded. As indicated on the figure, the highest resistance to the flow of current is where the sheets meet (“Resistance” 4). This fact allows a weld nugget to begin forming and grow exactly where it is needed – between the sheets.
The figure depicts the flow of current from one electrode to the other as an electrical circuit that contains seven “resistors”. Resistors 1 and 7 represent the bulk resistance of the copper electrodes, Resistors 2 and 6 represent the contact resistance between the electrodes and the sheets, Resistors 3 and 5 represent the bulk resistance of the sheets, and Resistor 4, as mentioned, represents the contact resistance between the sheets. Another fact that works strongly in the favor of resistance welding of steel is that as the steel is heated, its resistivity relative to copper increases even more. So, the initial contact resistance effectively heats the surrounding area which is in turn heated more rapidly because its resistance is higher since it is hotter. As a result, heating and weld nugget formation can occur quite rapidly. A typical weld time for RSW of steel is approximately 1/5 of a second. The current required in resistance welding is much higher than arc welding, and it is in the range of 8-15 kA.
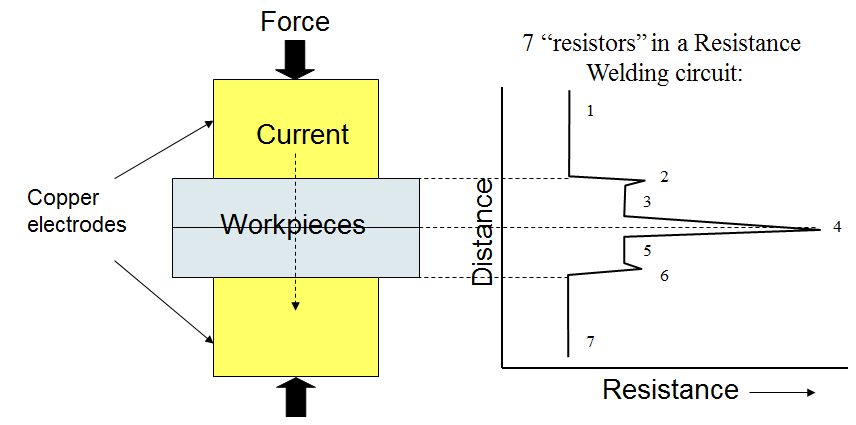
Figure 1: Resistances associated with steel Resistance Spot Welding.
Most welding processes produce welds that provide strong visible evidence of weld quality, so visual examination is often an important approach to verifying the quality of the weld. However, with most resistance welding processes visible examination is not possible due to the “blind” weld location between the sheets or parts being welded. As a result, maintaining weld quality with processes such as Resistance Spot Welding is highly dependent on what is known as a lobe curve (Figure 2), which is basically a process window for Resistance Spot Welding. The lobe curve represents ranges of weld current and time that will produce a spot weld nugget size that has acceptable mechanical properties for the intended application. So, weld quality monitoring with resistance welding processes relies highly on the ability to monitor parameters such as current and time. During production, if a weld is made with parameters that fall outside of the lobe curve, the weld is considered unacceptable. Ultrasonic testing is also often used in the automotive industry for Nondestructive Testing (NDT) of the blind location of Resistance Spot Welding.
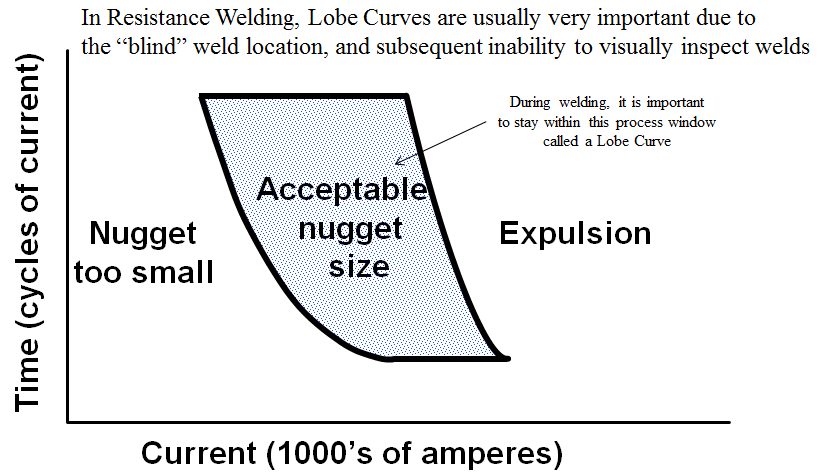
Figure 2: Resistance welding lobe curve.
RSW Electrode Geometry
Electrode geometry is a very important consideration with RSW. Figure 3 shows three common shapes, but there are many more options available including unique custom designs for specific applications. The basic electrode geometry is usually selected to improve the electrical-thermal-mechanical performance of an electrode. This is generally a geometry in which the cross-sectional area increases rapidly with distance from the workpiece, thereby providing a good heat sink. The choice of shape may also include considerations such as accessibility to the part and how much surface marking of the part is acceptable. The diameter of the electrode contact area is also a consideration. Too small an area will produce undersized welds with insufficient strength, while too large an area will lead to unstable and inconsistent weld growth characteristics.
