Blog, main-blog
Here at WorldAutoSteel, we have been studying the changes in the automotive industry for several years, focusing particularly on ride sharing, autonomous, electric vehicles and steel’s role in that marketplace. George Coates, Technical Director for WorldAutoSteel and The Phoenix Group, has been leading that effort and today contributes an article on the disruption of future mobility to the industry and the great opportunities we see for steel in meeting the challenges providers will face. We hope you enjoy the read, and we welcome your thoughts and comments. What changes and impacts do you envision for vehicle manufacture? How do you feel about the world of autonomy?
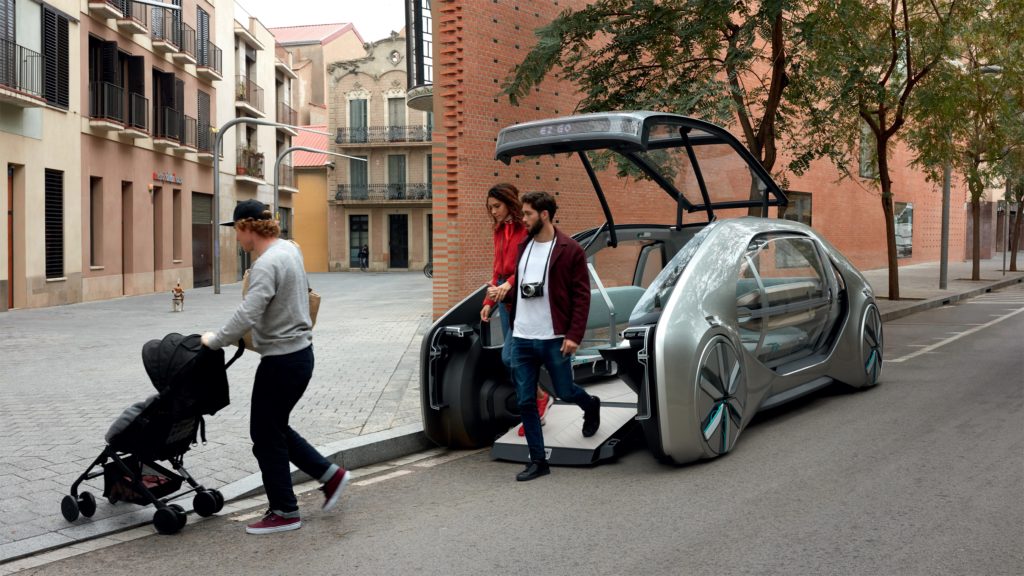
Renault’s Future Mobility concept, the E-Z Go
We’re approaching a critical milestone in automotive history when what we know as normal is about to change significantly. Future Mobility describes the revolution that’s already begun. We’re rethinking transportation from the movement of a vehicle to a more efficient concept for moving people and things. We’re about to discover the social advantages of connected, autonomous, shared and electric vehicles. And we’re completely changing the way we view transportation.
By 2030, electric vehicles (EVs) will be mainstream—not just within the premium segment, as they are today. EV’s will be popular and available across all vehicle variants and prolific in the commercial vehicle industry and in public transportation. Owners and fleet providers will experience the lower costs of electricity, lower maintenance costs, and the lower overall total cost of ownership (TCO). Fully autonomous or self-driving vehicles will introduce design freedom never experienced before, with the removal of the steering wheel, foot pedals and conventional dashboard. Communication and comfort will be re-imagined, with a vehicle that’s no longer designed around the driver but designed to serve the needs and comfort of the occupants, who are now users instead of owners.
With the rise of mobility services such as Uber, Didi, and a host of others, vehicle ownership is fast becoming an option. In a very short time, especially in urban areas such as China’s mega-cities, it is becoming cost-efficient to subscribe to a monthly ride share service for all of your transportation needs.
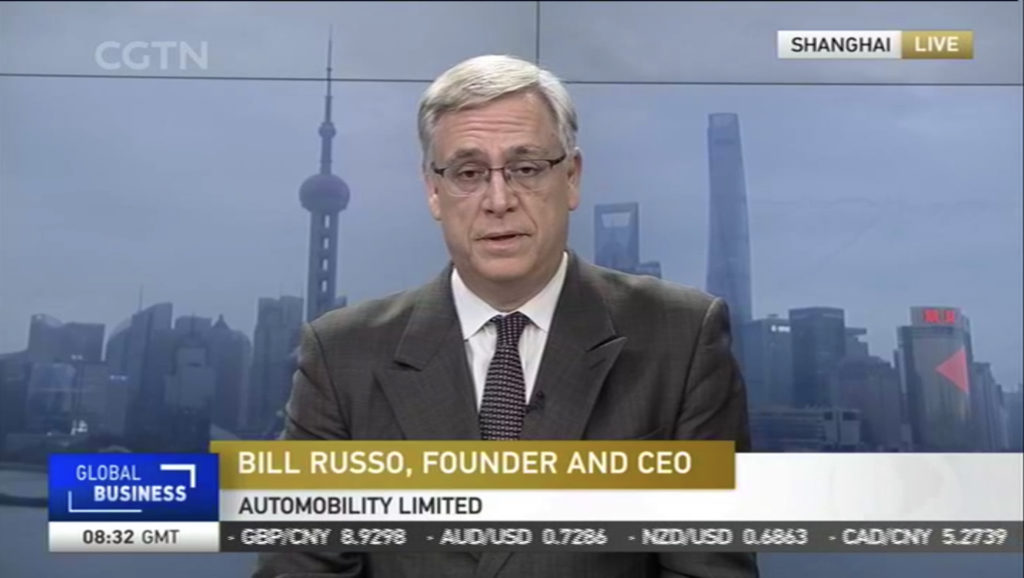
Bill Russo, CEO, Automobility LTD
Bill Russo, CEO of China-based Automobility, in a December 2018 article, Competing in the Digital Internet of Mobility, notes that the digital connectivity of these vehicles will open up profit opportunities well beyond the vehicle hardware. He says “An expanded understanding of mobility use cases and tailoring of the mobility hardware ‘form factor’ to the particular mobility need will be a way to create a value proposition that is rooted in the unique riding experience. In the user-centric world where users are passengers, the focus shifts from traditional driver-centric design to a user-centric productivity space. Instead of traveling in the cockpit, we will move in business class or economy class, depending on our preferences and budget.” Cities will be re-imagined in new social opportunities associated with autonomy, as these vehicles will serve the under-served, and infrastructures will shift in purpose to move people, as opposed to moving vehicles.
Where does steel fit?
The steel industry plans to be right in the middle of this revolutionary change. Fleet owners who provide ride hailing and ride sharing services need to manage the total cost of ownership, while maximizing the user experience for added revenue. To be profitable, they’ll want durable, lasting structures that are affordable to own, provide the user motion as well as emotional comfort, while being efficient to operate, and environmentally friendly – and steel is the only material that meets all these requirements.
