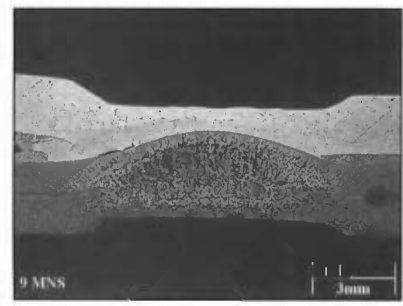
Aluminium/Steel Using Interlayer
In order to reduce the thickness of brittle intermetallic compound (IMC) formed at Aluminium/Steel interface to improve the mechanical properties of resistance spot welding of Aluminium/Steel, different interlayers, such as Al-cladded steelS-16, O-3, Y-4, Al-Si alloyW-15, Al-Mg alloyI-6, pure Al W-16, Zn coating.M-10, U-4, A-21 Sun et al.S-16 has done resistance spot welding of 1.4-mm SAE 1008 mild steel with 2-mm 5182-O aluminium alloy using 1 mm/1.5 mm cold rolled aluminium-clad steel as a transition metal with Aluminium/Steel thickness ratio of 20/80 (thickness ratio was not optimized). The formation of IMC cannot be observed at the interface for cold rolled aluminium-clad steel. The electrodes used were Class 2 30-deg truncated cone with 8-mm surface diameter and 3-inch face radius on the aluminium side and 30-deg truncated cone with 8-mm flat surface diameter on the steel side. Two separate nuggets created the aluminium and steel sides with a final nugget diameters of 10.1 mm and 8.2 mm, on aluminium and steel sides respectively, at the end of the 3rd pulse (Figure 1). With increasing welding time from 1 pulse to 3 pulses, the intermetallic compound layer thickness increased from 0 µm to 8.5 µm. As a comparison, the IMC layer thickness was approximately 65 µm for resistance spot welding of 1-mm AA 5052 and 0.8-mm low carbon steel without transition metal. The static and dynamic strength of the RSW samples in cross-tension and coach peel test were comparable to those of the peak load of self-piercing rivets (SPR). However, lap shear tensile testing of RSW samples had lower energy absorption than dissimilar SPR samples due to different failure modes (interfacial fracture may occur). Fatigue strength of RSW samples were lower than those of SPR samples due to stress concentration and tensile residual stress at the notch tip.
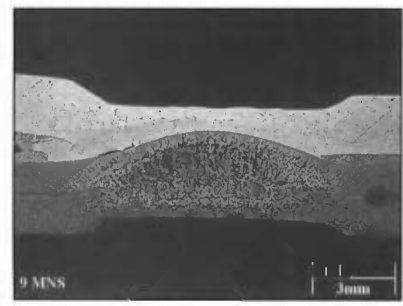
Figure 1: Cross-sectional macrostructure of resistance spot welding of SAE1008/A5182-O with 3 pulses of 12 cycles and welding current of 13.6 kA.S-16
Oikawa et al.O-3 have done resistance spot welding of 0.4 mm-thick cold rolled steel with 0.6 mm-thick pure aluminium with 0.77 mm-thick aluminium-clad steel sheet as the insert metal. Fe-Al IMCs have not been noted at the Aluminium/Steel interface of aluminium-clad steel sheet and a peel strength of 32.1 N/mm can be achieved. IMC layer thickness was about 5 µm at Al/steel interface when aluminium alloy and steel was resistance spot welded with aluminium clad steel sheet as insert. However, the tensile shear strength (Figure 2) and U-tension strength (Figure 3) can be 3.6 kN and 1.5 kN which were similar to Al/Al resistance spot weld joint and were much higher than direct resistance spot welding of 2.4 kN and 0.6 kN. However, it should be noted that resistance spot welding with aluminium-clad steel added weight, and difficulties in hot rolled aluminium cladding process result in high cost. Thus, more investigations have been done recently on improving the cladding method and using thinner and lighter metals as interlayers.
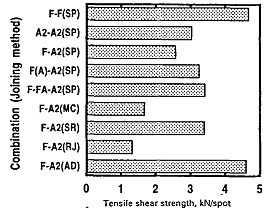
Figure 2: Comparison of tensile shear strength of Al/steel joints by various methods (SP-spot welding; MC-mechanical clinching; RJ-rivet joining; AD-adhesion bonding).O-3
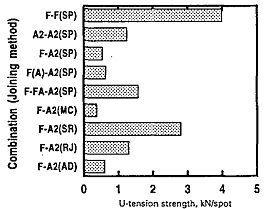
Figure 3: Comparison of U-tension strength of Al/steel joints by various methods (SP-spot welding; MC-mechanical clinching; RJ-rivet joining; AD-adhesion bonding).O-3
In order to reduce the IMC layer thickness, Zhang et al.W-15 used 4047 AlSi12 as an interlayer to suppress the IMC growth during resistance spot welding of 1 mm H22YD-Z100 Zn-coated high-strength steel sheets with 1.5 mm EN AW 6008-T66 aluminium alloy sheets. The effect of different interlayer thickness, i.e. 100 µm, 200 µm, 300 µm, 400 µm, on IMC growth behavior and mechanical properties were investigated. IMCs consisted of Fe2(Al,Si)5 and Fe4(Al,Si)13 and the thickness of IMCs reduced from 1.8 µm to 0.6 µm as the thickness of AlSi12 interlayer, increasing from 100 µm to 400 µm. But all were much thinner compared to 4 µm for spot welds without an interlayer. Nugget diameter reduced with increasing interlayer thickness and maximum tensile shear strength of 6.2 kN and pull-out failure mode were obtained with an interlayer thickness of 300 µm.
