Arc Welding
This is a summary of a paper of the same title, authored by K. Májlinger, E. Kalácska, and P. Russo Spena, used by permission.M-65
Researchers at the Budapest University of Technology and Economics and the Free University of Bozen-Bolzano tested gas metal arc welding (GMAW) of dissimilar Advanced High-Strength Steel (AHSS) sheets.M-65 The test pieces were 100 x 50 mm samples of 1.4 mm TWIP (TWIP1000) and 0.9 mm TRIP (HCTC800T) sheet steels were welded in a lap joint configuration with 0.8 mm diameter AWS ER307Si austenitic stainless steel wire to determine appropriate GMAW parameters for good quality welds. Quality was determined by external appearance, microstructure, and mechanical properties. Good welds were achieved with linear heat inputs (Q) with ranges from 500-650 kJ/m. The only fractures that occurred appeared within the weld bead by ductile failure modes. The HAZ of the TWIP steel showed grain coarsening and the HAZ of the TRIP steel experienced microstructural changes relative to the distance from the fusion boundary. The ultimate tensile strength (UTS) varies between 73%-84% of the weaker of the two steels.
Welding was conducted with an automated linear drive system with pure Argon (99.996% Ar) shielding gas at 10L/min. Wire feed rates were approximately 3.5 m/min with Direct Current Electrode Positive (DCEP) polarity. Changes in current, voltage, weld speed, and the resulting linear energy are compared in Table 1.
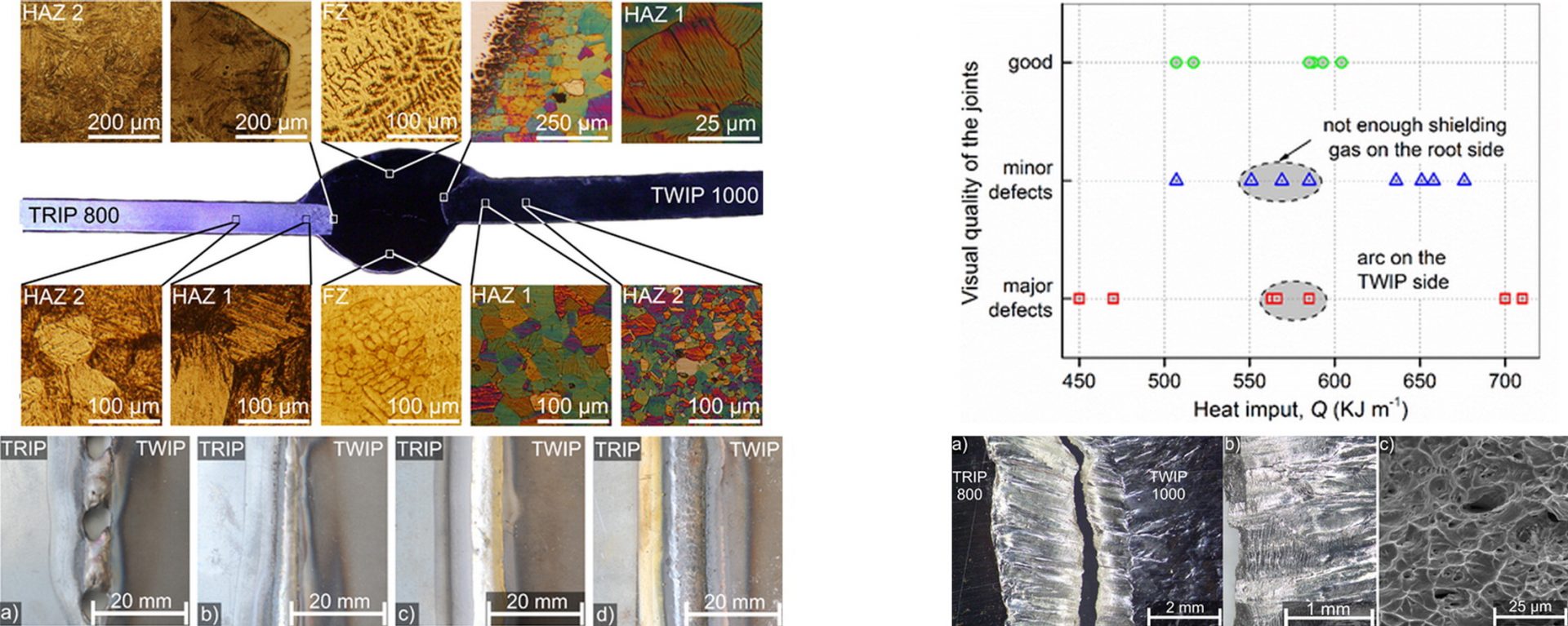
Figure 1: Overview of Dissimilar AHSS GMAW Welding.M-65
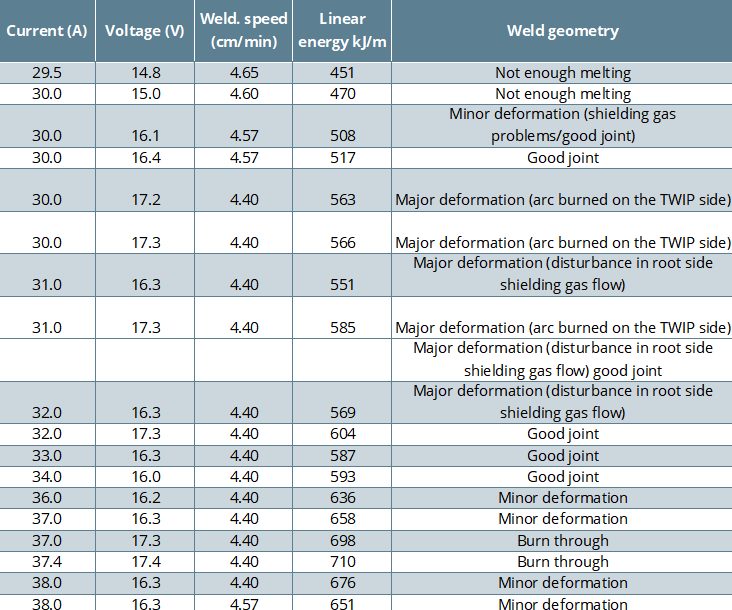
Table 1: Results of the preliminary welding tests in terms of TWIP-TRIP joint quality.M-65
After welding, transverse sections were cut from the welds and etched to show the microstructure. Vickers hardness testing was conducted on the weld samples based on the ASTM E384 standard. Tensile tests were performed on the samples according to the EN ISO 6892-1 standard. Tests were also conducted on unwelded TWIP and TRIP steels for comparison. Scanning electron microscopy (SEM) examinations were made of fracture surfaces to determine failure modes and examine for microscopic weld defects.
