Blog, homepage-featured-top, main-blog
Dr. Donald Malen, College of Engineering, University of Michigan, reviews the use of two recently developed Powertrain Models, which he co-authored with Dr. Roland Geyer, University of California, Bren School of Environmental Science.
The use of Advanced High-Strength Steel (AHSS) grades offer a means to lightweight a vehicle. Among the benefits of this lightweighting are less fuel used over the vehicle life, and better acceleration performance. Vehicle designers as well as Greenhouse Gas analysts are interested in estimating these benefits early in the vehicle design process. G-13
Models are constructed for this purpose which range from the use of a simple coefficient, (for example fuel consumption change per kg of mass reduction), to very detailed models accessible only to specialists which require knowledge of hundreds of vehicle parameters. Draw backs to the first approach is that the coefficient may be based on assumptions about the vehicle which do not match the current case. Drawbacks to the detailed models are the considerable expense and time needed, and the lack of transparency in the results; It is difficult to relate inputs with outputs.
A middle way between the simplistic coefficient and the complex model, is described here as a set of Parsimonious Powertrain Models. G-10, G-11, G-12 Parsimony is the principle that the best model is the one that requires the fewest assumptions while still providing adequate estimates. These Excel spreadsheet models cover Internal Combustion powertrains, Battery Electric Vehicles, and Plug-in Electric Vehicles, and predict fuel consumption and acceleration performance based on a small set of inputs. Inputs include vehicle characteristics (mass, drag coefficient, frontal area, rolling resistance), powertrain characteristics (fuel conversion efficiency, gear ratios, gear train efficiency), and fuel consumption driving cycle. Model outputs include estimates for fuel consumption, acceleration, and a visitation map.
Physics of the Models
Fuel consumption is determined by the quantity of fuel used over a driving cycle. The driving cycle specifies the vehicle speed vs. time. An example of a driving cycle is the World Light Vehicles Test Procedure (WLTP) cycle shown in Figure 1.
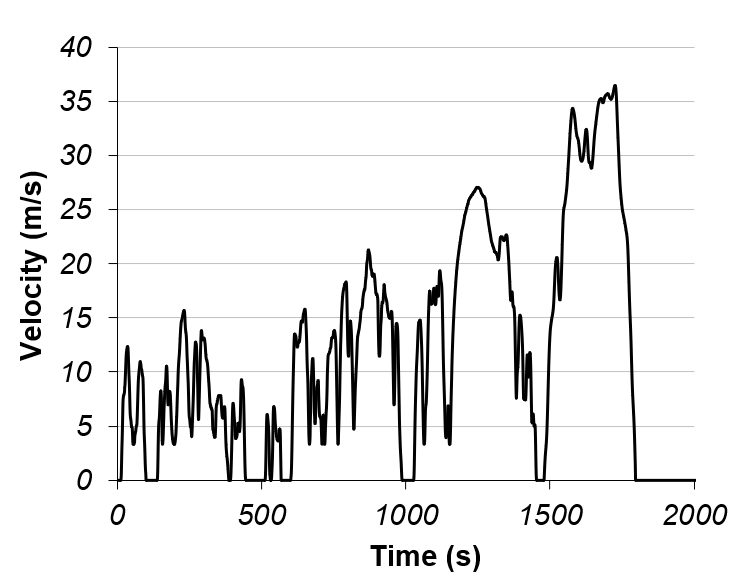
Figure 1: Fuel Consumption Driving Cycle (WLTP Class 3b).
Given the velocity history of Figure 1, the forces on the vehicle resisting forward motion may be calculated. These forces include inertia force, aerodynamic drag force, and rolling resistance. The total of these forces, called tractive force, must be provided by the vehicle propulsion system, see Figure 2.
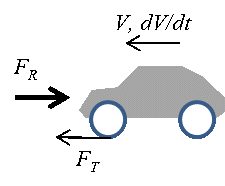
Figure 2. Tractive Force Required.