On Camera Now: George Coates, Technical Director, WorldAutoSteel and Phoenix Group from worldautosteel on Vimeo.
As always, steel is needed for the crash safety structures, and now add battery protection. Our market intelligence shows that due to the high cost to municipalities and regional governments, autonomous-only vehicles will be limited to dedicated areas for a long time to come. Meanwhile, vehicle-to-vehicle and vehicle-to-infrastructure connectivity will result in dramatic improvements in accident avoidance and reduced fatalities.
Because it will take many years before all vehicles on the road have these technologies in play, the need for passive safety will remain for the foreseeable future. Developing a structural design for the passenger compartment becomes challenging, since there’s a now a need to strike a balance between occupant safety and the occupant freedom. This is enabled by removing the driver and controls from the interior. Steel will be needed to provide the unique properties of both crash energy absorption and deflection, while also managing the loads associated with passengers in multiple and diverse seating configurations. Steel has the ability to provide needed strength while keeping the material thin, which lends more room in the passenger cabin for new seating arrangements and more seats. And battery housings made from steel will provide structural integrity for crash management, while also preventing battery pack damage and leakage.
Lightweighting will continue to be important in an effort to balance smaller battery sizes with maximum range. The steel industry has been and will continue to develop products, such as the ever-growing family of Advanced High-Strength Steels (AHSS), to meet both the mass reduction and the safety targets, affordably. With content innovation and the amazing flexibility of the Iron (Fe) element, researchers still have vast development possibilities for new steels that are stronger, more formable and cost effective.
Blog
Product benchmarking is the process of measuring and analyzing the performance of competitive products. Data from a benchmarking analysis is used at the early stages of product development where performance targets are being set for a new vehicle. As an example of benchmarking, consider setting the mass target for the body structure of a new vehicle program. We want to set a target that is light weight, but also one that is possible to achieve. We benchmark two competitive body structures to help us set the target, Figure 1.
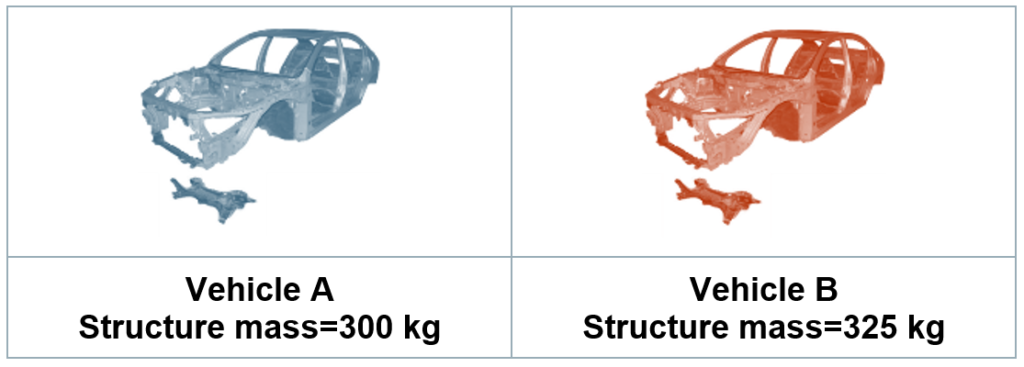
Figure 1: Mass data for two benchmarked vehicles.
From this limited data, it appears a sufficient target for the new program would be 300 kg, the lighter of the two. But there are questions to be resolved: Are these two structures representative of efficient light weighting? Also, if the vehicle under design is of a slightly different size than these two vehicles, how will this affect the applicability of benchmark comparison?
A means to begin to address these concerns is simply to look at more benchmark vehicles. The tear-down database at A2Mac1 Automotive Benchmarking contains mass data for several hundred vehicles. From this database, structure mass for 280 steel sedans is plotted in Figure 2. This expanded data allows us to see a more complete picture of the range of mass exhibited in the market place. Vehicle A and B considered before no longer stand out as exceptional. While this additional data provides an understanding of the average and range of body structure mass, there are concerns with interpreting this chart. Do the lighter structures represent efficient designs or are they just the structures of smaller vehicles?
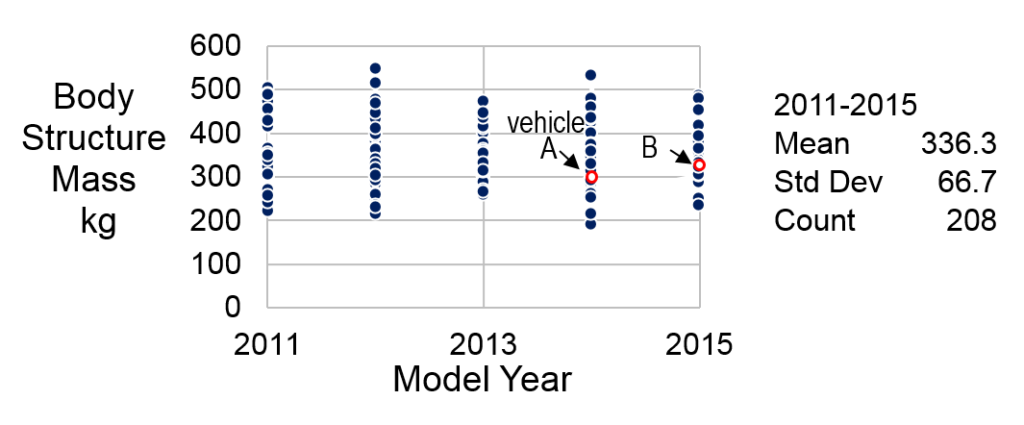
Figure 2: Body structure mass data for 280 benchmarked vehicles.
We can answer this question by investigating how structure mass varies with mass drivers. Two mass drivers for body structure are vehicle size as measured by plan view area, and structural loading taken to depend on the Gross Vehicle Mass. In Figure 3 we use the same vehicles shown in Figure 2, but now plot structure mass versus each mass driver.
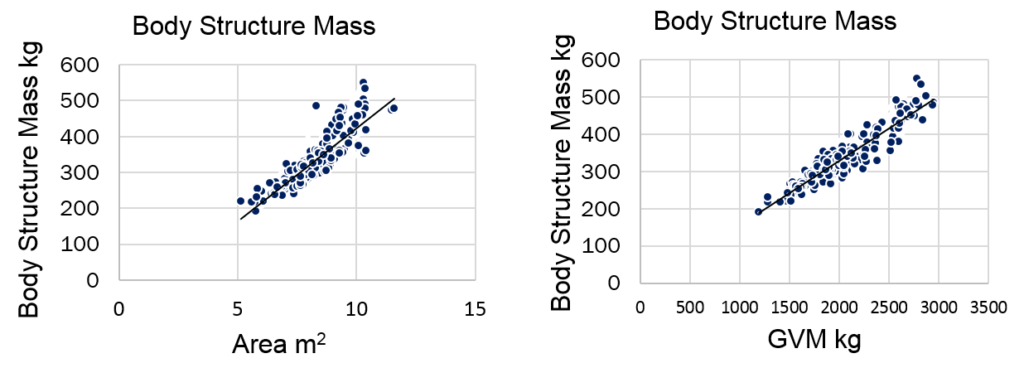
Figure 3: Structure mass vs. vehicle plan view area (left), and gross vehicle mass (right).