The study concluded that dissimilar welds between AHSS steels with the GMAW process can be achieved with consistent results desired for automotive applications.
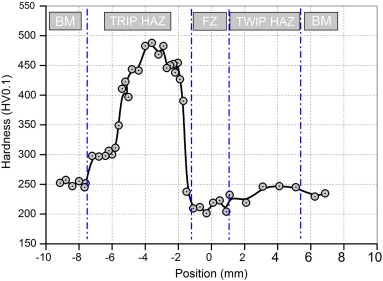
Figure 2: Vickers Hardness Across Weldment.M-65
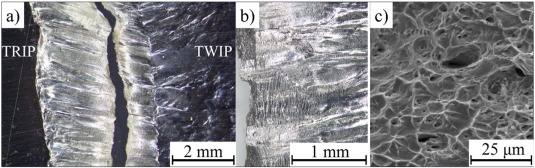
Figure 3: Ductile Failure in the fragile zones (FZ).M-65
Joining
The unique physical characteristics of Advanced High Strength Steels (AHSS) present some challenges to welding and bonding processes. AHSS differ from mild steels by chemical composition and microstructure, and it’s important to note that their microstructures will change from welding operations. For example, intensive localized heat associated with some welding processes causes a significant change in the local microstructure, and hence affect properties. Due to fast Cooling Rates (CR) typical in welding, it is normal to see martensite and/or bainite microstructures in the weld metal and in the Heat-Affected Zone (HAZ).
When joining AHSS, production process control is important for successful assembly. Manufacturers with highly developed joining control methodology will experience no major change in their operations. Others may require additional checks and maintenance. In certain instances, modifications to equipment or processing methodologies may be required for successful joining of AHSS.
The coating methods for AHSS are similar to those for mild steels. Welding of either AHSS or mild steels with coatings will generate fumes. The amount and nature of fumes will depend on the coating thickness, coating composition, joining method, and fillers used to join these materials. The fumes may contain some pollutants. The chemical composition of fumes and the relevant exhaust equipment must meet appropriate regulatory standards. Thicker coatings and higher heat inputs cause more fumes. Additional exhaust systems should be installed. While welding AHSS (with or without metallic or organic coatings and oiled or not oiled) gases and weld fumes are created similar to mild steels. The allowed fumes or gases must comply with respective national rules and regulations.
