Improvement by Metallurgical Approaches
The Hole Expansion test (HET) quantifies the edge stretching capability of a sheet metal grade having a specific edge condition. Many variables affect hole expansion performance. By understanding the microstructural basis for this performance, steelmakers have been able to create new grades with better edge stretch capability.
Multiphase microstructures with large hardness differences between the phases, specifically islands of the very hard martensite surrounded by a softer ferrite matrix, may crack along the ferrite-martensite interface (Figure 1). The larger the size of the initiated damage site (due to edge shearing), the smaller the critical stress required for crack propagation.M-6 The microstructure and damage are key components of the Shear Affected Zone, or SAZ.
Figure 1: Features and mechanisms of damage initiation and propagation in Dual Phase steel.M-6
One metallurgical approach to improve sheared edge stretchability is targeting a homogeneous microstructure. Steel suppliers have engineered product offerings like complex phase steel, where extensive grain refinement (reducing the size of the ferrite and martensite grains) is achieved. Consequently, the size of the initial damage resulting from shearing is reduced, raising the critical stress for crack propagation to higher levels and reducing the likelihood for crack propagation. Additionally, reducing the difference in hardness between the soft ferrite phase and the hard martensite phase improves the hole expansion ratio. Changes in chemistry, hot rolling conditions and intercritical annealing temperatures are some of the methods used to achieve this. Such metallurgical trends can include a single phase of bainite or multiple phases including bainite and removal of large particles of martensite. This trend is shown in Figure 2, adapted from Citation M-11.
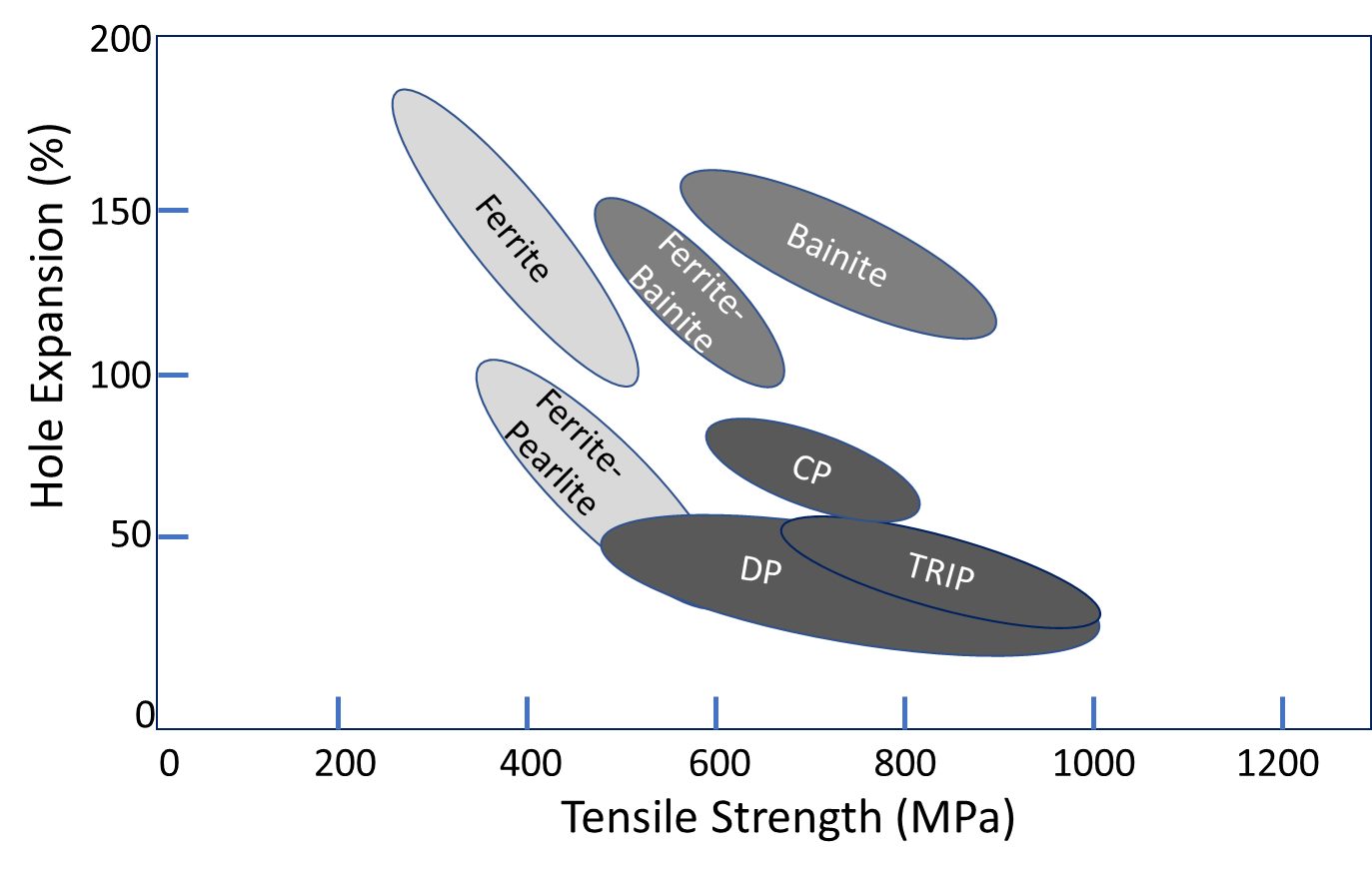
Figure 2: Hole Expansion as a Function of Strength and Microstructure. Adapted from Citation M-11.
An example of the impact of these modifications is shown in a paper published by C. Chiriac and D. HoydickC-10, where a 1 mm DP780 galvannealed steel was modified to produce a grade with improved hole expansion to achieve greater resistance to local formability failures such as edge fracture and shear fracture. These changes were made while retaining the same base metal chemistry and the same fraction of martensite in the structure, and resulted in similar tensile strength and total elongation but with a 50% increase in hole expansion (Table I and Figure 3). The key difference is a lower martensite hardness, and a smaller difference between the hardness of the martensite and ferrite. The modified DP grade has more homogeneous distribution of martensite with smaller ferrite and martensite grains (Figure 4).

