Conventional HSS, Steel Grades
Carbon-Manganese High Strength Steel
Carbon and manganese are the two most cost-effective alloying additions to increase strength. While effective at strengthening, these additions reduce ductility and toughness, and make welding more challenging.
The practical usage of these grades typically limits the highest strength to no more than 280 MPa. Adding enough carbon and manganese to achieve higher strength results in a product without sufficient ductility for challenging applications, low toughness, and welding difficulty. These products sometimes are referred to as structural steels, and achieve their strength from the mechanism of solid solution strengthening.
Until the commercialization of High Strength Low Alloy steels, the CMn approach was the only option for users to obtain a high strength sheet metal.
Some of the specifications describing uncoated cold rolled Carbon-Manganese (CMn) or structural steels are included below, with the grades typically listed in order of increasing minimum yield strength and ductility. Different specifications may exist which describe hot or cold rolled, uncoated or coated, or steels of different strengths. Many automakers have proprietary specifications which encompass their requirements. Note that ASTM terminology is based on minimum yield strength, while JIS and JFS standards are based on minimum tensile strength. Also note that JIS G3135 does not explicitly state that these grades must be supplied with a C-Mn chemistry. An HSLA approach is satisfactory as long as the mechanical property criteria are satisfied.
- ASTM A1008M, with the terms Grade 25 [170], Grade 30 [205], Grade 33 [230] Type 1, Grade 33 [230] Type 2, Grade 40 [275] Type 1, Grade 40 [275] Type 2, Grade 45 [310], Grade 50 [340], Grade 60 [410], Grade 70 [480], and Grade 80 [550] A-25
- JIS G3135 with the terms SPFC340, SPFC370, SPFC390, SPFC440, SPFC490, SPFC540, and SPFC590 J-3
- JFS A2001, with the terms JSC340W, JSC370W, JSC390W, and JSC440W J-23
Conventional HSS, Steel Grades
Carbon-Manganese Steels (CMn) are a lower cost approach to reach up to approximately 280MPa yield strength, but are limited in ductility, toughness and welding.
Increasing carbon and manganese, along with alloying with other elements like chromium and silicon, will increase strength, but have the same challenges as CMn steels with higher cost. An example is AISI/SAE 4130, a chromium-molybdenum (chromoly) medium carbon alloy steel. A wide range of properties are available, depending on the heat treatment of formed components. Welding conditions must be carefully controlled.
The 1980s saw the commercialization of high-strength low-alloy (HSLA) steels. In contrast with alloy steels, HSLA steels achieved higher strength with a much lower alloy content. Lower carbon content and lower alloying content leads to increased ductility, toughness, and weldability compared with grades achieving their strength from only solid solution strengthening like CMn steels or from alloying like AISI/SAE 4130. Lower alloying and elimination of post-forming heat treatment makes HSLA steels an economical approach for many applications.
This steelmaking approach allows for the production of sheet steels with yield strength levels now approaching 800 MPa. HSLA steels increase strength primarily by micro-alloying elements contributing to fine carbide precipitation, substitutional and interstitial strengthening, and grain-size refinement. HSLA steels are found in many body-in-white and underbody structural applications where strength is needed for increased in-service loads.
These steels may be referred to as microalloyed steels, since the carbide precipitation and grain-size refinement is achieved with only 0.05% to 0.10% of titanium, vanadium, and niobium, added alone or in combination with each other.
HSLA steels have a microstructure that is mostly precipitation-strengthened ferrite, with the amount of other constituents like pearlite and bainite being a function of the targeted strength level. More information about microstructural components is available here.
Some of the specifications describing uncoated cold rolled high strength low alloy (HSLA) steel are included below, with the grades typically listed in order of increasing minimum yield strength and ductility. Different specifications may exist which describe hot or cold rolled, uncoated or coated, or steels of different strengths. Many automakers have proprietary specifications which encompass their requirements. Note that ASTM, EN and VDA terminology is based on minimum yield strength, while JIS and JFS standards are based on minimum tensile strength. Also note that JIS G3135 does not explicitly state that these grades must be supplied with an HSLA chemistry. A C-Mn approach is satisfactory as long as the mechanical property criteria are satisfied.
- ASTM A1008M, with the terms HSLAS 45[310], 50[340], 55[380], 60[410], 65[450], and 70[480] along with HSLAS-F 50 [340], 60 [410], Grade 70 [480] and 80 [550]A-25
- EN10268, with the terms HC260LA, HC300LA, HC340LA, HC380LA, HC420LA, HC460LA, and HC500LAD-5
- JIS G3135, with the terms SPFC340, SPFC370, SPFC390, SPFC440, SPFC490, SPFC540, and SPFC590J-3
- JFS A2001, with the terms JSC440R and JSC590RJ-23
- VDA239-100, with the terms CR210LA, CR240LA, CR270LA, CR300LA, CR340LA, CR380LA, CR420LA, and CR460LAV-3
Lower Strength Steels, Steel Grades
Metallurgy of Mild Steels