Joining Processes
Considering recent developments of hybrid approaches to welding, there are now over 100 types of welding processes available for the manufacturer or fabricator to choose from. The reason that there are so many processes is that each process has its list of advantages and disadvantages that make it more or less appropriate for a given application. Arc welding processes offer advantages such as portability and low cost but are relatively slow and use a considerable amount of heating to produce the weld. High energy density processes such as laser welding generally produce low heat inputs and fast welding speeds, but the equipment is very expensive and joint fit-up needs to be ideal. Solid-state welding processes avoid many of the weld discontinuities produced by those requiring melting (fusion), but they may be expensive and often are restricted to limited joint designs. Resistance welding processes are typically very fast and require no additional filler materials but are often limited to thin sheet applications or very high-production applications such as in the automotive industry.
Most welding processes produce a weld (metallic bond) using some combination of heat, time, and/or pressure. Those that rely on extreme heat at the source such as arc and high energy density processes generally need no pressure and relatively small-to-medium amounts of time. This section introduces joining processes that are applicable to HSS automotive applications, while describing unique process attributes.
Arc Welding, Joining
A common issue when welding Advanced High-Strength Steels (AHSS) is with protective coatings causing weld defects. A group of researchers at the NMAM Institute of Technology and Dong-Eui University studied common issues with gas metal arc welding (GMAW) in the cold metal transfer (CMT) mode on a zinc-coated steel.V-2 The study used infrared thermography to observe the welds as they were created, helping to get detailed observations on some defects appearing in real time. With GMAW in CMT mode, the prevailing defect with welding a zinc-coated steel was porosity from metal vapors escaping through the weld. This issue could be addressed by adjusting the heat input and travel speed to provide more time for metal gases to escape.
In Figure 1, it shows that with a higher heat input, more heat is in the weld puddle. In low and medium heat inputs, the puddle is above melting temperature, but not as high as the high heat input. Figure 2 shows that the low heat input also has the fastest solidification rate, and the high heat input has the slowest solidification rate. Figure 3 shows where the zinc vapors from the molten coating evaporate through the weld. In the left picture, at low heat input, the nucleation is contained inside of the weld, and the fusion zone would collect in the fusion zone. In the middle picture, at medium heat input, the zinc vapors bubble out just as the metal starts to solidify. In the right picture, at high heat input, the zinc bubbles out in the weld puddle while it is still molten.
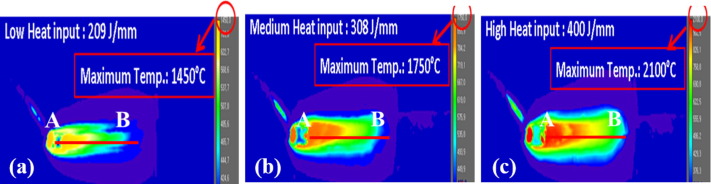
Figure 1: Infrared Thermography of Weld Bead.V-2
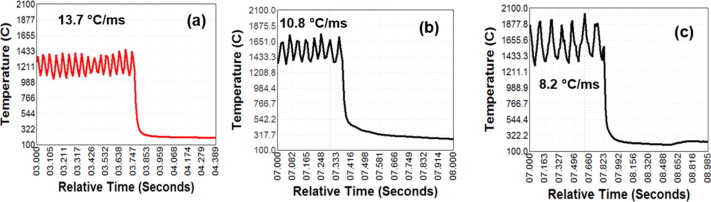
Figure 2: Variation of temperature during CMT for High, Medium, and Low Heat Input.V-2

Figure 3: Variation of Zinc Porosity Position vs Low, Medium, and High Heat Input.V-2
These factors combined indicate several factors that influence zinc porosity in GMAW CMT weldments. The researchers concluded that at low heat inputs, the zinc collects in the fusion zone. At medium heat inputs, the solidification rate and temperature gradient through the weld puddle traps the zinc in the fusion zone but also allows some to bubble out through the weld puddle. This caused the worst material properties of the three weldments for the researchers. At high heat inputs, the zinc bubbles out through the weld puddle, before solidification occurs. This condition is optimal, to reduce porosity with zinc metal vapors, the heat input should be increased so that the weldment temperature increases and solidification rate decreases.
