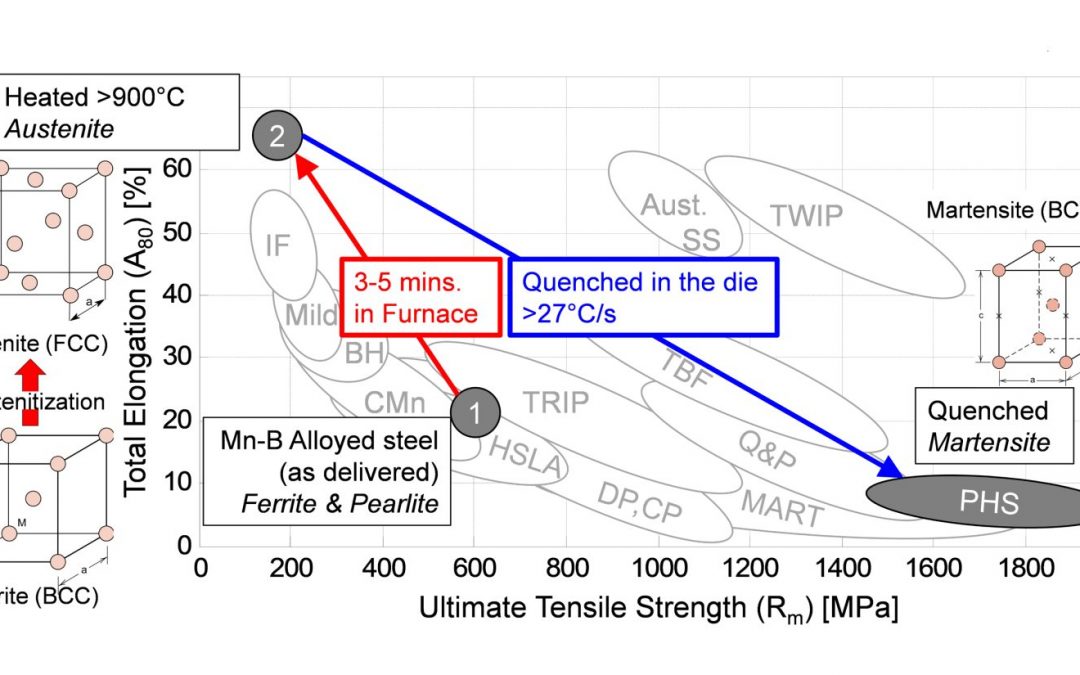
PHS Production Methods
- Direct Process
- Indirect Process
- Hybrid Process
- Pre-Cooled Direct Process
- Multi-Step Process
- Roll Form PHS
- Form Fixture Hardening
- Form Blow Hardening / Hot Gas Metal Forming
- 3DQ (3-Dimensional Hot Bending and Quenching)
- Steel Tube Air Forming (STAF)
In its simplest explanation hot stamping consists of five operations: (1) blanking (or cutting-to-length), (2) forming, (3) heating, (4) cooling (quenching) and (5) trimming/piercing. Each process route listed below has a distinct order or type of these operations.
In most sources, hot stamping is explained with only two processes: Direct hot stamping (also known as Press Hardening) and indirect hot stamping (also known as Form Hardening). While this used to be accurate, there are currently at least 10 processes for part manufacturing:
- Direct Process (Blanking > Heating > Forming > Quenching > Trimming)
- Indirect Process (Blanking > Forming & Trimming > Heating > Quenching > Trimming)
- Hybrid Process (Blanking > 1st Forming > Heating > 2nd Forming > Quenching > Trimming)
- Pre-cooled Direct Process (Blanking > Heating > Pre-cooling > Forming > Quenching > Trimming)
- Multi-Step Process (Blanking > Heating > Pre-cooling > Forming and Trimming > Air Quenching)
- Form Fixture Hardening (Roll Forming > Cut-to-length > Heating > Bending forming > Quenching > Trimming / piercing)
- Roll Form PHS (Roll Forming > Heating > Quenching > Cut-to-length > Trimming & piercing)
- Form Blow Hardening / Hot gas metal forming (Cut-to-length tube or roll formed / welded profile > Heating > Pressure forming > Quenching > Piercing)
- 3DQ (Cut-to-length tube > Local induction heating > 3-D Bending > Direct Water Quenching > Piercing)
- STAF (Cut-to-length tube > Cold preforming > Heating > Pressure Forming > Quenching > Piercing)
The video below explains some of these processes and how they are employed at Gestamp Automoción. Here, Paul Belanger, Director of Gestamp’s North American R&D Center, was interviewed by Kate Bachman, the Editor of STAMPING Journal®. Thanks are given to Paul and Kate, as well as FMA, Fabricators & Manufacturers Association®, for permission to reproduce this video.
Direct Process
The most common process route in hot stamping is still the direct process (also known as press hardening).D-20 Here, previously cut blanks are heated typically in a roller hearth or a multi-chamber furnace to over 900 °C to create a fully austenitic microstructure. Depending on the material handling system, transfer from the furnace to the press may take up 6 to 10 seconds.B-14 During this time, the blank may cool down to 700 °C.G-24 Forming is done immediately after the blanks are transferred on the die, and should be completed before the blank cools below 420 °C.G-24, K-18 The blanks are formed in hot condition (state ❷ in Figure 1), and quenched in the same die to achieve the required properties. For 22MnB5 steel, if the quenching rate is over 27 °C/s, the part will transform to almost 100% martensite. For productivity purposes, higher cooling rates are often realized.K-18 Typical cycle times for a direct process with the 22MnB5 chemistry could be between 10 and 20 seconds, depending on the thickness.B-14 Global R&D efforts target improvements in cycle time.