Mild steels are low carbon steels with no alloying elements added for substantial strengthening, and for that reason are characterized by relatively lower yield strength. Typically, mild steels have less than 0.10% carbon.
These steels have a microstructure that is primarily ferrite. The amount of pearlite in the microstructure is a function of the amount of carbon in the steel, with lower carbon resulting in a lower fraction of pearlite. More information about microstructural components is available here.
Ultra-low carbon steels are a type of mild steel. These grades are typically the lowest yield strength and highest ductility available. Generally, these steels have less than 0.005% carbon, or less than 50 ppm C. More information is contained on the page for Ultra-Low Carbon steels.
Different names may describe mild steels, but these differences came from steel mill production techniques that are no longer in use. Since all sheet steels in use today are continuously cast, there are no significant differences between these terms:
- Drawing Quality (DQ)
- Drawing Steel (DS)
- Aluminum Killed Drawing Quality (AKDQ)
- Drawing Quality Aluminum Killed (DQAK)
- Drawing Quality Special Killed (DQSK)
Mild steels are described in OEM, regional or global specifications with different syntax. While certain grade definitions between these specifications may be similar, the user is cautioned against using conversion charts without first confirming aspects which might be different, such as minimum, maximum, or typical values of chemical or mechanical properties. For example, ASTM specifications which cover lower strength steels list only typical values for tensile properties, but these are non-mandatory and the user may receive product outside the ranges shown. Additionally, JIS specifications which cover lower strength steels do not have minimum yield strength requirements, and the minimum elongation varies by thickness.
Some of the specifications describing uncoated cold rolled mild steel are included below, with the grades typically listed in order of increasing ductility. Different specifications may exist which describe hot or cold rolled, uncoated or coated, or steels of different strengths. Many automakers have proprietary specifications which encompass their requirements.
- ASTM A1008M, with the terms CS, DS, DDS, and EDDSA-25
- EN10130, with the terms DC01, DC03, DC04, DC05, and DC06D-3
- JIS G3141, with the terms SPCC, SPCD, SPCE, SPCF, and SPCGJ-2
- JFS A2001, with the terms JSC270C, JSC270D, JSC270E, JSC270F, and JSC260GJ-23
- VDA239-100, with the terms CR1, CR2, CR3, CR4, and CR5V-3
Conventional HSS, Steel Grades
ULC, IF, VD-IF, and EDDS are interchangeable terms that describe the most formable (high n-value) and lowest strength grade of steel. Adding phosphorus, manganese, and/or silicon to these grades increases the strength due to solid solution strengthening, precipitation of carbides and/or nitrides, and grain refinement.
For most alloys, steelmaking practices attempt to reduce phosphorus to very low levels, since increased phosphorus content is sometimes associated with an increased risk of embrittlement. However, in the ladle metallurgy station after steelmaking, small controlled amounts of phosphorus are added back to the melt when certain grades are produced, leading to the term “rephosphorized.” Phosphorus is a potent solid solution strengthening element, where only small additions result in large increases in yield and tensile strength.
When phosphorus or other solid solution strengthening elements are used to increase the strength of interstitial-free steels, IF-HS (Interstitial-Free High Strength) steel is produced. Using phosphorus leads to the term IF-Rephosphorized steel, or IF-Rephos.
These alloys have composition controlled to improve r-value. In some products, small amounts of boron are added to counteract the embrittlement effects brought on by the phosphorus.
These higher strength IF-HS grades are widely used for both structural and closure applications. Work hardening from forming increases panel strength, which is why they may be described as dent resistant steels. However, this alloying approach is not capable of producing a bake hardenable grade.
Compared bake hardenable steels, carbon-manganese steels, and HSLA steels at similar strength levels, IF-HS grades are more formable, resulting from the ultra-low carbon chemistry and interstitial-free microstructure.
Some of the specifications describing uncoated cold rolled interstitial-free high strength (IF-HS) steel are included below, with the grades typically listed in order of increasing minimum yield strength and ductility. Different specifications may exist. Many automakers have proprietary specifications which encompass their requirements. Note that EN and VDA terminology is based on minimum yield strength, while JFS standard is based on minimum tensile strength.
- EN10268, with the terms HC180Y, HC220Y, and HC260Y D-17
- VDA239-100, with the terms CR160IF, CR180IF, CR210IF, and CR240IF V-3
- JFS A2001, with the terms JSC340P, JSC370P, JSC390P, and JSC440P J-23
AHSS, Conventional HSS, Steel Grades
BH Grades
Bake Hardenable (BH) steels grades are conventional High Strength Steels that exhibit a Bake Hardening Effect. BH steels exhibit an increase in yield strength after room-temperature stamping followed by processing through a thermal cycle comparable to the time-temperature profile used in paint curing (or baking) – approximately 170 °C for 20 minutes. Bake hardenability is characterized by determining the Bake Hardening Index.
