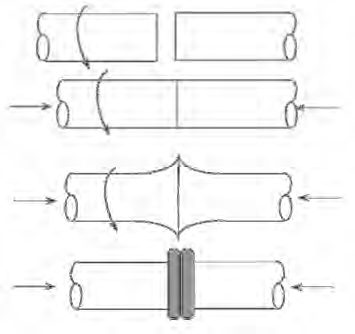
Solid State Welding
Introduction
Solid-State welding refers to a family of processes that produce welds without the requirement for molten metal. Solid-state welding theory emphasizes that the driving force for two pieces of metal to spontaneously weld (or form a metallic bond) to each other exists if the barriers (oxides, contaminants, and surface roughness) to welding can be eliminated. All solid-state welding processes are based on this concept, and use some combination of heat, pressure, and time to overcome the barriers. Approaches include friction, diffusion, explosion, and ultrasonic welding.
Since there is no melting, there is no chance of forming defects such as porosity or slag inclusions which are only associated with fusion welding processes. Solid-state welding processes also require no filler materials, and in some cases, can be quite effective at welding dissimilar metals that cannot be welded with conventional processes due to metallurgical incompatibilities. The equipment is typically very expensive, and some processes involve significant preparation time of the parts to be welded. Most of these processes are limited to certain joint designs, and some of them are not conducive to a production environment. Non Destructive Testing processes do not always work well with solid-state welding processes because of the difficulties of distinguishing a true metallurgical bond with these techniques.
In this section you’ll find examples of three types of solid state welding processes: Friction, High-Frequency for tubes and pipe and Magnetic Pulse. Generally these are characterized as follows. Click to the specific menu for details.
Friction Welding Processes
This family of processes relies on significant plastic deformation or forging action to overcome the barriers to solid-state welding. Frictional heating dominates at the beginning of the process, followed by the heating due to plastic deformation once the forging action begins. The friction welding processes which use rotation of one part against another are inertia and continuous (or direct)-drive friction welding. These are the most common of the friction welding processes and are ideal for round bars or tubes. In both inertia and Continuous-Drive (CD) friction welding, one part is rotated at high speeds relative to the other part (Figure 1). They are then brought together under force creating frictional heating which softens (reduces the YS) the material at and near the joint to facilitate the forging action, which, in turn, produces further heating. Following a sufficient amount of time to properly heat the parts, a high upset force is applied which squeeze the softened hot metal out into the “flash”. Any contaminants are squeezed out as well as the weld is formed. The flash is usually removed immediately after welding while it is still hot.A-11, P-6
High Frequency Tube/Pipe Welding
HF welding processes rely on the properties of HF electricity and thermal conduction, which determine the distribution of heat in the workpieces. HF contact welding and high-frequency induction welding are used to weld products made from coil, flat, or tubular stock with a constant joint symmetry throughout the length of the weld.
Magnetic Pulse Welding (MPW)
MPW is a solid-state process that uses electromagnetic pressure to accelerate one workpiece to produce an impact against another workpiece. The metallic bond created by this process is similar to the bond created by explosion welding. MPW, also known as electromagnetic pulse or magnetic impact welding, is highly regarded for the capability of joining dissimilar materials.