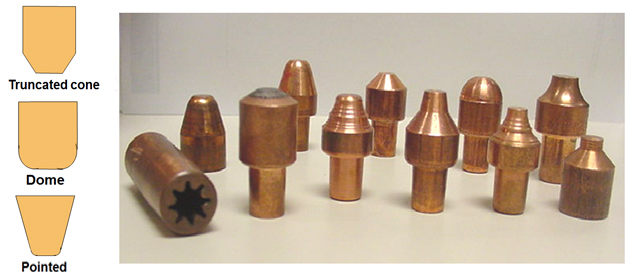
Figure 3: Typical RSW electrode geometries (left), example geometries used by automotive manufacturers (right).
Electrodes must be able to conduct current to the part, mechanically constrain the part, and conduct heat from the part. They must be able to sustain high loads at elevated temperatures, while maintaining adequate thermal and electrical conductivity. The choice of electrode alloy for a given application is often dictated by the need to minimize electrode wear. When electrodes wear, they typically begin to “mushroom”, or grow larger in diameter. Electrode wear is accelerated when there is an alloying reaction between the electrode and the part, a common problem when welding Aluminum (Al) and coated steels. As the electrode diameter increases, the current density decreases, resulting in a decrease in the size of the weld. Since the strength of a spot-welded joint is directly related to the size of the weld nugget, electrode wear can be a big problem.
A range of Copper (Cu)-based or refractory-based electrode materials are used depending on the application. The Resistance Welding Manufacturers Association (RWMA) sorts electrode materials into three groups: A, B, and C. Group A contains the most common Cu-based alloys (see Table 1), Group B contains refractory metals and refractory metal composites, and Group C contains specialty materials such as dispersion-strengthened copper. Within the groups, they are further categorized by a class number. The general rule of thumb is as the class number goes up, the electrode strength goes up but the electrical conductivity goes down. When electrical conductivity goes down, the electrode heats more easily, resulting in premature electrode wear. The choice of electrode material involves many factors, but generally higher strength electrodes will be selected when higher strength materials are being welded. It is also important that the electrical and thermal conductivities of the electrode are much higher than those of the material being welded.
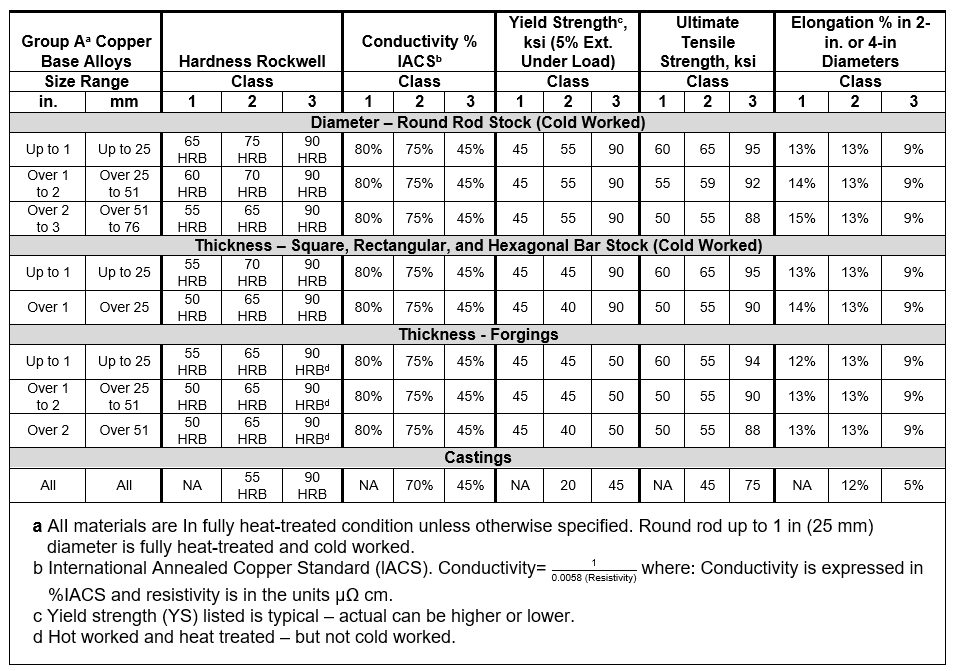
Table 1: Minimum mechanical and physical properties of Cu-based alloys for RWMA electrodes.A-18
The two most commonly used electrodes are the Class 1 and 2 electrodes of Group A. Class 1 electrodes [99% copper, 1% cadmium; 60 ksi UTS (forged); conductivity 92% International Annealed Copper Standard (IACS)] offer the highest electrical and thermal conductivity, and are typically used for spot welding Al alloys, magnesium alloys, brass, and bronze. Class 2 [99.2% copper, 0.8% chromium; 62 ksi UTS (forged), 82% IACS] electrodes are general-purpose electrodes for production spot and seam welding of most materials. IACS refers to a copper standard to which the electrodes are compared. Pure Cu has an IACS number of 100%.A-11, P-6, O-1