
Edge Stretching Tests
topofpage
- Hole Tension Test
- Edge Tension Test
- Side Bending Test
- Half-Specimen Dome Test (HSDT)
- Edge Flange Test
The ISO 16630 Hole Expansion Test and the VDA238-100 bend test are among the few standardized tests to characterize local formability, the term which describes when part and process design, in addition to sheet metal properties like strength and elongation, influence the amount of deformation the metal can undergo prior to failure.
Researchers have developed alternate tests to further investigate process parameters and more clearly understand and optimize non-steel related variables. Also important is the investigation of different strain states from the ones seen in the hole expansion and bending tests. Comparisons of the stretched or bent edge performance evaluating different process parameters using the same material help to better define optimum process parameters. Repeating the testing with different AHSS grades confirms if similar trends exist across different microstructures and strengths. Standardization of these alternate tests has not yet occurred, so use caution when comparing specific values from different studies.
Hole Tension Test
Microstructural damage in the shear affected zone reduces edge ductility. Damage has been evaluated with a modified tensile dogbone containing a central hole prepared by shearing or reaming, as shown in Figure 1. In contrast with a hole expansion test using a conical punch, the researchers described this as a Hole Tension test, which determines failure strain as a function of grade and edge preparation.

Figure 1: Hole Tension Test Specimen GeometryP-12
Edge Tension Test
A two-dimensional (2-D) edge tension test, also called Half-A-Dogbone test, also evaluates edge stretchability. There are multiple versions of this type of test, but they all are based on the same concept. Like a standard tensile test, the 2-D edge tension test pulls a steel specimen in tension until failure. Unlike a standard tensile test where both sides of the tensile specimen are milled into a “dog bone”, the 2D tension test uses half of a dogbone with different preparation methods for the straight edge and the edge containing the reduced section (Figure 2). The chosen preparation method for each face is a function of the parameter being investigated (ductility, strain, burr, and shear affected zone for example). Potential edge preparation methods include laser cutting, EDM, water jet cutting, milling, slitting or mechanical cutting at various trim clearances, shear angles, rake angles or with different die materials.

Figure 2: 2-D Edge Tension Test Sample. Note the edges are prepared differently based on the targeted property evaluated.
Side Bending Test
Instead of a dogbone or half-dogbone, some studies use a rectangular strip without a reduced section. Bending performance can be evaluated with a rectangular strip having one finished edge and one trimmed edge while preventing out-of-plane buckling, as shown in Figure 3.G-7
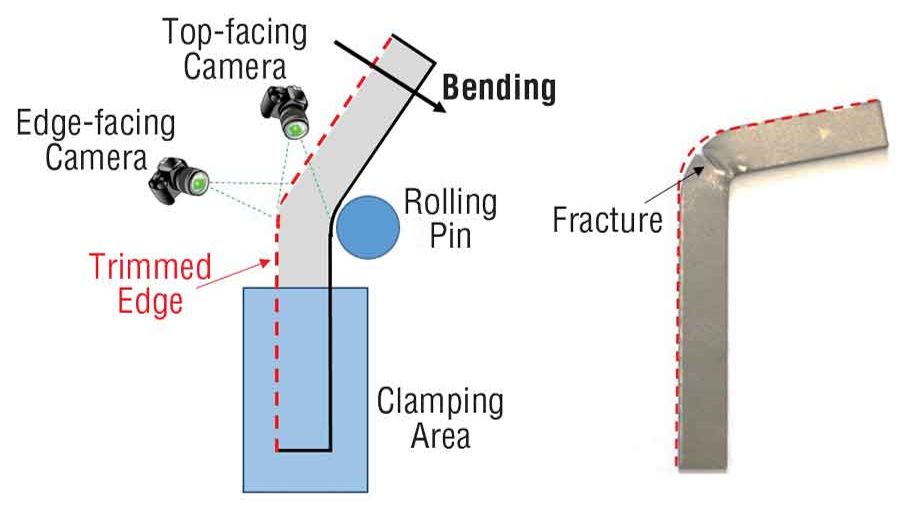
Figure 3: The side-bending test expands a trimmed edge over a rolling pin until detection of the first edge crack.G-7
Half-Specimen Dome Test
Deformation in these three tests occur in the plane of the sheet. Typical hole expansion tests, like production stampings, deform the sheet metal perpendicular to the plane of the sheet. However, hole expansion testing does not always give consistent test results. The half-specimen dome test (HSDT) also attempts to replicate this 3-dimensional forming mode (Figure 4), and appears to be more repeatable likely due to creating a straight cut rather than round hole.
In the HSDT, a rectangular blank is prepared with one edge having the preparation method of interest, like sheared with a certain clearance or laser cut or water-jet cut. The sample is then clamped with the edge to be evaluated over a hemispherical punch. The punch then strains the clamped sample creating a dome shape, with the test stopping with the first crack appears at the edge. Edge stretchability is quantified by measuring dome height or edge thinning or other characteristics.
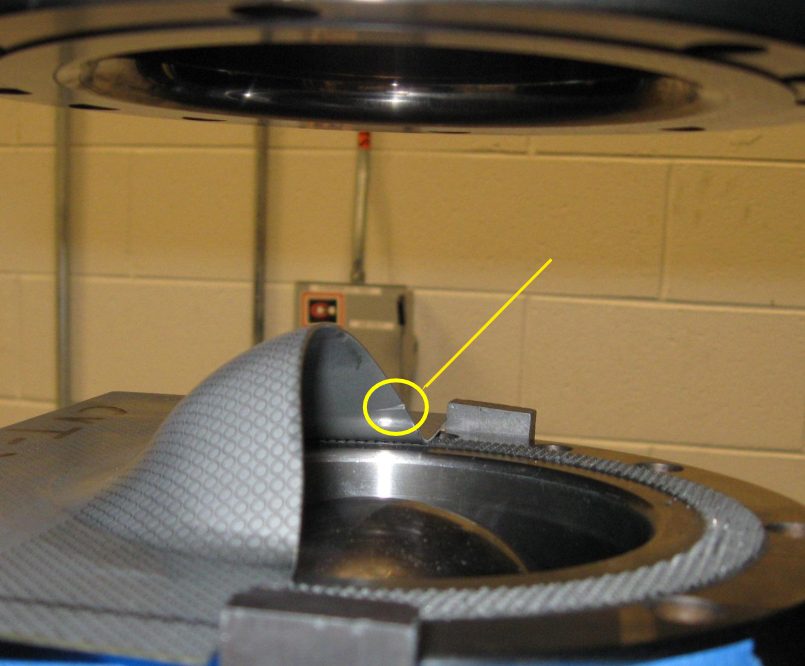
Figure 4: Half-Specimen Dome Test sample. Arrow points to edge crack.S-12
Edge Flange Test
Flanging limits depend on the part contour, edge quality, and material properties. Non-optimal flange lengths – either too long or too short – will lead to fracture. Different tools can assess the influence of flange length, including the one shown in Figure 5 from Citation U-3.
Figure 5: Tool design to investigate flange length before fracture. Flange height: 40mm in left image, 20mm in right image.U-3
Physical tests using this tool show that optimizing sample orientation relative to the rolling direction leads to longer flange lengths before splitting.U-3 Figure 6 highlights the results from testing DP800.
Figure 6: Flange height limits as a function of orientation in DP800.U-3
- Hole Tension Test
- Edge Tension Test
- Side Bending Test
- Half-Specimen Dome Test (HSDT)
- Edge Flange Test