Tooling
topofpage
Tool and die wear occurs due to the friction produced from the contact between the sheet metal and the tooling surface. Damage to the die surface can cause a gradual loss of tooling material, and scoring or burnishing damage to the sheet metal surface may be stress risers leading to premature failure in formed parts.
Impacting tool wear are the die material, strength of sheet metal, contact pressure, surface finish of the sheet and tooling, sliding velocity, temperature, coating of the die, and lubrication used. Advanced steel grades, where work hardening during stamping further increases the strength of an already high strength product, may result in additional die wear. Die wear beyond a critical point calls for replacement of the current die, impacting turnaround times and to production losses.
New die materials and better die coatings exist which minimize the impact of excessive tooling wear when forming AHSS. These new die materials include wrought and cast tool steels as well as powder metallurgy tool steels, which retain hardness without compromising the toughness of the material. Furthermore, hard material coatings and nitriding can improve the tribological properties of die surfaces.
Most tool materials for sheet metal forming are cast iron, cast steel, or tool steels.N-12 Cast iron grades used for stamping applications are gray cast irons (like G2500, G25HP and G3500) and pearlitic ductile irons (D4512, D6510, and D7003, among others). Cast steel grades include S0030, S0050A, S7140, and S2333. Tool steels include TD2 (a high wear / low shock resistant tool steel), TS7 (a high shock / low wear resistant tool steel) and TA2 (a balanced medium wear / medium shock resistant tool steel). These designations come from Reference NAAMS, with other designations in Citations A-37, A-38, I-11, J-7, J-8, J-9 Many of these designations overlap and represent the same or highly similar product. For example, ASTM A681 D2, JIS G4404 SKD11, and ISO 4957 X153CrMoV12 cover the same alloy tool steel.
In general, existing tool and die shop procedures to select the appropriate die material are applicable to select dies made to stamp Advanced High Strength Steels. However, the considerably higher strength level of these grades exerts proportionally increased load on the die material. AHSS grades might reach hardness values 4 to 5 times higher than mild steel grades. This is partially due to the microstructure of the sheet metal itself since some grades achieve higher strength from the microstructural phase martensite. Some martensitic grades (MS) have a tensile strength higher than 2000 MPa. This strength level corresponds to Rockwell C values higher than 57, meaning that the sheet metal hardness is approaching the tooling hardness.
The higher forces required to form AHSS require increased attention to tool specifications. The three primary areas are:
- Stiffness and toughness of the tool substrate for failure protection.
- Harder tool surface finishes for wear protection.
- Surface roughness of the tool.
The accepted amount of wear/galling between maintenance periods is a key factor in determining the performance requirements of draw dies, punches, and other tooling components. Some of the key elements that affect the die material specification include:
- The chosen sheet metal to be processed, as characterized by strength, thickness, surface coating, and surface profile (roughness and peak count).
- Die construction, machinability, radii sharpness, surface finish, and die hardness, specifically on draw beads and radii.
- Lubrication.
- Targeted cost per part.
Counteracting the increased applied load required to form AHSS grades is a potential reduction in sheet thickness. This thickness reduction leading to lighter weight parts is one of the key drivers promoting expanded use of Advanced High Strength Steels. Unfortunately, the reduced thickness of the steel increases the tendency to wrinkle. Suppressing these wrinkles requires higher blankholder forces. Any formation of wrinkles will increase the local load and accelerate the wear effects. Figure 1 shows a draw die with severe die wear due to excessive wrinkling on a DP980 part. It is not uncommon to replace these high wear areas with a more durable tool steel insert to minimize this type of excessive wear condition.

Figure 1: Draw die with significant wear due to excessive wrinkling on a DP980 part. S-45
Surface Hardening Treatments and Coatings
Surface treatments and coatings help increase tool life and reduce friction. Flame or induction hardening heat treatments, nitriding, and chrome plating are common surface treatment techniques used. However, each of these can fail under the high contact pressure that is present when stamping advanced high strength steels. Coating the inserts adds additional wear and friction benefits.
Many surface hardening options exist which improve the wear resistance.A-7 Carbon content limits the achievable surface hardness with either flame hardening or induction hardening. Tools hardened with either approach must be quenched after heating, which increases the risk of distortion. Laser beam hardening relies on the high thermal conductivity of underlying base tool steel to self-quench, which reduces the magnitude of distortion. Further minimizing distortion: the energy input in laser beam hardening is approximately 10% of flame hardening.
Carbon and nitrogen increase the strength and hardness of sheet steels. Similarly, carburizing and nitriding tool steels create a hard, wear-resistant surface layer. Carburizing is done at a higher temperature, which carries the risk of distortion. Nitriding takes primarily one of two forms: gas nitriding and plasma (ion) nitriding. Ion nitriding is faster than gas nitriding, accomplished at a lower processing temperature, and minimizes the thickness of the brittle “white layer.” A-39
Chrome plating of tools and dies has been an option to increase wear resistance, but may exhibit microcracking. Environmental concerns further limit its use. In addition, studies show that is it not the best option for tools used to form advanced high strength steels.Y-6
A high hardness, low friction coating results in a wear resistant surface that lowers the risk for galling. Coatings include titanium nitride (TiN), titanium carbide (TiC), titanium carbonitride (TiCN), titanium aluminum nitride (TiAlN) and chromium nitride (CrN). Common application methods are physical vapor deposition (PVD), chemical vapor deposition (CVD), and thermal diffusion (TD).
The strength of metallurgical bonds produced in the CVD and TD processes are greater than physical bond associated with the PVD approach. However, application of CVD and TD coatings occurs at around 1000 degrees C, which is likely in the austenite region of the tool steel. This high temperature can soften the die, which then necessitates a subsequent rehardening process, and may also cause dimensional distortion. For these reasons, several global automakers specify only PVD coatings.
The benefits of PVD coatings in reducing galling are apparent in Figure 2, which compares a cut edge after blanking of 200,000 parts of CR 500Y/800T-DP. Use of cutting steels with a PVD-applied TiAlN coating results in a cleaner, more uniform edge.
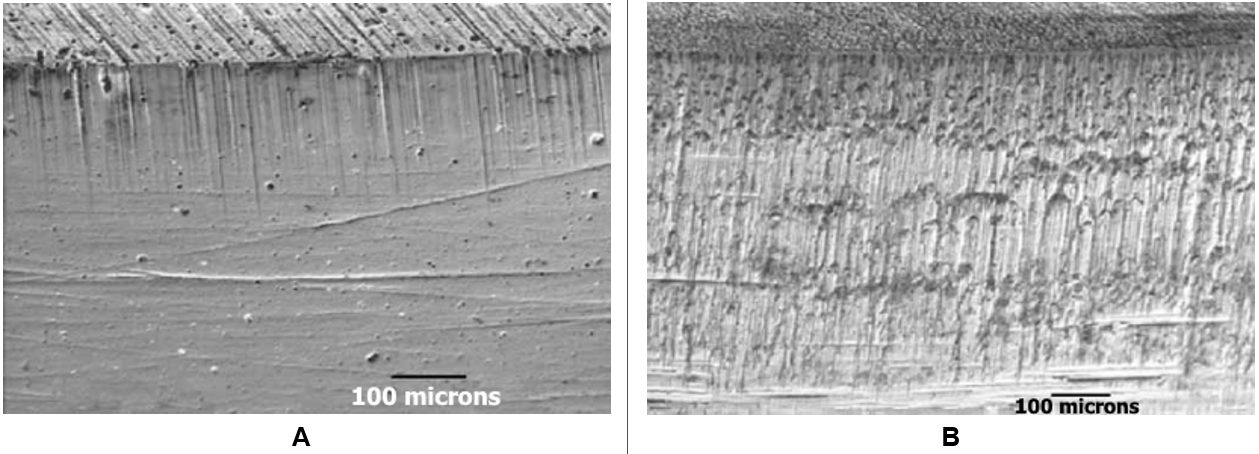
Figure 2: PVD-applied TiAlN-coated cutting steel (image A) reduces galling compared with an uncoated cutting steel (image B). Edges are shown after 200,000 parts produced from CR 500Y/800T-DP. T-20
Since coatings may crack, it is important that the substrate has sufficient hardness/strength to avoid even the slightest plastic deformation of the tool surface. Therefore, the recommended practice is to perform an initial surface hardening treatment, typically flame or induction hardening followed by ion nitriding, to develop substrate hardness and strength before applying the coating. Surface roughness must be as low as possible before coating, with average surface roughness (Ra) values below 0.2 μm recommended. This roughness level approximates a 600-grit sandpaper finish.
Considering the high cost of coated tool steels, a recommended approach is to construct large forming tools from relatively inexpensive and soft materials, such as cast iron or low-grade tool steel. Locations subject to severe wear are candidates for inserts of high-grade tool steels with an appropriate coating engineered for the application.
Ceramic tool inserts have extreme hardness for wear resistance, high heat resistance, and optimum tribological behavior, but have poor machinability and severe brittleness. Potentially offsetting the higher cost are reduced maintenance and increased productivity. While not commonly used, the ceramic tool inserts offer a possible solution to high interface loading and wear.
Select tool steel inserts for forming dies according to the sheet metal and the forming severity. These inserts should have a surface coating when processing DP 350/600 and higher grades. Initial tryout should be completed before coating, so that die adjustments and springback compensation efforts do not lead to removal of the newly applied coating. Allow for tooling recuts during this tryout loop to ensure the resulting tool has sufficient mass and stiffness. Different friction and metal flow conditions should be expected between the initially uncoated and the ultimately coated tool steels.
The optimal surface treatment may increase upfront cost, but will reduce the rework and die maintenance cost over the life of the die. Shown in the top two lines of Figure 3 are the benefits of plasma ion nitriding a flame hardened graphite-bearing cast iron tool (GGG70L) when forming 1 mm thick electrogalvanized dual phase steel. The bottom two lines show the effect on AISI D2 (DIN 1.2379 or JIS SKD11), highlighting only minimal tooling wear over the 5000 parts evaluated.

Figure 3: Plasma ion nitriding leads to reduced tool wear. GGG70L is a flame hardened spheroidal graphite-bearing cast iron and DIN 1.2379 is AISI D2 or JIS SKD11 cold work tool steel.T-11
Figure 4 compares the surface appearance of the same tool steel with different coatings. On the left is a chrome-plated tool which exhibited adhesive and abrasive wear, and ran for only 50,000 parts. Shown on the right is an ion nitrided tool steel which was chromium nitride coated using PVD, and produced more than 1.2 million parts.