Once vehicle speed and tractive force are known at each point of time during the driving cycle, the required torque and rotational speed may be determined for each of the drivetrain elements, as shown in Figure 3 for an Internal Combustion system, and Figure 4 for a Battery Electric Vehicle.
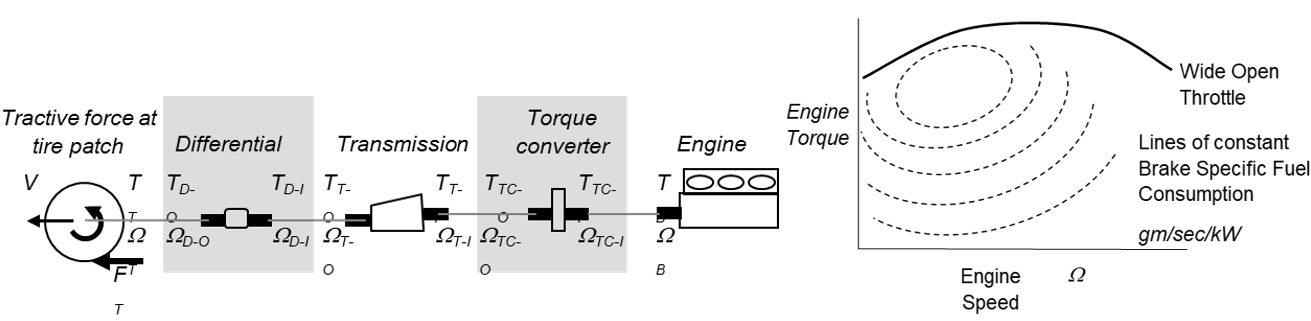
Figure 3. Internal Combustion Powertrain.
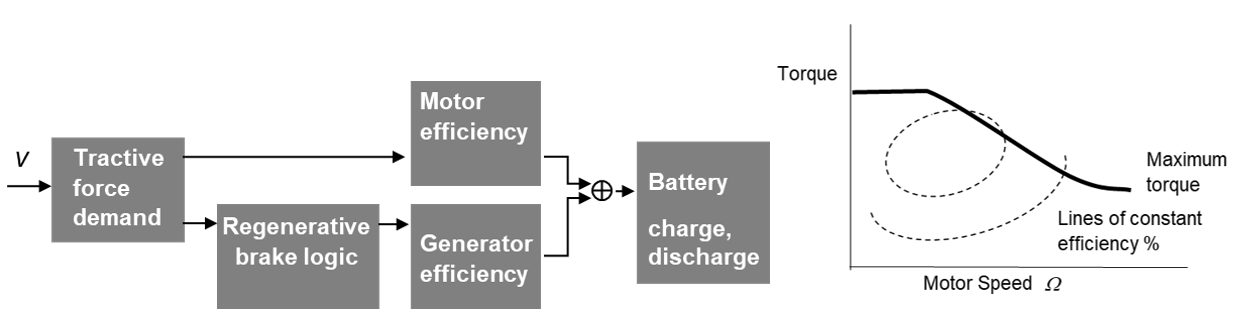
Figure 4. Battery Electric Vehicle Powertrain.
In this way, the required torque and speed of the engine or motor may be determined. Then using a map of efficiency, shown to the right in Figures 3 and 4, the energy demand is determined at each point in time. Summing the energy demand over time yields the fuel used over the driving cycle. The reader is referred to References 1 and 2 for a much more in depth description of the models.
Example Application
As an example application, consider the WorldAutoSteel FutureSteelVehicle (FSV).W-7 The FSV project, completed in 2011, investigated the weight reduction potential enabled with the use of AHSS, advanced manufacturing processes and computer optimization. The resulting material use in the body structure is shown in Figure 5.
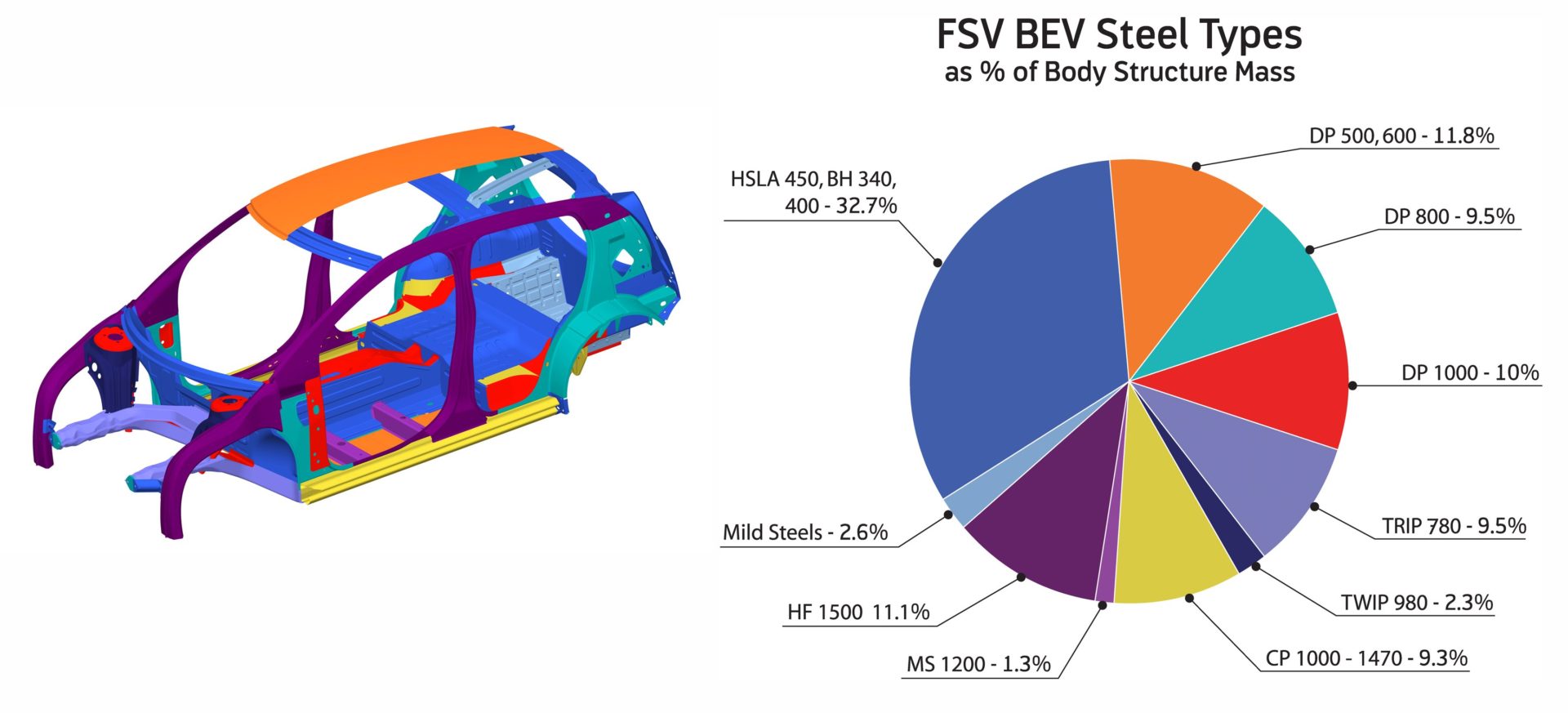
Figure 5. FutureSteelVehicle steel grade application.
This use of AHSS allowed a reduction in the vehicle curb mass from 1200 kg to 1000 kg. What are the effects of this mass reduction on fuel consumption and acceleration performance? The inputs required for the powertrain model are shown in Table 1 for the base case.
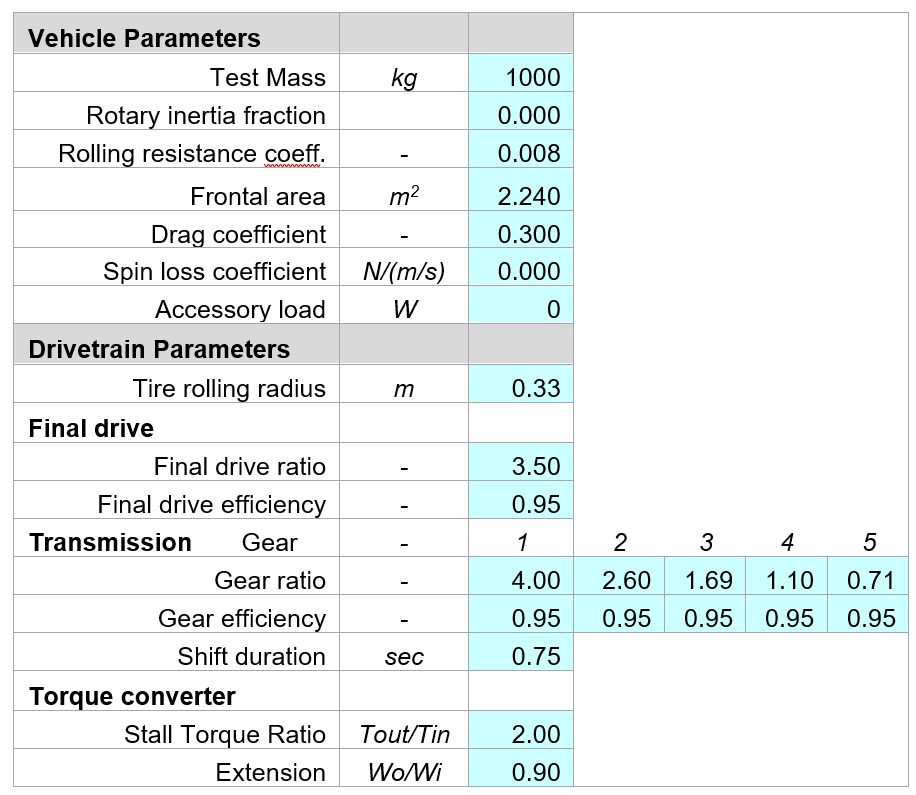
Table 1: Model Inputs for Base Case.
The results provided by the powertrain model are summarized in the acceleration-time vs. fuel consumption graph of Figure 6. Point A is the base case at 1200 kg curb mass. The lightweight case with same engine is shown as Point B. Note the fuel consumption reduction and also the acceleration time reduction. Often the acceleration time is set as a requirement. For the lighter vehicle, the engine size may be reduced to achieve the original acceleration time and an even greater reduction in fuel consumption as shown as Point C.
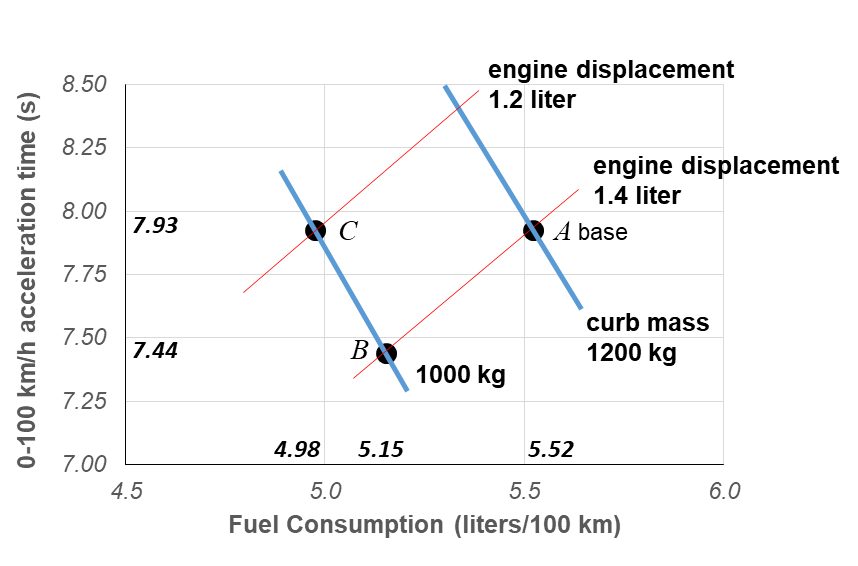
Figure 6. Summary of results of base vehicle and reduced mass vehicle.
Using the parsimonious powertrain models allows such ‘what-if’ questions to be answered quickly, with minimal data input, and in a transparent way. The Parsimonious Powertrain Models are available as a free download at worldautosteel.org.
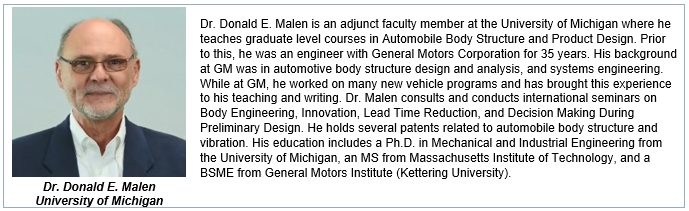
Blog, RSW Joint Performance Testing
top-of-page
Results of a Three-Year LME Study
