RSW Modelling and Performance
The advantages of numerical simulations for resistance welding are obvious for saving time and reducing costs in product developments and process optimizations. Today’s modeling techniques can predict temperature, microstructure, stress, and hardness distribution in the weld and Heat Affected Zone (HAZ) after welding. Commercial modeling software is available which considers material type, various current modes, machine characteristics, electrode geometry, etc. An example of process simulation results for spot welding of 0.8-mm DC 06 low-carbon steel to 1.2-mm DP 600 steel is shown in Figure 1. Obviously, this technique can apply to dissimilar thicknesses, material types, and geometries. Application of adhesives is also being used with these simulations. This simulation techniques are found to be very beneficial to predict vehicle crashworthiness as it can dramatically reduce the cost of crash evaluations.
You will find several articles in this section describing RSW modelling studies and procedures.
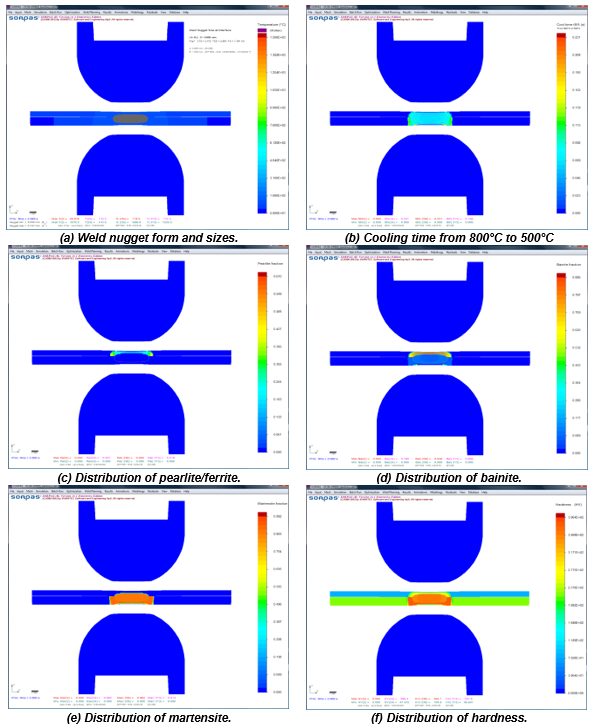
Figure 1: Simulation results with microstructures and hardness distribution for spot welding of 0.8-mm DC06 low-carbon steel to 1.2-mm DP 600 steel.Z-1
Resistance Spot Welding
In general, if any type of AHSS [Dual-Phase (DP), Transformation-Induced Plasticity (TRIP), Complex Phase (CP), Ferrite Bainite (FB), or Martensitic (MS)] is used for the first time, the user should take the welding schedules applied to mild steel and then:
- Increase the electrode force by 20% or more depending on Yield Strength.
- Increase weld time as appropriate.
If these changes are insufficient, try these additional changes:
- A multi-pulse welding schedule (several pulses or post heating).
- Larger tip diameter and/or change the type of electrode.
- Increase the minimum weld size.
When resistance welded, AHSS require less current than conventional mild steel or HSLA because AHSS have higher electrical resistivity. Therefore, current levels for AHSS are not increased and may even need to be reduced depending on material chemical composition. However, most AHSS grades may require higher electrode forces for equivalent thickness of mild steels because electrode force depends on material strength. If thick mild steel or HSLA steel (of the same thickness) is replaced by an equivalent thickness of AHSS, the same forces may be required during assembly welding.
AHSS often have tighter weld windows (welding parameters that give acceptable welds) when compared to mild steels, as shown in the Figure 1.
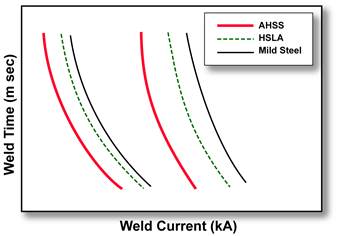
Figure 1: Schematic weld lobes for AHSS, HSLA, and mild steel with a shift to lower currents with increased strength.
