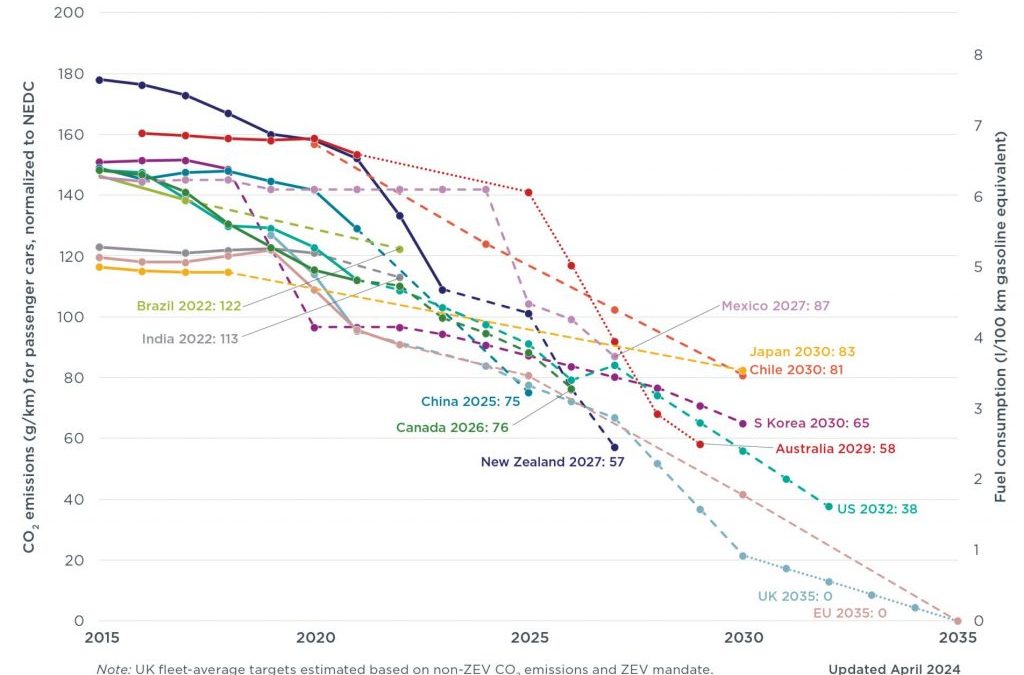
Emissions and Life Cycle Assessment
Vehicle programs must balance performance, safety, fuel efficiency, affordability and the environment, while maintaining designs that are appealing to customers. Use of higher strength steels allows for a reduction in the sheet metal thickness and in turn vehicle mass. The increased ductility offered by Advanced High Strength Steels facilitates part consolidation also contributing to lower weight and manufacturing cost while providing an efficient way to increase component and vehicle stiffness.
Low-density materials like aluminium, magnesium and composites have widespread use in luxury class vehicles, where amenities, comfort, and speed are prioritized over affordability. Penalties for not meeting fuel economy and emissions mandates are easily absorbed in the sales price.
On mass-market vehicles, where per-unit emissions are multiplied over higher volumes, automakers target selecting the most efficient way to achieve the lowest total emissions.
Compared with the limited number of low-ductility steels available decades ago, the lower density materials would have offered an easy but costly path to lightweighting. Back then, since there were not that many high-strength options, vehicle crashworthiness was improved by increasing thickness.
However, increasing metal strength allows for a thickness reduction while maintaining crash performance. The substantially higher strength steels available today have sufficient ductility to form complex stampings from sheets thin enough to be weight-competitive with components formed from lower-density materials that must be made from higher thickness to have comparable stiffness.
The spectrum of steel grades commercially available today have:
- higher strength, greatly contributing to the crash-energy management approach.
- higher ductility that allows for additional shape to be formed into the component, also increasing stiffness and potentially allowing for part consolidation,
- higher modulus than aluminium or magnesium that inherently leads to a stiffer component.