Arc Welding, Joining
In production, part geometry or joint application requires the use of gas metal arc welding (GMAW) to weld the joint. A commonly used Advanced High-Strength Steel (AHSS) is Dual Phase (DP) 600 which contains a hard martensite phase in a ferrite matrix (approximately 5-20% martensite). Under the heat input from GMAW, this microstructure near the weld [in the Heat Affected Zone (HAZ)] is destroyed, and a new microstructure develops. Researchers from RWTH Aachen University in GermanyR-24 used representative volume elements (RVE) in tandem with electron probe microanalysis and micromechanical finite element (FE) modeling to develop flow curves for 2.5 mm hot rolled DP 600 steel sheet. This can be used to help predict mechanical properties in the HAZ. The researchers observed bainite, coarse grain ferrite, and tempered martensite in the HAZ.
The researchers developed an engineering stress-strain curve for the GMA welded DP 600 steel as depicted in Figure 1. The stress distribution concentrates to the outside edge of the HAZ as shown in Figure 2, primarily in the softest regions of the HAZ (Figure 3). The soft region is where ductile failure is observed as seen in Figure 4. The soft region is a result of a loss of bainite and an increase in ferrite grain growth. Because ferrite is steel’s softest phase, it results in this soft region where plastic strain accumulates. The increasing presence of tempered martensite starts to raise hardness after this region.
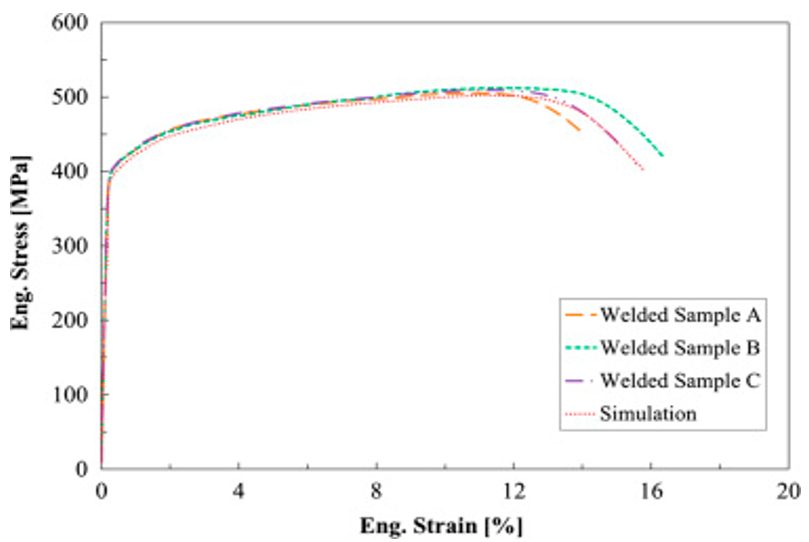
Figure 1: Stress-Strain Curve for GMA Welded DP600 Steel.R-24
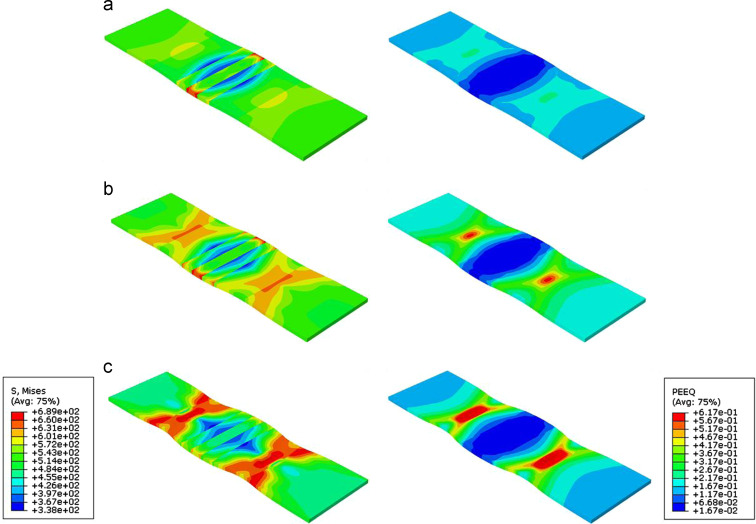
Figure 2: Hardness Map through FZ and HAZ with emphasis on softened zone.R-24
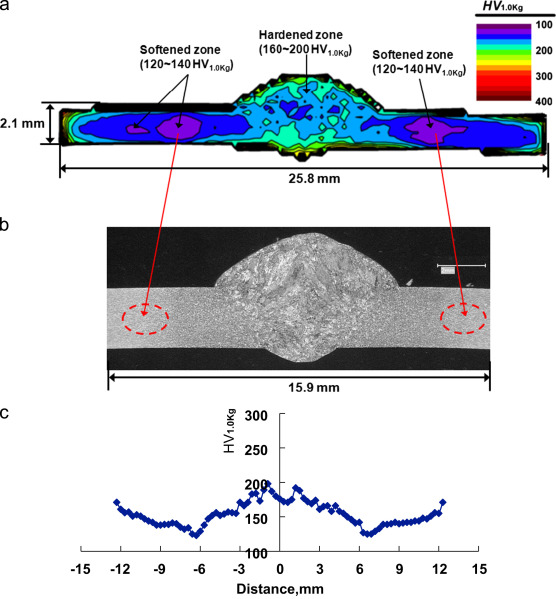
Figure 3: Hardness map of weld and HAZ.R-24
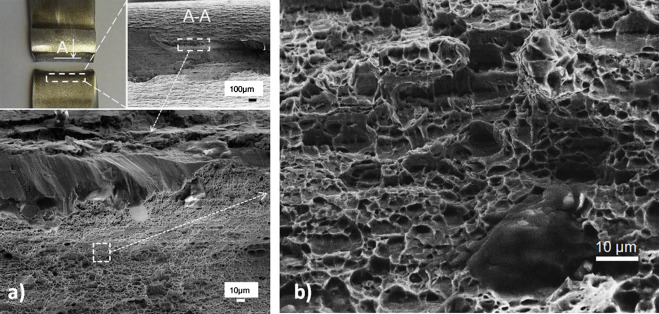
Figure 4: Ductile fracture in softened zone.R-24