The current range (kA) for AHSS of 600-1400MPa during RSW is shown in Figures 2 and 3. The process window for Resistance Spot Welding of AHSS is influenced by the electrode force and welding time used in a major way. The current range increases by an average of 500 A for every additional 500 N of electrode force (Figure 2). The current range also increases by an average of 250 A for each additional 40 ms of welding time (Figure 3). Extra amounts of electrode force and welding time lead to increased current range, allowing for a wider process window.
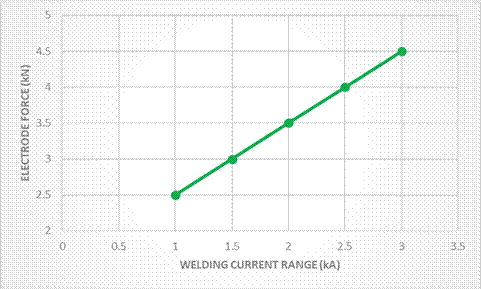
Figure 2: RSW with AHSS, current range for varying electrode force (Cap Type B 16/6, 6-mm tip diameter, single pulse, 340-ms weld time, 250-ms hold time, plug failures.).I-6
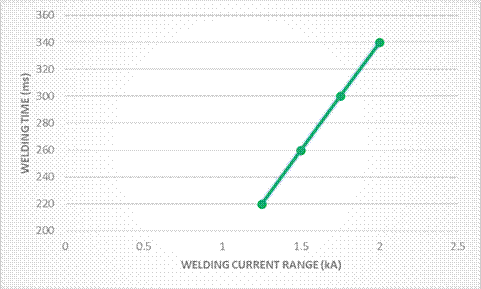
Figure 3: RSW with AHSS, current range for varying weld time (Cap Type B 16/6, 6-mm tip diameter, single pulse, 3.5-kN electrode force, 250-ms hold time, plug failures.).O-1
A more extensive weld studyT-5 of three DP HDGA (45/45 g/m2) coated steels showed similar welding behavior for all three steels. The 1.6-mm-thick steels were DP 340/590, DP 420/780, and DP 550/980. To characterize the welding behavior of the steels, useful current ranges and static weld tensile tests were performed. The useful current range is the difference between the welding current required to produce a minimum button size (Imin) and the current that causes expulsion of weld metal (Imax). In this study, the 4√t as the minimum button diameter was used, where “t” is the nominal sheet thickness. This is generally used in the automotive and steel industries. The weld current range was 2.2 kA for the DP 340/590 and DP 420/780 and 2.5 kA for the DP 550/980 steel (Figure 4). These current ranges are sufficiently wide to weld successfully the DP steels. The study also found no weld imperfections, which means these three DP steels are weldable with simple, easy to use welding parameters.
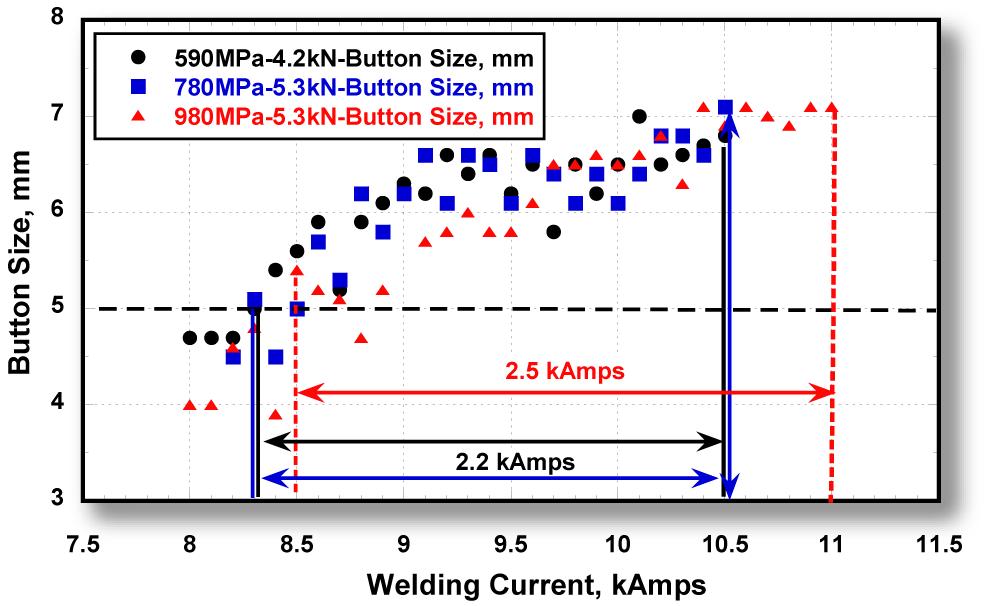
Figure 4: Welding current ranges for 1.6-mm DP HDGA steels with minimum tensile strengths of 590, 780, and 980 MPa.T-5
Average reported weld hardness was 380 HV (Vickers Hardness) for the DP 340/590 and 415 HV for the other two. Again, all three DP steels had similar weld hardness distributions. The study also concluded that weld fracture mode alone is not a good indicator of weld integrity and performance. The load to fracture should be considered more important in judging weld integrity.
