RSW Joint Performance Testing
The joint strength in the peeling direction begins to decrease when the Base Metal (BM) strength exceeds 780 MPa. It has been found that the Cross-Tension Strength (CTS) of HSS joints could be improved by using appropriate conditions for post-heat conduction. Unlike the conventional tempering process in which the weld is tempered after a sufficient cooling time (i.e., after completion of martensite transformation of the weld), the post-heat conduction process incorporates a short cooling time; hence, it will not cause significant decline in productivity. The post-heat conduction process is described in detail below.
Figure 1 illustrates the effect of cooling time on CTS. It is clear that CTS reaches a peak for a cooling time of 6 cycles and improves when the post-heat conduction time is increased, even when the cooling time is increased to 35 cycles. With the aim of investigating why CTS improved, as described above, the conditions of solidification segregation were analyzed, for example, Mn, Si, and P. An example of P segregation is shown in Figure 2. When post-heat conduction was not performed at all or was performed using the conditions under which CTS did not improve [as shown in Figure 2 (b)], the segregation of P in the same part decreased markedly. One reason for this is thought to be as follows. The element that was solidification- segregated during regular conduction was diffused during the post-heat conduction. As described in the preceding section, it is believed that the toughness of the nugget edge increased, thereby helping to enhance CTS.
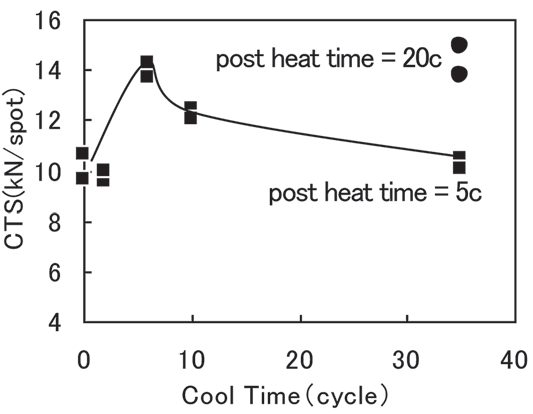
Figure 1: Effect of cool time on CTS (HS, 2-0-mm sheet thickness, 5-√t nugget diameter).N-5
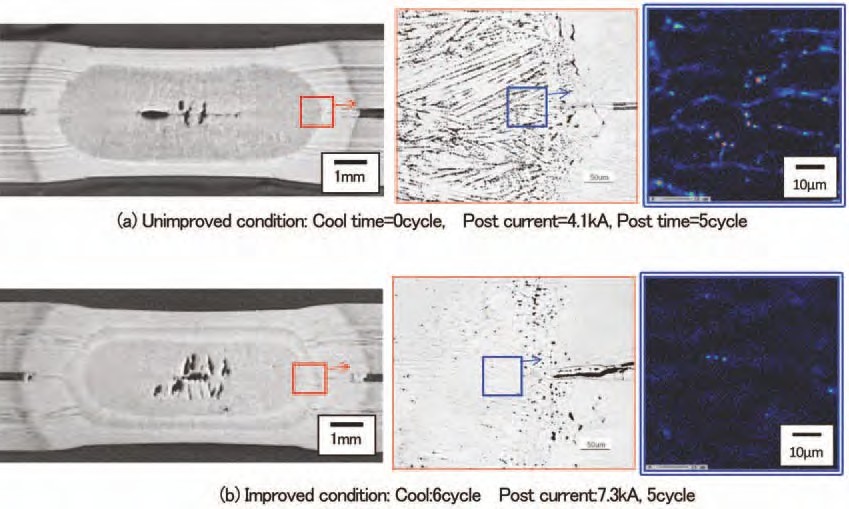
Figure 2: Effect of post-heat conditions on microstructure and solidification segregation at edge of nugget.N-5
The effect of post-heat conduction in easing such solidification segregation is supported by other researchers. It should be noted that the hardness of the nugget interior remains the same, regardless of whether the post-heat conduction is implemented. Therefore, the above improvement in CTS cannot be attributed to the effect of tempering. Conversely, the application of post-heat conduction increased the degree and width of softening of the HAZ. From the standpoint of fracture mechanics, the degree of influence of the widening of soft HAZ on the improvement in CTS was estimated to be about 4%. Therefore, the improvement in CTS by post-heat conduction can be attributed mainly to the enhancement of fracture toughness by the easing of solidification segregation.
Figure 3 shows comparison of CTS between with and without pulse pattern at the nugget diameter. The strength became higher when welded with pulse pattern, especially when the pulse current was between 8 and 9 kA. These results suggest that the pulsation pattern achieved adequate reduction in solidification segregation and soften the HAZ.
