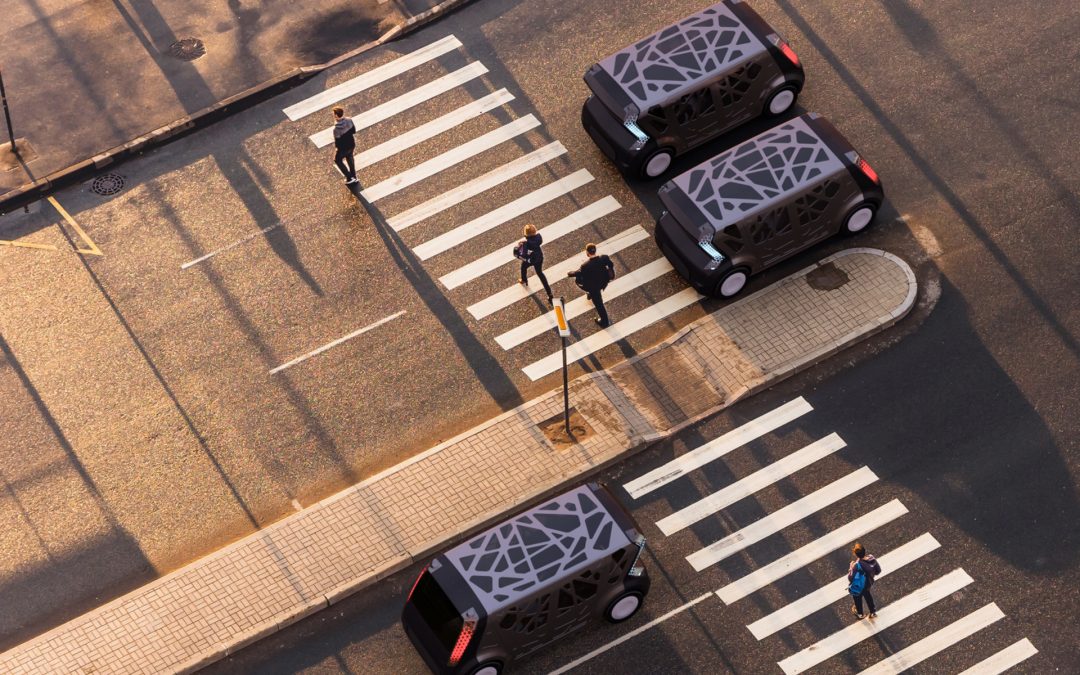
Designing For Vehicle Crash Requirements that Don’t Yet Exist

Steel E-Motive’s AHSS A- and C-Pillar placement provide good occupant protection in side pole crash scenarios. The A- and C-Pillar combined with AHSS door ring and door reinforcements compensate for the removed B-Pillar.
Since June 2020, we’ve been working with our engineering partners, Ricardo, on Steel E-Motive, a vehicle engineering program which is developing virtual concepts for two fully autonomous and connected electric vehicles designed for mobility as a service (MaaS) applications. We are using Advanced High-Strength Steel (AHSS) technologies and products to design autonomous vehicle concepts to enable MaaS solutions which are safe, affordable, accessible and environmentally conscious.
Steel E-Motive engineering and validation will be completed in 2022, at which time we will prepare communication and delivery of the final results. But right now, we are in the midst of crash simulation and material optimization to solve the new challenges posed by these vehicles.
Steel E-Motive is designed to operate in a mixed traffic mode operation (both driver-operated and autonomous vehicles); hence the vehicle should meet the current and future global high-speed crash test standards. The compact vehicle dimensions and proportions result in relatively short front and rear overhangs. To enhance user experience and take advantage of full autonomy, the front occupants are positioned in a rear facing configuration presenting a more significant challenge for crashworthiness in frontal impact. This requires a revised front crash strategy and load management approach for Steel E-Motive.
Neil McGregor, Steel E-Motive’s Chief Engineer, has written a blog about it, and you can find it posted on our Steel E-Motive website (web spiders prohibit us from duplicating the article here). Take a moment to read it there, but feel free to ask questions or comment about it here!