Figure 4: Tool steel surface. Left image: Chrome plated, failed after 50,000 parts; Right image: Ion nitride tool steel, chromium nitride PVD coating, produced more than 1.2 million parts. J-10
Heat produced from stamping AHSS grades interacts with the tool material and coating, which may impact friction and metal flow. 1mm thick hot dip galvannealed CR340Y/590T-DP-GA was evaluated in a laboratory set-up.S-46 Initially at room temperature, die surface temperature increased to 65 °C (150 °F) after 10 cycles of passing this DP590 grade across a tool radius and significant zinc powdering occurred. Less powdering occurred with the use of a die coolant. Cooling the dies also helped to reduce the surface scoring and associated friction [Figure 5].
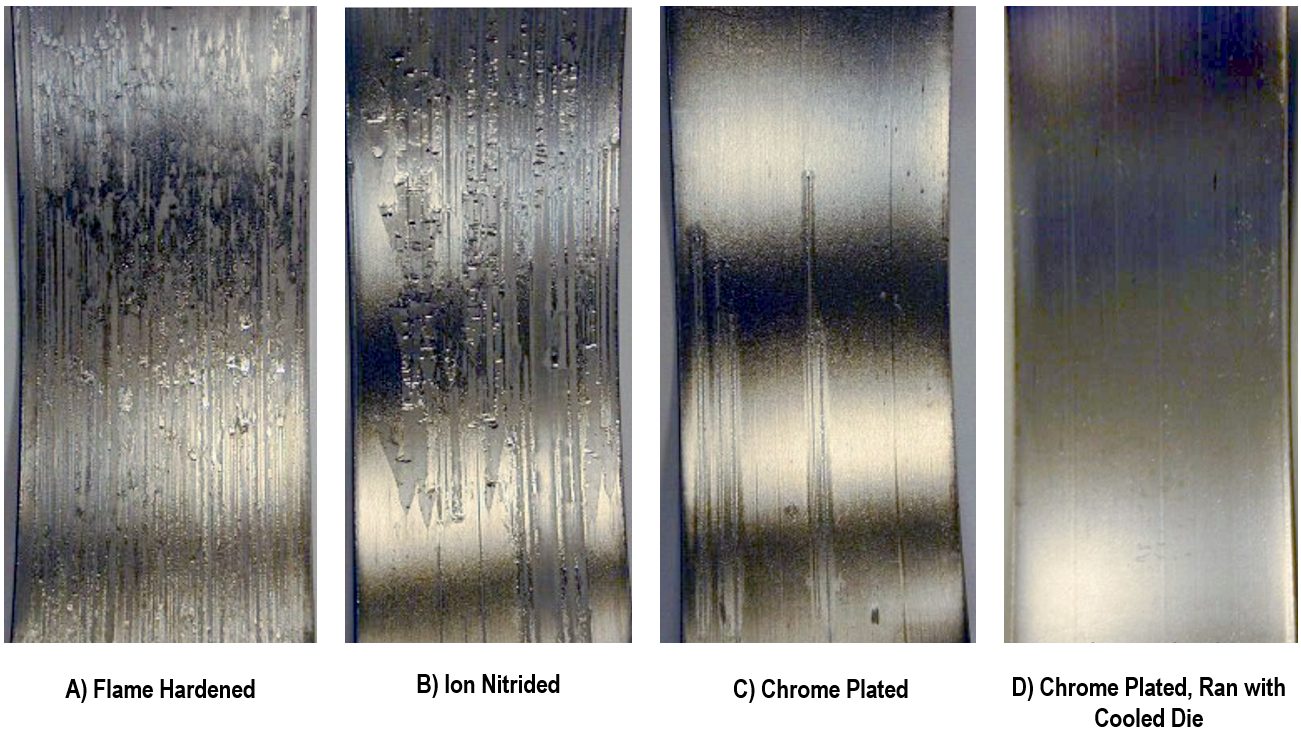
Figure 5: Coatings and Die Coolant on D2 Tool Steel Reduce Scoring and Friction with galvannealed dual phase steel. A) Flame Hardened; B) Ion Nitrided; C) Chrome Plated; and D) Chrome Plated with die coolant.S-46
Selection of tool steels for cutting, trimming, and punching tools have similar considerations as forming tools. The base tool steel must have excellent chipping and cracking resistance. Coatings will reduce tool wear. Hardening of the substrate prior to coating will minimize failure due to plastic deformation of the substrate. Coatings reduce the severity of the shock wave produced when cutting advanced high strength steels. See the Cutting / Blanking / Shearing / Trimming page for more information.
It is not advisable to use only one tooling solution for all Advanced High-Strength Steels. One study showed that die material and coating methods used in large volume production of steel grades up to and including those with 980 MPa minimum tensile strength were not suitable for forming a grade with 1180 MPa minimum tensile strength.W-18 Furthermore, this study recommends avoiding die materials such as ductile iron and low alloy cast steel when stamping 1180 grade steels.
In addition to selecting the correct die material, it must be processed appropriately. Figure 6 shows the effects of proper heat treatment when stamping a dual phase steel with 980MPa minimum tensile strength.S-45 This same study showed that a PVD coated tool performed best when forming a DP steel without a galvanized coating, yet the PVD coating led to significant zinc buildup when forming a galvanized DP steel. An ion nitride tool coating worked best for galvanized steels.
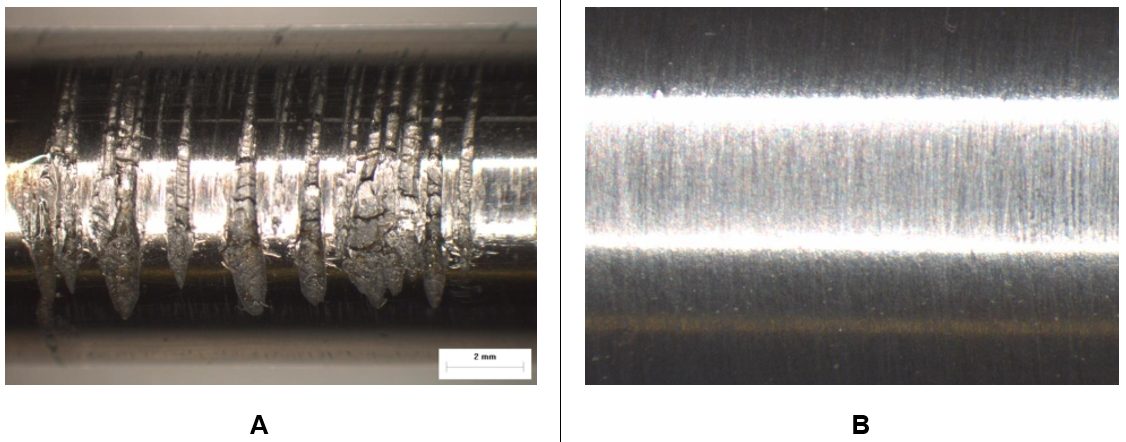
Figure 6: Effect of Heat Treatment on Tools to Stamp Dual Phase Steel. Image A) No heat treatment leads to wear; Image B) Proper heat treatment results in a surface without damage.S-45
There are five main types of cold work failure modes involving tool steels – wear, plastic deformation, chipping, cracking, and galling. There is also interaction between these failure modes. Figure 7 shows examples of these failure modes.T-20, U-7
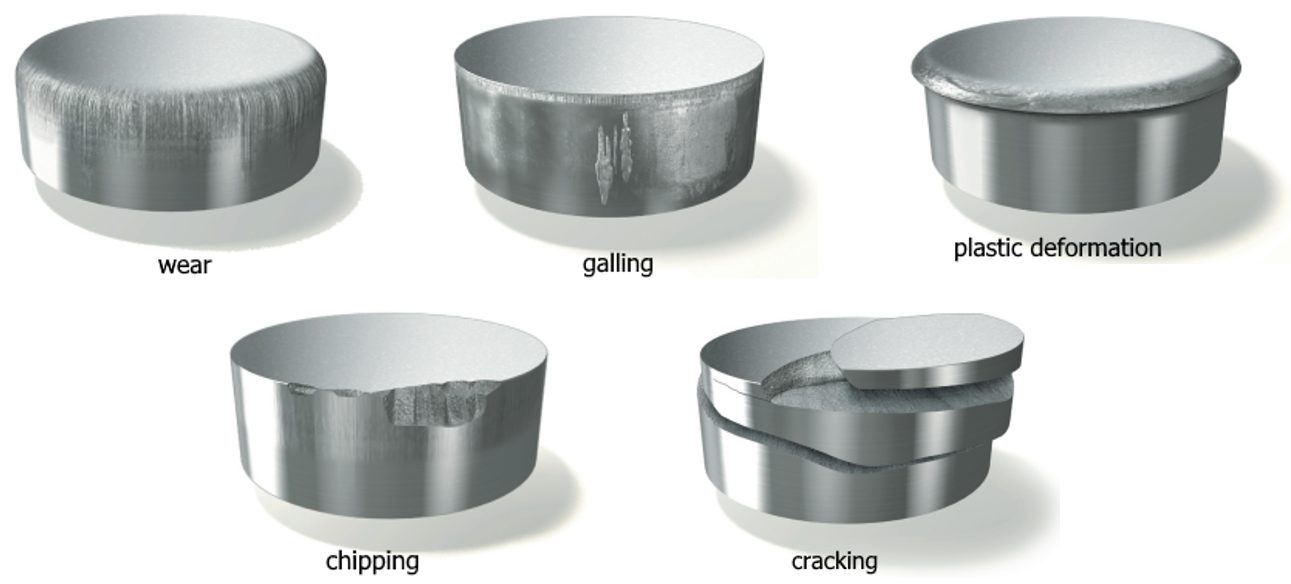
Figure 7: Stamping Tool Failure Modes. T-20, U-7
Wear is damage to the tooling surface resulting in material loss and is related to the tooling material hardness, and the type, volume, and distribution of hard particles like oxides or carbides. Wear can also be related to material type and process conditions and involves sliding contact between the tooling and the material. There are two types of wear: abrasive and adhesive.
Abrasive wear occurs when hard particles forced into a surface during the sliding contact leads to removal of metal from the tool steel. Tool steel properties promoting abrasive wear resistance include high hardness of the tool steel and of the carbides, as well as a high volume of large carbides. However, the high hardness targeted for wear resistance makes the material sensitive to notches. Large carbides act as crack initiators, increasing the risk of fatigue cracking.
Adhesive wear occurs with material transfer from one metal surface to another. The friction and heat generated as the sheet metal slides across the tool surface results in micro-welding between the asperities (peaks) on each surface. Failure of these micro-welds occurs with continued relative motion between the two surfaces, with small fragments torn from the weaker side surface and adhering to the other surface. The material ripped out of the tool steel will occasionally stick to the sheet metal surface. With continued metal motion, these pieces may score and damage the tool steel surface resulting in a combination of adhesive and abrasive wear known as mixed wear.
Galling is a physical/chemical adhesion of the sheet metal to the tool surface. The severity of the galling depends on the surface finish and chemical composition of the material and the tool steel and involves the friction and sliding contact between the tooling and the material. Galling, abrasive wear, and adhesive wear are related, and can be minimized through the use of proper surface treatments or coatings on top of a tool steel with high hardness (Figure 8).