The process is typically used for bare/uncoated steels or AlSi coated steels. Zn coated blanks are not suitable for direct process, as pure Zn melts around 420 °C and GA (Zn-Fe) coatings around 530-780 °C. (see Figure 3)G-25 If forming is done with liquid Zn over the blank, microcracks may fill with Zn and lower the fatigue strength of the final part significantly.K-20 A recently developed alloy minimizes these concerns, as explained in the “Pre-cooled Direct Process” section below.
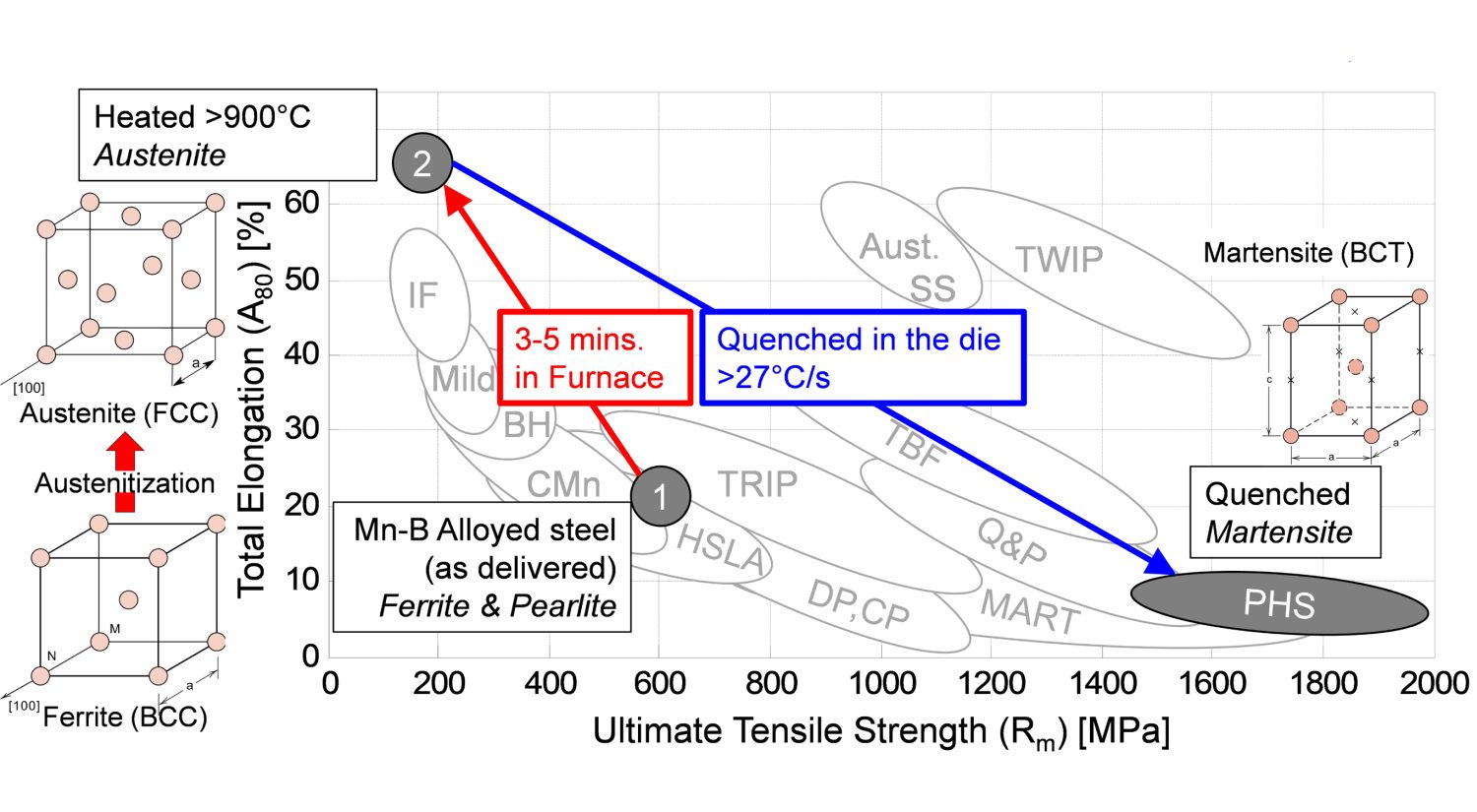
Figure 1: Summary of hot stamping processes. In direct process forming is done at state ❶, in indirect process at ❷B-14
Typical Al-Si coatings prevent scale formation and decarburization at elevated temperatures. The aluminum-rich coating contains 7% to 11 wt.% Si, and acts as a barrier to offer corrosion resistance during service.F-14 In automotive industry, typical coating weights are AS150 (75 g/m2 coating on each side) or AS80 (40 g/m2 coating on each side).A-51 Refer to our page on Al-Si coatings for more details.
When using uncoated blanks, controlled atmosphere in the furnace helps avoid excessive decarburization and scale formation. Surface scale locally changes the critical cooling rate, alters the metal flow and friction, and leads to premature tool wear. Without a controlled atmosphere, a surface conditioning step like shot blasting may be required after forming to remove the scale.A-52 Varnish coatings may also be used with direct hot stamping.
Formed parts must be trimmed and pierced to final geometry. In the direct process, the most common trimming method is laser cutting. The capital expense and cycle times associated with laser trimming factor into overall part cost calculations. In most plants, for every hot stamping line, there are 3 to 5 laser trimming machines.B-14
The grades used with the direct process may be referred to as PHS950Y1500T-DS (Press Hardening Steel with minimum 950 MPa yield, minimum 1500 MPa tensile strength, for Direct [Hot] Stamping).