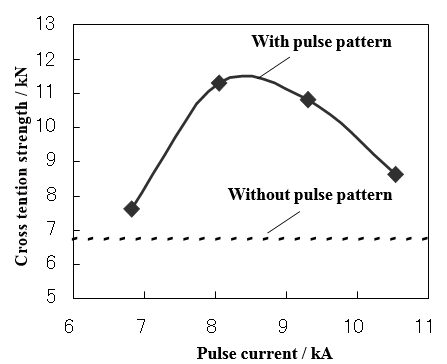
Figure 3: Comparison of CTS with and without pulse pattern.J-1
RSW Joint Performance Testing
In a comparative studyL-6 of the spot weld fatigue strength of various steels grades, some of which included grades such as 1.33-mm Fully Stabilized (FS) 300/420 (HDGA), 1.35-mm DP 340/600 (HDGA), 1.24-mm TRIP 340/600 (HDGA), and 1.41-mm TRIP 340/600 (HDGA), it was concluded that Base Metal (BM) microstructure/properties have relatively little influence on spot weld fatigue behavior (Figure 1). However, DP 340/600 and TRIP 340/600 steels have slightly better spot weld fatigue performance than conventional low-strength Aluminum-Killed Drawing Quality (AKDQ) steels. Further, it was found that the fatigue strength of spot welds is mainly controlled by design factors such as sheet thickness and weld diameter. Therefore, if down-gauging with HSS is considered, design changes should be considered necessary to maintain durability of spot-welded assemblies.
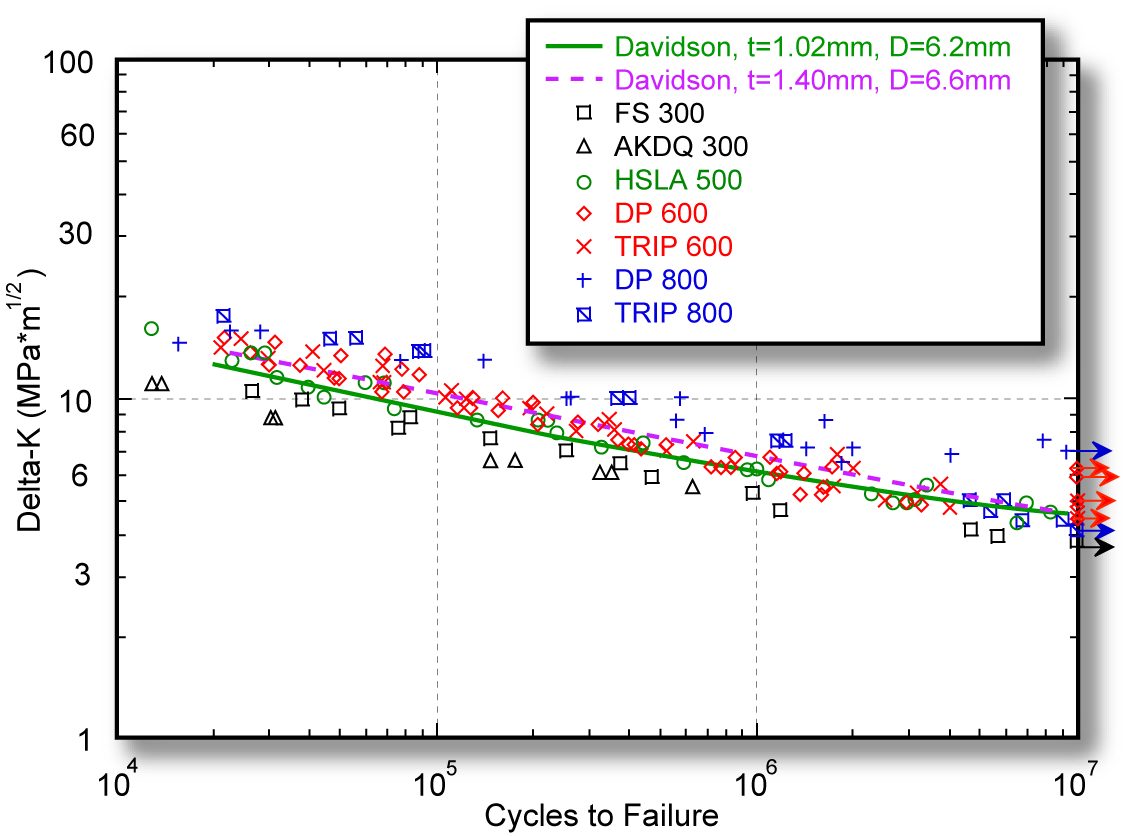
Figure 1: Tensile-shear spot weld fatigue endurance curves for various HSS
(The data are normalized to account for differences in sheet thickness and weld size. Davidson’s data in the plot refer to historical data.L-6).
Similar to mild steel, an increase in the number of welds in AHSS will increase the component fatigue strength (Figure 2). Multiple welds on AHSS will increase the fatigue strength more than mild steel.