Figure 8: Adhesive wear of the tooling leads to abrasive wear scratches on the DP600 sheet surface. Continued abrasive wear leads to galling of the sheet surface. Higher magnification images are shown on the bottom. G-18
Plastic deformation occurs when the stress from contact with the sheet metal exceeds the compressive yield strength of the tool material. A high hardness tool steel helps to avoid this damage.
Chipping occurs when the operating stress levels exceed the fatigue strength of the tool steel, typically found at sharp edges. Microcracks initiate in the high contact area of the tool surface, propagate, and ultimately result in pieces chipping out along edges or at corners. Chipping may initiate in areas affected by adhesive wear. Here, microcracks can nucleate, deepen, and spread, leading to a fatigue failure. A tool steel with high ductility has good chipping resistance, since microcrack initiation and propagation are more difficult.
Cracking occurs when the operating stress levels exceed the fracture toughness of the tool material. Crack formation occurs in the presence of stress concentrators, like grinding and machining marks or design features such as sharp corners or radii. Once the crack forms, unstable crack propagation leads to failure. Microstructural toughness promotes good cracking resistance, as does low hardness. However, low hardness has a detrimental effect on the resistance to the other failure mechanisms and is not normally a good solution.
Higher strength steels lead to greater demands on the wear resistance and mechanical strength of the tool material. Forming operations require high wear and galling resistance and compressive strength. Cutting operation require a combination of high wear resistance, high galling resistance, high compressive strength, high chipping, and total cracking resistance.
Tool materials must balance compressive strength and toughness with resistance to wear, thermal, and mechanical stresses.
Conventional highly alloyed tool steels are produced from large ingots. The slow solidification leads to microstructural segregation, forming large carbide networks which turn into carbide stringers after processing. These networks are beneficial for wear resistance, but reduces fatigue strength and toughness.
Alternate approaches minimizing segregation reduces these concerns. Two such production methods are electroslag remelting and powder metallurgy.T-20
Electroslag remelting (also known as electroslag refining, ESR) is a progressive melting process used to produce porosity-free ingots of uniform chemistry. Under a protective atmosphere, only a small portion of the ingot is liquid at any one time, and solidification occurs in a controlled manner. This processing approach results in tool steels with increased cleanliness, smaller carbides, and improved ductility and fatigue properties. It is relatively expensive, leading to its use in some specialized tool steel applications.
Rather than slowly solidifying in a large ingot, powder metallurgy (PM) production involves first atomizing a stream of molten metal using a high pressure inert gas, resulting in droplets that rapidly solidify into powder. Segregation is typically a fraction of the powder diameter, which is on the order of 100 μm. Hot isostatic pressing (HIPing) consolidates the collected powders, which is subsequently rolled or forged in a similar manner used for ingots.
Without the concern of macro-segregation or large carbides, the PM approach allows for manufacturing of more highly alloyed tool steels than is possible with conventional ingot metallurgy. Here, the carbides are smaller and more evenly distributed even compared with the ESR approach, leading to a balance of wear resistance and fatigue life. PM tool steels have enhanced resistance to abrasive wear, adhesive wear, chipping, and cracking. Coatings improve galling resistance.
Metal stampers and die shops experienced with mild and HSLA steels often have problems making parts from AHSS grades. The higher initial yield strengths and increased work hardening of these steels can require as much as four times the working loads of mild steel. Some AHSS grades also have hardness levels approaching the dies used to form them.
The higher stresses required to penetrate higher-strength materials require increased punch-to-die clearances compared to mild steels and HSLA grades. Why? This clearance acts as leverage to bend and break the slug out of the sheet metal. Stronger materials need longer levers to bend the slug. The required clearance is a function of the steel grade and tensile strength, and sheet thickness.
Increasing cutting clearance can result in punch cracking and head breakage due to higher snapthrough loads and reverse-unloading forces within the die. Adding shear angles to the punch face helps reduce punch forces and reverse unloading.
Tight cutting clearances increase the tendency for die galling and chipping. The severity of galling depends on the surface finish and microstructure of both the tool steel and work material. Chipping can occur when process stresses are high enough to cause low-cycle fatigue of the tooling material, indicating that the material lacks toughness.
Tempering of tools and dies represents a critical heat-treatment step and serves more than one purpose, but of primary concern is the need to relieve residual stresses and impart toughness. Dies placed in service without proper tempering likely will experience early failure.
Dies made from the higher-alloy tool-steel grades (D, M or T grades) require more than one tempering step. These grades contain large amounts of retained austenite and untempered martensite after the first tempering step and require at least one more temper to relieve internal stresses, and sometimes a third temper for even greater toughness.
Unfortunately, heat treatment remains a “black-box” process for most die shops and manufacturing companies, who send soft die details to the local heat treat facility, with hardened details returned. A cursory Rockwell hardness test may be conducted at the die shop when the parts return. If they meet hardness requirements, the parts usually are accepted, regardless of how they may have been processed—a problem, as hardness alone does not adequately measure impact toughness.
Consider this scenario: An automotive structural part has been in production for years as a conventional high strength steel with a minimum yield strength of 280 MPa, CR280Y350T-LA. In order to meet increasing global safety regulations, the automaker converts the part to a dual phase steel, CR340Y590T-DP. Even though these grades have relatively close minimum yield strength levels as produced at the steel mill, dual phase steels have excellent work hardening characteristics and are bake hardenable. These are among the reasons for their favorable response in crash events in comparison to HSLA grades.
The stamping location attempted to do a direct swap, substituting the DP steel for the HSLA grade with no changes to the part or process. Immediately after the grade change, scrap rates increased significantly. The failures were all determined to be local formability edge fractures; investigation revealed that the edge of the configured blank remained as the final product edge which split during forming and subsequent flanging. Examination of the edge revealed a burr as well as a non-uniform cut edge appearance. The tool showed signs of chipping.
Issues found, along with corrective actions:
- The tool steel used for HSLA (uncoated D2) was not appropriate for stamping DP590. Upgrade to a more durable tool steel with good chipping resistance. Add a surface treatment or coating if needed for additional wear resistance.
- The stamper used the traditional 10% tooling clearance when blanking HSLA. The recommended clearance for DP590 at the thickness studied is 15%.
- The flanging operation further expanded the edge beyond what occurred in the draw die. DP steels work harden to a much greater degree than HSLA steels. As such, stretch flanging a cut edge significantly increases the potential for edge fracture in this stronger product. Adding a metal gainer to the draw die ensures the flanging operation performs only bending and straightening, and does not further stretch a cut edge.
Making these changes to accommodate the new grade eliminated scrap from this process.
Upgraded Sheet Metal Forming (M-20)
Multi-phase steels are complex to cut and form, requiring specific tooling materials. The tooling alloys which have been used for decades, such as D2, A2 or S7, are reaching their load limits and often result in unacceptable tool life. The mechanical properties of the sheet steels achieve tensile strengths of up to 1800 MPa with elongations of up to 40%. Additionally, the tooling alloys are stressed by the work hardening of the material during processing.
The challenge to process AHSS quickly and economically makes it necessary for suppliers to manufacture tooling with an optimal tool steel selection. The following case study illustrates the tooling challenges caused by AHSS and the importance of proper tool steel selection.
A manufacturer of control arms changed production material from a conventional steel to an Advanced High-Strength Steel (AHSS), HR440Y580T-FB, a Ferrite-Bainite grade with a minimum yield strength of 440 MPa and a minimum tensile strength of 580 MPa. However, the tool steels were not also changed to address the increased demands of AHSS, resulting in unacceptable tool life and down time.
According to the certified metal properties, the 4 mm thick FB 600 material introduced into production had a 525 MPa yield strength, 605 MPa tensile strength, and a 20% total elongation. These mechanical properties did not appear to be a significant challenge for the tool steels specified in the existing die standards. But the problems encountered in production revealed serious tool life problems.
To form the FB 600 the manufacturer used D2 steel. D2 was successful for decades in forming applications. This cold work tool steel is used in a wide variety of applications due to its simple heat treatment and its easily adjustable hardness values. In this case, D2 was used at a hardness of RC 58/60.
While tools manufactured from D2 can withstand up to 50,000 load cycles when forming conventional steels, these particular D2 tools failed after only 5,000 – 7,000 cycles during the forming of FB 600. The first problems were detected on a curl station where mechanical overload caused the D2 tools to break catastrophically, as seen in Figure 9 below. Since the breakage was sudden and unforeseeable, each failure of the tools resulted in long changeover times and thus machine downtime.

Figure 9: Breakage seen in control arm curl tool made from D2, leading to premature failure. Conversion to a PM tool steel having higher impact resistance led to 10x increase in tool life.M-20
Since the cause of failure was a mechanical breakage of the tools, a tougher alternative was consequently sought. These alternatives, which included A2 and DC53® (a registered trademark of International Mold Steel) were tested at RC 58-60 and unfortunately showed similar tool life and failures.
Metallurgical analysis indicated that the failure resulted from insufficient impact strength of the tool steel. This was caused by the increased cross-cut that the work-hardened AHSS exerted on the curl. As an alternative material, a cold work steel with a hardness of 58-60, a tensile strength of about 2200 – 2400 MPa and high toughness was sought. These properties could not be achieved with conventional tool steels. The toolmaker used a special particle metallurgy (PM) tool steel to obtain an optimum combination of impact strength, hardness and wear resistance.
Particle metallurgy (PM) tool steels, due to their unique manufacturing process, represent improvements in alloy composition beyond the capabilities of conventional tool steels. Materials with a high alloy content of carbide formers such as chromium, vanadium, molybdenum and tungsten are readily available. The PM melting process ensures that the carbides are especially fine in particle size and evenly distributed (reference Table 1). This process results in a far tougher tool steel compared to conventional melting practices.

Table 1: Elemental Composition of Chosen Tool Steel
The manufacturer selected Z-Tuff PM® to be used at a hardness of RC 58-60. Employing the identical hardness as the conventional cold work steel D2, a significant increase in impact strength (nearly 10X increase as measured by un-notched Charpy impact values) was realized due to the homogeneous microstructure and the more evenly distributed precipitates. This positive effect of the PM material led to a significant increase in tool life. By switching to the PM tool steel, the service life is again at the usual 40,000 – 50,000 load cycles. By using a steel with an optimal combination of properties, the manufacturer eliminated the tool breakage without introducing new problems such as deformation, galling, or premature wear.
AHSS creates tooling demands that challenge the mechanical properties of conventional tool steels. Existing die standards may not be sufficient to achieve consistent and reliable performance for forming, trimming and piercing AHSS. Proper tool steel grade selection is critical to ensuring consistent and reliable tooling performance in AHSS applications. Powder metallurgical tool steels offer a solution for the challenges of AHSS.
- Areas seeing higher working loads require improved tool materials and coatings for both failure protection and wear protection.
- The higher initial yield strengths of AHSS, plus the increased work hardening of DP and TRIP steels can increase the working loads by 400% compared to Mild steels.
- Strength levels of some AHSS grades are associated with the same hardness as the tools intended to form them.
- Advanced powder metallurgy (PM) tool materials are appropriate for some AHSS applications.
- The dominant mode of failure of tool steels should be identified and communicated to the tool steel supplier to select the tool steel with the best properties to combat the tool failure mode for a given AHSS grade.
- PVD coated tool steels are appropriate for stamping AHSS grades without a galvanized coating but may result in zinc buildup when forming galvanized steels. Here, an ion nitride coating may be appropriate.
- Complete initial tryout before application of tool coating. Allow for tooling recuts during tryout loop to ensure the resulting tool has sufficient mass and stiffness.
- Proper selection of tool material, surface treatment, and coating leads to a reduction in maintenance, repair, and scrap/rework costs. Further offsetting the upfront tooling costs are improved process uptime, improved quality, and greater consistency.
Back to the Top
Hydroforming
Tube hydroforming creates complex shapes by using internal pressure to expand a tube against a die cavity. Frame rails, engine cradles, roof rails and bows, instrument panel beams, cross members, pillars, and seat frames are among the parts created using hydroforming. Benefits of this approach can include part consolidation, weight reduction, improved stiffness and strength, tighter dimensional tolerances, fewer secondary operations, and reduced cost compared with conventional stamping and welding approaches.
These benefits are highlighted in a truck front end structure shown in Figure 1, where hydroforming allowed for consolidation of 31 parts into 18, and resulted in a 31% weight reduction. M-67
Automotive body structures have incorporated hydroformed parts for several years, with recent vehicles using AHSS grades to improve crash energy management and impact performance. Some specific examples:
The hydroformed A-Pillar on the 2015 Mustang Convertible (Figure 2) distributes impact loads to the windshield header and the hinge pillar.M-16
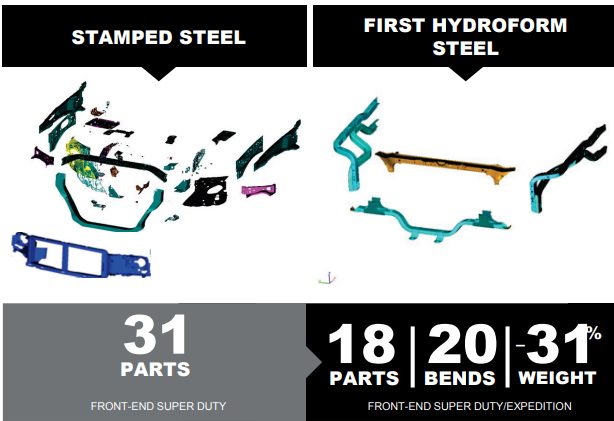
Hydroforming facilitates part consolidation and weight reduction relative to a stamped truck front end structure.M-67