WorldAutoSteel releases today the results of a three-year study on Liquid Metal Embrittlement (LME), a type of cracking that is reported to occur in the welding of Advanced High-Strength Steels (AHSS).The study results add important knowledge and data to understanding the mechanisms behind LME and thereby finding methods to control and establish parameters for preventing its occurrence. As well, the study investigated possible consequences of residual LME on part performance, as well as non-destructive methods for detecting and characterizing LME cracking, both in the laboratory and on the manufacturing line (Figure 1).
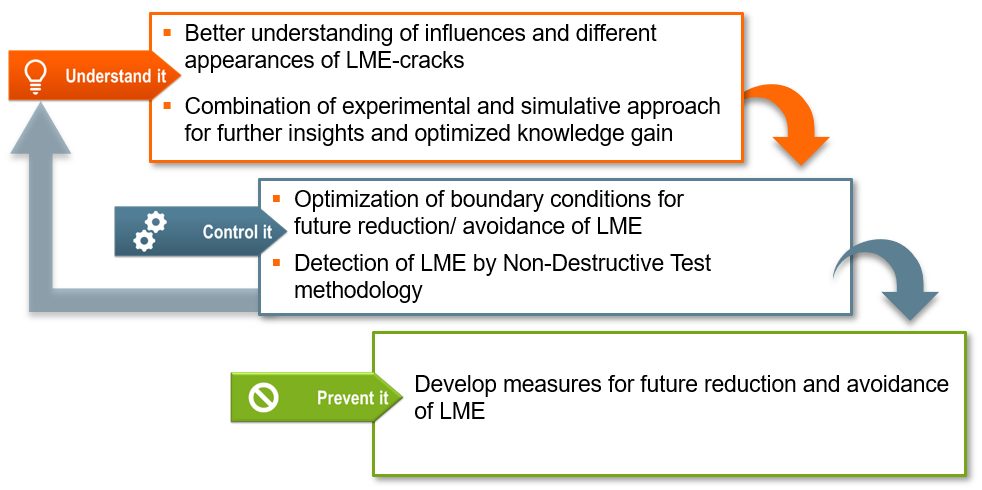
Figure 1: LME Study Scope
The study encompassed three different research fields, with an expert institute engaged for each:
- Laboratory of Materials and Joining Technology (LWF) Paderborn University, Paderborn, Germany, for experimental research,
- The Institute de Soudure, Yutz, France, for investigations regarding non-destructive testing, and
- Fraunhofer Institute for Production Systems and Design Technology (IPK), Berlin, Germany, for the development of a simulation model to accurately replicate welding conditions resulting in LME.
A portfolio containing 13 anonymized AHSS grades, including dual phase (DP), martensitic (MS) and retained austenite (RA) with an ultimate tensile strength (UTS) of 800 MPa and higher, was used to set up a testing matrix, which enabled the replication of the most relevant and critical material thickness combinations (MTC). All considered MTCs show a sufficient weldability under use of standard parameters according to SEP1220-2. Additional MTCs included the joining of various strengths and thicknesses of mild steels to select AHSS in the portfolio. Figure 2 provides the welding parameters used throughout the study.
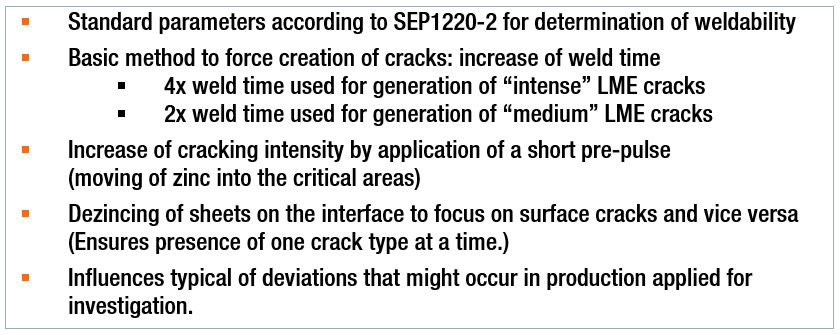
Figure 2: Study Welding Parameters
In parallel, a 3D electro-thermomechanical simulation model was set up to study LME. The model is based on temperature-dependent material data for dual phase AHSS as well as electrical and thermal contact resistance measurements and calculates local heating due to current flow as well as mechanical stresses and strains. It proved particularly useful in providing additional means to mathematically study the dynamics observed in the experimental tests. This model development was documented in two previous AHSS Insights blogs (see AHSS Insights Related Articles below).
Understanding LME
The study began by analyzing different influence factors (Figure 3) which resembled typical process deviations that might occur during car body production. The impact of the influences was analyzed by the degree of cracking observed for each factor. A select number of welding set-ups from these investigations were rebuilt digitally in the simulation model to replicate the process and study its dynamics mathematically. This further enabled the clarification of important cause-effect relationships.