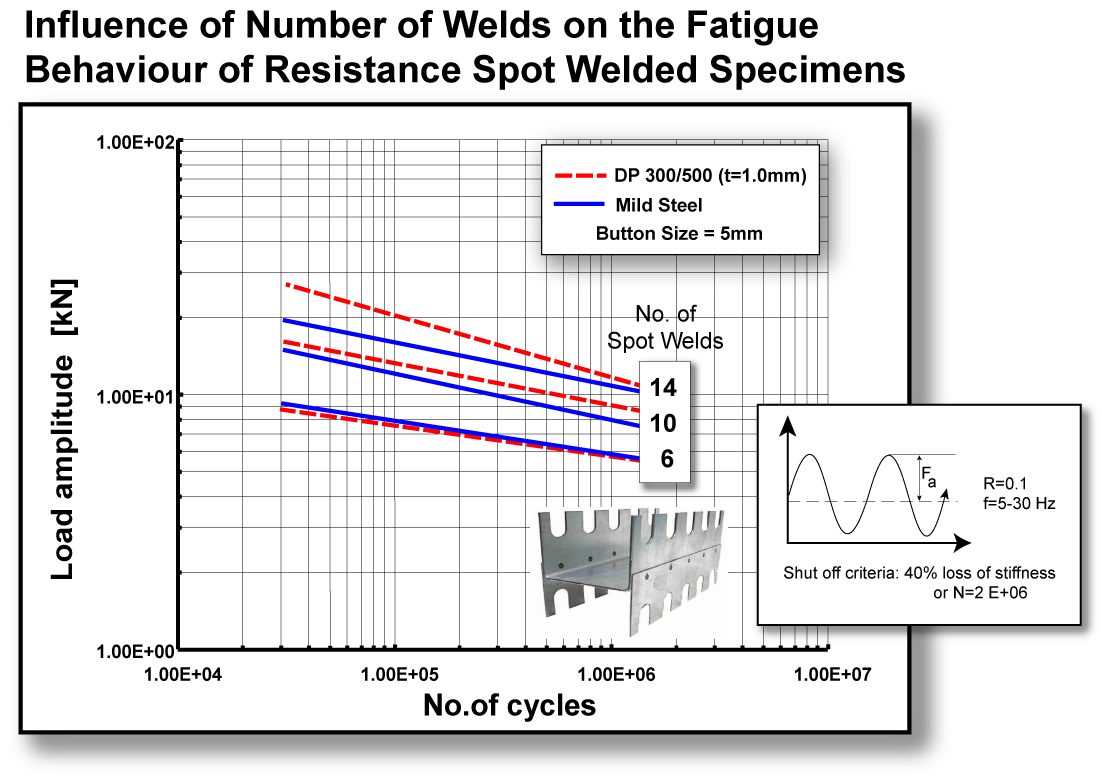
Figure 2: Effect of increase in number of welds in mild steel and DP steel components.S-4
Figure 3 is a representative best-fit curve based on numerous data points obtained from mild steel, DP steels with tensile strengths ranging from 500 to 980 MPa, and MS steel with a tensile strength of 1400 MPa. The curve indicates that the fatigue strength of single spot welds does not depend on the BM strength.
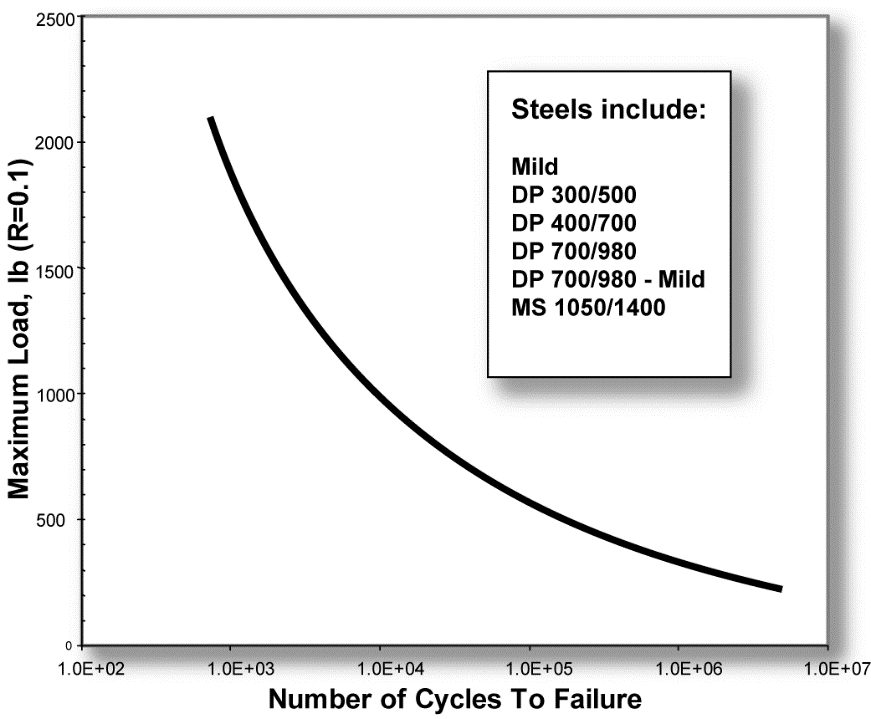
Figure 3: A best-fit curve through many data points for MS, DP steels, and MS steel (Fatigue strength of single spot welds does not depend on BM strength.L-2)
RSW Joint Performance Testing
Peel and chisel testing of resistance spot welds (RSW) in AHSS may produce fracture through the weld during destructive or teardown testing. This type of fracture becomes more common with increasing sheet thickness and BM strength. Weld metal fracture may accompany significant distortion of the metal immediately adjacent to the weld during testing. Such distortion is shown in Figures 1 and 2. Under these conditions weld metal fracture may not accurately predict serviceability of the joint. Weld performance of AHSS depends on microstructure, loading mode, loading rate, and degree of constraint on the weld.