Figure 2: 2015 Mustang Convertible: A-Pillar.M-16
The Door-to-Roof Support on the 2016 Nissan Titan XD (Figure 3) extends from the rocker/hinge pillar through the A-pillar and almost to the B-Pillar. Hydroforming this part from a Dual Phase Steel with 980MPa minimum tensile strength allowed for 25% section strength improvement allowing for thinner material at the same performance level. T-18, L-18

Figure 3: 2016 Nissan Titan XD: Door-To-Roof Support.T-18, L-18
The hydroformed Upper Load Beams of the 2017 Chrysler Pacifica (Figure 4) saved 1.8 kg per vehicle compared with a conventional approach.T-19

Figure 4: 2017 Chrysler Pacifica: Upper Load Beams.T-19
Each of the two hinge pillars on the 2019 Jeep Wrangler (Figure 5) contain 2 hydroformed tubes made from TRIP 400/690.B-8

Figure 5: 2019 Jeep Wrangler: Hinge Pillars.B-8
Tube hydroforming, as the name suggests, starts with a linear-welded tube, produces either with high frequency induction welding or laser welding. The tube is then bent to the general shape, and a pre-forming operation helps to put steel in the optimal position. After placing the preformed tube in the hydroforming die, end-plugs create a seal for subsequent internal pressurization. Figure 6 shows the changes to tube shape along the process of producing the hydroformed roof rails from DP800/1000 for the 2015 Ford Edge.H-13

Figure 6: Shape evolution to achieve a hydroformed roof rail from DP 800/1000.H-13
If the hydroforming process does not result in a change in the length of the pre-formed tube, then the only change is an increase in the local section diameter. This corresponds to a strain state of plane strain, which is the strain path associated with the greatest risk of cracks. Mounting the end-plugs on actuators allows for application of axial loads on the ends of the tube as the internal pressure changes. End feeding in this manner changes the strain state favorably, creating compression in the axial direction as the tube diameter stretches. With axial feeding, the strain state near the ends move to the left hand side of the Forming Limit Diagram, allowing for higher strains to be reached prior to failure – meaning that more complex shapes can be created. Away from the tube ends, the axial feeding has limited effect, so plane strain formability (the lowest point on the Forming Limit Curve) limits the product shape.
Formability is further limited compared with the incoming sheet, since the rolling, welding, sizing, bending, and pre-forming operations all decrease the available ductility prior to hydroforming. Understanding the effect of each operation which changes the strain and thickness in the tube allows for small process changes which may help to improve the amount of residual ductility for the subsequent tube hydroforming operation. The strains generated from each step results in the work hardening of the sheet steel, leading to an increase in strength and decrease in ductility.
Product and tool designs must account for these increased strengths and reduced formability parameters. The deformation available for the pre-form bend process and the subsequent hydroforming process will depend on the material selected, tube D/T ratio, tube manufacturing process, centerline radius of the pre-form bend, and the included angle of the bend. Tubes of higher strength AHSS will have limited elongation available. Avoid exceeding the available total elongation for bending limits or forming limits – especially in the work hardened areas of the pre-form bends. Refer to Figure 4 in the Tube Bending article for anticipated elongation values for several illustrative high strength steels formed into tubes of various D/T ratios.
The hydroforming process for tubes usually involves expanding the tube diameter from 3% to 30% depending on the design, materials selected and pressures available for forming. Tube production commonly utilizes one of three basic methods of hydroforming tubes, categorized by the internal pressure used for the expansion.
In high-pressure tube hydroforming, the tube is placed in the die and the die is closed. Pressurizing the tube now causes the metal to stretch as the circumference increases to conform to the inner circumference of the die – often with tight radii in corners and product features. Higher strength steels may be unable to expand sufficiently to fill the die geometry or create small radii without failure. Furthermore, high pressure could be necessary to obtain the correct geometry with minimum springback or fewer wrinkles compared to low-pressure hydroforming.
Low-pressure tube hydroforming begins with a tube whose circumference is slightly less than the final circumference of the finished geometry. Tube pressurization occurs after placing the tube in an open die, prior to closing. As the die closes, the circumference of the tube changes shape to conform to the closing die. The internal pressure is sufficient to prevent the tube from buckling during the shape change. A small circumference increase combined with a uniform wall thickness means that high strength and lower-formability metals can achieve tighter radii without failure. This low pressure process is suitable for tubes made from AHSS. This approach results in a change of the shape of the tube cross-section, rather than tube expansion.
A third process reduces the severity of circumferential expansion by using the end feeding approach previously described. Special end pistons push additional material into the die cavity from the tube end to provide more material for higher expansion of the tube circumference. This method of tube circumference expansion involves bi-directional strain. The end feeding is beneficial for hydroforming tubes from AHSS. Note that excessive end-feeding may increase the pressure required to form small corner radii.S-43
To assist with pre-production process and die design, computerized forming-process development is an excellent tool for examining the validity of applying different AHSS to potential part designs. However, proper inputs are critical: hydroforming tubes made from advanced high strength steels require highly developed forming limit curves generated which consider different tube D/T ratios, degrees of pre-form bend, and final geometrical shape. Each step as the straight tube is converted to a hydroformed part represents a non-linear strain path, which increases the importance of using the proper Forming Limit Curve. The FLC generated for the initial sheet steel will give a false indication of the available formability since it does not account for the impact of the forming steps prior to hydroforming.
An example of the material property changes from tube creation comes from Figure 7, which compares 1.88 mm thick mild steel (labeled as DDQ), HSLA 350/450, and DP 350/600 formed into a 76.2 mm (3 inch) diameter tube. Figure 7 shows the summary of average properties for the three steels. The much larger jump associated with tube forming of the dual phase steel grade is associated with the higher n-value of this product.

Figure 7: Strength Comparison on samples taken from the flat sheet and after tube forming.S-43
For trimming and piercing, the same general cautions utilized for stamped AHSS parts apply to hydroformed AHSS parts. Since Advanced High Strength Steels have higher tensile strength than conventional high-strength steels, engineering the trim tools to withstand higher loads is a requirement. Proper support for the trim stock during the trim operation will minimize edge cracking. Laser trimming, which is common for hydroformed parts, is still an excellent choice. However, the trimmed edge may see some hardening associated with the local heating and cooling from the laser beam.
Design Considerations
In general, the same design guidelines that support hydroforming of conventional steels apply to AHSS. However, consideration of part function and the available elongation for forming is necessary during development of the part design and manufacturing processes.
- Hydroforming tools need to be stiff and rigid in all directions, or else there is the risk of deviation from the targeted.
- Springback and shape distortion is more likely on longer tubes made from thinner sheet steels. Tight bending radii on higher strength steels increases the risk of springback. The tube diameter to wall thickness (D/t) ratio, cross section shape, forming process (bending, preforming method, hydroforming parameters) also affects springback.
- Pierce holes in the tube by cutting against the water pressure.
- Place welds in areas with low forming strains.
- The cross section can change, but the circumference should stay the same to minimize cracks.
- Avoid sharp radius/thickness due to forming forces.
Industry 4.0 and AHSS Applications
The manufacturing industry is currently experiencing a significant transformation of digitalization, connectivity, and higher flexibility of the manufacturing process. Recently, several studies were conducted by different researchers and companies on developing more complicated control systems with new sensors and applying a machine-learning algorithm to analyze the collected data from the sensors. Therefore, an extensive literature review was conducted to address the applications of Industry 4.0 (sensor, process control, and forming equipment control) for sheet metal forming.
This article introduces the latest information and provides insight on how to practically implement newly introduced technologies and tools for industrial sheet metal forming processes to make the forming processes more efficient and robust.
Needs for Industry 4.0 in Manufacturing
Manufacturing processes have become more efficient and productive with help from smart machines, intelligent systems, and data analytics. This rapid change in manufacturing leads to a new industrial revolution, frequently called Industry 4.0.
Industry 4.0 has been defined as “a name for the current trend of automation and data exchange in manufacturing technologies. It includes cyber-physical systems, the Internet of things (IoT) and cloud computing and cognitive computing and creating the smart factory”.I-17
Three key factors — connectivity, intelligentization, and automation (Figure 1) — characterize this new industrial revolution. The combination of these factors changes conventional production to a more customized, flexible, and on-demand manufacturing production, creating significant technical challenges.Y-13 To overcome these challenges, the integration of the three key factors highlighted in Figure 1 becomes essential for the manufacturing industry.
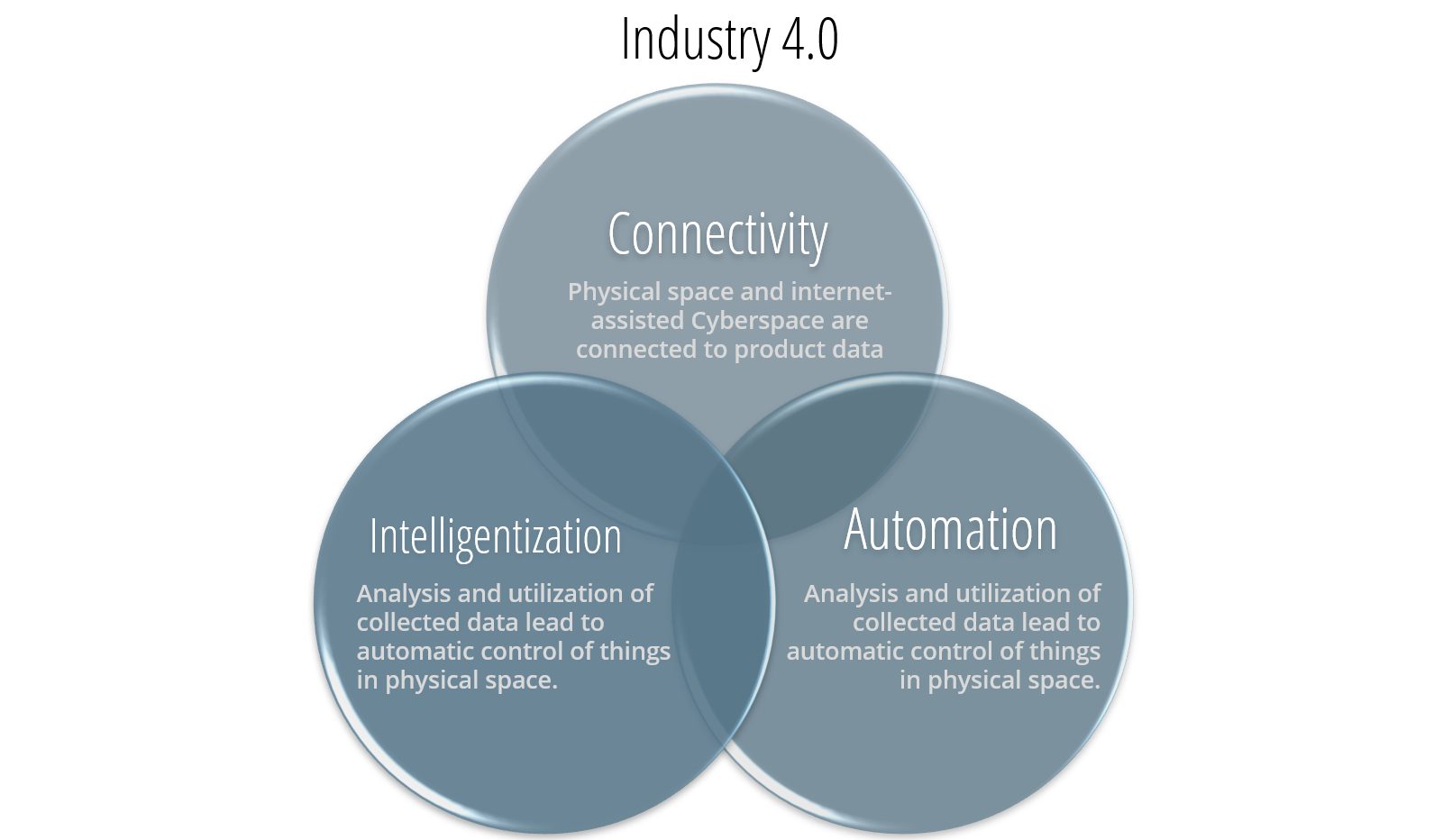
Figure 1: Key factors for Industry 4.0.Y-13
There is interest in the sheet metal industry on how to adopt Industry 4.0 into their legacy forming practices to significantly improve productivity and product quality. Figure 2 illustrates four important variables influencing the part quality: material properties, die friction response, elastic deflection of the tool, and press dynamic characteristics. These variables are usually difficult to measure or track during the production runs. When these variables significantly influence the part quality and the scrap rate increases, the operators manually adjust the forming press parameters (speed and pressure), lubricant amount, and tooling setup. However, these manual adjustments are not always possible or effective and can be costly for the increased part complexity. The use of new advanced high-strength and light-weight materials often escalates technical challenges associated with formability and robustness of the current forming process as well.