Recent years have seen an increased global sensitivity to tailpipe emissions, with Figure 1 highlighting regulations for passenger cars in different countries and regions. Many major markets have committed to fleet average emissions below 100 g CO2/km, and we’re on a negotiated global journey to Net Zero Emissions by 2050.
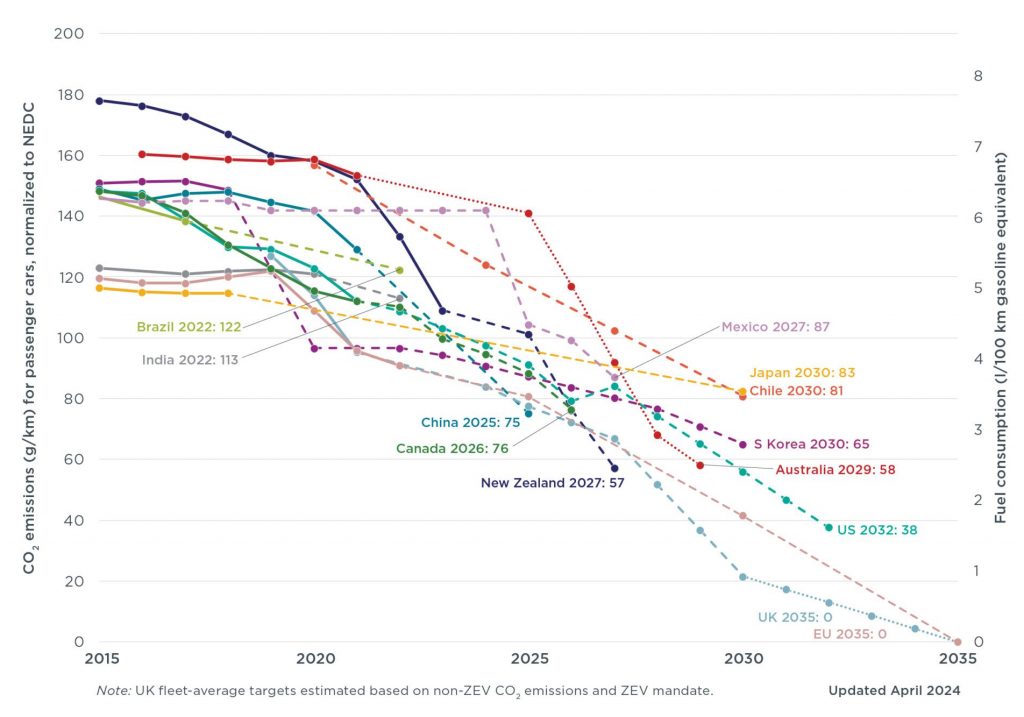
Figure 1: Passenger car emissions and fuel consumption targets, normalized to New European Driving Cycle I-2
The problem with the current regulation of automotive greenhouse gas (GHG) emissions is their focus solely on tailpipe emissions, produced from fuel combustion during vehicle use. The regulations ignore other significant sources of GHG emissions in the vehicle’s life cycle including vehicle production (including the emissions from material production) and treatment of the vehicle at the end of its useful life. This omission comes with serious risks. An unintended effect of this approach is an over-emphasis on vehicle lightweighting. While lightweighting can be an effective tool to reduce vehicle emissions, it must be done with a holistic knowledge of the implications related to the total vehicle life cycle GHG emissions.
Reducing vehicle mass decreases fuel consumption, which also reduces tailpipe emissions. This may, or may not, offset the increased production emissions from material production of the lower density materials. One possibility is that the reduction of emissions in the use phase results in overall lower emissions, but because of the trade-off between the use phase and production emissions, the result is not as low as predicted by a tailpipe-only metric – some of the use-phase savings is offset by the increased production emissions. Also possible is where the use phase savings and the production phase increase are approximately equal, resulting in no net savings at all. In the other extreme, the production emissions outweigh the use phase savings, resulting in the unintended consequences of an increase in the overall emissions. This last scenario is the very opposite of what government policy intends, but happens regularly when vehicles constructed with low density materials don’t reach their intended vehicle life.