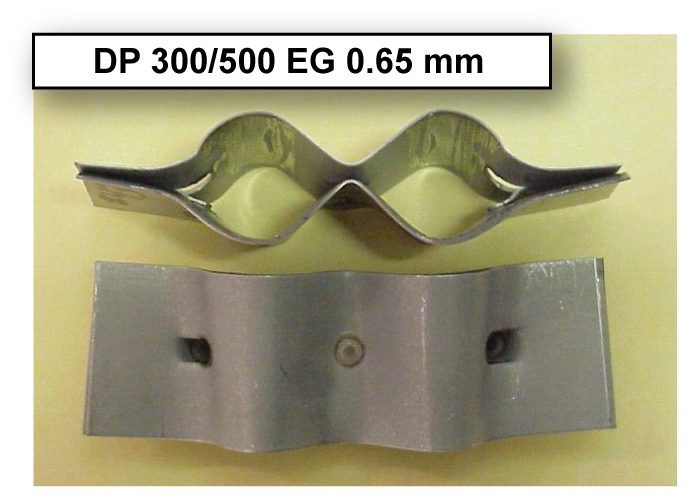
Figure 1: Example of laboratory dynamic destructive chisel testing of DP 300/500 EG 0.65-mm samples.M-1
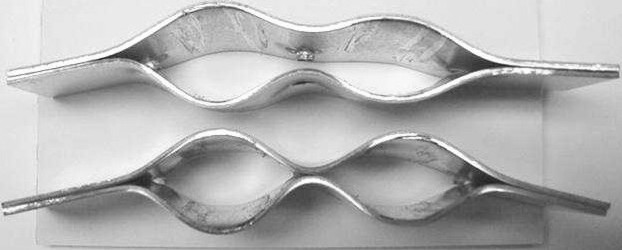
Figure 2: Example of laboratory dynamic destructive chisel testing of DP 350/600 GI 1.4-mm samples.M-1
Additionally, because of inherent stiffness of AHSS sheets, “nondestructive” chisel testing (Figure 3) on AHSS spot-welded panels will deform the panel permanently and may promote weld metal fracture. Therefore, this type of in-process weld check method is not recommended for AHSS with thicknesses greater than 1.0 mm. Alternative test methods should be explored for use in field-testing of spot welds in AHSS.
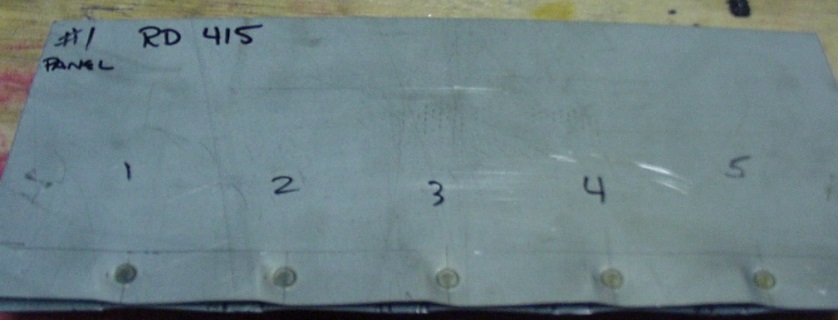
Figure 3: Semi-destructive chisel testing in 0.8-mm DP 300/500 EG.M-1
Ultrasonic nondestructive spot weld testing has gained acceptance with some manufacturers. It still needs further development before it can replace destructive weld testing completely. Some on-line real-time systems to monitor the resistance welding are currently available and are being used in some weld shops.
Weld-Shear Tension Strength
The Advanced High-Strength Steel (AHSS) weld tensile strength is proportional to material tensile properties and is higher than mild steel spot weld strength (Figure 4).
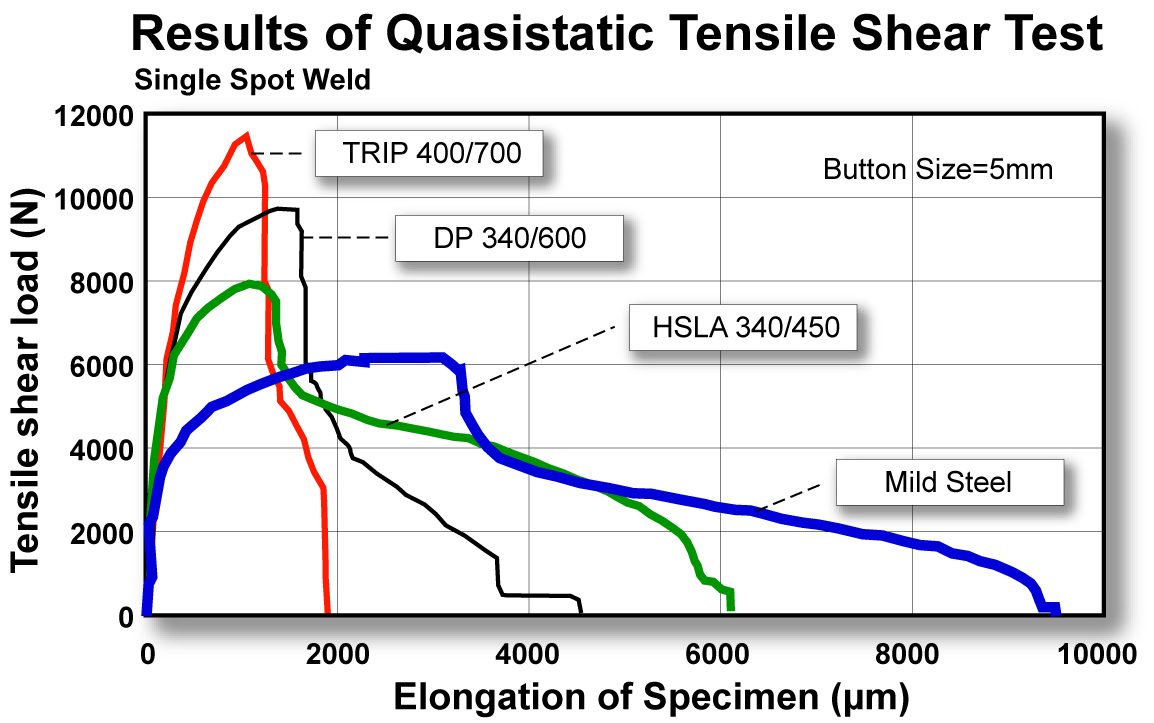
Figure 4: Tensile shear strength of single spot welds.L-4
While testing thick AHSS spot welds (from small button size to expulsion button) the fracture mode during shear-tension testing may change from interfacial to button pull out or plug. Despite interfacial fractures [Figure 5(a)], welds in AHSS may show high load-bearing capacity. In thin-gauge steels, the fracture is often in a button or plug (Figure 6).
