Forming Modes
top-of-page
The usual mode of bending is curvature around a straight-line radius (Figure 1). Through the thickness is a gradient of strains from maximum outer fiber tension (the outermost surface) through a neutral axis to inner fiber compression (the surface closest to the punch or bend axis). No strain occurs along the bend axis in the direction parallel to the bend axis, and therefore is in plane strain. The discussion below considers only bulk deformation, and excludes the implications of any edge effects. Bend testing procedures are linked here.

Figure 1: Typical bend where the outer surface is in tension, and the inner surface is in compression. A neutral axis lies in between.S-23
When sheet metal flows through draw beads or over the die radius into the punch opening, it is bent, straightened, and in the case of draw beads re-bent in the opposite direction. The net strain after this process may be relatively small. However, each of the sequential bending and unbending steps strain hardens the sheet metal, which reduces the ability for further deformation of the metal in subsequent operations.
Deformation at the outer surface during three-point bending depends on the stretchability capacity of the metal. The failure strain in the bend is related to the total elongation of conventional steel, but AHSS grades with multiphase microstructures such as DP and TRIP experience shear fracture that severely reduces the bendability before failure occurs. A higher total elongation helps sustain a larger outer fiber stretch of the bend before surface fracture, thereby permitting a smaller bend radius. Since total elongation decreases with increasing strength for a given sheet thickness, the minimum design bend radius must be increased (Figure 2).

Figure 2: Larger bend radius is needed as the total elongation decreases.S-23
The ratio of punch radius to sheet thickness, or the r/t ratio, allows for calculation of the amount of elongation on the outermost surface. This value can be compared against the total elongation of the metal as determined in a tensile test, or against the minimum elongation value allowed in the specification. If the part geometry will not allow for sufficient elongation for the selected metal grade, then either the part, process, or steel grade must change. [Note that this is not a perfect assessment, since elongation in a tensile test is measured relative to a 50 or 80 mm gauge length, which is likely different than the dimensions of the bent section.]
For design and springback control, usually a smaller r/t ratio is desirable. However, this may not be suitable in terms of formability. Increased material strength usually is associated with a reduction in total elongation, which in turn means a successful bend requires a larger r/t ratio.
For equal strengths, most AHSS grades have higher total elongations than conventional HSLA steels. However, several AHSS grades have limited local formability based on their microstructure, and may be at risk for cracking during edge expansion.
Cracking in production stamping conditions at stress levels below what is predicted with Forming Limit Diagrams may be attributed to these local formability failures. As an illustration, physical bend tests and simulations were performed for both HSLA and DP780 steels.S-11 The HSLA global formability failure aligned with simulation predictions (Figure 3), and was accompanied by a visible neck (Figure 4). In contrast, the DP780 showed no visible neck at the failure site (Figure 5) and no correlation between the simulation and actual test results (Figure 6).
Like hole expansion, bending limits in AHSS products are further lowered by shear fracture associated with the interfaces between the ductile ferrite and the hard martensite phase in the microstructure. This reduction becomes more severe as the strength increases, since increasing strength is achieved by increasing the volume of the hard martensite phase. More about shear fracture is found here.

Figure 3: Forming simulation of HSLA with strong correlation to actual testing.S-11

Figure 4: Close-up of visible necking before tensile failure in HSLA.S-11

Figure 5: Comparison of forming simulation with actual testing of the DP780. Note lack of correlation.S-11