Bake Hardenable steel grades have yield strength at shipment from the steel mills of 180 MPa to 300 MPa (approximately 25 ksi to 45 ksi). The grades at the lower strength levels are capable of being produced with a Class A surface finish and are used in applications where dent resistance is desired in thin sheet steel. Applications for the higher strength BH steels include structural parts where Class A surface is not required. The higher strength after forming and baking is the reason automakers might use these in body structure applications, potentially contributing to vehicle lightweighting efforts.
These grades work harden approximately 30 MPa when 2% strain is introduced, either from stamping or during a tensile test, which is similar to dent resistant IF-HS. In contrast to IF-HS, the paint-bake cycle after forming results in an additional yield strength increase. The minimum strength increase from baking is specified by some automakers as 20 MPa to 35 MPa, measured after applying a defined level of strain.
Higher yield strength directly improves the dent performance. Even though BH grades and their non bake hardening counterpart IF-HS grades may have similar yield strength and thickness after forming, bake hardenable steels will show superior dent resistance due to the increase in yield strength from the paint baking operation.
Ferrite is the main microstructural phase of BH steels. The strengthening from the paint bake cycle is due to the controlled amount of carbon remaining in solid solution (on the order of 25 ppm) when the steel leaves the production mill. At the baking temperatures after the part is formed, the dissolved carbon migrates to pin any free dislocations created from stamping. This increases the yield strength of the formed part for increased dent resistance. Formability does not suffer, since the strength increase occurs after stamping.
Most Advanced High Strength Steel (AHSS) grades also exhibit a Bake Hardening Effect, achieving yield strength increases of 40 MPa to 120 MPa from an appropriate thermal cycle. AHSS grades are not categorized with traditional bake hardenable steels, since their primary characteristics and applications are typically, but not exclusively, different. One exception are some Dual Phase (DP) steels available with a Class A surface, which are used as skin panels to combine excellent dent resistance with lightweighting benefits.
Some of the specifications describing uncoated Bake Hardenable (BH) steel are included below, with the grades typically listed in order of increasing minimum yield strength and ductility. Different specifications may exist which describe uncoated or coated, or steels of different strengths.
- ASTM A1008M, with the terms BHS 26 [180], BHS 31 [210], BHS 35 [240], BHS 41 [280], BHS 44 [300]A-25
- EN10268, with the terms HC180B, HC220B, HC260B, and HC300LAD-3
- JIS G3135, with the term SPFC340HJ-3
- JFS A2001, with the terms JSC270H, JSC340HJ-23
- VDA239-100, with the terms CR180BH, CR210BH, CR240BH, and CR270BHV-3
Bake Hardening Effect
Bake Hardenable Steel Grades and most AHSS grades exhibit a Bake Hardening Effect, meaning that there is an increase in yield strength after room-temperature stamping followed by processing through a thermal cycle comparable to the time-temperature profile used in paint curing (or baking) – approximately 170 °C for 20 minutes.
The degree to which a sample is bake hardenable is characterized by the Bake Hardening Index.
In Bake Hardenable Steel Grades, solid solution hardening elements like phosphorus, manganese, and silicon are used to achieve the desired initial strength. For AHSS, the initial strength is determined by the balance and volume fraction of microstructural components like ferrite, bainite, retained austenite, and martensite. In both cases, a specifically engineered amount of dissolved carbon in the ferritic matrix causes an additional increase in the yield strength through controlled carbon aging during the paint-bake thermal cycle. The bake hardening process in AHSS grades is more complex, and results in substantially higher values of the Bake Hardening Index.
Figure 1 shows the work hardening and bake hardening increases for samples of three High-Strength steel grades having the same as-received yield strength prior to 2% pre-straining and baking. The HSLA steel shows little or no bake hardening, while AHSS such as DP and Transformation Induced Plasticity (TRIP) steels show a large positive bake hardening index. The DP steel also has significantly higher work hardening than HSLA or TRIP steel because of higher strain hardening at low strains. No aging behavior of AHSS has been observed due to storage of as-received coils or blanks over a significant length of time at normal room temperatures. Hence, significant mechanical property changes of shipped AHSS products during normal storage conditions are unlikely.
The higher bake hardening index (BHI) of AHSS grades DP 600 and TRIP 700 is also shown in Figure 2. While BHI is determined at a prestrain of 2%, this graph indicates that even higher levels of bake hardenability can be achieved with increasing strain. In a stamping where most areas have more than 2% strain, combining this higher bake hardenability with the increased work hardening that occurs with increasing strain results in a formed panel having a strength markedly higher than the incoming flat steel. This is beneficial for crash energy management.