The HAZ is composed of a variety of microstructures that vary depending on their distance from the centerline. Close to the middle of the fusion zone, the microstructure is almost 100% bainite with small amounts of ferrite and martensite. Bainite is harder than the tempered steel/ferrite combination, which accounts for the hardness of the fusion zone. Away from the fusion zone, the bainite decreases, and the ferrite increases to where the microstructure is roughly 90% ferrite and 10% martensite, with no bainite in the microstructure (Figure 5).
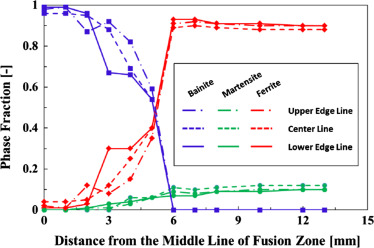
Figure 5: Phase fractions relative to weld centerline.R-24
Arc Welding
This article summarizes a paper by W. Mohr and N. Kapustka, EWI, entitled, “Fatigue of GMAW-P Lap Joints in Advanced High-Strength Steels.”M-13
EWI has performed fatigue tests on welds from four Advanced High-Strength Steels (AHSS) in the uncoated condition. The materials were provided in three thicknesses as follows, 2.0-mm DP 780, 1.8-mm 590 SF, 2.0-mm DP 980, and 2.8-mm CP 800. Referring to Figure 1(a), welding parameters were selected to meet the weld profile requirements listed below:
The travel speed to achieve such combinations was 23 mm/s for three of the sheets and 13 mm/s for the 2.8-mm-thick CP 800. Figure 1 shows a completed panel.

Figure 1: Completed Panel.M-13
Specimens were cut from the lap-welded panels in a configuration recommended by Z 2275, with minimum reduced sections of 20-mm wide, with 20-mm radii on both sides to a full width of 30 mm, as shown in Figure 2.
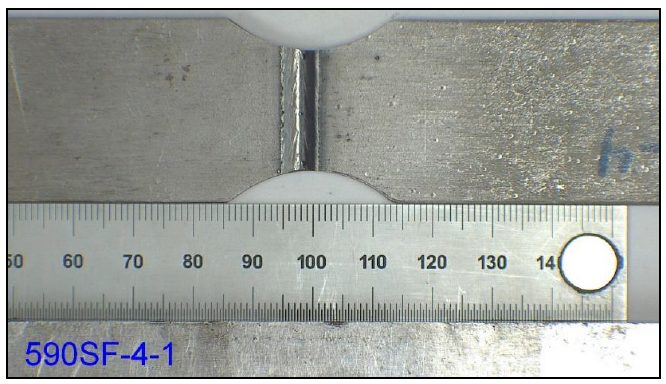
Figure 2: Specimen Design.M-13
Fixtures for the bend testing had eight, 6.3-mm radius rollers, four on top and four on the bottom, with offsets of the roller centers to accommodate the lap-joint configuration and the differing sheet thicknesses. The interior span was 120 mm, while the exterior span was 210 mm. The full bending fixture, with a specimen inserted, is shown in Figure 3.
