Blog, main-blog
A New Software Application for Thin Wall Section Analysis
Advanced High-Strength Steel (AHSS) grades offer increased performance in yield and tensile strength. However, to fully utilize this increased strength, automotive beam sections must be designed carefully to avoid buckling of the plate elements in the section. A new software application, Geometric Analysis of Sections—GAS2.0, available through the American Iron and Steel Institute, is a tool to aid in this design effort.
Plate Buckling in Automotive Sections
To understand how plate buckling affects the strength of a thin walled beam consider Figure 1. A square beam is made of four identical plates connected at their edges. Under an axial compressive load each plate may buckle. Considering just one of the plates, the stress that will cause buckling depends on the ratio of plate width and thickness (b/t). Thinner wider plates with large b/t ratio will buckle at a lower stress than thicker narrower plates.
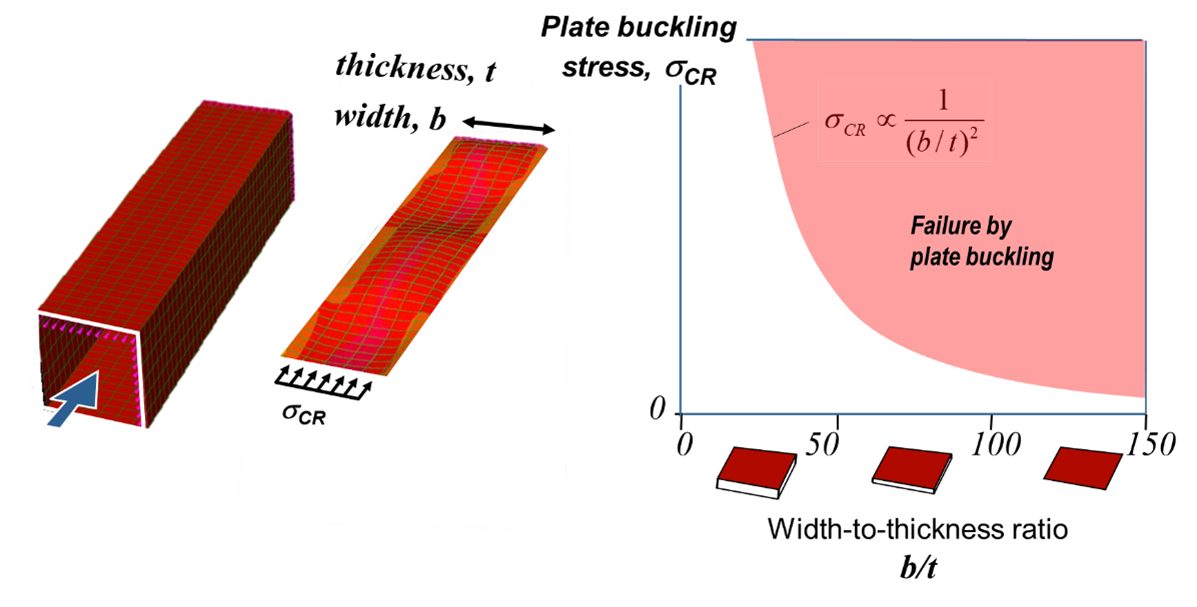
Figure 1: Plate Buckling Behavior.
Now consider a plate of mild steel (200 MPa yield stress) which has been designed to buckle just as yield stress is reached, Point A in Figure 2. The plate would have a b/t ratio of approximately 60. This design is taking full advantage of the yield strength of the material.
Now consider the same plate but substituting an AHSS grade (600 MPa yield stress) as shown in Figure 2. The plate will buckle at the same 200 MPa before reaching the material’s potential, Point B in the figure. To take advantage of this materials yield strength, the proportions of the plate will need to be changed, Point C. This illustration demonstrates the need to consider plate buckling particularly in the application of AHSS grades.