The correlation of structure mass for each of these mass drivers is very clearly demonstrated by the trend lines shown: Body structures are heavier for larger cars (left graph), and heavier when they must support greater vehicle mass (right graph). We can quantify these correlations with an equation determined by statistical regression, Equation 1. This equation represents the mass of an average or typical body structure, given its GVM and Area.
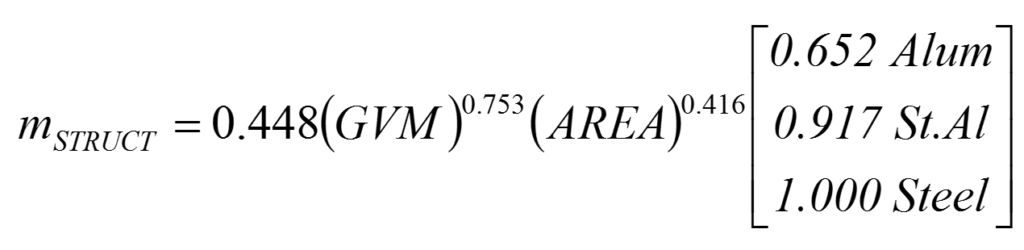
Equation 1
where
mSTRUCT=Mass of body structure (kg)
GVM =Gross vehicle mass (kg)
Area =Plan view area (Length x Width) (m2)
Now for each of the vehicles in our original data set we can calculate the expected structure mass using the vehicle’s GVM and Area. Figure 4 plots the actual measured structure mass vs. the mass expected for that vehicle using Equation 1. The diagonal line indicates those vehicles where the body mass is average or typical. For those structures above the line, body mass is heavier than expected given the area and GVM of the vehicle. And for those below the line, body mass is lighter than expected. This group below the line are the mass efficient body structures that are of interest for fuller analysis.

Figure 4: Actual measured structure mass compared to that expected using equation 1.
Note that looking only at structure mass, as in Figure 2, does not lead to understanding which structures are efficient. For example, Vehicle A in Figure 1 is the lighter of the two structures, 300 kg vs. 325 kg. However, after accounting for the two vehicle’s area and GVM, it can be seen from Figure 4 that Vehicle A is above the diagonal line, indicating a heavier than expected structure, while Vehicle B is on the line indicating it has a typical structure mass.
As a further example, consider the WorldAutoSteel FutureSteelVehicle (FSV). The FSV project, completed in 2011, investigated the weight reduction potential enabled with the use of Advanced High-Strength Steels (AHSS), advanced manufacturing processes, and the use of computer optimization. The resulting material use and body structure mass are shown in Figure 5.
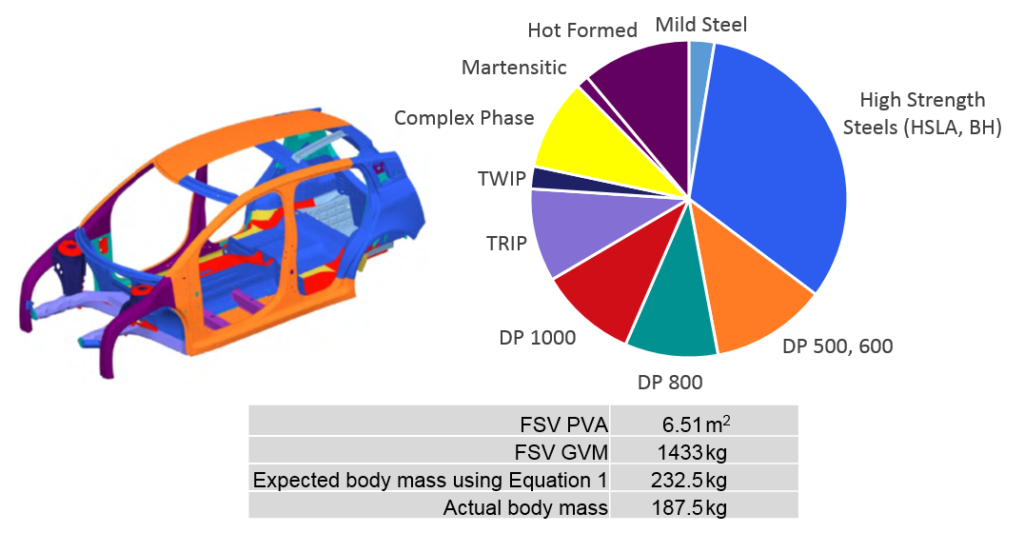
Figure 5: FSV material application and resulting body structure mass.
We can now graph the actual FSV structure mass with expected mass, Figure 6. The data point is well below the diagonal line quantifying the exceptional mass reduction enabled through extensive AHSS use.

Figure 6: FSV body structure compared with 280 normalized benchmarked structures.
Finally, statistical benchmarking reveals which current products would benefit most from lightweighting. Looking again at the plot of actual vs. expected body structure mass for a fixed expected mass, in this case 300 kg, Figure 7. For this set of similarly sized vehicles, there is a wide range of variability in actual mass, indicated by the arrow. For the several vehicles above the diagonal, these body structures are heavier than expected and have significant potential for lightweighting.

Figure 7: Variability in structure mass for similar size vehicles.
For more information on the statistical benchmarking method, see the studies referenced in No. 2 and 3 below. Dr. Malen’s statistical benchmarking methodology also is documented in SAE Paper No. 2015-01-0574
References:
1. A2Mac1.com, Automotive benchmarking.
2. Malen, D., Nagaraj, B., Automotive Mass Benchmarking 2017 study
3. Hughes, J. & Malen, D., Statistical Benchmarking of Automotive Closures, Great Designs in Steel, 2015,
4. FutureSteelVehicle Overview Report, April 2011,

Dr. Donald E. Malen University of Michigan
Dr. Donald E. Malen is an adjunct faculty member at the University of Michigan where he teaches graduate level courses in Automobile Body Structure and Product Design. Prior to this, he was an engineer with General Motors Corporation for 35 years. His background at GM was in automotive body structure design and analysis, and systems engineering. While at GM, he worked on many new vehicle programs and has brought this experience to his teaching and writing. Dr. Malen consults and conducts international seminars on Body Engineering, Innovation, Lead Time Reduction, and Decision Making During Preliminary Design. He holds several patents related to automobile body structure and vibration. His education includes a Ph.D. in Mechanical and Industrial Engineering from the University of Michigan, an MS from Massachusetts Institute of Technology, and a BSME from General Motors Institute (Kettering University).