Indirect Process
(Blanking > Forming & Trimming > Heating > Quenching > Surface Conditioning)
Typically used for galvanized blanks, indirect hot stamping, also known as form hardening, starts by cold forming the part (at ❶ in Figure 1) in a transfer press or a tandem transfer line. The direct process is limited in that only one forming die can be used. However, the indirect process can accommodate multiple die stations, allowing for the production of more complicated geometries, even those with undercuts. The part has almost the final shape exiting the cold forming press, where piercings and trimming could also be completed. The formed parts are then heated in a special furnace and quenched in a second die set.B-14,K-21,F-15
BMW 7 Series (2008-2015, codenamed F01) was the first car to have Zn-coated indirect hot stamped steel in its body-in-white.P-20 Zn-based coatings are favored for their cathodic protection. Zn-coated blanks may develop a thin oxide layer during heating, even if a protective atmosphere is used in the furnace. This layer helps preventing evaporation of the Zn (pure Zn evaporates at 907 °C at 1 atm. pressure), but must be removed before welding and painting. To achieve this, sandblasting, shot blasting or dry-ice (CO2) blasting are typically used.F-14, F-15 The grades for indirect process may be referred to as PHS950Y1500T-IS (Press Hardening Steel with minimum 950 MPa yield, minimum 1500 MPa tensile strength, for Indirect [Hot] Stamping).
The indirect process cannot be applied to Al-Si coated blanks, as they have a hard but brittle intermetallic layer which would crack during cold deformation.F-14
Hybrid (2-Step) Process
(Blanking > 1st Forming > Heating > 2nd Forming > Quenching > Trimming > Surface Conditioning)
In this process, as summarized in Figure 2, some of the forming occurs at the cold stage [❶ in Figure 1]. The semi-formed part then is heated in the furnace, significantly deformed to a final shape [❷ in Figure 1] and subsequently quenched in the same die. This process had found greater use in Europe, especially for deep drawn parts such as transmission tunnels. To avoid scale formation in the furnace and hot forming, a special varnish-type coating is commonly used. The final part must be surface cleaned with a process like shot blasting before welding to remove the varnish coating.S-63 Since the early 2010s, the process has been replaced by the direct process of Al-Si-coated blanks.N-15