Figure 2: Important variables influencing the stamping quality.H-35
The ultimate vision for Industry 4.0 in sheet metal forming is an autonomous forming process with maximum process efficiency and minimum scrap rate. This is very similar to the full self-driving (FSD) vision of the electric vehicle today.
The workflow of the current forming process starts by supplying the incoming coil or blank to the forming press where the material is formed and ends with the inspector assessing the part quality manually (Figure 2).K-27 Implementing Industry 4.0 technology will significantly change the workflow of the future forming process as illustrated in Figure 3. More sensors will be used to measure and monitor the variations of the incoming material, gauge, lubricant, temperature, and part quality. The digital data from the sensors will be analyzed using the data analytic method such as ‘machine learning’ and ‘deep learning.’ The analyzed data will be used to create a digital twin model or an algorithm for intelligently controlling the machines such as the part transfer system, forming press, and quality inspection robots. Likewise, the electronic vehicle progressively evolves in different levels of the FSD. In the early development stage, the prediction results of the artificial intelligence (AI) model will be checked and implemented by the machine operators for controlling the machine. When the AI model is sufficiently trained with the enormous production data, the autonomous forming process will be developed. This will be valuable for the automotive industry that has to process large production volumes with various steel grades. For example, the automotive industry increasingly experiences variations of the incoming material properties for Advanced High-Strength Steel (AHSS) and the significant effect on part quality associated with necking, wrinkling, and cracking, which drastically increases the production cost.

Figure 3: Comparison of the workflow of the current and future forming process with Industry 4.0.K-27
State-of-Art Sensors, Process Control, and Machine Control
Sensors for sheet metal forming: In-line monitoring of the incoming material properties using NDE sensors
The variation of the incoming material properties increases uncertainty in sheet metal forming by decreasing the consistent quality and increasing the overall manufacturing cost. A nondestructive evaluation (NDE) can be a useful tool to measure incoming material properties.
There are several types of NDE sensors. Most of the sensors need further development or are not suitable for production applications. However, some of the NDE sensors, such as the eddy current tools, laser triangulation sensors equipment, and equipment developed by Fraunhofer called 3MA (micromagnetic, multiparametric microstructure, and stress analysis), have already been applied to a few limited production applications. These sensors can be used to provide data during production to select the optimal parameters. They also can be used to obtain material properties for finite element model (FEM) analysis. Studies in deep drawing of a kitchen sink production used a laser triangulation sensor to measure the sheet thickness and an eddy-current sensor to measure the yield strength, tensile strength, uniform elongation, elongation to break, and grain size of the incoming material. The material data is used as an input for simulations to generate the metamodels to determine the process window, and it is used as an input for the feed-forward control during the process.K-27 Figure 4 shows how NDE tools are used for feed-forward controls and cameras for feedback control to determine the optimum press setting on sink forming production.

Figure 4: Process control for sheet metal forming of kitchen sink production.H-36
Another study proposed the use of Fraunhofer’s 3MA equipment to determine the mechanical properties of incoming blanks for a sheet forming process. The 3MA sensor correlates the magnetic properties of the material with the mechanical properties and calibrates the system with the procedure outlined in Figure 5. The study showed a good correlation between the measurements from the sensor and the tensile testing results; however, the sensor should be calibrated for each material. Also, the study proposed to use a machine-learning algorithm instead of a feed-forward control to predict the most effective parameters during the drawing process.K-28

Figure 5: Calibration procedure for 3MA sensors.K-28
Sensors for sheet metal forming: Real-time monitoring of part quality
Many researchers studied the control of the material flow by measuring the draw-in since the strain field of the blank is directly related to the failure. However, it is difficult to measure draw-in over the entire blank during the process so few locations on the blank can be measured. Figure 6 shows various sensors to monitor and control the material draw-in during forming. An extensive list of sensors applicable to metal forming was introduced.P-23

Figure 6: Sensors to monitor (left) and actuators to control (right) material flow and drawn-in for sheet metal forming.A-57
Sensors for real-time monitoring of part quality: Linear variable differential transducer (LVDT)
A LVDT was used to measure the material draw-in (sensor j in Figure 6 – double clicking the image will open it in a new window for ease of reference). However, it has several limitations. First, additional effort is needed for initial setup and maintenance in service which is difficult to apply for stamping productions that are exposed to tool vibration and tool temperature change. Secondly, they are not reliable if splitting or cracking occurs in the process. Finally, when the edge of the blank starts to wrinkle, the sensor could lose the edge and the measurement will be incorrect.L-33, M-29
Sensors for real-time monitoring of part quality: Roller-ball sensor
The roller-ball sensor (sensor b in Figure 6) is a computer mouse-type draw-in sensor based on a rotatory contact between the blank and the sensor. This sensor can measure the direction of the material flow; however, the contacting ball and roller might have wear issues, which can lead to incorrect measurements and high risk of any dirt contaminating the roller-ball contact surfaces. The roller-ball sensors are integrated into the tool, which increases the maintenance and development cost.L-33, M-29
Sensors for real-time monitoring of part quality: Inductance-based transducer
An inductance-based transducer sensor was developed to measure the draw-in during the forming process (Figure 7).M-29 This non-contact sensor has a thick cover of epoxy, protecting it from wear. It is also relatively easy to use and has a low cost. However, it must be calibrated for each material and the measurement error can increase considerably if wrinkling occurs during the forming process. Same as the roller-ball sensor, the inductance-based transducer is integrated into the tool, which increases the maintenance and development cost.

Figure 7: Principle of the inductance-based transducer sensor.M-29
Sensors for real-time monitoring of part quality: Vision sensor
A non-contact in-line sensor was developed to measure the material flow of a deep drawing process.D-25 This sensor has no risk of wear because it is non-contact. This sensor also detects the material flow direction. However, the sensor is integrated into the tool, thus there is a risk of degrading the performance of the sensor due to contamination on the lens with dirt and oil.
Cameras have been used to measure the draw-in between a 2-step drawing process of sink production.F-22 Cameras have a great advantage to measure material draw-in compared with other sensors because they are not integrated into the tool. For example, cameras can be used in different dies to measure the draw-in of the edge of the blank as shown in Figure 8. However, the draw-in cannot be measured continuously while the die is closed. It can only be measured after the die is opened and before the part is transferred to the next station. This is still an in-line control because it allows the adjustment of the planned schedule during the production. Nevertheless, for a single drawing stage process, it is an off-line close-loop control since it only allows adjustment between parts.

Figure 8: Image of the draw-in measurement taken with a camera.F-22
Similarly, a machine vision system with four cameras was used for real-time monitoring of the stamping part quality immediately after the die opened as shown in Figure 9.K-29 The system is capable of not only capturing the part quality with multiple images but also measuring the flange draw-in length of the part.

Figure 9: Real-time monitoring of the stamping quality using camera system.K-29
Sensors for real-time monitoring of part quality: Piezoelectric sensor
Piezoelectric sensors were used to measure the structural deformation of the punch corner as a result of part wall stresses.B-38 A closed-loop control system with part wall stress was proposed as a state variable. The part wall stress correlates directly with the strain distribution of the part, which is directly related to quality and failure. Multiple sensors must be located within the die or punch structure 10 or 15 mm below the contact surface; therefore, its implementation is complicated and expensive.B-38
Sensors for real-time monitoring of part quality: Wrinkling sensor
Opposing linear transducers were used to measure the wrinkle heightL-33 as shown in Figure 10. A closed-loop control sheet forming process was developed by measuring the wrinkle height with two linear displacement transducers positioned in the upper and lower binders. However, this sensor has two important limitations. First, the change in the blank thickness induces errors in the height measurement. Second, the sensor is limited to use for specific applications because failures can occur with the friction at the sensor tip that contact the blank and the sensor, and the sensor cannot detect wrinkles in the local area where it is mounted.

Figure 10: Opposing linear transducers for measuring wrinkle height.L-33
Forming Process Control
In the sheet metal forming industry, demand for high quality and cost-effective production is constantly growing. However, there are several uncertainties in forming that affect the robustness and reliability of the process. Some of these uncertainties are, for example, the variations of the incoming material properties and thickness, and die friction. One way to achieve a more robust production is to eliminate or reduce these variations, like, for example, improving the prediction of the material composition to reduce properties variations. However, this approach is not economical and not even possible in some cases. The other approach is to measure and compensate the uncertainties with feedback closed-loop control.
In the last two decades, several closed-loop control approaches have been developed to overcome these uncertainties in forming, to improve the quality of parts, and make the process more robust. Most of the effort has been on adjusting the blank holder force (BHF) and were proven successful in the laboratory environment; however, the feasibility of the proposed ideas was not proven for industrial applications.
The control and monitoring of process variables in sheet metal forming are essential to improve the quality and reduce the cost and time. Therefore, most studies focused on controlling different process variables such as punch force, punch speed, and blank holder force in sheet metal forming processes.
Control of Process Variables: Punch Force
The punch force is a process variable that is directly involved with failure. Many studies were conducted in monitoring and controlling the punch force during the 1990s and beginning of the 2000s.M-30,H-37 Today, most commercial presses have a built-in loadcell to measure the punch force during stamping. Therefore, the control of punch force is relatively easy to implement; however, its control in most applications is not enough to overcome all the uncertainties of the processes.
Control of Process Variables: Blank holder force (BHF)
Several studies showed the effectiveness of BHF control in sheet metal forming based on the measured or predicted material flow and draw-in. Previous studies on improving the actuators of the blank holder accurately implemented the desired BHF changes during the stroke with a Proportional–Integral–Derivative (PID) controller. This can be beneficial for reducing wrinkling and tearing by applying a uniform force around the binder.O-9 More recent studies used fuzzy control algorithmsM-31, artificial neural networksM-32, and more sophisticated controllers to improve formability. The draw-in data was used in a conventional closed-loop controller to adjust the BHF (Figure 11) and was suggested to integrate these empirical results in a fuzzy controller in the future.D-25

Figure 11: Block diagram of the closed-loop control system with an optical sensor.D-25
A controller based on classical state space control theory and time series was introduced to control the magnitude and distribution of the BHF.E-5 A unique blank holder plate with four cavities was designed to adjust contact pressure to locally change the BHF in one specific area (Figure 12). Experimental results showed that the novel feedback control system was able to eliminate process instabilities, such as tearing. Tearing happened consistently in an open-loop process, but it was avoided when the novel feedback control was implemented in the same process. However, the study also found that the reaction speed of the system is not fast enough for typical stamping production rates.