Table I: Comparison of a conventional DP780 steel with a similar chemistry modified to improve hole expansion.C-10
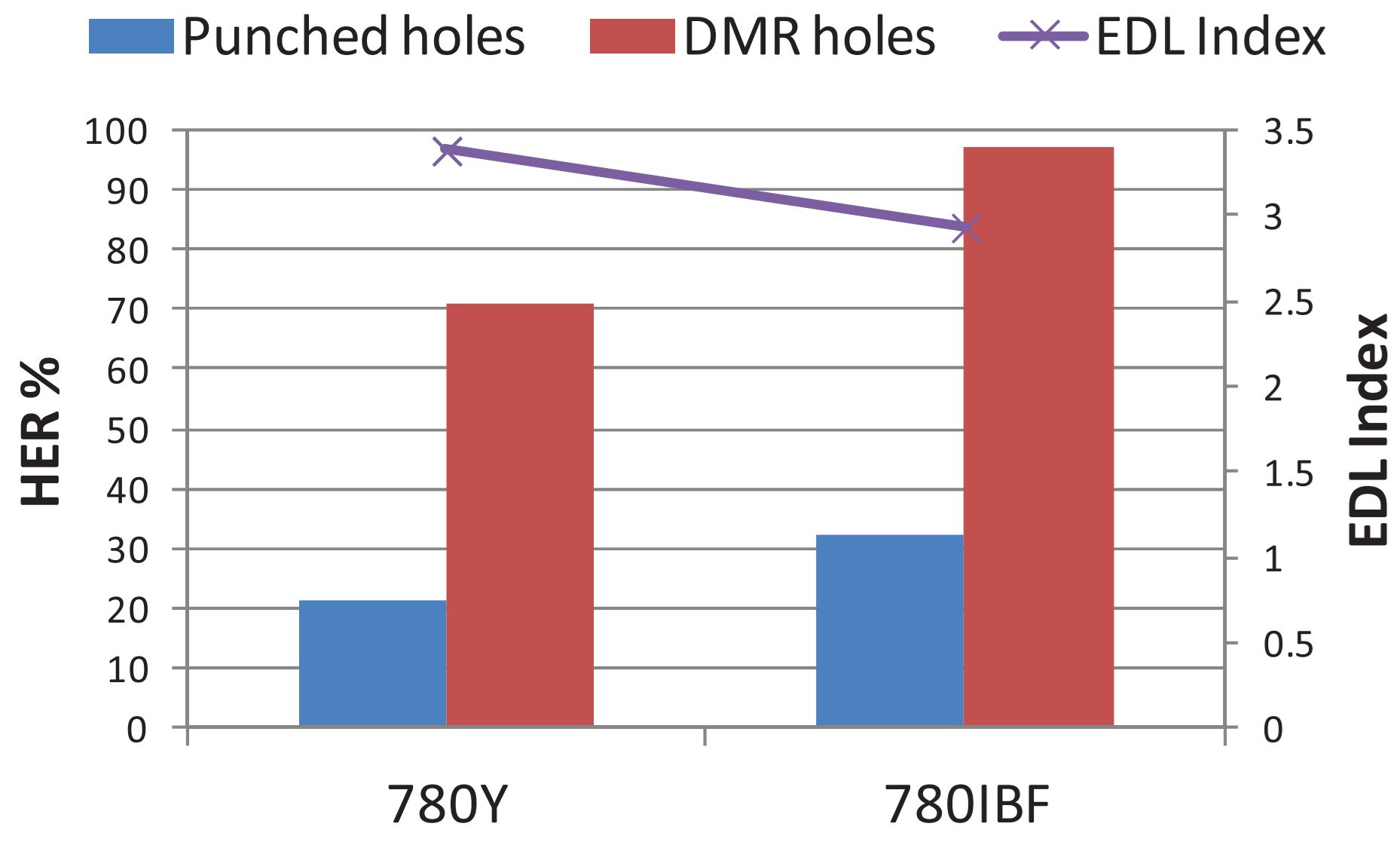
Figure 3: Improvement in Hole Expansion improves with grade modifications and edge quality. DMR = drilled, milled, and reamed hole; EDL = Edge Ductility Loss index, the ratio of the hole expansion of the DMR hole to that of the punched hole.C-10
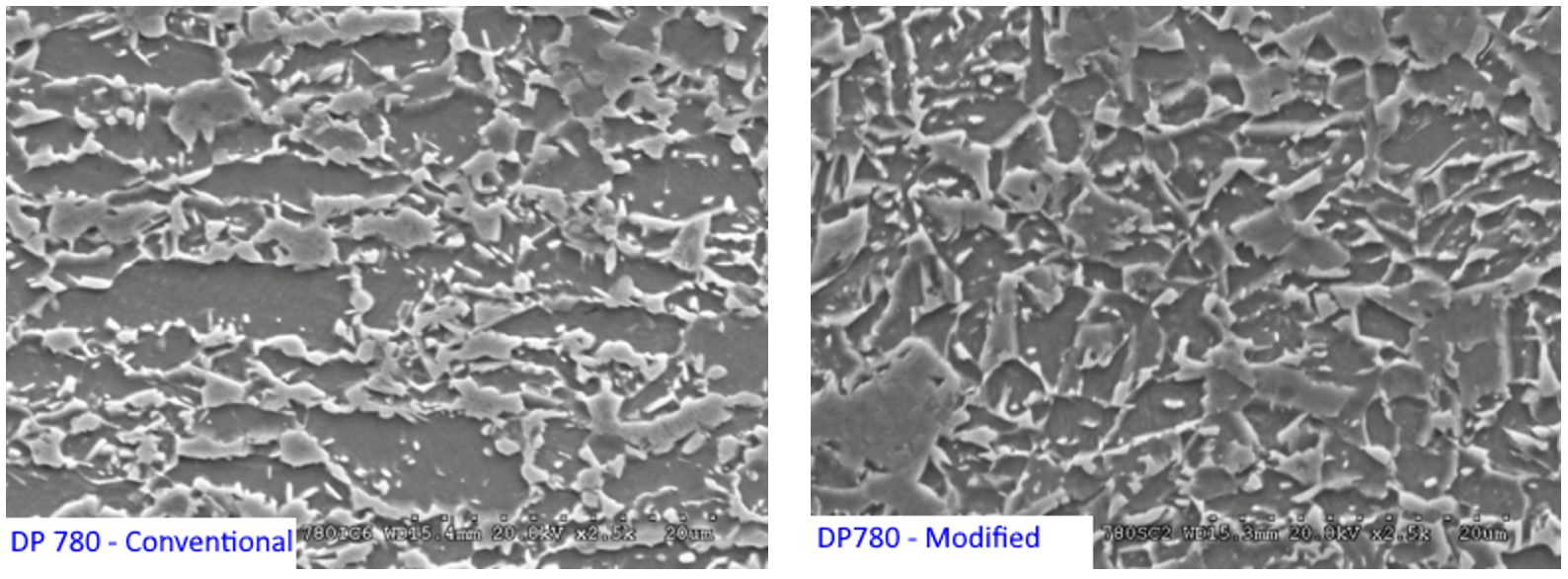
Figure 4: Comparison of the microstructure of a conventional DP780 steel (left) with a similar chemistry modified to improve hole expansion (right). Overall, there is the same fraction of martensite in both grades, but the modified chemistry has finer features.C-10
A presentation at a 2020 conferenceK-16 described a study which compared DP780 from six different global suppliers. Hole expansion tests were done on 1.4 mm to 1.5 mm mm thick samples prepared with either a sheared edge at 13% clearance, a sheared edge with 20% clearance, or a machined edge. Not surprisingly, the machined edge with minimal work hardening outperformed either of the sheared edge conditions. However, when considering only the machined edge samples, the hole expansion ratio ranged from below 30% to more than 70% (Figure 5). Presumably the only difference was the microstructural characteristics of the six DP780 products.
Figure 5: Variation in hole expansion performance from DP780 from 6 global suppliers.K-56