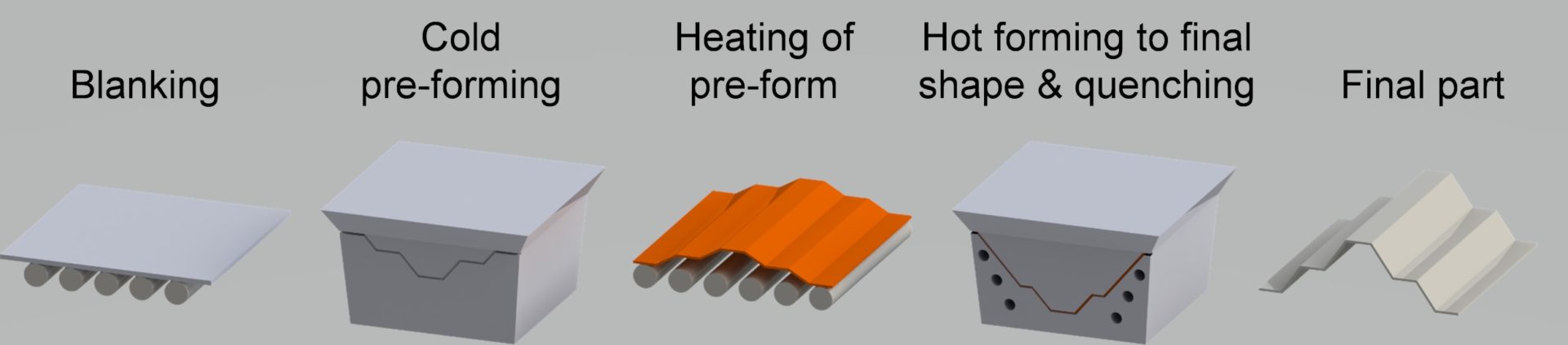
Figure 2: Summary of “hybrid process” where deformation is done both at cold and hot conditions.B-14
Pre-Cooled Direct Process
(Blanking > Heating > Pre-cooling > Forming > Quenching > Trimming > Surface conditioning)
A galvannealed (GA) coating primarily contains zinc and iron, and solidifies at temperatures between 530 °C and 782 °C, depending on the zinc content, as shown in Figure 3. Liquid Metal Embrittlement (LME) is not a concern if forming is done in the absence of liquid zinc.G-25 Hensen et al. conducted several studies heating galvannealed 22MnB5 blanks to 900 °C, but forming after a pre-cooling stage. As seen in Figure 4, the microcrack depth is significantly reduced when the forming starts at lower temperatures.H-26
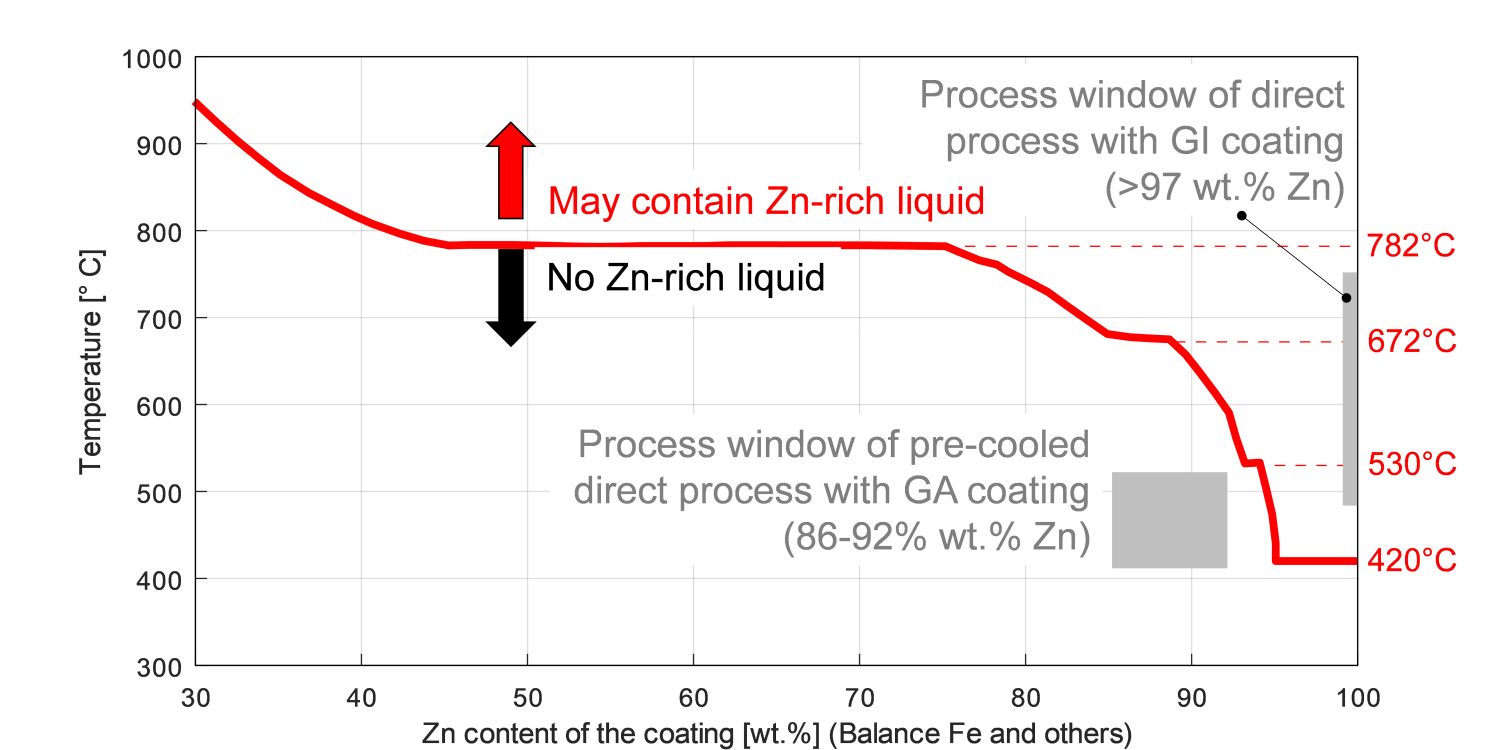
Figure 3: Temperature limit to ensure absence of Zn-rich liquid (re-created after Citations G-25 and G-26)
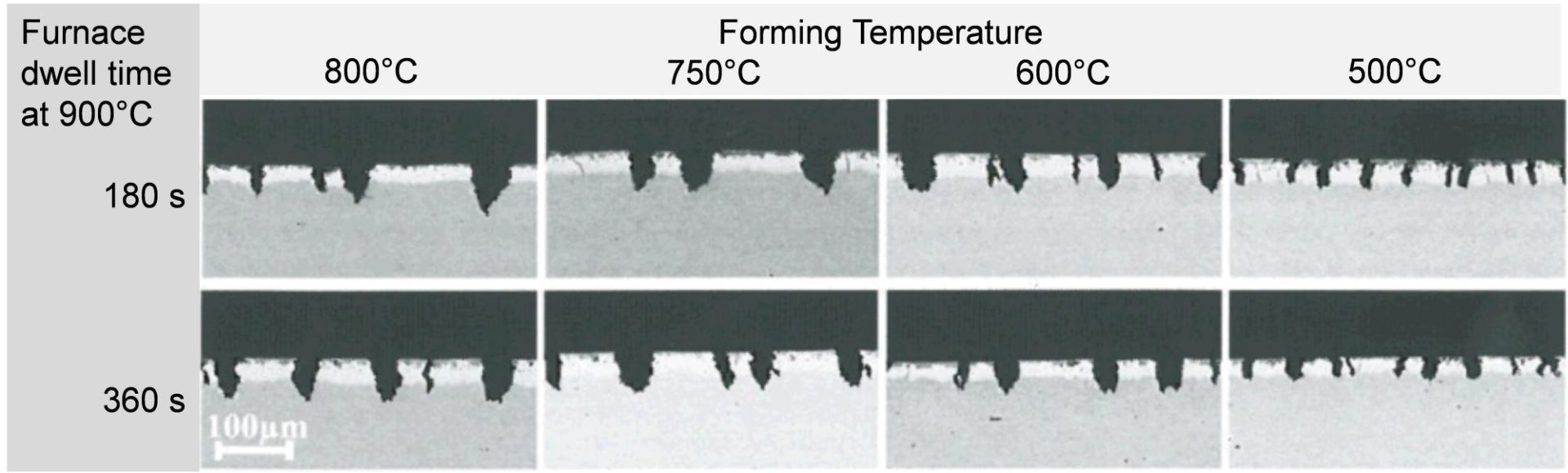
Figure 4: Crack depth reduces significantly if the forming is done at lower temperature (re-created after Citation H-26)
In the pre-cooled direct process, the blank is heated above the austenitization temperature (approximately 870-900 °C), and kept in the furnace for a minimum soaking time of 45 seconds. Once the blank leaves the furnace, it is first pre-cooled to approximately 500 °C and then formed. Typical 22MnB5 cannot be formed at this temperature due to two reasons: (1) its formability would be reduced and (2) forming could not be completed before the start of martensite formation at approximately 420 °C).K-22, V-8
The development of a “conversion-delayed” hot stamping grade (see PHS Grades with approximately 1500 MPa TS), commonly known as 20MnB8, addresses these concerns. This steel has lower carbon (0.20%, as the number 20 in 20MnB8 implies), but higher Mn (8/4 = 2%). . This chemistry modification slows the kinetics of the phase transformation compared with 22MnB5 – the critical cooling rate of 20MnB8 is approximately 10 °C/s. This allows the part to be transferred from pre-cooling stage to the forming die.