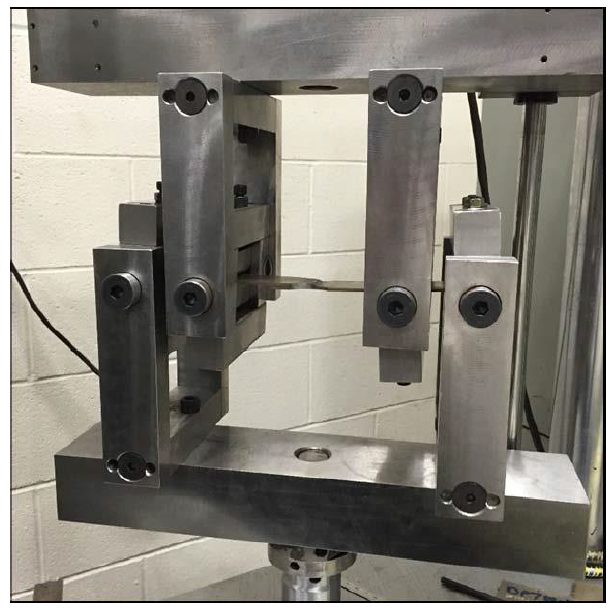
Figure 3: Bending Test Fixture.M-13
Weld profiles were achieved that met the weld profile requirements for each sheet material type. These weld profiles are shown for the four sheet materials in Figure 4. Fatigue testing results in tension at R = 0.3 gave lifetimes between 30,000 and 9 million cycles, with run-outs at 10 million cycles, as shown in Figure 5.
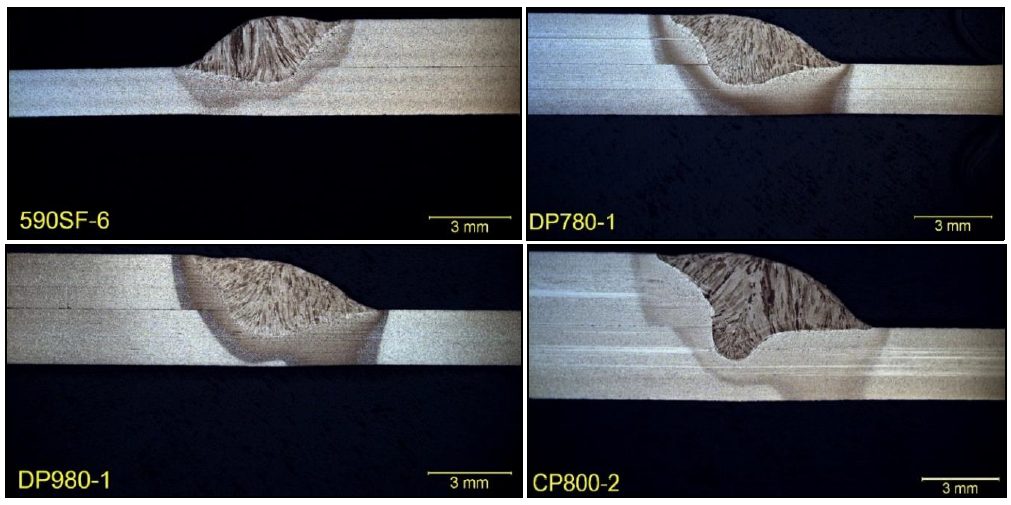
Figure 4: Cross Sections of Lap Joints (etched with 2% Nital).M-13
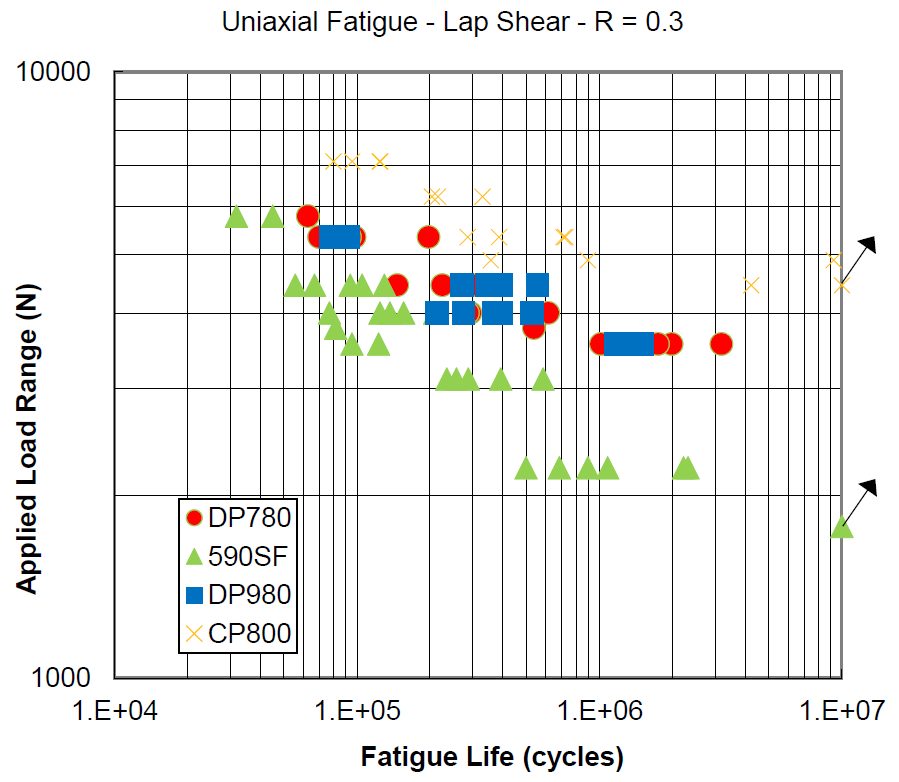
Figure 5: Results of Fatigue Testing in Tension at R= 0.3.M-13