A second studyT-6 compared two 1.6-mm-thick HDGA (45/45 g/m2) steels: DP 420/700 and TRIP 420/700. The weld current range for 18 cycles weld time was similar: 1.4 kA for the DP 420/700 and 1.5 kA for the TRIP 420/700. The average weld hardness was 400 HV for both steels. The study concluded that acceptable welds with no imperfections can be produced in both steel grades. Both steel grades are readily weldable with easily adoptable welding parameters. Weld tensile strength differences between the two steels were small and not considered statistically significant.
Weld schedules (Figure 5) with pulsed current profiles for AHSS can have weld-current ranges similar to mild steel. Even though there is no increased tendency for weld expulsion with AHSS avoiding weld expulsion is highly desirable with AHSS. Loss of nugget material can affect weld-nugget size and strength.
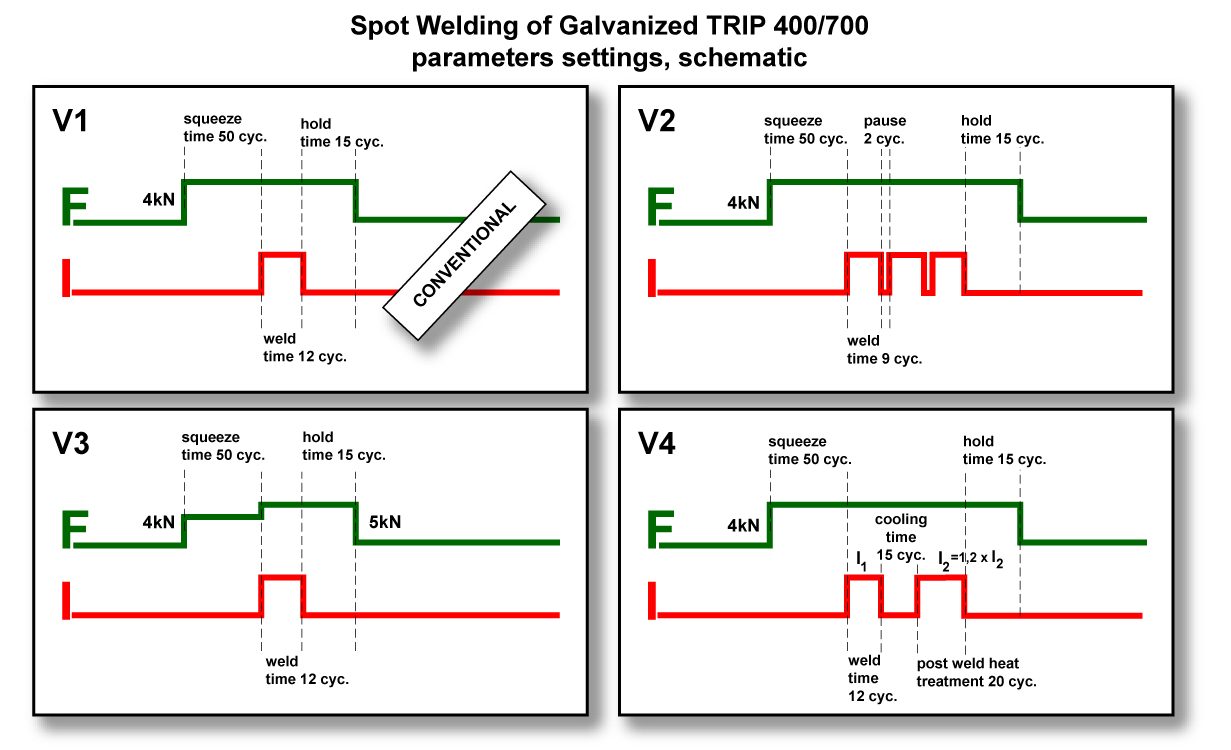
Figure 5: Schematics of optimized weld schedules for AHSS.B-1