In the pre-cooled direct process, first the blank is heated to over 870-900 °C and soaked for at least 45 seconds. Then the blank is transferred to “pre-cooling stage” in less than 10 seconds. Precooling must be done at a rate over 20 °C/s, until the blank is cooled to approximately 500 °C. Then the part is transferred from the pre-cooling device to the press in less than 7 seconds. The forming is done in one hit in a hydraulic or servo-mechanical press, which can dwell at the bottom. The cooling rate after pre-cooling is advised to be over 40 °C/s. The final part may have zinc oxides and surface cleaning is required.K-22, V-8 The grade may be referred to as PHS950Y1500T-PS (Press Hardening Steel with minimum 950 MPa yield, minimum 1500 MPa tensile strength, Pre-cooled and Stamped).
Recently, several researchers have shown that pre-cooling may be used for drawing deeper partsO-6 or to achieve better thickness distribution of the final part.G-24 Since formed parts are typically removed from the press at approximately 200 °C, a pre-cooled part may require shorter time to quench, thus increasing the parts per minute.G-24
Multi-Step Process
(Blanking > Heating > Pre-cooling > Forming and Trimming > Air Quenching)
22MnSiB9-5 (see PHS Grades with approximately 1500 MPa TS) is a new steel grade developed by Kobe SteelH-27 for a transfer press process, named as “multi-step”. This steel has higher Mn and Si content, compared to typical 22MnB5. As quenched, the material has similar mechanical properties with 22MnB5. As of 2020, there is at least one automotive part mass produced with this technology and is applied to a compact car in Germany.G-27 Although critical cooling rate is listed as 2.5 °C/s, even at a cooling rate of 1 °C/s, hardness over 450HV can be achieved.H-27 This critical cooling rate allows the material to be “air-hardenable” and thus, can handle a transfer press operation (hence the name multi-step) in a servo press. This material is available only with Zn coating and requires a pre-cooling step before the transfer press operation.B-15 The grade may be referred to as PHS950Y1500T-MS (Press Hardening Steel with minimum 950 MPa yield, minimum 1500 MPa tensile strength, for Multi-Step process).
Roll Form PHS
(Roll Forming > Heating > Quenching > Cut-to-length > Trimming & piercing)
Also known as inline hardening, this process is used to make profiles with constant cross sections and linear shapes. It is also possible to have closed profiles (tubes and similar) with this technology by adding a laser welding to the line (see Figure 5a). The process has been successfully used in many car bodies. Typical uses are: cross members, roof bows, side impact door beams, bumpers (with no sweep), front crash components and similar.G-28, H-28, F-16
The heating is typically done with induction heating, see Figure 5b. In one of the installations, the first induction coil operates at 25 kHz and the second at 200 kHz. The total heating power was approximately 700 kW and the line can run as fast as 6 m/s. It was found that if lubrication, speed and bending radius can be optimized, AlSi coated blanks could also be cold roll formed. However, they are not suitable for induction heating and may require a different process, such as form fixture hardening.K-23
Recently, voestalpine developed a Zn-coated steel for roll forming applications. This process also uses induction heating and water cooling. As the deformation is done at cold condition, the parts do not suffer from liquid metal embrittlement (LME).K-22
Form Fixture Hardening
(Roll Forming (or tube blank) > Cut-to-length > Heating > Bending & forming > Quenching > Trimming / Piercing)
