Citations
Citation:
G-49. J. Gu, F. Alamos, D. Schoch, J Bornhorst and H Kim, “A Study on Effects of the Press Speed on Sheared Edge Formability,” IDDRG 2020, IOP Conf. Series: Materials Science and Engineering, 967 (2020), 012064, doi.org/10.1088/1757-899X/967/1/012064.
Joining
The unique physical characteristics of Advanced High Strength Steels (AHSS) present some challenges to welding and bonding processes. AHSS differ from mild steels by chemical composition and microstructure, and it’s important to note that their microstructures will change from welding operations. For example, intensive localized heat associated with some welding processes causes a significant change in the local microstructure, and hence affect properties. Due to fast Cooling Rates (CR) typical in welding, it is normal to see martensite and/or bainite microstructures in the weld metal and in the Heat-Affected Zone (HAZ).
When joining AHSS, production process control is important for successful assembly. Manufacturers with highly developed joining control methodology will experience no major change in their operations. Others may require additional checks and maintenance. In certain instances, modifications to equipment or processing methodologies may be required for successful joining of AHSS.
The coating methods for AHSS are similar to those for mild steels. Welding of either AHSS or mild steels with coatings will generate fumes. The amount and nature of fumes will depend on the coating thickness, coating composition, joining method, and fillers used to join these materials. The fumes may contain some pollutants. The chemical composition of fumes and the relevant exhaust equipment must meet appropriate regulatory standards. Thicker coatings and higher heat inputs cause more fumes. Additional exhaust systems should be installed. While welding AHSS (with or without metallic or organic coatings and oiled or not oiled) gases and weld fumes are created similar to mild steels. The allowed fumes or gases must comply with respective national rules and regulations.
Joining Processes
Considering recent developments of hybrid approaches to welding, there are now over 100 types of welding processes available for the manufacturer or fabricator to choose from. The reason that there are so many processes is that each process has its list of advantages and disadvantages that make it more or less appropriate for a given application. Arc welding processes offer advantages such as portability and low cost but are relatively slow and use a considerable amount of heating to produce the weld. High energy density processes such as laser welding generally produce low heat inputs and fast welding speeds, but the equipment is very expensive and joint fit-up needs to be ideal. Solid-state welding processes avoid many of the weld discontinuities produced by those requiring melting (fusion), but they may be expensive and often are restricted to limited joint designs. Resistance welding processes are typically very fast and require no additional filler materials but are often limited to thin sheet applications or very high-production applications such as in the automotive industry.
Most welding processes produce a weld (metallic bond) using some combination of heat, time, and/or pressure. Those that rely on extreme heat at the source such as arc and high energy density processes generally need no pressure and relatively small-to-medium amounts of time. This section introduces joining processes that are applicable to HSS automotive applications, while describing unique process attributes.
About
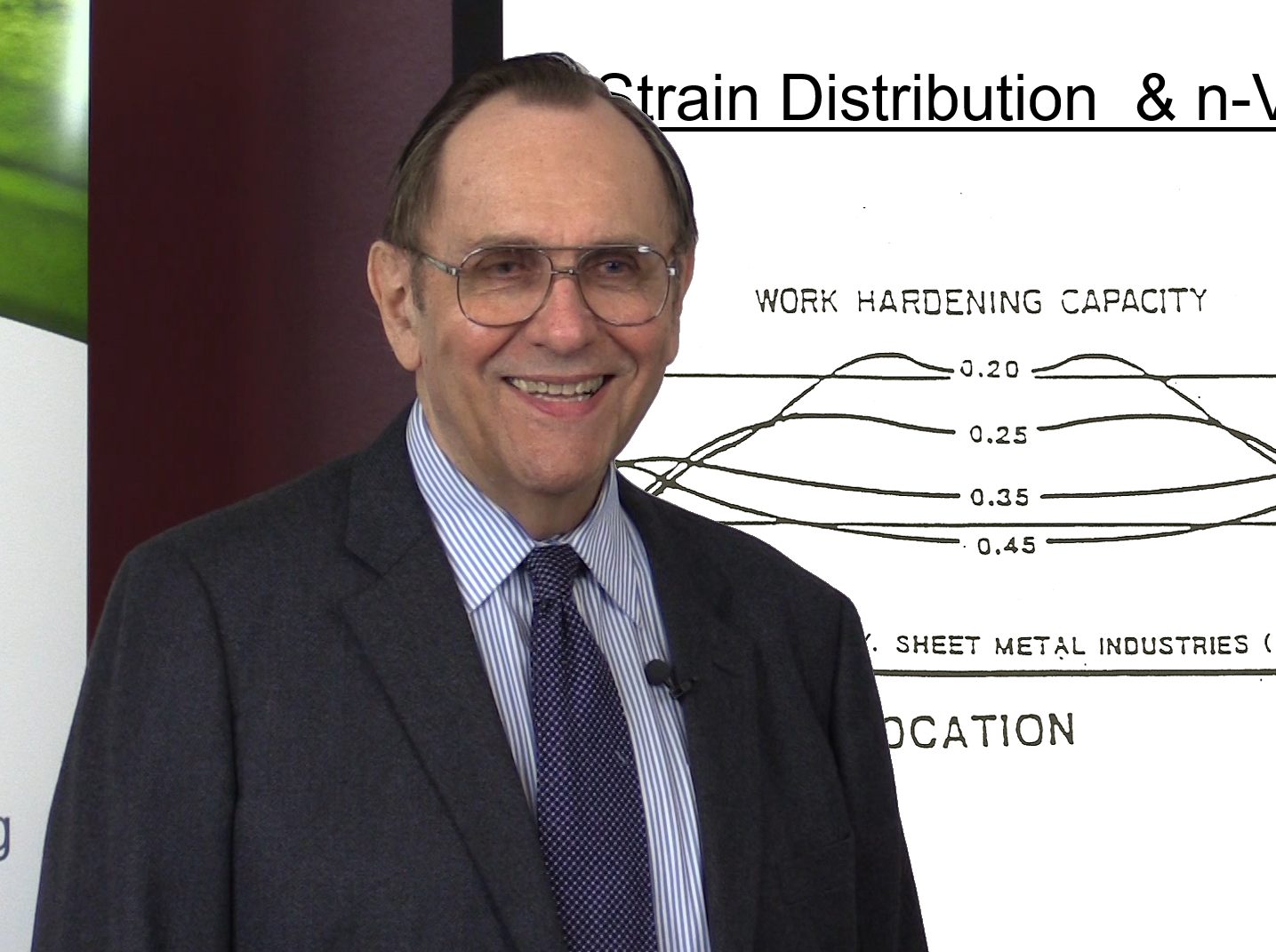
Dr. Stuart Keeler, Sc.D.