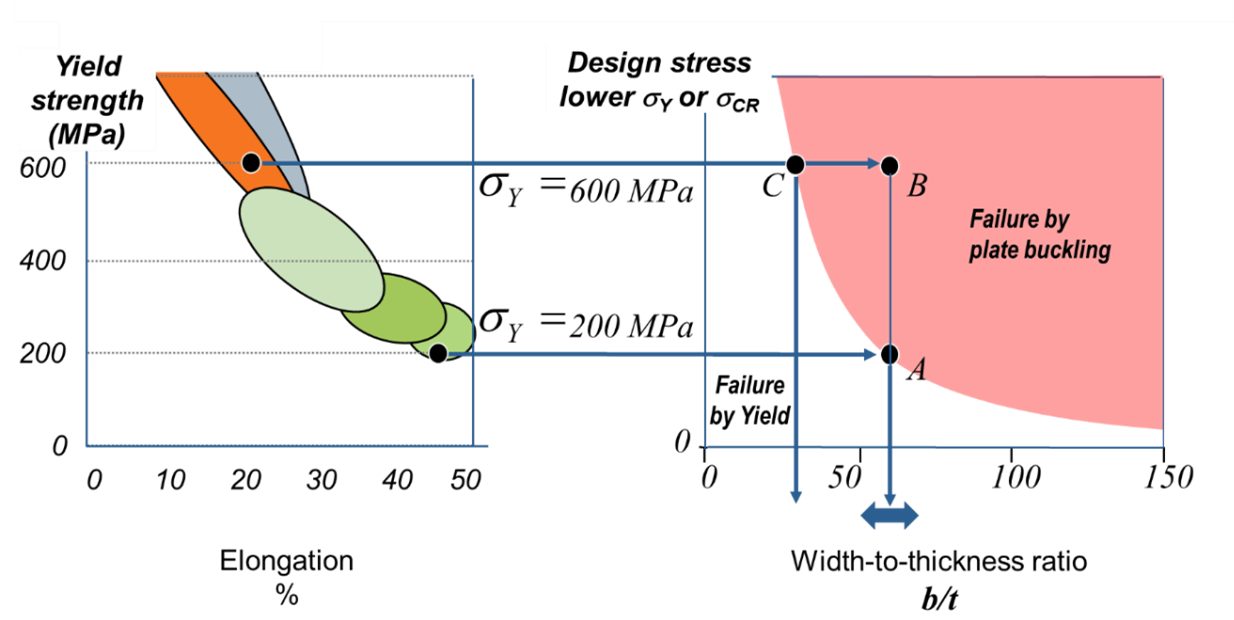
Figure 2: AHSS Substitution in a Plate.
Moving from a single plate to the more complex case of a beam section of several plates, consider Figure 3. On the left is the beam made of four plates with a compressive load causing the plates to just begin to buckle. However, this condition does not represent the maximum load carrying ability of the beam. The load can be increased until the stress at the corners of the buckled plates are at the material yield stress, center in Figure 3. Note that in this condition the stress distribution across the plate is nonlinear with lower stress in the center of each plate. One means to model this complex state is by using an imaginary Effective Section. Here the center portion is visualized as being removed and the remainder of the section is stressed uniformly at yield. The amount of plate width to be removed is determined by theory.W-21, A-42, Y-9, M-18 The effective section is a convenient way to visualize the efficiency of a section design given the material grade and provides an estimate of the maximum load carrying ability of the beam.