Post annealing (tempering pulse weld schedule) of TRIP steel may alter weld fracture mode and weld current range (Figure 6). However, since studies have shown that the occurrence of partial or IF fractures does not necessarily indicate poor weld quality, the use of pulsed current is not required to improve weld quality. Further, the effect of current pulsing on tensile and fatigue properties, as well as the electrode tip life, is not known. Therefore, users should perform their own evaluations regarding the suitability of such modified parameters.
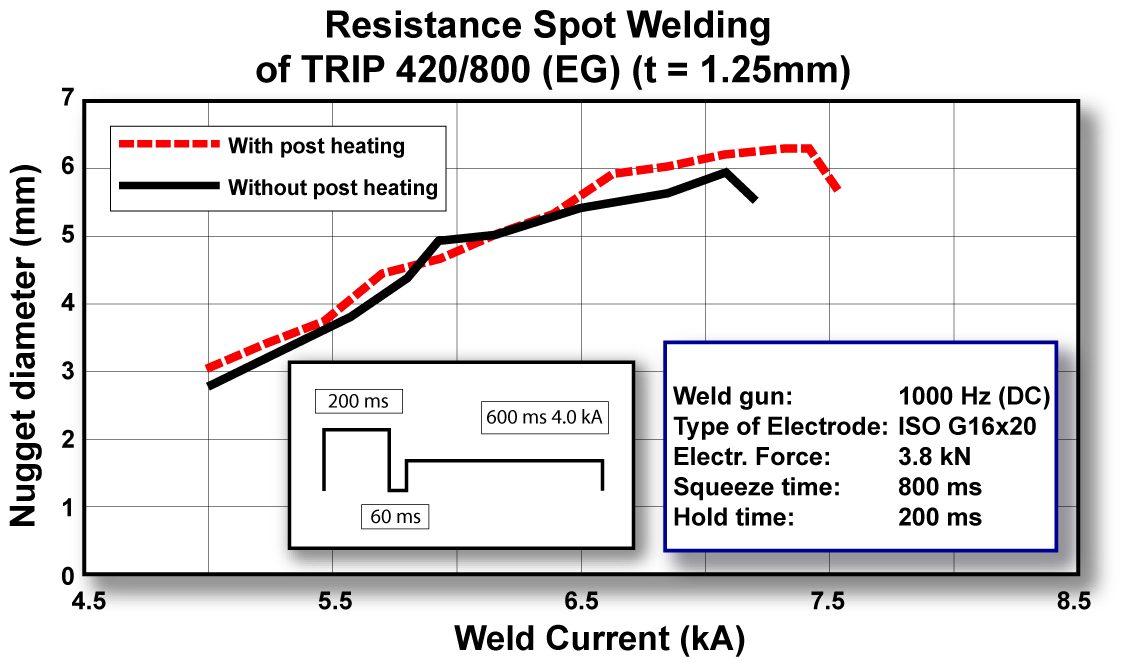
Figure 6: Post annealing may enlarge weld current range.B-1
Additional work using Quench and Partition (Q&P) 980 showed less current required than conventional steels because it has higher electrical resistivity. Due to ultra-high base metal (BM) strength, it needs higher electrode force than conventional steels which have equivalent thickness. The weld lobe of 1.6-mm Q&P 980 is shown in Figure 7 with the pulsed weld time and force of 5.8 kN. The yellow zone of this figure shows the fracture mode of full button (FBF) when peel tested. Some pictures of these weld spots’ fracture mode are captured in Figure 8, for diameters of 6.0 to 7.7 mm.