We were honored at WorldAutoSteel to have Dr. Stuart Keeler as the author of our first five volumes of AHSS Application Guidelines and an Advisor on Version 6. His knowledge and experience were instrumental in creating a repository of best practices that is one of the best in the world. He was a joy and privilege to work with, and many of us will always fondly remember our interactions with him in developing each version of the Guidelines. It was a great sorrow to us all when he passed away in 2019. It is to him we dedicate this first online edition of the AHSS Application Guidelines. May it carry on and facilitate his pioneering efforts to bring science to the press shop floor for the continual improvement and innovation of steel’s use in the manufacturing of vehicles and other equipment.
As a commemoration of Dr. Keeler’s long service to the steel industry, his dedication to the Guidelines and our own personal love and appreciation of his friendship, we share with you the details of his long and distinguished career. We hope it will inspire.
STUART KEELER, Sc.D.
Dr. Keeler began his extensive sheet metal career at the Massachusetts Institute Technology, where he received his Doctor of Science Degree in Mechanical Metallurgy. Dr. Keeler’s doctoral research on sheet metal forming limits led to his development of the Forming Limit Diagram, now used throughout the world to predict forming severity and tearing of sheet metal stampings.
A two-year stint at the Detroit Army Tank Automotive Command as an Ordnance Corps First Lt. in the Metallurgical Research Section followed graduation. During his tour of duty, Dr. Keeler started taking his exams for Professional Engineer – Metallurgy in the state of Michigan. In 1965, he completed his mandatory experience period and passed his final exam.
The next 24 years were spent at National Steel Corporation – primarily as Manager of Automotive Research in Detroit. During his stay at National Steel, he pioneered the notion of bringing science to the press shop, creating circle grid analysis, thinning strain analysis, statistical deformation control (SDC), and many other press shop troubleshooting procedures. In the early 80’s Dr. Keeler conceived, created, and helped equip the National Steel Product Application Center in Livonia, Michigan, which became a benchmark for customer technical assistance by other steel companies. His last major project for National Steel was to research and write a state of the art book for the American Iron and Steel Institute entitled Automotive Sheet Metal Formability – Report AU89-1.
In March of 1987, Dr. Keeler joined the Budd Company Technical Center as Manager of Sheet Metal Technology. As a Tier 1 supplier to the automotive OEMs, Dr. Keeler was responsible for all research, development, and technology transfer for sheet metal stampings and castings. His major accomplishment was the implementation of virtual sheet metal forming (computerized die tryout). Dr. Keeler also became trained in the Shalnin Problem Solving Process, after which he became The Budd Company corporate trainer. He then trained and coached 30 teams within the company divisions. On 1 October 1999 he retired from The Budd Company as Manager of Technical Development to continue his sheet metal forming work as Keeler Technologies LLC.
In recognition for his work in bringing science to the press shop, Dr. Keeler was elected a Fellow in both the Society of Automotive Engineers (FSAE) and the American Society for Metals (FASM). ASM International also presented Dr. Keeler with the 1992 William Hunt Eisenman Award for his contributions to the practical application of science and materials engineering. He was elected to two-terms during 1968-1972 and one term during 1988 to 1990 to the presidency of the International Deep Drawing Research Group. Dr. Keeler also served in several positions within SAE – last as Editor for SAE Transactions for Materials and Manufacturing.
Dr. Keeler has conducted courses, seminars, and lectures throughout the world. All of Dr. Keeler’s presentations — for the university or the press shop — were dynamic, interactive, down to earth, and even entertaining. He also has a 50-year history of writing practical and understandable articles and papers read by persons in both steel mills and press shops. Given a choice, however, he would be found on the press shop floor.