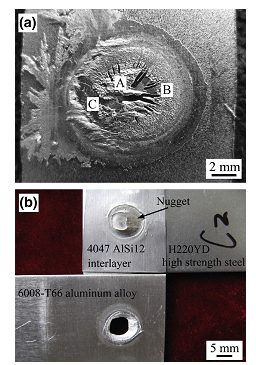
Figure 4: Fracture modes of H220YD high-strength steel/6008-T66 resistance spot weld joints (a) interfacial fracture without interlayer and (b) pull-out failure with 4047 AlSi12 interlayer thickness of 300 µm. W-15
Ibrahim et al.I-6 had investigated resistance spot welding of 2 mm A6061-T6 and 2 mm type 304 austenitic stainless steel with 80 µm thick Al-Mg alloy (80 wt % Al and 20 wt% Mg). Under the same welding condition, lap shear tensile strength was higher for welds with an Al-Mg interlayer than without the interlayer, and a peak strength of 8.4 kN can be obtained with welding current of 16.1 kA and welding force of 9.3 kN. A thin IMC layer of approximately 2 µm can be observed, which lead to a high strength. Fatigue strength of dissimilar RSW Aluminium/Steel samples were higher than Friction Stir Spot Welding samples. The failure mode depended on the load level. Pull-out failure occurred at high load (Pmax > 3 kN), shear fracture at 2.25 kN < Pmax <3 kN, upper Al sheet fracture at Pmax < 2.25 kN.
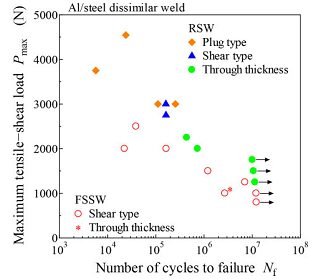
Figure 5: Relationship between peak load and number of cycles.I-6
Galvanized steel (GI) and Galvannealed steel (GA) are widely used in the automotive industry, and the presence of Zn layer may affect the weldability of Aluminium/Steel. Al-Zn eutectic liquid formed at Aluminium/Steel interface can efficiently remove oxide film and squeezed outside by electrode force. Thus, metallic surface of aluminium and steel can be revealed, and the Al-Fe IMC layer formed and a metallurgical bond was created.M-10, U-4 Arghavani et al.A-21 have investigated the resistance spot welding of 2 mm Al-5052 to 1 mm low carbon galvanized steel (ASTM A653 CS Type B-G60) (GI/Al) and compared that with the weldability of Al 5052 to uncoated steel DC01 (PS/Al). It showed the IMC layer at the GS/Al interface with the tongue-like layer of Fe2Al5 on the steel side and needle-like FeAl3 on the aluminium alloy side, as normally observed in Aluminium/Steel dissimilar welding (Figure 6).Z-3, U-4 GI/Al joints had thinner IMC layers at almost all the welding currents compared to PS/Al joints. And the IMC layer thickness in GI/Al increased initially with increasing welding current up to 12 kA and then decreased beyond it, which was due to heat consumption with Zn evaporation at higher welding current (I > 12 kA). Tensile shear strength of GI/Al welds were lower than PS/Al welds at welding current less than 12 kA since lower current led to incomplete nugget at GI/Al welds. However, tensile shear strength of GI/Al welds exceeded PS/Al welds at higher welding current since IMC layer thickness was over the critical value of approximately 5.5 µm for PS/Al joints at the higher welding current (Figure 7). Both GI/Al and PS/Al had an interfacial fracture mode with crack initiation at the peripheral regions of the weld and propagated through the IMCs layer/aluminium sheet.
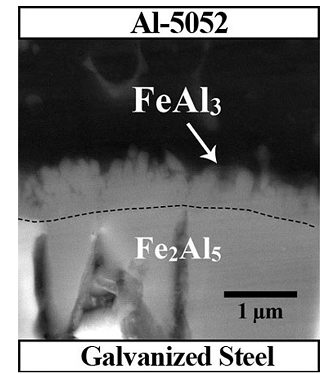
Figure 6: SEM image of IMC layer in GS/Al specimen.A-21
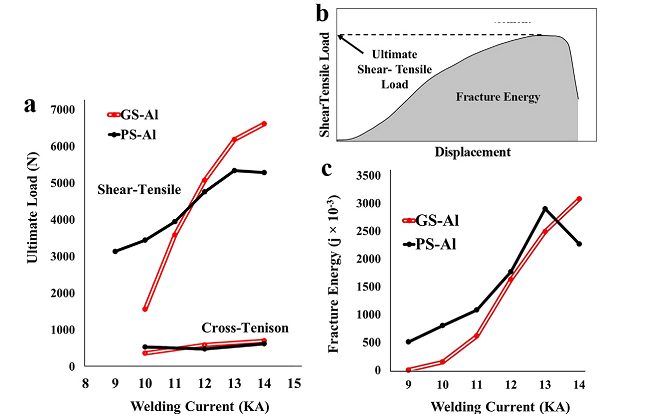
Figure 7: (a) Ultimate tensile shear and cross-tension strength vs welding current; (b) schematics of load-displacement curve and fracture energy calculation for tensile shear testing; (c) Fracture energy vs welding current.A-21