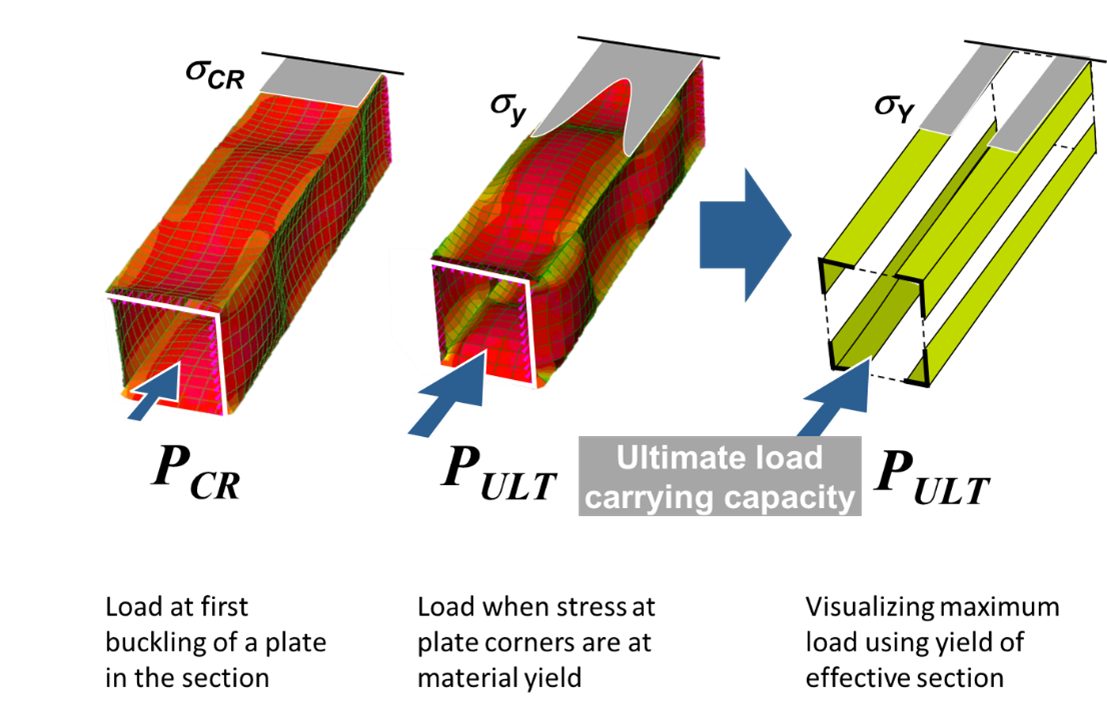
Figure 3: Concept of Effective Section.
Geometric Analysis of Sections – GAS2.0
Geometrical Analysis of Sections software determines the effective section for complex automotive sections. Figure 4 illustrates the GAS2.0 user interface. The user has the ability to construct sections or to import section data from a CAD system. Material properties for 63 steel grades are preloaded with the ability to also add user-defined steel grades. Two types of analysis are available. Nominal analysis, which provides classical area properties of the section, and Effective analysis which determines the effective section at material yield. Figure 5 summarizes both the tabular results and graphical results for each type of analysis.
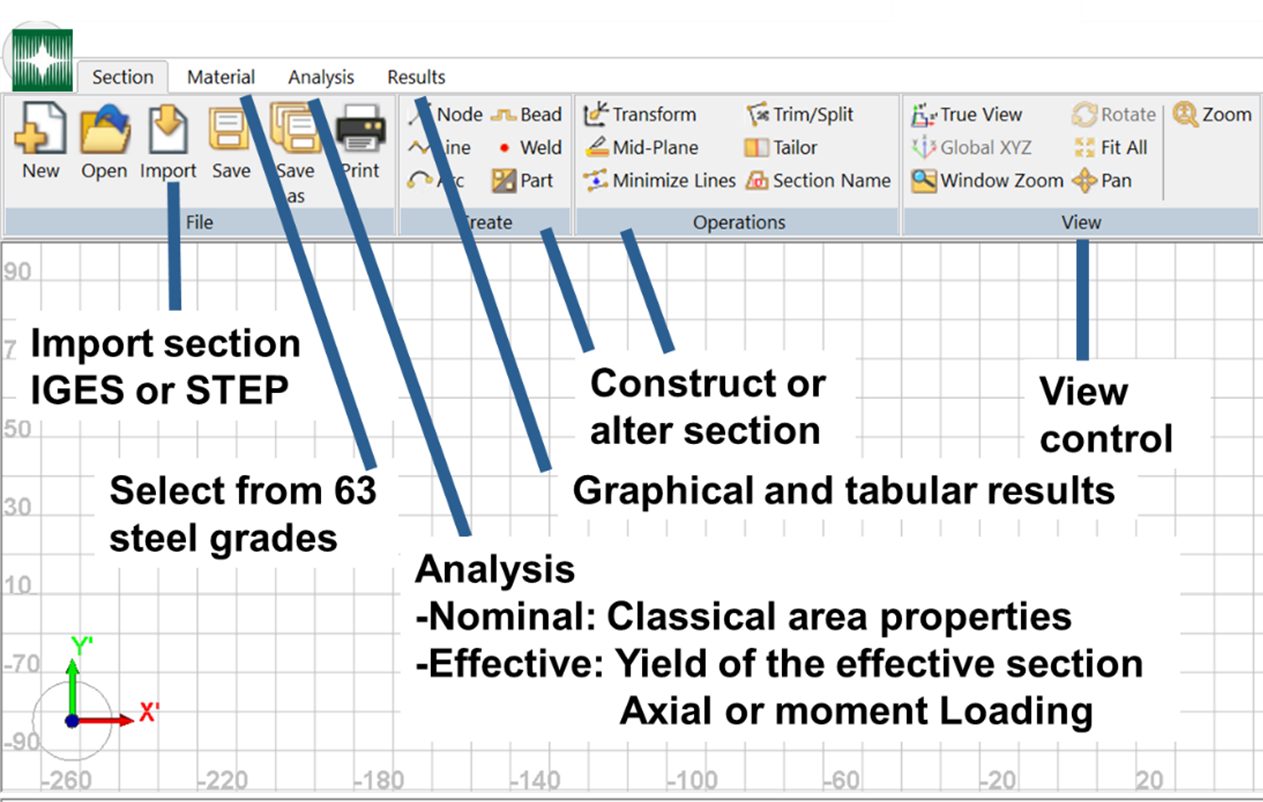
Figure 4: GAS2.0 User Interface.
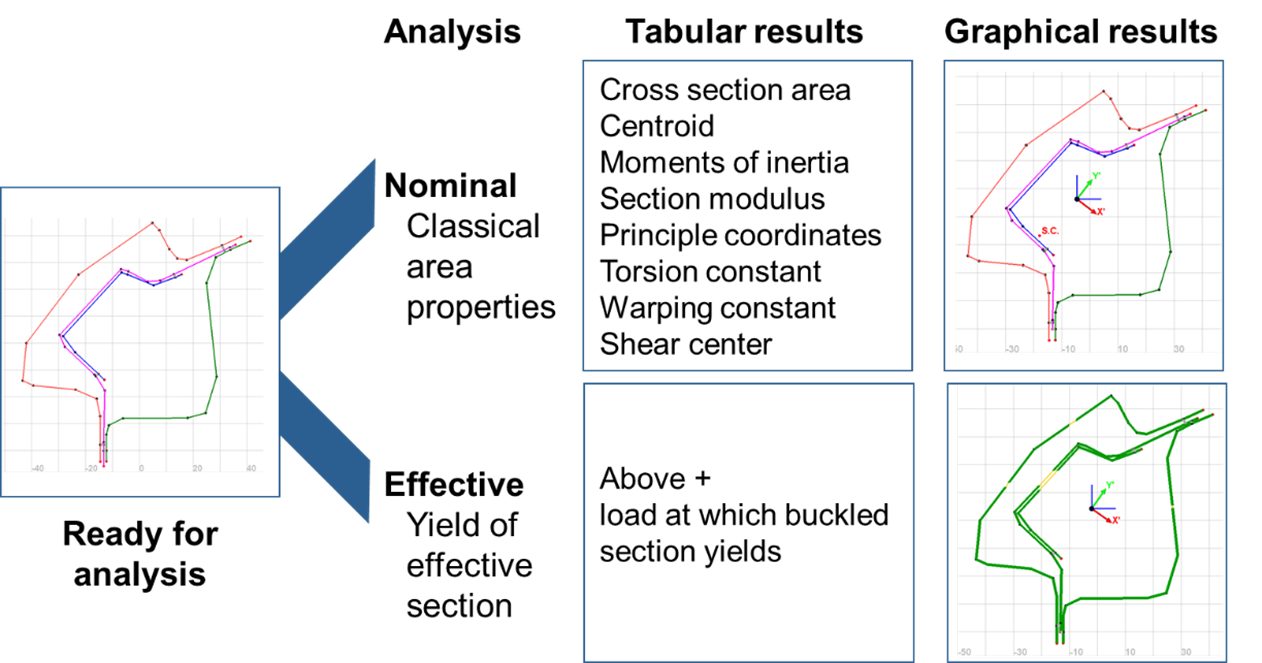