Blog, main-blog
Introduction
The introduction of Advanced High-Strength Steel (AHSS) to light vehicle body structure applications poses a significant challenge to organizations involved in vehicle repair. AHSS grades are typically produced by non-traditional thermal cycles and contain microstructural constituents whose mechanical properties can be altered by exposure to elevated temperatures. This temperature sensitivity can alter the mechanical behavior during repair welding or flame straightening, thus seriously affecting the structural performance of the AHSS components after the repair.
The American Iron and Steel Institute, with automotive partners – FCA US LLC, Ford Motor Company, General Motors Company – and I-CAR, have completed studies examining the mechanical behavior of various AHSS products after exposure to typical repair arc welding and flame straightening temperature cycles. Recommended practices for repairing components made of these materials were also developed. The studies evaluated many of the AHSS grades being applied and built into vehicle structures today.
AHSS Thermal Evaluation
Several steel grades were evaluated for their sensitivity to thermal exposure taking place during heating to soften the material for straightening, typically by flame. The test results, conclusions and recommendations contained herein are the consensus views of the team members.
A time-temperature test matrix was developed to represent the various thermal conditions encountered during repair welding and flame straightening as shown in Table 1. Individual steel performance result discussions are based on this test matrix and discussed by grade category and specific type.

Table 1: Time-Temperature Test Matrix.
Steel Performance
Conventional Steels
Interstitial free (IF) and high strength low alloy (HSLA) steels are conventional steel products which are essentially a single phase ferrite microstructure and obtain their strength by the addition of chemical elements. These steels have been used in body structures and closures for many years and are well-known to be repairable without substantial performance degradation by arc welding and flame straightening. For repair processes, this means conventional steels can be subjected to heat during repair with the finished repaired component having mechanical properties greater than the properties of the as-received steel. However, it is recommended heating is kept below 750 degrees Celsius to ensure no degradation in properties (Figure 1).

Figure 1: Ultimate tensile strength of Grade 4 IF and HSLA 340 steel after exposure to simulated repair thermal cycles.
Advanced High-Strength Steels
Dual Phase (DP) Steel
DP steels range in strength from 500 MPa to 1200 MPa and obtain their properties from the introduction of a martensitic phase into the ferrite microstructure. The ferrite phase provides formability, while the martensitic phase provides the improved strength. This category of steel grades obtains its microstructure, and thus its mechanical properties through a combination of alloying elements and thermomechanical processing. The processing involves some holding time at elevated temperatures and cooling at specific rates.
Two grades of DP steel were tested, DP 600 and DP 780. The number indicates the ultimate tensile strength (UTS) level of the material in MPa and is the common way to name these grades. UTS for both grades decreases with elevated temperature at a much faster rate than for conventional steels and is illustrated by DP 600 in Figure 2. At temperatures above 650 degrees Celsius the strength suddenly increases then upon additional heating decreases. This behavior is a result of changing the microstructure created during the original thermomechanical processing of the material. Once the microstructure is changed, it is very difficult to return it to its original state in a repair shop environment. Therefore, it is not recommended to subject DP steels to any kind of elevated temperature process for straightening or removing dents. The recommended repair procedure is to remove and replace the DP component. OEM repair guidelines and procedures should be referenced for approved cut and weld lines for replacement.
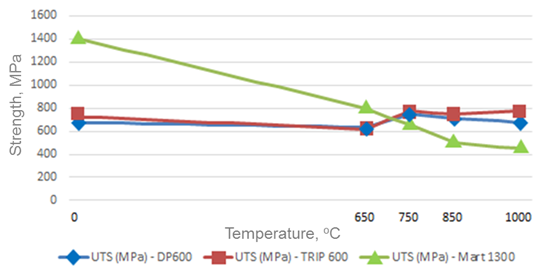
Figure 2: Ultimate tensile strength of advanced high-strength steels after exposure to simulated repair thermal cycles.
Transformation Induced Plasticity (TRIP) Steels
TRIP steels have a similar range of strength as DP steels, 500 MPa to 1200 MPa, while providing improved formability. The improved formability is obtained with the introduction of additional phases of austenite and bainite into the microstructure. These phases improve the work hardening properties of steel and provide additional energy absorption characteristics. TRIP steel microstructures are obtained in a similar manner as DP steels, and therefore have similar behaviors when heating.
TRIP 600 and 780 were evaluated in the studies and confirmed the expected results as demonstrated by TRIP 600 in Figure 2. Heating during repair of TRIP steel will also adversely affect their mechanical properties and thus the performance of the as repaired component may be compromised. OEM recommended repair procedures are similar to DP steels.
Martensitic Steel (MS)
MS steels typically have a microstructure of 100 percent martensite and have tensile properties greater than 980 MPa. Martensite is the strongest microstructural phase in steel and is obtained by alloying and rapid controlled cooling. This grade is used in areas where exceptional strength and anti-intrusion are needed, including such applications as the A-pillars, B-pillars, rockers and rails.
The effect of heat on MS 1300 is shown in Figure 2. Like other AHSS, it is adversely affected by heat and the performance of the as repaired component may be compromised. Thus, heat should be used only as outlined in OEM repair procedures.
Summary
The steel industry, working closely with automotive OEMs and the repair community, have developed and validated repair procedures applicable to the new AHSS used in today’s vehicles. Each OEM has taken the results from the AHSS repairability studies and developed their own repair guidelines.
The steel industry continues to develop AHSS grades with strength levels at and above 1000 MPa. These microstructures contain martensite and will be affected by heat exposure during repair as shown in previous studies. Collaborative studies will continue to update repair procedures for higher strength AHSS, including DP, MS and Press Hardened grades, and new 3rd Gen. AHSS as they are introduced.