Figure 6: Close-up of local formability failure on DP780 with no visible necking before failure.S-11
Rotary Bending
One way to address springback involves the use of rotary benders. Rotary benders transfer the vertical movement of a press stroke into a precise, rotary forming motion. A rocker or rotating die can simultaneously hold, bend, and overbend the sheet past 90° to counter material springback (Figure 7).
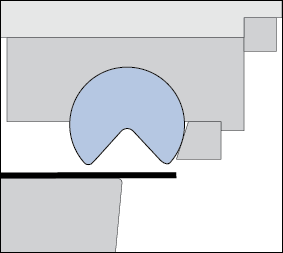
Figure 7: The rotation of the rocker bends the sheet metal around the anvil with less pressure than needed for wipe toolsD-8
Use rotary bending tooling where possible instead of flange wipe dies. Rotary bending allows for easy adjustment of the bending angle to correct for changes in springback due to variations in steel properties, die set, lubrication, and other process parameters. In addition, the tensile loading generated by the wiping shoe is absent.
There are four sequential steps to the process:
1) Downward pressure from the rocker clamps the part with the bending lobes before bending starts
2) Induced rotation of the rocker bends material around the anvil
3) The rocker bends the sheet metal past final angle to compensate for springback
4) The rocker releases the sheet metal to allow springback to desired angle
Using rotary benders to roll darts into the part during bending provides another way to reduce springback and stiffen the part (Figure 8).
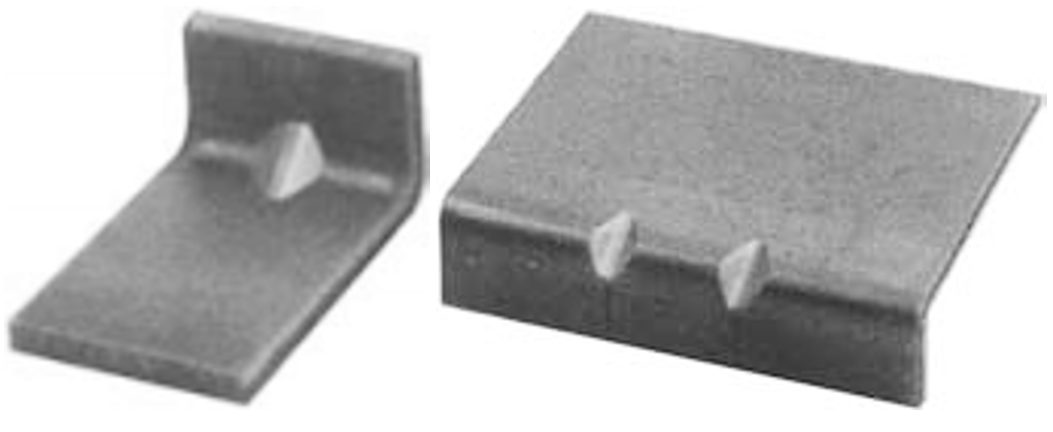
Figure 8: Stiffening darts can be created as part of the rotary bending operation.R-7
Back to the Top
Simulation
Evaluating sheet metal formability using computer software has been in common industrial use for more than two decades. The current sheet metal forming programs are part of the transition to virtual manufacturing that includes analysis of casting solidification and rolling at the metal production facility, welding, moulding of sheet/fiber composites, automation, and other manufacturing processes. Computer simulation of sheet metal forming is known by several terms, including computerized forming process development and computerized die tryout.
Many highly developed software programs closely replicate the physical press shop forming of sheet metal stampings. These programs have proven to be accurate in predictions of blank movement, strains, thinning within the blank, wrinkles, buckles, and global formability concerns of necking strains and forming severity as defined by conventional forming limit curves. Accurate prediction of local formability related failures such as cut edge expansion is more challenging due to modeling of the production process influence as opposed to the ideal laboratory edge. Prediction of springback generally provides helpful results in understanding the trends and effects. The quality of springback predictions vary with the specific stamping geometry, the selected metal grade, the input information, and user experience, as discussed in Simulation Inputs.
Virtual forming-process development is ideally suited to the needs of current and potential users of AHSS grades. A full range of analysis capabilities is available to evaluate AHSS behavior in a new stamping. These programs allow rapid “what-if” scenarios to explore the impacts of different grades of AHSS, alternative processing, or even design optimization. A Design of Experiments on actual tooling in a physical press shop is limited to only a few variables and may be subject to noise variables clouding the results. In the virtual press shop, changing variables is done with a stroke of the keyboard, and is far easier to undo than permanent changes to the tooling.
Virtual die tryout has numerous advantages, allowing for assessing the viability of part, process, and die design all before cutting the first hard die. Addressing problems before costly and time-consuming die construction starts leads to improved quality and a better use of resources.
The type of software used depends on the goals and available information at each stage of the process, shown in Figure 1. At the beginning of the styling to production cycle, feasibility – whether the stamping can even be manufactured – is the key question. With only the 3D CAD file of the final part and material properties, One-Step or inverse codes can rapidly ascertain strain along section lines, thinning, forming severity, trim line-to-blank, hot spots, blank contour, and other key information. This approach takes the finished part geometry and unfolds that shape to generate a starting blank, calculating the strain between the two shapes (formed vs. flat). Since it starts with the finished geometry rather than the blank, the process is the inverse of reality. All deformation takes place in a single step, or one step, leading to the description of a one step inverse code. Although this takes reduced computing time, only some simulation packages allow incorporation of the forming process, tooling geometry, and the changes in metal properties associated with deformation.
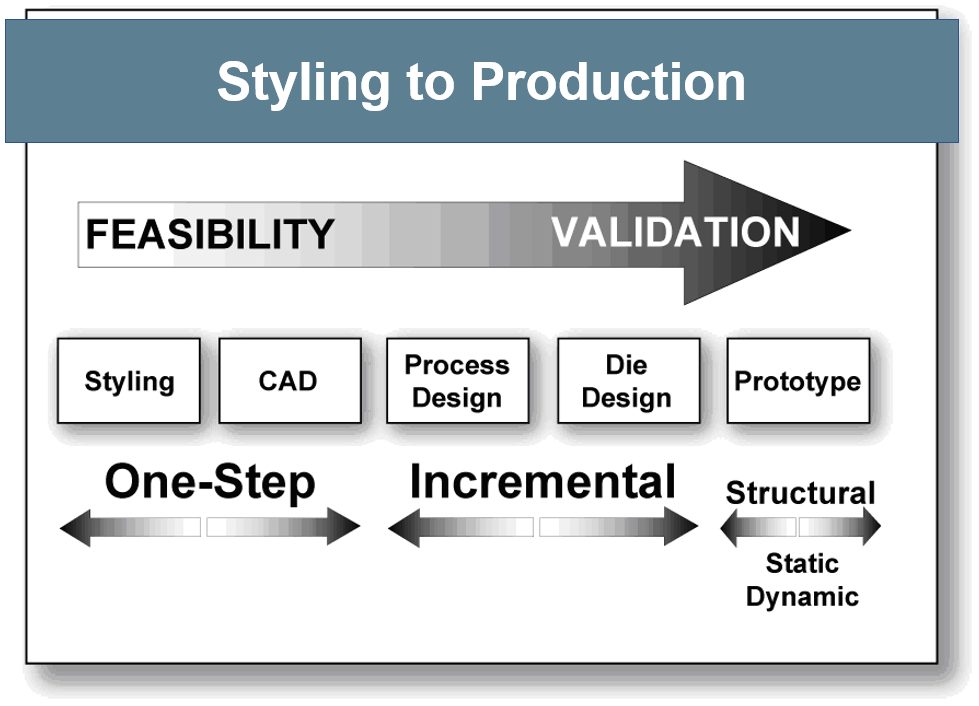
Figure 1: Software types change during processing stage.
Achieving more accurate results involves incremental simulation, where the virtual forming process attempts to replicate reality. This approach models the tools (punch, die, and blankholder) and process parameters (like the blankholder forces, blank shape, and bead geometry, location and restraining forces). Each increment, or time-step, reflects the sheet metal deformation at a different position of the press stroke. Subsequent increments rely on the output from the prior increments. As the quality of the inputs increase, so does the precision of the results.
During selection of process and die design parameters, software evaluates how each new input affects the strains and blank movement (including wrinkles and splits), and generates a press-loading curve. The analysis creates a visual record of the blank deformation into the final part through a transparent die. Each frame of the video is equivalent to an incremental hit or breakdown stamping. Problem areas or defects in the final increment of forming can be traced backwards through the forming stages to the initiation of the problem, allowing problems to be addressed when before they even occur. Some software packages allow analysis of multi-stage forming, such as progressive dies, transfer presses, or tandem presses. This virtual environment also shows the effects of trimming and other offal removal on dimensional precision and springback.