Figure 5. GAS2.0 Analysis Results.
Figure 6 illustrates an example of an Effective Analysis for a rocker section. In the graphical screen, the effective section is shown in green. Ideally, the whole section would be effective to fully use the materials yield capability. Also shown in the graphical screen are the section centroid, orientation of the principle coordinates, and stress distribution. In the right text box are tabular results. At the bottom of the tabular results is the axial load that causes this stress state and represents the ultimate load carrying ability of this section.
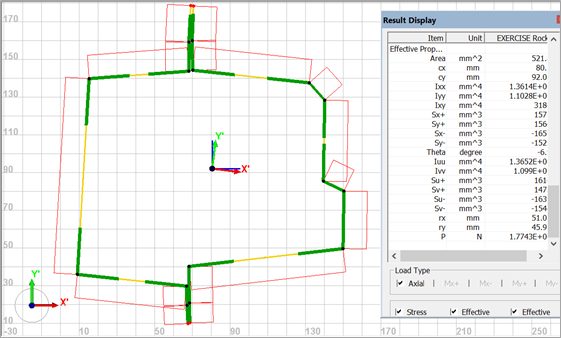
Figure 6: GAS2.0 Graphical Results.
It is clear that much of the material in the section of Figure 6 is not fully effective. GAS2.0 allows the user to conveniently modify the section. For example, in Figure 7 a