An inspiring story
You are most likely wondering why WorldAutoSteel is writing a blog about a bicycle. It is because when we talked to Jia-Uei Chan, Regional Business Development at our member company, thyssenkrupp Steel Europe (TKSe), about the journey of inventing the world’s first Advanced High-Strength Steel road bike, we were incredibly inspired. This is more than a story about a steel bicycle. This is the story of steel innovation, conceived in a WorldAutoSteel members workshop to brainstorm ideas on transforming steel’s image to the sophisticated and advanced material it is. Their journey led to new steel applications, patentable processes, and in the steelworks bicycle, ideas that we think can inspire new automotive applications as well. And anyway, who doesn’t like an inspiring story?
Bikes of this genre have some of the same requirements of modern vehicles: lightweight, strength and durability, affordability, and high performance. To achieve these, the thyssenkrupp steelworks team developed what they called inbike® technology, which combines high-strength steel, half-shell technology and automated laser welding.
How it was made
The bike frame is made from DP 330/590 steel, used for its cold forming abilities, stamped as thin as 0.7mm. The steel blanks are pressed into a die to form two half-shells in a deep-drawing process.
A major challenge was to bring these two half shells together in such a way that minimized gaps and achieved a tight fit, enabling automated laser welding (this process requires no gaps over 6 meters of contact length), while ensuring that the frame achieves an elegant, seamless look. Enter innovation.
At the stamping plant, the half-shells were fitted with “dimples,” (See Figure 1) tiny bumps on the welding flanges that create channels at the weld seam for the zinc, preventing vaporized zinc from remaining trapped in the seam during subsequent welding. The half shells were then clamped in a special device and shipped to the laser specialist (See Figure 2).
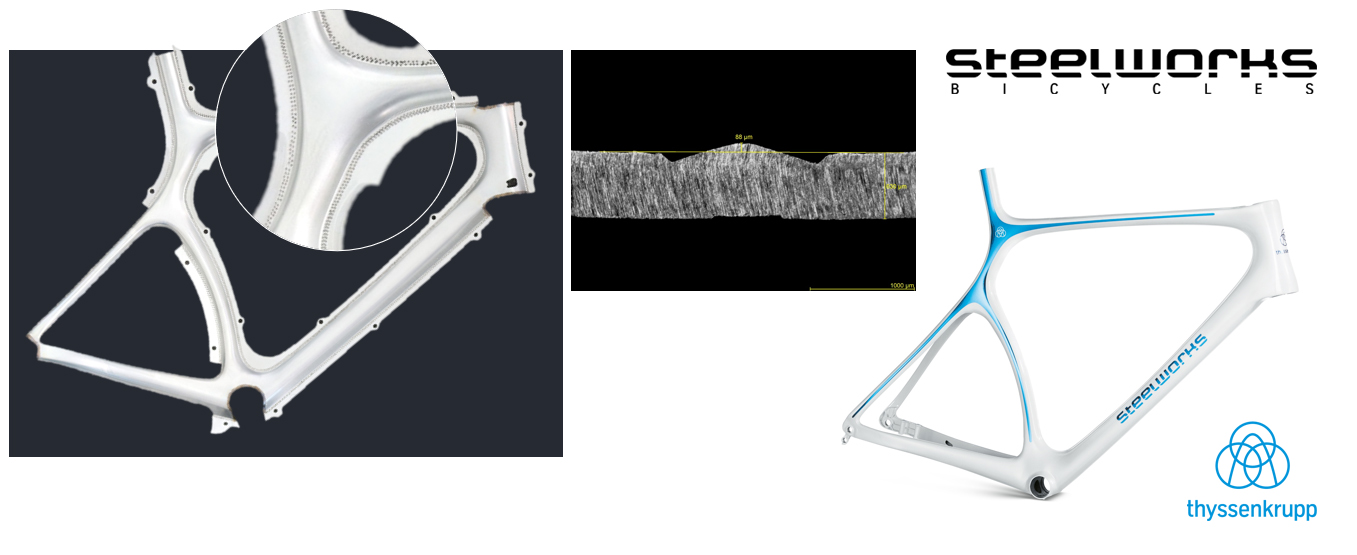
Figure 1: Tiny bumps prevent vaporized zinc from remaining trapped in the seam during subsequent welding.
The particular challenge lay in the reliable processing and fusing of both frame halves by means of automated laser welding in such a way that no damage to the frame would occur, while also ensuring the weld seam lay as close as possible to the bend radius of the frame halves. The complex frame shape is welded by following a sophisticated trajectory in a 3-D space. After countless continuous improvement exercises, the steelworks team was able to achieve a very flat, elegant weld seam design. This translates into a very stable bike, with a frame that has the needed rigidity in the bottom bracket area to enable high biomechanical power transmission, but with high elasticity in the seat tube configuration to make for an unusually comfortable ride. In comparison, aluminium and carbon fiber bikes are very stiff and characteristic of an unpleasant ride experience.
Inventing the possibility
Tackling a project that is such a reach beyond the norm is never easy. The thyssenkrupp steelworks team repeatedly heard from qualified experts that the project was actually not feasible. At the same time, they had partners who were so fascinated by the challenge that they wanted to make it possible. Chan related to WorldAutoSteel that there were many times when giving up was the more attractive option. Endurance won out. And as it turns out, the half-shell technology invented out of necessity for this bike could find an application in the tough requirements of an electric vehicle battery case.
Says Chan, “We genuinely believed that steel is the perfect material for a road bike. And we wanted to break with convention and make the most out of steel with high-tech engineering.” Have a look at steelworks.bike, and you will undoubtedly agree they did just that.