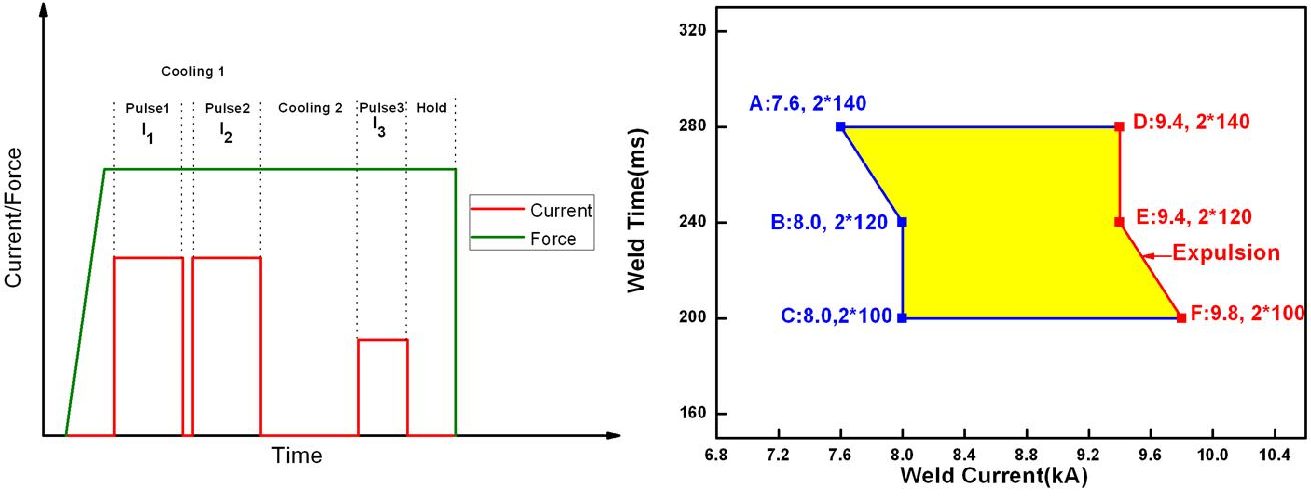
Figure 7: Pulsed current profile and weld lobe of 1_6-mm Q&P 980.B-4
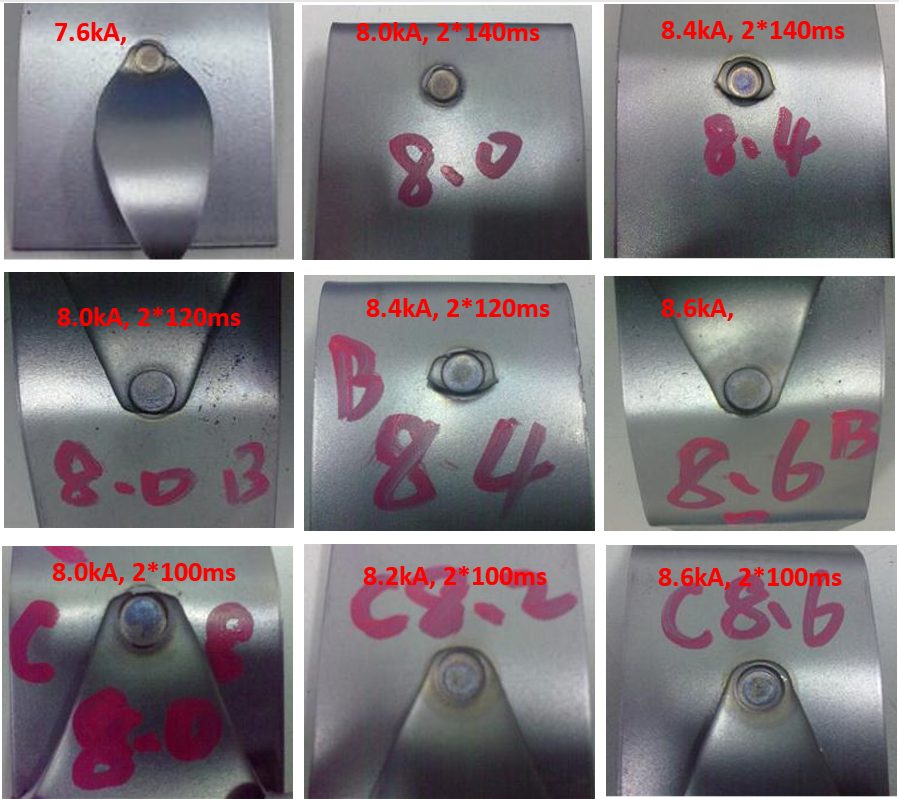
Figure 8: Fracture mode of weld spots in yellow zone.B-4
Hardness measurements and cross sections through the spot weld different zones can be identified as depicted in Figure 9. In a first step, the spot-welded joint can be subdivided into three zones: weld, Heat Affected Zone (HAZ), and BM. The weld is covered by the HAZ, where the melting temperature is not reached but high enough to change the microstructure. This region is dominated by inhomogeneous properties due to the different temperature and cooling gradients. Considering the hardness measurements of AHSS 3 sample, even a softening in the HAZ compared to the BM can be observed. Finally, the HAZ is surrounded by the BM, which does