The main difference between roll form PHS and form fixture hardening is the secondary “hot bending and forming” in the press. Here, cold roll formed profiles are cut-to-length and heated in a furnace. Heated profiles are then transferred to a press die, where sweep bending and/or further forming operations are completed. The parts are subsequently quenched in the same press die, similar to direct process. A typical line layout can be seen in Figure 6a. The secondary forming makes variable sections possible, as seen in Figure 6b. As the parts are cold roll formed and furnace heated, uncoated, Zn-coated and AlSi-coated (with precautions not to crack AlSi) blanks may be used in this process.H-28, K-23
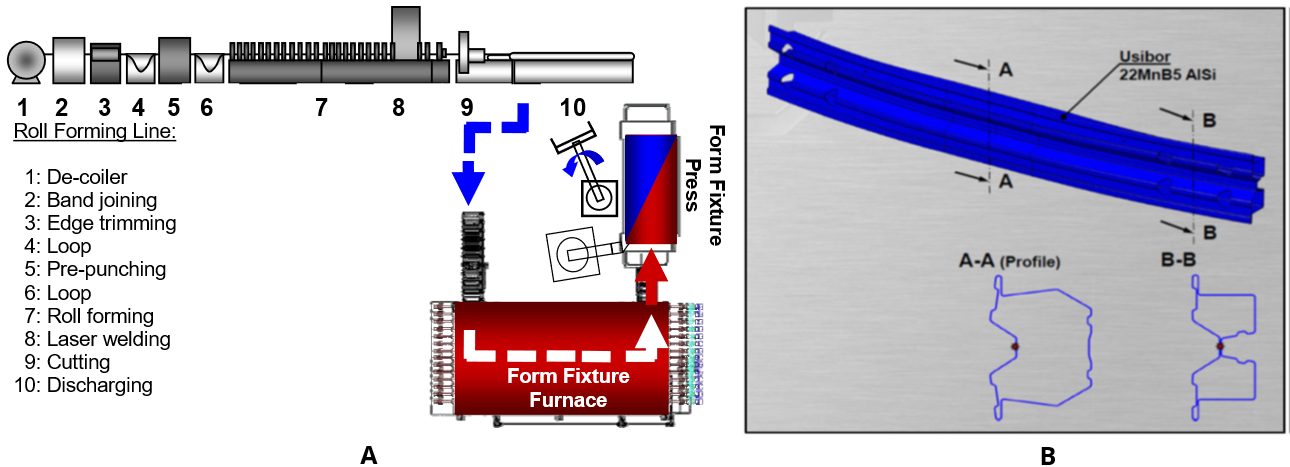
Figure 6: Form fixture hardening: (a) schematic of a lineK-23, (b) bumper beam of Ford Mustang (2004-2014) made by this process.L-26
Form fixture hardening parts have been used in low volume cars such as Porsche 911 or Bentley Mulsanne. In some cars, form fixture hardening was used to manufacture the A-pillar of the convertible (cabriolet) versions of high-volume cars, especially in Europe. Most of these applications involved uncoated boron alloyed tubes (similar to 22MnB5).H-28 The 5th generation Ford Mustang (2004-2014) had form fixture hardened bumper beams in the front and rear, as seen in Figure 6b.L-26 The form fixture hardening process allows for use of AlSi coatings, since the steel goes through a furnace rather than an induction hardening step. Special care must be taken in cold roll-forming process to ensure the AlSi coating is not damaged.K-23
Form Blow Hardening / Hot Gas Metal Forming
(Cut-to-length tube or roll formed and welded profile > Heating > Pressure forming > Quenching > Piercing)
In hot gas metal forming, the tube or roll formed closed profile is heated first and placed onto a die set. The ends of the tube are sealed and pressurized gas or granular medium is forced inside the tubular blank. The forming forces are applied by the high pressure built inside the tube.C-16 It is also possible to end-feed material as in the case of (cold) tube hydroforming. After the deformation, the part is quenched either with water (form blow hardening) or by the air inside and the surface of the tool cavity (hot gas metal forming). In the latter case, similar to direct process, a water-cooling channel system inside the die inserts are typically required.K-23
Fraunhofer IWU has developed a hot gas metal forming setup in which both forming and quenching are done by compressed air. As shown in Figure 7a, the internal pressure can be increased to 70 MPa (700 bars) in only 6 seconds. The tools are cooled with internal cooling channels, Figure 7b. The parts produced with this technique have hardness values between 460 and 530 HV. Crashbox and camshafts are among the parts produced.L-27, N-16
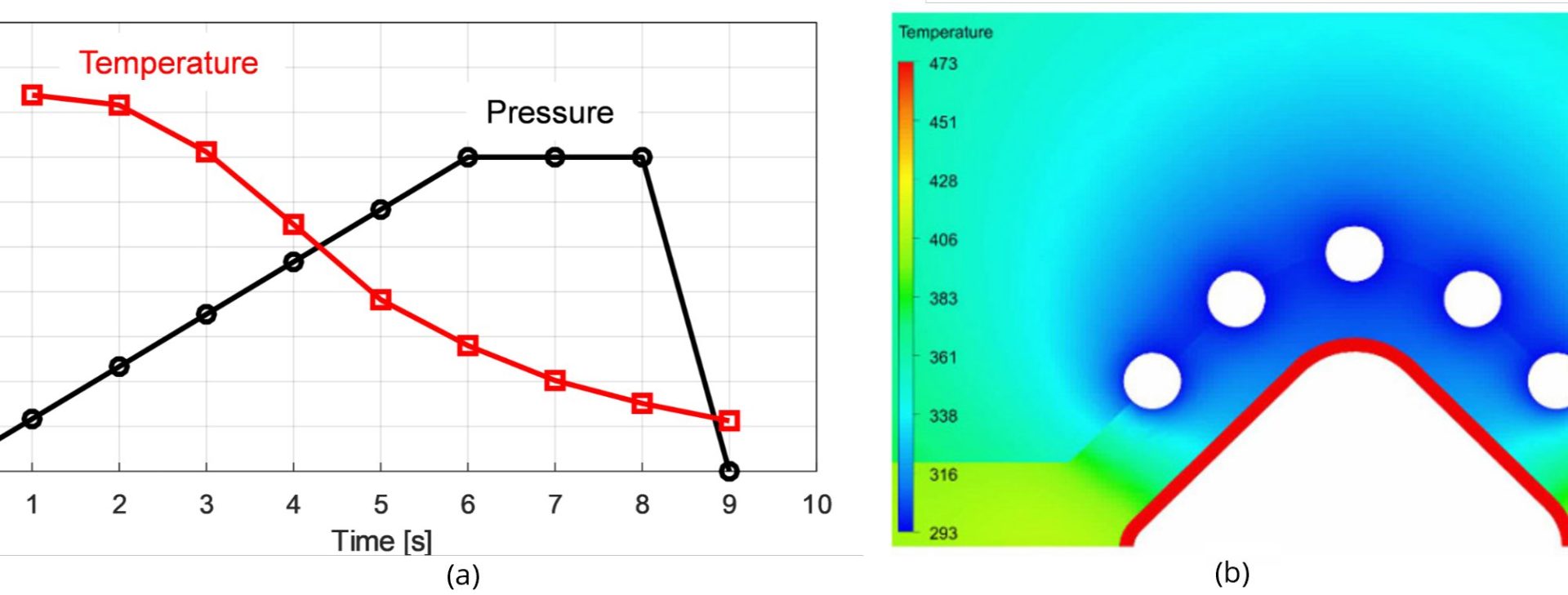
Figure 7: Blow forming and quenching with air: (a) change of pressure in the tube and temperature of the tube, (b) simulation of heat transfer to the dies and cooling channels (recreated after Citation N-16)
In 2011, Spanish car maker SEAT published a study on form blow hardening process. In this study, they replaced the A-pillar and cantrail assembly of the SEAT León (Mk2, SOP 2005) with one form blow hardened part. The results were summarized asO-7:
- 7.9kg weight reduction per car,
- Sheet material utilization increased from 40 to 95%,
- Number of components in the assembly on one side of the car reduced from 5 to 2, and the roof rail was eliminated.