bead has been added to the left side wall increasing its bulking resistance. Note that the side wall is now largely effective, and the ultimate load at the bottom of the text box has increased substantially.
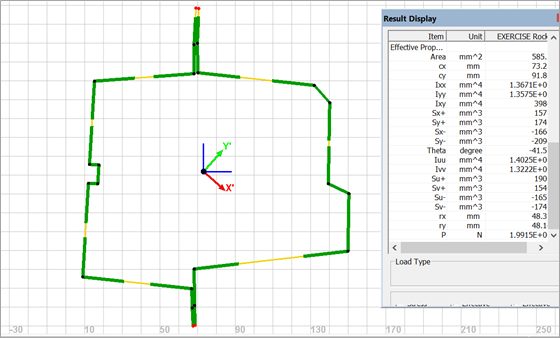
Figure 7: Improved Design Concept.
Role of GAS in the Design Process
GAS2.0 can play a significant role in early stage design, see Figure 8, by quickly creating initial designs which are more likely to function and to ensure that adequate package space is set aside for structure. This will result in fewer problems to fix later in the design sequence. During the detail design stage, GAS2.0 can supplement Finite Element Analysis by identifying problems earlier, and by screening design concepts for those with the greatest promise prior to more detailed analysis by FEA.

Figure 8: Role of GAS2.0 in Design Process.