Figure 3: Overview of All Applied Influence Factors (those outlined in yellow resulted in most frequent cracking.)
Generally, the most frequent cracking was observed for sharp electrode geometries, increased weld times and application of external loads during welding. All three factors were closely analyzed by combining the experimental approach with the numerical approach using the simulation model.
Destructive Testing – LME Effects on Mechanical Joint Strength
A destructive testing program also was conducted for an evaluation of LME impact on mechanical joint strength and load bearing capacity in multiple conditions, including quasi-static loading, cyclic loading, crash tests and corrosion. In summary of all load cases, it can be concluded that LME cracks, which might be caused by typical process deviations (e.g. bad part fit up, worn electrodes) have a low intensity impact and do not affect the mechanical strength of the spot weld. And as previously mentioned, the study analyses showed that a complete avoidance of LME during resistance spot welding is possible by the application of measures for reducing the critical conditions from local strains and exposure to liquid zinc.
Controlling LME
In welding under external load experiments, the locations of the experimental crack occurrence showed close correlation with the strains and remaining plastic deformations computed by the simulation model. It was observed that the cracks form at the location of the highest plastic strains, and material-specific threshold values for critical strains were derived. The threshold values then were used to judge the crack formation at elongated weld times.
At the same time, the simulation model pointed out a significant difference in liquid zinc diffusion during elongated weld times. Therefore, it is concluded that liquid zinc exposure time is a second highly relevant factor for LME formation.
The results for the remaining influence factors depended on the investigated MTCs and were generally less significant. In more susceptible MTCs (AHSS welded with thick Mild steel), no significant cracking occurred when welded using standard process parameters. Light cracking was observed for most of the investigated influences, such as low electrode cooling rate, worn electrode caps, electrode positioning deviations or for gap afflicted spot welds. More intense cracking (higher penetration depth cracking) was only observed when welding under extremely high external loads (0.8 Re) or, even more, as a consequence of highly increased weld times.
For the non-susceptible MTCs, even extreme situations and weld set-ups (such as the described elongated weld times) did not result in significant LME cracks within the investigated AHSS grades.
Methods for avoidance of LME also were investigated. Changing the electrode tip geometry to larger working plane diameters and elongating the hold time proved to eliminate LME cracks. In the experiments, a change of electrode tip geometry from a 5.5 mm to an 8.0 mm (Figure 4) enabled LME-free welds even when doubling the weld times above 600 ms. Using a flat-headed cap (with small edge radii or beveled), even the most extreme welding schedules (weld times greater than 1000 ms) did not produce cracks. The in-depth analysis revealed that larger electrode tip geometries clearly reduce the local plastic deformation around the indentation. This plastic strain reduction is particularly important, as longer weld times contribute to a higher liquid zinc exposure interval, leading to a higher potential for LME cracks.
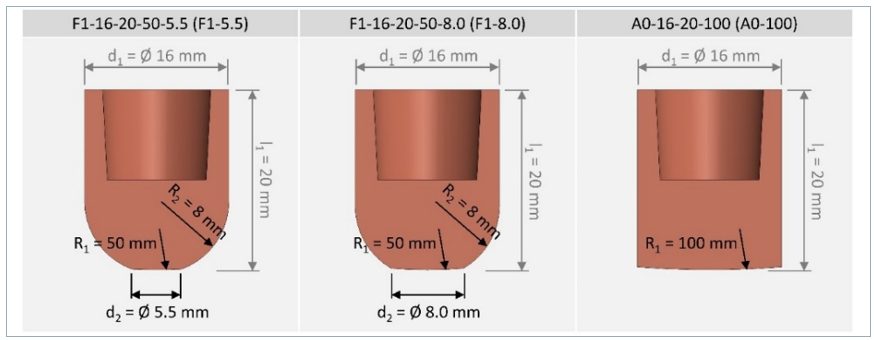
Figure 4: Electrode Geometries Used in Study Experiments
It was also seen that as more energy flows into a spot weld, it becomes more critical to parameterize an appropriate hold time. Depending on the scenario, the selection of the correct hold time alone can make the difference between cracked and crack-free welds. Insufficient hold times allow liquid zinc to remain on the steel surface and increased thermal stresses that form after the lift-off of the electrode caps. Elongated hold times reduce surface temperatures, minimizing surface stresses and thus LME potential.
Non-Destructive Testing: Laboratory and Production Capabilities
A third element of the study, and an aid in the control of LME, is the detection and characterization of LME cracks in resistance spot welds, either in laboratory or in production conditions. This work was done by the Institute of Soudure in close cooperation with LWF, IPK and WorldAutoSteel members’ and other manufacturing facilities. Ten different non-destructive techniques and systems were investigated. These techniques can be complementary, with various levels of costs, with some solutions more technically mature than others. Several techniques proved to be successful in crack detection. In order to aid the production source, techniques must not only detect but also characterize cracks to determine intensity and the effect on joint strength. Further work is required to achieve production-level characterization.
The study report provides detailed technical information concerning the experimental findings and performances of each technique/system and the possible application cost of each. Table 1 shows a summary of results:
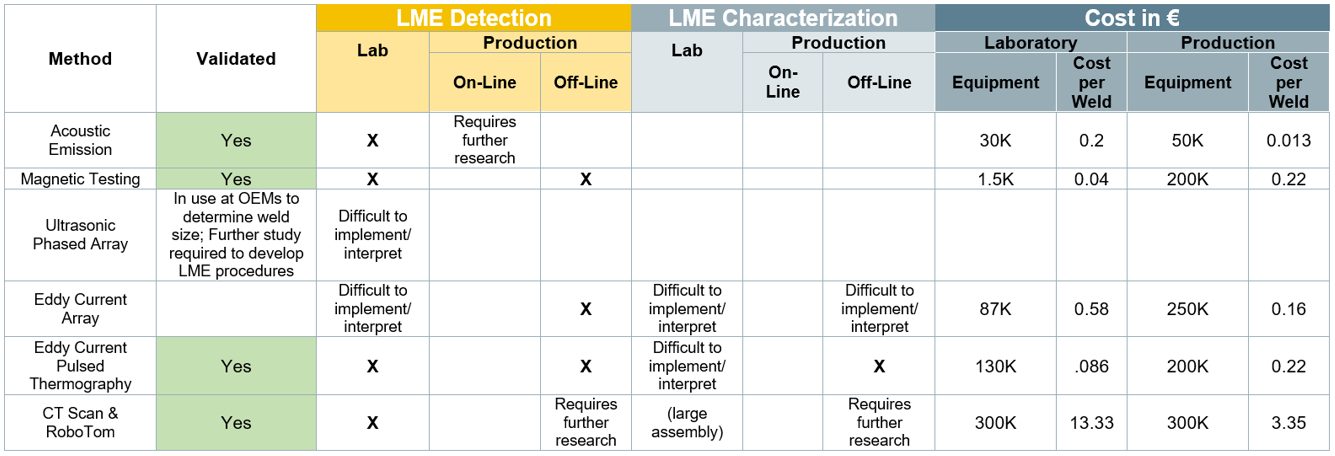
Table 1: Summary of NDT: LME Detection and Characterization Methods
Preventing LME
Suitable measures should always be adapted to the specific use case. Generally, the most effective measures for LME prevention or mitigation are:
- Avoidance of excessive heat input (e.g. excess welding time, current).
- Avoidance of sharp edges on spot welding electrodes; instead use electrodes with larger working plane diameter, while not increasing nugget-size.
- Employing extended hold times to allow for sufficient heat dissipation and lower surface temperatures.
- Avoidance of improper welding equipment (e.g. misalignments of the welding gun, highly worn electrodes, insufficient electrode cooling)
In conclusion, a key finding of this study is that LME cracks only occurred in the study experiments when there were deviations from proper welding parameters and set-up. Ensuring these preventive measures are diligently adhered to will greatly reduce or eliminate LME from the manufacturing line. For an in-depth review of the study and its findings, you can download a copy of the full report at worldautosteel.org.