One advantage of this technology is the possibility to use the same die set for different wall thickness tubes. By doing so, parts can be produced for different variants of a car (i.e., coupe and cabrio, or North American spec. vs. emerging market spec.). This information applies to monolithic (i.e., same thickness throughout the tube) and tailor rolled/welded tubes as well.F-16 In 2017, tubular parts are hot gas formed by using 1900 MPa PHS tubes for customer trials.F-17
Since 2018, form blow hardening is being used in the Ford FocusB-16 and Jeep Wrangler.B-17 In the Ford Focus, a tailor rolled tube with thicknesses between 1.0 and 1.8 mm is used in Europe, whereas in China it is a monolithic (same thickness everywhere) 1.6 mm thick tube.F-16
3-Dimensional Hot Bending and Quenching (3DQ)
(Cut-to-length tube > Local induction heating > 3-D Bending > Direct Water Quenching > Piercing)
In the 3DQ process, a tubular profile with constant cross section is quickly heated by induction heaters. By using movable roller dies, the part is bent. As the material is fed, water is sprayed on the induction heated portion of the tube to quench and harden it. The schematic of the process and the material strength through the process is illustrated in Figure 8. It is also possible to replace the movable roller dies with an industrial robot to bend and twist the tubular part.T-25
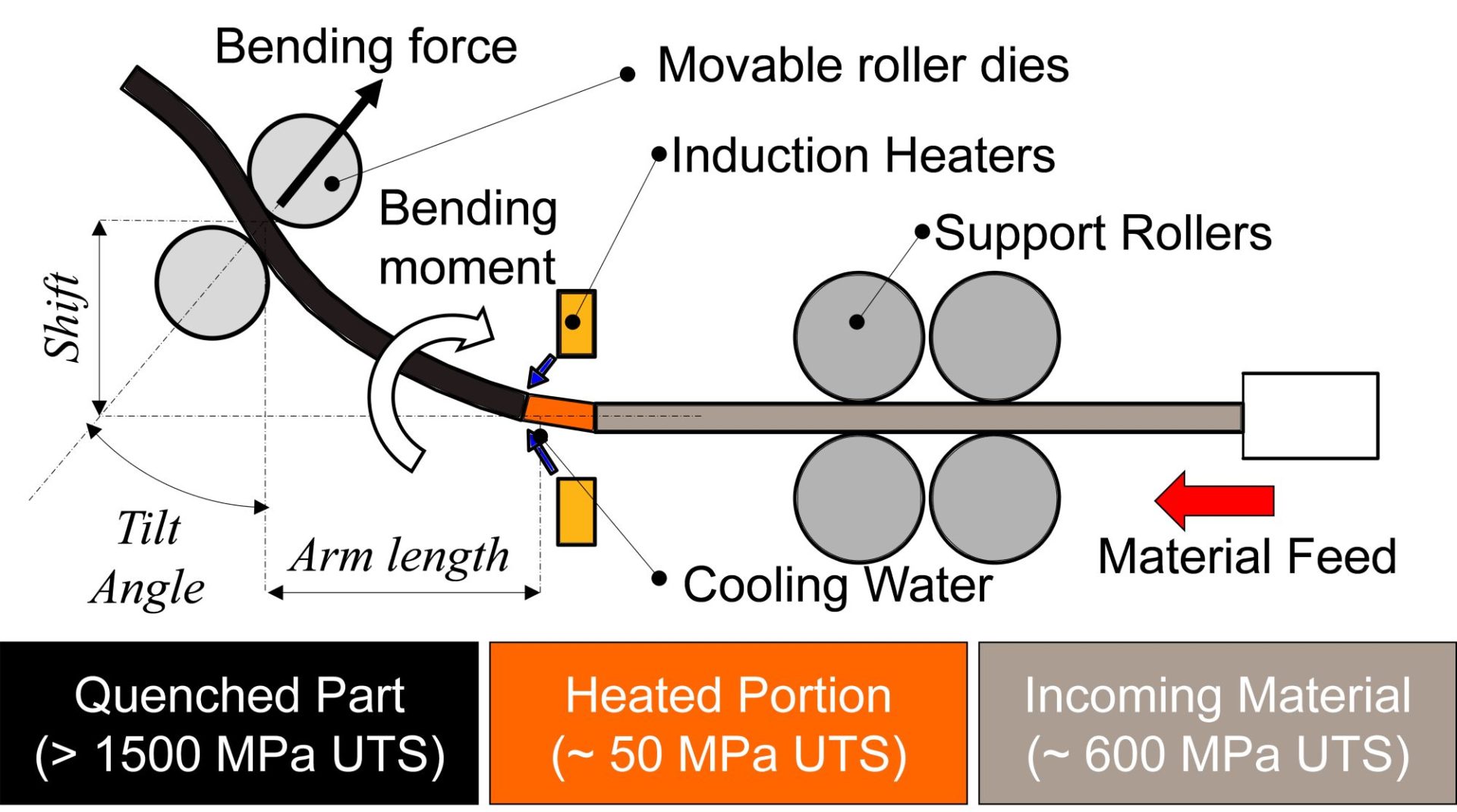
Figure 8: Schematic of 3DQ system (re-created after Citation T-25)
In January 2013, Mazda announced that the ISOFIX connection in the rear seats of a Premacy MPV (known as Mazda 5 in some markets) model was produced by this method, as shown in Figure 9a.M-24 In 2016, Honda started production of the sports car NSX (known as Acura NSX in some markets). This vehicle’s A-pillars were produced by 3DQ process, as shown in Figure 9b.H-29
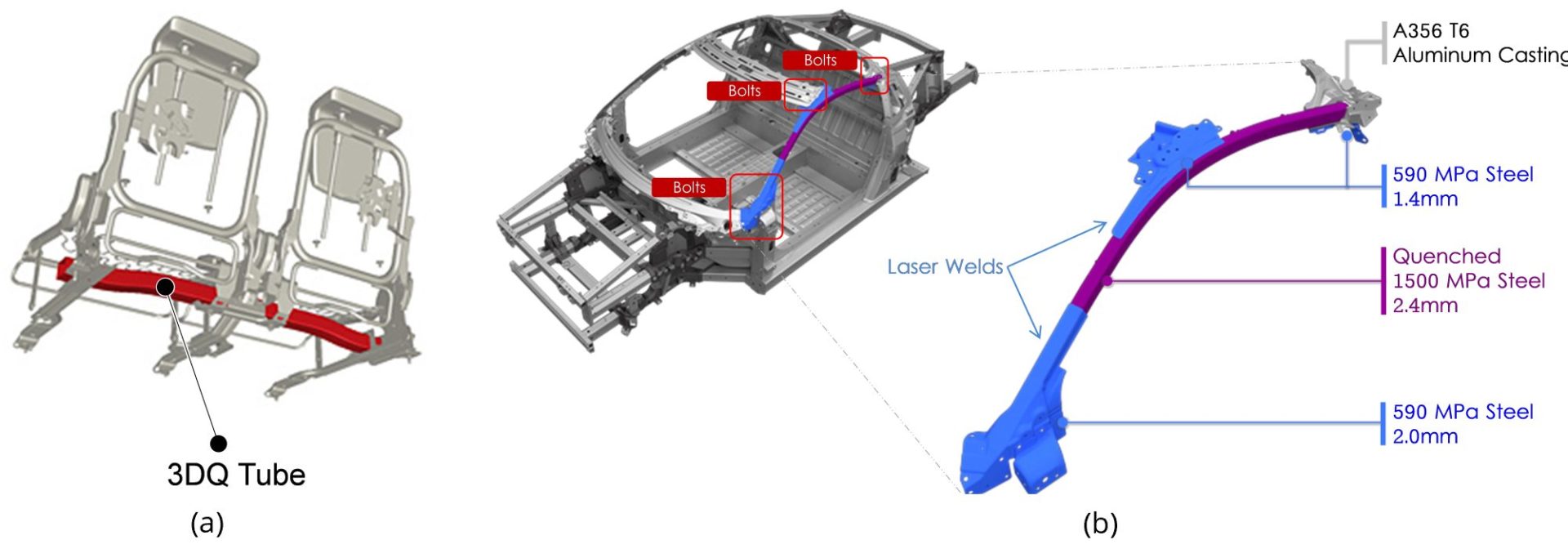
Figure 9: 3DQ applications: (a) Seat reinforcement of Mazda 5/PremacyM-24, (b) Acura NSX’s A-pillar.H-29
The technology has been used on uncoated blanks. In 2019, an academic study showed the feasibility of using Zn coated blanks in the 3DQ process.R-10