GAS2.0 is available for free download at www.steel.org, Included in the resources at steel.org is an American Iron and Steel Institute introductory webinar conducted by Dr. Don Malen on 16 June 2020, as well as a number of GAS2.0 tutorials and training modules.
homepage-featured-top, main-blog
In this edition of AHSS Insights, George Coates and Menachem Kimchi get back to basics with important fundamentals in forming and joining AHSS.
As the global steel industry continues its development of Advanced High-Strength Steels (AHSS), including 3rd Gen products with enhanced formability, we’re reminded that successful application is still dependent on the fundamentals, both in forming and joining. In this blog article, we address some of those forming considerations, as well as highlighting common joining issues in manufacturing.
Forming Considerations
The somewhat lower formability of AHSS compared to mild steels can almost always be compensated for by modifying the design of the component and optimizing blank shape and the forming process.
In stamping plants, we’ve observed inconsistent practices in die set-up and maintenance, surface treatments and lubrication application. Some of these inconsistencies can be addressed through education, via training programs on AHSS Application Guidelines. These Guidelines share best practices and lessons learned to inform new users on different behaviors of specific AHSS products, and the necessary modifications to assist their application success. In addition to new practices, we’ve learned that applying process control fundamentals become more critical as one transitions from mild steels to AHSS, because the forming windows are smaller and less forgiving, meaning these processes don’t tolerate variation well. If your present die shop is reflective of housekeeping issues, such as oil and die scrap on the floor or die beds, you are a candidate for a shop floor renovation or you will struggle forming AHSS products.
Each stamping operation combines three main elements to achieve a part meeting its desired functional requirements:
There is good news, in that our industry is responding with new products and services to improve manufacturing performance and save costs.
As an example, lubrication application is often overlooked, and old systems may be ineffective. In the forming of AHSS, part temperatures can become excessive, and break down lubricant performance. Figure 1 shows an example of part temperatures from an Ohio State University study conducted with DP 980 steels.O-1

Figure 1: Example Temperature distribution for DP 980 Steel.O-1
Stampers often respond by “flooding” the process with extra lubricant, thinking this will solve their problem. Instead, lubricant viscosity and high temperature stability are the most important considerations in the lubricant selection, and new types exist to meet these challenges. Also, today there are new lubrication controllers that can finely control and disperse wet lubricants evenly across the steel strip, or in very specific locations, if forming requirements are localized. These enable better performance while minimizing lubricant waste (saving cost), a win-win for the pressroom.
Similarly, AHSS places higher demands on tool steels used in forming and cutting operations. In forming applications, galling, adhesive wear and plastic deformation are the most common failure mechanisms. Surface treatments such as PVD, CVD and TD coatings applied to the forming tool are effective at preventing galling. Selection of the tool steel and coating process used for forming AHSS will largely depend on the:
- Strength and thickness of the AHSS product,
- Steel coating,
- Complexity of the forming process, and
- Number of parts to be produced.
New die materials such as “enhanced D2” are available from many suppliers. These improve the balance between toughness, hardness and wear resistance for longer life. These materials can be thru-hardened, and thus become an excellent base material for PVD or secondary surface treatments necessary in the AHSS processing. And new tool steels have been developed specifically for hot forming applications.
Joining Considerations
In high-volume production different Resistance Spot Welding (RSW) process parameters can be used depending on the application and the specifications applied. Assuming you chose the appropriate welding parameters that allows for a large process window, manufacturing variables may ruin your operation as they strongly effect the RSW weld quality and performance.
Material fit-up
One of the great advantages of the RSW process is the action of clamping the material together via the electrode force applied during the process. However due to the pre-welding condition/processing such as the stamping operation, this fit-up issue, as shown in Figure 2, can be very significant especially in welding an AHSS product. In this case the effective required force specified during the process setup for the application is significantly reduced and can result in an unacceptable weld, over-heating, and severe metal expulsion. If the steels are coated, higher probability for Liquid Metal Embrittlement (LME) cracking is possible.