Figure 12: Block diagram of the closed-loop control (left) and schematic of the blank-holder plate with adjusted cavity pressure (right).E-5
In stamping, the forming speed can be changed by programming different strokes per minute (SPM) in the press. Depending on the tool design, the speed of either the punch or die can be altered with different SPM inputs. Most stamping presses output the value of SPM and depending on whether it is a mechanical or hydraulic press, the forming speed can be estimated with the SPM value. A faster forming speed can give larger productivity of the stamping process. However, it can also influence the material formability and heat generations on the tool, particularly for high-strength steel. Therefore, the forming speed is usually determined considering the press capacity (i.e., available mechanical energy), lubricant behavior, and sheet materials (gauges and strength). A novel study used intelligent technology to process the control and optimization of a deep drawing process.M-31 A new punch speed and BHF in-line fuzzy control (Figure 11) increased the productivity of the process with a 25% reduction of the cycle time.
Control of Process Variables: Part Wall Stress
A closed-loop control system with part wall stress as a state variable was used.B-38 A piezoelectric sensor was used to measure elastic deformation of the punch corner as a result of the part wall stresses. A tool was equipped with a segmented elastic blank holder with 10 hydraulic pistons that control the blank holder pressure in each segment using a proportional-integral (PI) controller. Figure 13 shows the block diagram of the closed-loop control loop, where y(s) is the reference part wall stress, w(s) is the input of the feedforward controller, u(s) is the hydraulic piston’s pressure, and s is the punch displacement. This closed-loop control showed higher robustness to disturbances, such as the incorrectly positioned blank that caused wrinkling or tearing on conventional processes compared to a conventional deep drawing process by increasing the possible draw-in depth and producing successful parts.

Figure 13: Closed-loop control using the part wall stress as a state variable.B-38
Feedback control vs. Machine-learning control for sheet metal forming processes
Several studies have been recently conducted to improve the quality and robustness of a deep drawing kitchen sink production. These studies have implemented a feed-forward and feedback control successfully, improving part quality significantly. The block diagram of the process is shown in Figure 14. First, the feed-forward control is used to gain knowledge about the blank to reduce the uncertainties of the incoming material. NDE sensors were used to measure the variations of the incoming material properties. Second, the feedback control is used to compensate for the other non-measurable uncertainties. Cameras were used to measure the draw-in of the part between the first and second drawing stages of the 2-step forming process. A PID controller is used to control the press setting during forming, where the process variable is the draw-in of the blanks. This control approach integrated with FEM, stochastic simulations, metamodels, and new and sophisticated intelligent data processor systems has considerably improved the robustness of small to medium batch productions.H-35, F-22, F-24, F-25, F-26, F-27

Figure 14: Block diagram of closed-loop control with feed-forward and feedback controls for sheet metal production.H-36
An intelligent system known as “Q-Guard” was introduced to link the product and process design to production, covering the entire production process from the raw material to the final product.H-36 Stochastic simulations were used to generate metamodel to obtain the process window for the control system. The block diagram of the Q-Guard system is given in Figure 15.

Figure 15: Schematic of the Q-Guard intelligent control system.H-36
Recent advances in servo presses have the potential to expand the capability of close-loop controls in sheet metal forming. Servo presses have more flexible slide motions and more precise control compared to conventional presses, allowing new combinations of more sophisticated motion of the press slide and BHF control. Servo presses have many features that have a positive impact on different forming applications. First, they have a flexible slide motion. The slide motion can be modified to follow different numerical control servo programs shown in Figure 16. A recent study has shown that using different servo motions can drastically improve part quality in production. The servo motion was chosen based on the variation of the incoming material properties.K-28 Also, a flexible slide motion can improve production productivity and make it more consistent. Second, the die cushion can vary the BHF and back-pressure loads during a sheet forming process. Finally, internet-of-things (IoT) tools and artificial intelligence (AI) can be combined with the control systems of the servo press to manage the machine conditions or parameters. A possibility is to combine IoT and AI with a monitoring system to predict and manage maintenance needs.K-30

Figure 16: Slide servo press motion examples (a) normal, (b) coining, (c) step, and (d) pulse.K-30
Industrial Applications for stamping AHSS/3rd Gen steels
The effects of the incoming material properties for part quality were investigated in a study which analyzed bake-hardenable 210Y/340T steel and a 3rd Gen steel with 980 MPa minimum tensile strength using a 300-ton servo press and the cross-form tool as shown in Figure 17.K-28 Samples from three coils each of 0.75mm BH340 and 1.2mm 980 3rd Gen were obtained from the same steel mill and tested. The results indicated the variation of the incoming material properties can significantly influence the part quality. A servo press is also capable of adapting to this variation by implementing an advanced slide motion or conventional crank motion to obtain consistent quality parts depending on the strength and formability of the sheet materials.

Figure 17: The cross-form test tool operated with a 300-ton servo press (left) and the machine vision system for inspecting the part quality (right).K-28
Industrial Applications for stamping of the body panels in the transfer press line
Recently, six different sensors and machine vision systems were applied to an automotive transfer press line in the US.R-13 These sensors are monitoring the blank properties, blank dimensions (width and thickness), lubricant oil film thickness, and the draw panel geometry and quality as shown in Figure 18. The sensor data can be used for data analytics for feedback to control the die cushion and lubrication system.

Figure 18: Applications of various sensors and camera system for the transfer press line.R-13
Industrial Applications for hot stamping of PHS
The automotive industry is adopting the use of press-hardening steels (PHS) in vehicle structural components to maximize crashworthiness. In the hot stamping process, press hardening steels are initially heated to 900°C in the furnace, and the heated blank is transferred to the forming press. The die immediately closes and keeps the part under pressure for 5 to 10 seconds for quenching by circulating water through the cooling channels inside the die. In this thermal-mechanical process, precise control of the blank temperature and time is essential to obtain the ultra-high-strength part up to 1,500 – 2,000 MPa tensile strength. Various vision sensors and thermal cameras are applied for the hot stamping production line as shown in Figure 19. The data from the sensors and cameras are used for controlling the press machine and transfer system. It is expected that a machine-learning control algorithm will be implemented with these sensors for hot stamping production shortly.K-29