Weld root cracking dominated in the 590 SF, as well as the DP 780 and DP 980, with an example shown in Figure 6. Weld toe cracking was observed on the 2.8-mm-thick CP 800, with an example shown in Figure 7.
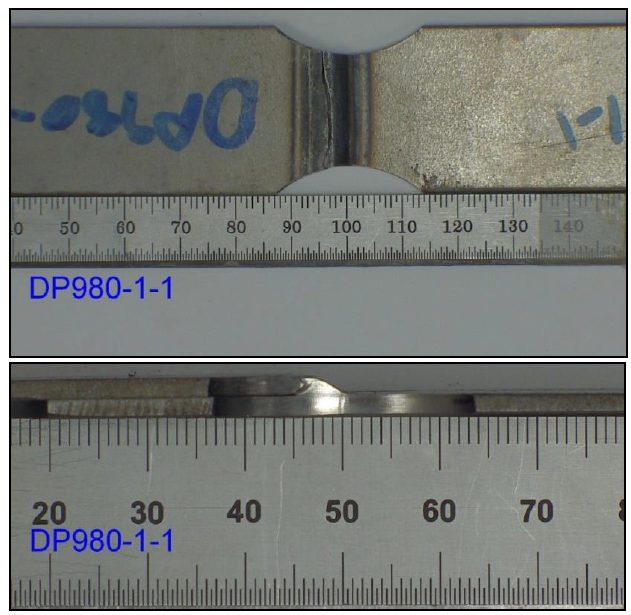
Figure 6: Example for a Root Crack Breaking Through the Weld Metal on DP 980.M-13
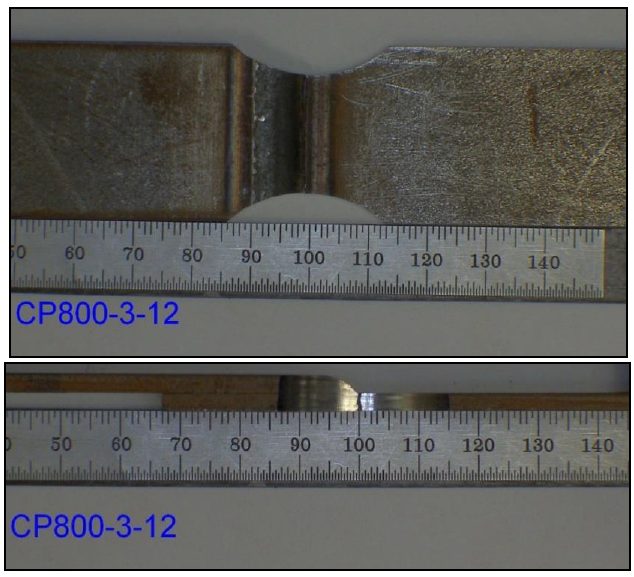
Figure 7: Example of a Toe Crack Breaking Through the Base Metal.M-13
Fatigue testing in bending at R = -1 gave lifetimes between 30,000 and 2 million cycles, with run-outs on tests that continued to up to 7 million cycles, as shown in Figure 8.