Figure 2: Examples of Pre-Welding Condition/Processing Fit-Up Issues.
For welding AHSS, higher forces are generally required as a large part of the force is being used to force the parts together in addition to the force required for welding. Also, welding parameters may be set for pre-heating with lower current pulses or current up-slope to soften the material for easier material forming and to close the gap.
Electrodes Misalignment
During machine set up, the RSW electrodes need to be carefully aligned as shown in Figure 3A. However, in many production applications, electrode misalignment is a common problem.
Electrode misalignment in the configurations shown in Figure 3B may be detrimental to weld quality of any RSW application. Of course, the electrode misalignment shown in this figure is exaggerated but the point is that it happens frequently on manufacturing welding lines.
In these cases, the intendent contact between the electrodes is not achieved and thus the current density and the force density (pressure) required for producing an acceptable weld cannot be achieved. With such conditions, overheating, expulsion, sub-size welds and extensive electrode wear will result. Again, if coated steels are involved, the probability for LME cracking is higher.
Note also that following specifications or recommendations for water cooling the electrode is always important for process stability and extending electrode life.

Figure 4: Sequence of Squeeze Time and Welding Current Initiation.
Squeeze Time
The squeeze time is the time required for the force to reach the level needed for the specific application. Welding current should be applied only after reaching this force, as indicated in Figure 4. All RSW controllers enable the easy control of squeeze time, just as with the weld time, for example. In many production operations, a squeeze time is used that is too low due to lack of understanding of its function. If squeeze time is too low, high variability in weld quality in addition to severe expulsion will be the result.
The squeeze time required for an application depends on the machine type and characteristics (not an actual welding parameter such as weld time or welding current for example).
Some of the more modern force gauges have the capability to produce the curve shown in the Figure so adequate squeeze time will be used. If you do not know what the required squeeze time for your machine/application is, it is recommended to use a longer time.
For more on these topics, browse the Forming and Joining menus of these Guidelines.
Blog, main-blog
Introduction
The introduction of Advanced High-Strength Steel (AHSS) to light vehicle body structure applications poses a significant challenge to organizations involved in vehicle repair. AHSS grades are typically produced by non-traditional thermal cycles and contain microstructural constituents whose mechanical properties can be altered by exposure to elevated temperatures. This temperature sensitivity can alter the mechanical behavior during repair welding or flame straightening, thus seriously affecting the structural performance of the AHSS components after the repair.
The American Iron and Steel Institute, with automotive partners – FCA US LLC, Ford Motor Company, General Motors Company – and I-CAR, have completed studies examining the mechanical behavior of various AHSS products after exposure to typical repair arc welding and flame straightening temperature cycles. Recommended practices for repairing components made of these materials were also developed. The studies evaluated many of the AHSS grades being applied and built into vehicle structures today.
AHSS Thermal Evaluation
Several steel grades were evaluated for their sensitivity to thermal exposure taking place during heating to soften the material for straightening, typically by flame. The test results, conclusions and recommendations contained herein are the consensus views of the team members.
A time-temperature test matrix was developed to represent the various thermal conditions encountered during repair welding and flame straightening as shown in Table 1. Individual steel performance result discussions are based on this test matrix and discussed by grade category and specific type.

Table 1: Time-Temperature Test Matrix.
Steel Performance
Conventional Steels
Interstitial free (IF) and high strength low alloy (HSLA) steels are conventional steel products which are essentially a single phase ferrite microstructure and obtain their strength by the addition of chemical elements. These steels have been used in body structures and closures for many years and are well-known to be repairable without substantial performance degradation by arc welding and flame straightening. For repair processes, this means conventional steels can be subjected to heat during repair with the finished repaired component having mechanical properties greater than the properties of the as-received steel. However, it is recommended heating is kept below 750 degrees Celsius to ensure no degradation in properties (Figure 1).