One of the perceived advantages to using materials of lower density is the expectation that they will result in lower GHG emissions. To illustrate why this is not true, consider the emissions from the material production stage of a typical automotive component. The mid-range GHG values for each material are taken from the above chart and then multiplied by the projected material weight that is required to make a hypothetical component. (The actual mass for an equivalent component varies based on the material used and the component design.)
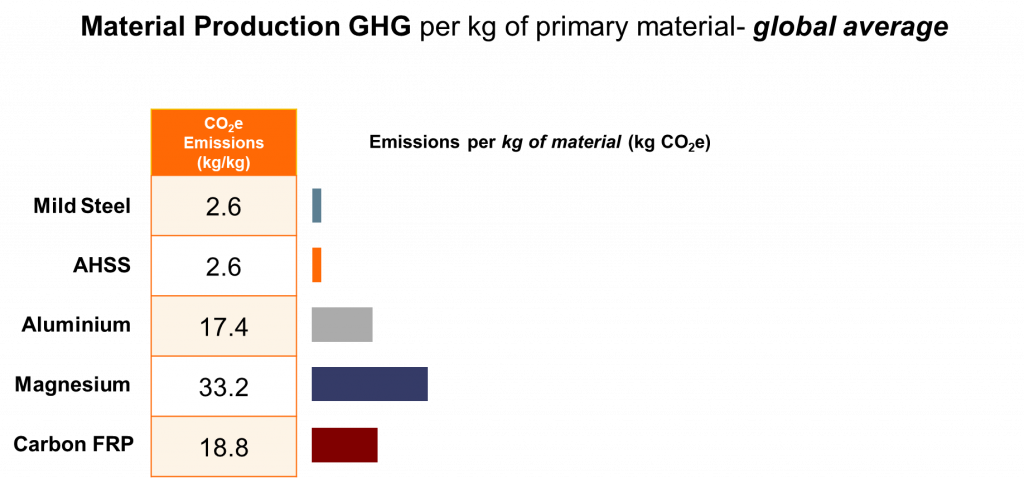
Figure 2: Material average GHG emissions from primary production, in kg CO2e per kg of material.W-40
Furthermore, low-density materials create an offsetting emissions problem, as production of these materials is GHG-intensive, and therefore costly to the environment. The production of these alternative materials can produce 7 to 20 times more emissions than steel, as shown in Figure 2.
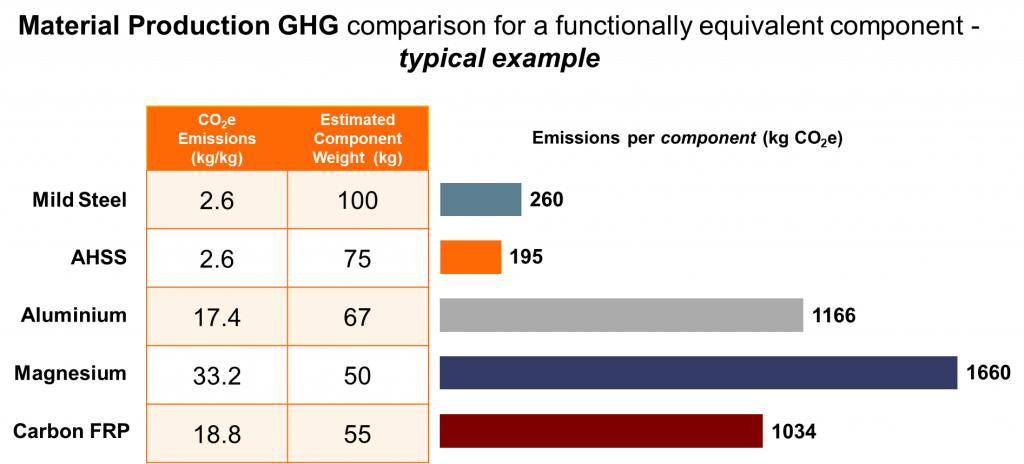
Figure 3: Material GHG emissions in kg CO2e for functionally equivalent generic components.W-40
Figure 3 shows that the use of lower density materials does not necessarily mean a reduction in greenhouse gas emissions. Although less weight is required for some alternative materials to achieve the same component functional performance, the emissions from the material production stage can still be many times higher than those of the baseline component. Therefore, the increase in material production emissions may outweigh the reduction in use phase emissions even after factoring in the mass savings benefit.