Figure 19: Application of the thermal sensors and camera system in hot stamping production.K-29
Key Points
The sheet metal forming industry is implementing Industry 4.0 practices to stay competitive and overcome the production challenges of forming new AHSS and more complex part geometries. In summary:
- Industry 4.0 is being adopted in sheet metal stamping process.
- The incorporation of Industry 4.0 practices using in-line sensors and process control has improved the productivity and product quality in the sheet metal forming industry.
- The development of the draw-in sensors has significantly improved part quality as well as the robustness of the forming process.
- Sensors that are embedded in the tool have several limitations for industry application because of high maintenance cost.
- Cameras can be used to measure the draw-in with more flexibility than sensors embedded in the tool.
- NDE tools can be used to measure the variation of the incoming material properties and reduce the scrap rate.
- Fuzzy control algorithms, artificial neural networks, intelligent control software, and more sophisticated controllers can be used to improve the quality of the parts; however, some control systems are not fast enough for production rates.
- The implementation of new intelligent systems to control parts for the entire production process will lead to more efficient, consistent, and robust production. These systems include Q-Guard control, machine learning, and artificial networks.
- Servo-motor presses have several competitive advantages over conventional hydraulic and mechanical presses for closed-loop controls in sheet metal forming in terms of the more options for the machine control.
- As introduced with the case studies of this report as well as the literature, Industry 4.0 technology have been implemented in applications such as cold stamping of AHSS structural members and mild steel closures, as well as hot stamped parts, all of which consistently obtains high-quality panels.A-58
Back To Top
Coil Processing
Steel production and processing are continuous operations where the last step is coiling. Steelmakers and processors use tension when coiling to avoid producing “soft” or collapsing coils. Coiling induces tensile and compressive stresses into the strip, and these stresses can contribute to blank or part distortion in subsequent processes. Unless sufficient winding tension adjustments are made, the degree of these stresses change throughout the coil – whereas the outer laps of the coil may be on the order of 6 feet (1800 mm) in diameter, the inner laps typically are wound on a 20 inch to 24 inch (500 mm to 600 mm) diameter mandrel. In addition, the magnitude of these stresses increases with higher strength products, leading to coil shape imperfections like coil set and crossbow.
Coil set is a bow condition parallel with the rolling direction, and curves downward in the same direction as the upper outside lap of an overwound coil (Figure 1a). Here, the top surface of the coil or strip is stretched more than the bottom surface, and typically becomes more severe as the coil is processed and the lap diameter decreases. Crossbow is a bow condition perpendicular to the rolling direction, and curves downward in the same direction as the upper outside lap of an overwound coil, with the center portion of the sheet raised a measurable amount above the sheet edges (Figure 1b).
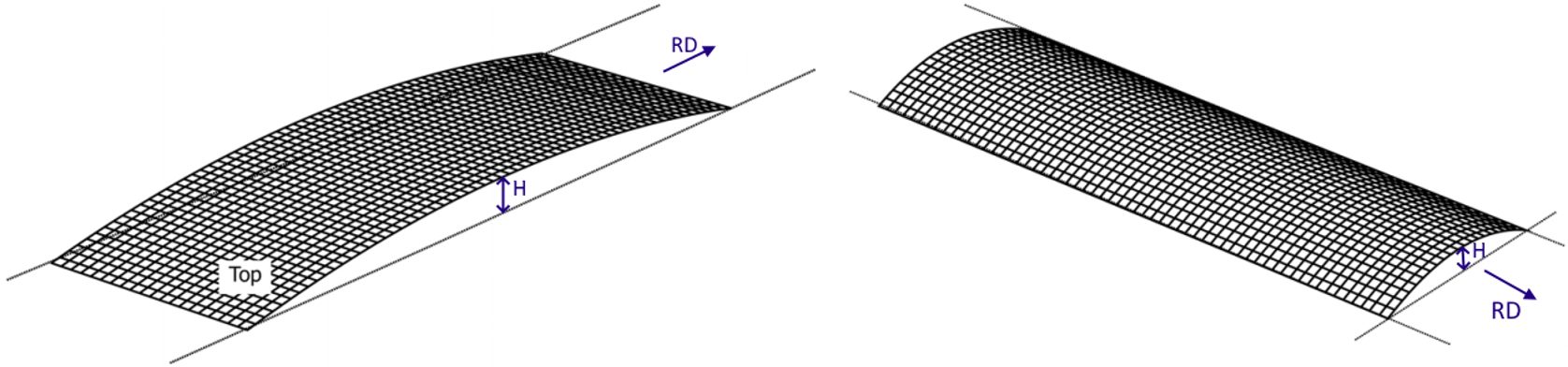
Figure 1: Coil shape imperfections – A) Coil set and B) CrossbowA-30
The first operation when unwinding a coil is some type of shape correction to ensure flatness before further processing. There are two main types of equipment used to create a flat coil – a straightener and a precision leveler. While these two types of equipment are similar, a precision leveler has additional capabilities. Both bend the coil back and forth over a series of work rolls to alternately stretch and compress the upper and lower surfaces (Figure 2). Critical equipment parameters include roll diameter, roll spacing, backup rolls, roll material type, gear design, backup rolls, overall system rigidity, and power requirements. The amount of force required to relieve the residual stresses is a function of the sheet thickness and yield strength. Equipment sufficient for shape correction on conventional grades may not be sufficient to completely flatten the advanced steel grades available now and in the future.
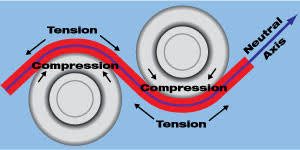
Figure 2: Alternately stretching and compressing the upper and lower sheet surfaces by passing the coil through work rolls.C-8
Straighteners and levelers have a series of rolls that progressively flex the strip to remove the residual stresses. Each successive roll pair has an adjustable gap to deform the sheet to a targeted amount with the goal of resulting in a flat coil once the steel passes through all the rolls. The entry end has the smallest gap, putting in the most deformation. The last pair of rolls has the largest gap, usually set for metal thickness. The gap profile varies based on thickness, yield strength, and equipment (Figure 3). Many equipment manufacturers have generated tables to guide the operator as to the best settings for various yield strength/thickness combinations.
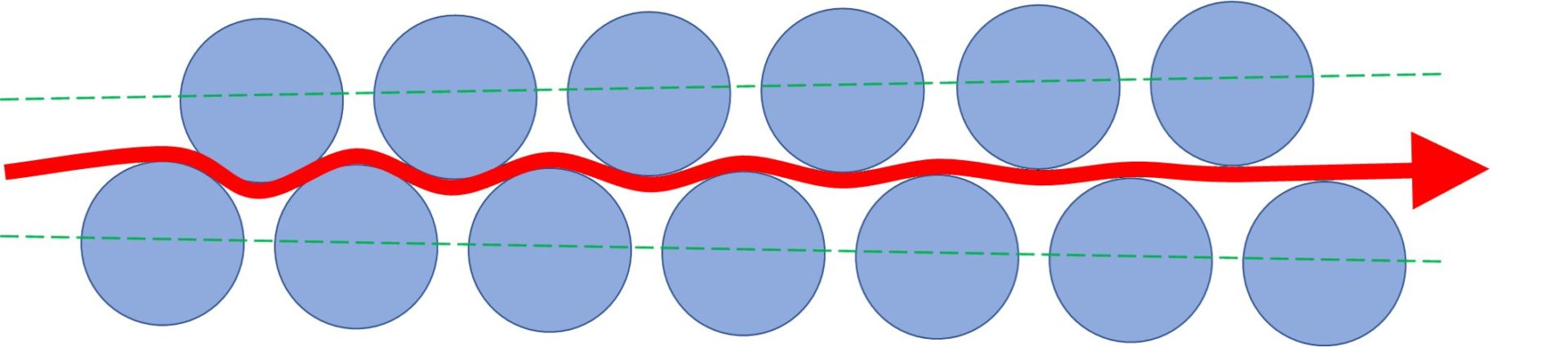
Figure 3: The severity of the bending and unbending around the work changes with the roll gap, roll diameter, and roll spacing.
Removing coil set requires permanent yielding in the outer 20 percent of the top and bottom surfaces of the metal. The central 80 percent of the thickness remains unchanged.T-14 Straighteners are appropriate for this type of shape correction (Figure 4). Only end bearings support the simplest straighteners, with no backup rolls used. Closing the entry roll gap risks deflection of the unsupported center, potentially leading to creating edge waves in the coil.
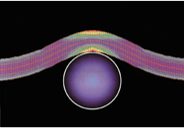
Figure 4: Computer generated analysis showing a straightener roll working the outer 20% of the steel strip. The different colors indicate the bending force, which is symmetrical the neutral fiber (the center part that is neither compressed nor stretched). Red areas indicate stresses beyond the yield point, and yellow areas indicate material is at the yield point. Other areas are in the elastic range.T-15
Eliminating crossbow and other shape imperfections like buckles or waves requires permanent yielding in the outer 80 percent of the top and bottom surfaces, with only the central core — 20 percent — remaining in the elastic range.T-14 Precision levelers, which applies tension to the strip as it bends around more smaller diameter rolls, can achieve this deformation (Figure 5). While this deformation can get the coil shape closer to flat, it also reduces the inherent formability of the grade. Processors should use only the least amount of deformation necessary to correct the shape to retain sufficient formability for stamping or other operations.
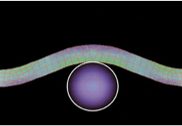
Figure 5: Computer generated analysis showing a leveler roll working the outer 80% of the steel strip while it is under tension. The stress pattern is not symmetrical, with higher stresses seen on the outside of each bend. Passing through the multiple small-diameter rolls under tension results in stresses exceeding the yield point through most or all of the cross section.T-15
Yield point elongation (YPE), Lüders lines, and stretcher strains are names describing the same phenomenon seen in some annealed or aged metals. A related defect called fluting occurs in V-bending. Leveling at-risk coils with repeated cycles of bending and unbending, like shown in Figure 3, may be an effective way to minimize stretcher strains or fluting. However, process control is critical, since excessive leveling work hardens the coil and results in increased strength and reduced ductility. On the other hand, insufficient leveling does not address the defects related to the yield-point phenomenon.
Recent studies K-24, K-48, K-49 describe the importance of sufficient leveling, using real-world examples as well as simulation to model the phenomena and show potential corrective actions, as shown in the following animations.K-50
Figure 6 shows an animation of V-bending without any roller leveling. The fluting defect occurs, since the formed panel shape does not conform to the punch. Figure 7 is an animation of leveling with roller penetration deep enough to produce deformation equivalent to an 85% plastic fraction. Figure 8 presents a closer view of the V-bending, highlighting improved formed panel shape conformance to the punch. The references cited above detail the simulation methodology.
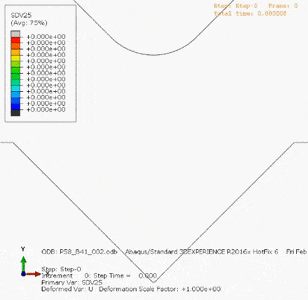
Figure 6: V-bending without roller leveling leads to fluting.K-50
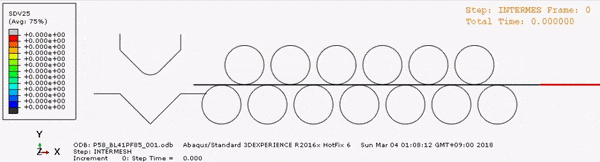
Figure 7: Leveling to produce 85% plastic fraction.K-50
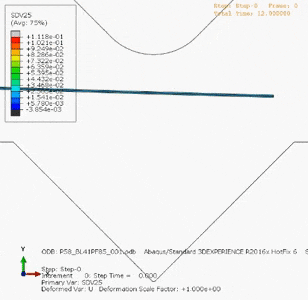
Figure 8: V-bending after leveling to produce 85% plastic fraction minimizes the fluting defect.K-50
Design and Processing Implications
The progressively higher yield strengths for AHSS are challenging the capabilities of straighteners and precision levelers that were not designed for flattening these high strength materials. Equipment manufacturers have been studying and developing solutions to address this issue. There are a series of factors related to the design of straighteners and precision levelers affected by advanced steel grades:
Roll Diameter – Leveling rolls for AHSS generally are smaller in diameter than those used for mild steel, providing a smaller radius around which to bend the material. This is because exceeding the higher yield strength of Advanced High Strength Steels requires a more aggressive bend.
Roll Spacing – Work roll center-spacing will be closer for AHSS than for comparable mild steels. Closer spacing leads to the requirement of more force to reverse-bend the material, resulting in greater power requirements for processing.
Roll Support – Larger journal diameters with larger radii and bearing capacity will withstand the greater forces and higher power required to straighten AHSS.
Roll Depth Penetration – The upper rolls must have enough travel to be able to penetrate the lower fixed rolls sufficiently so the deformation exceeds the yield strength of the AHSS grade. This penetration may need to be as much as 50 to 60 percent greater than for mild steels.
Roll Deflection – Given the greater force requirements for straightening AHSS, work roll deflection becomes a concern especially with smaller-diameter rolls more likely to flex and deflect. Processing wider sheet also increases the deflection risk. Excessive work roll deflection results in undesirable side effects such as edge waves, increased journal stresses and premature gear failure. Backup rollers prevent excessive work roll deflection.
Roll Material – Higher strength materials and special heat treatment should be employed to ensure rolls can withstand greater stresses for longer periods without experiencing fatigue failure.
Gear Materials – Gears that drive the rolls should be produced from heat treated high strength materials to produce smooth running, chatter free roll drive for long life under high loads.
Gear Positioning – Closer roll center spacing requires higher power transmission and results in a smaller gear-pitch ratio, which reduces gear power ratings.
Gear Sizes – To compensate for the gear positioning issue, flattening AHSS grades requires wider gear faces as well as stronger outboard support of journals and idler shafts to produce higher gear power ratings.
Frame Rigidity – The higher strength of advanced steels results in stresses throughout all the components of the processing unit. Frame rigidity is vital to prevent work roll deflection.
Equipment manufacturers have also developed design solutions that address processing of AHSS. As an example, several manufacturers have designed equipment with removable cartridges allowing for swapping between sets containing differently sized rolls, gears, and support structures. As they switch jobs from AHSS to conventional steels, they swap in the appropriate cartridge. This also allows for off-line roll cleaning and maintenance.
Remember that the likelihood of coil set and residual stresses in the coil increases with strength. Operators must take proper precautions when cutting the strapping banks used in coil shipment to avoid “clock-springing.”
Newer processing equipment may contain additional hold-down arms or other features to protect both plant personnel and equipment from damage.E-11
Material Handling Considerations When Working With Higher Strength Steels (U-13)
Stamping AHSS materials can affect the size, strength, power and overall configuration of every major piece of the press line, including material-handling equipment, coil straighteners, feed systems and presses.
Higher-strength materials, due to their greater yield strengths, have a greater tendency to retain coil set. This requires greater horsepower to straighten the material to an acceptable level of flatness. Straightening higher-strength coils requires larger-diameter rolls and wider roll spacing in order to work the stronger material more effectively. But increasing roll diameter and center distances on straighteners to accommodate higher-strength steels limits the range of materials that can effectively be straightened. A straightener capable of processing 600-mm-wide coils to 10 mm thick in mild steel may still straighten 1.5-mm-thick material successfully. But a straightener sized to run the same width and thickness of DP steel might only be capable of straightening 2.5 mm or 3.0-mm thick mild steel. This limitation is primarily due to the larger rolls and broadly spaced centers necessary to run AHSS materials. The larger rolls, journals and broader center distances safeguard the straightener from potential damage caused by the higher stresses.
Mechanical Properties
Introduction to Mechanical Properties
Tensile property characterization of mild and High Strength Low Alloy steel (HSLA) traditionally was tested only in the rolling direction and included only yield strength, tensile strength, and total elongation. Properties vary as a function of orientation relative to the rolling (grain) direction, so testing in the longitudinal (0°), transverse (90°), and diagonal (45°) orientations relative to the rolling direction is done to obtain a better understanding of metal properties (Figure 1).
A more complete perspective of forming characteristics is obtained by also considering work hardening exponents (n-values) and anisotropy ratios (r-values), both of which are important to achieve improved and consistent formability.