AHSS grades are suited for load bearing or crash-sensitive applications, and forming simulation helps to optimize performance. Previously, the static and dynamic capabilities of part and assembly designs were analyzed using CAD-generated stamping designs with inputs of initial sheet thickness and as-received yield strength. Often the tests results from real parts did not agree with these early analyses because the effects from forming were not incorporated. State-of-the-art applications now model the forming operation first, allowing for local thinning and work hardening to occur. That point-to-point sheet thickness and strength levels are mapped to the crash simulation inputs, resulting in crash models nearly identical to physical test outputs. Correcting deficiencies of the virtual parts by tool, process, or even part design occurs before tool construction has even begun.
Many simulation packages can evaluate the performance of AHSS grades in many forming environments. A simple constitutive equation with a single n-value sufficiently approximated the stress-strain response of older grades. The n-value of AHSS grades changes with strain, so when simulating AHSS grades, input the full stress-strain curve instead of choosing just one n-value. However, this capability may not be present in some proprietary industrial and university software. Use caution when using these programs to analyze AHSS stampings.
Today’s AHSS grades are not the commodities of yesteryear, but instead are highly engineered products unique to the production equipment and processing route chosen by the steelmaker. Although many companies may be capable of meeting the minimum and maximum mechanical properties associated with a specific grade, different suppliers may take up a different portion of the acceptable window. Working with your production steel supplier helps ensure you are using company-specific forming data.
Also remember that there are multiple products associated with a targeted tensile strength. For example, not only are there different families of 980 MPa minimum tensile strength steels (like dual phase, TRIP, and Q&P), but within each family there are multiple options. A grade designated as “DP980” may have enhanced global formability as measured with total elongation, enhanced local formability as measured in a hole expansion test, or have a balance between those properties. The associated material card for simulation will be different, and use of the incorrect card in development could lead to an under-engineered process when attempting to run with production steel.
Key Points
- A virtual tryout evaluates the stamping and die design, and can detail areas of severe forming, buckles, excessive blank movement, and other undesirable deformation before starting tool construction.
- Evaluating alternative “what-if” scenarios in a virtual environment is faster and more efficient than grinding and welding on physical tooling, and mistakes have no permanent impact.
- Design of Experiments (DOE) studies are challenging to do in the physical press shop. The large number input changes required by the process makes it difficult to attribute changes to the intended variables tested or to some noise factor. Simulation allows for easier and faster evaluations when changing one or more parameters.
- AHSS grades change properties when deformed under different forming conditions. Forming simulation captures these changes to show how the final product will react.
- Observing the sheet metal transition from a flat blank to the engineered stamping in a transparent die is a valuable troubleshooting tool provided by virtual forming.
- Simulation codes accurately capture blank motion, thinning strains within the body of the stamping, and other global formability issues like severity compared with the conventional forming limit curve. However, prediction of local formability concerns like sheared edge stretchability is lacking due to the challenges of capturing all the effects related to creating that cut edge.
- The virtual forming codes do not accurately predict springback or the success of springback correction procedure because of the lack of accurate data everywhere in the stamping during the entire forming operation. However, users report reduction in recuts of the die from 12 or more to three or four based on information from the code.
A well-defined material card and accurate descriptions of metal flow throughout the stamping are critical for precise springback predictions, as discussed in the section on Simulation Inputs. Lacking that, many simulation packages can at least provide guidance on the trends which may help guide springback countermeasures.
structural performance
Normal vehicle use leads to repeated loading of components and joints. Stress concentrations in the body structure may lead to plastic strains at stresses below the yield strength due to cyclic fatigue. Conventional High-Strength Steel fatigue behavior correlates with their tensile strength. However, in multiphase steels, the strain distribution between phases within the steel microstructure affects the fatigue response, leading to a different response depending on which phases accommodate the strain.
The fatigue strength of DP steels is higher than that of precipitation-hardened steels or fully bainitic steels of similar yield strength for several metallurgical reasons. The dispersed fine martensite particles retard the propagation of fatigue cracks. For TRIP steels, the transformation of retained austenite can relax the stress field and introduce a compressive stress that can also improve fatigue strength. General categorization may not be possible – studies have reported cyclic hardening occurs in Dual Phase steels where the martensite volume fraction is less than 0.5 while Dual Phase steels at higher martensite content (higher strength) soften under cyclic loading conditions. C-15, W-27 Furthermore, fatigue limits are complicated by environmental factors like the presence of hydrogen.
Figures 1 and 2 illustrate the general improvements in fatigue capability offered by Advanced High-Strength Steel (AHSS) grades.