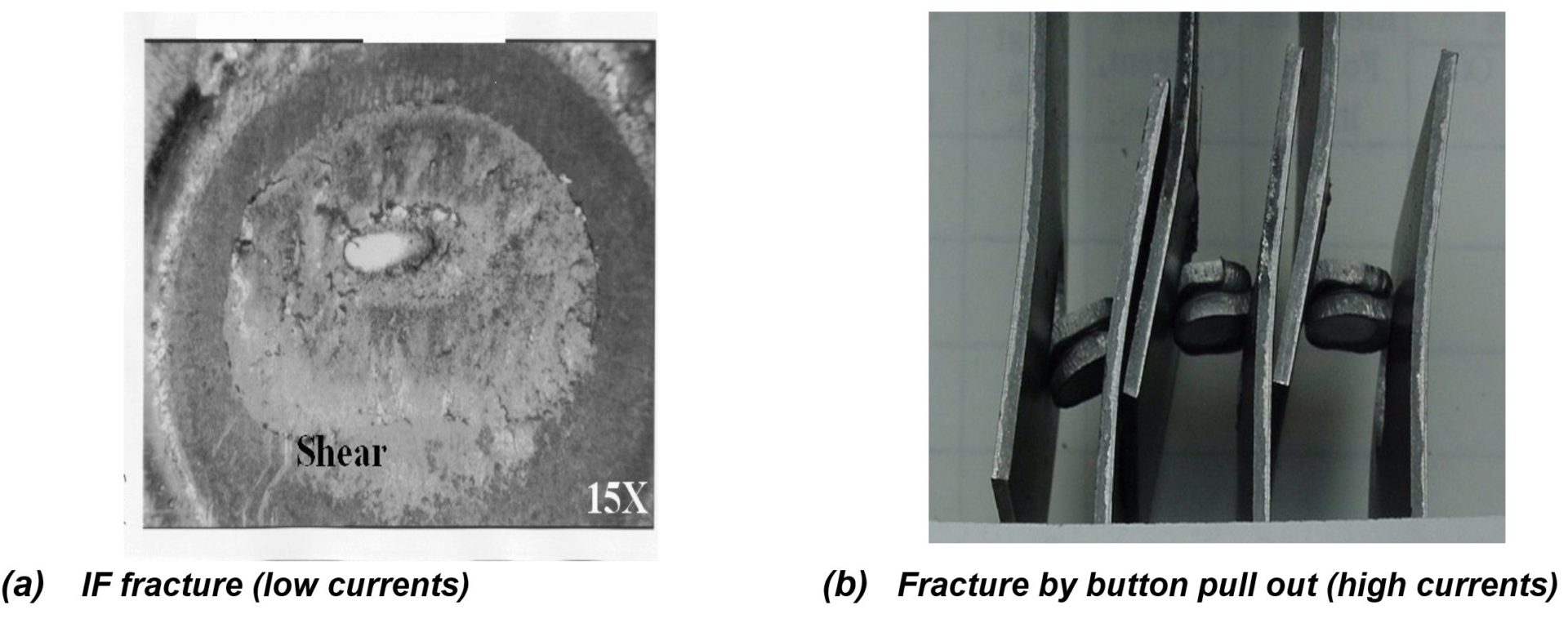
Figure 5: Fracture modes in thick (1.87-mm) DP 700/980 CR during tension-shear testing.