LME Study Authors
The LME study authors were supported by a committed team of WorldAutoSteel member companies’ Joining experts, who provided valuable guidance and feedback.
Related Articles: More on this study in previous AHSS Insights blogs:
Journal Publications:
- Julian Frei, Max Biegler, Michael Rethmeier, Christoph Böhne & Gerson Meschut (2019) Investigation of liquid metal embrittlement of dual phase steel joints by electro-thermomechanical spot-welding simulation, Science and Technology of Welding and Joining, 24:7, 624-633, DOI: 10.1080/13621718.2019.1582203
- Christoph Böhne, Gerson Meschut, Max Biegler, Julian Frei & Michael Rethmeier (2020) Prevention of liquid metal embrittlement cracks in resistance spot welds by adaption of electrode geometry, Science and Technology of Welding and Joining, 25:4, 303-310, DOI: 10.1080/13621718.2019.1693731
-
Auto/Steel Partnership LME Testing and Procedures
Back To Top
Blog, main-blog
In static or dynamic conditions, the spot weld strength of Advanced High-Strength Steels (AHSS) may be considered as a limiting factor. One solution to improve resistance spot weld strength is to add a high-strength adhesive to the weld. Figure 1 illustrates the strength improvement obtained in static conditions when crash adhesive (in this case, Betamate 1496 from Dow Automotive) is added. The trials were performed with 45-mm-wide and 16-mm adhesive bead samples.