The microstructural differences that enhance local formability characteristics may be detrimental to global formability characteristics and vice versa. Conventional dual phase steels, with a soft ferrite matrix surrounding hard martensite islands, excel in applications where global formability is the limiting scenario. These steels have a low YS/TS ratio and high total elongation. However, the interface between the ferrite and martensite is the site of failures that limit the sheared edge extension of these grades. On the other end of the spectrum, fully martensitic grades are the highest strength steels available. These have a high YS/TS ratio, and low total elongation. Having only a single phase helps these grades achieve surprisingly high hole expansion values considering the strength, as seen in Figure 6.
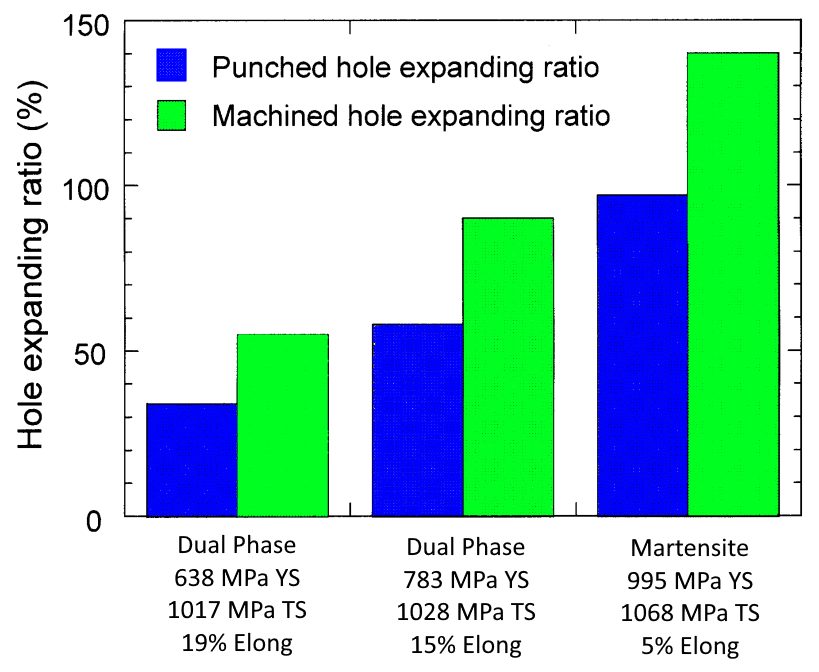
Figure 6: Hole Expansion as a Function of Edge Quality and Microstructure. Adapted from Citation.H-7
Knowing that a higher volume fraction of martensite is needed to increase strength, combined with the awareness that minimizing the hardness differences between microstructural phases is needed to increase hole expansion (Figure 7), allows steelmakers to fine-tune their chemistry and mill processing to target specific balances of strength, tensile elongation, and cut edge expandability as measured in a tensile test.