Steel Tube Air Forming process (STAF)
(Cut-to-length tube > Cold bending > Heating > Press Forming > Pressure Forming > Quenching > Piercing)
Steel Tube Air Forming process (STAF) is a modified and enhanced version of hot gas metal forming. In the STAF process, a metal tube is bent in a small press at room temperature. The preformed tube is transferred to the main press, where it is heated to the critical temperature using electrical conduction (Joule heating) by passing current through the tube. The first step creates the flanges where the press closes on the partially air blow formed tube. In the second step, air pressure completes the process by forming the desired cross section and overall shape.
As seen in Figure 10, the parts made with the STAF process can have a flange area for further welding/joining to other car body components. Some peripheral parts can be integrated into a single STAF part, improving productivity and manufacturing cost. The continuous closed cross section is created without the need for spot welding, improving stiffness and further reducing manufacturing costs. These factors combine to result in mass savings compared with conventional hot formed components, as indicated in Figure 11. F-18, F-41, F-42
Figure 10: The Steel Tube Air Forming process compared with other manufacturing approaches. STAF integrates flange formation without the need for additional spot welding.F-42 HSS stands for High-Strength Steel and may refer to conventional HSS or Advanced High-Strength Steels (AHSS).
Figure 11: The STAF process may reduce part count, assembled weight, and manufacturing complexity compared with other manufacturing approaches.F-41
The following video, kindly provided by Sumitomo Heavy Industries, highlights the STAF process along with associated benefits.F-41
![]() |
Thanks are given to Eren Billur, Ph.D., Billur MetalForm, who contributed this article. |
- Direct Process
- Indirect Process
- Hybrid Process
- Pre-Cooled Direct Process
- Multi-Step Process
- Roll Form PHS
- Form Fixture Hardening
- Form Blow Hardening / Hot Gas Metal Forming
- 3DQ (3-Dimensional Hot Bending and Quenching)
- Steel Tube Air Forming (STAF)