PHS and PQS Overview
A Brief Overview of Press Hardening
Press hardening (also commonly known as hot stamping or hot press forming) combines forming and heat treatment technology to create high strength complex shapes. Elevated temperature allows for production of complex shapes. This can be achieved by 10 different processes. To summarize:
- Forming from the “as delivered” ferritic-pearlitic microstructure (i.e., at ❶ in Figure 1). The formed part is later heated in a special furnace and quenched in a cooled press die. This process is commonly known as “Indirect Hot Stamping”, “Form Hardening” or “Post Form Heat Treatment”.
- Forming after heating a blank to over 880 °C to create an austenitic microstructure (i.e., at ❷ in Figure 1). The process is known as “Direct Hot Stamping”, “Press Hardening” or “Hot Press Forming”.
Selection of the process type usually depends on the coating and part complexity.
In press hardening, the required press forces are relatively low – compared to the final part strength – and springback is significantly reduced, if not eliminated. The parts get their final properties during the quenching cycle. In Press Hardening, OEMs require the final mechanical properties within the formed part to be guaranteed by the part supplier. In contrast, in cold stamping, the mechanical properties of the incoming sheet steel must be guaranteed by the steel supplier.
If the cooling rate is faster than the critical cooling rate of the steel, the final microstructure will be almost fully martensitic producing what is called the “Full Hard” (FH) condition. Depending on a part design, “soft zones” may be required. In this case, the heat treatment is controlled such that the soft zones have other phases such as bainite and in some cases ferrite and pearlite. The process of tailoring the microstructure distribution is called as “tailored tempering” or “tailored properties”. Parts with tailored properties may be described as a “multi-strength part” or a “tailored-part”.
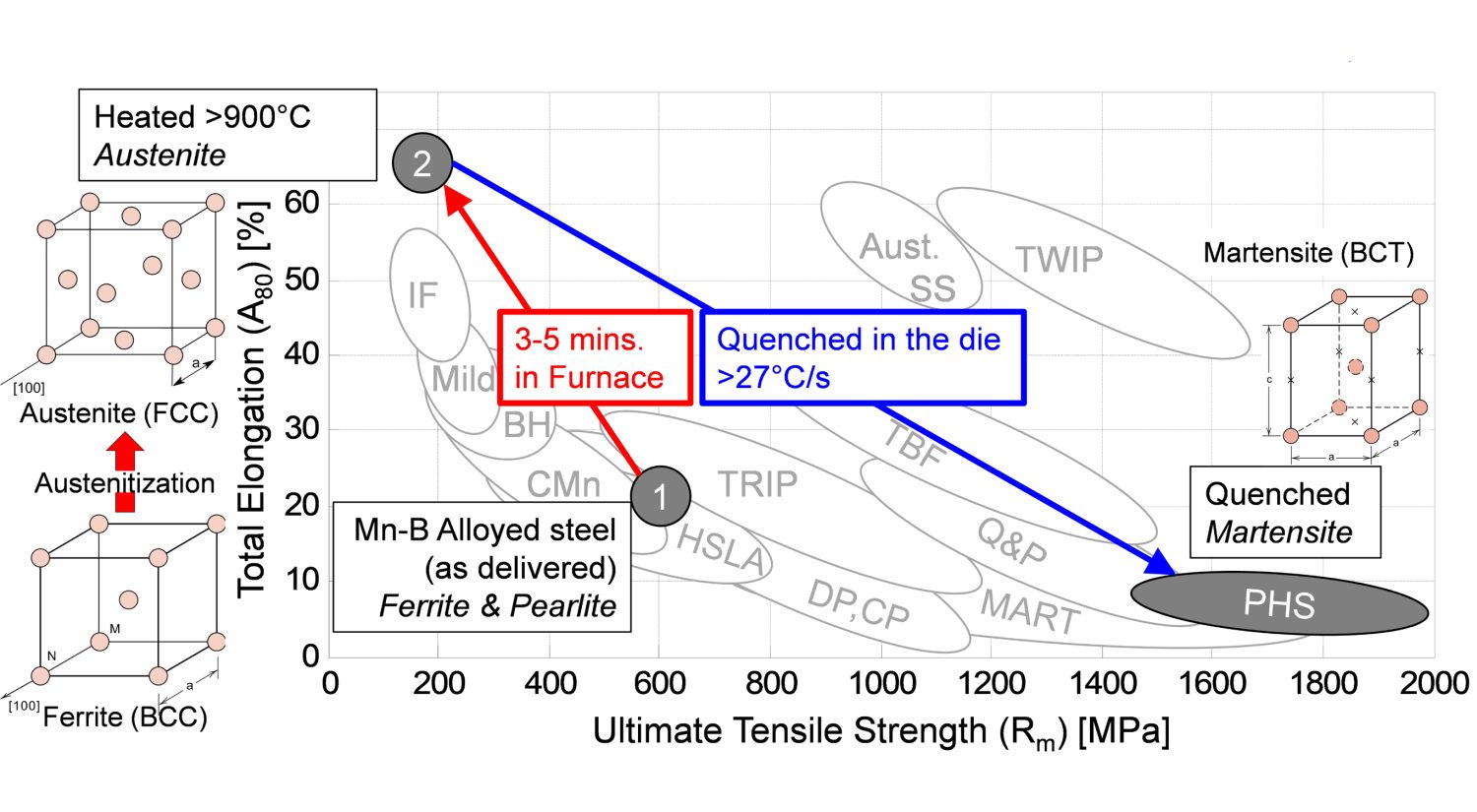
Figure 1: A short summary of press hardening process (re-created after B-14).
Press hardening steels use carbon and manganese, with boron for additional hardenability. They have been used in the automotive industry since 1980s, however their use has increased significantly in the last two decades. There are mainly three groups of PHS grades:
- PHS1500 (see PHS Grades with TS approximately 1500 on link page): refers to the first and most commonly used PHS grade 22MnB5 or the recently developed grades like 20MnB8 used in the “pre-cooled direct process” or the air-hardening 22MnSiB9-5 used in the “multi-step process.” These grades have approximately 1,500 MPa (typical range: 1300-1650 MPa) tensile strength after quenching.
- Higher elongation grades – with some also known as Press Quenched Steels (PQS): PQS450, PQS550, PHS1000, and PHS1200 (see the section on Grades With Higher Ductility on the linked page): these grades have high elongation and/or bending angle after quenching. Tensile strength should range from 450 MPa to 1,300 MPa after the hot stamping process.
- Higher strength grades: PHS1800 and PHS2000 (see PHS Grades with TS over 1500 on link page): these grades have tensile strength of 1,800 MPa to 2,000 MPa after quenching.
- Emerging grades (see Other grades for press hardening process on link page for this and the stainless link following), such as Medium-Mn steels, and even some types of stainless steels are suitable for the hot stamping process.
Other PHS Pages in these Guidelines:
Press Hardened Steels – Metallurgy
PHS Production Methods
PHS Simulation
PHS Tailored Products
PHS Automotive Applications and Usage
![]() |
Thanks are given to Eren Billur, Ph.D., Billur MetalForm, who contributed this article. |