not show any local changes within the structure. These modifications of microstructure in the HAZ and weld are essential for the load-bearing capacity because the strength and ductility are drastically changed in comparison to the BM. Normally a high hardness is related to high strength and less ductility.
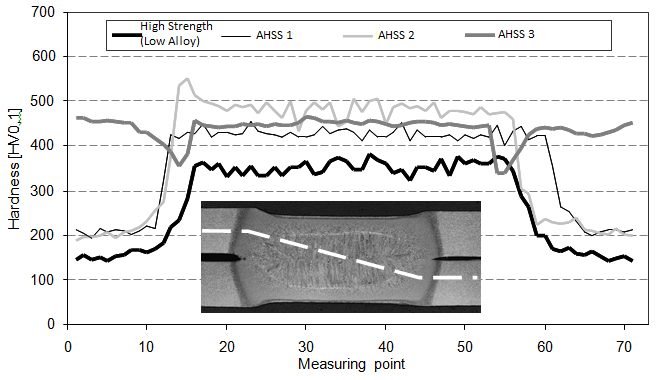
Figure 9: Hardness distribution through spot welds of various strength steels.P-7
Weld spot micrograph and microhardness of 1.6-mm Q&P 980 is shown in Figure 10, in which no weld defects, such as cracks, shrinkage void, pore, no fusion, deep indentation, etc. were found. Hardness testing is typically performed as shown in Figure 11 (diagonal traverse across the weld from BM of top coupon to BM of bottom coupon) using a suitable instrument for micro-indentation hardness testing (Vickers or Knoop).