Figure 1: Fatigue characteristics of TRIP steel CR450Y780T-TR compared to conventional steels.T-24

Figure 2: Fatigue limit for AHSS compared to conventional steels.T-2
The table below lists some fatigue properties for conventional and advanced high strength steels.
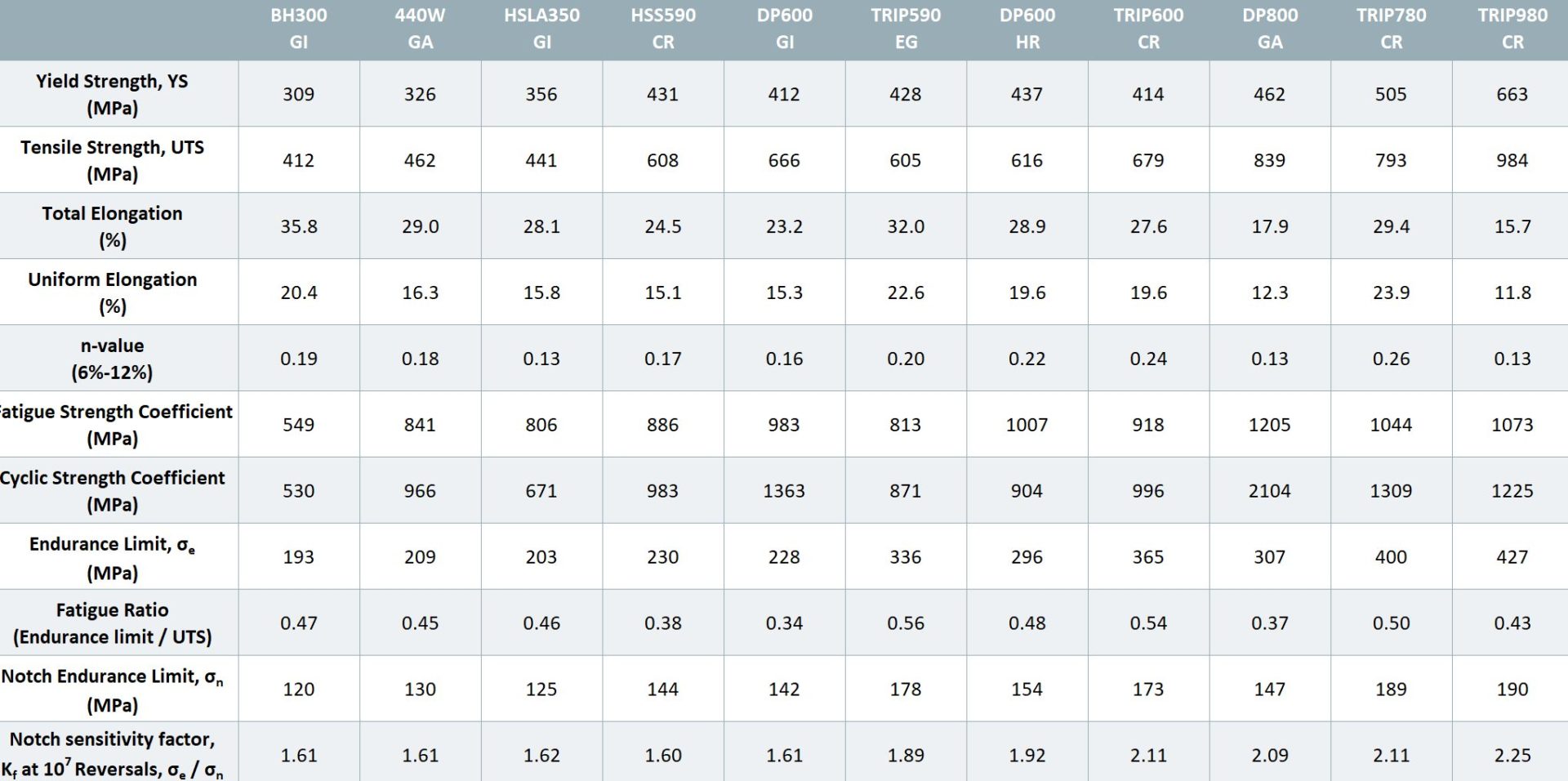
Table 1: Fatigue properties for HSS and AHSS grades Y-11
Cutting, Cutting-Blanking-Shearing-Trimming
A cut edge has four distinct zones with different characteristics:
- Rollover – The plastically deformed zone bent as the cutting tools contact the edge of the sheet surface.
- Burnish – The zone where the cutting tools penetrate into the sheet metal, prior to any fracturing. The sheet metal stresses are such that the surface compresses into the cutting tool, which gives it a flat, smooth, and shiny appearance. The shear zone is another name for this region.
- Fracture – The zone where the cutting steels fracture the sheet metal, leading to separation from the remainder of the sheet. The surface of this region is rougher than the burnish zone, and is at an angle from the cutting direction.
- Burr – The metal elongated and pushed out on the trailing edge of the cut.
The cutting process also deforms the metal near the shear face, creating what is known as the shear affected zone (SAZ). The degree and influence of this deformation is a function of the cutting process (shearing, water jet, laser, and so on) as well as the steel microstructure and strength. Many studies conclude plastic deformation within the SAZ is a key contributor to sheared edge stretching failures.
The Shear Affected Zone is the area of work-hardened steel and microstructural damage behind the sheared edge. The deformation pattern in the SAZ includes a large shear-induced rotation of the grains that increases with proximity to the sheared edge. An etched cross-section such as that shown in Figure 1 highlights the grain rotation and gives a visual indication of the size of the zone.

Figure 1: Shear Face Components and Shear Affected Zone.K-1
Work hardening in the SAZ leads to a way to quantify the depth of the SAZ: by creating a hardness profile with readings starting at the edge and progressing deeper into the metal. The end of the SAZ occurs when the hardness readings level off to the bulk hardness.
Figure 2 compares the edge and hardness readings for CP800 and DP780, showing the depth of the SAZ for DP780 is about 41% of the initial sheet thickness of 1.56 mm, and the depth of the CP800 SAZ is 20% of the initial 2.90 mm sheet thickness.P-12

Figure 2: A) Sheared edge and SAZ of CP800; B) Sheared edge and SAZ of DP780; C) CP800 microstructure away from edge; D) DP780 microstructure away from sheared edge; E) hardness profile for the two sheared edges in the rolling direction.P-12
Plastic deformation from cutting and subsequent edge expansion forms micro-voids and creates other microstructural damage. The voids grow and combine with neighboring voids to create micro-cracks, which in turn combine with other micro-cracks resulting in the cracks that cause fractures in stampings.
Void nucleation in DP steels occurs through two mechanisms: decohesion of the ferrite-martensite interface or fracture of martensite islands.P-12, A-27, A-28 Figure 3 shows an example of both.

Figure 3: Aligned voids along loading direction. White solid square shows interface damage between martensite and ferrite. White dashed circles show voids formed by cracking of martensite.A-28
The study in Citation P-12 compared CP800 and DP780. The CP800 microstructure contains ferrite, bainite, and martensite. The DP780 microstructure has more martensite, with a larger strength differential between the phases, which combines to result in a lower nucleation strain and accelerated void nucleation compared with CP800. The DP grade has a larger SAZ, further promoting nucleation, growth, and coalescence of voids. This results in failure at a lower strain and leads to the lower edge stretchability of the DP780 compared to the CP800 alloy.P-12 The ductility of bainite restrains void initiation at high strains, which may play a role in improved sheared edge performance.S-24, S-25
Fracture initiation energy, a measure of fracture toughness correlates with hole expansion and stretch-flangeability as shown in Figure 4.Y-5

Figure 4: Correlation between fracture initiation energy and hole expansion ratio of various metals. Steels A – D are AHSS grades with Tensile strength ranging from 725 – 1000 MPa.Y-5
In addition to microstructural damage and fracture mechanics, simulation models improve in accuracy when the incorporating the effect of the temperature increase in the localized deformation zone. Simulation of the blanking of AISI 1050 shows a temperature at the cut edge of 440 °C. The edge temperature may be even higher in AHSS grades due to their higher strength.A-29