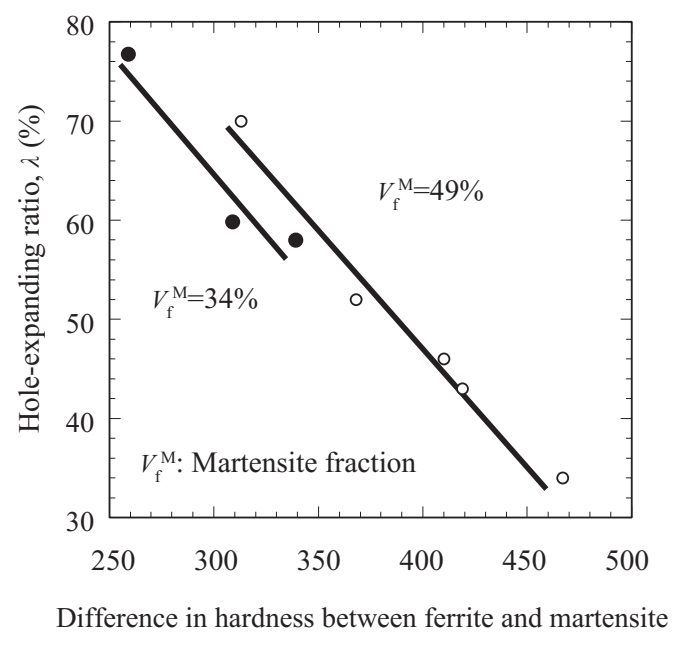
Figure 7: Improved Hole Expansion by Reducing the Hardness Difference between Ferrite and Martensite.H-8
This expands the selection of grades from which manufacturers can choose. Traditional material selection and identification may have been based on tensile strength to satisfy structural requirements – DP980 is a dual phase steel with 980MPa minimum tensile strength. However, newly engineered grade options offer users an extra level of refinement depending on the functional needs of the part. Products can be specified as needing high tensile elongation, high hole expansion, or a balance of these two. In the example shown in Figure 8, note that all 3 grades have nearly identical tensile strength.