Figure 1: Comparison of work hardening (WH) and bake hardening (BH) for TRIP, DP, and HSLA steels given a 2% prestrain. S-1, K-3

Figure 2: Bake hardening responses of several HSS and AHSS products with varying pre-strain, reproduced from Figure 3 in Citation B-6. The bracketed numbers after each grade are references within the cited paper.
Bake Hardenability of Exposed Quality Dual Phase Steels
Dent resistance is a function of the yield strength in the formed panel after it completes the paint baking cycle. Based on this premise, grades with higher bake hardenability, such as AHSS, should have substantially higher dent resistance. Application of AHSS grades to capitalize on improved dent resistance also requires their production at the desired thickness and width along with surface characteristics appropriate for Class A exposed quality panels. Some DP steels meet these tight requirements specified by the automotive industry.
A recent studyK-49 highlights this improved dent resistance. This work presents the experimental results and associated numerical investigation of the dent testing of DP270Y490T, a DP steel grade with 490 MPa minimum tensile strength. Tests performed to the SAE J2575 procedureS-7 measure the resultant dent depth after testing, so therefore smaller depths indicate improved performance. Compared with samples not processed through a bake hardening cycle, dent depth reductions occur with hotter and longer cycles, as shown in Figure 3. Increasing temperature plays a more significant role in dent depth reduction than increasing time. This work also reinforces that bake hardenability must be incorporated into simulation models in order to improve the accuracy of dent resistance predictions.
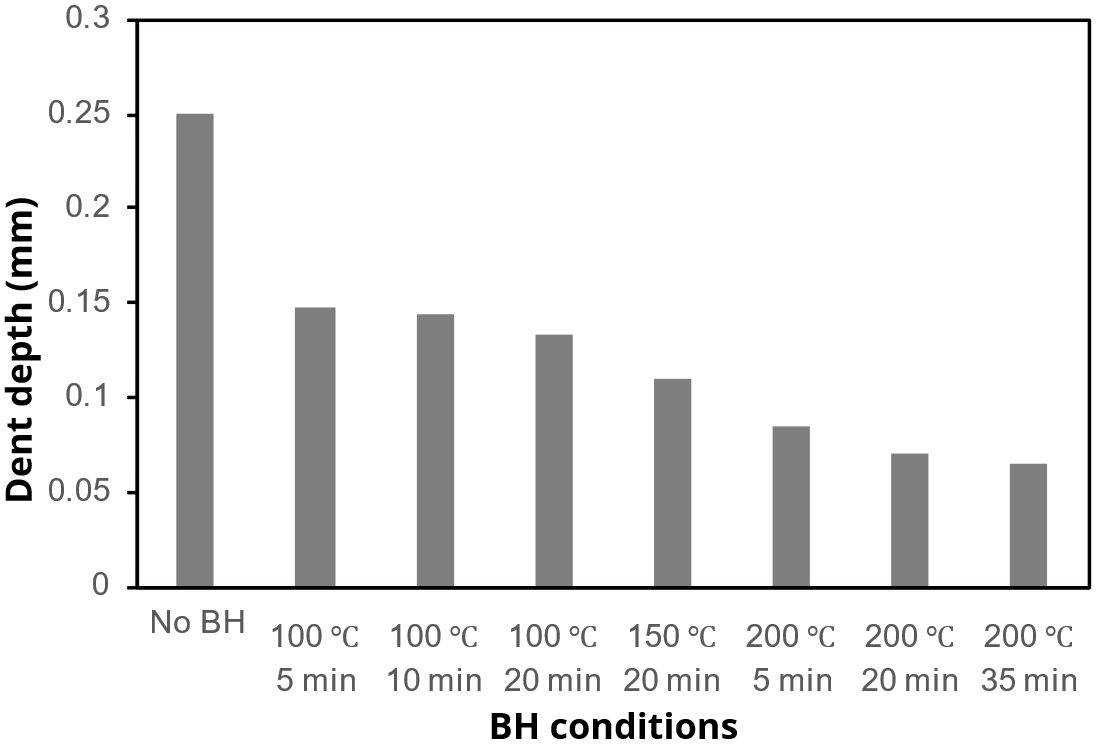
Figure 3: Dent resistance of DP270Y490T according to SAE J2575S-7 as a function of baking test conditions.K-49 Lower dent depth indicates better dent resistance.
Measuring The Bake Hardenability Index
Bake hardenability is characterized by determining the Bake Hardening Index, or BHI.
The Bake Hardening Index (BH2) is determined by taking a conventional tensile test sample and pulling it to 2% strain. This is known as a 2% pre-strain. The sample is then put into an oven for a thermal cycle designed to be typical of an automotive paint curing (paint baking) cycle: 170 °C for 20 minutes. The temperature and time may be different depending on the end-user specifications.
Some companies may specify BH0, which uses the same thermal cycle without the 2% pre-strain. BH5 or BH10 (5% or 10% pre-strain, respectively) may also be reported.
The experimental procedure and calculation of BH2 is standardized in EN 10325D-4 and JIS G 3135J-3, and is similarly described in several other specifications.
Figure 4 defines the measurement for work hardening (B minus A), unloading to C for baking, and reloading to yielding at D for measurement of bake hardening (D minus B). Note that the bake hardening index shown here is measured up to the lower yield point, which is consistent with the EN 10325 definition. JIS G 3135 prescribes the use of the upper yield point.