Figure 1: Tensile Shear Strength and Cross Tensile Strength on DP 600.A-16
Another approach to improve the strength of welds is done by using laser welding instead of spot welding. Compared to spot welding, the main advantage of laser welding, with respect to the mechanical properties of the joint, is the possibility to adjust the weld dimension to the requirement. One may assume that, in tensile shear conditions, the weld strength depends linearly on the weld length as indicated in the results of a trial A-16, shown in Figure 2.

Figure 2: Tensile-shear strength on laser weld stitches of different length.A-16
However, a comparison of spot weld to laser weld strength cannot be restricted to the basic tensile shear test. Tests were also conducted to evaluate the weld strength in both quasi-static and dynamic conditions under different solicitations, on various AHSS combinations. The trials were performed on a high-speed testing machine, at 5 mm/min for the quasi-static tests and 0.5 m/s for the dynamic tests (pure shear, pure tear or mixed solicitation, as shown in Figure 3). The strength at failure and the energy absorbed during the trial were measured. Laser stitches were done at 27mm length. C- and S-shape welds were performed with the same overall weld length.

Figure 3: Sample geometry for quasi-static and dynamic tests.A-16
The weld strength at failure is described in Figure 4, where major axes represent pure shear and tear (Figure 4). For a reference spot weld corresponding to the upper limit of the weldability range, globally similar weld properties can be obtained with 27mm laser welds. The spot weld equivalent length of 25-30 mm has been confirmed on other test cases on AHSS in the 1.5- to 2 mm thickness range. It has also been noticed that the spot weld equivalent length is shorter on thin mild steel (approximately 15-20 mm). This must be considered when shifting from spot to laser welding on a given structure. There is no major strain rate influence on the weld strength; the same order of magnitude is obtained in quasi-static and dynamic conditions.

Figure 4: Quasi-static and dynamic strength of welds, DP 600 2 mm+1.5 mm.A-16
The results in terms of energy absorbed by the sample are seen in Figure 5. In tearing conditions, both the strength at fracture and energy are lower for the spot weld than for the various laser welding procedures. In shear conditions, the strength at fracture is equivalent for all the welding processes. However, the energy absorption is more favorable to spot welds. This is due to the different fracture modes of the welds; for example, interfacial fracture is observed on the laser welds under shearing solicitation. Even if the strength at failure is as high as for the spot welds, this severe failure mode leads to lower total energy absorption.

Figure 5: Strength at fracture and energy absorption of Hot Rolled 1500 1.8-mm + DP 600 1.5-mm samples for various welding conditions.A-16
Figure 6 represents the energy absorbed by omega-shaped structures and the corresponding number of welds that fail during the frontal crash test (here on TRIP 800 grade). It appears clearly that laser stitches have the highest rate of fracture during the crash test (33%). In standard spot welding, some weld fractures also occur. It is known that AHSS are more prone to partial interfacial fracture on coupons, and some welds fail as well during crash tests. By using either Weld-Bonding or adapted laser welding shapes, weld fractures are mitigated, even in the case of severe deformation. As a consequence, higher energy absorption is also observed.