Figure 1. Tensile Test Sample Orientation Relative to Rolling Direction
Hardness readings are sometimes included in this characterization, but hardness readings are of little use in assessing formability requirements for sheet steel. Hardness testing is best used to assess the heat treatment quality and durability of the tools used to roll, stamp, and cut sheet metal.
The formability limits of different grades of conventional mild and HSLA steels were learned by correlating press performance with as-received mechanical properties. This information can be fed into computer forming simulation packages to run tryouts and troubleshooting in a virtual environment. Many important parameters can be measured in a tensile test, where the output is a stress-strain curve (Figure 2).

Figure 2: Representative Stress-Strain Curve Showing Some Mechanical Properties
Press shop behavior of Advanced High-Strength Steels is more complex. AHSS properties are modified by changing chemistry, annealing temperature, amount of deformation, time, and even deformation path. With new microstructures, these steels become “Designer Steels” with properties tailored not only for initial forming of the stamping but in-service performance requirements for crash resistance, energy absorption, fatigue life, and other needs. An extended list of properties beyond a conventional tensile test is now needed to evaluate total performance with virtual forming prior to cutting the first die, to ensure ordering and receipt of the correct steel, and to enable successful troubleshooting if problems occur.
With increasing use of advanced steels for value-added applications, combined with the natural flow of more manufacturing occurring down the supply chain, it is critical that all levels of suppliers and users understand both how to measure the parameters and how they affect the forming process.
Highlights
-
- The multiphase microstructure in Advanced High Strength Steels results in properties that change as the steel is deformed. An in-depth understanding of formability properties is necessary for proper application of these steels.
- Tensile test data characterizes the ability of a steel grade to perform with respect to global (tensile and necking) formability. Different tests like hole expansion and bending characterize performance at cut edges or bend radii.
- DP steels have higher n-values in the initial stages of deformation compared to conventional HSLA grades. These higher n-values help distribute deformation more uniformly in the presence of a stress gradient and thereby help minimize strain localization that would otherwise reduce the local thickness of the formed part.
- The n-value of certain AHSS grades, including dual phase steels, is not constant: there is a higher n-value at lower strains followed by a drop as strain increases.
- TRIP steels have a smaller initial increase in n-value than DP steels during forming but sustain the increase throughout the entire deformation process. Part designers can use these steels to achieve more complex geometries or further reduce part thickness for weight savings.
- TRIP steels have retained austenite after forming that transforms into martensite during a crash event, enabling improved crash performance.
- Normal anisotropy values (rm) approximately equal to 1 are a characteristic of all hot-rolled steels and most cold-rolled and coated AHSS and conventional HSLA steels.
- AHSS work hardens with increasing strain rate, but the effect is less than observed with mild steel. The n-value changes very little over a 105 (100,000x) increase in strain rate.
- As-received AHSS does not age-harden in storage.
- DP and TRIP steels have substantial increase in YS due to a bake hardening effect, while conventional HSLA steels have almost none.
Formability
Automotive product designers target small radii for springback control, sectional stiffness, packaging constraints, and design features. These small radii lead to new challenges as applications for AHSS grades continue to increase. One of these challenges is an increased sensitivity to crack formation in those designs with small die radius to material thickness (R/T) ratios. Cracks forming at small R/T in AHSS grades are known as shear fractures.
General forming limit curves or other press shop criteria cannot predict shear fractures, nor are they flagged when traditional approaches are used in forming simulation packages. However, these shear fractures do occur in die tryout. Shear fractures are another form of local formability failure associated with multiphase AHSS such as DP and TRIP.
Shear fractures on AHSS may exhibit similarities to edge fracture, specifically the absence of necking prior to failure. This is in contrast with global formability failures, which are characterized by significant thinning near the fracture. Shear fractures occur almost immediately (within 1 mm of displacement) after reaching maximum load, meaning there is essentially no post-uniform elongation. This is contrary to the tensile behavior where significant post-uniform ductility remains prior to fracture.K-9
Figures 1 and 2 highlight the appearance of a crack on the bend radius caused by shear fracture. No thinning is observed, which is consistent with failures limited by local formability concerns.

Figure 1: Shear fracture in DP780.F-5

Figure 2: Shear fracture in DP980.D-7
Figure 3 shows a typical shear fracture on a DP780 part viewed from different angles. The shear fracture occurred on the sharp radius on the left whereas the larger radius on the right experienced no failure. Depth of draw and draw bead configuration were the same on both sides of the draw panel. Restraining force was also similar on both sides of the blankholder. The significant variable was the die radius.
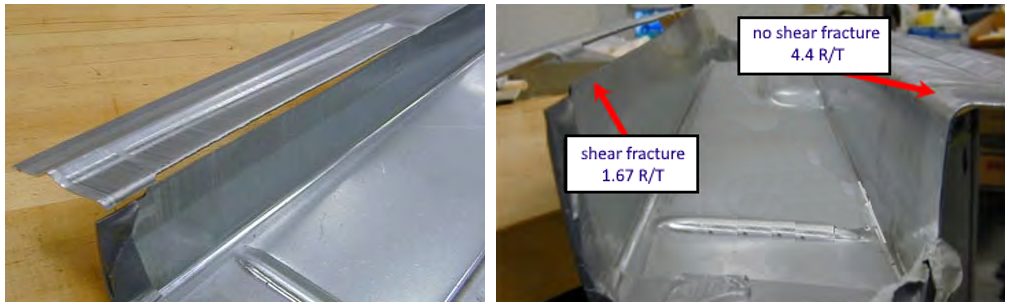
Figure 3: Different Views of a DP780 Part with Small R/T Leading to Shear Fracture at Bead Radius. An R/T = 1.67 led to shear fracture on the left side of the image, while the symmetric area on the right side had an R/T = 4.4, with no shear fracture even though it had the same depth of draw, draw bead configuration, and restraining force.U-6
It is helpful to describe the characteristic differences between conventional tensile fracture and shear fracture, as shown in Figure 4. A conventional tensile fracture is called a Type I fracture, and has been the typical fracture type historically encountered. Type I fractures occur off the radius, and is preceded by necking or metal thinning. Successful prediction of this type of fracture occurs with conventional application of strain analysis and Forming Limit Diagrams. This is in contrast with shear fracture – categorized as a Type III fracture – which occurs within the die radius, with no thinning from necking (typical for local formability failures). Type II fractures occur at or near the tangent of the radius in metal drawn over the radius.

Figure 4: Schematic descriptions of different fracture types ranging from shear fracture to conventional tensile fracture.S-19
Numerous studies show that radius to thickness ratios (R/T) are significant indicators of performance with respect to shear fracture on AHSS. This research led to the establishment of R/T ratio guidelines. While bend testing also categorizes products based on achievable R/T, the significant difference is that the ends are not restrained in a standard bend test. Shear fracture testing typically involves some type of restraining force, such as that seen in a Bending Under Tension test.
As with edge fracture, AHSS grades may be available at a similar strength but with improved minimum R/T ratio. Guidelines have been established for minimum R/T ratios based on bend test results as well as real world case studies. For DP340/590 and above, the R/T ratio should be at least 3T for product features such as embossments where there is relatively limited metal motion. Pulling these grades across a radius or through a draw bead under tension increases the minimum R/T ratio to at least 5T.
As strength levels increase, it is necessary to increase R/T ratios to avoid shear fractures. One study recommended a minimum R/T of 8 for DP800W-4 while another has a critical R/T of at least 7T for DP980S-19. Differences such as these are likely due to different test conditions such as the tension applied during bending, test speed and lubrication. Higher deformation rates (forming speed) and better lubrication tends to promote shear fracture and cause fracture on material close to the die radius.S-19 A combination of high forming speed and back tension leads to DP590 and DP780 having a critical R/T value of 12, with DP980 having a critical R/T of over 16.S-20
Shear fracture is sensitive to rolling direction. If the radius is running in the rolling direction, the bend will be transverse to the rolling direction which is the worst-case scenario when trying to avoid shear fracture. Understanding the directionality of minimum R/T ratios when designing the part to avoid shear fractures is therefore important. One study evaluated DP780, which discovered a critical minimum R/T of 5 to avoid shear fracture, although this varied with back tension and pulling speed. At all R/T ratios tested, the samples oriented so the bend radius was parallel to the rolling direction failed at lower stress than if the bend radius was perpendicular (transverse) to the rolling direction. Tighter R/T magnifies this effect, as does a higher strength grade. At 1.5 R/T, shear fracture with bends perpendicular to the rolling direction occurred when the stress reached 81% of the tensile strength, where in samples with the bend parallel to the rolling direction, failure occurred at 66% of the tensile strength.S-21
Microstructure also plays a role. Phase distribution uniformity, fine microstructural phases, and a decrease in hardness ratio between martensite and ferrite all increase formability as measured by the smallest achievable R/T resulting in split-free panels.W-4, H-6 These are the same factors that result in improved hole expansion values.
Forming Limit Curves are the limiting strain states based on the onset localized deformation, or necking. Generating conventional FLCs typically involves using a 100mm diameter hemispherical punch to deform 1mm to 2mm thick sheet steels, resulting in R/T ratios of 25 or higher. Many decades of use have shown that conventional FLC approaches can be used to assess part robustness and predict failure in areas having large R/T ratios and failure modes affected by global formability. These show up as Type I fractures.
When the R/T ratio is within the shear fracture limit but above the simple bending limit (no stretching imposed to bending), failure may occur in the radius or outside the radius, depending upon the tension level applied during forming. If the failure occurs inside the radius, the failure limit derived from the shear fracture tests should be used as the criterion to predict failure. Finally, when the R/T ratio is smaller than the limit from the simple bending test, the failure occurs in the radius.
In addition to large R/T, most Forming Limit Curves are generated from tests are conducted at a very low strain rate, maintaining an isothermal condition (no heat generated from deforming the sheets). While these conditions are consistent with those adopted for the simulations, they differ significantly from those encountered in industrial practice.
Ignoring the role of deformation-induced heating is one of the most significant reason for the limited success of shear fracture prediction in conventional forming simulation. Strain rates for stamping are typically 1,000x to 10,000x greater than the strain rates for tensile testing. Contact between the sheet metal and the tooling at tight radii also drives up the local temperature. Maximum temperature at the die-sheet interface of 70°C has been found on DP590, but 105°C for CP800.F-6 Stamping DP780 leads to die temperatures of 180°C and blank temperatures of 108°C.P-11 Stamping DP980 produces contact temperatures of over 200°C in certain conditions.F-28
Using a simulation model that accounts for the thermal effects of forming and the associated response in the sheet metal, along with the traditional mechanical deformation response, has been shown to dramatically improve simulation accuracy to predict when shear fracture will occur.K-9, S-20, S-22
Therefore, it is important for the part designer to design an appropriate die radius for a given AHSS product and forming conditions / processes used to manufacture the part. Forming simulation is an excellent tool to derive an appropriate die radius for the specified part and forming process, recognizing that the failure criterion in the simulation must incorporate all conditions and failure modes encountered, including shear fracture.
Key Points
-
- AHSS grades are at risk of crack formation in designs with small die radius to material thickness (R/T) ratios. These cracks are known as shear fracture.
- The strains associated with shear fracture are below that which are associated with the Forming Limit Curve.
- As with edge fractures, shear fractures are also a function of microstructure, strength level, and rolling direction. Consider these variables when designing parts and conducting die try-outs with prototype steel.