Blog
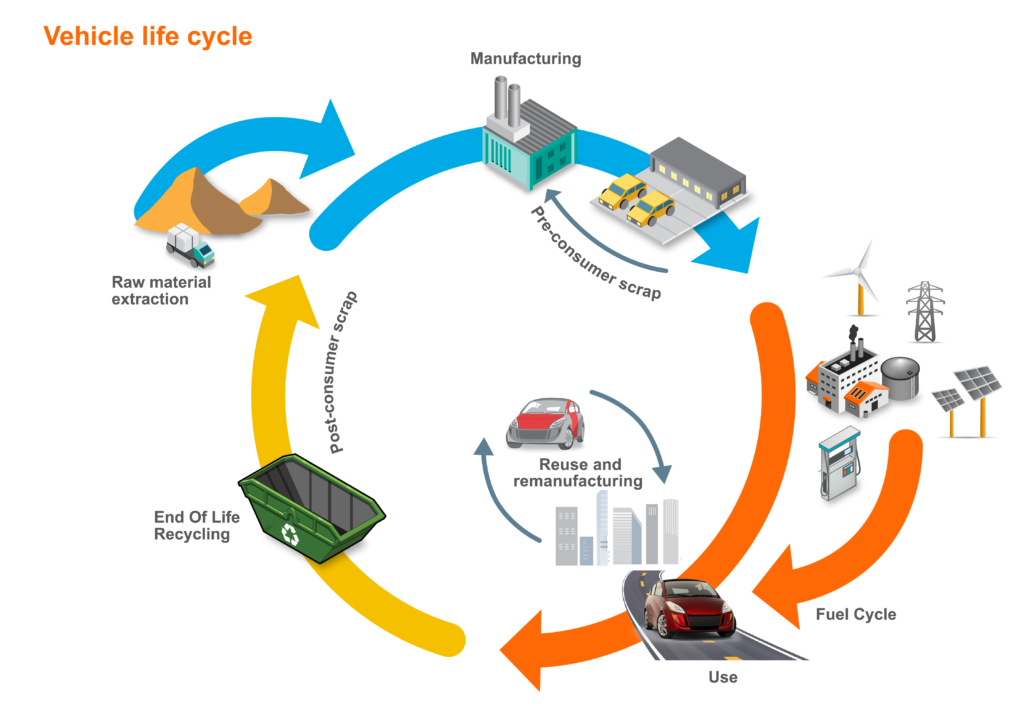
Vehicle LCA encompasses all phases of the product cycle, from raw material extraction to end of life recycling and disposal.
Life Cycle Assessment (LCA) continues to gain traction as the preferred method for assessing the environmental impacts of a product, and we are seeing more and more automotive LCA studies, and claims or conclusions based on LCA, being published. Here are five things to look for in an automotive LCA study. This is not an exhaustive list – there are many more things that need to be considered when conducting an LCA (the international standard that lays out requirements and guidelines for LCA, ISO 14044, lists 14). For a detailed look at LCA, I recommend Environmental Life Cycle Assessment, an excellent textbook published by the American Center for Life Cycle Assessment (ACLCA).
1. Is the study comparing “apples to apples”?
This can sometimes be a bit of a challenge in an automotive LCA, as cars are complex products made up of many systems and sub-systems, with supply chains that reach around the world. It is easy to lose sight of apparently subtle differences.
One such difference arises in material comparisons of an existing product and one at the design stage. Before making choices about which material has the lower impact, it is important to decide if this is a fair comparison. Have both designs been fully optimized? Does the theoretical design meet all the requirements (e.g. crash, NVH) of an existing design that has gone through all the additional steps necessary to get to production?
Functional equivalence is another important factor to consider. For example, it would be inappropriate to compare the “body” of a vehicle with a body-on-frame design with the “body” of a vehicle with a unibody design. Though both systems are casually referred to as the “body”, their functional requirements are very different. Similarly, when comparing an assembly of stamped parts to a single casting, it is important to include all the stamped parts that are required to meet the same functional performance as the cast part.
2. Has the best and most appropriate data been used?
As with any assessment tool, data is key, and there are many factors that can help determine which is the most appropriate to be used in a particular study. There are ten of these factors listed in ISO 14044, but I will only talk about three of them here. If you want more detail, Guidance on Data Quality Assessment for Life Cycle Inventory Data, published by USEPA’s National Risk Management Research Laboratory is a great resource.
Temporal scope – the temporal scope of the data describes when the data was collected, as well as the time period to which the data applies. An often-used rule of thumb is that the data used for the study should be no more than five years old. The goal is to use either data that reflects the time period when the product under study was actually produced or the most recent data that captures the current state of the art (these may of course be the same thing).
Geographical scope – the geographical scope of the data describes the location to which the data applies. This is critical, as the same process may have a very different impact profile in different locations. For example, primary aluminium made largely using electricity from hydropower in Canada will have a much different impact from primary aluminium made in China, where the electricity used comes almost entirely from coal. With automakers increasingly developing global platforms (i.e. using the same parts all over the world, as often as possible), it is important to consider how the results of an LCA might change if a product is produced in a region other than the one studied. The same is true when considering where a product is used. For example, the differences in electricity generation in Canada and China will greatly affect the impact of charging an electric vehicle.
Technological scope – the technological scope of the data describes the technology to which the data applies. Often the same product can be made from a variety of production pathways. Much like production in different regions, production via different pathways can result in much different impacts. An example of this is primary magnesium production. Magnesium produced via the Pidgeon process (a declining, but still-used method) can have a global warming impact more than 1.5 times higher than magnesium produced via the electrolytic method.
3. How sensitive are the results to changes in the choices made?
Because LCA involves choices about things like data and functional requirements (as well as a host of other parameter choices), it is important to understand what happens to the results if different choices are made or underlying conditions change. Inclusion of a sensitivity analysis of this kind allows us to evaluate the results of an LCA and look for areas that might require further study, perhaps by looking for more precise data. It could also affect decisions we might make based on the results. If the results of a study are very sensitive to the location in which the materials are made, we want to evaluate this if we are considering making the product in many different places.
4. What is the fundamental approach taken?
ISO 14040, which lays out the principles and framework for LCA, describes two fundamental approaches to LCA:
- one which assigns elementary flows and potential environmental impacts to a specific product system typically as an account of the history of the product, and
- one which studies the environmental consequences of possible (future) changes between alternative product systems.
It is important to consider which approach was used, and what the chosen approach means in terms of interpreting the results. In a very basic sense, the key lies in the words “history” and “future”. A study that considers the historical impact of a product (i.e. the impact of any product that has already been made) tells us about the impact of that particular product, but may be of limited use in making decisions about what the impact of that same product may be in the future. Studies of the potential future impact of a product, while necessary for decision making, are fraught with all the perils of predicting the future. Both approaches are valuable, and it is important to understand which approach was taken in order to make decisions about how to use the results of the study. The ILCD Handbook: General guide for Life Cycle Assessment, published by the Joint Research Center of the European Commission, provides guidance on when to use each approach in assessing the technological representativeness of LCI data.
5. How broadly can I apply the results?
It is often tempting to apply the results of a study more broadly than is justified. Given all the factors listed above (as well as the many others not included), it is critical that careful consideration be given when making decisions based on the results of automotive LCA studies in order to make sure that the scope of the study is in alignment with the scope of the decision. It is clearly inappropriate to make global decisions based on local studies, or to make future decisions based solely on past conditions. LCA is a valuable, well-developed tool for assessing environmental impacts, but we must be careful to use it appropriately.
The UCSB Automotive Energy and GHG Model, developed on behalf of WorldAutoSteel, is a publicly available, peer-reviewed tool for the assessment of automotive emissions on a life cycle basis. Version 5 of the UCSB Model can be downloaded for free at www.worldautosteel.org. At the UCSB Model page, you’ll find a video workshop at the end featuring Russ Balzer explaining the contents of the Model. A user guide is also available for download.