Figure 5: 1.27mm AISI 1050 steel blanked with 15% clearance. The simulation shows temperature, with the cut face getting as hot as 440 °C.A-29
When factoring in the considerations described here, simulation accuracy of hole expansion and sheared edge stretching improves significantly. Citations L-13 and L-14 provide additional background information about the Shear Affected Zone.
FLC and FLD
Conventional Forming Limit Curves (FLCs) gained widespread industrial use since being introduced by Dr. Stuart Keeler in the 1960’s. Applications from feasibility analysis to stamping plant troubleshooting use these principles. The strain hardening exponent (n-value) and thickness are inputs into a shortcut to create the curve placement and shape, but this is applicable to only mild steels, conventional High-Strength Steels, and some Advanced High-Strength Steels. Furthermore, this shortcut is an approximation, coming from a best-fit curve generated from data points gathered over multiple grades.
A typical method used in creating most FLCs includes deforming samples of different widths with a 100 mm (4 inch) diameter hemispherical punch – known as the Nakajima method. An alternate approach uses a flat-bottom cylindrical punch, known as the Marciniak method (Figure 1). Independent of the punch shape used, generating FLCs involves measuring the strains resulting from deforming a blank to a formed shape. The conventional FLC plots major strain on the vertical axis against minor strain on the horizontal axis. This FLC applies only to in-plane stretching in linear strain paths, and assumes that there are no through-thickness stress or strain differences. Assessing bendability or cut edge ductility is not possible with this approach.
![Figure 1: Punch Shape Used to Create Forming Limit Curves Result in Through-Thickness Strain Differences Which Influence the Shape and Placement of The FLC [Reference 1]](https://ahssinsights.org/wp-content/uploads/2020/09/2.3.3.2-Fig1-Domes.svg)
Figure 1: Punch Shape Used to Create FLCs Result in Through-Thickness Strain Differences Which Influence the Shape and Placement of The FLC S-37
Figure 2 compares the FLCs generated by deforming DP980 with the three punch shapes highlighted in Figure 1. Note the higher strains associated with the 50 mm diameter hemispherical punch compared with the strains generated from the 100 mm diameter hemispherical punch. This punch curvature difference impacts the magnitude of the strains that develop through the thickness of the sheet. On samples deformed with a hemispherical punch, the selected strain measurement technique (circle/square grid analysis or Digital Image Correlation, for example) directly measures strains on the outer top surface only, with the middle and inner surface having progressively lower strains as a function of the R/T ratio. A punch or feature with small R/T leads to high strains on the outermost surface. Strains exceeding the FLC on only this outer surface will not lead to necks on the formed panel. Exceeding the FLC through the entire thickness – from the inner surface to the outer surface – must occur for the sample to show a neck.T-17
![Figure 2: FLCs of the same batch of DP980 Showing Dependence on Punch Shape and Curvature [References 1 and 3]](https://ahssinsights.org/wp-content/uploads/2020/09/2.3.3.2-Fig2-FLC-different.svg)
Figure 2: FLCs of the same batch of DP980 Showing Dependence on Punch Shape and Curvature.S-37, M-15
In addition to the through-thickness strain differences from the punch curvature, the metal flow differences resulting from the punch shapes leads to directional changes in the strain path taken by the deforming metal. A channel drawn part with a hat-shaped cross section in which there are no features like embossments is likely to have a linear strain path. Forming every other engineered stamped part geometry involves some degree of a non-linear strain path (NLSP).
The importance of strain path and deformation history comes from the changes in the forming limit that occur once metal deformation starts. The black curve in Figure 3 shows the FLC for an alloy generated in a conventional manner with as-received metal, assuming a linear strain path. The red curve results from testing the same metal that initially stretched to an equal-biaxial plastic pre-strain of 0.07. In this strain path, substantially less deformation can occur before reaching the forming limit. However, the strain path changes if the local part contour is different, and that strain path results in a different amount of subsequent deformation prior to necking. The magnitude and direction of the shift changes based on the strain and the orientation relative to the rolling direction. Citation S-38 highlights these curves and presents more examples of the effects of different strain paths. The important conclusion is that the amount of deformation that a metal is capable of withstanding prior to necking changes throughout the forming process and depends on the local part shape (among other variables), and cannot be discerned by using only the conventional strain based FLC.
![Figure 3: Experimental FLCs for a linear strain path (in black) and for a bilinear strain path after 0.07 strain in equal biaxial tension in strain space (in red) [Reference 4]](https://ahssinsights.org/wp-content/uploads/2020/09/2.3.3.2-Figure3-FLC-strainPath.svg)
Figure 3: Experimental FLCs for a linear strain path (in black) and for a bilinear strain path after 0.07 strain in equal biaxial tension in strain space (in red) S-38
Figure 4 shows the strain paths associated with the FLCs presented in Figure 2, with along with a magnified portion of one of the curves. This non-linearity is a characteristic of samples formed with a dome, associated with the sample wrapping around the punch during the initial contact and experiencing a combination of biaxial bending and stretching. Citation M-15 presents a method to correct for strain path effects.
![Figure 4: Strain Path for FLCs shown in Figure 2. A) 100mm diameter flat punch; B) 100mm diameter hemispherical punch; C) 50mm diameter hemispherical punch; and D) Magnified portion of one curve from Figure 4B showing the non-linearity of the strain path [References 1 and 3]](https://ahssinsights.org/wp-content/uploads/2020/09/2.3.3.2-Figure4-FLC-strainPath.svg)
Figure 4: Strain Path for FLCs shown in Figure 2. A) 100 mm diameter flat punch; B) 100 mm diameter hemispherical punch; C) 50 mm diameter hemispherical punch; and D) Magnified portion of one curve from Figure 4B showing the non-linearity of the strain path.S-37, M-15
Accounting for tool contact pressure is critical as well, since pressure through the sheet thickness suppresses the onset of necking. Applying this compensated FLC in simulation or in hands-on analysis parts analysis requires modification for the unique characteristics of each part, with appropriate adjustments for local curvature, contact pressure and deformation history. Citations S-37 and M-15 detail methods to compensate for the effects of strain path, curvature, and tool pressure. Figure 5 shows that after incorporating these corrections, the curves condense to one shape independent of the variables used.
![Figure 5: As-generated FLCs compared with FLCs after strain path, curvature, and tool contact pressure corrections [References 1 and 3]](https://ahssinsights.org/wp-content/uploads/2020/09/2.3.3.2_5.jpg)
Figure 5: As-generated FLCs compared with FLCs after strain path, curvature, and tool contact pressure corrections.S-37, M-15
In summary, FLCs generated from relatively similar simple tools are sensitive to small differences in R/T ratio, incorporation of tool contact pressure, and deviations from a linear strain path. By comparison, engineered stampings require substantially more complex tool shapes with differing degrees of curvature, tool contact pressure, and strain paths all within one part. These complex part shapes contribute to an even wider variation in the yield surface and hardening mechanisms important for simulation, and impacts predictions of formability, springback, and stress analysis.
A common requirement during tooling buyoff – where all strains need to be below the FLC by at least a certain amount called the safety margin – magnifies these challenges. AHSS grades already have low FLCs relative to their lower strength counterparts, so it is critical that the chosen FLC does not further reduce efficient application of these grades. Minimizing sensitivity to the changes in strain path occurring across a complex part requires using a different approach – a FLC with the axes in stress-space rather than the conventional strain-space.
This discussion has centered on conventional strain-based FLCs, which incorporate an assumption of a linear strain path as a flat sheet deforms to the final shape. Stress-based Forming Limit Curves (sFLC or FLSC) are insensitive to deformation history and can be adjusted to reflect the differences in local tool geometry or contact pressure across the stamping. Forming analysis software readily converts conventional FLCs into stress-based units. Figure 6 converts the two strain paths presented in Figure 3 into stress-space, and shows the two experimental stress FLCs generated with different strain paths are independent of the loading history and essentially overlap. Citations S-38, S-39, S-40 and S-41 contain information about stress-based FLCs, as well as their generation and usage.