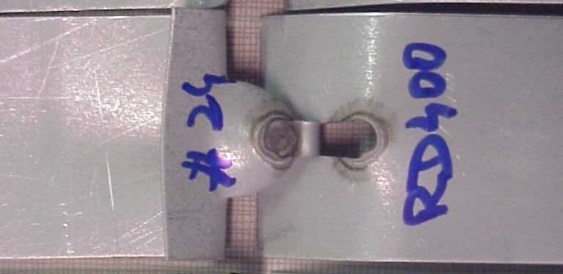
Figure 6: Fracture modes in thin (0.65-mm) DP 300/500 EG during tension-shear testing.L-2
In a studyL-6, Finite-Element Modeling (FEM) and fracture mechanics calculations can be used to predict the RSW fracture mode and loads in shear-tension tests of AHSS. The results were compared to those obtained for an Interstitial Free (IF) steel. The results of the work confirmed the existence of a competition between two different types of fracture modes, namely Full Button Failure (FBF) pull-out and interfacial fracture. The force required to cause a complete weld button pull-out type fracture was found to be proportional to the tensile strength and to the thickness of the BM as well as the diameter of the weld. The force to cause an interfacial weld fracture was related to the fracture toughness of the weld, sheet thickness, and weld diameter. For High-Strength Steels (HSS), it was determined that there is a critical sheet thickness above which the expected fracture mode could transition from pull-out to interfacial fracture. In this analysis, it was shown that, as the strength of the steel increases, the fracture toughness of the weld required to avoid interfacial fracture must also increase. Therefore, despite higher load-carrying capacity due to their high hardness, the welds in HSS may be prone to interfacial fractures. Tensile testing showed that the load-carrying capacity of the samples that failed via interfacial fracture was found to be more than 90% of the load associated with a FBF pull-out. This indicates that the load-bearing capacity of the welds is not affected by the fracture mode. Therefore, the mode of fracture should not be the only criteria used to judge the quality of spot welds. The load-bearing capacity of the weld should be the primary focus in the evaluation of the shear-tension test results in AHSS.
Presently, some steel sheets have tensile strengths of 1,500 MPa or more. Such steels are subjected primarily to hot-press forming. The strengths of spot-welded joints are illustrated in Figure 7. The tensile shear strength of welded joints tends to increase with increasing steel sheet strength. Conversely, the Cross-Tension Strength (CTS) of welded joints tends to decline when the steel sheet strength is 780 MPa or more. This is thought to occur for the following reason. With increasing steel sheet strength, the stress concentration at the nugget edge increases, and nugget ductility and toughness decrease. When the amount of any added element [such as Carbon (C)] is increased in order to secure the desired steel sheet strength, the hardness of the weld metal (nugget) obtained increases; this, in turn, causes the nugget toughness to decrease. Nugget toughness also decreases when the contents of embrittling elements (P and S) are increased. The following equation of equivalent carbon content has been proposed to express the effects of these elements has been known.


Figure 7: Effect of tensile strength of steel sheet on TSS and CTS of spot-welded joints.
It is believed that C, Silicon (Si), and Manganese (Mn) contribute to the increase in nugget hardness and Phosphorus (P) and Sulfur (S) contribute to the increase in segregation, thereby causing a decline in nugget toughness. The threshold value on the right-hand side represents the strength of a welded joint and the soundness of the fracture mode in a cross-tension test. When the Ceq (spot) is within the range indicated by the above equation, fracture always occur outside the nugget (plug fracture) and CTS is high. However, attempts have been made to enhance CTS by controlling the composition of steel sheet appropriately. It was reported that even when the steel sheet strength is maintained constant, the strength of the weld increases as C content decreases and the Si content increases. This is thought to occur for the following reason. With the increase in C content, the hardness of the weld increases and the sensitivity of the fracture to the stress concentration at the nugget end increases, thereby causing CTS to decline. By contrast, as the content of Si – a hardenability element – is increased, the region that is quench-hardened by Si widens, that is, the change in hardness in the region from the nugget to the BM becomes milder, thereby improving CTS.
According to a well-known material mechanics model, it is expected that the CTS of the spot- welded joints will improve with the increase in steel sheet strength. However, this contradicts the observed phenomenon. Therefore, a cross-tension test was considered based on fracture mechanics and attempted to clarify the dominant factors of CTS.
Understanding the fracture of spot-welded joints in the cross-tension test as a problem of crack propagation from around the nugget, the problem was studied using an elastic-plastic fracture mechanics model in order to obtain a general understanding of fracture, from the ductile fracture to the brittle fracture. According to elastic-plastic fracture mechanics, it is assumed that the crack starts to propagate when the crack propagation driving force (J) around the nugget under a tensile load reaches the fracture toughness (Jc) of the nugget edge. Therefore, it was attempted to derive the value of J and measure the value of Jc of the edge during the cross- tension test.
Figure 8 shows the distribution of maximum principal stress at the nugget edge under a load of 4 kN. The broken line in the figure indicates the fusion line. It is clear that the virtual crack in the edge opened during the deformation. The decline in potential energy that was caused by the opening was divided by the crack area to obtain the value of J. Figure 9 shows the dependence of the J-value on nugget diameter under a load of 5 kN, obtained for each of the two types of cracks. It is clear that, in either cracking direction, the J-value under the same load decreases with the increase in nugget diameter. According to the analysis result obtained for a nugget diameter of 3 √t, the J-value when the crack was allowed to propagate in the interfacial direction was slightly larger than that when the crack was allowed to propagate in the sheet thickness direction. However, for larger nugget diameters (4 and 5 √t), the J-value when the crack was allowed to propagate in the sheet thickness direction became larger than that when the crack was allowed to propagate in the interfacial direction.