Vehicles are transitioning to alternative-energy powertrains and away from those based on fossil fuels. In these new-energy vehicles powered entirely by renewable electricity, emissions from the vehicle production stage, which includes material production, could account for as much as 95% of total emissions. In this scenario, the usage phase accounts for a mere 5% of the lifetime emissions. This is the opposite of what is found with vehicles having conventional Internal Combustion Engine (ICE) powertrains. For this reason, use of low GHG material such as steel becomes even more important as the world moves towards a renewable future.
Life Cycle Assessment
Life Cycle Assessment (LCA) is an environmental accounting methodology that considers a product’s entire life cycle, with cradle-to-grave assessments typically including impacts from raw material extraction and production (manufacturing phase), through its useful life (use phase), and to the end-of-life disposal or recycling of the product (end-of-life phase). It also takes into account the full life cycle of energy sources used across all lifecycle phases. This process illuminates any potential trade-offs between phases and highlights the true environmental impact, beyond the focus on tailpipe-only emissions.
Recent years have seen a greater adoption of using Life Cycle Assessment to assess a vehicle’s true environmental impact rather than solely focusing on what comes out of the tailpipe. LCA accounts for the total emissions including those coming from material production, vehicle use, and the chosen end-of-life path. The principles, framework, requirements and guidelines for Life Cycle Assessment are laid out in international standards ISO 14040I-3 and ISO 14044I-4.
Most major OEMs utilize some form of life cycle thinking or LCA, recognizing its importance and effectiveness in product and process design. Material producers also accept and use LCA. Together with many of their member companies, the trade associations of the steel, aluminium, and plastics industries are among the most active members of the global LCA community.
The European Union requires accounting for embedded lifecycle emissions. Following a phase-in period, there will be monetary penalties assessed against companies not providing this information. These requirements will drive OEMs to demand pertinent details from all of their material suppliers.
Environmental policies target achieving a total net reduction in emissions, including GHG (measured in carbon dioxide equivalents, or CO2e, that is a measure of all greenhouse gases attributable to a product that affect global warming potential. Thus, CO2e includes gases other than CO2.
Properly applied, LCA enables automakers to ensure that improvements in one phase are not offset by worse performance in another phase. This assessment of potential trade-offs is critical to environmental improvement. For example, if the increase in production emissions of a lightweight material is greater than the decrease in use phase emissions, vehicle light-weighting in this manner counter-productively increases total emissions.
LCA can be used to assess a broad array of environmental impacts beyond the global warming potential of greenhouse gases, including acidification, ecotoxicity, and ozone depletion.
The Path To Net Zero Emissions
Fully autonomous Mobility as a Service vehicles such as the Steel E-Motive concept have the potential to address the ongoing and future requirements for decarbonisation of passenger transportation. Figure 4 shows the emissions walk-down beginning with a present-day C-sized BEV operating as a taxi.
Near term, a 60% reduction in Life Cycle emissions can be realized by an increased use of reduced CO2 steel and decarbonized battery production, along with an increased use of ride-sharing. Through 2035, as all available emissions reduction strategies are deployed – including autonomous MaaS vehicles with increased occupancy and extended vehicle and battery lives – an 86% reduction in emissions from a 2022 baseline is feasible.
Achieving Net Zero post 2035 requires carbon capture technologies, 100% renewable grid supplies, and carbon offsets or credits.
Each of these steps are described in detail within the Steel E-Motive Engineering Report.