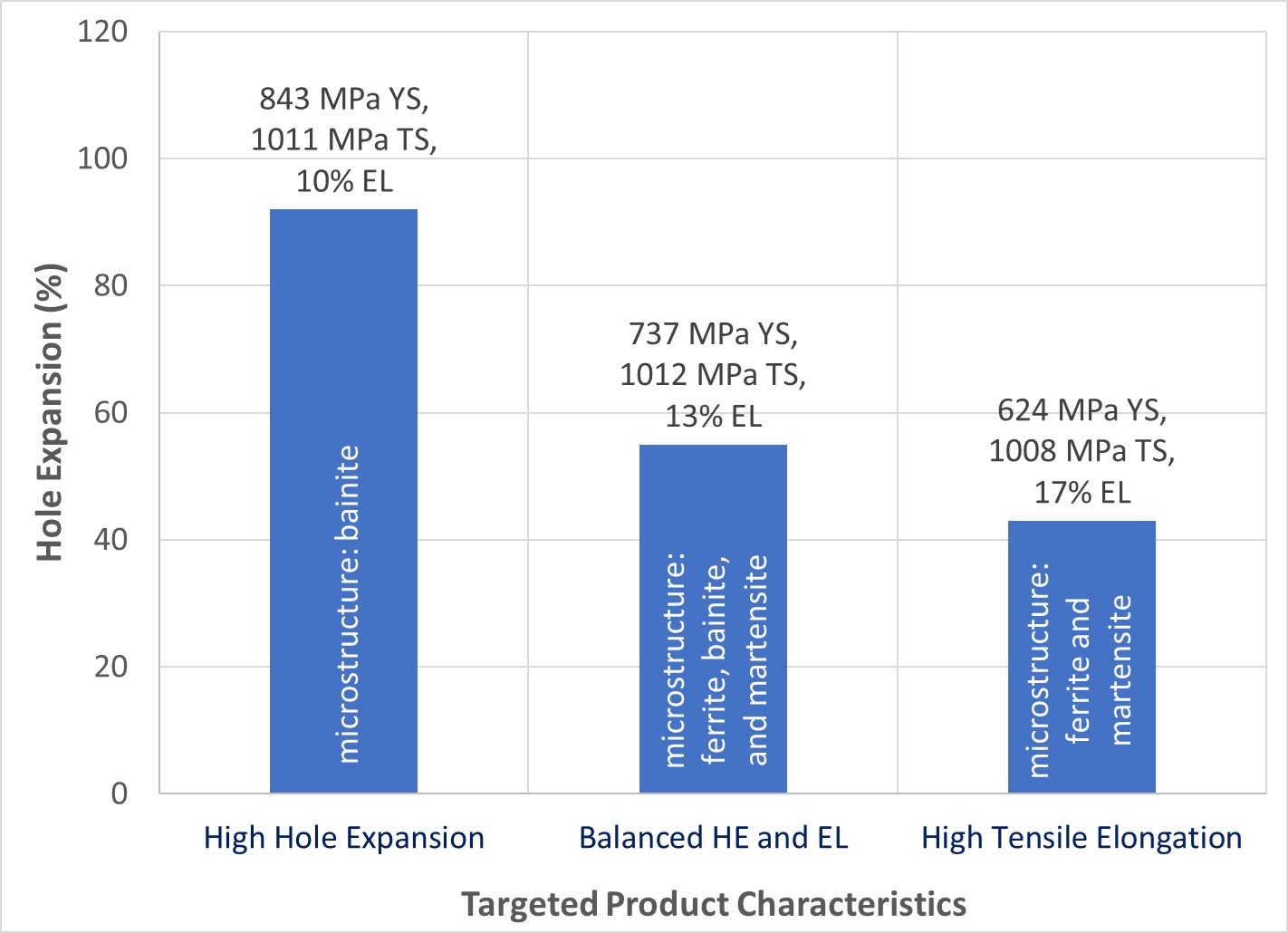
Figure 8: Engineered Microstructures Achieve Targeted Product Characteristics. (Data from Citations N-8 and F-5)
The influence of microstructure and the hardness differences between the phases is also seen in the hole expansion values of AHSS grades at strengths below 980 MPa. A study from 2016 shows the impact of a small amount of martensite on a ferrite-bainite microstructure.N-9 Both products compared had a microstructure of 80% ferrite. In one product, the remaining phase was only bainite, while the other had both martensite and bainite. The presence of just 8% martensite was sufficient to decrease the hole expansion capacity by 40%. (Figure 9).