Figure 4: Measurement of work hardening index and bake hardening index. BHI is measured using the lower yield point in EN 10325D-4 and with the upper yield point in JIS G 3135J-3.
Back To Top
2ndGen AHSS, AHSS, Steel Grades
TWinning Induced Plasticity (TWIP) steels have the highest strength-ductility combination of any steel used in automotive applications, with tensile strength typically exceeding 1000 MPa and elongation typically greater than 50%.
TWIP steels are alloyed with 12% to 30% manganese that causes the steel to be fully austenitic even at room temperature. Other common alloying additions include up to 3% silicon, up to 3% aluminum, and up to 1% carbon. Secondary alloying additions include chromium, copper, nitrogen, niobium, titanium, and/or vanadium.D-29 The high alloying levels and substantially greater levels of strength and ductility place these into the 2nd Generation of Advanced High Strength Steels. Furthermore, due to the density of the major alloying additions relative to iron, TWIP steels have a density which is about 5% lower than most other steels.
Calling this type of steel TWIP originates from the characteristic deformation mode known as twinning. Deformation twins produced during sheet forming leads to microstructural refinement and high values of the instantaneous hardening rate (n-value). The resultant twin boundaries act like grain boundaries and strengthen the steel. On either side of a twin boundary, atoms are located in mirror image positions as indicated in the schematic microstructure shown in Figure 1. Figure 2 highlights the microstructure of TWIP steel after annealing and after deformation.