Figure 1: Ultimate tensile strength of Grade 4 IF and HSLA 340 steel after exposure to simulated repair thermal cycles.
Advanced High-Strength Steels
Dual Phase (DP) Steel
DP steels range in strength from 500 MPa to 1200 MPa and obtain their properties from the introduction of a martensitic phase into the ferrite microstructure. The ferrite phase provides formability, while the martensitic phase provides the improved strength. This category of steel grades obtains its microstructure, and thus its mechanical properties through a combination of alloying elements and thermomechanical processing. The processing involves some holding time at elevated temperatures and cooling at specific rates.
Two grades of DP steel were tested, DP 600 and DP 780. The number indicates the ultimate tensile strength (UTS) level of the material in MPa and is the common way to name these grades. UTS for both grades decreases with elevated temperature at a much faster rate than for conventional steels and is illustrated by DP 600 in Figure 2. At temperatures above 650 degrees Celsius the strength suddenly increases then upon additional heating decreases. This behavior is a result of changing the microstructure created during the original thermomechanical processing of the material. Once the microstructure is changed, it is very difficult to return it to its original state in a repair shop environment. Therefore, it is not recommended to subject DP steels to any kind of elevated temperature process for straightening or removing dents. The recommended repair procedure is to remove and replace the DP component. OEM repair guidelines and procedures should be referenced for approved cut and weld lines for replacement.
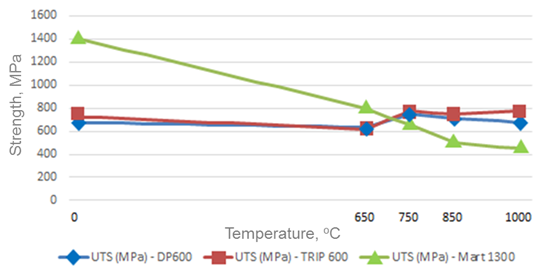
Figure 2: Ultimate tensile strength of advanced high-strength steels after exposure to simulated repair thermal cycles.
Transformation Induced Plasticity (TRIP) Steels
TRIP steels have a similar range of strength as DP steels, 500 MPa to 1200 MPa, while providing improved formability. The improved formability is obtained with the introduction of additional phases of austenite and bainite into the microstructure. These phases improve the work hardening properties of steel and provide additional energy absorption characteristics. TRIP steel microstructures are obtained in a similar manner as DP steels, and therefore have similar behaviors when heating.
TRIP 600 and 780 were evaluated in the studies and confirmed the expected results as demonstrated by TRIP 600 in Figure 2. Heating during repair of TRIP steel will also adversely affect their mechanical properties and thus the performance of the as repaired component may be compromised. OEM recommended repair procedures are similar to DP steels.
Martensitic Steel (MS)
MS steels typically have a microstructure of 100 percent martensite and have tensile properties greater than 980 MPa. Martensite is the strongest microstructural phase in steel and is obtained by alloying and rapid controlled cooling. This grade is used in areas where exceptional strength and anti-intrusion are needed, including such applications as the A-pillars, B-pillars, rockers and rails.
The effect of heat on MS 1300 is shown in Figure 2. Like other AHSS, it is adversely affected by heat and the performance of the as repaired component may be compromised. Thus, heat should be used only as outlined in OEM repair procedures.
Summary
The steel industry, working closely with automotive OEMs and the repair community, have developed and validated repair procedures applicable to the new AHSS used in today’s vehicles. Each OEM has taken the results from the AHSS repairability studies and developed their own repair guidelines.
The steel industry continues to develop AHSS grades with strength levels at and above 1000 MPa. These microstructures contain martensite and will be affected by heat exposure during repair as shown in previous studies. Collaborative studies will continue to update repair procedures for higher strength AHSS, including DP, MS and Press Hardened grades, and new 3rd Gen. AHSS as they are introduced.