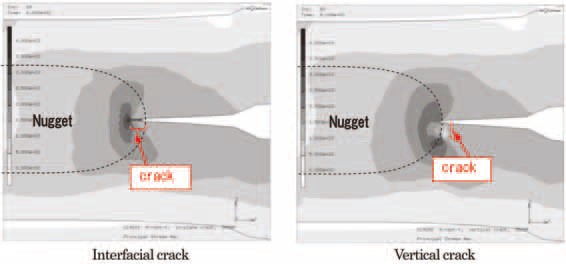
Figure 8: Deformed state and distribution of maximum principal stress at edge of nugget under the lead of 4 kN.N-5
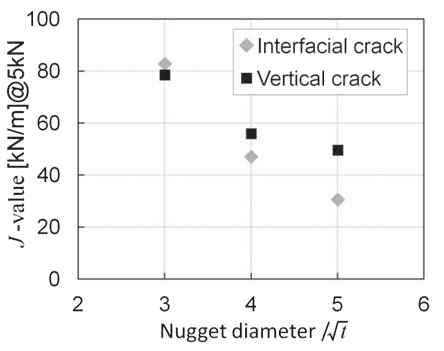
Figure 9: Dependence of J-value on nugget diameter under the load of 5 kN.N-5
In Figure 10, the fractured 0.30% C specimen revealed a grain boundary fracture at the edge and a cleavage fracture surface inside the nugget.
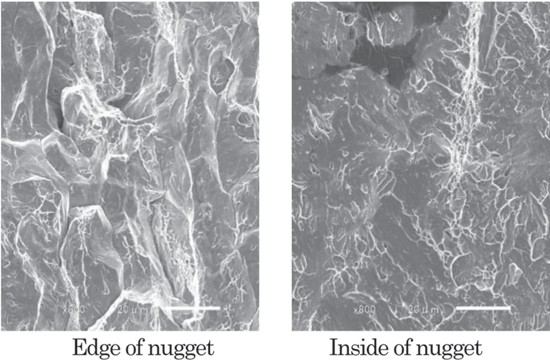
Figure 10: SEM images of fracture surface of miniature CT specimens after testing (0.30 mass % C).N-5
The CTS of welded joints was 2.4 kN for the 0.30% C steel sheet and 6.6 kN for the 0.13% C steel sheet, the ratio between them being 0.38. According to the fracture toughness test results, the fracture stress ratio [Jc (0.30% C)/Jc (0.13% C)]; the square root of J is proportional to stress) is 0.35. Thus, the above ratio was close to the test result. The 0.30% C joint subjected to the cross-tension test revealed a grain boundary fracture at the edge and a cleavage fracture surface inside the nugget.
Fracture Mode
Several automotive and national specifications are using the criterion of fracture modes as an indication of weld quality in production when using AHSS. During peel and chisel testing, results vary from FBF appearance to a complete interface fracture. An example of the various fracture modes experience by the automotive industry is shown in Figure 11.
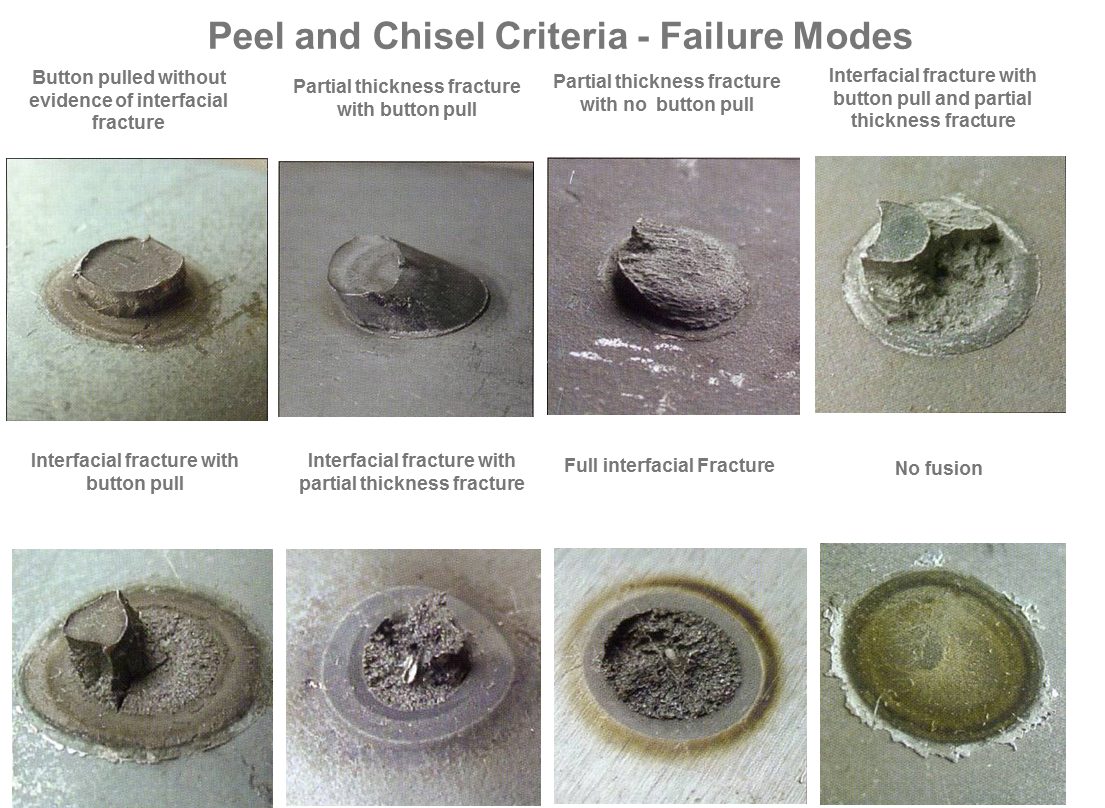
Figure 11: Peel and chisel test fracture modes in automotive industry.