Figure 1: Schematic of TWIP steel microstructure.

Figure 2: TWIP steel in the annealed condition (left) and after deformation (right) showing deformation twins. The number of deformation twins increases with increasing strain.K-42
EDDS or Interstitial-Free or Ultra-Low Carbon steels are different descriptions for the most formable lower-strength steel. Possible test results for this grade are 150 MPa yield strength, 300 MPa tensile strength, 22% to 25% uniform elongation, and 45% to 50% total elongation. In contrast, test results on TWIP steels may show 500 MPa yield strength, 1000 MPa tensile strength, 55% uniform elongation, and 60% total elongation.
The stress-strain curves for these two grades are compared in Figure 3. The TWIP curves show the manifestation of Dynamic Strain Aging (DSA), also known as the PLC effect, with more details to follow.

Figure 3: Uniaxial tensile stress-strain curves for an interstitial-free (IF) extra-deep-drawing steel and an austenitic Fe-18%Mn-0.6%C-1.5%Al TWIP steel. Curves are presented both terms of engineering (s,e) and true (σ,ε) stresses and strains, respectively.D-30
Figure 4 compares the results of bulge testing ferritic interstitial-free (IF) steel and austenitic Fe-18%Mn-0.6%C-1.5%Al TWIP steel. The TWIP steel is still undamaged at a dome height that is 31% larger than the IF steel dome height at failure.D-30

Figure 4: Comparison of dome testing between EDDS and TWIP.D-30
Excellent stretch formability is associated with high n-values. Shown in Figure 5 is a plot showing how the instantaneous n-value changes with applied strain. N-value increases to a value of 0.45 at an approximate true (logarithmic) strain of 0.2 and then remains relatively constant until an approximate true strain of 0.3 before increasing again. The high and uniform n-value delays necking and minimizes strain peaks. Twins continue to form at higher strains, leading to finer microstructural features and continued increases in n-value at higher strains.

Figure 5: Instantaneous n-value changes with applied strain. TWIP steels have high and uniform n-value leading to excellent stretch formability.C-30
A microstructural deformation phenomenon known as the Portevin-LeChatelier (PLC) effect occurs when deforming some TWIP steels to higher strain levels. The PLC effect is known by several other names as well, including jerky flow, discontinuous yielding, and dynamic strain aging (DSA).
The severity varies with alloy, strain rate, and deformation temperature. Figure 6 shows how DSA affects the appearance of the stress strain curve of two TWIP alloys.D-29 The primary difference in the alloy design is the curves on the right are for steel containing 1.5% aluminum, with the curves on the left for a steel without aluminum. The addition of aluminum delays the serrated flow until higher levels of strain. Note that both alloys have negative strain rate sensitivity.