Does the subject of Life Cycle Assessment confuse you or would you like to learn more? There is a great free online course at our sister organization steeluniversity, “Introduction to LCA”, taught by Dr. Matthias Finkbeiner, head of the department of Sustainability Engineering at Technical University of Berlin, who introduces LCA methodology to analyse the environmental burdens of product and service systems. The course is fun and interactive, and you can finish it at your own pace.

Russ Balzer, LCACP, Technical Director, WorldAutoSteel and Phoenix Group
Russ Balzer is the LCA Technical Director at WorldAutoSteel and Phoenix Group. As Technical Director, Russ manages a variety of engineering projects, and has tactical and strategic responsibilities in WorldAutoSteel’s efforts to use and promote Life Cycle Assessment (LCA). Russ recently achieved LCACP certification and was recognized for his work in the field of LCA with the ACLCA’s Rising Star Award.
Blog
Life Cycle Assessment (LCA), and particularly vehicle product life cycle assessment, is a topic we are very passionate about here at WorldAutoSteel. So much so that we focus on LCA intensively for the entire month of October across all of our communications channels. Though it’s not an AHSS forming or joining topic, it is one that is critical to truly reducing vehicle emissions for future generations. Russ Balzer, Technical Director at WorldAutoSteel and our resident LCA professional, in this blog and the next, will talk about LCA, its importance, and the tools WorldAutoSteel has developed to provide environmental insight to design decision tradeoffs.
All over the world there are continuing and growing efforts to address transportation greenhouse gas (GHG) emissions, which remain a major unresolved issue. These efforts are intended to help the transportation sector make its contribution to global emissions reduction goals. Unfortunately, much of this effort is focused on reducing emissions only from the vehicle tailpipe, with no consideration of the other sources of emissions in that vehicle’s life. This is not an effective way to meet these goals. In fact, this approach could lead to the unintended consequence of increasing GHG emissions in some cases. Fortunately, there is a better way – life cycle assessment (LCA), a tool for looking at the environmental impact of a product across its entire life cycle (Figure 1).
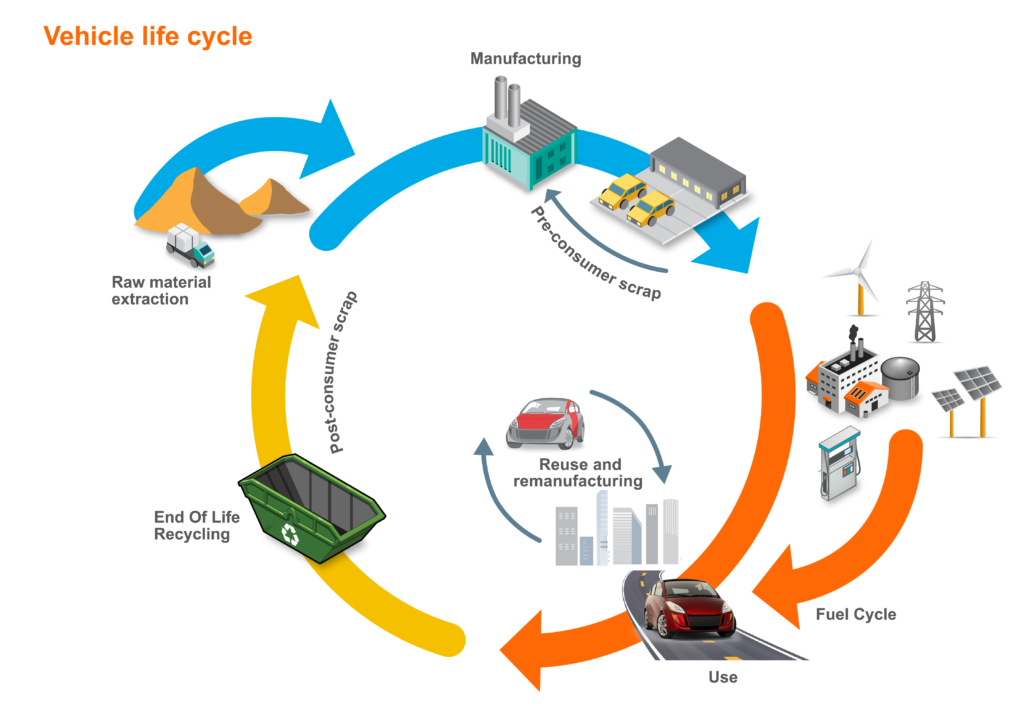
Figure 1: Vehicle LCA encompasses all phases of the product cycle, from raw material extraction to end of life recycling and disposal.
Focusing solely on the tailpipe emissions means ignoring other significant sources of GHG emissions, such as vehicle production and emissions generated (or avoided) at the end of the vehicle’s useful life (see Figure 2 on Page 2). An example of this is that tailpipe-only thinking can put too much emphasis on lightweighting. Don’t get me wrong, lightweighting can be an important part of the solution. Three of the four main drivers of fuel consumption (and therefore tailpipe emissions) – rolling resistance, acceleration and gravity (as in climbing a hill) – are dependent on the vehicle’s mass. So we can see why vehicle lightweighting is an obvious choice. It is a direct way to reduce these power demands and achieve better fuel consumption and fewer tailpipe emissions. The problem with lightweighting arises when we are so focused on reducing a vehicle’s mass that we fail to consider the consequences to the vehicle’s overall emissions.
One of the potential consequences arises from the use of lower-density materials like aluminium, magnesium and even carbon fibre to replace steel in a vehicle. From a tailpipe perspective, this can seem like a good (if expensive) solution. Vehicle mass may be reduced, resulting in improved fuel consumption and fewer tailpipe emissions. Sadly, it is not that simple. These low-density materials come with an environmental cost in addition to their higher financial cost. This cost comes in the form of higher GHG emissions in the production of the material itself. On a global average basis, GHG emissions from aluminium production can be as much as eight times as high per kilogram of material as the GHG emissions from steel production. For carbon fibre and magnesium the difference in production GHG emissions is even greater. This means that, even though you may save tailpipe emissions with some applications of these low-density materials, there is always a trade-off of higher production emissions.