Figure 6: After converting the conventional FLCs in Figure 3 to stress-space, the experimental stress-based FLCs show no significant differences.S-38
Citation H-20 presents a related method to transition from strain-based to stress-based Forming Limit Curves. The proposed stress-based failure criterion postulates that localized necking occurs when a critical normal stress condition is met. This approach adequately describe the experimental strain-based forming limit data in most evaluated materials, failing only with a 3rd Generation AHSS alloy containing a high percentage of retained austenite. For this grade, the authors speculate that a material model more advanced than the one employed in this study will improve correlation.
Accurate simulation requires accurate and complete inputs, including the full range of metal properties, with correct material flow and hardening models, and an understanding of the conditions that will produce failure. Any shortcuts taken increases the likelihood that simulation will not fully match reality for all materials, part shapes, and production processes. A conventional strain-based FLC assumes no effect of part geometry, tool contact pressure, and deformation history – all of which occur on engineered stampings to differing degrees. Analysts should incorporate stress-based FLCs into their simulation with appropriate adjustments to address local geometry and contact pressure to ensure an accurate representation of the metal’s forming characteristics.
For use in the die shop or stamping plant, a growing number of optical systems have built-in features to map strain measurements on to an sFLC. Use caution when employing this approach since these systems measure only the final net strain, and not the strain history as the panel deforms. Proper application involves capturing metal flow from individual breakdown panels and adjusting the FLC accordingly as the panel gets closer to the home position.
Special thanks to Dr. Thomas Stoughton, Technical Fellow, General Motors Research & Development, for assistance in preparing this information.
Forming Modes
Drawing is the sheet metal forming process where the punch that creates the part shape forces the sheet metal to pull in from the flange area. In contrast with stretch-drawing or stretch forming, little metal thinning occurs in pure drawing. There is not a generally accepted definition for the term “deep drawing,” although some references describe it as when the depth of draw is greater than the diameter.
Drawability, or the ability for a sheet metal to be drawn into a cup, is assessed by the cup drawing test to measure the Limiting Draw Ratio, or LDR. Here, a cylindrical punch contacts and then pushes a circular blank into the die (Figure 1). The ratio of the largest blank diameter successfully drawn into a cup to the punch diameter used for drawing is the LDR.