Figure 6: Welding process and weld shape influence on the energy absorption and weld integrity on frontal crash tests.A-16
Up to a 20% improvement can be achieved in torsional stiffness, where the best results reflected the combination of laser welds and adhesives. Adhesive bonding and weld- bonding lead to the same stiffness improvement results due to the adhesive rather than the additional welds. Figure 7 shows the evolution of the torsional stiffness with the joining process. Optimized laser joining design leads to the same performances as a weld bonded sample in fracture modes, shown in Figure 8.
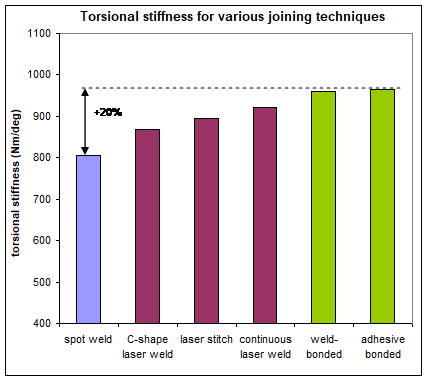
Figure 7: Evolution of the torsional stiffness with the joining process.A-16

Figure 8: Validation test case 1.2-mmTRIP 800/1.2-mm hat-shaped TRIP 800.
Top-hat crash boxes were tested across a range of AHSS materials including DP 1000. The spot weld’s energy absorption increased linearly with increasing material strength. The adhesives were not suitable for crash applications as the adhesive peels open along the entire length of the joint. The weld bonded samples perform much better than conventional spot welds. Across the entire range of materials there was a 20-30% increase in mean force when weld bonding was used; the implications suggesting a similarly significant improvement in crash performance. Furthermore, results show that a 600 MPa weld bonded steel can achieve the same crash performance as a 1000 MPa spot-welded steel. It is also possible that some down gauging of materials could be achieved, but as the strength of the crash structure is highly dependent upon sheet thickness, only small gauge reductions would be possible. Figure 9 shows the crash results for spot-welded and weld bonded AHSS.

Figure 9: Crash results for spot-welded and weld bonded AHSS.
Blog, main-blog
Forty years ago, the metal forming community needed to figure out how to stamp a new exotic family of steels making inroads into automotive body construction. These grades, called High Strength Low Alloy steels, were much stronger than the commonplace mild steels, and were more formable than the high-strength options available at that time. Initially, only a few steelmakers were able to offer these new grades, but over time more companies added the equipment and know-how necessary to support their customers with these products. Automakers and their supply chain stampers needed to adapt as an increasing number of parts transitioned to HSLA steels.
Fast-forward a few decades, and metal formers are facing similar challenges. Successful forming and joining of Advanced High-Strength Steels is made easier with processes that are tuned to work with the characteristics associated with these alloys. One such technique to improve formability is to employ Active Binder Force Control.
In conventional stamping, a draw ring applies pressure around the binder in order to control the sheet metal flow into the cavity. The ring may be referred to as a binder plate, draw pad, pressure pad, or blank holder. Creating the restraining force typically is done with urethane springs, coil springs, gas springs (like air or nitrogen), or press cushion systems actuated by gas or hydraulic cylinders.
Where the traditional approach applies binder pressure uniformly throughout the press stroke, modern stamping presses can be equipped with cushions having multipoint-control systems (see Figure 1 example). The associated pressure profile can be adjusted around the panel and throughout the stroke to optimize metal flow, prevent splits and wrinkles, and minimize thinning.

Figure 1. An Example of Multi-Point Press Forming Method.P-31
Incorporating Active Binder Control capabilities has several benefits for the press shop, panel quality, and product design, including:
- A segmented blankholder combined with individually programmable hydraulic cylinders, sometimes called a flexible binder, allows for precise control of one segment independent of the others.
- Pulsating blank holder force has been shown to reduce press tonnage requirements and increase metal flow, with the frequency and amplitude being key variables that must be adjusted based on the grade and thickness of interest.
- Pre-acceleration of the cushion reduces shock loading, which minimizes the press-damaging snap-through loads associated with reverse tonnage.
The merits of a variable blank holder force on AHSS springback were documented in a 2004 conference paper.M-63 With the traditional constant binder force approach, springback in the form of side-wall curl was seen in parts made from either a DP590 grade or a mild steel grade used as a control. Increasing the constant binder force helped to reduce springback in the mild steel part.
In Figure 2, CBF reflects tests conducted with constant binder force. VBF-LH and VBF-MLH reflect variable binder force tests conducted with a low-high force profile sequence and a medium-low-high force profile, respectively.

Figure 2: Variable Binder Force Reduces Springback.M-63
By employing a variable binder force, springback of both the mild steel and the DP 590 material was substantially reduced. Employing either variable binder force approach reduced the thinning from forming the DP 590 material, resulting in a more uniform strain distribution across the entire channel profile (Figure 3).

Figure 3: Uniform Strain Distribution Achieved with Variable Binder Force.M-63
More recently, a presentation from 2018 showed CP 800 panel quality improvements associated with variable blank holder force capabilities.D-33 Panel results from a constant binder force of 300 kN and 400 kN are shown in Figures 4 and 5, respectively. Both exhibit severe wrinkling in the flange. Applying 500 kN binder force was not feasible due to exceeding the press tonnage curve limits throughout the stroke.

Figure 4: CP800 Panel Formed with Constant Binder Force of 300 kN, and Associated Close-Up of Flange.D-33

Figure 5: CP800 Panel Formed with Constant Binder Force of 400 kN, and Associated Close-Up of Flange.D-33
Figure 6 shows the panel produced with a variable binder force. The chosen profile fit within the press tonnage requirements and minimized wrinkles.