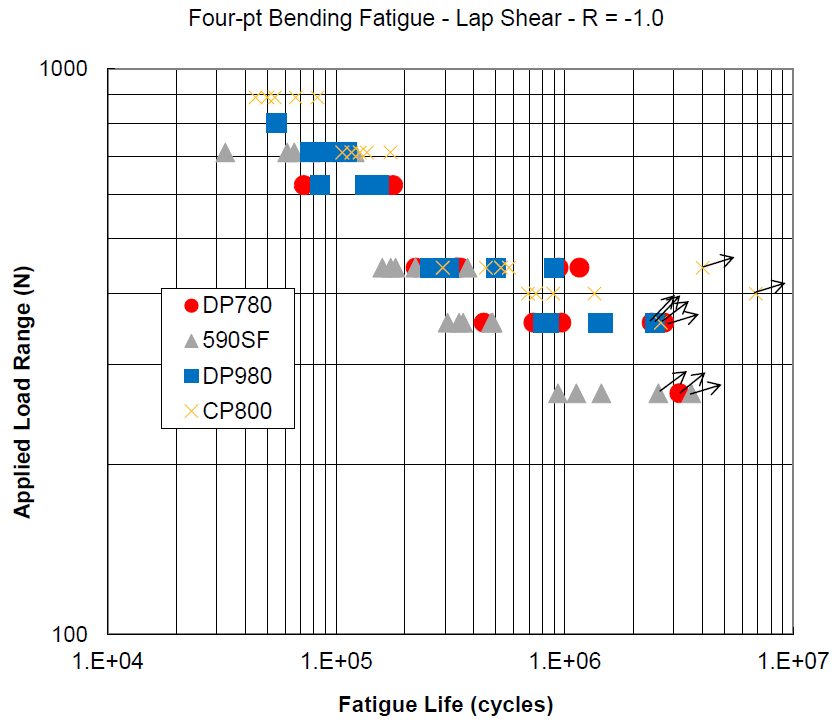
Figure 8: Four-Point Bending Tests at R = -1.M-13
Taking the differing thicknesses, minor variations in minimum width, and the stress concentrations from the radii into account, the concentrated stress range was calculated to compare the four materials on a common basis, as shown in Figure 9.
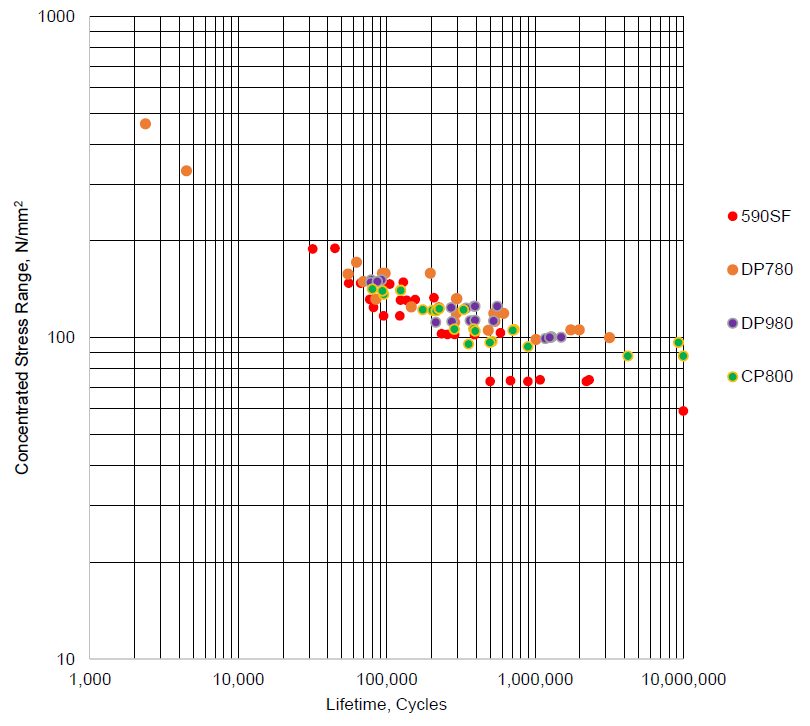
Figure 9: Concentrated Stress Range versus Lifetime for Tension Tests.M-13
The fatigue cracks initiated at the root for the 1.8-mm 590 SF on both tension and bending testing. The fatigue cracks initiated at the weld toe for the 2.8-mm CP 800 on both tension and bending testing. The fatigue cracks initiated from the weld root in the tension testing and from primarily the weld cap in bending testing, for the 2.0-mm-thick DP 780 and 2.0-mm-thick DP 980.