Figure 1: In the cup drawing test, a punch deforms a circular blank into a cylindrical cup. The largest ratio of blank diameter to punch diameter successfully drawn into a cup is the Limiting Draw Ratio (LDR).
In the LDR test, metal in the circular blank flows over the die radius and into the cup wall. The metal movement from the flat blank to the vertical sidewalls is the only metal movement which happens, since there is no metal flow within the flat bottom region.
As shown in Figure 2, the flange of the circular blank undergoes radial tension and a circumferential compression as the flange moves in a radial direction towards the circular die radius in response to a pull generated by a flat bottom punch. Blank holder pressure is set to prevent buckles in the blank.
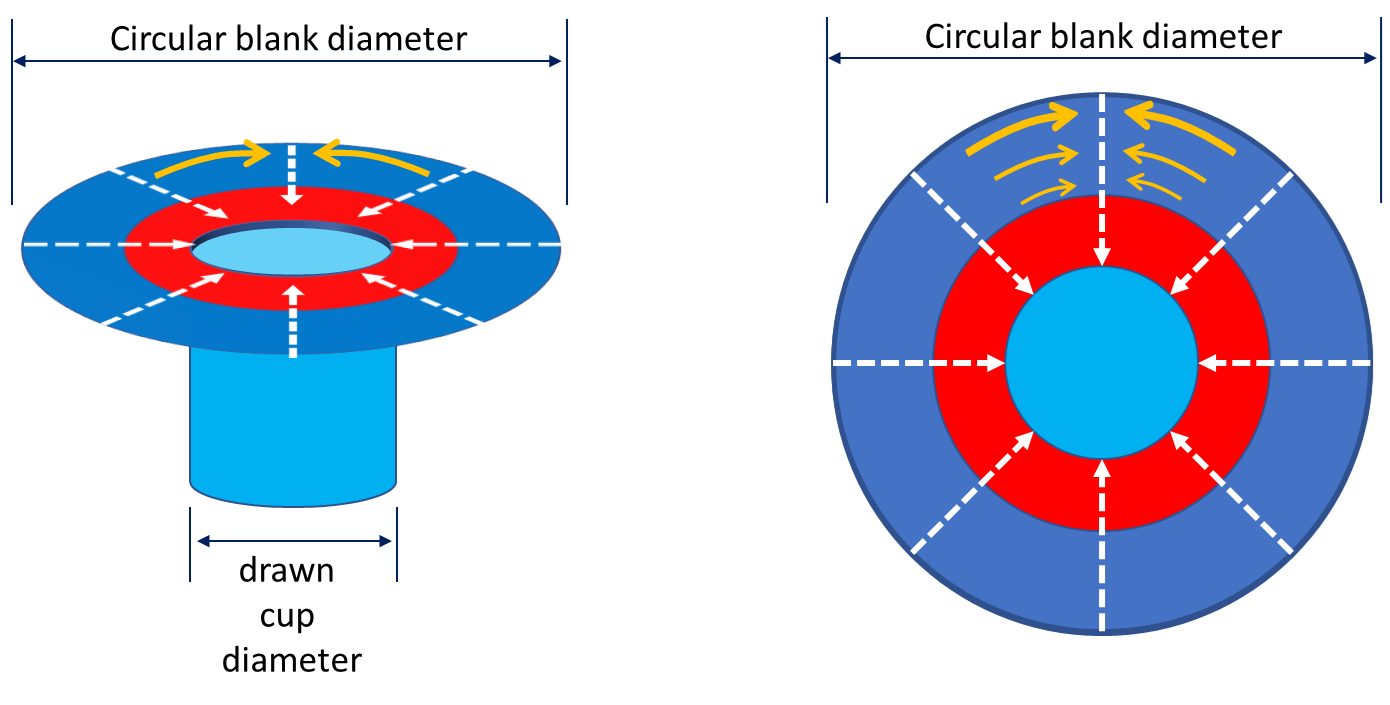
Figure 2: Tension and compression in a drawn cup. Dashed white arrows indicate the radial tension created during cup forming; orange arrows indicate flange compression as a greater amount of metal feeds into progressively smaller regions.
The steel property that improves cup drawing or radial drawing is the normal anisotropy or rm value. Values greater than 1 increase in the Limiting Draw Ratio. In contrast, the LDR is insensitive to the strength of the steel and the n-value. High-strength steels with UTS greater than 450 MPa and hot-rolled steels have rm values approximating one and LDR values between 2.0 – 2.2. Therefore, DP and HSLA steels have similar LDR values. However, TRIP steels have a slightly improved LDR deep drawability.T-2 Since the transformation of retained austenite to martensite is influenced by the deformation mode (Figure 3), the amount of transformed austenite to martensite generated by shrink flanging in the flange area is less than the plane strain deformation in the cup wall. This difference in transformation from retained austenite to martensite makes the wall area stronger than the flange area, thereby increasing the LDR. The benefit of the increased LDR is seen in Figure 4 which shows cups formed from different grades having the same tensile strength.