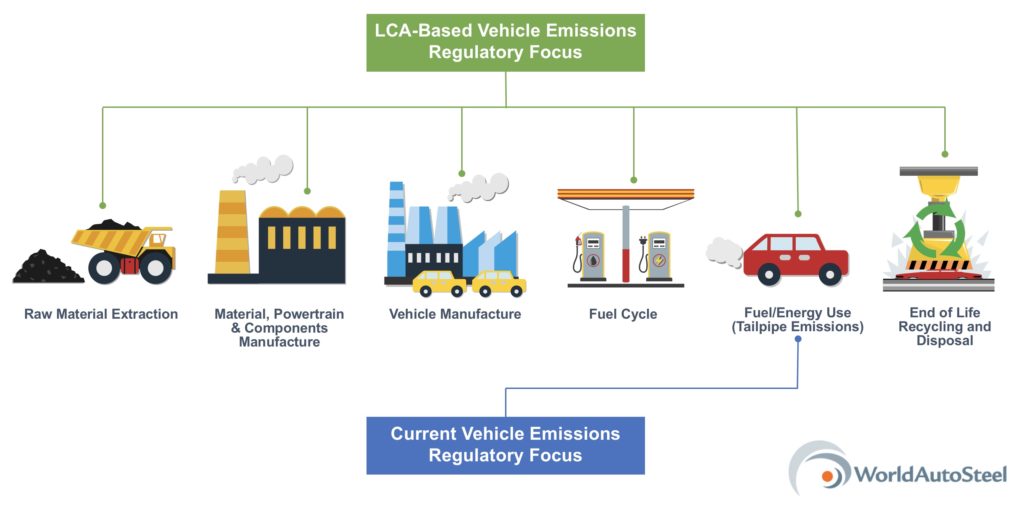
Figure 2: The difference between a regulatory focus that includes LCA and current tailpipe emissions.
In the best case, the reduction of emissions in the use phase does result in overall lower emissions, though, because of the trade-off between the tailpipe and production emissions, not as low as predicted by a tailpipe-only metric. Also possible is an intermediate case in which the use phase savings and the production phase increase are approximately equal, resulting in no net savings at all. In the worst case, the production emissions outweigh the use phase savings, resulting in the unintended consequence—higher overall emissions, the very opposite of what the regulation intends.
All three of these cases have two things in common. First, under a tailpipe-only regulation, we don’t know what the actual emissions are, because production emissions impacts are not being monitored. Second, because the low-density materials we are talking about are more expensive, all three of these cases come at a higher cost. So, we must ask ourselves: do we want to force automakers and consumers to pay more money without knowing the outcome? It’s time to consider another route to reducing emissions, and we believe that taking a life cycle approach is the correct route.
LCA assesses all the stages of a product’s life, from raw material extraction through production, use, and end of life processing. Though awareness of LCA has grown rapidly over the last 10-15 years, LCA methodology and practice have been developing since the early 1970s. Today, it is a mature assessment tool with global standards. Many car manufacturers are already using life cycle thinking and LCA, recognizing its importance and effectiveness in product and process design. LCA is equally accepted and used by material producers. In fact, together with many of their member companies, the trade associations of the steel, aluminium, and plastic industries are among the most active members of the global LCA community.
WorldAutoSteel has been directly involved with LCA since 2007, when we partnered with Dr. Roland Geyer of the University of California at Santa Barbara to develop an LCA tool for the assessment of material choices in passenger vehicles. The UCSB Automotive Materials Energy and Green House Gas (GHG) Comparison Model that Dr. Geyer developed on behalf of WorldAutoSteel is now in its fifth version and continues to be one of the most comprehensive publicly available vehicle LCA tools in the world.
The UCSB model is a full vehicle model assessing both GHG and energy effects of automotive material substitution over the entire life cycle of the vehicle.
Computation and parameter values are kept separate for maximum transparency and flexibility. This allowed the computational structure to be peer reviewed by members of the LCA community. The model calculates 27 main result values: three environmental indicators x three life cycle stages x three vehicles, as shown in Figure 3.
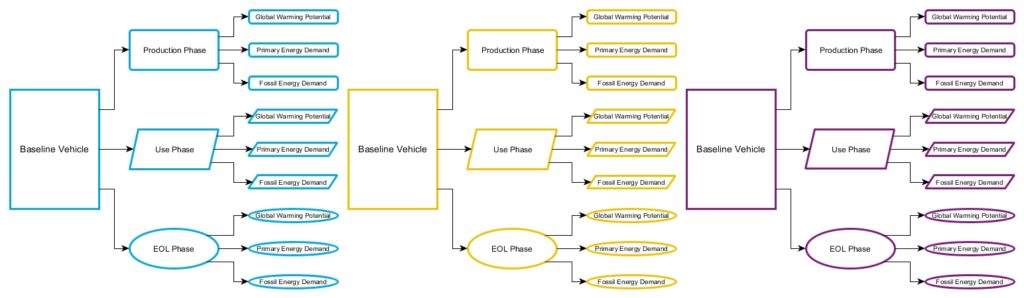
Figure 3: UCSB Model calculates 27 main result values.
The model has the flexibility to allow a multitude of different scenario evaluations, offering 14 structural material categories, 24 total material categories, adjustable material recycling methodology, a variety of biofuel and electricity pathways, as well as the powertrains, driving cycles and vehicle classes noted in Figure 4.

Figure 4: UCSB Model analysis options.
To maximize flexibility and transparency, all calculations are shown, and no parameter values are locked or hidden. This makes the UCSB Model an excellent tool for teaching LCA, particularly automotive LCA.
GHG emissions in the transport sector must be reduced to meet global emissions reduction goals. Lightweighting of passenger vehicles can be an important part of the emissions reduction solution in the transport sector, but only if lightweighting scenarios are viewed in the context of the overall vehicle emissions. Many companies inside and outside of the transport sector use Life Cycle Assessment, which considers environmental impacts from the whole of a vehicle’s life cycle, as their primary method to develop this overall view. The UCSB Automotive Energy and GHG Model, developed on behalf of WorldAutoSteel, is a publicly available, peer-reviewed tool for the assessment of automotive emissions on a life cycle basis. Version 5 of the UCSB Model can be downloaded for free at the WorldAutoSteel website here.
At the UCSB Model download page, you’ll find a video workshop featuring Russ Balzer explaining the contents of the Model. A user guide is also available for download.
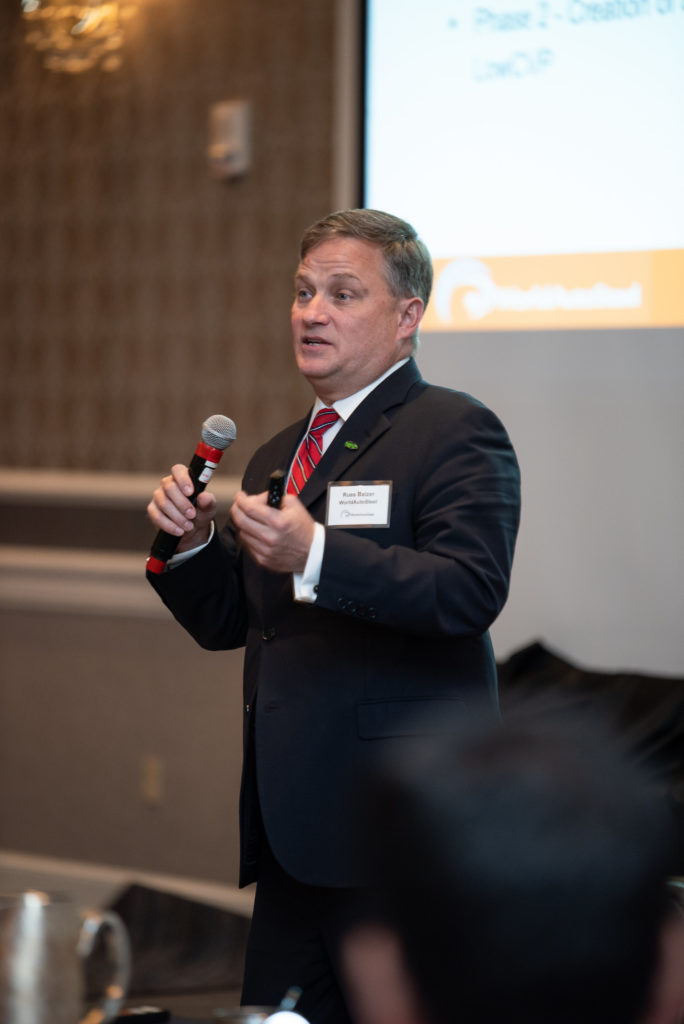
Russ Balzer, Technical Director, WorldAutoSteel
Russ Balzer is the LCA Technical Director at WorldAutoSteel and Phoenix Group. As Technical Director, Russ manages a variety of engineering projects, and has tactical and strategic responsibilities in WorldAutoSteel’s efforts to use and promote Life Cycle Assessment (LCA). Russ recently achieved ACLCA LCACP certification and was recognized for his work in the field of LCA with the ACLCA’s Rising Star Award.