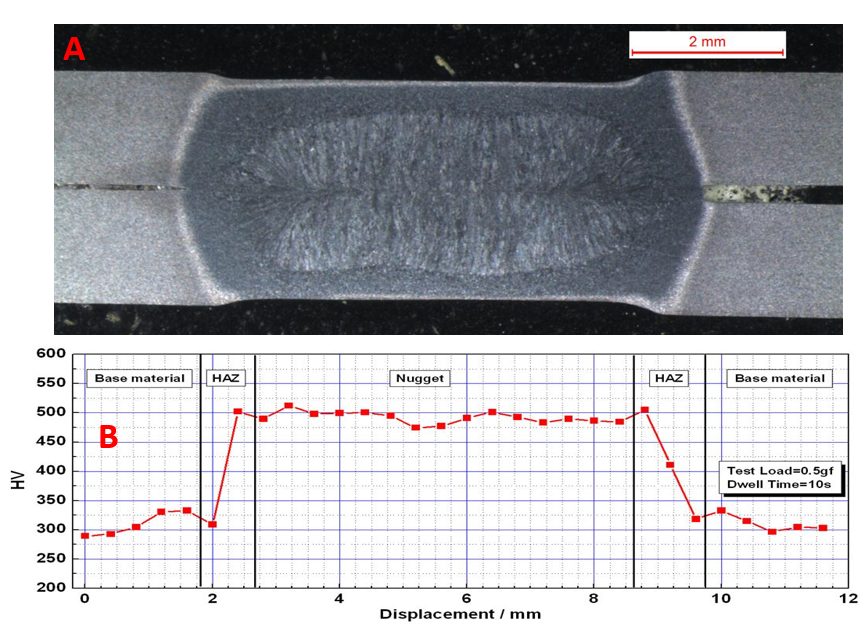
Figure 10: Weld spot micrograph and microhardness of 1.6-mm DP 980.B-4
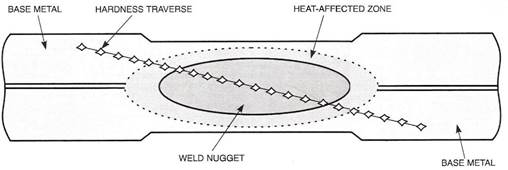
Figure 11: Typical cross-sectioned weld and hardness traverse.A-13
The different hardness values seen in a typical cross-sectioned weld depict different microstructural regions.P-8 Figure 12 shows the temperature distribution of a typical 2T weldment of hot stamped boron steel. At the solidified weld nugget, we see the highest temperatures and steadily decrease toward the unaffected base metal. The weld metal, coarse grain heat affected zone, fine grain heat affected zone, and unaffected base metal are made up of martensitic microstructure. The base metal has this microstructure due to the heat treatment (hot stamping) process. The