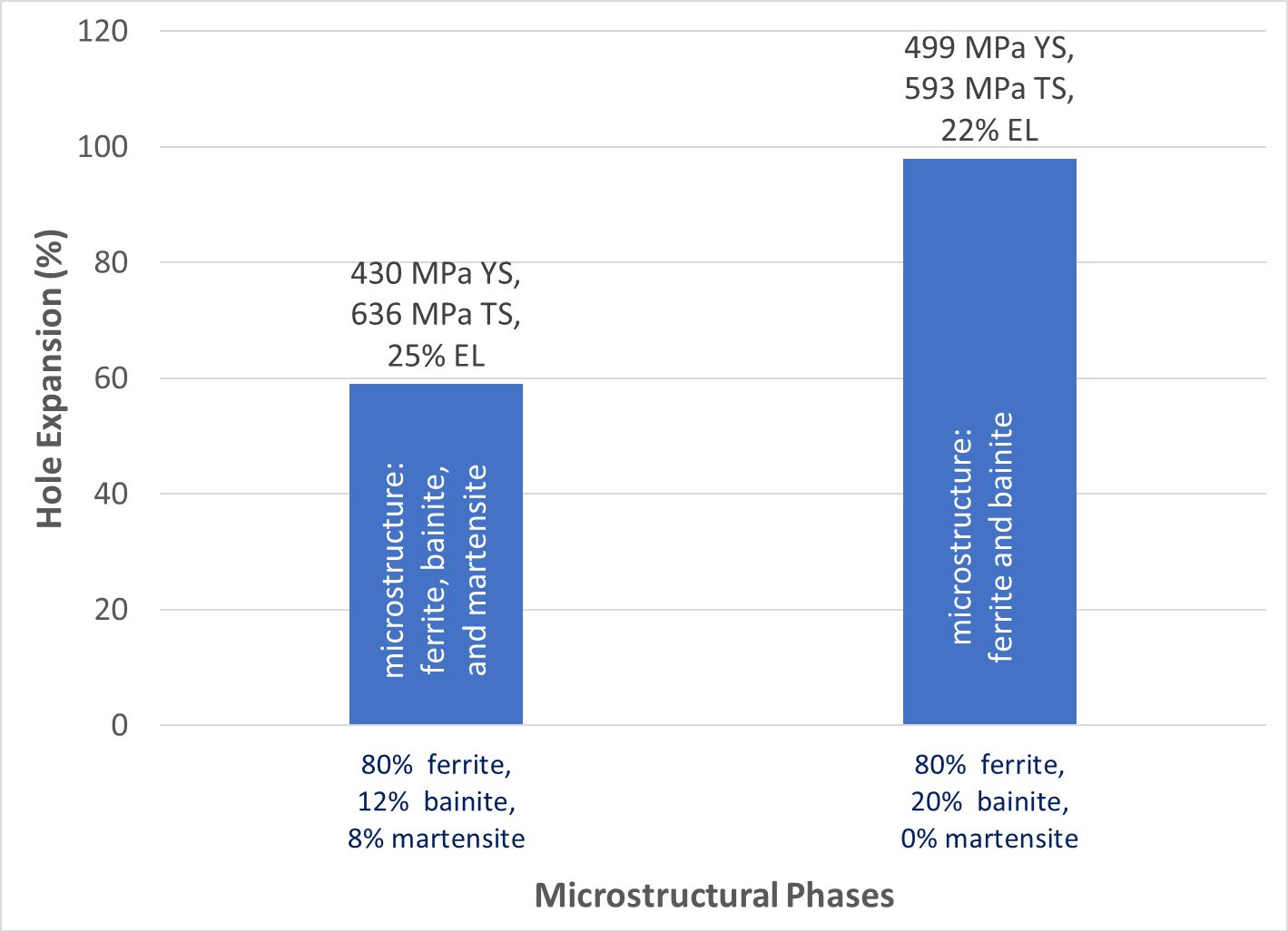
Figure 9: High Hardness Differences in Microstructural Phases Decrease Edge Ductility at All Strength Levels. Adapted from Citation N-9.
Rolling direction may also influence edge fracture sensitivity on some multiphase AHSS grades. When testing a sample, edge fractures may occur first at the hole edge along the rolling direction, which corresponds to a tensile axis in the transverse direction. If the chosen grade exhibits this behavior, locate stretch flanges perpendicular to the rolling direction when possible during die and process development to increase resistance to edge fracture. If this is not practical, identify locations where inserting scallops/notches in the stretch flange will not negatively impact the part structure, fit or die processing.
During die development and die try-out, it is important to use the production-intent AHSS grade – not just one that has the same tensile strength. Blank orientation relative to the rolling direction in these trials must also be production-intent. Often the blank die is the last completed die, so prototype blanks may be prepared by laser, EDM, water jet or even by hand during tryout. These cutting methods will have different sheared edge extension, as measured by the hole expansion test, compared with the production-intent shearing. These differences may be sufficiently significant to prevent replication of production conditions in tryout.