Figure 3: The cup wall in plane strain strengthens more than the shrink flange due to increased amounts of transformed martensite in TRIP steels.T-2
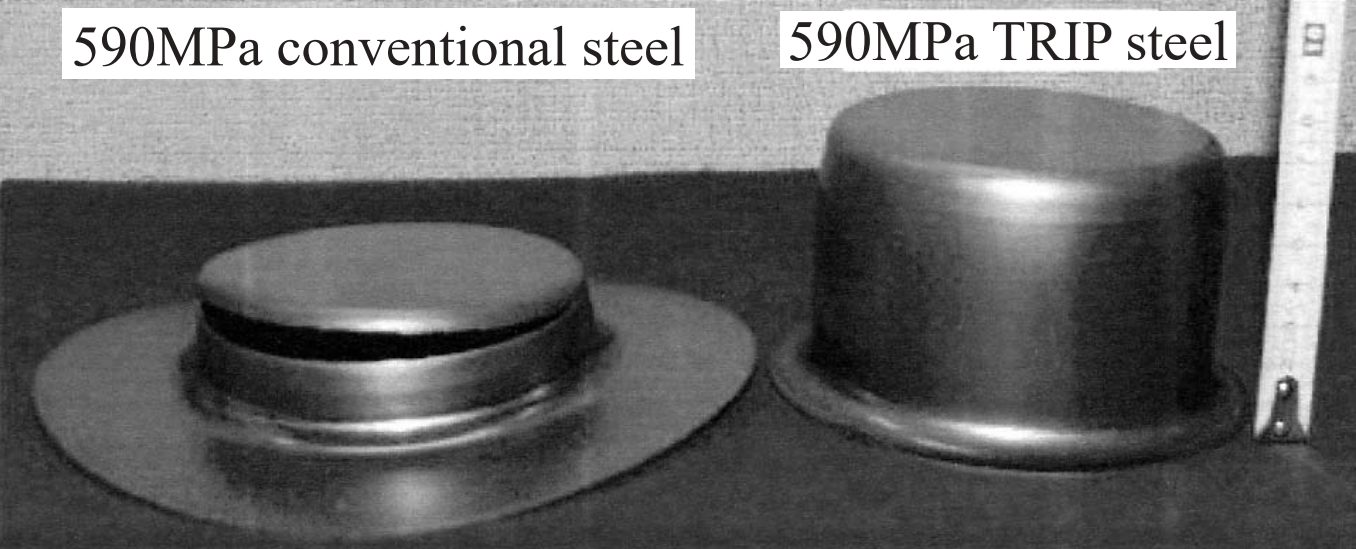
Figure 4: Cups formed from 590MPa tensile strength steels, highlighting greater draw depths possible with TRIP steels.T-2
In a study of different gradesC-9, laboratory cup drawing experiments show an approximate LDR of 2.0 – 2.2 for the DP steels tested (Figure 5). Note that a doubling of the yield strength has no effect on the LDR. An increased rm value of mild steel created a small increase in LDR over DP steel. The LDR of the MS (martensitic) steel evaluated may have been impacted by the reduced bendability going over the die radius. Figure 6 shows the cup draw depths possible for the grades reported in Figure 5.S-26
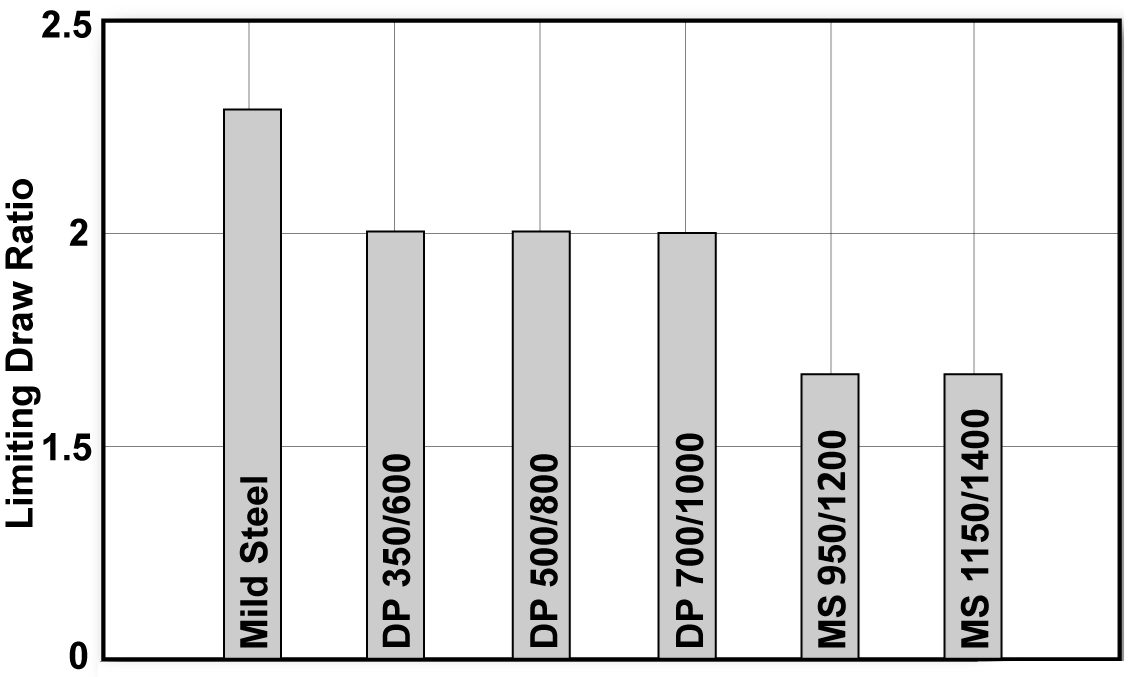
Figure 5: LDR tests for Mild, DP, and MS steels.C-9
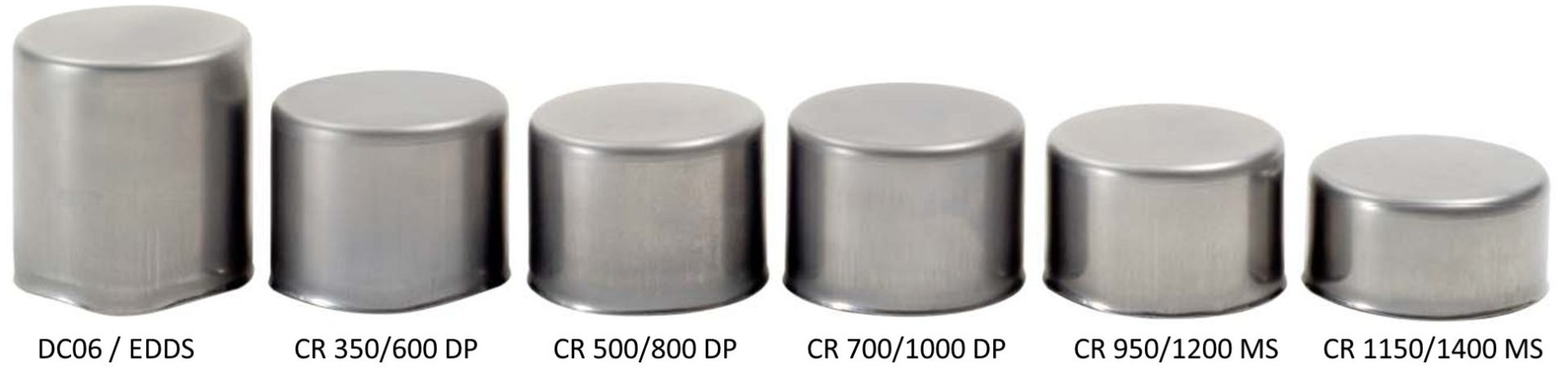
Figure 6: Cups used in the testing reported in Figure 5.S-26
Even though r-value is the only steel property influencing the formability of drawn flat-bottom cups through its relationship with LDR, not all cups have flat bottoms. Some have hemispherical or other configurations for bottoms. Adding a dome-like shape to the cup results in a more complex forming operation which is now sensitive to material properties like n-value and microstructures.
Corners of box-shaped stampings and the ends of closed channels contain design features similar to drawn cups, providing insight on an analytical approach.
- The four corners of a box-shaped drawn panel should each be analyzed as one-quarter of a cup. Buckles forming in the binder area indicate compressive flow. The corners of the blank will form the same as a deep drawn cup.
- The side walls are formed by metal flowing from the binder across the die radius. The term for this metal flow is bend-and-straighten.
In summary, higher LDR values are achievable in steels with greater values of the normal anisotropy ratio, rm. The absolute value of the LDR, however, also depends on the lubrication, blank holder load, die radius and other system inputs. Figure 7 compares a higher viscosity lubricant on the left with a lower viscosity lubricant on the right.S-26 Die radii need to be balanced: large radii promotes metal flow and may lead to wrinkles, while small radii restricts metal flow and may lead to splits.
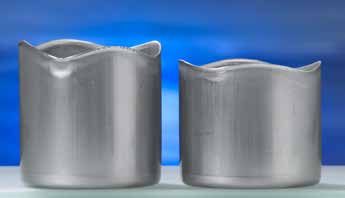
Figure 7: The influence of lubricant viscosity on drawing. The cup formed with the higher viscosity lubricant is on the left.S-26