weld metal, coarse grain heat affected zone, and fine grain heat affected zone are exposed to austenitizing temperature upon welding and are cooled rapidly reforming the martensite microstructure. The subcritical heat affected zone has a unique microstructure of over-tempered martensite. In this region, the peak temperature re below the Ac1, causing the base metal martensitic microstructure to decompose into ferrite and cementite. Micrographs of the different weld regions can be seen in Figure 13.
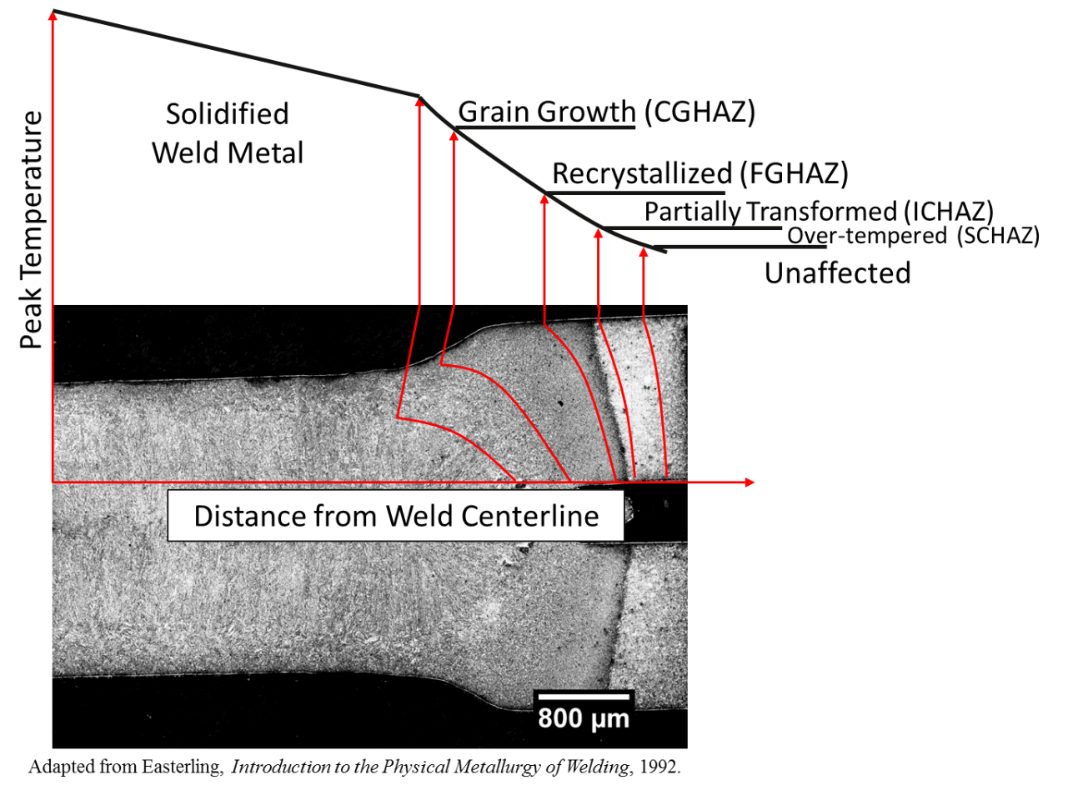
Figure 12: Temperature distribution of a typical 2T RSW of hot stamped boron steel.P-8
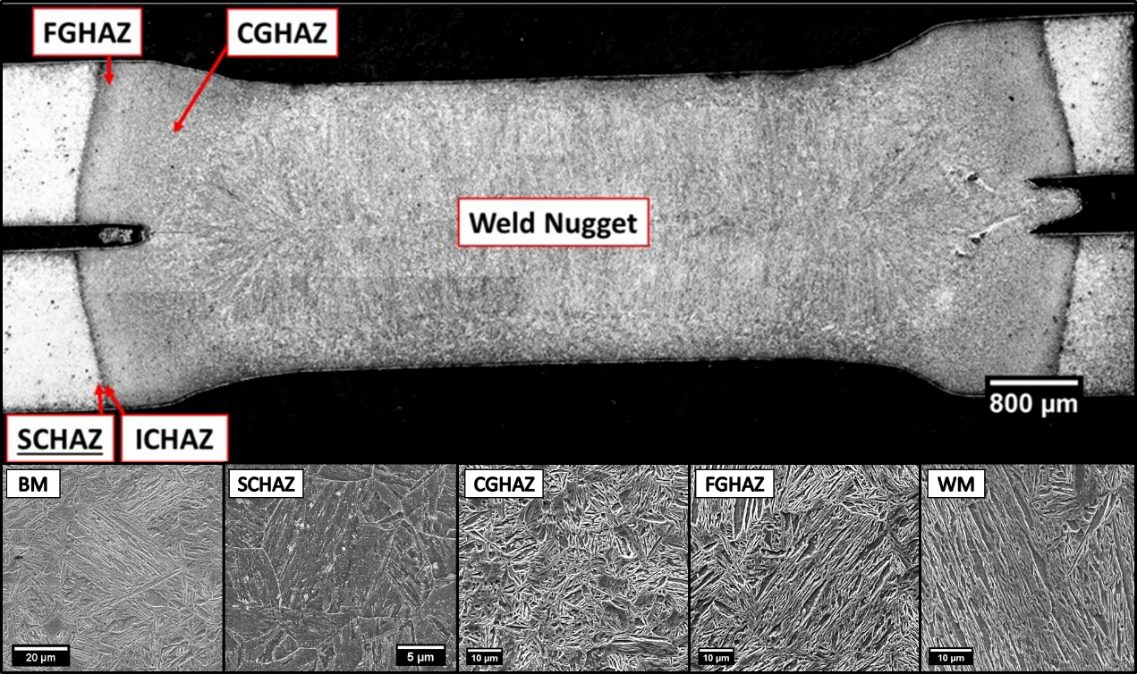
Figure 13: Different microstructures seen throughout the HAZ of a 2T hot stamped boron steel joint.P-8