Figure 6: Influence of aluminum additions on serrated flow in Fe-18%Mn-0.6%C TWIP (Al-free on the left) and Fe-18%Mn-0.6%C-1.5% Al TWIP (Al-added on the right).D-29
The primary macroscopic manifestations of the Portevin-LeChatelier (PLC) effect areD-29:
- negative strain rate sensitivity.
- stress-strain curve showing serrated or jerky flow, indicating non-uniform deformation. Strain localization takes place in propagating or static deformation bands.
- the strain rate within a localized band is typically one order of magnitude larger, while that outside the band is one order of magnitude lower, than the applied strain rate.
- limited post-uniform elongation, meaning uniform elongation is just below total elongation. Said another way, fracture occurs soon after necking initiation.
The PLC effect leads to relatively poor sheared edge expansion, as measured in a hole expansion test. Figure 7 on the left highlights the crack initiation site in a sample of highly formable EDDS-IF steel, showing the classic necking appearance with extensive thinning prior to fracture. In contrast, note the absence of necking in the TWIP steel shown in the right image in Figure 7.D-29
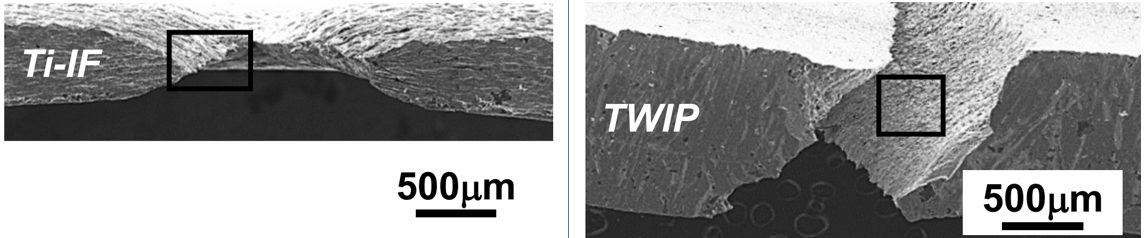
Figure 7: Sheared edge ductility comparison between IF (left) and TWIP (right) steel. TWIP steels lack the sheared edge expansion capability of IF steels.D-29
The stress-strain curves of several TWIP grades are compared in Figure 8.

Figure 8: Engineering stress-strain curve for several TWIP Grades.P-18
Complex-shaped parts requiring energy absorption capability are among the candidates for TWIP steel application, Figure 9.

Figure 9: Potential TWIP Steel Applications.N-24
Early automotive applications included the bumper beam of the 2011 Fiat Nuova Panda (Figure 10), resulting in a 28% weight savings and 22% cost savingsN-24 over the prior model which used a combination of PHS and DP steels.D-31

Figure 10: Transitioning to a TWIP Bumper Beam Resulted in Weight and Cost Savings in the 2011 Fiat Nuova Panda. N-24, D-31
In the 2014 Jeep Renegade BU/520, a welded blank combination of 1.3 mm and 1.8 mm TWIP 450/950 (Figure 11) replaced a two-piece aluminum component, aiding front end stability while reducing weight in a vehicle marketed for off-road applications.D-31

Figure 11: A TWIP welded blank improved performance and lowered weight in the 2014 Jeep Renegade BU/520.D-31
Also in 2014, the Renault EOLAB concept car where the A-Pillar Lower and the Sill Side Outer were stamped from TWIP 980 steel.R-21 By 2014, GM Daewoo used TWIP grades for A-Pillar Lowers and Front Side Members, and Hyundai used TWIP steel in 16 underbody parts. Ssangyong and Renault Samsung Motors used TWIP for Rear Side Members.I-20
Other applications include shock absorber housings, floor cross-members, wheel disks and rims, wheelhouses, and door impact beams.
A consortium called TWIP4EU with members from steel producers, steel users, research centers, and simulation companies had the goal of developing a simulation framework to accurately model the complex deformation and forming behavior of TWIP steels. The targeted part prototype component was a backrest side member of a front seat, Figure 12. Results were published in 2015.H-58

Figure 12: TWIP4EU Prototype Component formed from TWIP Steel.H-58
In addition to a complex thermomechanical mill processing requirements and high alloying costs, producing TWIP grades is more complex than conventional grades. Contributing to the challenges of TWIP production is that steelmaking practices need to be adjusted to account for the types and amounts of alloying. For example, the typical ferromanganese grade used in the production of other grades has phosphorus levels detrimental to TWIP properties. In addition, high levels of manganese and aluminum may lead to forming MnO and Al2O3 oxides on the surface after annealing, which could influence zinc coating adhesion in a hot dip galvanizing line.D-29