Blog
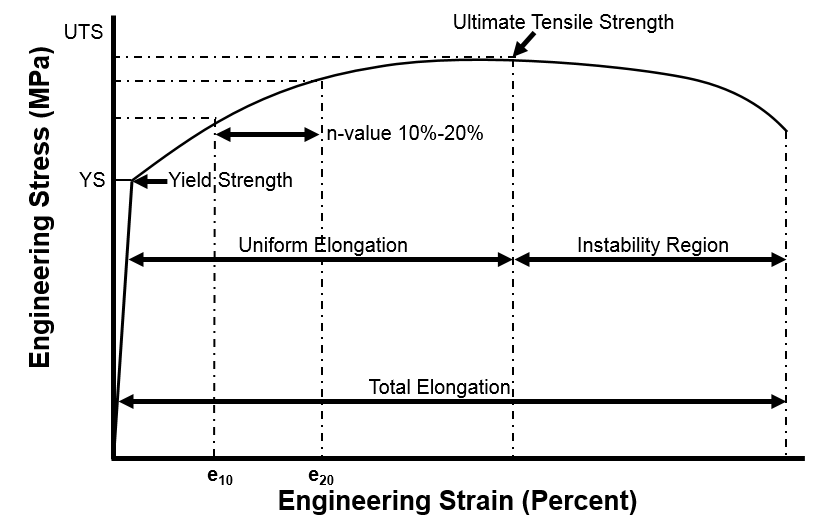
Typical Stress-Strain Curve
For many years, steel producers and stamping plants have gathered the mechanical properties of sheet metal. Individuals recorded properties such as yield strength, n-value and R-value to name a few. As new materials are introduced into the stamping plants, new mechanical properties tests are being discussed. The current use of aluminum and Dual Phase steels has highlighted issues that were insufficiently described by the typical or standard values provided by the tensile test: edge cracking and variation in springback from run to run are two examples. Resulting outcomes can encompass excessive scrap, excessive re-working of parts to remove edge cracks, and even result in excessive downtime as die makers try to correct the issue. The introduction of increasingly complex and sophisticated materials will exacerbate the inefficiencies of the current stamping process. The learning curve can be frustrating.
Proper training for your workforce regarding material mechanical properties and the know-how to develop robust stamping recipes for Advanced High-Strength Steel (AHSS) will benefit the plant. The typical tensile test provides the yield strength, ultimate tensile strength, n-value, uniform and total elongation. And typically, a strain analysis is performed, producing a forming limit diagram to measure a material’s formability. But these tests are reflective of global forming behaviors and don’t adequately describe an advanced material’s performance in localized formability. We need to ask if typical mechanical properties provide adequate information to truly assess the impact to the stamping operation – and if not, what new tests will provide insight on how these materials react to certain forming loads.
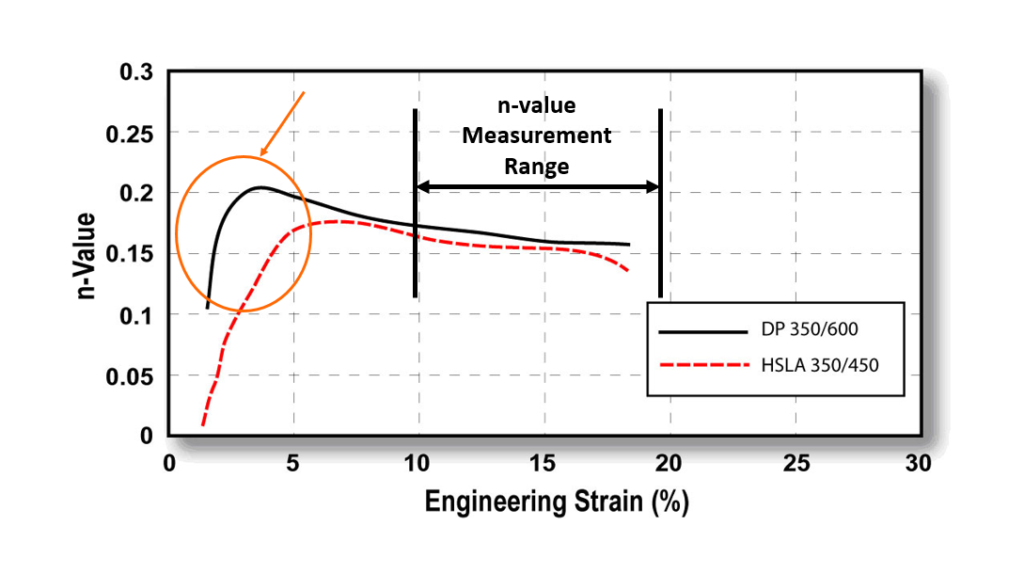
Instantaneous n-value
A new output is instantaneous n-value. Instantaneous n-value identifies the strain gradient – how the material will work-harden at initial contact with the die geometry. If only the standard n-value (work hardening exponent) is observed, measured between 10% and 20% strain, the increase in work hardening that occurs during deformation will be missed. Hole expansion and three-point bend tests are now commonly performed. The hole expansion test identifies the materials ability to stretch at the sheared edge. The three-point bend test identifies the stretchablity of a material via the minimum bend radius that can be achieved for that specific material.
Focusing on AHSS, these materials are characterized by multiple phase structures designed to improve formability. These designer steels are being created to improve crash worthiness through higher strength and lighter gauge thicknesses. To build upon the current understanding of material mechanical properties and resulting forming behaviors, training on AHSS products, testing and stamping process countermeasures is encouraged.