There is an approximate relationship between hardness and fracture mode in resistance spot- welded joints. It is found that peel-type loading of resistance spot-welded joints (e.g., coach peel, cross-tension tensile, and chisel testing) begins to produce partial plug and interfacial fractures at hardness levels exceeding 450 Hardness Value (HV). The relationship between post-weld hardness and fracture mode in peel-type loading is illustrated in Figure 12. It can be seen that there are no set levels of hardness, where one type of fracture mode changes to another type of fracture mode. Instead, there is much overlap between the hardness levels, where specific fracture mode types occur. This indicates that post-weld hardness is not the only factor determining fracture mode.
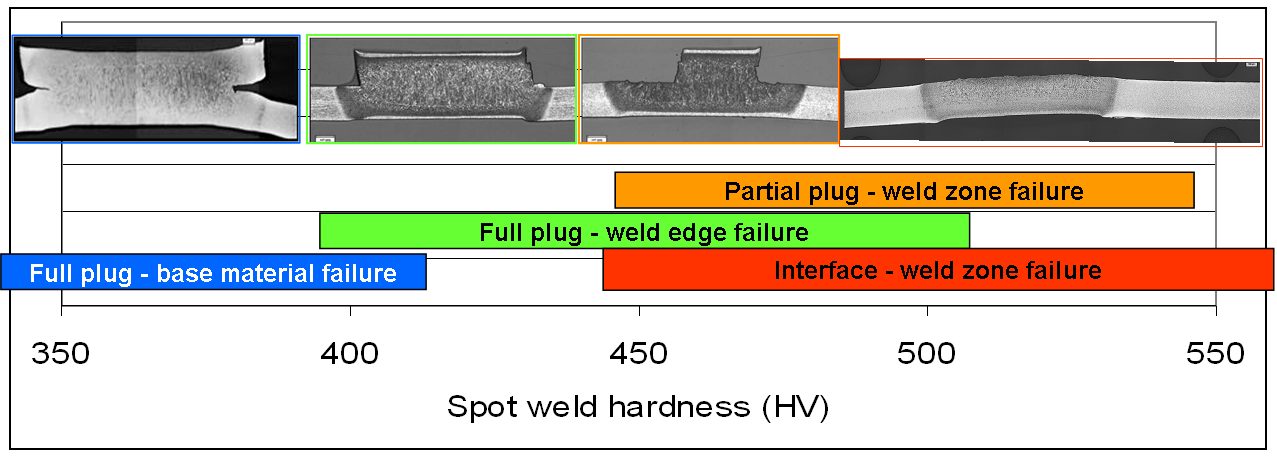
Figure 12: Schematic relationship between RSW hardness and failure mode in peel-type loading.
There are various approaches to predict the fracture of spot welded joints by detailed numerical simulations. However, there are many issues such as the adequate recording of different fracture modes or a numerical methodology for dissimilar welds, which mostly appear in automotive structures. Therefore, a new simulation approach has been developed managing to close the existing gap. This method is based on different damage criteria for each spot weld zone (BM, HAZ, and weld) in order to capture all relevant fracture modes. The model parameters are identified via an inverse method on the basis of simple standardized test (tensile shear tests and peel test), which makes the application efficient. All relevant fracture modes (interfacial fracture and plug fracture) can be detected. A precise prediction of spot welds behavior for similar and dissimilar joints were demonstrated. The results show that the material parameters determined for one sheet thickness are transferable to investigations with differing sheet thicknesses. Consequently, the experimental effort to characterize substitute spot weld models for full car crash simulations can be reduced.
The determination of the specific model parameters for a similar weld combination of DP automotive application steel with a low yield stress and large ultimate strength was presented (thickness of 1.5 mm, ferrite matrix with areas of martensite). A characterization of the plastic flow behavior for each zone is required. For the BM a tensile test provides the flow curve in the region of uniform elongation. In order to capture the plastic flow behavior of the transformed zones in a physical manner, the BM curve is scaled by the averaged hardness change in the HAZ and the weld. To determine the Gurson model parameters for the HAZ, a static peel test is done. This loading results in a high stress concentration in the vicinity of the notch which leads to fracture initiation and evolution in the HAZ. The numerical damage parameters for the HAZ are fitted according to the experiment (Figure 13).
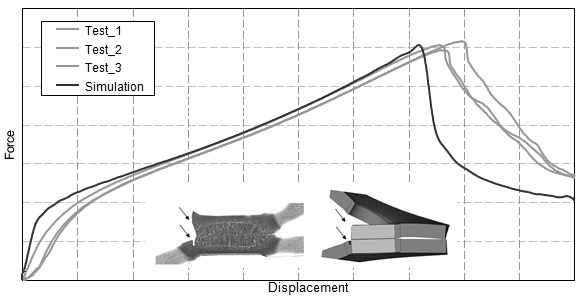
Figure 13: Parameter fitting for HAZ via peel test for DP steels.P-7
Back To Top