Figure 6: CP800 Panel Formed with Variable Binder Force Ramping from 300 kN to 600 kN, and Associated Close-Up of Flange.D-33
Active drawbead control is an offshoot of these techniques, allowing for the magnitude and timing of drawbead engagement to be optimized for the requirements of each part. A description of using stake beads to minimize springback is available in the Springback article – active drawbead control is one approach to actuate beads.
The initial laboratory studies relating to active binder force control go back nearly 20 years ago. In the coming years, more information will enter the public domain on how metal formers are using these concepts in production. When you look to purchase a servo press, be sure to ask your press manufacturer about programmable cushions.
Blog, main-blog
Several recent studies are forecasting that; “Within the next 10 to 15 years, urban transportation will be dominated by Electric and Automated vehicles”.B-50 Meaning most of us will be driving Battery Electric Vehicles (BEVs) in the not-distant future. In 2011, just eight years ago, there were only three BEVs on the market with 70 to 80 miles range on a single charge. These were the first generation BEVs. Since then, the number of EVs on the market has increased, with significant improvements in range (now approaching 300 miles). BEV 2020 vehicles cover all current segments, from small cars to SUV’s and trucks (Figure 1). These vehicles will be available from most OEMs as well as several new start-up companies. The construction material for body structures of these vehicles is predominantly steel, while some of the premium vehicles ($60,000 to $100,000) are aluminium. And the prevailing OEM message seems to be “anything TESLA can do, we can do better”.
So how will this change the vehicle body structure design, choice of construction material, its implications for manufacturing and assembly, and ultimately, the impact on automotive steel?
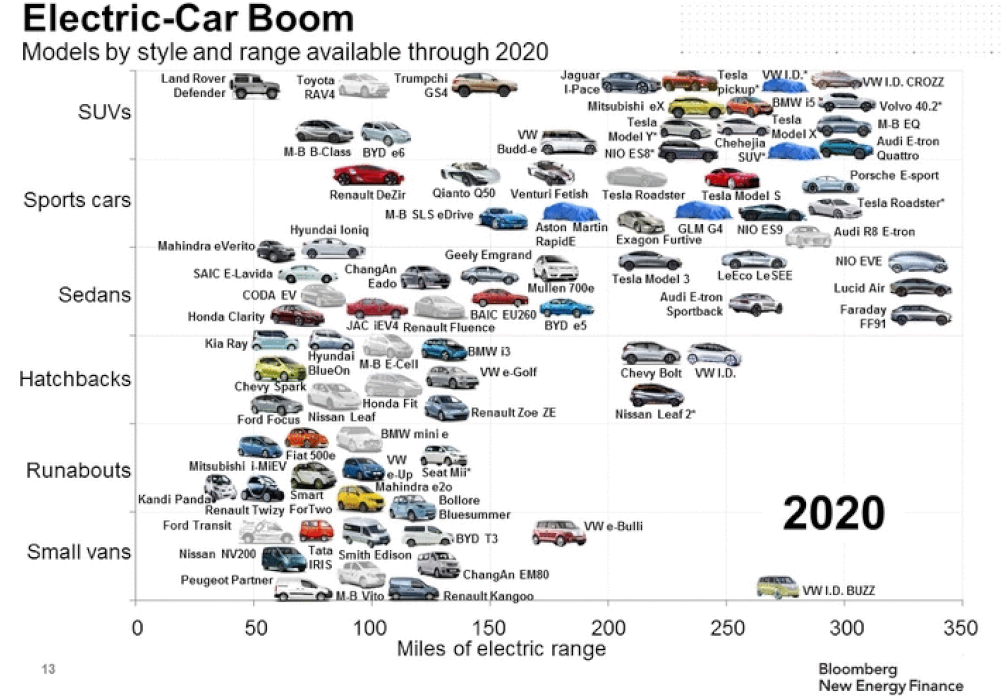
Figure 1: Electric Vehicle Boom – Models by Style and Range Available Through 2020.B-50 CHART SUMMARY: a) Covers all current segments, b) Structures predominantly Steel, c)Some premium vehicles highlight Aluminium, d)Products from most OEMs as well as several new start-up companies.
The driver for this electrification boom is increasing affordability. The upfront cost of BEVs will become competitive on an unsubsidized basis starting in 2024.F-38 By 2030 in the U.S., almost all light duty vehicle segments will reach cost parity as battery prices continue to fall.B-73 Forecasters, such as McKinsey, Morgan Stanley and Bloomberg, predict that about half of all new vehicle production will be electric somewhere between 2035 and 2040. However, Tesla’s CEO Elon Musk’s prediction is much more aggressive. He expects more than half of new vehicles in the U.S. will be electric within the next 10 years, roughly 10 to 15 years ahead of most other predictions.
The Main Drivers of BEV Cost Reduction
- Lithium-ion battery prices have fallen 75% since 2013, hitting $176/kWh in 2018 (Figure 2). Industry-wide prices fell due to the adoption of new cell designs and the availability of higher energy-density cathodes. Prices are expected to drop further in coming years to below $100 per kWh. Besides the reduction in cost, packaging efficiency and the cell energy density also is improving.
- Package space required by other BEV powertrain systems also is being optimized, e.g., motor, transmission, differential and power electronics. This is yielding significant weight and cost reductions, which are then directly reinvested into lower-cost structural materials, such as Advanced High-Strength Steels (AHSS) versus higher cost Aluminium, to keep the overall price of the vehicle low.
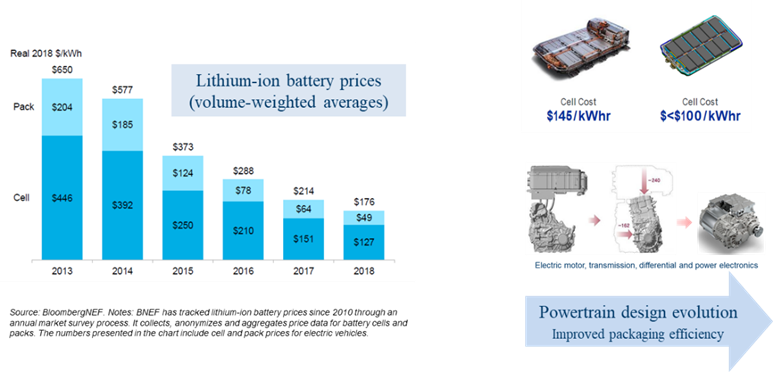
Figure 2: BEV Price Parity with Gas-powered Cars by 2024 – Main Drivers.B-74
BEV to ICE Vehicle Structural Differences and Advantages for Steel
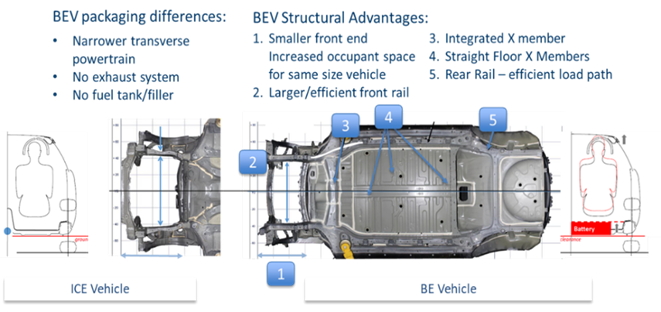
Figure 3: BEV to ICE Vehicle Structural Differences.M-64
BEV packaging differences compared with ICE Vehicles are shown in Figure 3, and include:
- Narrower and compact transverse electric powertrains, leading to shorter front end, with increased occupant space for same size vehicle and larger/efficient front crash rails.
- Lack of an exhaust system eliminates the need for the tunnel, allowing straighter/ efficient cross-members.
- No fuel tank/filler leads to more efficient rear rail load path.
- High voltage electric powertrain and large (300 litres, 500 kg) under-floor battery pack crash protection requirements result in higher safety requirements for BEV front and side structures.
- Safety. The BEV body structure load path requirements are ideal for AHSS application. The floor cross members, without the presence of the tunnel, are straight and can use very high-strength martensitic roll formed sections. Cross members can be stamped from 3rd Generation Steels offering Giga-Pascal strength and over 20% elongation. For frontal crash load management and to minimize passenger/battery compartment intrusions for increased safety, 3rd Generation steels offer the most mass/cost efficient solution. The very high strengths offered by AHSS and UHSS for the safety-critical structural members such as the rocker, rails, cross members and pillars, greatly enhance the required protection of the BEV powertrain and high energy/voltage battery systems. The battery enclosure construction greatly benefits from AHSS usage, providing protection from road-debris impacts from below the vehicle, along with fire protection into the passenger compartment. Advanced steels also enable reduced section sizes for the occupant compartment, required for improved panoramic visibility, without compromising occupant safety and comfort.
- Cost. For widespread adoption of BEVs to occur, the overall cost of the vehicle must be affordable, and its range must be above the ‘range anxiety limit’ of most drivers. Various surveys indicate this range to vary greatly from 75 miles to over 400 miles. Using steel for the vehicle structure leads to the lowest cost BEV, just as with ICE-based vehicles. The vehicle range can be increased through lightweighting and/or by increasing the size of the battery; a cost comparison of these two options is shown in Figure 4. With battery cost reduction approaching $100 per kWh, lightweighting is cost effective at approximately US$2.00 per kg saved. Lightweighting is still very important and the latest steel grades, in particular 3rd Generation steels, offer the most cost-effective lightweighting option. In comparison, if we consider lightweighting with aluminium, the cost is typically in the order of US$6.00 per kg saved. This could be cost effective if the battery cost is over $250 per kWh, which was the case a decade ago. We can see the evidence of this in OEM decisions at that time. For example, the 2011 Nissan Leaf BEV closures were aluminium; but the latest 2019 Nissan leaf BEV closures are steel.
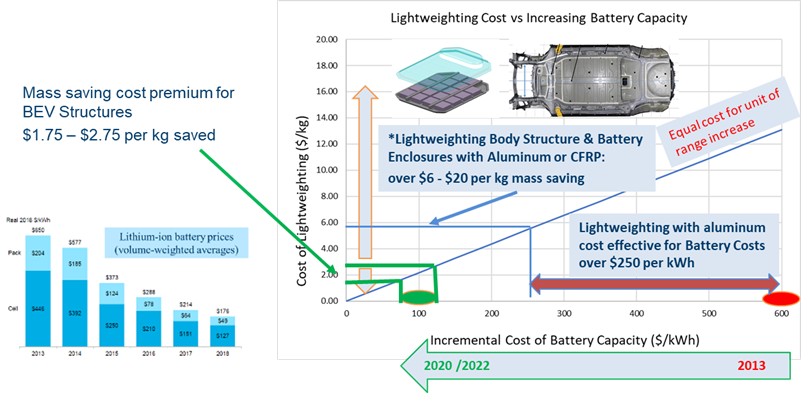
Figure 4: BEV Range Increase – Lightweighting Cost versus Battery Cost 2020 – 2022.M-64
Battery Electric Vehicles – Boom or Bust for AHSS?
For the increased safety required for BEVs to protect the high voltage systems, the structural load paths are ideally suited for the Giga Pascal level strengths offered by AHSS and UHSS. The Battery Enclosure structure offer an additional 85 kg per vehicle opportunity, an increase of approximately 10% sheet metal over ICE vehicles. Also, using advanced steels the BEV structure can take full advantage of well-established body shop practices for manufacturing and assembly, such as stamping, roll forming and spot welding. With future increased focus on BEV affordability, safety and sustainability, steel offers the best solutions and flexibility to address these key challenges.
Blog
We’ve been monitoring the evolution of vehicle legislation in the world closely, advocating for life cycle thinking to be considered for the next generation of regulations. The European Union has been actively pursuing Post 2020 regulations, looking hard at CO2 emissions reduction. On 15 May 2019, the new EU CO2 emission legislation for cars and vans for the post-2021 period entered into force, with the objective of contributing to decarbonisation and modernisation of Europe’s road transport sector in line with the EU’s commitments under the Paris International Climate Agreement. The main instrument to achieve this is a further reduction of tailpipe CO2 emissions from new cars by 37.5% by 2030 compared with the 2021 baseline as well as providing incentives to car manufacturers to sell more low-emission vehicles (<50gCO2/km) in the EU.
The direction of EU policy appears clear: cars need to emit less CO2. Others are questioning the focus on emissions reduction in the use phase of a vehicle and whether this will result in overall emissions savings. In fact, improvements in the driving phase could be cancelled out by increased emissions from the production and later the recycling of the vehicle as manufacturers turn to alternative materials and powertrains that could be more energy intensive to produce.
So, what is the solution?
Perhaps it is already in the recently adopted EU. The legislative text is for all intents and purposes a continuation of the existing CO2 emission legislation with more stringent tailpipe-based targets and verification. Yet it features one notable new element: the idea of reporting on the life cycle emissions of cars.
Article 7 – Monitoring and reporting of average emissions
10. The Commission shall no later than 2023 evaluate the possibility of developing a common Union methodology for the assessment and the consistent data reporting of the full life-cycle CO2 emissions of passenger cars and light commercial vehicles that are placed on the Union market. The Commission shall transmit to the European Parliament and to the Council that evaluation, including, where appropriate, proposals for follow-up measures, such as legislative proposals.
By 2023, the European Commission is tasked with assessing the feasibility of creating an EU methodology for harmonised and consistent reporting of full vehicle life cycle CO2 emissions.

Figure 1: Average historical CO2 emission values and adopted CO2 standards for new passenger cars in the EU. All CO2 values refer to New European Driving Cycle (NEDC) measurements. Source: ICCT
With a reporting framework of this kind, regulators could better anticipate the impact of changes in the vehicle fleet on overall emissions and identify the appropriate policy instruments, thereby being able to future-proof the legislation.
Going forward, the European Commission is expected to undertake a feasibility study to identify possible ways to measure vehicle life cycle emissions in a consistent and harmonised way. The conclusions of this work and any possible recommendations for implementing the methodology into EU law would be part of a report to the European Parliament in time for a review of the Regulation by 2023.
As life cycle assessments are already used by a wide range of stakeholders in the automotive sector, it will also be up to them to contribute to this work and help ensure future debates on the best way to decarbonise the EU road transport sector can draw on their experience.